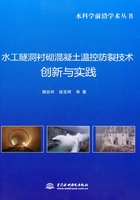
2.2 混凝土原材料质量控制
原材料质量控制是混凝土质量控制的基础。一方面,原材料的品质性能随着社会发展和科学技术进步而不断改良,而且各工程混凝土的骨料、水泥、粉煤灰等原材料往往不同;其次是各个工程建设管理者和参建各方对混凝土质量控制的理解与要求也不同,因此,混凝土原材料的质量控制也在不断进步与发展。
2.2.1 水泥质量控制
混凝土用水泥的质量控制技术要求和检验,是随着三峡工程的开工建设而不断改进的。三峡集团公司管理建设的主要工程使用的水泥熟料矿物组成及化学成分要求见表2.1,水泥品质检验项目与技术指标见表2.2。
表2.1 水泥熟料矿物组成及化学成分要求

表2.2 水泥品质检验项目与技术指标

续表

三峡集团公司对三峡工程混凝土质量高度重视,一开始就对原材料的质量严格控制,在国家标准[9]的基础上结合三峡工程实际专门制定了“三峡标准”,除表2.1和表2.2外,进行补充完善和改进的内容如下。
(1)同品种、同强度等级水泥出厂前按600t作为一编号。
(2)为降低拌合楼出机口混凝土温度,规定散装水泥运至工地的入罐温度≤65℃。
(3)从三峡工程长期的安全考虑,将《中热硅酸盐水泥、低热硅酸盐水泥、低热矿渣硅酸盐水泥》GB 200—2003中规定的MgO≤5.0%,如水泥压蒸安定性合格,允许放宽至6%,调整为水泥中MgO为3.5%~5.0%。
(4)考虑到SO3含量对混凝土凝结时间的影响,三峡标准要求三氧化硫应控制在1.4%~2.2%。
(5)水泥细度小,早期发热快,不利于混凝土温控,结合水电大体积混凝土特性,同时需要水泥有一个合理的颗粒级配,水泥细度采用比表面积代替筛余,同时规定混凝土比表面积宜控制在250~300m2/kg。2003年对三峡标准进行了修订,修订后对水泥细度提出了更高的要求,即细度规定较 1998 年的标准要粗些,可能导致水泥 3d强度达不到国标要求,规定水泥3d强度不作为判定水泥品质是否合格的依据。
(6)凡三氧化硫、安定性、初凝时间中任一项不符合表 2.2 要求者,以及氧化镁含量超出本标准上限要求者,均为废品。
(7)凡比表面积、终凝时间、烧失量、混合材料名称与掺量、水化热、强度(中热水泥3d强度除外)中的任一项不符合表2.2要求者,以及氧化镁含量低于本标准下限要求者,均为不合格品(不合格品可降级用于次要工程)。
溪洛渡水电站工程在借鉴三峡工程经验的基础上,补充进行如下修改:
(1)水泥比表面积大,水化热大,早期发热快,不利于温控。因此,规定了中热水泥比表面积宜为250~320m2/kg,大于320m2/kg的批次数量不得超过15%,最大值不超过340m2/kg;低热水泥比表面积为250~330m2/kg,大于330m2/kg的批次数量不得超过15%,最大值不超过350m2/kg。
(2)溪洛渡坝型为混凝土双曲拱坝,大坝受力条件复杂,从大坝安全角度出发,对大坝混凝土开裂进行敏感性分析结果表明:若大坝混凝土自生体积变形为 0 时,抗裂安全系数 K为2.13,若大坝混凝土自生体积变形为40×10-6时,K增加为3.30;若大坝混凝土自生体积变形值为-40×10-6时,K降低为1.59。可见混凝土自生体积变形对大坝抗裂安全系数很敏感。因此希望通过混凝土的微膨胀来补偿部分由于混凝土温降而引起的收缩变形以及水泥矿物组分在水化过程中的体积收缩变形,以提高大坝抗裂安全系数,增强大坝的安全性,根据实际情况提出混凝土自生体积变形不小于-20×10-6的要求;为达到这一要求,改善混凝土变形性能,充分利用MgO的微膨胀特性,提出了中热水泥中MgO含量的下限值要大于4.2%的要求,同时应采取提高水泥中方镁石含量的技术措施生产水泥。为了提高地下工程衬砌混凝土的抗裂性,在地下工程中使用的水泥也按大坝标准组织生产。
