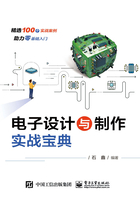
3.4 点阵板及表面贴装元器件手工焊接实践
3.4.1 实例5:点阵板手工焊接实践
点阵板(万能板/通用板)是一种按照标准IC间距(2.54mm)布满焊盘,并可按自己的意愿插装元器件及连线的印制电路板,俗称洞洞板,如图3.121所示。相比专业的PCB制版,点阵板具有使用门槛低、成本低廉、使用方便、扩展灵活等优势,如在学生电子设计竞赛中,通常需要在几天时间内争分夺秒地完成作品,此时就可使用点阵板。
(1)焊接前的准备
在焊接点阵板之前,需要准备足够的细导线用于走线。细导线分为单股和多股,如图3.122所示。单股细导线可弯折成固定形状,剥皮之后还可以当作跳线;多股细导线质地柔软,焊接后显得较为杂乱。

图3.121 点阵板

图3.122 焊接用的细导线
点阵板具有焊盘紧密等特点,要求焊接精度较高,建议使用功率为30W左右的尖头电烙铁。焊锡丝也不能太粗,建议选择线径为0.5~1mm的焊锡丝。
(2)点阵板的焊接方法
对于元器件在点阵板上的布局,可采用顺藤摸瓜的方法,即以核心元器件为中心,其他元器件见缝插针。这种方法是边焊接边规划,无序中体现着有序,效率较高。由于初学者缺乏经验,所以不太适合采用这种方法。初学者可以先在纸上做好初步布局,然后用铅笔画到点阵板正面,进而将走线规划出来,便于焊接。
点阵板的焊接方法一般采用细导线飞线连接,走线尽量水平和竖直,整洁清晰,如图3.123所示。现在流行一种锡接走线法,工艺不错,性能稳定,但比较浪费锡,如图3.124所示。纯粹的锡接走线法难度较大,受到焊锡丝、个人焊接工艺等各方面的影响。如果先拉一根细铜丝,再随着细铜丝拖焊,则简单许多。
(3)点阵板的焊接步骤与技巧
很多初学者焊接时很不稳定,容易短路或断路,其原因为布局不够合理、焊接工艺不良、缺乏技巧等。

图3.123 细导线飞线连接

图3.124 锡接走线法
①初步确定电源线、接地线的布局。
电源线贯穿电路始终,合理布局电源线对简化电路起到十分关键的作用。某些点阵板布置有贯穿整块板子的铜箔,应将其用作电源线和接地线。如果无此类铜箔,也需要对电源线、接地线的布局有一个初步的规划。
②善于利用元器件的引脚。
点阵板的焊接需要大量的跨接、跳线等,不要急于剪断元器件多余的引脚,有时直接跨接到周围待连接的元器件引脚上会事半功倍。另外,本着节约材料的目的,可以把剪断的元器件引脚收集起来作为跳线。
③善于设置跳线。
特别要强调这一点,多设置跳线不仅可以简化连线,而且美观实用,如图3.125所示。
④充分利用敷铜板上的空间。
芯片座里面隐藏元器件,既美观,又能保护元器件,如图3.126所示。

图3.125 善于设置跳线

图3.126 充分利用敷铜板上的空间
⑤善于利用元器件自身的结构。
如图3.127所示的矩阵键盘是一个利用元器件自身结构的典型例子。图中的轻触式按键有4个引脚,两两相通,可以利用这一特点来简化连线,电气相通的两个引脚可充当跳线。
⑥善于利用排针。
排针有许多灵活的用法,比如两块敷铜板相连,就可以用排针和排座,排针既起到了两块敷铜板间的机械连接作用,又起到电气连接的作用。
⑦在需要时割断铜箔。
在使用连孔板时,为了充分利用空间,必要时可用小刀或打磨机割断某处的铜箔,可以在有限的空间放置更多的元器件。

