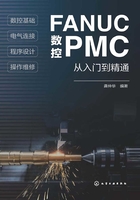
第1章 数控技术基础
1.1 数控技术与数控系统
1.1.1 数控技术概述
(1)数控技术与机床
数控(numerical control,NC)是利用数字化信息对机械运动及加工过程进行控制的一种方法。数控技术的发展和电子技术的发展保持同步,至今已经历了从电子管、晶体管、集成电路、计算机到微处理机的演变,由于现代数控都采用计算机控制,因此,又称计算机数控(computerized numerical control,CNC)。
数字化信息控制必须有相应的硬件和软件,这些硬件和软件的整体称为数控系统(numerical control system)。数控系统包括了计算机数控装置(computerized numerical controller,CNC)、集成式可编程序控制器(PLC或PMC)、伺服驱动、主轴驱动等,其中,数控装置是数控系统的核心部件。
由于数控技术、数控系统、数控装置的英文缩写均为CNC或NC,因此,在不同的使用场合,CNC或NC一词具有三种不同含义,即:在广义上,代表一种控制方法和技术;在狭义上,代表一种控制系统的实体;有时,还可特指一种具体的控制装置(数控装置)。
数控技术的诞生源自于机床,其目的是解决金属切削机床的轮廓加工——刀具轨迹的自动控制问题。这一设想最初由美国Parsons公司在20世纪40年代末提出,1952年,Parsons公司和美国麻省理工学院(Massachusetts Institute of Technology)联合,在一台Cincinnati Hydrotel立式铣床上安装了一套试验性的数控系统,并成功地实现了三轴联动加工,这是人们所公认的第一台数控机床。1954年,美国Bendix公司在Parsons专利的基础上,研制出了第一台工业用数控机床,随后,数控机床取得了快速发展和普及。
机床是对金属或其他材料的坯料、工件进行加工,使之获得所要求的几何形状、尺寸精度和表面质量的机器,是机械制造业的主要加工设备。由于加工方法、零件材料的不同,机床可分为金属切削机床、特种加工机床(激光加工、电加工等)、金属成型机床、木材加工机床、塑料成型机床等多种类型,其中,以金属切削机床最为常用,工业企业常见的车床、铣床、钻床、镗床、磨床等都属于金属切削机床。
机床用来制造机器零件,它是制造机器的机器,故又称为工作母机。没有机床就不能制造机器,没有机器就不能生产工业产品,就谈不上发展经济,因此,机床是国民经济基础的基础。没有好的机床就制造不出好的机器,就生产不出好的产品,所以,机床的水平是衡量一个国家制造业水平、现代化程度和综合实力的重要标志。
(2)数控技术的产生
数控技术最初是为解决金属切削机床自动控制问题所研发。在金属切削机床上,为了能够完成零件的加工,机床一般需要进行以下三方面的控制。
①动作顺序控制。机床对零件的加工一般需要有多个加工动作,加工动作的顺序有规定的要求,称为工序,复杂零件的加工可能需要几十道工序才能完成。因此,机床的加工过程需要根据工序的要求,按规定的顺序进行。
以图1.1.1(a)所示最简单的攻丝机为例,为完成攻丝动作,它需要进行图1.1.1(b)所示的“丝锥向下、接近工件→丝锥正转向下、加工螺纹→丝锥反转退出→丝锥离开工件”4步加工。

图1.1.1 动作的顺序控制
动作的顺序控制只需要根据加工顺序表,按要求依次通断接触器、电磁阀等执行元件便可完成,这样的控制属于开关量控制,即使利用传统的继电-接触器控制系统也能实现,而可编程序控制器(PLC)的出现,更是使之变得十分容易。
