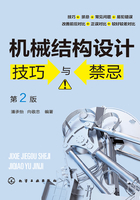
2.2 滚动轴承结构设计技巧与禁忌
常用的滚动轴承绝大多数已经标准化,其结构类型和尺寸均是标准的,因此滚动轴承设计时,除了正确选择轴承类型和确定型号尺寸外,还需合理设计轴承的组合结构,要考虑轴承的配置和装卸、轴承的定位和固定、轴承与相关零件的配合、轴承的润滑与密封和提高轴承系统的刚度等。正确的类型选择和尺寸的确定以及合理的支承结构设计,都将对轴承的受力、运转精度、提高轴承寿命和可靠性、保证轴系性能等起着重要的作用。下面就这些方面应注意的问题加以分析。
2.2.1 滚动轴承的主要结构类型及选用原则
(1)滚动轴承的主要结构类型及特性
滚动轴承的结构类型很多,常用滚动轴承的类型及特性见表2⁃3。
表2⁃3 常用滚动轴承的类型及特性


注:基本额定动载荷比、极限转速比是指同一尺寸系列轴承与深沟球轴承之比(平均值)。
(2)滚动轴承结构选用原则
选用滚动轴承结构时,必须了解轴承的工作载荷(大小、方向、性质)、转速及其它使用要求,正确选择轴承结构应考虑以下主要因素。
① 轴承载荷
轴承所受载荷的大小、方向和性质是选择轴承结构的主要依据。以下选用原则可供考虑。
a.相同外形尺寸下,滚子轴承一般较球轴承承载能力大,应优先考虑。
b.轴承承受纯的径向载荷,一般可选用向心类轴承。
c.轴承承受纯的轴向载荷,一般可选用推力类轴承。
d.承受径向载荷的同时,还有不大的轴向载荷时,可选用深沟球轴承、接触角不大的角接触球轴承或圆锥滚子轴承。
e.承受轴向力较径向力大时,可选用接触角较大的角接触球轴承或圆锥滚子轴承,或者选用向心轴承和推力轴承组合在一起的结构,以分别承担径向载荷和轴向载荷。
f.载荷有冲击振动时,优先考虑滚子轴承。
② 轴承的转速
a.球轴承与滚子轴承相比,有较高的极限转速,故在高速时应优先选用球轴承。
b.高速时,宜选用同一直径系列中外径较小的轴承,外径较大的轴承,宜用于低速重载的场合。
c.实体保持架较冲压保持架允许高一些的转速,青铜实体保持架允许更高的转速。
d.推力轴承的极限转速均很低。当工作转速高时,若轴向载荷不十分大,可考虑采用角接触球轴承承受纯轴向力。
e.若工作转速超过样本中规定的极限转速,可考虑提高轴承公差等级,或适当加大轴承的径向游隙等措施。
③ 轴承的刚性与调心性能
a.滚子轴承的刚性比球轴承高,故对轴承刚性要求高的场合宜优先选用滚子轴承。
b.支点跨距大、轴的弯曲变形大或多支点轴,宜选用调心型轴承。
c.圆柱滚子轴承用于刚性大,且能严格保证同轴度的场合,一般只用来承受径向载荷。当需要承受一定轴向载荷时,可选择内、外圈都有挡边的类型。
④ 轴承的安装和拆卸
a.在轴承座不剖分而且必须沿轴向安装和拆卸轴承时,应优先选用内、外圈可分离的轴承,如圆锥滚子轴承、圆柱滚子轴承等。
b.在光轴上安装轴承时,为便于定位和拆卸,可选用内圈孔为圆锥孔(用以安装在锥形的紧定套上)的轴承。
⑤ 经济性
a.与滚子轴承相比,球轴承因制造容易,价格较低,条件相同时可考虑优先选用。
b.同型号尺寸公差等级为P0、P6、P5、P4、P2的滚动轴承价格比为1∶1.8∶2.3∶7∶10。在满足使用要求情况下,应优先选用0级(普通级)公差轴承。
2.2.2 滚动轴承类型的选择
(1)滚动轴承类型选择应考虑受力合理
滚动轴承由于结构的不同,各类轴承的承载性能也不同,选择类型时,必须根据载荷情况和轴承自身的承载特点,使轴承在工作中受力合理,否则将严重影响轴承以及整个轴系的工作性能,乃至影响整机的正常工作。下面仅就一些选型受力不合理情况进行分析。
① 一对圆锥滚子轴承不能承受较大的轴向载荷和径向载荷 轴同时受到较大的轴向载荷和径向载荷时,不能采用只有两个圆锥滚子轴承的结构,如图2⁃45(a)所示。因为在大轴向载荷作用下,圆锥滚子、滚道发生弹性变形,使得轴的轴向窜动量超过预定值,径向间隙增大,因此在径向载荷作用下,发生冲击振动,轴承将很快损坏。

图2⁃45 承受较大轴向力和径向力的支承
可考虑改为图2⁃45(b)所示形式,在左端改用轴向可以滑动的圆柱滚子轴承,这样,左端的圆柱滚子轴承即使在右端承受较大轴向载荷时产生微小轴向位移,也不会引起左端的径向间隙,从而避免了因径向力作用而造成的振动和轴承损坏。
② 轴承组合要有利于载荷均匀分担 采用两种不同类型的轴承组合来承受大的载荷时要注意受力是否均匀,否则不宜使用。例如,图2⁃46(a)所示铣床主轴前支承采用深沟球轴承和圆锥滚子轴承的组合,这种结构是很不合适的,因为圆锥滚子轴承在装配时必须调整,以得到较小的间隙,而深沟球轴承的间隙是不可调整的,因此有可能由于径向间隙大而没有受到径向载荷的作用,两轴承受载很不均匀。合理设计可将两个圆锥滚子轴承组合为一个支承,而另一支承可采用深沟球轴承或圆柱滚子轴承,如图2⁃46(b)所示。

