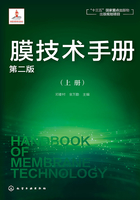
1.4 膜分离过程
1.4.1 常用的膜分离过程
图1-5是各类膜过程的发展现状。按其发展程度和销售状况,已经被广泛应用的膜分离过程有10个。

图1-5 各类膜过程的发展现状
D—渗析;MF—微滤;UF—超滤;RO—反渗透;ED—电渗析;CR—控制释放; GS—气体分离;PV—渗透汽化;BPM—双极膜;ME—膜电解;LM—液膜; MBR—膜生物反应器;MC—膜接触;MD—膜蒸馏;MR—膜反应器; FT—促进传递;CM—催化膜;FO—正渗透;AT—主动传递; AM—亲和膜;MA—膜吸收;MEC—膜能量转换;MEX—膜萃取
1.4.1.1 微孔过滤
微孔过滤(微滤,microfiltration)是膜分离过程中最早产业化的。以天然或人工合成的聚合物制成的微孔过滤膜最早出现于19世纪中叶。1918年Zsigrnondy等首先提出了商品规模生产硝酸纤维素微孔过滤膜的方法,并于1921年获得专利。1925年在德国Gottingen成立了世界上第一个滤膜公司——Sartorius GmDH,专门生产和经销滤膜。1949年美国、英国等国相继生产硝酸纤维素膜,用于水质检验。
微孔过滤膜的孔径一般在0.02~10μm范围内。但是在滤谱上可以看到,在微孔过滤和超滤之间有一段是重叠的,没有绝对的界线。同时,目前各种手册和膜公司刊出的滤谱中各种膜过程的分离范围并非完全相同,而且在不断变化。
微孔过滤膜的主要特征如下:
①孔径均一 微孔过滤膜的孔径十分均匀。例如,平均孔径为0.45μm的膜,其孔径变化仅0.02μm。因此,微孔过滤具有很高的过滤精度。
②孔隙率高 微孔过滤膜的孔隙率一般可高达80%左右。因此,过滤通量大,过滤所需的时间短。
③滤膜薄 大部分微孔过滤膜的厚度在150μm左右,仅为深层过滤介质的1/10,甚至更小。所以,过滤时液体被过滤膜吸附而造成的损失很小。
微孔过滤的截留主要依靠机械筛分作用,吸附截留是次要的。
由醋酸纤维素与硝酸纤维素等混合组成的膜是微孔过滤的标准常用滤膜。此外,已商品化的主要滤膜有再生纤维素膜、聚氯乙烯膜、聚酰胺膜、聚四氟乙烯膜、聚丙烯膜、聚碳酸酯核径迹膜(核孔膜)、陶瓷膜等。
在实际应用中,褶叠型筒式装置和针头过滤器是微孔过滤的两种常用装置。
微孔过滤在工业上主要用于无菌液体的生产、超纯水制造和空气过滤;在实验室中,微孔过滤是检测有形微细杂质的重要工具[7]。
1.4.1.2 超滤
20世纪50年代前后,微孔过滤、高滤(反渗透)和超滤都称为超滤;后来被分为三个区域,即反渗透、超滤和微滤;90年代又被分成四个区域,即反渗透、纳滤、超滤和微滤。自从纳滤出现后,一般认为超滤过程的分子量截留范围大致为1000~1000000,其主要分离对象是蛋白质。
超滤(ultrafiltration)也是一个以压力差为推动力的膜分离过程,其操作压力在0.1~0.5MPa左右。一般认为超滤是一种筛孔分离过程。如图1-6所示,在静压差推动下,原料液中的溶剂和小的溶质粒子从高压的料液侧透过膜到低压侧,所得的液体一般称为滤出液或透过液。而大粒子组分被膜拦住,使它在滤剩液中浓度增大。这种机理不考虑聚合物膜化学性质对膜分离特性的影响。因此,可以用细孔模型来表示超滤的传递过程。但是,有一部分人认为不能这样简单地分析超滤现象。孔结构是重要因素,但不是唯一因素,另一个重要因素是膜表面的化学性质。

