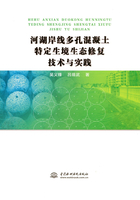
2.2 多孔混凝土制备工艺
2.2.1 拌和工艺
多孔混凝土制备原材料按配合比计算后,获得多孔混凝土材料的材料配合比、质量比、水灰(胶)比等关键参数。当在现场生产多孔混凝土时,制备原料配合比随当地材料性状参数而可能发生变动,特别是不同产地的粗骨料的特征参数(含水率)变化较大。一般情况下,水灰(胶)比随粗骨料粒径的减小而适当增加,最大不宜超过0.30。
用水量的确定:根据设计孔隙率选定胶结材料(水泥)的用量,然后根据多孔混凝土拌和料的工作性要求选定。
多孔混凝土混合物是浆体包裹骨料,浆体必须具有一定的黏聚性,以保证包覆于骨料后仍为颗粒状,一般以手攥成团为度,坍落度在50mm内,混合料成型后骨料表面的浆体将颗粒黏聚在一起,保持一定孔隙,随着期龄水化硬化产生强度,成为硬化的整体的多孔结构。
多孔混凝土的混合料中由于使用了矿物外加剂,需要严格控制生产制备过程,其制备采用现场搅拌较为适宜,首先宜选用滚筒式搅拌机,也可以选用强制式搅拌机或自落式搅拌机。图2.2描述了多孔混凝土浆料的拌和工艺。
图2.2 多孔混凝土混合料工艺流程
现场生产时,上述制备工艺可根据具体情况适当调整。由于碎石骨料表面粗糙,容易挂浆,可将骨料和胶结材一同加入搅拌,边搅拌边加水,30s内加至用水量的50%~70%后,投入矿物外加剂、减水剂等,再搅拌30s,随着搅拌逐渐加入其余水量至工作性合适为止。在黏聚性要求较高的情况下,也可采用掺用树脂改性的方法以提高黏聚性和改善工作性。
2.2.2 混合浆料性能
岸线修复型多孔混凝土应用时,首先按照设计配合比和拌和工艺制备混合料,根据岸线水力特征和结构特征选用一定形状的预制构型,从而制备岸线修复多孔混凝土预制构件。多孔混凝土拌和料性能影响其预制过程的效率和力学性能。
(1)拌和物要求。多孔混凝土拌和物的性能必须满足如下要求:浆体包裹骨料成团,坍落度控制在20~50mm,颗粒间应有一定黏结力,不跑浆,整体呈多孔堆积状态。
(2)工作性。采用控制胶结材流动度的方法能够实现对多孔混凝土的工作性进行控制,胶结材的流动度控制在180~210mm。
(3)表观密度。多孔混凝土的表观密度宜控制在1800~2000kg/m3。
(4)出料后的允许时间。多孔混凝土拌和物出料后的运输应遮盖,低温时应有保温措施,出现终凝的拌和物不得用于坡面现场铺装或预制砌块。根据混凝土混合料的特性和初凝时间,拌和物从出料到运输再到浇筑(预制)完毕所允许的最长时间应符合表2.2的规定。
表2.2 拌和料从出料到运输再到浇筑(预制)完毕的允许最长时间