②切削速度控制。金属切削机床使用刀具加工零件,为了提高加工效率和表面加工质量,需要根据刀具和零件的材料、直径及表面质量的要求,来调整刀具与工件的相对运动速度(切削速度),即改变刀具或零件的转速。
改变切削速度属于传动控制,它既可通过齿轮变速箱、传动带等机械传动实现,也可利用电气传动直接改变电动机转速实现,早期的直流调速和现代的交流调速都可以用于机床的切削速度控制。
③运动轨迹控制。为了将零件加工成规定的形状(轮廓),必须控制刀具与工件的相对运动轨迹(简称刀具轨迹)。例如,对于图1.1.2所示的叶轮加工,在加工时必须同时对刀具的上下(Z轴)、叶轮的回转(C轴)和摆动(A轴)进行同步控制,才能得到正确的轮廓。

图1.1.2 运动轨迹的控制
刀具轨迹控制不仅需要控制刀具的位置和运动速度,而且需要进行多个运动的合成控制(称为多轴联动)才能实现,这样的控制只有通过数字技术(数控)才能实现。因此,机床采用数控的根本目的是解决运动轨迹控制的问题,使之能加工出所需要的轮廓。
1.1.2 数字控制原理
(1)轨迹控制原理
数控机床的刀具轨迹控制,实质上是应用了数学上的微分原理,例如,对于图1.1.3所示XY平面的任意曲线运动,其控制原理如下。

图1.1.3 轨迹控制原理
①微分处理。CNC根据运动轨迹的要求,首先将曲线微分为X、Y方向的等量微小运动ΔX、ΔY,这一微小运动量称为CNC的插补单位。
②插补运算。CNC通过运算处理,以最接近理论轨迹的ΔX、ΔY独立运动(或同时运动)折线,来拟合理论轨迹。
这种根据理论轨迹(数学函数),通过微分运算确定中间点的方法,在数控上称为“插补运算”。插补运算的方法很多,但是,以目前的计算机处理速度和精度,任何一种插补方法都足以满足机械加工的需要,故无需对此进行深究。
③脉冲分配。CNC完成插补运算后,按拟合线的要求,向需要运动的坐标轴发出运动指令(脉冲);这一指令脉冲经伺服驱动器放大后,转换为伺服电机的微小转角,然后利用滚珠丝杠等传动部件,转换为X、Y轴的微量直线运动。
由此,便可得到以下结论。
①能够参与插补运算的坐标轴数量,决定了数控系统拟合轨迹的能力,理论上说,2轴插补可拟合任意平面曲线,3轴插补可拟合任意空间曲线;如能够进行5轴插补运算,则可在拟合任意空间曲线的同时,控制任意点的法线方向等。
②只要数控系统的脉冲当量(插补单位,如ΔX、ΔY等)足够小,微量运动折线就可以等效代替理论轨迹,使得刀具实际运动轨迹具有足够的精度。
③只要改变各坐标轴的指令脉冲分配方式(次序、数量),便可改变拟合线的形状,从而获得任意的刀具运动轨迹。
④只要改变指令脉冲的输出频率,即可改变坐标轴(刀具)的运动速度。
因此,理论上说,只要机床结构允许,数控机床便能加工任意形状的零件,并保证零件有足够的加工精度。
一般而言,数控设备对脉冲频率的要求并不十分高,因此,控制轴数、联动轴数、脉冲当量是衡量数控设备性能指标的关键参数。
(2)轴与轨迹控制数
在数控系统上,能够进行插补控制的轴称为进给轴或NC轴,显然,NC轴越多,能够通过数控装置控制的运动也就越多,系统的控制能力也就越强;进一步说,如果计算机的运算速度足够高,同一数控装置还可以同时进行多条轨迹的插补运算,这样的系统就具备了多轨迹控制能力。
数控系统的多轨迹控制功能在不同公司生产的数控系统上有不同的表述方法。例如,FANUC公司称为“多路径控制(multi-path control)”,SIEMENS公司则称为“多加工通道控制(multi-machining channel control)”等。