图1-6 超滤过程原理示意
超滤过程发展中有两大里程碑,第一个里程碑是在20世纪60年代中期,Loeb和Sourirajan将醋酸纤维素非对称膜热处理后用于反渗透,而未热处理的就是超滤膜。这也是第一代商业超滤装置所用的膜。第二个里程碑是人们认识到超滤技术中边界层效应非常重要,于是在60年代后期,设计出适宜工业用的装置。
超滤膜早期用的是醋酸纤维素膜材料,后来还用了聚砜、聚丙烯腈、聚氯乙烯、聚偏氟乙烯、聚酰胺、聚乙烯醇等高分子膜材料以及无机膜材料。超滤膜多数为非对称膜,也有复合膜。超滤操作简单,能耗低,现已用于超纯水制备、电泳漆回收及其他废水处理、乳制品加工和饮料精制、酶及生物制品的浓缩分离等方面。
1.4.1.3 反渗透
反渗透(reverse osmosis)过程是渗透过程的逆过程,即溶剂从浓溶液通过膜向稀溶液中流动。如图1-7所示,正常的渗透过程按照溶剂的浓度梯度,溶剂从稀溶液流向浓溶液。若在浓溶液侧加上压力,当膜两侧的压力差Δp达到两溶液的渗透压差Δπ时,溶剂的流动就停止,即达到渗透平衡。当压力增加到Δp>Δπ时,溶剂就从浓溶液一侧流向稀溶液一侧,即为反渗透。

图1-7 渗透和反渗透现象示意
1960年Loeb和Sourirajan制成了具有极薄皮层的非对称醋酸纤维素膜,使反渗透过程迅速地从实验室走向工业应用。非对称分离膜的出现,也大大推动了其他膜过程的开发和工业应用。目前应用的反渗透膜可分为非对称膜和复合膜两大类。前者主要以醋酸纤维素和芳香聚酰胺为膜材料;后者支撑体多为聚砜多孔滤膜,超薄皮层的膜材料多通过界面聚合法或原位聚合法制备而成。反渗透膜的膜材料必须是亲水性的。
反渗透过程的推动力为压力差。其分离机理曾引起广泛的争论。无孔机理(溶解-扩散模型)和有孔机理(选择吸附-毛细孔流理论)之争持续了若干年。此外,还有氢键模型及Donnan平衡模型(针对荷电膜)。无论如何,反渗透过程中膜材料与被分离介质之间的化学特性起着第一位的作用,然后才是膜的结构形态。这一点目前已取得共识。
反渗透过程主要用于海水及苦咸水的脱盐、纯水制备以及低分子量水溶性组分的浓缩和回收。
1.4.1.4 纳滤
纳滤(nanofiltration)研究始于20世纪70年代中期,到80年代中期实现了商品化,主要产品有芳香族聚酰胺复合纳滤膜和醋酸纤维素非对称纳滤膜等。在滤谱上它位于反渗透和超滤之间。在前期的研究中,有人将其称为疏松的反渗透膜(loose reverse osmosis membrane),后来由于这类膜的孔径是在纳米范围,所以称为纳滤膜。纳滤特别适用于分离高价离子及分子量为几百的有机化合物。它的操作压力一般不到1MPa,目前已被广泛用于制药工业、食品工业和水的软化等领域。
纳滤膜多数荷电,目前提出的纳滤膜分离机理主要有Donnan平衡模型、细孔模型、固定电荷模型、空间电荷模型及静电位阻模型。
随着医药、石化等领域对有机溶剂体系中提纯、浓缩的需求日益增长,纳滤膜在有机溶剂分离中的应用也越来越引起研究人员的兴趣。
1.4.1.5 渗析
当把一张半透膜置于两种溶液之间时,会出现双方溶液中的大分子原地不动而小分子溶质(包括溶剂)透过膜互相交换的现象,这种现象称为渗析(也称透析,dialysis)。渗析现象是1854年由Graham首先发现的。
渗析过程的原理如图1-8所示。中间以膜(虚线)相隔,A侧通原料液,B侧通溶剂。溶质由A侧根据扩散原理、溶剂(水)由B侧根据渗透原理相对移动。借助于两种溶质扩散速度之差,使溶质之间分离。浓度(化学位)差是渗析过程的推动力。

