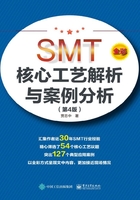
3.5 波峰焊接
发展过程
波峰焊接,指将熔化的软铅焊料,经过机械泵或电磁泵喷流成焊料波峰,使预先装有电子元器件的PCB通过焊料波峰,实现元器件焊端或引脚与PCB焊盘之间机械和电气连接的一种软钎焊工艺。虽然再流焊相对波峰焊有很多优点,但是,在可预见的未来,波峰焊接仍是一种主要的焊接技术。
波峰焊接工艺的使用已经有几十年的历史了,经历了插装元器件时代的单波峰焊接工艺和表面组装时代的双波峰焊接工艺两个发展阶段,如图3-48所示。目前使用的波峰焊接机主要都是双波峰焊接机。
波峰焊接机,称呼起来比较拗口,通常简称为波峰焊机。

图3-48 波峰焊接机的发展历程
双波峰焊接工作原理
双波峰焊接机的功能系统主要包括三部分,即助焊剂喷涂系统、预热系统和双波峰焊接系统。助焊剂喷涂系统的功能是将助焊剂均匀地涂覆在PCB的焊接面。预热系统的功能有三个,即获得适当温度和黏度;促进助焊剂活化;减少热冲击与变形。双波峰焊接系统是双波峰焊接机最重要的功能部件,决定焊接的效果。
双波峰焊接系统,是为适应插装元件与表面贴装元器件混合安装特点而在单波峰焊接机的基础上发展起来的,自发明以来,其结构已基本固定为“紊流波+平滑波”的结构形式,如图3-49所示。

图3-49 双波峰布局与特点
紊流波的主要功能是产生一个向上冲击的紊流波,将因“遮蔽效应”(见图3-50)而形成的气泡赶走,使锡波能够紧密地与焊盘接触从而减少漏焊现象的发生。向上冲击的紊流波也有利于安装孔的良好填锡。

图3-50 遮蔽效应
平滑波,正如其名,其主要功能是产生一个无波峰与波谷的平滑锡波,用于焊缝形态的修正。平滑波的结构与宽度对波峰焊接质量的影响很大,一定程度上决定了波峰焊接的直通率,也是不同品牌波峰焊接机的价值所在。
1)平滑波工艺分析
平滑波可分为三个工艺区域:PCB进入区(A点前)、传热区(A、B间的区域)和PCB离开区(B点后),如图3-51所示。

图3-51 平滑波的三个区
(1)焊剂。PCB进入A、B之间的区域时,PCB完全被焊料桥连,可焊面上的焊剂被焊料排走,非可焊面(阻焊层具有吸附焊剂的能力)上焊剂仍然存在,如图3-52所示。

图3-52 焊剂的覆盖
(2)分离点B。B点的位置是动态的,是由传送系统的倾角、传送速度及具体的PCBA确定的。如果是阻焊面,在B1点与锡波断开;如果是引线或焊盘,要到B2点的位置断开。如果引线比较长,B1、B2之间距离就会比较长,如果长到引线锡料孤立垂直分离时,就可能形成桥连缺陷(传热中断的结果)。
因此,PCB的设计,应尽可能提供“连续载波”的能力。
(3)平滑波延伸段,主要的功能是降低锡波的分离速度,合适的夹角为7°~10°。分离速度影响焊点的形态,过快的分离对不同的焊点结构(由焊盘大小和引脚伸出长度构成的焊点)影响不同,具体来讲就是拽锡量的不同。一般而言,过快的分离速度会导致更多的干瘪焊点(不饱满焊点)和比较少的桥连现象;过慢的分离速度会获得更加饱满的焊点及更多的桥连。
(4)AB长度与传送速度决定了PCB接触锡波的时间,它是波峰焊一个重要的工艺参数。接触时间决定焊点的受热量,从而影响到插孔内焊锡的垂直填充高度。
2)平滑波的主要波形
平滑波的波形有几十种,流行的波形有单面波、双面波(或T形波)、λ波(PCB传送速度相对锡波流速为0的波)、带延伸板的λ波,图3-53是比较常见的波形。