图3.127 善于利用元器件自身的结构
⑧充分利用双面板。
双面板比较昂贵,既然选择,就应该充分利用。双面板的每一个焊盘都可以当作过孔,可灵活实现正、反面电气连接。
图3.128为采用点阵板制作的直流稳压电源板实物图。图3.129为由单片机控制的LED灯柱实物图。

图3.128 采用点阵板制作的直流稳压电源板实物图

图3.129 由单片机控制的LED灯柱实物图
3.4.2 实例6:表面贴装元器件手工焊接实践
越来越多的电路板采用表面贴装元器件(贴片元器件),与传统的封装相比,贴装元器件可以减小电路板的面积,易于大批量加工,布线密度高。贴片电阻和贴片电容的引线电感大大减小,在高频电路中具有很大的优越性。
随着电子系统设计技术的发展,贴片元器件的手工焊接和拆卸是电子爱好者经常接触的操作。但对于贴片元器件,不少人仍感到畏惧,特别是初学者,觉得它不像传统的引线元器件那样易于把握。本节将介绍常见贴片元器件手工焊接需要的工具和基本焊接方法。
1.工具和材料的特殊需要
要高效自如地焊接、拆卸贴片元器件,关键是要有合适的工具和材料。下面是一些最基本的工具和材料。
(1)镊子
焊接贴片元器件一般选用不锈钢尖头镊子,避免其他磁性镊子吸附较轻的贴片元器件。
(2)电烙铁
焊接贴片元器件一般选用尖头电烙铁(尖端的半径在1mm以内),或者使用斜口的扁头电烙铁,有条件的可使用温度可调和带ESD保护的焊台。
(3)热风枪
热风枪一般用来拆卸多脚的贴片元器件,也可以用于焊接。图3.130是吹塑料用的热风枪,其吹出的热风温度可达400~500℃,足以熔化焊锡,经济适用,在很多销售电子元器件的店面都能买到。
(4)焊锡丝
当选用尖头电烙铁时,一般选用细焊锡丝(0.3~0.5mm);当选用斜口扁头电烙铁拖焊时,可选用较粗的焊锡丝。
(5)辅助工具
当IC的相邻两脚被锡短路时,传统的吸锡器派不上用场,可采用专门的编织带(去锡丝)吸,也可使用多股软铜丝吸。
放大镜要有座和带环形灯管的那一种,如图3.131所示,手持式的不行,因为有时需要在放大镜下双手操作。放大镜的放大倍数一般要求5倍以上,最好能达到10倍。

图3.130 吹塑料用的热风枪

图3.131 手工焊接贴片元器件放大镜
还要准备助焊剂、异丙基酒精等。使用助焊剂的目的主要是增加焊锡的流动性,使焊锡可以用电烙铁牵引,并依靠表面张力的作用光滑地包裹在引脚和焊盘上。焊接后,用异丙基酒精清除电路板上的助焊剂。
2.焊接方法
(1)贴片阻容元器件的焊接
贴片阻容元器件的焊接过程如下。
①在一个焊点上点上焊锡,用电烙铁加热焊点,如图3.132所示。
②用镊子夹住元器件,焊上一端后,检查是否放正,如图3.133所示。

图3.132 加热焊点并上锡

图3.133 焊接贴片阻容元器件一端
③若元器件已经放正,则焊接另一端,如图3.134所示。
焊接好的贴片阻容元器件如图3.135所示。

图3.134 焊接贴片阻容元器件另一端

图3.135 焊接好的贴片阻容元器件
(2)PQFP封装贴片IC的焊接
PQFP封装贴片IC的手工焊接过程如下。
①焊接之前,先在IC所有焊盘上涂上助焊剂,用电烙铁处理一遍,以免焊盘镀锡不良或被氧化,造成不好焊,芯片一般不需要处理。一遍助焊剂要涂够,大部分情况下两遍较少,助焊剂比一遍更容易形成堆积。
②在电烙铁容易接触到的焊盘上涂上焊锡,如图3.136所示。