图1-8 渗析过程原理示意
虽然渗析过程是最早发现和研究的膜分离过程,但由于过程渗透速度慢,选择性又不高,化学性质相似或分子大小相近的溶质体系很难用渗析法分离,除酸碱回收外,工业上很少采用。目前渗析过程主要用于人工肾。
血液透析膜所用的膜材料,1965年以前几乎全是赛璐玢,它很快又被铜纺(cuprophan)膜所取代。目前用于透析膜的膜材料已有聚酰胺、聚碳酸酯、聚砜、聚丙烯酯、聚甲基丙烯酸甲酯、纤维素酯等多种聚合物。
1.4.1.6 电渗析
电渗析(electrodialysis)是20世纪50年代发展起来的膜分离技术。它以电位差为推动力,利用离子交换膜的选择透过性,从溶液中脱除或富集电解质。
电渗析的选择性取决于所用的离子交换膜。离子交换膜以聚合物为基体,接上可电离的活性基团。阴离子交换膜简称阴膜,它的活性基团常为氨基。阳离子交换膜简称阳膜,它的活性基团通常是磺酸根。离子交换膜的选择透过性是指,膜上的固定离子基团吸引膜外溶液中的异电荷离子,使它能在电位差或浓度差的推动下透过膜体,同时排斥同种电荷的离子,阻拦它进入膜内。因此,阳离子能通过阳膜,阴离子能通过阴膜。见图1-9。

图1-9 离子交换膜功能示意
根据膜中活性基团分布的均一程度,离子交换膜大体上可以分为异相膜、均相膜及半均相膜。聚乙烯、聚丙烯、聚氯乙烯等的苯乙烯接枝聚合物是离子交换膜最常用的膜材料。性能最好的是用全氟磺酸、全氟羧酸类膜材料制备的离子交换膜。
电渗析用于水溶液中电解质的去除(即水脱盐)、电解质的浓缩、电解质与非电解质的分离和复分解反应等领域。
1.4.1.7 膜电解
膜电解(membrane electrolysis)是电渗析和电解相结合的一种技术,也称为离子膜电解法、单阳/阴膜法、膜辅助电解法等。利用离子交换膜允许带一种电荷的离子通过而限制相反电荷离子通过的特性,将单元电解槽分隔为阳极室和阴极室,使电解产品分开,该技术具有多功能性、能量利用率高、可控制性、环境兼容性高及经济性等特点。
膜电解所使用的膜材料与电渗析相同,多用全氟磺酸、全氟羧酸类的离子交换膜。20世纪70年代,使用美国杜邦公司开发的化学性质非常稳定的全氟磺酸和全氟羧酸复合膜——阳离子交换膜(Nafion系列),实现了膜电解在氯碱工业的大规模应用。采用离子膜法电解NaCl溶液制取NaOH、Cl2和H2,并以它们为原料生产一系列化工产品。膜电解法制碱技术,具有设备占地面积小、能连续生产、生产能力大、产品质量高、能适应电流波动、污染小等优点,成为目前工业化制碱最先进的工艺方法。2010年,我国山东东岳集团在国家科技项目支持下,研制出全氟离子膜,成功在万吨级氯碱装置上使用,打破了该类膜产品长期依靠进口的被动局面。20世纪80年代中后期,膜电解技术开始应用于环境领域,除了电渗析浓缩淡化的作用外,膜电解可以通过在电解槽内发生一系列电化学过程,达到去除废水中污染物的目的。膜电解技术广泛应用于碱性废水处理、有机酸废水处理、电镀废水处理、冶金废水处理等场合。电解水制氢气是膜电解的另一种重要应用,主要包括碱性水溶液电解法、质子交换膜电解法以及高温电解法。其中质子交换膜电解法制氢的产品纯度高达99.999%,具有能耗低、性能稳定、可以在高电流密度下运行等优点,被认为是未来最具发展前景的电解水制氢技术。
1.4.1.8 膜传感器
膜传感器(membrane sensor)是一种借助薄膜的功能实现信息传送或转换的器件。
目前,用于制备膜传感器的薄膜材料种类繁多,按照材料的种类膜传感器可分为无机膜传感器、有机膜传感器、生物膜传感器以及固体膜传感器和液体膜传感器等。根据功能膜的特征,膜传感器又可分为直接转换型传感器和间接转换型传感器两类。直接转换型传感器在识别物质的同时,膜的物性发生变化,从而直接发出信号;间接转换型传感器在识别物质的同时,膜的物性虽然也发生了变化,但是不能直接发出信号,需要外加信号发生器来发出信号。以电化学生物膜传感器为例,其主要由负载了生物识别材料的电极构成,通过生物材料与待测物质之间的化学反应产生电子的传递形成电信号并被测定,其检测机理如图1-10所示。