多轨迹控制本质上是利用现代计算机的高速处理功能,同时运行多个加工程序,同时进行多种轨迹的插补运算,使得一台数控装置具备了同时控制多种轨迹的能力,从而,真正实现了早期数控系统曾经尝试的计算机群控(DNC)功能,使得多主轴同时加工、复合加工乃至FMC(柔性加工单元)、FMS(柔性制造系统,参见后述)等现代化数控机床的控制技术成为现实。
随着微处理器运算速度的极大提高,当代先进的数控系统都具有多轴、多轨迹控制功能。例如,FANUC公司生产的最新一代FANUC 30i MODEL B系统,最大可用于96轴、15路径(轨迹)控制;SIEMENS公司最新一代SIEMENS 840Dsl数控系统,最大可用于93轴、30加工通道(轨迹)控制等。
(3)联动轴数
在数控系统上,能参与插补运算的最大坐标轴数称为同时控制轴数,简称联动轴数。联动轴数曾经是衡量CNC性能水平的重要技术指标之一,联动轴数越多,数控系统的轨迹控制能力就越强。
数控系统的联动轴数与控制对象的要求有关。理论上说,对于平面曲线运动只需要2轴联动,空间曲线只需要3轴联动;对于空间曲线及法线的控制,则需要5轴联动;如果能同时控制X、Y、Z直线运动及绕X、Y、Z的回转运动(A、B、C轴),便可实现三维空间的任意运动轨迹控制。
需要注意的是,计算机技术发展到了今天,就数控装置而言,无论是其处理速度还是运算精度,处理多轴插补运算已不存在任何问题,因此,数控装置具有多少轴联动功能,实际上已不那么重要;作为数控系统最重要的是怎样保证坐标轴能完全按照数控装置的指令脉冲运动,确保实际运动轨迹与理论轨迹一致。因此,国外先进的数控系统都需要将伺服驱动和数控装置作为一个整体进行设计,并通过数控装置进行坐标轴的闭环位置控制,来确保坐标轴实际运动和指令脉冲一致,在这一点上,目前国产数控的技术水平还暂时达不到,在使用时需要引起注意。
(4)脉冲当量
数控装置单位指令脉冲所对应的坐标轴实际位移,称为最小移动单位或脉冲当量,高精度数控系统的脉冲当量通常就是数控装置的插补单位。
脉冲当量是数控设备理论上能够达到的最高位置控制精度,它与数控系统性能有关。使用步进电机驱动的经济型数控,由于步进电机步距角的限制,其脉冲当量通常只能达到0.01mm左右;国产普及型数控的脉冲当量一般可达到0.001mm;进口全功能数控的脉冲当量一般可达到0.0001mm,甚至更小,例如,用于集成电路生产的光刻机(数控激光加工机床),其脉冲当量已经可达纳米(0.000001mm)级。
数控设备的实际运动精度和位置测量装置密切相关,采用电机内置编码器作为位置检测元件时,可保证电机转角的准确;采用光栅或编码器直接检测直线距离或回转角度时,可以保证直线轴或回转轴的实际位置准确。
国产经济型数控的步进电机为开环控制,无位置检测装置,故存在失步现象。国产普及型数控的伺服电机内置编码器一般为2500P/r(脉冲/转),通过4倍频线路,对于滚珠丝杠导程为10mm的直线运动系统,如果伺服电机和滚珠丝杠为1:1连接,其位置检测精度可到1μm。进口全功能CNC的电机内置编码器光栅的分辨率已可达228P/r左右,同样对于滚珠丝杠导程10mm的传动系统,如果伺服电机和滚珠丝杠为1:1连接,其位置检测精度可以达到0.04μm。
1.1.3 数控系统组成
数控系统的基本组成如图1.1.4所示。数控系统是以运动轨迹作为主要控制对象的自动控制系统,其控制指令需要以程序的形式输入,因此,作为数控系统的基本组成,需要有数据输入/显示装置、计算机控制装置(数控装置)、脉冲放大装置(伺服驱动器及电机)等硬件和配套的软件。

图1.1.4 数控系统的组成
(1)数据输入/显示装置