(3)为了降低水泥水化热,规定铝酸三钙的含量不大于4%。
(4)为了提高混凝土抗裂性,规定铁铝酸四钙含量不小于15%。
(5)溪洛渡工程主要使用玄武岩人工骨料,虽然玄武岩骨料经检验为非活性骨料,但考虑到溪洛渡工程的重要性和耐久性,规定了水泥碱含量不得超过0.55%。
(6)为了保证混凝土的质量和均匀性,规定了中热水泥28d抗压强度为49±3.5MPa,为了提高混凝土的抗裂性,规定28d抗折强度不小于7.5MPa;规定了低热水泥28d抗压强度为47±3.5MPa,为了提高混凝土的抗裂性,规定28d抗折强度不小于7.5MPa。
(7)为了减小混凝土水化温升,利于温控,对水泥水化热提出了更严格的要求,规定了中热水泥3d水化热不大于241kJ/kg,7d水化热不大于283kJ/kg;低热水泥3d水化热不大于220kJ/kg,7d水化热不大于250kJ/kg,28d水化热不大于300kJ/kg。
向家坝水电站结合工程实际,对水泥检测标准补充修改如下规定:
(1)凡中热水泥检验结果氧化镁大于 5%、三氧化硫、初凝时间、安定性中的任一项不符合表2.2技术要求时为废品。高抗硫水泥检验结果凡氧化镁、初凝时间、安定性中的任一项不符合表2.2技术要求时为废品。
(2)中热水泥检验结果凡硅酸三钙、铝酸三钙、比表面积、终凝时间、烧失量、水化热、强度中的任一项不符合表2.2技术要求时为不合格品。低热水泥检验结果凡烧失量、三氧化硫、氧化镁、凝结时间、安定性、强度中的任一项不符合表2.2技术要求时为不合格品。高抗硫水泥检验结果凡硅酸三钙、铝酸三钙、比表面积、终凝时间、烧失量、不溶物、强度中的任一项不符合表2.2技术要求时为不合格品。
(3)针对向家坝水电站坝址地质水质含SO42-·HCO3-Ca2+·Mg2+,有硫酸盐侵蚀,限制了中热水泥与高抗硫酸盐水泥中三氧化硫含量≤2.5%。
(4)针对硫酸盐侵蚀问题,限制了中热水泥14d线膨胀率≤0.06%,高抗硫酸盐水泥14d线膨胀率≤0.04%。
根据三峡水利枢纽、溪洛渡和向家坝水电站工程的实践经验与技术进步,针对乌东德与白鹤滩工程地质、水质、温度等环境条件,拟在乌东德、白鹤滩水电站“全面”使用低热硅酸盐水泥,制定了低热水泥性能检测指标(表2.3)。
表2.3 白鹤滩、乌东德工程低热水泥性能指标

其中对水泥熟料提出了更严格的要求,如:C3A≤4%,f-CaO≤0.8%;水泥中碱含量≤0.5%;水泥水化热3d≤220kJ/kg,7d≤250kJ/kg,28d≤300kJ/kg。另外,乌东德水电站,存在硫酸盐侵蚀问题,对水泥增加了SO3≤2.5%、14d线膨胀率≤0.04%的要求。
三峡水利枢纽工程、溪洛渡和向家坝水电站水工隧洞工程主要采用 42.5 中热水泥,在工程应用过程中取得了较好的效果。工程应用水泥检测和试验结果见表2.4。
比较表2.4与表2.1和表2.2的技术指标要求可以看出:
(1)为了严格控制水泥质量的稳定性,尽量减小因水泥质量波动而带来的不利影响,在依据国家和行业规程规范的基础上,结合工程具体要求,对水泥相关技术指标提出了更明确的要求。
(2)通过制定工程标准,在施工过程中对水泥进场质量进行控制,检测结果表明,水泥质量相对稳定,且达到工程标准要求的合格率均≥96.5%。
表2.4 不同工程42.5中热、低热水泥检测结果统计