图1-10 生物膜传感器的原理示意
酶膜传感器是一类使用范围最广且已有实际应用的电化学生物膜传感器。最早的酶膜传感器是由美国科学家Clark和Lyons于1962年制备而成的,其通过负载葡萄糖氧化酶催化血液中的氧气与葡萄糖反应而产生电信号以实现血糖的检测,随后该技术在辛辛那提儿童医院放大推广。基于酶膜的电催化作用,大量的科学家通过负载不同的生物酶制备出多种针对不同检测对象的酶膜传感器,如乳酸、尿酸、过氧化氢、谷氨酸等传感器已被大量应用于临床医疗及食品工业等领域。
另一类以微生物识别分子单元的传感器称为微生物膜传感器。它以微生物的代谢功能为指标,识别和检测化学物质。微生物膜传感器的性能长期稳定优良,适用于工业过程和环境等的监测。检测乙酸、乙醇、谷酰胺酸、BOD、氨等的传感器已在实际中应用。
此外,还有免疫响应膜传感器、DNA膜传感器等。
人们正在积极进行膜传感器的集成化和智能化的研究,未来的膜传感器会更加灵敏、快速及低成本,同时,通过与网络大数据的联动可以使膜传感器的采集数据家庭化、系统化,实现足不出户便可对空气、水质、身体状况等信息的实时采集。
1.4.1.9 膜法气体分离
文献上最早发表的有关气体膜分离(gas separation)的报道是1831年美国J.V.Mitchell关于气体透过橡胶膜的研究。但是,直到1965年S.A.Stern等为从天然气中分离出氦进行了含氟高分子膜试验和工业装置的设计,以及美国杜邦公司首创了中空纤维膜及其高压分离装置并申请了以聚丙烯腈膜、对苯二酸-乙二醇缩聚膜分离氢、氦的专利之后,膜法气体分离的研究与开发才迅速发展起来。
用膜分离气体,主要是以压力差为推动力,依据原料气中各组分透过膜的速率不同而分离,见图1-11。分离机理视膜的不同而异,主要可分为两类:一类是通过非多孔膜的渗透,另一类是通过多孔膜的流动。实际应用的气体分离膜绝大多数是非对称膜。通常有三种渗透过程在起作用:①溶解的气体通过聚合物致密皮层(非多孔层)的扩散;②通过表皮层下部微孔过渡区的Knudsen扩散;③通过膜底层的Poiseuille流动。总的传递阻力为各层阻力之和。

图1-11 膜法气体分离过程示意
1—原料气;2—膜;3—残留物;4—渗透物
气体分离膜的膜材料主要是有机聚合物,如聚砜、醋酸纤维素、聚酰亚胺、聚4-甲基-1-戊烯、聚二甲基硅氧烷、聚1-(三甲基硅基)丙炔等,也有少量沸石分子筛等无机材料。
1979年美国Monsanto公司研制成功Prism中空纤维膜分离器,使膜法气体分离迅速走向工业应用。目前,膜法气体分离主要用于化肥及石油化工中含氢气体的浓缩和回收、以空气为原料制富氮气体和富氧气体、天然气中氦和CO2的分离和空气除湿等方面。
1.4.1.10 渗透汽化
渗透汽化(渗透蒸发,pervaporation)是指液体混合物在膜两侧组分的蒸气分压差的推动下,依靠各组分在膜中的溶解与扩散速率的不同来实现混合物分离的一种膜分离方法。渗透汽化膜分离过程的定量研究是20世纪50年代开始的。70年代以后,随着能源紧张情况的出现,渗透汽化引起广泛重视。80年代初,第一代渗透汽化膜走向工业化。
渗透汽化与常用的膜分离技术的最大不同点在于在渗透过程中发生由液相到气相的相变化。它的分离机制通常用溶解扩散模型来描述,可分为三步:①被分离的液相物质在膜表面上被选择吸附并溶解;②以扩散形式在膜内渗透;③在膜的另一侧变成气相而脱附。
在渗透汽化过程中,膜的上游侧的压力一般维持常压,而膜的下游侧则有三种方法维持较低的组分蒸气分压:①采用惰性气体吹扫,也称为扫气渗透汽化(sweeping gas pervaporation);②用真空泵获得真空,也称为真空渗透汽化(vacuum pervaporation);③采用冷凝器冷却,也称为热渗透汽化(thermo pervaporation)。实验室一般采用真空渗透汽化(图1-12),工业上大多采用热渗透汽化。