图2⁃46 铣床主轴轴系支承
③ 避免轴承承受附加载荷
a.角接触轴承不宜与非调整间隙轴承成对组合 如果角接触球轴承或圆锥滚子轴承与深沟球轴承等非调整间隙轴承成对使用[图2⁃47(a)、(c)],则在调整轴向间隙时会迫使球轴承也形成角接触状态,使球轴承增加较大的附加轴向载荷而降低轴承寿命。成对使用的角接触轴承[图2⁃47(b)、(d)]的应用是为了通过调整轴承内部的轴向和径向间隙,以获得最好的支承刚性和旋转精度。

图2⁃47 角接触轴承不宜与非调整间隙轴承组合
b.滚动轴承不宜和滑动轴承联合使用 一根轴上既采用滚动轴承又采用滑动轴承的联合结构[图2⁃48(a)、(c)]不宜使用,因为滑动轴承的径向间隙和磨损均比滚动轴承大许多,因而会导致滚动轴承歪斜,承受过大的附加载荷,而滑动轴承却负载不足。图2⁃48(a)可改成图2⁃48(b)所示结构。如因结构需要不得不采用滚动轴承与滑动轴承联合的结构,则滑动轴承应设计得尽可能距滚动轴承远一些,直径尽可能小一些,或采用具有调心性能的滚动轴承[图2⁃48(d)]。

图2⁃48 滚动轴承不宜和滑动轴承联合使用
④ 推力球轴承不能承受径向载荷 推力球轴承只能承受轴向载荷,工作中存在径向载荷时不宜使用。例如图2⁃49的铸锭堆垛装置升降台支承轴承,选用推力球轴承就属于这种不合理情况,现分析如下。铸锭机堆垛装置的升降台是将铸锭机排出的金属锭进行自动码垛的配套机构,码垛操作要求升降台每升降一次,必须同时顺时针或逆时针方向转过90°。

图2⁃49 铸锭机堆垛装置升降台支承轴承设计错误
升降台为立式圆筒形,通过推力球轴承支承在柱塞式液压缸的顶部,台面装有辊道以承接排列好的金属锭(每层五锭,共码四层),堆完一垛金属锭后,由另设的液压缸推入辊道输送机。升降台利用柱塞式液压缸控制其上升或下降,利用水平液压缸、齿条、齿圈传动来控制正、反转(90°),按照规定的程序操作以达到预期的运行目标。
本例中,在液压缸的顶部采用推力球轴承,受力不合理,因为推力球轴承只能承受轴向力,不能承受径向力,而此装置在工作过程中却有径向力存在。径向力产生的原因有二,一是渐开线齿形工作时存在径向力;二是当沿辊道滚动方向推出升降台上的锭垛时,也有水平方向力作用于升降台上。另外,轴承座孔尺寸过大,与轴承之间有1mm的间隙,在径向力作用下,升降台工作时产生水平偏移,影响齿条同齿轮的正常啮合,严重时有可能将轴承从轴承座推出,若将推力球轴承改为推力角接触球轴承,并在它下面加一个深沟球轴承(为更可靠),同时将轴承座与轴承外圈的配合改为过渡配合,这样推力角接触轴承可以承受以轴向载荷为主的径向、轴向联合载荷,从而解决了升降台工作时的水平移动问题,也改善了齿条、齿轮的啮合状态。

图2⁃50 两调心轴承组合时调心中心应重合
R—径向轴承半径;R1—推力轴承半径
⑤ 两调心轴承组合时调心中心应重合 调心球轴承与推力调心滚子轴承组合时,两轴承调心中心要重合。如图2⁃50(a)所示为某磁选机转环体通过主轴支承在上、下两个轴承箱的轴承上,上轴承为调心球轴承,下轴承为推力调心滚子轴承。这种组合支承两轴承的调心中心必须重合,如若不然将使两轴承的滚动体和滚道受力情况恶化,致使轴承过早损坏。其原因分析如下。
调心球轴承调心中心为O,推力调心滚子轴承调心中心为O1,设计时两者应同心,即O与O1在一点。若由于设计不周或轴承底座不平以及安装调试等误差,O与O1不重合,如图2⁃50(b)所示,造成偏心,这种偏心将迫使滚动体在滚道内运行轨迹发生变化,中心在O1点时,轨迹为Ⅰ,若因上述偏心等原因使中心移至O2,则轨迹为Ⅱ,滚动体在滚道内运动轨迹的这种变化,使滚动体与滚道受到附加载荷,当轴受力变形后,两调心轴承的运动互相干涉,这种结构原则上很难达到自动调心的目的。所以对此类轴承组合设计时,应特别注意较全面的计算负荷,选用合适的尺寸系列轴承,一般可考虑选用直径系列和宽度系列大些的轴承类型,应注意使O与O1点重合,如图2⁃50(c)所示,同时还要注意安装精度和轴承座底面的加工精度等。也可考虑改用其它类型的支承。
在图2⁃51(a)重载托轮支承中,若采用调心滚子轴承与推力调心滚子轴承,则也属于调心中心不重合,受力不合理情况,可考虑采用圆锥滚子轴承,如图2⁃51(b)所示。

图2⁃51 托轮支承轴承
⑥ 调心轴承不宜用于减速器和齿轮传动机构的支承 在减速箱和其它齿轮传动机构中,不宜采用自动定心轴承[图2⁃52(a)],因调心作用会影响齿轮的正确啮合,使齿轮磨损严重,可采用图2⁃52(b)所示形式,用短圆柱滚子轴承(或其它类型轴承)代替自动调心轴承。