续表

续表

续表

2.2.2 粉煤灰质量控制
《水工混凝土掺用粉煤灰技术规范》(DL/T 5055—2007)将混凝土和砂浆用粉煤灰,按其细度、需水量比和烧失量三项指标划分等级,技术要求见表2.5,三峡集团公司对粉煤灰的质量技术要求见表2.6。
表2.5 粉煤灰技术要求

表2.6 三峡集团公司水电工程使用粉煤灰技术要求

溪洛渡水电站、向家坝水电站和三峡水利枢纽工程均采用Ⅰ级粉煤灰,粉煤灰检测结果见表2.7~表2.9。
表2.7 溪洛渡水电站粉煤灰检测结果统计表

续表

表2.8 向家坝水电站粉煤灰检测结果统计

续表

续表

表2.9 三峡水利枢纽粉煤灰检测结果统计

续表

续表

由表2.7~表2.9可以看出,三峡水利枢纽工程、溪洛渡水电站工程、向家坝水电站工程在施工期使用的Ⅰ级粉煤灰除少数批次细度、烧失量检测结果出现超标外,其他检测结果合格率均为100%,粉煤灰质量整体稳定。
2.2.3 硅灰质量控制
硅灰的粒径为 0.1~1.0μm,是水泥粒径的 1/100~1/50,比表面积为 20×103~25×103m2/kg,密度为2.1~2.2g/cm3,松散堆积密度为250~300kg/m3。《砂浆和混凝土用硅灰》(GB/T 27690—2011)对硅灰的技术要求见表2.10。
表2.10 硅灰技术要求

注 1.硅灰浆折算为固体含量按此表进行检验。
2.抑制碱骨料反应性和抗氯离子渗透性为选择性项目,由供需双方协商决定。
溪洛渡水电站工程使用硅粉检测结果见表2.11。由表2.11可以看出,硅粉在使用过程中,由于判定标准的变化,Cl-含量、活性指数的评定标准也发生相应改变,但检测合格率均≥70%。硅粉质量整体稳定。
表2.11 硅粉品质检测结果

续表

2.2.4 骨料质量控制
2.2.4.1 粗骨料质量控制与级配比例
骨料包括粗骨料和细骨料(砂)。常用的粗骨料有卵石和碎石两种。水工隧洞混凝土骨料质量控制采用相应的国家和行业标准,根据具体工程原材料的特点有所补充。溪洛渡水电站工程采用人工粗骨料,加工粗骨料的母岩为硐室开挖的玄武岩和大戏场料场开采的灰岩。碎石粒径按150(120)~80mm、80~40mm、40~20mm、20~5mm方孔筛分级,代号分别为D150 (D120)、D80、D40、D20。不同部位混凝土的最大骨料粒径,按DL/T 5144规定应尽量采用较大的粗骨料粒径。骨料的不同级配组合,在混凝土配合比试验设计中选定。各粒级粗骨料的品质检验项目和指标应符合表2.12要求。粗骨料的分离可用各粒级骨料的中径筛即115mm、60mm、30mm、10mm方孔筛的筛余量作检验,各粒级中径筛的筛余量宜在40%~70%,否则应对骨料防分离措施进行改进。同时,对粗骨料加工与检验提出要求:
(1)取用溪洛渡水电站导流洞、泄洪洞、地下厂房区尾水洞、大坝基础开挖的玄武岩加工粗骨料,取料部位除按设计规定外,尚应定期进行岩石变化与碱活性的跟踪监测(由三峡集团公司溪洛渡工程建设部组织),扩增碎石新料源时,须经工程设计单位与三峡集团公司总工程师批准。
(2)粗骨料的开采、运输、堆放设施与加工设备特性应符合规范和设计要求。成品骨料应按同料源、同规格堆放,并有良好的防混、防分离、防跌碎、防污染及遮阳避雨措施与排水等设施。
(3)粗骨料成品质量检验,应每班检验超径含量、逊径含量、中径筛筛余量、含泥量各一次,抽样点为筛分楼出料皮带输送机处。
(4)粗骨料成品的出厂检验,应按同料源、同规格碎石骨料每2000t为一供货批作检验(数量不足一供货批时,按一批计)。每一供货批产品,均应检验超径含量、逊径含量、针片状颗粒含量、中径筛筛余量、含泥量各一次(D20小骨料需增测10mm中径筛筛余量)。D150~D40级骨料的中径筛筛余量检测,每月1~2次。抽样点为成品料仓出料廊道皮带输送机处。
(5)粗骨料检验结果应按合同与管理规定向有关部门提交产品生产与出厂质量检验报告。报告内容应包括产地、类别、规格、代表数量、检验日期、检验结果和质量标准等。
表2.12 粗骨料品质检测项目和指标