图3-53 常见波形
不同的平滑波波形结构决定了波峰焊接机的性能,例如:
(1)窄的平滑波。利于消除大部分的桥连现象,但热容量大的焊点(粗引线)有可能因受热不足而增加桥连。如何满足不同粗细引线的焊接要求,就成为波峰焊接工艺控制的难点。
(2)宽的平滑波。适合大热容量板(或焊点)的焊接,焊点也比较饱满,但桥连会比较多。
(3)带延伸的平滑波,适合高效率的生产。由于焊点与波的分离属于慢速垂直分离,速度慢了往往会产生更多的桥连现象。
(4)锡波产生的方式主要有机械式(波轮)和电磁式(早期推出的电磁式波往往打不高,是一个不足)。
对于波峰焊接机来讲,一方面,不同品牌波峰焊接机的波峰系统设计不同,特别是平滑波的波形设计不同;另一方面,又没有一种平滑波的设计适用于所有种类的PCBA。这就要求在选择波峰焊接机的时候,要全面考虑你的工艺需求、主要产品的工艺特性和名列前三(TOP3)的焊接问题。比如,焊接的是装有密脚连接器的PCBA还是装有大热容量的元器件的PCBA,它们对波峰焊接机(具体而言就是波形)的要求是不一样的。前者更多地要考虑设备应对桥连的能力,后者更多地要考虑设备应对插装孔的焊锡垂直填充的能力。关注点不同,对设备的要求也不同。现实情况是,很多企业在选择波峰焊接机时根本没有考虑自己的工艺需求,往往是设备买回去使用以后,发现焊接问题比较多。这种情况反映了企业对波峰焊接工艺的不了解,也反映了波峰焊接工艺的复杂性。必须指出,波峰焊接的质量在一定程度上取决于设备的性能,这点与再流焊接有所不同!
双波峰焊机的选型
波峰焊接机一般由焊剂喷涂系统、预热系统、波峰系统、传送系统和控制部分组成。选型时应了解各部分的工作原理和应用特点。
1)焊接喷涂系统
焊剂喷涂主要有两大类,即压缩空气雾化方式和焊剂直接雾化方式。
主要应用问题:焊剂喷嘴堵塞、焊剂覆盖不全、助焊剂排风管道细(≤6″)或抽风不足,焊剂散出比较多,气味大。
2)预热系统
应了解预热系统的加热元器件与特点。一般波峰焊接机所用的加热元器件有电热管、石英灯管、红外板和热风及其组合。
石英灯管热惯性小、能量密度大。
红外板容易裂,目前采用的不多。
热风多作辅助用,用于元器件面的加热。
3)传送系统
传送系统可分位两类三种:夹爪类,主要有三段式和一段式;框架类。
(1)夹爪类。适合多品种小批量产品的生产,但设备利用效率较低,小板,特别是质量分布不平衡小板(如一头有铜柱)容易卡。三段式或一段式取决于波形的设计(是否需要大倾角)。
三段式,主要用于高效率波峰焊接机。高效波峰焊接机需要长的预热系统和加长的宽平滑波,为了不把传送系统抬得太高,一般设计成三段式,如图3-54所示。
一段式,主要用于短预热系统,结构紧凑,传送可靠。

