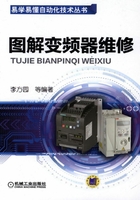
5.1 变频器的制动原理与方式
5.1.1 制动问题的提出
一般而言,负载的能量可以分为动能和势能两种。动能(由负载的速度和重量确定其大小)随着物体的运动而累积,当动能减为零时,该事物就处在停止状态。机械抱闸装置的方法是用制动装置把物体动能转换为摩擦能消耗掉。对于变频器,如果输出频率降低,电动机转速将跟随频率同样降低,这时会产生制动过程,由制动产生的功率将返回到变频器侧,由于二极管不控整流器能量传输不可逆,产生的再生电能传输到直流侧滤波电容上,产生泵升电压;而以GTR、IGBT为代表的全控型器件耐压较低,过高的泵升电压有可能损坏开关器件、电解电容,甚至会破坏电动机的绝缘性能,从而威胁系统安全工作,这就限制了通用变频器的应用范围。因此,必须将这些功率消耗掉,如可以用电阻发热消耗,即能耗制动,如图5-1所示。
在用于提升类负载时,如负载下降,能量(势能)也要返回到变频器(或电源)侧,这种操作方法被称作“再生制动”。如果在负载减速期间或者长期被倒拖时,由电动机侧流到变频器直流母线侧产生的功率如果不通过热消耗的方法消耗掉,而是把能量返回送到变频器电源侧或者通过直流母线并联的方式由其他电动状态的电动机消耗的方法叫做回馈制动。显然,如需要将能量直接返回到电源侧还需要一种特殊的装置,即能量回馈单元,如图5-2所示。
图5-1 能耗制动
图5-2 能量回馈单元
总而言之,为了改善制动能力,不能单纯期望靠增加变频器的容量来解决问题,而必须采用处理再生能量的方法:电阻能耗制动和回馈制动。
小贴士
在以下应用场合,用户必须考虑配套使用制动方式:电动机拖动大惯量负载(如离心机、龙门刨、巷道车、行车的大小车等)并要求急剧减速或停车;电动机拖动位能负载(如电梯,起重机,矿井提升机等);电动机经常处于被拖动状态(如离心机副机、造纸机导纸辊电动机、化纤机械牵伸机等)。以上几类负载的共同特点是,要求电动机不仅运行于电动状态(一、三象限),而且要运行于发电制动状态(二、四象限)。
5.1.2 共用直流母线方式的回馈制动
对于频繁起动、制动,或是四象限运行的电动机而言,如何处理制动过程不仅影响系统的动态响应,而且还有经济效益的问题。于是,回馈制动成为人们讨论的焦点,然而在目前大部分的通用变频器还不能通过单独的一台变频器来实现再生能量的情况下,如何用最简单的办法来实现回馈制动呢?
为解决以上问题,这里介绍了一种共用直流母线方式的再生能量回馈系统,通过这种方式,它可以将制动产生的再生能量进行充分利用,从而起到既节约电能又处理再生电能的功效。
1.工作原理
我们知道通常意义上的异步电动机多传动包括整流桥、直流母线供电回路、若干个逆变器,其中电动机需要的能量是以直流方式通过PWM逆变器输出。在多传动方式下,制动时感生能量就反馈到直流回路。通过直流回路,这部分反馈能量就可以消耗在其他处在电动状态的电动机上,制动要求特别高时,只需要在共用母线上并上一个共用制动单元即可。
图5-3所示是典型的共用直流母线的回馈制动方式,M1处于电动状态,M2经常处于发电状态,三相交流电源380V接到VF1上。
图5-3 共用直流母线的回馈制动方式
处于电动状态的电动机M1上的变频器VF1端,VF2通过共用直流母线方式与VF1的母线相连。在此种方式下,VF2仅作为逆变器使用,M2处于电动时,所需能量由交流电网通过VF1的整流桥获得;M2处于发电时,反馈能量通过直流母线由M2的电动状态消耗。
2.应用范围
共用直流母线的制动方式可应用于造纸机械、印刷机械、离心分离机以及系统驱动等。在这些应用中,有一个共同的特点:即处于发电状态的M2的容量远远小于处于电动状态的M1的容量,而且当M1的电动状态停止时(即变频器VF1待机),M2的发电状态随即转为电动状态。这样,直流母线电压就不会快速升高,系统始终处于比较稳定的状态。
3.制动特点
采用共用直流母线的制动方式,具有以下显著的特点:
1)共用直流母线和共用制动单元,可以大大减少整流器和制动单元的重复配置,结构简单合理,经济可靠。
2)共用直流母线的中间直流电压恒定,电容并联储能容量大。