图2⁃52 减速箱、轴系支承
(2)轴系刚性与轴承类型选择禁忌
① 两座孔对中性差或轴挠曲大应选用调心轴承 当两轴承座孔轴线不对中或由于加工、安装误差和轴挠曲变形大等原因,使轴承内、外圈倾斜角较大时,若采用不具有调心性能的滚动轴承,由于其不具调心性,在内、外圈轴线发生相对偏斜状态下工作时,滚动体将楔住而产生附加载荷,从而使轴承寿命降低[图2⁃53(a)、(b)、(c)],所以这种情况下应选用调心轴承[图2⁃53(d)、(e)]。

图2⁃53 座孔不同心或轴挠曲大应选用调心轴承
② 多支点刚性差的光轴应选用有紧定套的调心轴承 多支点的光轴(等径轴),在一般情况下轴比较长,刚性不好,易发生挠曲。如果采用普通深沟球轴承[图2⁃54(a)],不但安装拆卸困难,而且不能自动调心,使轴承受力不均而过早损坏,应采用装在紧定套上的调心轴承[图2⁃54(b)],不但可自动调心,且装卸方便。

图2⁃54 多支点刚性差的光轴宜采用紧定套调心轴承
(3)高转速条件下滚动轴承类型选择禁忌
下列轴承类型(图2⁃55)不适用于高速旋转场合。

图2⁃55 不适用于高速旋转的滚动轴承
① 滚针轴承不适用于高速 滚针轴承[图2⁃55(a)]的滚动体是直径小的长圆柱滚子,相对于轴的转速滚子本身的转速高,这就限制了它的速度能力。无保持架的轴承滚子相互接触,摩擦大,且长而不受约束的滚子具有歪斜的倾向,因而也限制了它的极限转速。一般这类轴承只适用于低速、径向力大而且要求径向结构紧凑的场合。
② 调心滚子轴承不适用于高速 调心滚子轴承[图2⁃55(b)]由于结构复杂,精度不高,滚子和滚道的接触带有角接触性质,使接触区的滑动比圆柱滚子轴承大,所以这类轴承也不适用于高速旋转。
③ 圆锥滚子轴承不适用于高速 圆锥滚子轴承[图2⁃55(c)]由于滚子端面和内圈挡边之间呈滑动接触状态,且在高速运转条件下,因离心力的影响要施加充足的润滑油变得困难,因此这类轴承的极限转速较低,一般只能达到中等水平。
④ 推力球轴承不适用于高速 推力球轴承[图2⁃55(d)]在高速下工作时,因离心力大,钢球与滚道、保持架之间有滑动,摩擦和发热比较严重。因此推力球轴承不适用于高速。
⑤ 推力滚子轴承不适用于高速 推力滚子轴承[图2⁃55(e)]在滚动过程中,滚子内、外尾端会出现滑动,滚子愈长,滑动愈烈。因此,推力滚子轴承也不适用于高速旋转的场合。
为保证滚动轴承正常工作,除正确选择轴承类型和确定型号外,还需合理设计轴承的组合结构。下面各节就轴承组合结构设计的技巧与禁忌进行阐述。
2.2.3 滚动轴承轴系支承固定形式
(1)轴系结构设计应满足静定原则
滚动轴承轴系支承结构设计必须使轴在轴线方向处于静定状态,即轴系在轴线方向既不能有位移(静不定),也不能有阻碍轴系自由伸缩的多余约束(超静定),轴向静定准则是滚动轴承支承结构设计最基本的重要原则。

图2⁃56 轴系支承和静定问题
若轴在轴向约束不够(静不定),则表示轴系定位不确定,这种情况必须避免。如图2⁃56(a)、(b)所示轴系,两个轴承在轴线方向均没有固定,轴系相对机座没有固定位置,在轴向力作用下,就会发生窜动而不能正常工作。所以必须将轴承加以轴向固定以避免静不定问题,但每个轴系上也不能有多余的约束,否则轴系在轴向将无法自由伸缩(超静定),一般由于制造、装配等误差,特别是热变形等因素,将引起附加轴向力,如果轴系不能自由伸缩,将使轴承超载而损坏,严重时甚至卡死,所以轴系支承结构设计也应特别注意防止超静定问题出现。在轴系支承结构中,理想的静定状态不是总能实现的,一定范围内的轴向移动(准静定)或少量的附加轴向力(拟静定)是不可避免的,也是允许的,在工程实际中准静定和拟静定支承方式是常见的,它们基本上可看作是静定状态,重要的是这些少量的轴系轴向移动和附加轴向力的值的范围必须是在工程设计允许之中。如图2⁃56(c)、(d)所示即属这种情况。
按照上述静定设计准则,常见的轴系支承固定方式有三种:两端单向固定;一端双向固定、一端游动;两端游动。前两种应用较多,下面分别进行阐述。
(2)两端单向固定
普通工作温度下的短轴(跨距l≤350mm),支承常采用两端单向固定形式,每个轴承分别承受一个方向的轴向力,为允许轴工作时有少量热膨胀,轴承安装时,应留有0.25~0.4mm的轴向间隙(间隙很小,通常不必画出),间隙量常用垫片或调整螺钉调节。轴向力不太大时可采用一对深沟球轴承,如图2⁃57所示;若轴向力较大时,可选用一对角接触球轴承或一对圆锥滚子轴承,如图2⁃58所示。

图2⁃57 两端固定的深沟球轴承轴系

图2⁃58 两端固定的角接触轴承轴系
在使用圆锥滚子轴承两端固定的场合,一定要保证轴承适当的游隙,才能使轴系有正确的轴向定位。如果仅仅采用轴承盖压紧定位,如图2⁃59所示轴系,轴承盖无调整垫片,则不能调整轴承间隙;压得太紧,造成游隙消失,润滑不良,运转中轴承发热,烧毁轴承,严重时甚至卡死;间隙过大,轴系轴向窜动大,轴向定位不良,产生噪声,影响传动质量。所以使用圆锥滚子轴承两端固定时,一定要设置间隙调整垫片,如图2⁃60(a)所示,也可以采用调整螺钉,如图2⁃60(b)所示。