图1-12 渗透汽化过程示意
1—双组分液体进料;2—贫液渗透物;3—渗透蒸气; 4—冷凝器;5—渗透物; 6—真空泵
渗透汽化适用于液体混合物中低含量组分的脱除、恒沸物/近沸物的分离及分离与反应过程的耦合。渗透汽化膜按优先渗透组分可分为有机溶剂脱水膜、水中脱除有机物膜、有机物与有机物分离膜。对于有机溶剂脱水,典型的膜有PVA/PAN复合膜和分子筛膜;对于从水中脱除有机物,典型的膜有PDMS复合膜和有机-无机杂化膜。用于有机物与有机物分离的膜目前尚未实现工业化。
有机溶剂脱水是渗透汽化应用研究最多、技术最成熟的领域。渗透汽化的工业应用主要也集中在这一领域,如乙醇脱水、异丙醇脱水及丙酮脱水等。
1.4.1.11 膜蒸馏
膜蒸馏(membrane distillation)是膜技术与蒸发过程结合的新型膜分离过程。20世纪60年代Findly首先介绍了这种分离技术。1982年Gore报道了采用一种称为Gore-Tex膜的聚四氟乙烯膜进行膜蒸馏和潜热回收的情况,并论述了采用这种技术进行大规模海水淡化的可能性,引起了人们的重视。膜蒸馏原理示意见图1-13。

图1-13 膜蒸馏原理示意
膜蒸馏所用的聚合物膜必须是疏水性的微孔膜,常用的有聚偏氟乙烯(PVDF)、聚丙烯(PP)和聚四氟乙烯(PTFE),其中以聚四氟乙烯的疏水性为最好。膜的孔径一般在0.1~0.4μm,孔径过大容易导致液态水的泄漏使得过程崩溃。增大膜的孔隙率是提高膜通量的重要手段,文献报道的孔隙率范围为35%~85%。
膜蒸馏是在常压和低于溶液沸点的温度下进行的。热侧溶液通常在较低的温度(例如40~50℃)下操作,因而常常可以使用低温热源或废热。与反渗透相比,膜蒸馏设备要求低,过程中溶液浓度变化的影响小;与常规蒸馏相比,膜蒸馏具有较高的蒸馏效率,蒸馏液更为纯净。膜蒸馏是一个有相变的膜过程,它主要用于海水淡化和水溶液的浓缩[8]。目前已有10~100t/d的膜蒸馏海水淡化的商品装置。提高热能利用率是目前改进膜蒸馏的主攻方向。
1.4.1.12 正渗透
正渗透(forward osmosis)是一种利用膜两侧溶液的渗透压差为驱动力,驱使水分子从高化学势一侧向低化学势一侧自发迁移的膜过程。正渗透的分离原理如图1-14所示,膜两侧分别为待处理液和汲取液,待处理液中的水分子在渗透压差的驱动下通过半透膜进入汲取液,获得浓缩的待处理液和稀释的汲取液,最后将溶质从稀释的汲取液中分离出来,得到最终产水。

