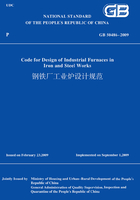
3.2 Structural Steel,Bar and Wire Rod Reheating Furnace
3.2.1 Furnace type selection and main structure design should be in conformity with the following.
1 For reheating of billets for large and medium-sized structural steel rolling mill,walking-beam type reheating furnace with upper and lower heating section should be selected.
2 For the heating of small-sized billets with thickness equal or less than 130mm,walking-bottom type furnace should be adopted,while walking-beam type reheating furnace with upper and lower heating section should be applied for heating of big-sized billets with thickness more than 130mm.
3 Reheating furnaces of medium and small-sized structural steel rolling mill to process common carbon structural steel can be of pusher-type,and should be of walking-beam type while they are used to heat high quality steel.
4 For reheating of stainless steel and decarburized-easily steel,walking-beam type reheating furnace should be selected.
5 Bar and wire rod walking-beam type reheating furnace should adopt side charging and side discharging by cantilever roll table inside the furnace.A hydraulic pusher can be equipped at charging side。
6 Some measures against bend of billets after their entry into the furnace should be taken when bar and wire rod walking-beam type reheating furnace is used to heat cold billets.
7 A new bar and wire rod pusher-type reheating furnace should be designed with shorter billets discharging area for the purpose of side discharging by pusher.It can be designed with no water-cooled billet discharge channel.
8 Walking-beam type reheating furnace for structural steel rolling to be used to heat large billets can adopt end charging by pusher and charger and end discharging by billet withdrawal equipment.
3.2.2 Reheating furnace for high speed wire rod mill or continuous bar mill is better to be provided in one workshop.
3.2.3 Furnace hearth intensity should be economical and reasonable.For a new furnace,it should be in conformity with Table 3.2.3 below.
Table 3.2.3 The design data of furnace hearth intensity

Notes:1 Furnace hearth intensity in the table is applicable for gas fired furnace to heat cold common carbon steel up to the discharging temperature at 1200℃.
2 Furnace hearth intensity in the table isn't applicable for the furnace characterized with overall hot charging or regenerative combustion.
3.2.4 Thermal load supplied for the furnace shall meet the following requirements.
1 For the furnace characterized by hot charging ratio of 100% or more than 90%,thermal load supplied for one furnace should correspond to the heat quantity needed by reference billet with lower hot charging temperature.
2 The total flow rate of energy sources(fuel,etc.)should be calculated on the basis of simultaneity utility(productivity)factor when several furnaces are in operation simultaneously.
3 Thermal load of the furnace with several heating sections can be designed 1.2-1.3 times as much as its rated heat supply capacity.
3.2.5 Combustion devices should be selected as per the following requirements.
1 Select appropriate combustion devices on the basis of furnace type and dimension,heating technology,fuel type,thermal load and environmental requirements.
2 For large gas fired reheating furnace used to heat billets with length more than 10.0m,burners should be of flame adjustable type or equipped with pulse control when they are mounted at the side wall of the furnace.
3.2.6 Furnace mechanical equipments should meet the following requirements.
1 There should be corresponding equipments operated in the form of interlocked logic for billets charging & discharging and moving in the reheating furnace.
2 Hydraulically driven walking mechanism of double-layer frame,double-layer wheel structure and with centering & guiding devices shall be adopted for structural steel,bar and wire rod walking-beam type reheating furnace.
3 There should be billet locating devices at the charging side of walking type reheating furnace.
3.2.7 The design of furnace brick lining should comply with the following provisions:
1 Furnace brick lining materials should be selected on the basis of thermal insulation effect,service life,economy and rationality apart from premises of meeting service performance like usage temperature and load bearing capacity.
2 Some effective heat insulating measures must be taken for each part of the furnace liner and composite insulating body made of different materials shall be applied based on different interface temperature.
3 Anchor bricks should be set up for furnace roof and wall lining when they are integrated masonry structure made of refractory castables or plastic material.The spacing of the roof anchor bricks should be 300-400mm,and that of the wall anchor bricks should be 450-600mm.
4 Some heat-resistant thrust plates should be set up for the furnace sloping roof which is casted by refractory castables or plastic materials on condition that there is greater thrust;vertical wall with height more than 3m of lower heating section can also be provided with heat-resistant thrust plate.
5 Discharging channel or discharging area of side discharging furnace should be laid with electromelting brick or refractory brick,or other materials with resistance against high-temperature,friction,scale,rapid cooling and heating.
6 The length and width of refractory brick lining should be a multiple of 116mm,and the height should be a multiple of 68mm.The length and width of common brick lining should be a multiple of 120mm,and the height should be a multiple of 60mm.