图2⁃59 圆锥滚子轴承间隙无法调整(不合理)

图2⁃60 圆锥滚子轴承间隙的调整(合理)
(3)一端双向固定,一端游动
对于跨距较大(l>350mm)且工作温度较高的轴系,轴热胀后伸缩量大,宜采用一端双向固定,一端游动的支承结构,这种支承是较理想的静定状态,既能保证轴系无轴向移动,又可避免因制造安装等误差和热变形等因素引起的附加轴向力。常见的一端固定、一端游动的支承结构如图2⁃61、图2⁃62所示。当轴向载荷不大时,固定端可采用深沟球轴承(图2⁃61),轴向载荷较大时,可采用两个角接触轴承“面对面”或“背对背”组合在一起的结构,如图2⁃62所示(右端两轴承“面对面”安装)。

图2⁃61 一端固定、一端游动轴系(一)

图2⁃62 一端固定、一端游动轴系(二)
为保证支承性能,使轴系正常工作,固定端与游动端必须考虑固定可靠、定位准确,这里说明几项值得注意的设计原则。
① 固定端轴承必须能双向受力 在一端固定、一端游动支承形式中,由于游动端轴承在轴向完全自由,即不能承受任何轴向力,所以固定端轴承必须要能承受轴向正反双向力。也就是说,能作为固定端的轴承的一个先决条件是:它必须能承受正反双向轴向力,按此原则,深沟球轴承、内外圈有挡边的圆柱滚子轴承和一对角接触轴承的组合等可用作固定端轴承[图2⁃63(a)],而滚针轴承、内外圈无挡边的圆柱滚子轴承、单只角接触球轴承和单只圆锥滚子轴承等不可用作固定端轴承[图2⁃63(b)]。

图2⁃63 可以作固定端轴承的轴承
图2⁃64所示为一蜗杆⁃蜗轮减速器,蜗杆轴支承采用了一端固定、一端游动的支承方式,图2⁃64(a)采用了单只角接触球轴承作为固定端是错误的,因为角接触球轴承只能承受单方向轴向力,不能满足双向受力要求,轴系工作中轴向固定不可靠。图2⁃64(b)所示采用了一对角接触球轴承,可以承受双向轴向力,轴系工作时轴向固定可靠,所以是正确的。

图2⁃64 蜗杆⁃蜗轮减速器支承形式
② 游动端轴承的定位 在一端固定、一端游动支承形式中,游动端轴承的功能是保证轴在轴向能安全自由伸缩,不允许承担任何轴向力。为此,游动端轴承的轴向定位必须准确,其设计原则是:在满足轴承不承担轴向力的前提下,尽量多加轴向定位。如采用有一圈无挡边的圆柱滚子轴承作游动端,则轴承内外圈四个面都需要轴向定位,图2⁃65(a)所示是错误的,图2⁃65(b)所示是正确的。

图2⁃65 游动端轴承的轴向定位
③ 游动端轴承圈的固定 游动端轴承的轴向“游动”(移动),可由内圈与轴或外圈与壳体间的相对移动来实现,究竟让内圈与轴还是外圈与壳体之间有轴向相对运动,这应取决于内圈或外圈的受力情况,原则上是受变载荷轴承圈周向与轴向全部固定,而仅在一点受静载作用的轴承圈可与其外围有轴向的相对运动。一般情况下,内圈和轴颈同时旋转,受力点在整个圆周上不停地变化,而外圈与壳体一样静止不动,只在一处受静载,比如齿轮轴系、带轮轴系,此时,游动端的轴承应将外圈用于轴向移动,而不应使内圈与轴之间移动。图2⁃66所示为圆盘锯轴系支承结构,图2⁃66(a)中使轴与内圈间相对移动是不合理的,图2⁃66(b)所示使外圈与壳体间轴向移动是合理的。

图2⁃66 圆盘锯轴系游动端轴承圈的固定
(4)两端游动
要求能左右双向游动的轴,可采用两端游动的轴系结构。例如人字齿轮由于在加工中,很难做到齿轮的左右螺旋角绝对相等,为了自动补偿两侧螺旋角的这一制造误差,使人字齿轮在工作中不产生干涉和冲击作用,齿轮受力均匀,应将人字齿轮的高速主动轴的支承做成两端游动,而与其相啮合的低速从动轴系则必须两端固定,以便两轴都得到轴向定位。通常采用圆柱滚子轴承作为两游动端,如图2⁃67(a)所示。图2⁃67(b)采用角接触球轴承则无法实现两端游动,属不合理结构。图2⁃67(a)的具体结构见图2⁃68。

图2⁃67 人字齿轮高速主动轴的两端游动支承

图2⁃68 高速人字齿轮轴的两端游动支承具体结构
2.2.4 滚动轴承的配置
(1)角接触轴承正装与反装的基本原则
一对角接触轴承并列组合为一个支点时,正装时[图2⁃69(a)]两轴承支反力在轴上的作用点距离B1较小,支点的刚性较小;反装时[图2⁃69(b)]两轴承支反力在轴上的作用点距离B2较大,支承有较高的刚性和对轴的弯曲力矩有较高的抵抗能力。如果轴系弯曲较大或轴承对中较差,应选择刚性较小的正装,而反装则多用于有力矩载荷作用的场合。
一对角接触轴承分别处于两个支点时,应根据具体受力情况分析其刚度,当受力零件在两轴承之间时,正装方案刚性好,当受力零件在悬伸端时,反装方案刚性好,两方案的对比见表2⁃4。
表2⁃4 角接触轴承不同安装形式对轴系刚度的影响