图3-54 三段式传送系统
(2)框架类。可以减少板的变形,也可一次多板过炉。缺点就是现场操作比较麻烦。
主要应用问题:较重的板掉板、卡板。
4)波峰系统
它是波峰焊接机的关键功能部件,决定波峰焊接机的性能,选型时一定要根据要焊接的产品工艺特点进行选择。
5)氮气应用
相对有铅工艺而言,无铅工艺有三个明显的不同:焊料的润湿性比较差;焊料的熔点比较高,流动性比较差;无铅焊料比较贵。因此,很多的无铅波峰焊接机具有氮气气氛焊接功能。在选择具有可接氮气功能的波峰焊接机时,应当意识到,氮气保护隧道是否可以打开,关系到能否焊接温度敏感元件的问题。如果隧道上盖可以打开,它就能够焊接薄膜电容之类的温度敏感元件,否则就比较困难。
工艺控制
波峰焊接工艺,相对于再流焊接工艺而言是复杂的。根据安捷伦公司对全球有影响的25家大型EMS企业的焊点质量统计与分析,波峰焊接焊点的不良率平均高于1500ppm,这远高于再流焊接工艺,像手机板的焊接,焊点的不良率一般小于50ppm。之所以如此,主要是波峰焊的工艺调试非常复杂,不仅参数多,而且要根据解决的焊接问题进行个性化的参数设置。因此,要提升波峰焊的质量,需要根据单板工艺特点对工艺参数进行“调试”。
1)焊剂喷涂
用双面胶纸把一张白纸粘贴在PCB上,进行焊剂涂覆,检查焊剂喷涂是否均匀,是否漏喷,焊剂是否入孔,特别是OSP孔。
漏喷常常是引起桥连、空洞、透锡率不足和拉尖的常见原因。
2)预热
预热有如下几个目的:
(1)使大部分焊剂挥发,避免焊接时引起飞溅、造成锡波温度下降(因为焊剂挥发需要吸热)。
(2)获得适当的黏度。黏度太低,焊剂容易过早地被锡波带走,会使润湿变差。
(3)获得适当的温度。减少PCBA进入焊锡波时的热冲击和板变形。
(4)促进焊剂活化。
合适预热结果的评判:
(1)对有铅焊接而言,焊接面约为110℃。对于给定的PCBA,可以通过测量元器件表面温度判断;也可以用手摸,发黏即可,太干容易引起焊接问题。
(2)OSP板,预热温度需要适当提高,如130℃。
(3)ENIG板,要视使用单波还是双波确定。双波需要较高的预热温度,单波则需要较低的预热温度,以避免焊盘边缘反润湿。
3)焊接
(1)紊流波向上应具有一定的冲击力,形成无规则的谷与峰。
(2)平滑波锡波面必须平整,波高用来实现无缺陷焊接的目标。
不同的波形要求不同,如某品牌波峰焊接机,波比较低时,桥连、拉尖就比较多(受热不足);波比较高时,焊点的饱满性会变差(快速下拉)。这些都基于其窄的弧形波特性。
拉尖,通常是因为焊锡还没有拉下,其上部已经凝固所致。之所以凝固,是因为引线散热比较快或引线比较长,为了避免拉尖,有时需要将平滑波压得深些以提高引线的热容量,也可以通过降低传送速度来实现(高速传送前提下)。
波高的调节一定要配合传送速度进行调节,单纯的调节波高往往难以实现目标。
4)传送速度
影响焊点的受热和分离速度。一般不可单独调节,需要根据波形、所焊PCBA进行调节。
5)导轨宽度
以PCB可以自由拉动为宜,太紧会加剧PCB的变形甚至使PCB上弓(会出现规则的非焊区),也会加速夹爪的磨损(因为大多数波峰焊接机都依靠铝型材侧面支撑夹爪,少数焊接机在侧面镶嵌有铜条,抗磨性会好些)。
波峰焊接工艺之所以难,是因为每个参数有一个合适的点,参数的影响往往非线性,可参考以下内容加以理解。
波峰焊接工艺的复杂性
波峰焊接,一般不良率比再流焊接高,除了本身可控性差外,一定程度上也是不被重视造成的。随着插装元器件的使用越来越少,在很多的工厂,波峰焊接工艺已经被边缘化,往往不愿意投入资源进行波峰焊接工艺的优化工作。
波峰焊接工艺参数对焊接质量的影响往往比较复杂,有些参数对焊接缺陷率的影响并非线性关系,而且与引线的热容量、波峰喷嘴的设计有关。
波峰焊接无铅化所遇到的挑战一点不比再流焊接少,由于无铅焊料的流动性差、表面张力大,无铅波峰焊接对应的缺陷比较高,尤其是孔的透锡性和桥连缺陷。有人应用DOE方法研究了焊料温度、焊接时间(接触时间)、PCB顶面的预热温度和焊剂量对桥连和透锡的影响,表3-6为DOE采用的试验条件,试验结果如图3-55和图3-56所示。
表3-6 波峰焊接工艺参数试验条件


图3-55 各因素对桥连的影响
(数值越高,代表桥连越少,200代表完全无桥连)

图3-56 各因素对透锡性的影响
(数值越高,质量越好,4662代表所有孔都百分百透锡)
从这两个表我们可以认识到波峰焊接的复杂性及难控制性。
常见问题及对策
1.桥连
影响桥连的因素很多,设计、焊剂活性、焊料成分、工艺等,需多方面持续改进。
根据所产生的原因,桥连可以大致分成两类:焊剂不足型和垂直布局型。
(1)焊剂不足型。特征是多引线连锡、焊盘、引线头(最容易氧化)无润湿或局部润湿,如图3-57所示。

