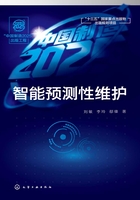
3.2.2 基于CPS的智能预测性维护模型
工业4.0是价值链组织技术和概念的集合术语,基于无线射频(Radio Frequency Identification,RFID)、信息物理系统、物联网(Internet of Things,IoT)、服务互联网(Internet of Services,IoS)和数据挖掘(Data Mining,DM),促进了智能工厂愿景的实现。在工业4.0的模块化和结构化智能工厂中,CPS监测物理对象和运营过程,创建物理世界的虚拟副本,并实现离散化过程控制和决策;信息物理系统通过物联网能够实时地与其他CPS系统和人类进行交流和合作;通过数据挖掘和服务互联网,价值链参与者可以在内部和跨组织提供和利用服务。挪威Wang等人给出一个工业4.0的定义,确定了一些实现的主要原则,并展示一种图3.4所示的实现零缺陷制造(Zero-Defect Manufacturing,ZDM)的智能预测维护模型与系统[7]。

图3.4 实现零缺陷制造的智能预测性维护模型与系统
IPdM系统基于CPS、IoT、IoS、计算智能、数据挖掘、群体智能(Swarm Intelligence,SI)等许多关键技术,需要被研究和开发以适应行业需求。IPdM中有6个主要模块:传感器和数据采集,信号预处理和特征提取,维护决策,关键性能指标(Key Performance Indicators,KPI),维护调度优化,误差校正、补偿与反馈控制。
(1)传感器和数据采集模块
这是实施设备诊断和预测IPdM维护策略的第一步。该模块的任务是选择合适的传感器和最佳的传感器安装策略。数据采集过程将传感器信号变成设备状态信息,不同传感器用来收集不同数据,如温度传感器、振动传感器、声发射传感器等。
(2)信号预处理和特征提取模块
通常来说,传感器信号的处理有两个步骤。一个是信号处理,可以提高信号的特性和质量,相关的信号处理技术包括滤波、放大、数据压缩、数据验证和去噪等,这些技术可以提高信噪比。另一个是特征提取,提取能够表征偶然的失效或错误的信号特征。一般而言,特征可以从时域、频域(快速傅里叶变换、离散傅里叶变换)和时频域(小波变换、小波包变换,或者经验模态分解)等三个域进行提取。主成分分析(Principal Component Analysis,PCA)是通过正交变换将一组可能存在相关性的变量转换为一组尽可能多地反映原来变量信息的统计方法,实现特征的降维。
(3)维护决策模块
维护决策模块提供充足、高效的信息辅助维护人员采取维护措施的决策。维护决策模块分为故障诊断和故障预测两类,故障诊断[包括支持向量机、人工神经网络(如自组织映射、综合反向传播等算法)]的重点是检测、隔离和识别故障发生,故障预测(如自回归滑动平均模型、ANN等)试图在发生错误或失效之前预测设备的剩余使用寿命RUL(Remaining Useful Life)。决策支持模型可分为四类:物理模型,统计模型,数据驱动模型,混合模型。由于IPdM策略主要依赖于反映设备状况的信号和数据,数据驱动模型和混合模型将处于主导地位。
(4)关键性能指标模块
关键性能指标KPI(Key Performance Indicators)图也叫蜘蛛网图或健康雷达图,用于显示部件的退化程度。每条雷达线显示部件从0(完美)到1(损坏)的状况。颜色则显示了级别,如安全、警告、报警、故障和缺陷,可以可视化地评估设备性能。
(5)维护调度优化模块
维护调度优化是一种NP问题(非确定性多项式问题),群体智能算法是一个很好解决这类问题的方法。IPdM可以应用遗传算法(Genetic Algorithm,GA)、粒子群优化(Particle Swarm Optimization,PSO)、蚁群算法和蜜蜂群算法动态地寻找最优的预测维护调度方案。
(6)误差校正、补偿与反馈控制模块
该模块将利用维护决策支持模块的结果进行误差校正、补偿和反馈控制。