图3.136 在焊盘上涂助焊剂并部分上锡
③用镊子小心地将PQFP芯片放到电路上,注意不要损坏引脚,使其与焊盘对齐,保证芯片的放置方向正确。把电烙铁的温度调到300℃左右,用电烙铁尖沾上少量焊锡,用工具向下按住已对准位置的芯片,焊接两个对角位置上的引脚,使芯片固定不能移动。焊完对角引脚后,重新检查芯片的位置是否对准。若有必要,可进行调整或拆除,并重新在电路板上对准位置。
④在IC引脚上大面积堆满焊锡时,可用电烙铁尖接触每个引脚的末端,直到看见焊锡流入引脚,如图3.137所示。
⑤采用专用的去锡丝带或松香配多股软细铜丝,并用电烙铁加热吸去多余的焊锡,分别如图3.138和图3.139所示。

图3.137 贴片IC引脚上大面积堆满焊锡

图3.138 将软细铜丝置于IC引脚焊锡上用电烙铁加热
⑥用清洗剂或酒精清洗焊接后的电路板,如图3.140所示。

图3.139 去锡后的贴片IC

图3.140 用酒精清洗焊接后的电路板
⑦用高倍显微镜查看焊点,检查有无虚焊、短路、漏焊。
3.4.3 实例7:BGA芯片的手工拆卸植球及焊接实践
1.工具和材料的选用
(1)植锡板
植锡板分为两类:一类是把所有型号都做在一块大的通用连体植锡板上;另一类是每种IC单独一块板。这两种植锡板的使用方式不一样。
连体植锡板的使用方法是将锡浆印到IC上后,就把植锡板扯开,用热风枪吹成球。这种方法的优点是操作简单,成球快;缺点如下。
①锡浆不能太稀。
②对于有些不容易上锡的IC,如软封的FLASH或去胶后的CPU,吹球的时候,锡球会乱滚,极难上锡。
③一次植锡后,不能对锡球的大小及空缺点进行二次处理。
④植锡时,不能连植锡板一起用热风枪吹,否则植锡板会变形隆起,无法植锡。
每个IC单独一块植锡板的使用方法是将IC固定到植锡板下面后,刮好锡浆,连板一起吹,成球冷却后,再将IC取下。其优点是,热风吹时,植锡板基本不变形,一次植锡后,若有缺脚或锡球过大过小现象,可进行二次处理,特别适合新手。本书选用小植锡板进行介绍。
(2)锡膏
建议使用瓶装高品质的BGA芯片专用锡膏,颗粒细腻均匀。
(3)锡膏刮刀
对锡膏刮刀一般没有什么特殊要求,只要能够把锡膏均匀地刮到小植锡板上即可。
(4)热风枪
最好使用有数控恒温功能的热风枪,不同的BGA芯片用不同的热风嘴吹,一般情况下,使用快克850D或以上的热风枪即可。
(5)助焊膏
助焊膏要求对IC和PCB没有腐蚀性,沸点仅稍高于焊锡的熔点,在焊接时,焊锡熔化不久便开始沸腾,吸热气化,可使IC和PCB的温度保持在这个温度。
(6)洗板水
洗板水对松香、助焊膏等有极好的溶解性,酒精对松香、助焊膏的溶解性不强。
2.拆卸
用热风抢折卸BGA芯片如图3.141所示。
3.植球
(1)焊盘的清理
在BGA芯片的引脚上加适量的助焊膏,用电烙铁将残留焊锡去除,用天那水洗净。
(2)固定
焊盘清理干净后,将BGA芯片装入植球台,如图3.142所示。

