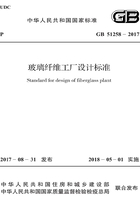
8.3 纤维成形
8.3.1 纤维成形工艺布置应分为成形区、卷绕区和废丝收集区三层,并应符合下列规定:
1 成形区布置应符合下列规定:
1)成形区内净空高度宜为1.9m~2.4m;
2)漏板砖下表面距成形区地面的高度宜为2.0m~2.4m;
3)相邻炉位间距应根据漏板尺寸及安装方式、拉丝机选型综合确定,间距宜减小;
4)成形区内应设置空气调节系统,应建立相对密封的气流控制区,保持温度、湿度恒定,区内不宜结露、滴露。
2 卷绕区布置应符合下列规定:
1)卷绕区内宽度应根据原丝输送方式及拉丝机尺寸综合确定;采用人工手推车或原丝筒输送链时,若使用二分拉拉丝机,卷绕区内宽度宜为6m,若使用三分拉或四分拉拉丝机,卷绕区内宽度宜为7m;采用智能小车(AGV)时,卷绕区内宽度宜为9m;
2)卷绕区层高宜为3.0m~3.5m;
3)卷绕区内宜设置调节区内温度、湿度的空气调节系统,区内不宜结露、滴露;
4)卷绕区外应设置拉丝机安装及维修的通道;
5)卷绕区外宜设置环形排水沟;
6)采用自动化物流时,应分别设置人流、物流出口。
3 废丝收集区布置应符合下列规定:
1)废丝收集区层高不宜小于3.5m;
2)废丝收集区应设置排水沟和集水坑,排水沟应利于各炉位顺畅排水,集水坑容积应与生产线排水设计相匹配。
4 成形区进出口应设置两道门,卷绕区和废丝收集区进出口宜设置两道门。
8.3.2 漏板及漏板附件应符合下列规定:
1 生产漏板的材质宜采用铂铑合金或锆弥散型铂铑合金,铑含量宜为5%~20%;
2 启动漏板的材质宜为SUS310S;
3 漏板法兰边应设置通水强制冷却设施;
4 漏板开口尺寸应与漏板砖开口尺寸相匹配;
5 漏板浇注应采用无定形的耐火材料,浇注料的耐热温度应大于浇注料的工作温度80℃以上;
6 漏板托架宜选择具有持久耐温性能和低电磁感应特性的材料,并应设置中心定位装置,漏板与通路应平行或水平垂直。
8.3.3 漏板导电装置的设计应符合下列规定:
1 漏板导电装置应满足抗氧化、耐高温、易散热的要求;
2 连接处表面应光滑、接触电阻小;
3 漏板导电装置应有固定托架支撑,不得使漏板受力;
4 漏板导电装置各部件均应留有调整空间。
8.3.4 纤维成形附属装置设计应符合下列规定:
1 丝根冷却器设计应符合下列规定:
1)丝根冷却器设计应使每个丝根强制冷却强度一致;
2)丝根冷却器的安装位置应具有可调节性;
3)丝根冷却器的供水管路应单独设置。
2 喷雾器设计应符合下列规定:
1)丝饼纱宜采用单流体喷雾器;直接无捻纱应根据成形扇面大小,选用双流体或单流体喷雾器;
2)喷雾器应设置在漏板与单丝涂油器之间的单纤维扇面区;
3)喷雾器应能均匀喷出雾滴,雾滴直径宜小于100μm;
4)喷雾水宜采用去离子水,并应符合本标准第11.2.8条第5款的规定。
3 单丝涂油器设计应符合下列规定:
1)辊式单丝涂油器和带式单丝涂油器可根据不同浸润剂使用要求选用;
2)单丝涂油器应使每根玻璃纤维上都能均匀涂覆上浸润剂;
3)涂油器的辊子或胶带应易于拆卸、清洗和更换;
4)涂油器固定安装后应能上下、前后、左右可调。
4 分束器、集束器宜选用耐磨性、润滑性好的材质,安装后应能上下、前后、左右可调。
8.3.5 拉丝机布置应符合下列规定:
1 拉丝机作业机头长度方向的中心线应与对应漏板的中心线平行,水平距离可根据生产产品不同选择,宜为450mm~850mm;
2 拉丝机面板与拉丝面板应密封。
8.3.6 原丝输送方式、自动化程度应与整体生产工艺要求相匹配,可采用人工小车、输送链、智能小车等输送方式。
8.3.7 废丝收集可采用废丝槽、废丝桶、废丝板链等多种方式,废丝收集区应留有满足废丝运输车通过的通道。
8.3.8 纤维成形空气调节系统设计应符合下列规定:
1 成形区内应设置空气调节系统,风量应根据漏板大小进行设计,送风温度宜为13℃~17℃,区内温度宜为20℃~24℃,湿度不宜小于80%;
2 成形区内通路底部应设置隔热措施;
3 成形的漏板前后应设有送风装置;
4 卷绕区内宜设置空气调节系统,温度宜为23℃~28℃;
5 废丝收集区应设置回风道,风道应保证每个炉位抽排风的风量均匀。
8.3.9 拉丝车间应设置原丝质量检验、称重计量等设施。