3)各电动机工作在不同状态下,能量回馈互补,优化了系统的动态特性。
4)提高系统功率因数,降低电网谐波电流,提高系统用电效率。
5.1.3 回馈到交流电网的制动方式
事实上,从变频器内部研究和设计的方面看,应用或寻求哪一种控制策略可以使变频驱动电动机的损耗最小而效率最高?怎样才能使生产机械储存的能量及时高效地回馈到电网?这正是提高效率的两个重要途径。第一个环节是通过变频调速技术及其优化控制技术实现“按需供能”,即在满足生产机械速度、转矩和动态响应要求的前提下,尽量减少变频装置的输入能量;第二个环节是将由生产机械中储存的动能或势能转换而来的电能及时地、高效地“回收”到电网,即通过有源逆变装置将再生能量回馈到交流电网,一方面是节能降耗,另一方面是实现电动机的精确制动,提高电动机的动态性能。这里讨论的就是变频调速系统节能控制的第二个环节——变频调速能量回馈控制技术。在能源资源日趋紧张的今天,这项研究无疑具有十分重要的现实意义。
1.双PWM形式
(1)PWM回馈原理
双PWM控制技术打破了过去变频器的统一结构,采用PWM整流器和PWM逆变器提高了系统功率因数,并且实现了电动机的四象限运行,这给变频器技术增添了新的生机,形成了高质量能量回馈技术的最新发展动态。
图5-4所示为采用PWM整流的电压型变频器的系统构成图。它的主电路是普通的三相桥式电路,在电源输入侧接有滤波电感,以便使输入电流为正弦形。采用直流电压、输入电流双闭环控制。电流控制常采用追踪方式PWM,直流电压的控制采用比例积分(PI)控制。通过追踪式PWM技术,使用滞环比较器,使得实际电流锯齿状地追踪设定电流的变化。设定电流的波形是电源电压波形,为正弦形,其相位和电源电压同相位,同时相位也可以视需要而调整。设定电流的大小由直流电压调节器决定。直流电压调节器的输入为直流电压的误差信号,即直流电压的设定值和检测值之差。采用PI控制可以实现直流电压的无静差。
图5-4 双PWM控制的变频器构成图
(2)双PWM回馈形式一
VACON公司的CXR系列变频器就是采用双PWM的结构,能广泛应用于离心分离机、倾倒装置、起重机、重载传送装置等需要四象限运行的场合,如图5-5所示为CXR配置方案和波形图。
VACON CXR专为需要连续制动的场合开发。CXR产生的再生能量是无谐波的,可以被回馈给电源。它可以有效地补偿电源的功率因数。VACON CXR由两个同样(尺寸)的单元CXI组成,其中一个连接到电动机,另一个通过滤波器连接到电源。VACON CXI是一种以CX为基础的直流供电的PWM逆变器,它不包含整流桥。滤波器为LCL形成。两个CXI单元的直流回路相连。控制电动机的单元与VACON CX相同,其功能是:相同的控制面板、I/O连接和电动机控制。
图5-5 VACONCXR配置方案和波形图
(3)双PWM回馈形式二
为了解决电动机处于再生发电状态产生的再生能量,ABB、西门子公司已经推出了电动机四象限运行的双PWM型电压源交-直-交变频器。图5-6所示为ABB公司的ACS811系列四象限变频器示意图。
图5-6 ACS811系列四象限变频器结构图
2.能量回馈单元
能量回馈单元的作用,就是取代原有的能耗电阻式制动单元,消除发热源,改善现场电气环境,可减少高温对控制系统等部件的不良影响,延长了生产设备的使用寿命。同时由于能量回馈单元,能有效地将变频器电容中储存的电能回送给交流电网,供周边其他用电设备使用,可节约生产用电,一般节电率可达20%~40%。
能量回馈单元已经有非常成熟的产品,如安川公司的VS-656RC5、日本富士公司的RHR系列和FRENIC系列电源再生单元,它把有源逆变单元从变频器中分离出来,直接作为变频器的一个外围装置,可并联到变频器的直流侧,将再生能量回馈到电网中。
能量回馈单元是带有再生功能和制动功能的能量回馈单元,与变频器配合使用,可以发挥出超群的节能效果。与制动电阻单元相比,VS-656RC5不仅节省空间,而且其制动效果更加明显。VS-656RC5的典型应用是应用在起重机、升降机、电梯、离心机、卷绕机等大功率反馈负载。
能量反馈单元具有如下特点:
1)降低运行成本,包括减少电能损耗、提高功率因数、改善电网运行质量等。
