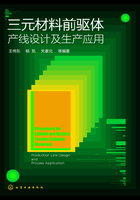
2.3 几种典型的三元前驱体的工业结晶方式
三元前驱体的产品规格较多,按产品中镍钴锰的成分差别可分为镍1~镍9系产品;按产品的平均粒径(D50)大小可分为3μm、4μm、6μm、8μm,10μm、12μm、14μm等多种规格;按粒度分布可分为宽分布、窄分布;按成分分布结构还可分为常规、核壳、梯度等规格。这些规格纵横交错,得到的产品规格多达几十种,如图2-13。
在三元前驱体产品生产之前,通常要根据图2-13确定产品规格,才能决定采用何种结晶操作工艺。产品的组成成分决定了盐溶液的配制比例以及氨水浓度。例如王伟东等[1]对不同组分三元前驱体的适宜氨水浓度作了总结,发现随着镍含量的升高,其采用的氨水浓度越来越高,如图2-14。产品的平均粒径和径距则和晶核生成数目、晶体颗粒的停留时间相关,而这些因素又与结晶操作方式是分不开的。在进行大规模三元前驱体工业生产前,还要从生产线投资、生产效率、控制方式等几方面考虑如何在较低的投资下高效地生产出符合要求的产品。所以三元前驱体的工业结晶操作方式不仅要考虑产品的规格要求,还要考虑生产线投资与产能要求。下面介绍一下行业中几种典型的三元前驱体的工业结晶操作方式及特点。

图2-13 三元前驱体产品结构三维图

图2-14 不同组分的三元前驱体制备适宜的氨水浓度[1]
2.3.1 多级连续溢流法
多级连续溢流法是三元前驱体行业中最早的一种生产方式,它的生产流程是将盐、碱、氨水溶液并流至反应釜内进行结晶反应,当反应釜满后浆料从溢流口流出,如果溢流出的浆料合格,可直接作为合格产品输入储料罐;若不合格,则可通过中转罐流入其他反应釜继续反应。其生产流程如图2-15。
从图2-15可以看出,多级连续溢流法不仅可以单台反应釜连续生产,还可将多台连续反应釜串接在一起进行多级结晶操作[6]。通常由3~6个连续反应釜组成一组独立生产线。这种多级连续结晶操作模式不仅可以增加产能,同时还具备处理生产过程中产生的不合格浆料的缓冲能力。多级连续溢流法生产线设备简单,仅由反应釜、中转罐、储料罐构成,因此它的投资较少。由于采用连续法的结晶操作,操作过程中固含量为稳定状态,因此连续溢流法反应控制简单且生产效率较高,尤其适合于粒度分布较宽的大颗粒三元前驱体的生产。

图2-15 连续溢流法结晶操作流程简图
多级连续溢流法生产过程中反应釜的固含量完全取决于配制的盐、碱溶液浓度,因此固含量较低,通常在100g/L左右。有的厂家为了提高产能,还会给每台反应釜配置一台清母液溢流的装置,如沉降槽。提固后其固含量不超过200g/L,且要保持固含量的稳定,以便于操作过程中稳定控制。
2.3.2 单釜间歇法
单釜间歇法是以单个反应釜为独立系统,每台反应釜配置一台提固器。它的生产流程是将盐、碱、氨水溶液并流至反应釜进行反应,当反应釜液位满后,流入提固器进行浓缩,浓缩后的浓浆返回至反应釜继续反应,母液则排出釜外。当粒径及振实密度合格后一次从釜内卸出,清洗反应釜再重复进行下一批操作。其生产流程如图2-16。
从图2-16可以看出,单釜间歇法生产线的每个反应釜都是独立的,因此可同时生产多种规格的产品。单釜间歇法生产线由反应釜、提固器、储料罐构成。提固器为反应过程的浆料提浓装置,间歇法通常要求固含量达到500~800g/L,因此对提固器的固液分离能力要求较高,否则易造成提固器的堵塞。一台高效提固器的价格比反应釜还高,因此它的生产线投资较大,反应釜的投资一般为连续法的2倍以上。
单釜间歇法采用间歇法的结晶操作,操作过程中固含量逐渐升高,且有限定的结晶停留时间,其结晶控制比连续溢流法复杂。每批产品都要从底水加热开始至产品卸出、反应釜清洗结束。如果提固器堵塞,还需停车维修,导致每批次产品的处理周期较长,而且原料液流量较小,所以它的生产效率低下,其产能通常仅为连续溢流法的50%左右,但它适合生产粒度分布较窄、颗粒大小均匀的产品。

图2-16 单釜间歇法流程简图
虽然单釜间歇法的生产效率低下,但有些特殊的三元前驱体产品如核壳前驱体、梯度前驱体无法采用连续溢流法完成,而必须采用单釜间歇法制备。核壳前驱体是指前驱体颗粒由两层不同组分的前驱体构成,其中靠里一层称为内核,通常为高镍组分,靠外一层称为外壳,通常为低镍组分,两层组分的镍、钴、锰的平均含量为该前驱体的实际组分,如图2-17。梯度前驱体是晶体颗粒从球体中心沿半径方向镍、钴、锰的组分浓度呈梯度变化,通常镍组分浓度从球心沿半径方向浓度逐渐降低,钴或锰组分浓度逐渐增加,整体颗粒的镍、钴、锰的平均组分为该前驱体的实际组分,如图2-18。为了保证制备出的前驱体各镍、钴、锰的组分与设计不发生偏离,需要采用单釜间歇法制备。