图1-14 正渗透原理示意
正渗透膜主要包括醋酸纤维素类膜和聚酰胺薄膜复合膜两大类,分别采用相转化法和界面聚合法制备,此外还有层层组装复合膜、双皮层膜、仿生膜等新型的正渗透膜。理想的正渗透膜材料应具备的基本特征包括:拥有对溶质有高截留率的致密皮层;较好的亲水性,水通量高且耐污染;支撑层尽量薄;机械强度高;耐酸、碱、盐等腐蚀的能力。
正渗透操作过程无需提供外压或者只存在很低的液压,相比于其他压力驱动膜过程,有着能耗较低、产水率高、污染低的优点,适用于多种类型原料液的处理,目前已被广泛应用于各个领域,包括污水处理与淡水净化、海水淡化、食品、医药、压力阻尼渗透发电等。正渗透技术早在20世纪60年代就被提出应用于海水淡化,但由于正渗透膜性能的限制,直到2008年才于地中海直布罗陀投产全球第一套海水淡化装置。正渗透技术的低污染优势,使其广泛应用于垃圾渗滤液、废水浓缩、冷却塔补给水等高污染水体的处理和零排放过程。
1.4.2 发展中的新膜过程
1.4.2.1 膜萃取
20世纪80年代初,一个将膜过程和液-液萃取过程结合的膜萃取(membrane extraction)过程开始出现。在膜萃取过程中,两非互溶相由多孔膜隔开,通过膜孔接触,两相中的一相能够润湿膜孔而另一相则不能润湿膜孔。两不互溶溶剂之间的传质发生在微孔膜孔口的液/液界面处,该孔口侧不被接触的溶液所润湿,从而防止了扩散进入另一相。微滤膜或超滤膜通常被用于膜萃取过程,为两个不互溶相提供接触界面。在此过程中,膜不发挥选择性,而只是起到为两相提供界面的作用[9]。溶剂能够通过反萃取剂再次萃取溶质而获得再生,图1-15所示为膜萃取和反萃取过程示意图。

图1-15 膜萃取和反萃取过程
1~3—泵;4~10—压力表;11~13—流量计
膜萃取的传递过程是在把料液相和萃取相分开的微孔膜表面上进行的。因此,它不存在通常萃取过程中液滴的分散与聚集问题。膜萃取的优点如下:①没有液体的分散和聚集过程,可减少萃取剂的夹带损失;②不形成直接接触的液-液两相流动,可使选择萃取剂的范围大大拓宽;③两相在膜两侧分别流动,使过程免受“反混”的影响和“液泛”条件的限制;④与支撑液膜相比,萃取相的存在,可避免膜内溶液的流失。
膜萃取通常由载体辅助进行,载体在第一个膜组件中的界面处与溶质反应,并在另一个膜组件中的界面处释放。在载体介导的膜萃取过程中,萃取反应动力学起到很重要的作用,因此需要特别关注。溶质分配系数的浓度依赖性是另一个需要考虑的参数,它影响浓度梯度,并可能导致整体传质系数随浓度发生变化。文献中已建立了一些数学模型,如早期的静态传质系数、可变分布系数,而后期的模型则考虑了萃取与反萃取界面的形成与脱离反应动力学、基于反应动力学的阻力分析,这种反应动力学与依赖于溶质与载体浓度的总阻力有关,它的范围可能在30%~80%之间。
1.4.2.2 膜结晶
膜结晶(membrane crystallization)操作旨在促进过饱和溶液形成晶体,结合了膜过程中的传质、传热原理。晶体在聚合物膜表面发生异相成核,过饱和度S是溶液中结晶的推动力,定义为实际溶质浓度c与平衡浓度c*(饱和浓度)之比:
(1-1)
通过膜选择性地去除溶剂,能够增加溶质的浓度,直至所需的过饱和度[10]。或者,膜用于选择性地供给反溶剂以引起过饱和,从而产生分相。
传质机理取决于膜的具体类型:对于微孔疏水膜(在一定温度或浓度梯度下在气相中传质),采用粉尘气体模型(dusty gas model);对于薄膜复合膜(在一定压力或浓度梯度下在液相中传质),采用溶解-扩散模型(solution-diffusion model)。
膜的形貌和物理化学参数,如孔隙率、粗糙度或亲水/疏水性显著影响结晶动力学。事实上,临界晶核(一半概率生长,一半概率溶解)的形成是一个活化过程,此过程需要克服吉布斯能垒ΔG*。对于溶液主体中的均相成核,可以用以下公式计算:
(1-2)
式中,γL是晶核-溶液界面的表面张力;Ω是溶质的摩尔体积;Δμ是结晶相与母液之间的化学势梯度。相应的临界晶核R*由下式计算:
(1-3)
膜表面能够降低结晶过程所需的活化能,从而起到促进结晶的作用,使过饱和状态下原本不能自发成核的分子发生聚集,晶核产生速率增加。
为了定量评估这种效应,需要表示晶核-溶液(γL)、晶核-膜(γi)和溶液-膜(γS)界面之间的力学平衡本构关系。对于理想的硬质光滑表面,可以用杨氏方程表示:
(1-4)
上面结晶相能量平衡式的引入能够用来估算平板膜成核时ΔG*的减小。
这种情况下以及多孔或粗糙膜,ΔGheterogeneous/ΔGhomogeneous的数值见表1-7。
表1-7 膜的物理化学参数对多相(heterogeneous)结晶与均相(homogeneous)结晶临界晶核(R*)及吉布斯自由能比值(ΔGheterogeneous/ΔGhomogeneous)的影响