2)提高制动能力,如果以传统的标准制动电阻器与变频器的组合,制动转矩大约为120%额定转矩/10s,10%ED;而VS-656RC5与变频器的组合,制动转矩则提高到150%额定转矩/30s或者100%额定转矩/min(25%ED)或者80%额定转矩/连续再生。
能量回馈单元接线如图5-7所示。
图5-7 能量回馈单元接线
图5-6中,电抗器L1的作用是用于电源协调,而电抗器L2的作用则是用于电流抑制。当电动机处于电动状态时,电动功率方向是从三相电源经变频器的整流桥流出;当电动机处于发电状态时,发电功率方向则是从变频器的中间回路经能量回馈单元流向三相电源。
5.1.4 能耗制动设计的基本计算公式
能耗制动中涉及制动单元和制动电阻的选配计算方法,包括以下几种:
1.制动转矩TB的计算
假设电动机从现在的运行速度开始制动,在一定的减速时间里,到达新的一个稳定转速,这样的一个制动过程所需的电磁转矩TB可以由以下公式计算:
式中,TB为制动电磁转矩(N·m);GD2M为电动机的转动惯量(N·m2);GD2L为电动机负载侧折算到电动机侧的转动惯量(N·m2);TL为负载阻转矩(N·m);N1为制动前电动机速度(r/min);N2为制动后电动机转速(r/min);ts为减速时间(s)。
一般情况下,在进行电动机制动时,电动机内部存在损耗,折合成制动转矩大约为电动机额定转矩的20%,因此若所计算出的制动电磁转矩小于20%的电动机额定转矩,则表明无需外接制动装置。
在能耗制动中,要有足够的制动转矩才能产生需要的制动效果,制动转矩太小,变频器仍然会过电压跳闸。制动转矩越大,制动能力越强,制动性能越好。但是,制动转矩要求越大,设备投资也会越大。在制动转矩进行精确计算出现困难的时候,我们还可以进行估算来满足工程要求。
有这样一些经验值:按100%制动转矩设计,可以满足90%以上的负载;对电梯、提升机、吊车,按100%;开卷和卷取设备,按120%计算;离心机负载为100%;需要急速停车的大惯性负载,可能需要120%的制动转矩;普通惯性负载为80%。在极端的情况下,制动转矩可以设计为150%,此时对制动单元和制动电阻都必须仔细核算,因为此时设备可能工作在极限状态,一旦计算错误可能会损坏变频器本身。超过150%的转矩是没有必要的,因为超过这个数值,变频器本身也工作到了极限,没有增大的余地了。
2.制动电阻的阻值计算
制动电阻的选择必须基于这样一个原则:电动机再生电能必须被电阻完全吸收。
在制动单元工作过程中,直流母线的电压升降取决于常数RC,R为制动电阻的阻值,C为变频器的电解电容的容量。由充放电曲线我们知道,RC越小,母线电压的放电速度越快,在C保持一定(变频器型号确定)的情况下,R越小,母线电压的放电速度越快。由以下公式可以求出制动电阻的阻值(Ω):
式中,UC为制动单元动作电压值(V),取值可以参照本书相关内容(通常可以取710V);TM为电动机额定转矩(N·m)。
这里,设定N2为0,这样该阻值就能满足电动机各种减速状况的要求。
3.制动单元的选择
在进行制动单元的选择时,制动单元工作时流过开关管的最大瞬时电流要小于该器件的额定电流是选择的唯一依据,通过计算出最大电流值,就可以选择合适的制动单元,计算公式如下:
式中,UC为制动单元直流母线电压值(V),在交流380V进线电源时取800V;RB为制动电阻阻值(Ω);IC为制动电流瞬时值(A)。
一般变频器的硬件过电压保护值为760V,考虑其动作的滞后,将其适当加大,但不会超过800V,因此在计算IC时适当加大了UC。
4.制动电阻的标称功率
由于制动电阻为短时工作制,即每次通电时间很短,在通电期间,电阻温升远远达不到稳定温升,但瞬时功率很高;每次通电后的间歇时间较长,在该段时间内其温度在不断下降,如此循环往复,最终电阻达到一定的稳定温升,一般有80~100℃。因此根据电阻的特性和技术指标,我们知道电阻的标称功率(即额定功率)将小于通电时的消耗功率(W),一般可以由下式求得:
PR=aPSED%(5-4)
式中,PR为制动电阻的标称功率或额定功率(W);PS为制动期间的平均消耗功率(W);ED%为制动使用率,这里选择10%;a为制动电阻降额系数,一般选1.5~2,该值可以由电阻的降额曲线查得。