图3-57 焊剂不足型桥连特征
(2)垂直布局型。特征是焊点饱满、引线头包锡、连锡悬空,如图3-58所示。这是常见的桥连类型,正如其分类名称那样,它主要与PCB上元器件布局有关,其次与焊盘大小、引线间距、引线粗细、引线的伸出长度、焊剂的活性、锡波高度、预热温度和链速等有关,影响因素比较多、复杂,难以全部解决。一般多发生在引线间距比较小(≤2mm)、伸出比较长(≥1.5mm)、比较粗的连接器类元器件,如欧式插座。

图3-58 垂直布局型桥连特征
改进措施:
1)设计
(1)最有效的措施就是采用短引线设计。采用2.5mm间距的引线,长度控制在1.2mm以内;2mm间距的引线,长度控制在0.5mm以内。最简单的经验就是“1/3原则”,即引线伸出长度应取其间距的1/3。只要做到这点,桥连现象基本可以消除。
(2)连接器等元器件,尽可能将元器件的长度方向平行于传送方向布局并设计盗锡工艺焊盘,以提供连续载波能力,如图3-59(a)所示;如果已经设计为图3-59(b)所示的布局,焊接时可以转90°方向,使之平行于传送方向焊接。
(3)使用小焊盘设计,因为金属化孔的PCB焊点的强度基本不靠焊盘的大小。对减少桥连缺陷,焊盘环宽越小越好,只要满足PCB制造需要的最小环宽即可。

图3-59 连接器布局位向
2)工艺
(1)使用窄的平滑波波峰焊接机进行焊接。
(2)使用合适的传送速度(以引线能够连续脱离为宜)。链速快或慢,都不利于桥连现象的减少。传统的解释是因为链速快,打开桥连的时间不够或受热不足;链速慢,有可能导致引线靠近封装端温度下降。但实际情况远比这复杂,有时,热容量大、长的引线,宜快,反之,宜慢(大热容量与小热容量引线在传送速度方面的要求总是相反的)。因此,实践中要多试。
链速快慢判别标准视焊接对象、所用设备而定,是一个动态的概念。一般以0.8~1.2m/min为分界点。
(3)预热温度要合适,应使焊剂达到一定的黏度。黏度太低容易被焊锡波冲走,会使润湿变差。过度预热会使松香氧化并发生聚合反应,减缓润湿过程。这些都会增加桥连的概率。
(4)对非焊剂原因产生的桥连,可以通过降低波高的方法进行消除(以波刚接触最长引线尖端为目标,这是TAMULA的建议)。
(5)选用黏性小的无铅焊料合金,如NIHON SUPERIOR的SN100C(Sn-Cu-Ni-Ge,其熔点为227℃),声称是一种无桥连、无缩孔,业界最成功的无银无铅焊料,焊接质量如图3-60所示。

图3-60 使用SN100C焊料焊接的结果
图3-61为连接器因传送方向改变而出现桥连的实际案例。以图3-61所示方向反方向过波峰,因PCB的变形使连接器实际接触时间增加,同时,由于变形使连接器脱锡时快速分离。这两点可能导致连接器桥连概率增加。

图3-61 传送方向对桥连的影响
有时也会因为波不平所致,因此,应定期检查波的平稳性。生产中有时发现喷嘴被锡渣堵塞、保护非焊接孔翻锡的胶纸剥离等会干扰波的平稳性,造成桥连。
2.漏焊及虚焊
漏焊,主要涉及片式元件,与元器件高度和布局方向及元器件封装和焊盘外伸长度有关。原因是元器件的“遮蔽效应”和焊剂的“气囊隔绝”,有时也与焊剂涂覆、焊盘/引线氧化有关。
虚焊多与焊盘或焊端氧化、热量不足、引线长过波峰时扰动有关。
改进措施:
(1)优化元器件布局和焊盘设计,如图3-62所示。

图3-62 片式元件的布局
(2)对于元器件面插孔被盖的插装焊点,也称为人造盲孔式焊点,如图3-63(d)所示,波峰焊接很容易形成填充不实、有针孔的焊点,如图3-63(c)所示。波峰焊接焊接时一定要打开紊流波,原因是这种焊接不良是由于插孔内助焊剂挥发气体无法排出而形成的。打开紊流波,有利用其不规则的波将助焊剂挥发气体赶出,从而可以形成填充良好的焊点。

图3-63 案例
(3)充分预热或减少焊剂量(前提是使用了高焊剂量),消除“气囊隔绝”效应的影响。
(4)还要注意挡条和托架的设计不要影响元器件的受热与受锡空间。
3.掉片
掉片一定是焊点受到机械外力的作用,不然不会无缘无故地掉落。对于红胶工艺的波峰焊接,多半与PCB的变形有关。PCB变形缩小了PCB与波峰喷嘴间的距离,如果元器件高度大于此距离,就会被喷嘴刮掉,如图3-64所示。

