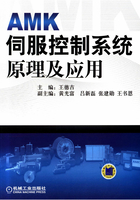
1.3 伺服系统的发展趋势
从当前伺服驱动产品的应用来看,交流伺服电动机和交流伺服控制系统逐渐成为主导产品,数字化交流伺服系统的应用越来越广,用户对伺服驱动技术的要求也越来越高。在实际应用中,精度更高、速度更快、使用更方便的交流伺服产品已经成为主流产品。总的来说,伺服系统的发展趋势可以概括为以下几个方面。
1.交流化
伺服技术将继续迅速地由直流(DC)伺服系统转向交流(AC)伺服系统。从目前国际市场的情况看,几乎所有的新产品都是AC伺服系统。在工业发达国家,AC伺服电动机的市场占有率已经超过80%。在国内生产AC伺服电动机的厂家也越来越多,正在逐步地超过生产DC伺服电动机的厂家。可以预见,在不远的将来,除了在某些微型电动机领域,AC伺服电动机将完全取代DC伺服电动机。
2.全数字化
采用新型高速微处理器和专用数字信号处理器的伺服控制单元将全面代替以模拟电子器件为主的伺服控制单元,从而实现完全数字化的伺服系统。全数字化的实现,将原有的硬件伺服控制变成了软件伺服控制,从而使在伺服系统中应用现代控制理论的先进算法(如最优控制、人工智能、模糊控制、神经元网络等)成为可能。
3.采用新型电力电子半导体器件目前,伺服控制系统的输出器件越来越多地采用开关频率很高的新型功率半导体器件,主要有大功率晶体管(GTR)、金属氧化物半导体场效应晶体管(MOSFET)和绝缘栅双极型晶体管(IGBT)等。这些先进器件的应用显著地降低了伺服单元输出回路的功耗,提高了系统的响应速度,降低了运行噪声。尤其值得一提的是,最新型的伺服控制系统已经开始使用一种把控制电路功能和大功率电子开关器件集成在一起的新型模块,称为智能控制功率模块(Intelligent Power Modules,IPM)。这种器件将输入隔离、能耗制动、过温、过电压、过电流保护及故障诊断等功能全部集成于一个不大的模块之中。其输入逻辑电平与TTL信号完全兼容,与微处理器的输出可以直接接口。它的应用显著地简化了伺服单元的设计,并实现了伺服系统的小型化和微型化。
4.高度集成化
新的伺服系统产品改变了将伺服系统划分为速度伺服单元与位置伺服单元两个模块的做法,代之以单一的、高度集成化、多功能的控制单元。同一个控制单元,只要通过软件设置系统参数,就可以改变其性能,既可以使用电动机本身配置的传感器构成半闭环调节系统,又可以通过接口与外部的位置或速度或力矩传感器构成高精度的全闭环调节系统。高度的集成化还显著地缩小了整个控制系统的体积,使得伺服系统的安装与调试工作都得到了简化。
5.智能化
智能化是当前一切工业控制设备的流行趋势,伺服驱动系统作为一种高级的工业控制装置当然也不例外。最新数字化的伺服控制单元通常都设计为智能型产品,它们的智能化特点表现在以下几个方面:首先它们都具有参数记忆功能,系统的所有运行参数都可以通过人机对话的方式由软件来设置,保存在伺服单元内部,通过通信接口,这些参数甚至可以在运行途中由上位计算机加以修改,应用起来十分方便;其次它们都具有故障自诊断与分析功能,无论什么时候,只要系统出现故障,就会将故障的类型以及可能引起故障的原因通过用户界面清楚地显示出来,这就降低了维修与调试的复杂性。除以上特点之外,有的伺服系统还具有参数自整定的功能。众所周知,闭环调节系统的参数整定是保证系统性能指标的重要环节,也是需要耗费较多时间与精力的工作。带有自整定功能的伺服单元可以通过几次试运行,自动将系统的参数整定出来,并自动实现其最优化。对于使用伺服单元的用户来说,这是新型伺服系统最具吸引力的特点之一。
6.模块化和网络化
在国外,以工业局域网技术为基础的工厂自动化(Factory Automation,FA)工程技术在最近十年得到了长足的发展,并显示出良好的发展势头。为适应这一发展趋势,最新的伺服系统都配置了标准的串行通信接口(如RS-232C或RS-422接口等)和专用的局域网接口。这些接口的设置,显著地增强了伺服单元与其他控制设备间的互联能力,从而与CNC系统间的连接也由此变得十分简单,只需要一根电缆或光缆,就可以将数台,甚至数十台伺服单元与上位计算机连接成为整个数控系统。也可以通过串行接口,与可编程序控制器(Programmable Logic Contrller,PLC)的数控模块相连。
综上所述,伺服系统将向两个方向发展。一个是满足一般工业应用要求,对性能指标要求不高的应用场合,追求低成本、少维护、使用简单等特点的驱动产品,如变频电动机、变频器等;另一个就是代表着伺服系统发展水平的主导产品——伺服电动机、伺服控制器,追求高性能、高速度、数字化、智能型、网络化的驱动控制,以满足用户较高的应用要求。