此外,对粗骨料的验收、检验与堆放提出了具体要求:
(1)粗骨料的产、供单位应向使用单位提交每一供货批产品的质量检验报告和出厂合格证。供货量按合同规定交接点的地磅或胶带秤进行计量验收。
(2)粗骨料的使用单位应按同品种、同规格粗骨料的供货批量,分批验收、检验与堆放。粗骨料的储、运、用设施应符合设计要求,并有良好的防混、防分离、防跌碎、防污染措施与排水设施。
(3)粗骨料的验收检验应按每验收批来料进行超径含量、逊径含量、针片状颗粒含量、含泥量(D20级小骨料需增测10mm中径筛筛余量)检测;其全部项目检验,每月1~2次。抽样点为来料交接点皮带输送机处。
(4)当观察或发现来料质量异常,应及时进行抽样检验并上报,如混料、含油污染骨料等应拒收或按废料处置。
(5)各项检验结果应按合同与管理规定向有关部门提交产品验收质量检验报告。
粗骨料级配是根据振实密度、空隙率试验(表 2.13)选取,按照振实密度较大、空隙率较小、需要填充的砂浆量较少的原则选择,并在实际混凝土生产过程中,在尽量选择最优的骨料级配的同时应考虑料源的平衡,减少弃料。溪洛渡水电站最终确定粗骨料最佳级配为:四级配特大石∶大石∶中石∶小石=30∶20∶25∶25;三级配大石∶中石∶小石=50∶20∶30;二级配中石∶小石=60∶40。
表2.13 粗骨料不同级配振实密度、空隙率试验结果

2.2.4.2 最佳砂率选择
最佳砂率优选的原则是,在保持水胶比、用水量不变的条件下,混凝土拌合物能够获得较好的工作性,且坍落度达到最大时所对应的砂率。并且观察混凝土在振捣过程中的泛浆情况,综合确定混凝土配合比砂率。砂率过大,将导致混凝土中的砂浆量过多,易造成混凝土干缩开裂;砂率过小,混凝土中的砂浆含量不足,不能有效填充混凝土内部空隙,使混凝土的密实性得不到保证,同时还影响混凝土浇筑质量。
溪洛渡水电站最优砂率试验采用42.5中热水泥,粉煤灰掺量为30%,固定水灰比0.50,掺用高效减水剂 JM-PCA(掺量为 0.7%),AIR202 引气剂,粗骨料级配按选择的最佳级配进行,混凝土含气量按5%±1%、坍落度按30~50mm控制,试验结果见表2.14,振动台振60s后容量筒混凝土中骨料及浮浆情况如图2.1所示。
按容量筒振后混凝土表面有少量骨料外露及混凝土拌合物和易性来综合判定,0.50 水胶比条件下,各级配混凝土最佳砂率分别是:一级配为38%、二级配为32%、三级配为28%、四级配为25%。
表2.14 最佳砂率选择试验结果