图3-64 波峰焊接掉片
原因:板变形。
改进措施:使用托盘。
4.锡珠
锡珠主要出现在插件焊点附近,为焊锡飞溅所为,如图3-65所示,主要与PCB使用的阻焊剂品牌有关,阻焊剂表面越光越容易黏附焊锡珠。
同时还与其他工艺因素,如PCB受潮、焊剂预热不充分及使用掩模板有关。如掩模板开口边缘会渗进焊剂,高温迅速挥发,引起焊锡飞溅并黏附在阻焊层表面。

图3-65 锡珠现象
改进措施:烘板去潮。
注意再充分的预热也不能代替PCB的去潮工艺,潮气的排出需要较长的时间(25℃、≥4h)。
5.拉尖
拉尖现象如图3-66所示,此现象主要出现在单面板波峰焊接情况下,多与长引线、粗引线、易散热元器件有关。金属孔安装的双面板很少会出现拉尖现象。

图3-66 拉尖现象
主要原因:
(1)焊剂活性不足或涂敷量少。
(2)引线剪脚端面可焊性不好或有毛刺。
(3)受热不足,这是拉尖产生的最常见原因。波峰焊从原理上讲,一个焊点的形成有两个先后接续的过程——焊料填充(包括孔内与焊缝)和多余焊料修整。拉尖的形成发生在焊料修整阶段,但受到填充时热量的供给以及元器件散热快慢的影响。如果元器件引脚或插孔孔壁冷得快,在锡波脱离焊点时引脚的温度可能已经下降到焊料的凝固温度以下,这时引脚端头上的多余焊料就没有办法被锡波拖走或回流到焊缝,就会形成拉尖。
(4)焊剂提前失效。传送速度太慢,会在焊点脱离PCB前挥发完,引起拉尖。
注意:
传送速度必须合适,太快或太慢,都会引起拉尖(尽管原因不同)。如某电源板传送速度为145cm/min时没有问题,但调到100cm/min就会出现问题。
因此,消除拉尖缺陷时,速度的调整应该先判断快还是慢,应小幅度改变,不可跨越式调整,否则会找不到合适的点。一般而言,速度快,形成的拉尖比较光亮,速度慢,形成的拉尖比较暗并伴有锡丝甚至锡网出现。
(5)与元器件的布局或过波峰的方向有关,如图3-67所示。

图3-67 布局对拉尖的影响
一般而言,最后脱离锡波的边,锡波不稳,锡波比较低,如果元器件离边很近,就很容易引起拉尖。因此,建议把元器件离边比较近的边作为波峰焊接的入边,这样影响会小些。
6.冷焊
掩模选择性波峰焊常见的焊接不良就是冷焊。掩模选择性波峰焊使用的掩模板通常采用合成石制作,合成石掩模板阻断了锡波与PCB的接触,相等于隔绝了锡波对PCB的加热,使被掩模板遮蔽的PCB部分成了冷源。如果选择焊接窗口开口比较小且周围均被掩模板遮盖,那么波峰焊焊点的温度往往很低,焊点的热量很快被周围冷的PCB吸收,最终形成冷焊点。
如果确认PCBA上的插件后续采用掩模选择性波峰焊接,那么插装元器件的布局应该遵从:
(1)尽可能集中布局。
(2)在插件周围10mm范围不要布贴片元器件。
这样的布局,一方面考虑了掩模板开窗的设计要求,另一方面也考虑了局部的受热需要。因为掩模板局部波峰焊接的受热条件不好,焊点仅从小的开窗受热,过小的孔也不利于锡波的流动。
插件的布局以及掩模板开窗的设计要求如图3-68所示,图3-69为一不良设计实例。

图3-68 掩模板设计要领

图3-69 掩模板开窗的不良设计
7.ENIG孔盘周边发黑(实际为无润湿部分)
图3-70是无铅焊接经常可遇到的一种焊接缺陷,ENIG板插孔焊点的焊盘周边存在不规则反润湿孔状斑点(黑),但正面再流焊接焊点没有问题。