图3.141 BGA芯片的拆卸

图3.142 将BGA芯片装入植球台
(3)涂抹助焊膏
助焊膏分为有铅和无铅两种。有铅助焊膏不能用于无铅焊接,因为如果是用有铅助焊膏焊接无铅芯片,那么没等锡球达到熔点温度,助焊膏就已经挥发完了。推荐有铅、无铅焊接统一使用优质无铅助焊膏。涂抹助焊膏时,应在BGA芯片的一边或相对的两边(切忌在BGA芯片四边都涂抹助焊膏,如果在BGA芯片四边都涂抹助焊膏,等于密封了,助焊膏流不到BGA芯片中心)涂抹,涂抹的量要适当大一点,如图3.143所示。在加热过程中,助焊膏会向BGA芯片下方流动,并从其他边流出,此时为了方便观察BGA芯片下方的锡球变化,可用棉签擦去流出的助焊膏。如果在加热过程当中发现助焊膏加的量少了,则不能再次涂抹助焊膏,可用镊子夹住小块松香涂抹在BGA芯片边上需要加助焊膏的位置。
(4)准备好锡球
按要求准备好锡球,如图3.144所示。

图3.143 BGA芯片涂抹助焊膏

图3.144 锡球
(5)放置锡球
把涂抹好助焊剂或焊膏的BGA芯片放置在工作台上,助焊剂或焊膏面向上。准备一块与BGA芯片匹配的植锡板,植锡板的开口尺寸应比锡球直径大0.05~0.1mm,把植锡板四周用垫块架高,放置在涂抹好助焊剂或焊膏的BGA芯片上方,使植锡板与BGA芯片之间的距离等于或略小于锡球的直径,在显微镜下对准。将锡球均匀地撒在植锡板上,把多余的锡球用镊子拨(取)下来,使植锡板表面恰好在每个漏孔中保留一个锡球。移开植锡板,检查并补齐锡球,如图3.145所示。

图3.145 BGA芯片放置锡球
(6)用热风枪慢慢加热
最好用BGA拆焊台,一般至少要设置20段以上温度曲线,加热时间为3~5min。预热区、升温区、焊接区、冷却区的升(降)温速率是不一样的,每个区的时间分配也是有讲究的。
①第一升温斜率,温度为75~155℃,速率最大值为3.0℃/s。
②预热温度为155~185℃,时间为50~80s。
③第二升温斜率,温度为185~220℃,速率最大值为3.0℃/s。
④最高温度为225~245℃。
⑤220℃以上时,应保持40~70s。
⑥冷却速率最大不超过6.0℃/s。
完成植球的BGA芯片如图3.146所示。
(7)焊接
装好预热台,对好BGA芯片位置,开始焊接,如图3.147所示,用镊子轻轻移动BGA芯片,感觉焊接效果。焊接完成的BGA芯片如图3.148所示。

图3.146 完成植球的BGA芯片

图3.147 BGA芯片焊接

图3.148 完成焊接的BGA芯片
4.手工焊接注意事项
焊接完成后,首先检查BGA芯片是否焊平,从BGA芯片的四边看,每边都应与主板平行,可以看到锡球没有被拉长、压扁;否则,可能是操作问题或主板变形了引起锡球被拉长、压扁。
如果使用BGA拆焊台,在温度设得合适的情况下制板还起泡,那么应该是板子受潮了,在加热的过程中水蒸气膨胀导致起泡,特别是在一些气候比较潮湿的地区,但主要原因可能是在拆焊BGA芯片时,底部预热不充分,建议在制板之前,将BGA芯片和板一起预热几分钟(2~3min即可)。
BGA焊接的特点是,主板由于尺寸、厚度、材料等关系,与BGA芯片比起来导热性能要差很多,升温速度明显要慢很多,热透所花的时间要长很多,当主板低温时,从芯片方向向下传导的热量,会很快被主板吸收,对于加热锡球起到的作用微乎其微。由此应注意以下两点:
(1)提前预热。芯片毕竟是一个多层结构,而且主板(基板)是PCB材料,导热性能再好,上、下层也会存在温差,骤然间出现一个很大的温差很容易损坏芯片。
(2)根据经验,芯片承受高温的能力很强,但长时间承受高温的能力并不强:
①加热时间尤其是高温区加热时间要尽量缩短;
②一旦发现锡球熔透了,应马上停止加热,进行下一步操作;
③焊接时一定要加助焊膏;
④锡球熔化时,从芯片上面给它一个向下的压力,让锡球和焊点充分接触。