数据输入/显示装置用于加工程序、控制参数等数据的输入,以及程序、位置、工作状态等数据的显示。CNC键盘和显示器是任何数控系统都必备的基本数据输入/显示装置。
CNC键盘用于数据的手动输入,故又称手动数据输入单元(manual data input unit,简称MDI单元);现代数控系统的显示器基本上都使用液晶显示器(liquid crystal display,LCD)。数控系统的键盘和显示器通常制成一体,这样的数据输入/显示装置简称MDI/LCD单元。
作为数据输入/显示扩展设备,早期的数控系统曾经采用光电阅读机、磁带机、软盘驱动器和CRT显示器等外部设备,这些设备目前已经淘汰,个人计算机(PC机)、存储卡、U盘等是目前最常用的数控系统数据输入/显示扩展设备。
(2)数控装置
数控装置是数控系统的核心部件,它包括输入/输出接口、控制器、运算器和存储器等。数控装置的作用是将外部输入的控制命令转换为指令脉冲或其他辅助控制信号,以便通过伺服驱动装置或电磁元件,控制坐标轴或辅助装置运动。
坐标轴的运动速度、方向和位移直接决定了运动轨迹,它是数控装置的核心功能。坐标轴的运动控制信号(指令脉冲)通过数控装置的插补运算生成,指令脉冲经伺服驱动装置的放大后,驱动坐标轴运动。衡量数控装置的性能和水平,必须从其实际位置控制能力上区分。
国产普及型数控目前只具备产生位置指令脉冲的功能,输出的脉冲需要通过通用型伺服驱动器进行放大、转换成电机转角,数控装置并不能对坐标轴的实际位置进行实时监控和闭环控制,也不能根据实际轨迹调整各插补轴的指令脉冲输出,因此,其实际位置、轨迹控制精度通常较低。
进口全功能数控不仅能够产生位置指令脉冲,而且坐标轴的闭环位置控制也通过数控装置实现,因此,数控装置不但可以对坐标轴的实际位置进行实时监控和闭环控制,而且可以根据实际轨迹调整各插补轴的指令脉冲输出,以获得高精度的运动轨迹。进口控制装置技术先进、结构复杂、价格高,但其位置、轨迹控制精度均大大优于国产普及型数控。
(3)伺服驱动
伺服驱动装置由伺服驱动器(servo drive,亦称放大器)和伺服电机(servo motor)等部件组成,按日本JIS标准,伺服(servo)是“以物体的位置、方向、状态等作为控制量,追踪目标值的任意变化的控制机构”。
伺服驱动装置不仅可和数控装置配套使用,还可构成独立的位置随动系统,故又称伺服系统。早期数控系统的伺服驱动装置采用步进电机或电液脉冲马达等驱动装置,到了20世纪70年代中期,FANUC公司率先开始使用直流伺服电机驱动装置;自20世纪80年代中期起,交流伺服电机驱动已全面替代直流伺服驱动,而成为数控系统的主流。在现代高速加工机床上,已开始逐步使用图1.1.5所示的直线电机(linear motor)、内置力矩电机(built-in torque motor)或直接驱动电机(direct drive motor)等新颖无机械传动部件的直线、回转轴直接驱动装置。

图1.1.5 新颖驱动电机
伺服驱动系统的结构与数控装置的性能密切相关,因此,它是区分经济型、普及型与全功能型数控的标准。经济型CNC使用的是步进驱动;国产普及型CNC由于数控装置不能进行闭环位置控制,故需要使用具有位置控制功能的通用型伺服驱动;进口全功能型CNC本身具有闭环位置控制功能,故使用的是无位置控制功能的专用型伺服驱动。
(4)PLC