图3-70 ENIG孔盘周边发黑无润湿现象
原因分析:
切片观察,通孔内焊接良好,不润湿发生在孔盘边,如图3-71所示。

图3-71 切片图
同时,发生ENIG盘边不润湿现象的焊点,常常伴有焊点表面缩孔现象,如图3-72所示。

图3-72 焊点表面缩孔现象
此类不润湿多为ENIG表面处理存在轻微黑盘现象,孔盘边缘往往是黑盘严重的地方,再加上波峰焊接的冲刷作用及无铅合金的特性,容易发生此类现象。
8.OSP孔透锡不良
无引线处金属化孔几乎不透锡,有引线处透锡也比较差,如图3-73所示。

图3-73 OSP板孔透锡差
原因分析:
OSP膜是有机膜,本身不润湿,焊接面上的OSP膜必须分解后才能被润湿。因此,与膜厚、温度或焊剂有关。
一般要将OSP分解,有两种方法:
(1)足够的焊剂。OSP膜对焊剂量比较敏感,焊剂不足就分解不了,也就不能润湿。
(2)也可采用提高预热温度的办法,但也会带来负面影响,也可能使焊剂提前分解。
改进措施:
(1)必须有足够的焊剂喷到孔内(如果移动速度太快就会漏喷),加大焊剂涂敷量是有效的方法之一,必须保证焊接前焊剂处于黏性状态。
(2)适当提高预热温度和焊接温度,此点作为参考。
(3)OSP膜厚度必须控制,太厚,在短短的2~3s间不容易将其分解掉,就会产生此类问题;另外,也与OSP的质量有关,如F2、106A等型号的OSP膜,就不会有问题,而一些杂牌的OSP就容易发生此类问题。
9.孔填充不实(气孔)
这是典型的、由设计引起的问题。波峰焊接孔内的填充与孔及引线的间隙(指孔径减引线直径)有关,此间隙不能大于0.4mm。
经验数据:
(1)单面板(非金属化)插孔与引线的合适间隙为0.05~0.3mm(最优为0.15mm),但超过0.4mm,孔穴率明显增加,如图3-74所示。
(2)金属化孔与引线的合适间隙一般为0.2~0.4mm(最优为0.4mm),间隙过大也容易发生不完全填充。

图3-74 间隙与填充合格率的关系
宽的扁形引线配圆孔是非常糟糕的设计,焊接时很容易产生不完全填充,如图3-75所示!

图3-75 不完全填充实例
(3)焊盘尺寸与连接强度,金属化孔主要靠孔连接,焊盘大小关系不大,但对单面板来说,焊点强度完全靠焊盘决定,一般取孔径的1.5倍。
10.吹气孔
吹气孔多与PCB的钻孔工艺、电镀质量和吸潮有关。
许多PCB小厂,经常长时间不更换钻头,使用钝的钻头钻出的孔壁比较粗糙,电镀后孔壁容易存在纤维毛刺或孔,焊接时湿气喷出形成火山口型吹孔,如图3-76所示。

图3-76 吹气孔
一般情况下,如果使用钝的钻头钻孔且电镀通孔(指电镀铜层)孔壁比较薄就会发生此问题。孔是PCB排气的一个主要通道!
原因分析:
(1)切片,测量孔壁厚度,应满足20μm的要求(IPC-2221A)。
(2)横截面做切片,逐层分析。
改进措施:烘板。
注意:再充分的波峰焊预热也不能代替PCB的烘干工艺,潮气的排出需要较长的时间。
11.叠板
叠板的危害是引起进入边元器件漏焊。
如果插件传送带(进入波峰焊接机之前)的链速比波峰焊接机的链速快,后面的PCB就很容易叠在前面的PCB上,引起PCB叠板,如图3-77所示。

图3-77 叠板现象
12.板面脏
板面脏与所用焊剂、板面颜色、预热温度有关。板面颜色越深越明显;温度越高,板面越干净(一般免洗焊剂预热温度达到120~130℃时,就会比较干净)。但温度过高,有可能会引起焊剂提前失效,增加焊接缺陷率。
13.翻锡
板尺寸大受热变形或波压锡太多。
14.元器件被浮起
某产品上的单排连接器,在速度100cm/min时焊接良好,提高速度后出现图3-78所示单侧插翘起/浮起现象。
速度快,插座受到的向上力比较大,再加上受热不足(温度不变前提下),很容易被浮起。

图3-78 单排连接器单侧被浮起
设计上可减小插孔孔径,利于减少被浮起的风险。
也可采用工装压住(有弹性顶针的镂空压板)。