图2⁃69 角接触轴承的正装与反装
为说明角接触轴承正装和反装对轴承受力和轴系刚度的影响,现以图2⁃69(c)、(d)的锥齿轮轴系为例进行具体分析。设锥齿轮受圆周力FT=2087N,径向力FR=537N,轴向力FA=537N,两轴承中点距离100mm,锥齿轮距较近轴承中点距离40mm,轴转速1450r/min,载荷有中等冲击,取载荷系数fd=1.6。轴系采用一对30207型轴承,分别正装和反装。由设计手册查得轴承的基本额定动载荷Cr=51500N,尺寸a=16mm(支点距外圈外端面距离),c=15mm(外圈宽)。现按两种安装方案进行计算,其结果列于表2⁃5。由表可知:正装由于跨距l小,悬臂b较大,因而轴承受力大,轴承1所受径向力正装时约为反装时的2.2倍,锥齿轮处的挠度,正装时约为反装时的2.1倍,所以正装时轴承寿命低,轴系刚性差。但正装时轴承间隙可由端盖垫片直接调整,比较方便,而反装时轴承间隙由轴上圆螺母进行调整,操作不便。
表2⁃5 锥齿轮轴系支承方式的刚度、轴承受力与寿命计算对比


(2)游轮、中间轮不宜用一个滚动轴承支承
游轮、中间轮等承载零件,尤其当其为悬臂装置时,如果采用一个滚动轴承支承[图2⁃70(a)],则球轴承内外圈的倾斜会引起零件的歪斜,在弯曲力矩的作用下,会使形成角接触的球体产生很大的附加载荷,使轴承工作条件恶化,并导致过早失效。欲改变这种不良工作状况,应采用两个滚动轴承的支承[图2⁃70(b)]。

图2⁃70 游轮、中间轮的支承
(3)合理配置轴承可提高轴系旋转精度
① 轴承精度对主轴旋转精度影响较大 图2⁃71所示为主轴轴承精度的配置与主轴端部径向振摆的关系。轴系有两个轴承,一个精度较高,假设其径向振摆为零,另一个精度较低,假设其径向振摆为δ,若将高精度轴承作为后轴承,如图2⁃71(a)所示,则主轴端部径向振摆为δ1=(L+a)δ/L,若将精度高的轴承作为前轴承,如图2⁃71(b)所示,则主轴端部径向振摆为δ2=(a/L)δ,显然δ1>δ2,由此可见,前轴承精度对主轴旋转精度影响很大,一般应选前轴承的精度比后轴承高一级。两种方案对比分析见表2⁃6。

图2⁃71 轴承精度配置对主轴精度影响
表2⁃6 轴承精度配置对主轴精度影响对比

② 两个轴承的最大径向振摆应在同一方向 图2⁃72中前后轴承的最大径向振摆为δA和δB,按图2⁃72(a)所示,将两者的最大振摆装在互为180°的位置,主轴端部的径向振摆为δ1,按图2⁃72(b)所示将两者的最大振摆装在同一方向,主轴端部的径向振摆为δ2,则δ1>δ2,可见,图2⁃72(b)结构较为合理。所以同样的两轴承,如能合理配置,可以取得比较好的结果。

图2⁃72 轴承振摆方向配置对主轴精度的影响
③ 传动端滚动轴承的配置 为了保证传动齿轮的正确啮合,在滚动轴承结构为一端固定、一端游动时,不宜将游动支承端靠近齿轮[图2⁃73(a)],而应将游动支承远离传动齿轮[图2⁃73(b)]。

图2⁃73 传动端滚动轴承的配置
又例如,滚动轴承支承为一端固定、一端游动时,若如图2⁃74(a)所示主轴前端靠近游动端,则对轴向定位精度影响很大。所以,固定端轴承应装在靠近主轴前端[图2⁃74(b)],另一端为游动端,热膨胀后轴向右伸长,对轴向定位精度影响小,较为合理。

图2⁃74 固定端应靠近主轴前端
2.2.5 滚动轴承游隙及轴上零件位置的调整
(1)角接触轴承游隙的调整
角接触轴承,例如圆锥滚子轴承、角接触球轴承,间隙不确定,必须在安装或工作时通过调整确定合适的间隙,否则轴承不能正常运行,因此使用这类轴承时,支承结构设计必须保证调隙的可调。例如,一齿轮传动轴系,两端采用一对圆锥滚子轴承的支承结构,其结构如图2⁃75(a)所示,这是一种常用的以轴承内圈定位的结构。这种结构工作时,轴系升温后发热伸长,由于圆锥滚子轴承的间隙不能调整,所以轴承压盖将与轴承外圈压紧,使轴承产生附加轴向力,阻力增大,轴系无法正常工作,严重时甚至卡死。图2⁃75(b)所示结构将轴承内圈定位改为轴承外圈定位,在轴端用圆螺母将轴承内圈压紧,当轴受热伸长时,轴承内圈位置可以自由调整,轴承不会产生附加载荷,轴系可正常工作。

图2⁃75 圆锥滚子轴承间隙的调整
(2)轴上零件位置的调整
某些传动零件,如图2⁃76(a)所示的圆锥齿轮,要求安装时两个节圆锥顶点必须重合;蜗杆传动[图2⁃76(b)]要求蜗杆轴线位于蜗轮中心平面内,才能正确啮合。因此,设计轴承组合时,应当保证轴的位置能进行轴向调整,以达到调整锥齿轮或蜗杆的最佳传动位置的目的。

