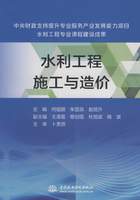
任务一 砂石骨料生产
一、料源规划
水利水电工程砂石料料源有天然砂砾石骨料、人工骨料与工程开挖利用料。部分规模小、部位分散、距离长(如堤防工程、调水工程)的工程亦可结合当地商品砂石料生产情况直接采购成品骨料。
(一)天然料场
按其产地、料层位置可分为陆上料场、河滩料场和河床水下料场等几类。其天然骨料级配往往与工程要求有较大差距,需通过级配加工或外购骨料补充不足级配料来调整,以满足工程需要。采取何种工艺,需结合料场分布位置、开采条件、储量、料源品质等因素综合考虑。天然骨料开采、加工条件一般优于人工料场,应创造条件尽量利用。天然砂砾石料场的开采往往受水文条件影响,其开采与储备必须统筹计划。同时还必须处理好开采对通航、环保及对水资源的影响。
一般覆盖层较厚的陆上料场,杂质含量较高,但开采不受河水的影响。
大部分的天然砂石料场为河滩料场,一般在枯水期出露,在汛期淹没或部分淹没,绝大部分砂石料位于水下。
河床料场实际上就是指常年处于河水面以下的料场,这种料场常与河滩料场连成一片。
(二)人工料场
人工料场是作为人工骨料的原岩料场,也常称为采石场,人工料场具有与施工干扰较少,受自然因素影响小等特点,可常年开采,加工出的成品骨料质量稳定,管理相对集中,有利于均衡生产,级配易于按需调整,减少堆料场地。
(三)工程开挖利用料
水利水电工程施工中,诸如导流隧洞、大坝基础、通航建筑物及电站厂房等主体工程的开挖,常有大量工程弃渣要外运弃置,其中有很大一部分可利用作为人工骨料的原材料。工程弃渣的利用大大降低砂石骨料的成本,能减少工程弃渣处置费用,有利于环保,应优先考虑,综合利用。
工程弃渣的利用应尽量使工程开挖施工进度与弃渣利用时间结合。工程弃渣的利用水平亦与工程管理密切相关。
统筹规划、协调管理是充分利用工程弃渣的关键,一般应遵循以下原则:
(1)应在石方开挖出渣前,规划建设好可利用料堆储场地。
(2)石方开挖工程要选用合适的钻爆参数,以使可利用料的出渣块度适应加工厂粗碎设备的粒径要求。
(3)从施工总进度计划着手,在不影响控制进度的前提下,协调开挖和浇筑进度,以减少利用料堆储量,提高利用率。
(4)尽量创造条件,使利用料直接从开挖现场运至加工系统,减少二次挖运量,降低成本。
(5)避免有用料与无用料混杂,避免降低系统的加工能力。
二、骨料加工
(一)毛料开采
1.砂石料毛料开采量的确定
砂石料毛料开采量是以主体工程混凝土量为计算依据,并考虑工程地质缺陷处理、超挖回填、临建工程、施工损耗等附加混凝土工程量。一般在规划设计时大中型工程可按5%~8%考虑;施工设计时需结合主体工程的坝型设计及坝址地质条件等因素综合分析确定。对水工混凝土而言,砂石料需要量应按各级配混凝土需要量,按比例分别计算。在初步估算时可按每立方米混凝土约需1.5m3砂石净骨料(其中粗骨料约1.067m3,细骨料0.433m3)计算,折合成料场开采量需计入开采、加工、运输,储存等损耗系数。人工料和天然料各种系数有所差别,计算时应分别考虑。
2.河滩、河床天然料场的开采
河床或河滩开采天然砂砾料,一般使用链斗式采砂船开采,配套砂驳作水上运输至岸边,然后用皮带机上岸,最后组织陆路运输至骨料加工厂毛料堆场。
天然料场受施工和自然因素影响较大,在料源规划时,必须充分考虑工程特点、采运设备技术性能、运输线季节性中断及料场的储量与质量间的相互关系。一般坝上游料场在截流或蓄水后往往淹没在水下,开采运输困难,应安排在截流或蓄水前使用,有的料场则因航深及开采设备自身条件限制,只能在丰水或枯水季节使用。
较大的天然砂砾料场,砂石的天然级配在深度和广度上往往有所变化,因此常需分层分区进行开采,一般应遵循以下原则:
(1)分层分区应保证开采和运输线路的连续性。
(2)应将覆盖层薄、料层厚、易开采、运距近、交通方便的料区安排在工程的高峰施工时段(或年度)开采,以便提高生产效率,减少采运设备。
(3)对于陆基水下开采的河滩料场,应尽可能将洪水位(或汛期开采水位)以上的料层或料区留待汛期开采,枯水期则集中开采洪水位以下部位的料层或料区。