图2-17 核壳前驱体[7]
核壳前驱体的制备流程如图2-19,分别配制两种不同浓度的镍、钴、锰混合盐溶液,其中盐溶液1为高镍组分,盐溶液2为低镍组分,盐溶液1与盐溶液2中的各镍、钴、锰的平均含量为该核壳前驱体的实际组分。将盐溶液1、碱溶液、氨水溶液以一定流速流入反应釜,结晶出高镍组分的二次晶体颗粒,在此期间反应釜内液位满后,通过提固器只将母液排出。当盐溶液1反应完后,继续向反应釜内输入盐溶液2结晶,控制成核速率,让低镍组分形成的一次晶体只在原有的高镍二次颗粒表面聚结长大。同样反应釜液位满后,只排出母液。当盐溶液2反应完毕,即得到核壳前驱体。

图2-18 梯度前驱体[8]

图2-19 核壳前驱体制备流程
梯度前驱体的制备流程如图2-20,分别配制两种不同浓度的镍、钴、锰混合盐溶液,其中盐溶液1为高镍组分,盐溶液2为低镍组分,盐溶液 1 与盐溶液 2 中的各镍、钴、锰的平均含量为该梯度前驱体的实际组分。将盐溶液1、碱溶液及氨水溶液以一定流速输入反应釜内结晶,与此同时,将盐溶液 2 以一定流速输入盐溶液 1 内,反应过程中如果反应釜液位满后,通过提固器只将母液排出。随着反应的进行,盐溶液1 中的镍浓度逐渐降低,而钴或锰的浓度逐渐升高,控制反应釜内的成核速率,尽量控制无新的聚结颗粒出现,让新生成的晶体在原有的二次颗粒上聚结长大,当盐溶液 1与盐溶液 2 反应完毕,得到的晶体颗粒为镍、钴、锰的浓度为梯度变化的梯度前驱体。

图2-20 梯度前驱体制备流程
2.3.3 多级串接间歇法
单釜间歇法产能较小,在每批操作时,必须要在有限的时间内达到产品粒度要求,因此较难控制,操作弹性小。多级串接间歇法[6]是将多个间歇反应釜串接起来,当某间歇釜达到规定的固含量限度,釜内浆料仍未达到要求时,可将其一分为二,分至另一反应釜(俗称“分釜”),两个反应釜再继续反应;若还未达到要求可将其再分釜,将其二分为四,只要釜的数量足够,可不断分釜下去。其生产操作流程如图2-21。

图2-21 多级串接间歇法流程简图
从图2-21可以看出,多级串接间歇法的生产线配制几乎和单釜间歇法一样,只是单釜间歇法以单个反应釜为独立系统,而多级串接间歇法以多个间歇反应釜为系统。由于多级串接的间歇法采用的是多级间歇操作,晶体颗粒在整个结晶过程中的停留时间得到很大提升。假设每次分釜后的浆料体积为反应釜有效容积的一半,其停留时间可由式(2-36)表示:

式中,τ为停留时间,h;N为分釜次数;MT为间歇操作最终的固含量,g/L;VR为反应釜的容积,L;Q盐为反应釜内的进盐流速,L/h;a为常数。
从式(2-36)可以看出,每分釜一次,其晶体颗粒在釜内的停留时间均同时增加0.5倍,因此它特别适合于需要停留时间较长且粒度分布较窄的产品的制备。例如需要通过增加停留时间来提高振实密度的小粒度(D50为3~4μm)、窄粒度分布三元前驱体;或者需要通过增加停留时间来增加颗粒粒径的大颗粒(D50为12μm以上)、窄粒度分布前驱体。由于停留时间得到提升,原料液的进液流量可以大大提高,从而增大产能。可见同样的生产设备配置,改变结晶操作方式,可以大规模地提高生产效率。
相比于单釜,多级串接间歇法的分釜操作不仅延长了晶体颗粒的结晶时间,实际上还增加了产线“纠错”能力,对反应过程中产生的不合格产品具备较大处理能力,所以它的控制难度下降很多。由于各反应釜需要连通,每条产线仅能同时做一种规格的产品。
2.3.4 母子釜半连续半间歇法
母子釜半连续半间歇法的独立产线通常由一个母釜和多个子釜构成。母釜通常为连续反应釜,子釜通常为间歇反应釜,母釜连续产生的浆料输至子釜继续反应结晶、长大,直至粒度合格再一次性卸出。其生产流程如图2-22。

图2-22 母子釜半连续半间歇法流程
从图2-22可以看出,母子釜半连续半间歇法生产线是在单釜间歇法的基础上,增加了一台小体积的母反应釜,通常母釜用于制备粒径较小的颗粒,以减小晶体颗粒的停留时间,母釜的体积较小,一般为2~3m3,因此相比于单釜间歇法的投资成本,母子釜法的投资成本只是略微增加。子釜的数量取决于母釜的造浆能力,一般为4~8个。
母子釜法通过母釜的连续反应增加了晶体颗粒的停留时间,因此对后面子釜颗粒停留时间的要求较小,同时减少了子釜的开车时间,较大地提高了生产效率。母子釜法的结晶控制包括母釜的连续法段控制和子釜的间歇法段控制两部分,母釜的连续法段为单变量控制,子釜的间歇法控制也由于母釜分担了一部分结晶停留时间,控制难度下降,因此母子釜法的结晶控制难度也较低。母子釜法虽然有连续反应段,但晶体颗粒在连续段的停留时间较少,所以它生产出的产品具有粒度分布较窄的特点。
从上面介绍的几种结晶操作工艺来看,按母子釜半连续半间歇法工艺布置的产线具有涵盖多种结晶工艺操作的能力。所以三元前驱体生产线按母子釜法工艺设计具有更多规格产品的容纳能力。
表2-3为几种工业结晶操作方式的比较。
表2-3 几种结晶操作方式的比较