图2⁃76 轴上零件位置的调整
图2⁃77(a)结构没有轴向调整装置,该图设计中有两个原则错误:一是使用圆锥滚子轴承而无轴承游隙调整装置,游隙过小,轴承易产生附加载荷,损坏轴承,游隙过大,轴向定位差,两种情况均影响轴承使用寿命;二是没有独立的锥齿轮锥顶位置调整装置,在有适当轴承游隙的情况下,应能调整圆锥齿轮锥顶位置,以确保圆锥齿轮的正确啮合。为此,可将确定其轴向位置的轴承装在一个套杯中[图2⁃77(b)],套杯则装在外壳孔中,通过增减套杯端面与外壳间垫片厚度,即可调整锥齿轮或蜗杆的轴向位置。图2⁃77(b)中调整垫片1用来调整轴承游隙,调整垫片2用来调整锥顶位置。

图2⁃77 圆锥齿轮锥顶位置调整装置
2.2.6 滚动轴承的配合
(1)滚动轴承配合制及配合种类的选择
滚动轴承的配合主要是指轴承内孔与轴颈的配合及外圈与机座孔的配合。滚动轴承是标准件,为使轴承便于互换和大量生产,轴承内孔与轴的配合采用基孔制,即以轴承内孔为基准孔,轴承外径与外壳孔的配合采用基轴制,即以轴承的外径为基准轴,在配合中均不必标注。与内圈相配合的轴的公差带,以及与外圈相配合的外壳孔的公差带,均按圆柱公差与配合的国家标准选取,这里值得一提的是滚动轴承内孔的公差带在零线之下,而圆柱公差标准中基准孔的公差带在零线之上,所以轴承内圈与轴的配合比圆柱公差标准中规定的基孔制同类配合要紧得多。图2⁃78表示了与滚动轴承配合的回转轴和机座孔常用公差及其配合情况,从图中可以看出,对于轴承内孔与轴的配合而言,圆柱公差标准中的许多过渡配合在这里实际成为过盈配合,而有的间隙配合,在这里实际变为过渡配合。轴承外圈与外壳孔的配合与圆柱公差标准中规定的基轴制同类配合相比较,配合性质类别基本一致,但由于轴承外径公差值较小,因而配合也较紧。

图2⁃78 滚动轴承的配合
滚动轴承配合种类的选取,应根据轴承的类型和尺寸、载荷的大小和方向以及载荷的性质等来决定。滚动轴承的回转套圈受旋转载荷(径向载荷由套圈滚道各部分承受),应选紧一些的配合;不回转套圈受局部载荷(径向载荷由套圈滚道的局部承受),选间隙配合,可使承载部位在工作中略有变化,对提高寿命有利。常见的配合可参考表2⁃7。一般来说,尺寸大、载荷大、振动大、转速高或温度高等情况下应选紧一些的配合,而经常拆卸或游动套圈则采用较松的配合。
表2⁃7 滚动轴承的配合

依据上述原则,图2⁃75中圆锥滚子轴承内圈与轴颈的配合选用间隙配合显然是不合适的,应选用圆柱公差标准中的过渡配合而实质上是过盈配合的k6(见图2⁃78公差带关系图)。如果只是从表面上选取圆柱公差标准中的过盈配合,如p6、r6等也是不合适的,因为这样会造成轴承内孔与轴颈过紧,过紧的配合是不利的,会因内圈的弹性膨胀使轴承内部的游隙减小,甚至完全消失,从而影响轴承的正常工作。以上几种配合方案对比见表2⁃8。
表2⁃8 回转轴颈与轴承内圈配合选择对比

(2)采用过盈配合避免轴承配合表面蠕动
承受旋转载荷的轴承套圈应选过盈配合,如果承受旋转载荷的内圈与轴选用间隙配合[图2⁃79(a)],那么载荷将迫使内圈绕轴蠕动,原因如下:因为配合处有间隙存在,内圈的周长略比轴颈的周长大一些,因此,内圈的转速将比轴的转速略低一些,这就造成了内圈相对轴缓慢转动,这种现象称为蠕动。

图2⁃79 采用过盈配合避免轴承配合表面蠕动
由于配合表面间缺乏润滑剂,呈干摩擦或边界摩擦状态,当在重载荷作用下发生蠕动现象时,轴和内圈急剧磨损,引起发热,配合表面间还可能引起相对滑动,使温度急剧升高,最后导致烧伤。
避免配合表面间发生蠕动现象的唯一方法是采用过盈配合[图2⁃79(b)]。采用圆螺母将内圈端面压紧或其它轴向紧固方法不能防止蠕动现象,这是因为这些紧固方法并不能消除配合表面的间隙,它们只是用来防止轴承脱落的。
2.2.7 滚动轴承的装拆
(1)滚动轴承的装配
① 滚动轴承安装要定位可靠

图2⁃80 滚动轴承轴向定位结构
滚动轴承的内圈与轴的配合,除根据轴承的工作条件选择正确的尺寸和公差外,还需注意轴承的圆角半径r和轴的圆角半径R的选取。如果轴承圆角半径r小于轴的圆角半径R[图2⁃80(a)],则轴承无法安装到位,定位不可靠。所以,必须使轴承的圆角半径r大于轴的圆角半径R[图2⁃80(b)],以保证轴承的安装精度和工作质量。如果考虑到轴的圆角太小应力集中较大因素的影响和热处理的需要,需加大R,从而难于满足r>R时,可考虑轴上安装间隔环,如图2⁃80(c)所示。另外轴肩的高度也不可太浅[图2⁃80(d)],否则轴承定位不好,影响轴系正常工作。
② 避免外小内大的轴承座孔 如图2⁃81(a)所示的轴承座,由于外侧孔小于内侧孔,需采用剖分式轴承座,结构复杂。若采用图2⁃81(b)所示形式,可不用剖分式,对于低速、轻载小型轴承较为适宜。