续表

图2.1 混凝土表面浮浆情况
(a)一级配s=40%;(b)二级配s=30%;(c)三级配s=26%;(d)四级配s=23%
2.2.4.3 细骨料质量控制
砂按其生产工艺和方法的不同分为天然砂和人工砂两类。按细度模数大小,砂可分为粗砂(细度模数FM为3.7~3.1)、中砂(FM为3.0~2.3)、细砂(FM为2.2~1.6)、特细砂(FM为1.5~0.7)。
(1)砂的粗细程度及颗粒级配。砂的颗粒级配合理与否直接影响到混凝土拌合物的稠度。合理的砂子级配,可以减少拌合物的用水量,节约水泥,并得到流动性、均匀性及密实性均较佳的混凝土。另外砂的粗细对混凝土性能的影响也较大。采用粗砂拌制的混凝土和易性较差,拌合物易分离,混凝土泌水性较大。而采用细砂或特细砂配制的混凝土虽然混凝土和易性好,但其比表面积大,使混凝土用水量及水泥用量增加,混凝土温升高、干缩大、易开裂。
(2)砂的表观密度与吸水率控制。砂的表观密度,按其颗粒饱和状态分为表观密度与饱和面干表观密度。表观密度是砂在完全干燥状态下测得的密度,饱和面干表观密度是在颗粒外表面干燥而内部孔隙水饱和状态下测得的密度。砂在饱和面干状态下,砂颗粒开启孔隙所吸收水分的质量与饱和面干砂质量之比的百分数称为饱和面干吸水率(简称吸水率)。一般砂的吸水率在l%~2%。
砂的表观密度大说明砂粒坚硬致密,可用于配制高品质混凝土。砂的吸水率大,骨料密度小,强度一般较低,会影响骨料界面和水泥石的黏结强度,降低混凝土强度和抗冻性。
在混凝土中骨料处于吸水饱和状态,这部分吸水对水泥的水化和混凝土的流动性是不起作用的,因此采用饱和面干表观密度,可以更准确地反映骨料在混凝土中的实际状态。故我国水工混凝土配合比设计时,砂、石骨料以饱和面干状态为基准。
(3)砂中黏土、淤泥及细屑含量控制。砂中黏土、淤泥及细屑含量指天然砂中粒径小于0.08mm的细屑含量。砂中所含的泥若包裹在骨料表面,不利于骨料与水泥的黏结,将影响混凝土强度及耐久性;若含泥是以松散颗粒存在,由于其颗粒细与比表面积大,会增加混凝土的用水量,特别是黏土的体积不稳定,干缩湿胀,会对混凝土产生干湿体积变化的破坏作用。砂中的泥块含量是烘干砂中粒径大于1.25mm的颗粒,用水捏碎,小于0.630mm颗粒的含量。
(4)人工砂石粉含量控制。《水工混凝土试验规程》(SL 352—2006)规定人工砂中小于0.16mm的颗粒称为石粉;小于0.08mm的颗粒称为微粒。《建设用砂》(GB/T 14684—2011)中把人工砂石粉含量定义为人工砂中粒径小于75μm的颗粒含量,并用压甲蓝MB值判定颗粒是泥土还是石粉。人工砂中含适量的石粉,能改善混凝土拌合物的性能,改善混凝土的孔隙结构,提高混凝土的密实性。对于碾压混凝土,人工砂中的石粉能大大提高混凝土的可碾性。但石粉含量较大会提高混凝土的用水量,降低混凝土的强度,也对混凝土的干缩产生不利影响。
溪洛渡水电站工程采用人工砂骨料,加工砂骨料的母岩为硐室开挖的玄武岩和大戏场料场开采的灰岩。细骨料的品质检验项目和指标应符合表2.16的要求。
表2.16 混凝土用细骨料品质检验项目和指标