(4)河滩和河床料场的分区开采应注意避免汛期冲走有用料层,对某些料场,还可以创造条件,使开采后形成的料坑被洪水挟带的砂砾石重新淤积起来,枯水期重新加以利用。
(5)料区的开采计划应尽可能照顾各个时期的级配平衡。
3.人工料场的开采
一般采用钻爆法松动岩体,然后沿作业面用正铲、反铲或装载机装渣,用自卸汽车、列车、皮带机等运至骨料加工厂毛料堆场。与一般土石方开挖作业不同,料场要求采用钻爆作业控制开采块石的粒径,一般采用微差挤压爆破法,控制爆破后的骨料粒径,尽量降低超过粗碎设备允许进料粒径的超径大块石的含量,同时避免过多石渣的产生。一般颚式和旋回破碎机的允许最大进料粒径为进料口尺寸的80%~85%,准确数据应以生产厂家的技术资料为准。
(二)粗骨料生产
无论以天然河床料场、人工料场、工程开挖利用料为原料的骨料不能直接用于拌制混凝土,需要通过破碎、筛分、冲洗等加工过程,制成符合级配要求、除去杂质的各级粗、细骨料。把骨料破碎、筛分、冲洗、运输和堆放等一系列生产过程集中布置,成为骨料加工厂。当采用天然骨料时,加工的主要作业是筛分和冲洗;当采用人工骨料时,主要作业是破碎、筛分、冲洗和棒磨制砂。
1.破碎
为了将开采的石料破碎到规定的粒径,往往需要经过几次破碎才能完成。因此,通常将骨料破碎过程分为粗碎(将原石料破碎到70~300mm)、中碎(破碎到20~70mm)和细碎(破碎到1~20mm)三种。
骨料用碎石机进行破碎。碎石机的类型有颚式碎石机、锥式碎石机、辊式碎石机和锤式碎石机等。
2.筛分与冲洗
筛分是将天然或人工的混合砂石料,按粒径大小进行分级。冲洗是在筛分过程中清除骨料中夹杂的泥土。骨料筛分作业的方法有机械和人工两种。大中型工程一般采用机械筛分。
在筛分的同时,一般通过筛网上安装的几排带喷水孔的压力水管,不断对骨料进行冲洗,冲洗水压应大于0.2MPa。
在骨料筛分过程中,由于筛孔偏大,筛网磨损、破裂等因素,往往产生超径骨料,即下一级骨料中混入的上一级粒径的骨料。相反,由于筛孔偏小或堵塞、喂料过多、筛网倾角过大等因素,往往产生逊径骨料,即上一级骨料中混入的下一级粒径的骨料。超径和逊径骨料的百分率(按重量计)是筛分作业的质量控制指标。要求超径石不大于5%,逊径石不大于10%。

图3-1 筛分楼分层布置示意图(单位:m)
1—进料皮带机;2—出料皮带机;3—沉砂箱; 4—洗砂机;5—筛分楼;6—溜槽
大中型工程常设置筛分楼,利用楼内安装的2~4套筛、洗机械,专门对骨料进行筛分和冲洗的联合作业,其设备布置和工艺流程如图3-1所示。
进入筛分楼的砂石混合料,首先经过预筛分,剔出粒径大于150mm(或120mm)的超径石。经过预筛分运来的砂石混合料,由皮带机输送至筛分楼,再经过两台筛分机筛分和冲洗,四层筛网(一台筛分机设有两层不同筛孔的筛网)筛出了五种粒径不同的骨料,即特大石、大石、中石、小石、砂子,其中特大石在最上一层筛网上不能过筛,首先被筛分出,砂子、淤泥和冲洗水则通过最下一层筛网进入沉砂箱,砂子落入洗砂机中,经淘洗后可得到清洁的砂。
经过筛分的各级骨料,分别由皮带机运送到净料堆储存,以供混凝土制备的需要。
3.制砂
制砂工艺是砂石加工厂的关键技术,以前多以棒磨机为主要制砂设备。近年来随着冲击式破碎机、旋盘式破碎机、“石打石”立轴式破碎机等新机型的出现,制砂工艺由单一棒磨机制砂方式,发展到多种类型及联合型的制砂方式。在联合式制砂工艺中,棒磨机往往起调整砂细度模数和补充产量的作用。单一方式制砂一般用于中小型或临时工程,联合型则适合大型或特大型工程。如三峡工程,采用了棒磨机、筛分石渣,“石打石”立式冲击破碎机制砂后混合的工艺;二滩工程为棒磨机与旋盘式制砂机联合制砂工艺。
新型破碎机制砂成本均较棒磨机低,设备结构简单,土建工程量少,其共同的工艺特点是破碎机产品中小于5mm颗粒含量高,最大排料粒径在40mm左右,采用检查筛分可分成小于5mm的砂与中、小石。国内大部分工程采用湿法制砂工艺,国外大部分工程采用干法生产,近年我国一些工程也采用干法生产工艺,并取得成功。