图2⁃81 避免外小内大的轴承座孔

图2⁃82 轴承部件应便于分组装配
③ 轴承部件装配时要考虑便于分组装配 在设计轴承装配部件时,要考虑到它们分组装配的可能性。图2⁃82(a)所示结构,由于轴承座孔直径D选得比齿轮外径d小,所以必须在箱体内装配齿轮,然后再装右轴承。又因为带轮轮辐是整体无孔的,需要先装左边端盖然后才能安装带轮。而图2⁃82(b)的结构则比较便于装配,因为轴承座孔D比齿顶外径d大,可以把预先装在一起的轴和轴承作为整体安装上去。并且为了扭紧左边轴承盖的螺钉,在带轮轮辐上开了一些孔,更便于操作。
④ 在轻合金或非金属机座上装配滚动轴承禁忌 不宜在轻合金或非金属箱体的轴承孔上直接安装滚动轴承[图2⁃83(a)],因为箱体材料强度低,轴承在工作过程中容易产生松动,所以应如图2⁃83(b)所示,加钢制衬套与轴承配合,不但增强了轴承处的强度,也增加了轴承处的刚性。
⑤ 避免两轴承同时装入机座孔 一根轴上如果都使用两个内、外圈不可分离的轴承,并且采用整体式机座时,应注意装拆简易、方便。图2⁃84(a)所示因为在安装时两个轴承要同时装入机座孔中,所以很不方便,如果依次装入机座孔[图2⁃84(b)]则比较合理。

图2⁃83 轻合金箱体上的轴承

图2⁃84 避免两轴承同时装入机座孔
⑥ 机座上安装轴承的各孔应力求简化镗孔 对于一根轴上的轴承机座孔需精确加工,并保证同轴度,以避免轴承内、外圈轴线的倾斜角过大而影响轴承寿命。
同一根轴的轴承孔直径最好相同,如果直径不同时[图2⁃85(a)],可采用带衬套的结构[图2⁃85(b)],以便于机座孔一次镗出。机座孔中有止推凸肩时[图2⁃85(c)],不仅增加成本,而且加工精度也低,要尽可能用其它结构代替,例如用带有止推凸肩的套筒。当承受的轴向力不大时,也可用孔用弹性挡圈代替止推凸肩[图2⁃85(d)]。

图2⁃85 机座上安装轴承各孔应简化镗孔
⑦ 轴承座受力方向宜指向支承底面 安装于机座上的轴承座,轴承受力方向应指向与机座连接的接合面,使支承牢固可靠,如果受力方向相反,如图2⁃86(a)所示,则轴承座支承的强度和刚度会大大减弱。合理结构如图2⁃86(b)所示。在不得已用于受力方向相反的场合,要考虑即使万一损坏轴也不会飞出的保护措施。

图2⁃86 轴承座受力方向宜指向支承底面
⑧ 轴承的内、外圈要用面支承 滚动轴承是考虑内、外圈都在面支承状态下使用而制造的,如果是图2⁃87(a)的使用方式,外圈承受弯曲载荷,则外圈有破坏的危险,采用这种使用方式的场合,外圈要装上环箍,使其在不承受弯曲载荷的状态下工作,如图2⁃87(b)所示。

图2⁃87 轴承内、外圈要用面支承
(2)滚动轴承的拆卸
对于装配滚动轴承的孔和轴肩的结构,必须考虑便于滚动轴承的拆卸。
图2⁃88(a)中轴的凸肩太高,不便轴承从轴上拆卸下来。合理的凸肩高度应如图2⁃88(b)所示,约为轴承内圈厚度的2/3~3/4,凸肩过高将不利于轴承的拆卸。为拆卸,也可在轴上铣槽[图2⁃88(c)]。

图2⁃88 轴承凸肩高度应便于轴承拆卸
图2⁃89(a)中ϕA<ϕB,不便于用工具敲击轴承外圈,将整个轴承拆出。而图2⁃89(b)中,因ϕA>ϕB,所以便于拆卸。

图2⁃89 轴承外圈的拆卸
又如图2⁃90(a)所示,圆锥滚子轴承可分离的外圈较难拆卸,而图2⁃90(b)所示结构,外圈则很容易拆卸。

图2⁃90 可分离外圈的拆卸
2.2.8 滚动轴承的润滑与密封
(1)滚动轴承的润滑及其密封
① 滚动轴承的润滑 滚动轴承一般高速时采用油润滑,低速时采用脂润滑,某些特殊环境如高温和真空条件下采用固体润滑。滚动轴承的润滑方式可根据速度因数dn(d为滚动轴承的内径,mm;n为轴承转速,r/min)值选择(表2⁃9)。dn值间接地反映了轴颈的圆周速度。
表2⁃9 滚动轴承润滑方式的选择

② 滚动轴承的密封 滚动轴承的密封按照其原理不同可分为接触式密封和非接触式密封两大类。非接触式密封不受速度的限制。接触式密封只能用于线速度较低的场合,为保证密封的寿命及减少轴的磨损,轴接触部分的硬度应在40HRC以上,表面粗糙度宜小于Ra1.6~0.8μm。
各种密封装置的结构和特点见表2⁃10。
表2⁃10 密封装置


(2)滚动轴承润滑禁忌
① 高速脂润滑的滚子轴承易发热 由于滚子轴承在运转时搅动润滑脂的阻力大,如果高速连续长时间运转,则温度升高,发热大,润滑脂会很快变质恶化而丧失作用。因此滚子轴承(图2⁃91)不适于高速连续运转脂润滑条件下工作,只限于低速或不连续场合。高速时宜选用油润滑。