续表

2.2.5 外加剂质量控制
2.2.5.1 外加剂质量控制
国家标准《混凝土外加剂的分类、命名与定义》(GB/T 8075—2005)将混凝土外加剂定义为:混凝土外加剂是一种在混凝土搅拌之前或拌制过程中加入的、用以改善新拌混凝土和(或)硬化混凝土性能的物质,掺量不大于 5%(特殊情况除外)。减水剂和引气剂是水工混凝土常用外加剂。外加剂适应性检验内容及指标列于表2.17。外加剂现场验收质量检验包括:(1)外加剂匀质性检验,检验内容及指标见表2.18;(2)掺外加剂混凝土性能检验,检验内容及指标见表2.19。
表2.17 外加剂适应性检验内容及指标

表2.18 外加剂匀质性检验内容及指标

续表

注 1.带*的检验项目为日常检验项目,其他项目为形式检验项目。引气剂的掺量很小,其总碱量和硫酸钠含量可以不作为日常检验项目。聚羧酸类高性能减水剂的总碱量和硫酸钠含量很低,也可以不作为日常检验项目。
2.生产厂家应在相关的技术资料中明示产品匀质性指标的控制值。
3.S、W、D分别为含固量、含水率和密度的生产厂控制值。
表2.19 掺外加剂混凝土性能检验内容及指标

注 1.除含气量和相对耐久性外,表中所列数据为掺外加剂混凝土与基准混凝土的差值或比值。
2.凝结时间差性能指标中的“-”号表示提前,“+”号表示延缓。
3.1d、3d抗压强度比不作为验收控制指标。
4.相对耐久性(200次)性能指标中“≥80”表示将28d龄期的受检混凝土试件快速冻融200次后,动弹性模量保留值≥80%。
5.减水剂的转型:每年的11月、12月、1月、2月使用标准型;3—10月使用缓凝型。
2.2.5.2 外加剂品种的确定
溪洛渡工程前期,为了选择适合工程需要的外加剂,通过对不同厂家和品种的外加剂进行品质检测和混凝土性能试验,经过初选、复选,最终确定品质和综合性能较好的减水剂品种有聚羧酸类减水剂JM-PCA、NOF-AS、X404C、Glenium26R及萘系减水剂JM-ⅡC、ZB-1A。引气剂GK-9A、AIR202、QH-SY、ZB-1G四种。采用的外加剂种类有高性能减水剂、高效减水剂和引气剂。
自2009年7月—2013年6月[8],按供货计划要求共监理生产和检验不同种类和型号的混凝土外加剂325批20930t,其中2009年29批1757t,2010年92批5401t,2011年119批7507t,2012年77批5465t,2013年8批800t。外加剂进场检测合格率均为100%。外加剂品质检测结果见表2.20~表2.31。
表2.20 ZB-1A减水剂品质检测结果统计表

表2.21 JM-Ⅱ(C)减水剂品质检测结果统计表

注 2009年,标准修订前,高效减水剂的受检混凝土的初凝结时间差,标准型为+180~+420min,缓凝型为+420~+600min。
表2.22 JM-PCA(Ⅰ)减水剂品质检测结果统计表

注 ①:JM-PCA(Ⅰ)减水剂2010年1月开始执行溪洛渡高性能减水剂标准。2009年12月底前的JM-PCA(Ⅰ)减水剂为高效减水剂,标准型初凝结时间差为+180~+420min,最大值+315min满足当时要求。
②③:2009年12月底前为高效减水剂,3d龄期抗压强度比≥130%即满足要求,28d龄期抗压强度比≥120%即满足要求。
表2.23 X404(C)减水剂品质检测结果统计表

注 ①用于全灰岩混凝土,减水率要求在25%左右。
② X404(C)减水剂2010年1月开始执行溪洛渡高性能减水剂标准。2009年12月底前的X404(C)减水剂为高效减水剂,初凝结时间差满足当时的要求。
表2.24 ZB-1G引气剂(粉剂)品质检测结果统计表