PLC是可编程序逻辑控制器(programmable logic controller)的简称,数控系统的PLC通常与数控装置集成一体,这样的PLC专门用于机床控制,故又称可编程机床控制器(programmable machine controller,简称PMC)。根据不同公司的习惯,数控系统的集成PLC在FANUC数控系统上称为PMC,而在SIEMENS等其他数控系统上仍然称为PLC。
数控系统的PLC用于数控设备中除坐标轴(运动轨迹)外的其他辅助功能控制,例如,数控机床主轴、刀具自动交换、冷却、润滑、工件松/夹等。在简单的国产普及型数控系统上,辅助控制命令经过数控装置的编译后,也可用开关量输出信号的形式直接输出,由强电控制电路或外部PLC进行处理;在进口全功能型数控系统上,PMC(PLC)一般作为数控装置的基本组件,直接与数控装置集成一体,或者通过网络连接使两者成为统一整体。
(5)其他
随着数控技术的发展和机床控制要求的提高,数控系统的功能在日益增强。例如,在金属切削机床上,为了控制刀具的切削速度,主轴是其必需部件;特别是随着车铣复合等先进数控机床的出现,主轴不仅需要进行速度控制,而且需要参与坐标轴的插补运算(Cs轴控制),因此,在全功能数控系统上,主轴驱动装置也是数控系统的基本组件之一。
此外,在位置全闭环控制的数控机床上,用于直接位置测量的光栅、编码器等也是数控系统的基本部件。为了方便用户使用,系统生产厂家标准化设计的机床操作面板等附件,也是数控系统常用的配套部件;在先进的数控系统上,还可以直接选配集成个人计算机的人机界面(man machine communication,MMC),进行文件的管理和数据预处理,数控系统的功能更强,性能更完善。
1.1.4 数控系统分类
我国目前使用的数控系统一般可按系统性能分为国产普及型和进口全功能型两类。数控系统的主要应用对象——数控机床是一种加工设备,既快又好地完成加工,是人们对它的最大期望,因此,机床实际能够达到的轮廓加工精度和效率,是衡量其性能水平最重要的技术指标,而数控装置的控制轴数、联动轴数等虽代表了数控装置的插补运算能力,但它们并不代表机床实际能达到的轮廓加工精度和效率。
数控系统所使用的伺服驱动器的结构和性能,是决定机床轮廓加工精度的关键部件,也是判定普及型和全功能型数控系统的依据。
(1)普及型数控系统
国产普及型数控系统的一般组成如图1.1.6所示,它通常由CNC/MDI/LCD集成单元(简称CNC单元)、通用型伺服驱动器、主轴驱动器(一般为变频器)、机床操作面板和I/O设备等硬件组成,数控系统对其配套的驱动器、变频器的厂家和型号无要求。

图1.1.6 普及型数控系统的组成
普及型数控系统的数控装置只能输出指令脉冲,不具备闭环位置控制功能,因此,它只能配套本身具备闭环位置控制功能的通用型交流伺服驱动器,这是它和全功能型数控系统的最大区别。由于伺服电机的位置测量信号不能反馈到数控装置上,故数控装置不能对坐标轴的实际位置、速度进行实时监控和调整,从这一意义上说,对数控装置而言,其位置控制仍然是开环的,只是它的最小转角不受步距角限制,也不存在步进电机的失步现象。
国产普及型数控系统所使用的通用型伺服驱动器是一种利用指令脉冲控制伺服电机位置和速度的通用控制器,它对上级位置控制器(指令脉冲的提供者)同样无要求,因此,也可用于PLC的轴控制。此外,为了进行驱动器的设定与调试,通用型伺服驱动器必须有数据输入/显示的操作面板。
由于普及型数控系统的数控装置不具备闭环速度、位置控制功能,这样的数控装置实际上只是一个具有插补运算功能的指令脉冲发生器,实际坐标轴的运动都需要由各自的驱动器进行独立控制,因此,运动轨迹的精确控制只存在理论上的可能。