PS(W)可由以下公式求得:
这里必须指出,制动使用率是根据负载的实际情况选定的,不同的工艺条件,ED%就不一样。图5-8为制动使用率的示意。
图5-8 制动使用率的示意
这里以典型的升速、保持、降速为一个过程,从前一次减速制动到现在的减速制动为一个周期Tc,减速时间即制动时间为Tb,则制动使用率就是由以下公式计算:
一般而言,ED%取值根据负载的实际制动特性,当然也可以由下面的经验值进行估算:电梯ED%=(10~15)%;油田磕头机ED%=(10~20)%;开卷和卷取ED%=(50~60)%(最好按系统设计指标核算);离心机ED%=(5~20)%;下放高度超过100m的吊车ED%=(20~40)%;偶然制动的负载ED%=5%;其他ED%=10%。
以上所讲的都是电动机处于重复减速的周期制动情况,如果属于非重复减速,其制动电阻的额定功率选择是不同的。另外,如果强迫风冷代替自然冷却,电阻的额定功率可以进一步减小。总之一句话,制动电阻的额定功率的计算基准是:电动机再生电能必须能被电阻完全吸收并变为热能释放。
小贴士
确定了阻值和功率就可以基本确定变频器制动电阻的参数,同时在制作方式上应采用双线并绕的无感电阻,当然也可用普通的箱式电阻,但需在电阻两端并接一只续流二极管,可使用快恢复二极管,耐压在1000V以上。
5.1.5 能耗制动的基本应用方案
能耗制动的基本应用就是变频器、制动单元和制动电阻,且是一一对应的。由于制动单元一般具有通用性,制动电阻又可以功率和阻值自由选配,所以一对一的单机应用型能耗制动方案对品牌并无特殊要求。
能耗制动的基本应用方案一般有以下三种:
1.无保护型
图5-9所示就是适用于用户选用的普通制动电阻。只要确保制动电阻的功率和散热条件良好,并不至于发生火灾隐患的情况下,就可以选用无保护型接线。
图5-9中,制动单元的端子说明如下:P为直流母线正端,N为直流母线负端,可以输入的电压规格为DC600V/40A;PB为制动电阻的一端,另外一端为P,接输出制动电阻;G为制动单元接地;TA/TB/TC为故障继电器的公共点、常闭触点和常开触点,可以接交流220V/10A或直流30V/1A以下的控制电路。
图5-9 无保护型制动单元配线
2.接触器保护型
图5-10所示的接线就是通过进线接触器来保证变频器与制动单元的电气安全,也就是说当制动单元发生故障(TA/TB动作)或者制动电阻热保护(TH1/TH2动作),立即切断接触器KM,变频器和制动单元就处于安全保护状态。
图5-10 保护型制动单元配线
采用接触器保护型的接线方式必须确保制动单元的动作触点和制动电阻的热触点处于有效的状态内,否则容易导致接触器不动作或频繁动作,反而造成系统损坏。
图5-11 控制端子保护型制动单元配线
3.控制端子保护型
图5-11所示的接线就是通过定义控制端子为变频器的保护功能时封锁变频器的电压输出,也就是说当制动单元发生故障(TA/TB动作)或者制动电阻热保护(TH1/TH2动作),变频器的控制端子X1就处于有效接通的状态,变频器就认为外部设备故障,显示故障报警代码并停止输出。这种功能是利用变频器特有的对输入外部设备的故障监视功能。
4.能耗制动的扩充应用方案
由于制动单元的规格并不是以电动机的规格为基础,而是按照制动时的电流来选配,因此制动单元的型号相对较少,只有几种。如果单个的制动单元并不能完全解决制动问题时,就可以采用扩充应用方案,也就是制动单元并联的方案。
这里以某制动单元AMB-G7B-C03为例开展多单元并联方案,该制动单元都有主/从控制单元设置,当一台制动单元运行时,把开关选择为主控制;当采用扩充应用方案时,即多台制动单元并联运行,优先选取其中一台作为主控制,其余的作为从控制,如图5-12所示。
图5-12 制动单元多单元并联
图5-12中可以看到,当多台制动单元并行运行时,控制单元1作为主控单元,控制单元2、3作为从控单元,制动电阻单元的过热保护接线,控制端子M+(输出控制正信号)、S+(输入控制正信号)和M-(输出控制负信号)、S-(输入控制负信号)之间的导线长度不得超过1m,并行连接的制动单元总数不得超过10。