超过规定时间时,应事先对混凝土配合比进行调整,通过增加缓凝剂和减水剂来满足拌和物的工作性要求。
2.2.3 多孔成型工艺
多孔混凝土成型方法不同于普通混凝土,一般不能采用密实振捣法,通常采用静压法或低频振捣成型。静压成型即使用压力试验机对试模内的拌和物施加压力,成型压力应控制在3MPa左右,加压时间可以通过压力试验机的加压阀控制,保持匀速施压,时间为30s,然后保持3MPa的压力,恒压时间为90s。振捣成型一般采用低频振动机,振动频率为30~50Hz,工作气压30MPa,振动时间为10~20s。
多孔混凝土不同的成型方法,对透水性混凝土的性能产生较大影响。研究过程中分别采用了静压成型和振动成型两种方法,以探讨不同成型工艺对多孔混凝土的影响。多孔混凝土混合料搅拌后,由于水泥浆体和粗集料颗粒间内摩擦作用而具有一定黏性,所以当混合料被浇筑到模具后靠自重产生的流动性是较小的,因此需要来自压力或振动这样的外力来使其密实。当混合料受到振动时引起颤动,这种颤动此起彼伏,破坏了颗粒间的黏结力和机械啮合力,使混合料的内阻力大为降低,最后使混合料部分或全体“液化”。在振动液化过程中,固相颗粒由于混合料黏度的降低,加上重力的作用产生移动,趋于最适宜的稳定位置,水泥浆填充粗集料之间的空隙,使混凝土原来的堆聚结构更为密实。对于多孔混凝土,因其孔隙率的特性,需要对振动的频率和振动时间加以控制,使混凝土既有一定的密实体系,又能保证其多孔堆聚结构。
静压成型的参数是成型压力为3.0MPa,加压时间30s,恒压时间为90s。振动台成型是将拌和好的混合料放入模具,上面加上配重块,放在振动台上振动,振动一定时间后,将模具搬离振动台。实验室的振动台频率控制在30~50Hz。一般振动时间越长,混凝土越密实,但透水性混凝土要求成型后有一定的连通孔隙率,因此振动时间不宜过长,否则会使浆体过多沉积在混凝土底部,堵塞透水通道,使混凝土失去透水性。振动成型时间(10s、15s、20s)对多孔混凝土性能的影响见表2.3。
表2.3 不同成型方法对透水性混凝土性能的影响

注 “—”表示未列入控制参数。
在相同配合比和养护条件下,振动成型试件的透水系数明显低于静压成型试件的透水系数,28d抗压强度均超过28MPa。静压成型的试件强度较高,因为静压成型的试件水泥浆体分布均匀、结构稳定;而振动成型的浆体分布不均造成面层浆体过少,导致强度降低。在实测孔隙率方面,两者的差别不大,观察试件外观,静压成型的试件孔隙分布均匀,浆体包裹均匀。多孔混凝土的透水系数差别较大,静压成型的透水系数达5.8cm/s,而振动成型的多孔混凝土透水系数较小,并随着振动时间的增加而减小。静压成型可形成多孔混凝土较好的性能参数,振动成型的抗压强度、渗透系数较低。在工程使用时,应根据现场条件和设备配置,选用适合的成型工艺。
2.2.4 养护模式
多孔混凝土成型后养护的目的是保证混凝土凝结硬化得以正常进行,使混凝土能获得所需的物理力学性质和耐久性。养护是透水性混凝土生产中时间最长的工序,缩短养护周期对提高设备的利用率、缩小场地占有面积、提高劳动生产率及降低成本均有很大的意义。
多孔混凝土正是由于内部贯通孔隙的存在,其水分流失较快,其养护方式和要求比普通混凝土更为严格。养护对多孔混凝土的强度发展和形成十分重要,多孔混凝土因孔隙较多水分极易挥发,成型后的多孔混凝土要注意保湿,这样有利于水泥浆体的水化。
通过实验研究了多孔混凝土的标准养护和蒸汽养护两种方法,其中蒸汽养护可以提高多孔混凝土的生产效率和工程应用效果。表2.4中描述了多孔混凝土不同养护方法对多孔混凝土强度的影响。蒸汽养护的试件比标准养护的试件强度略高,且蒸汽养护的恒温最佳时间是8h,恒温阶段是混凝土发生水化和水热合成使强度增加的主要阶段,随着恒温时间的延长,水化产物越来越多,强度增加的也越来越快,但达到一定时间后强度增加趋于稳定,因此对试件的蒸汽养护有个最佳的恒温时间。
表2.4 不同养护方法对透水性混凝土强度的影响

在实际生产施工时,多孔混凝土多采用自然养护。自然养护指在自然条件下,采取浇水湿润、防风、防干、保湿防冻等措施进行养护,使混凝土中水泥充分水化,保证其力学性能。自然养护分覆盖浇水养护和喷洒塑料薄膜养护液养护,对于透水性混凝土宜采用覆盖浇水养护。