大多数国产普及型数控装置无集成PLC,它们只能输出最常用的少量辅助功能(M代码)信号,如主轴正转(M03)、反转(M04)、停止(M05),冷却启动(M08)、停止(M09),刀架正转(TL+)、反转(TL-)等,用户不能通过PLC程序对坐标轴、主轴及刀架进行其他控制。
综上所述,尽管国产普及型数控系统的价格低、可靠性较高,部分产品也开发了多轴插补运算功能,但其位置控制的方式决定了这样的系统不能用于高精度定位和轮廓加工,故不能用于高速高精度数控机床。
(2)全功能型数控系统
全功能型数控系统的一般组成如图1.1.7所示。

图1.1.7 全功能型数控系统的组成
全功能型数控系统的闭环位置控制必须由数控装置实现,闭环速度控制在不同系统上有所不同,早期系统通常由伺服驱动器实现,当前的系统多数由数控装置控制。全功能型数控系统的各组成部件均需要在CNC的统一控制下运行,其功能强大、结构复杂、部件间的联系紧密,伺服驱动器、主轴驱动器、PMC等通常都不能独立使用。
当前的全功能型数控系统一般都采用网络控制技术。在FANUC数控系统上,数控装置与驱动器之间使用光缆连接的高速FANUC串行伺服总线(FANUC serial servo bus,FSSB)网络控制,集成PMC与I/O单元之间采用了I/O-Link现场总线网络控制,数控系统连接简单、扩展性好、可靠性高。
全功能型数控系统的闭环位置控制通过数控装置实现,伺服驱动器与数控装置密不可分,驱动器参数设定、状态监控、调试与优化等均需要通过数控装置的MDI/LCD单元进行,驱动器无操作面板,也不能独立使用。
全功能型数控装置不但能实时监控运动轴的位置、速度及误差等参数,而且所有坐标轴的运动都可作为整体进行统一控制,确保轨迹的准确无误,这是一种真正意义上的闭环轨迹控制系统。在先进的数控系统上,还可通过“插补前加减速”“AI先行控制(advanced preview control)”等前瞻控制功能,进一步提高轮廓加工精度。这也是进口全功能型数控机床的定位精度、轮廓加工精度远远高于国产普及型数控机床的原因所在。
全功能型数控系统的PLC有集成PLC(PMC)和外置PLC两种,前者多用于5轴以下的紧凑型系统,后者多用于大型、复杂系统。
在使用集成PLC的数控系统上,PLC与数控装置通常共用电源和CPU;用户可根据实际控制需要,通过选择所需的I/O单元或I/O模块,构成相对简单的PLC系统,数控装置和I/O单元(模块)间可通过网络总线连接。集成PLC配套的I/O单元(模块)结构紧凑、I/O点多,但模块种类少,I/O连接要求固定,点数有一定的限制,通常也不能选配特殊功能模块;此外,由数控系统生产厂家标准设计的机床操作面板等部件,一般集成PLC总线接口,可直接作为PLC的I/O单元使用,无需另行选配I/O单元。集成PLC的软件功能相对简单、实用,PLC一般设计有专门针对数控机床的回转分度、自动换刀等特殊功能指令。集成PLC的程序编辑、调试与状态监控,可直接通过数控装置的MDI/LCD单元进行。
大型、复杂全功能型数控系统的功能强大、I/O点数众多,因此,通常需要使用外置式大中型PLC。外置PLC具有独立的CPU和电源、I/O模块,其结构与模块化结构的大中型通用PLC相同,因此,在SIEMENS、AB等既生产CNC又生产PLC的公司,通常直接使用带CNC网络总线通信接口的大中型通用PLC,这样的数控系统,可使用通用PLC的全部模块,其规格、种类齐全,如果需要,还可选配模拟量控制、轴控制等特殊功能模块。外置PLC的软件功能强大、指令丰富,PLC程序的设计方法与通用型PLC完全相同,但是其PLC程序的编辑、调试与状态监控,同样可通过数控装置的MDI/LCD单元进行。