图2⁃91 不适于高速连续运转脂润滑的滚子轴承
② 避免填入过量的润滑脂 在低速、轻载或间歇工作的场合,在轴承箱和轴承空腔中一次性加入润滑脂后就可以连续工作很长时间,而不需要补充或更换新脂。若装脂过多[图2⁃92(a)],易引起搅拌摩擦发热,使脂变质恶化而丧失润滑作用,影响轴承正常工作。润滑脂填入量一般不超过轴承空间的1/3~1/2[图2⁃92(b)]。
③ 不要形成润滑脂流动尽头 在较高速度和载荷的情况下使用脂润滑,需要有脂的输入和排出通道,以便能定期补充新的润滑脂,并排出旧脂。若轴承箱盖是密封的,则进入这一部分的润滑脂就没有出口,新补充的脂就不能流到这一头,持续滞留的旧脂恶化变质而丧失润滑性质[图2⁃93(a)],所以一定要设置润滑脂的出口。在定期补充润滑脂时,应先打开下部的放油塞,然后从上部打进新的润滑脂[图2⁃93(b)]。

图2⁃92 避免填入过量的润滑脂

图2⁃93 不要形成润滑脂流动尽头
④ 立轴上脂润滑的角接触轴承要防止润滑脂从下部脱离轴承 安装在立轴上的角接触轴承,由于离心力和重力的作用,会发生脂从下部脱离轴承的危险[图2⁃94(a)],对于这种情况,可安装一个与轴承的配合件构成一道窄隙的滞流圈来避免[图2⁃94(b)]。

图2⁃94 要防止润滑脂从下部脱离轴承
⑤ 浸油润滑油面不应高于最下方滚动体的中心 浸油润滑和飞溅润滑一般适用于低、中速的场合。油面过高[图2⁃95(a)]搅油能量损失较大,温度上升,使轴承过热,是不合理的。一般要求浸油润滑时油面不应高于最下方滚动体中心[图2⁃95(b)]。

图2⁃95 浸油润滑油面高度
⑥ 轴承座与轴承盖上的油孔应畅通 如图2⁃96(a)所示,轴承座与轴承盖上的油孔直径比较小,油孔很难对正,因此不能保证油孔的畅通,应采用图2⁃96(b)所示的结构,其轴承盖如图2⁃96(c)所示,这样油便可畅通无阻。轴承盖上一般应开四个油孔,如果轴承盖上没有开油孔,则润滑油无法流入轴承进行润滑。

图2⁃96 轴承座与轴承盖上的油孔
(3)滚动轴承密封禁忌
① 脂润滑轴承要防止稀油飞溅到轴承腔内使润滑脂流失 当轴承需要采用脂润滑,而轴上传动件又采用油润滑时,如果油池中的热油进入轴承中,会造成油脂的稀释而流走,或油脂熔化变质,导致轴承润滑失效。
为防止油进入轴承及润滑脂流出,可在轴承靠油池一侧加挡油盘,挡油盘随轴一起旋转,可将流入的油甩掉,挡油盘外径与轴承孔之间应留有间隙,若不留间隙[图2⁃97(a)],挡油盘旋转时与机座轴承孔将产生摩擦,轴系将不能正常工作。一般挡油盘外径与轴承孔间隙约为0.2~0.6mm[图2⁃97(b)、(c)]。常用的挡油盘结构如图2⁃97(d)所示。

图2⁃97 旋转式挡油盘密封装置
② 毡圈密封处轴颈与密封槽孔间应留有间隙 毡圈密封是通过将矩形截面的毡圈压入轴承盖的梯形槽中,使之产生对轴的压紧作用实现密封的,轴承盖的梯形槽与轴之间应留有一定间隙,若轴与梯形槽内径间无间隙[图2⁃98(a)],则轴旋转时将与轴承盖孔产生摩擦,轴系无法正常工作。正确结构如图2⁃98(b)所示。毡圈油封形式和尺寸如图2⁃98(c)所示。

图2⁃98 毡圈油封
③ 正确使用密封圈密封 密封圈用耐油橡胶或皮革制成,起密封作用的是与轴接触的唇部,有一圈螺旋弹簧把唇部压在轴上,以增加密封效果。使用时要注意密封唇的方向,密封唇应朝向要密封的方向。密封唇朝向箱外是为了防止尘土进入[图2⁃99(a)],密封唇朝向箱内是为了避免箱内的油漏出[图2⁃99(b)]。如防尘采用图2⁃99(b)或防箱内油漏出采用图2⁃99(a)则是错误的。如果既要防止尘土进入,又要防止润滑油漏出,则可采用两个密封圈,但要注意密封圈的安装方向,使唇口相对的结构是错误的[图2⁃99(c)],正确结构应使两密封圈唇口方向相反,如图2⁃99(d)所示。

图2⁃99 密封圈密封唇的方向
④ 避免油封与孔槽相碰 安装油封的孔,尽可能不设径向孔或槽,图2⁃100(a)所示的结构是不合理的,对壁上必须开设径向孔或槽时,应使内壁直径大于油封外径,在装配过程中可避免接触油封外圆面,如图2⁃100(b)所示。

图2⁃100 避免油封与孔槽相碰
⑤ 弯曲的旋转轴不宜采用接触式密封 如果轴系刚性较差,而且外伸端作用着变动的载荷,不宜在弯曲状态旋转的轴上采用接触式密封[图2⁃101(a)],因为由于载荷的变化,接触部分的单边接触程度也发生变化,密封效果较差,同时由于这种单边接触促进接触部分的损坏,起不到油封的作用,所以这种情况宜采用非接触式密封[图2⁃101(b)]。

图2⁃101 弯曲的旋转轴不宜采用接触式密封
⑥ 多尘、高温、大功率输出(入)端密封不宜采用毡圈密封 毡圈密封结构简单、价廉、安装方便,但摩擦较大,尤其不适于在多尘、温度高的条件下使用[图2⁃102(a)],容易漏油,这种条件下可采用图2⁃102(b)所示的结构,增加一有弹簧圈的密封圈,或采用非接触式密封结构形式。

图2⁃102 多尘、高温、大功率端不宜采用毡圈密封