表2.25 ZB-1G引气剂(胶状)品质检测结果统计表

表2.26 ZB-1A减水剂匀质性检测结果统计表

表2.27 JM-Ⅱ(C)减水剂匀质性检测结果统计表

表2.28 JM-PCA(Ⅰ)减水剂匀质性检测结果统计表

续表

注 用于低热水泥混凝土的JM-PCA(Ⅰ),生产厂家控制值:含固量≥20%,PH 6±1。
表2.29 X404(C)减水剂匀质性检测结果统计表

表2.30 ZB-1G引气剂(粉剂)匀质性检测结果统计表

表2.31 ZB-1G引气剂(胶状)匀质性检测结果统计表

2.2.5.3 外加剂掺量优选
试验采用泄洪洞工程C9060混凝土,水胶比0.33、粉煤灰掺量30%、砂率32%、二级配混凝土,坍落度控制90~110mm,含气量控制3.0%~4.0%,掺硅粉5%+掺PVA纤维0.9kg/m3,减水剂掺量由低到高分别取0.7%、0.8%、0.9%和1.0%,直至混凝土拌合物出现泌浆、板结为止,根据混凝土性能试验结果寻找减水剂适宜掺量,确保混凝土单位用水量较低。混凝土拌合物试验结果见表2.32和表2.33,混凝土强度试验结果见表2.34。
表2.32 外加剂掺量优选混凝土拌合物试验结果

从表2.32可知:
(1)在相同水胶比条件下,混凝土拌合物用水量随减水剂掺量增加而减少,减水剂每增加 0.1%,单位用水量减少 1~2kg/m3。峨胜低热水泥混凝土拌合物用水量相对较低,为 108 kg/m3,华新中热、嘉华和石门低热水泥混凝土拌合物用水量基本相当,为115~116 kg/m3。
(2)采用X404减水剂,石门低热水泥减水剂掺量适宜为0.7%,峨胜低热水泥与华新中热水泥混凝土减水剂掺量适宜为0.8%,嘉华水泥减水剂掺量适宜为0.9%;采用JM-PCA减水剂,峨胜低热水泥减水剂掺量适宜为 0.7%,石门低热水泥与华新中热水泥混凝土减水剂掺量适宜为0.8%,嘉华水泥减水剂掺量适宜为0.9%。
(3)外加剂掺量优选试验结果表明,在选择的掺量范围内,掺两种减水剂对不同品种水泥混凝土的拌合物用水量的影响规律基本一致,即使减水剂掺量增加至 0.9%,对混凝土用水量也影响不大,应以新拌混凝土不出现板结、泌浆现象来选择适宜掺量,减水剂掺量一般选定为0.8%,并采用0.8%掺量进行不同水泥混凝土拌合物坍落度、含气量损失比较试验。
表2.33 混凝土拌合物性能检测结果

从表2.33可知,在相同减水剂掺量条件下,采用X404减水剂,不同品种水泥1h混凝土拌合物坍落度损失率为38.7%~45.3%,含气量损失率为21.6%~35.9%;采用JM-PCA减水剂,不同品种水泥 1h 混凝土拌合物坍落度损失率为 33.3%~54.0%,含气量损失率为 25.0%~31.7%。不同品种水泥及两种高性能减水剂对混凝土拌合物性能无显著性影响。
表2.34 混凝土强度试验结果

续表

从表 2.34 可知,相同水泥使用不同厂家减水剂混凝土抗压强度基本一致;3d、7d、28d和90d龄期时,中热水泥混凝土抗压强度发展系数为0.45、0.63、1.00和1.14,低热水泥混凝土抗压强度发展系数为0.33、0.54、1.00和1.19。试验结果表明,中热水泥混凝土早龄期强度发展系数大于低热水泥混凝土,28d、90d抗压强度基本与低热水泥混凝土相当。