如图1-16所示,相比于在母液中成核(θ=180°),在接触角θ<180°的聚合物膜表面形成临界晶核难度更高,这种现象被称为多相成核。

图1-16 三种不同接触角(θ=90 °、110 °、180 °)条件下,吉布斯自由能与晶核半径之间的关系
(吉布斯自由能在临界半径R*时达到最大值。
参数:c/c*=1.5;Ω=1.9×10-28m3/mol;γL=0.004J/m2)
膜的形貌和物理化学性质影响成核速率,能够改变稳态或亚稳态构象的形成。尽管晶体具有相同的化学组成,但不同构象晶体的溶解度、溶解速率、稳定性、熔点、密度及其他性质差异很大,从而显著影响药用活性成分的效力、生物利用度和安全性。通过膜结晶调控晶型已经得到了验证:甘氨酸(α相和γ相)、乙酰氨基酚(Ⅰ型和Ⅱ型)、L-谷氨酸(α相和β相)和L-组氨酸(α相和β相)。
诱导时间是研究成核动力学的一个重要参数,定义为:从达到过饱和状态开始直至形成临界晶核的时间。一般来说,高成核率(低ΔG*)有利于缩短诱导时间,这在蛋白质结晶过程中特别明显。
1.4.2.3 促进传递
如图1-17所示,促进传递(facilitated transport)是在膜中进行的一种抽提(萃取)[2]。

图1-17 氧气促进传递原理示意
促进传递膜与固态膜分离过程的对比列于表1-8。促进传递有以下特点:①它具有极高的选择性;②通量大;③极易中毒。
表1-8 促进传递膜与固态膜性能的比较

促进传递的研究是从活性生物膜开始的。后来促进传递被用于酸气处理、金属离子回收和药剂纯化等方面,但是直至1975年,都未能在工业上应用。1980年以来,在促进传递上的主要研究工作集中在改进膜的稳定性。
表1-9列出了促进传递过程可能的应用领域。在金属离子分离中最有希望的是铜的分离,在气体分离中是从空气中分离氧和氮。
表1-9 促进传递过程的应用

①以10分为满分,用数字对促进传递膜在不同应用领域的重要性进行评价。
1.4.2.4 膜反应过程
膜反应过程是将反应与膜分离两个具有不同功能的单独过程相耦合,旨在利用膜的特殊功能,实现物质的原位分离、反应物的控制输入、相间传递的强化等,达到提高反应转化率、改善反应选择性、提升反应收率、延长催化剂使用寿命、简化工艺流程和减少设备投资等目的。
膜反应过程最初被用于一些特定反应中,通过连续萃取出产物而打破反应平衡,以提高产品选择性和/或收率,如生物反应过程中连续地移除代谢产物,保持较高的反应收率;脱氢反应过程中不断地移除氢气,促进反应向目标产品方向进行;酯化反应过程中连续地分离出水,提高产品转化率和产物的收率。膜反应过程在其他反应中也展现出优势,如加氢反应、部分氧化反应或全部氧化反应。随着研究的展开以及膜材料的发展,膜反应过程的研究范围逐渐扩大,不再局限于打破反应的平衡限制,而是利用膜的选择渗透性,将产物从反应区域中分离出来,目的是保持催化剂活性的同时抑制副反应,边分离边反应,使得反应可以连续稳定地运行。也可用作某种反应物的分配器,用于串联或平行反应中,控制反应物的输入方式和进料浓度。在某些催化反应中,甚至不需要膜具有渗透选择性,膜仅仅是在膜两侧流动的反应物之间起到控制反应界面的作用[11]。
膜反应过程是通过膜反应器来实现的。膜反应器根据膜材料不同,可分为无机膜反应器和有机膜反应器;根据膜材料的结构,可分为致密膜反应器和多孔膜反应器;根据膜的催化性能,可分为催化膜反应器和惰性膜反应器;根据膜的渗透性能,可分为选择渗透性膜反应器和非选择渗透性膜反应器等;根据催化剂的装填方式,可分为固定床膜反应器、流化床膜反应器和悬浮床膜反应器等。
膜反应过程主要应用于生物反应和催化反应领域。在条件较为温和的生物反应领域,膜反应过程首先是在研究开发相对成熟的有机膜领域得到了发展,如在活性污泥法基础上发展出来的膜生物反应器,将膜过程与活性污泥的生物反应耦合成一个生物化学反应分离系统,取代普通生物反应器的二次沉淀池,具有固液分离效率高、选择性高、出水水质好、操作条件温和、无相变、适用范围广、装置简单、操作方便等突出优点,在废水处理领域具有广阔的应用前景。将酶促反应与膜分离过程相耦合构成酶膜反应器,依靠酶的专一性、催化性及膜特有的功能,集生物反应与反应产物的原位分离、浓缩和酶的回收利用于一体,能够有效消除产物抑制、减少副产物的生成、提高产品收率,广泛应用于有机相酶催化、手性拆分与手性合成、反胶团中的酶催化、辅酶或辅助因子的再生、生物大分子的分解等方面。
无机膜材料的发展为膜反应过程在催化领域苛刻条件下的应用开辟了途径。如以金属及其合金以及固体氧化物所制备的致密膜构建的致密膜反应器,利用致密膜对氢(如钯及其合金膜)或氧(如混合导体透氧膜)极高的选择性,提供反应所需的高纯氢气/氧气或移出反应生成的氢气/氧气,继而提高反应效率;以陶瓷膜为元件构建的多孔膜反应器,利用膜的选择性分离与渗透功能,实现产物或超细催化剂的原位分离,应用于加氢或氧化等石油化工生产过程中,使间歇反应过程转变成连续反应过程,缩短了化工生产流程,提高了产品收率。
膜反应过程的研究、开发与应用已取得显著成效。随着各种问题的解决和膜性能的提高,膜反应过程的应用前景十分广阔。
1.4.3 膜分离与其他化工分离和反应过程的结合
为实施某一具体对象的分离,将膜分离与其他分离和反应单元操作结合起来,发挥各自的优点,往往能获得很好的分离效果,取得良好的经济效益。这是近年来膜分离技术发展的一个新动向。
①膜分离与蒸发操作相结合 以2% CuSO4水溶液的浓缩为例,若想将浓度提高到80%,经济的方法是先用反渗透从2%提高到20%,再经蒸发浓缩达到80%。实践表明,膜分离与蒸发操作结合的能耗仅为单纯蒸发的1/10。
②膜分离与吸附操作相结合 以美国Permea公司设计的一种飞机上用的分离器为例,先用膜法把空气中的氧含量从21%浓缩到40%~45%,再用吸附法进一步分离氧气和氮气。这种方法较之单用吸附法效率提高了三倍,设备尺寸也小得多。氮气可用作油箱的保护气,氧气用于机上人员的呼吸。
③膜分离与冷冻操作相结合 例如,Cryotronics公司用膜分离法先把空气中的氮气提浓到99%,再用氦冷冻系统把气态氮液化成液氮。又如,Air Products和Chemicals公司用膜法及冷冻法串联和并联相结合的流程分离氢气/甲烷混合气中的空气,结果比任何一种单独的方法都好,冷凝温度由-158℃升高至-134℃,能耗与成本均降低。
④膜分离与离子交换树脂法相结合 Ionics公司在美国南部地区的一个发电厂,为革新工艺,在原有的澄清/过滤与离子交换树脂装置之间加了一个电渗析装置,用以除去水中大部分的离子,结果大大延长了离子交换装置的运转周期,再生频率下降至原来的1/5~1/10,化学品消耗、废料排出量及操作人员都有所减少,并提高了生产能力。
⑤膜分离与催化反应相结合 例如Cryotronics公司所生产氮气的纯度为99.9995%。其制备方法是:用燃料气在空气中燃烧后,除用公司提供的用于海洋石油平台的高纯氮装置去除氧气和二氧化碳得到氮气外,再用膜分离把氮气提浓到99.59%,加入适量的氢气,经过金属钯催化剂除去残氧。氮中的氧含量可降至5μL/L以下。