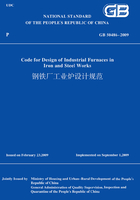
3.7 Cooled Parts in Reheating Furnace
3.7.1 Cooled parts in reheating furnace should satisfy the following requirements:
1 Water-cooled parts in reheating furnace shall be reduced or avoided;when water-cooled parts can not be dispensed with,the surface of water-cooled parts should not be directly exposed in the reheating furnace.
2 Design of water-cooled part should be easy for water adjustment,operation,inspection,disassembling and safe in operation.
3 Structural design of water-cooled part should be that cooling water must fill up the space where the cooled part resides,and that a certain part of drain pipe must be higher than the water cooled part.
4 Water governor valve should be installed on open circuit water cooled part;no draw off valve should be installed on the drain pipe,or installed after the spool drilled.
5 Safety distance between walking beam or other ancillary parts on it and fixed part should not be less than 50mm.
6 Water drainage point shall be set at the lowest part of water cooled parts and pipeline system.
7 Cooling water should enter from the bottom of water-cooled part and be drained from the top;water cooling system for the same kind of water-cooled parts can be connected in series when the cooling water pressure,temperature and service conditions allow.
8 T.O.P.pressure of water supply main of water cooling system should be based on water cooling system resistance and water supply condition of plant.T.O.P pressure for reheating furnace water supply should not be less than 0.2MPa.When closed circuit water circulating system is adopted,supply-water pressure should be increased on the basis of return water requirements.
9 Industrial clean recirculating water shall be adopted for water tubes and water-cooled parts in reheating furnace,and total hardness of cooling water should be no greater than 150mg/L(CaCO3),inlet temperature should be less than 35℃,outlet calculation temperature should be less than 50℃,and evapouration cooling system should adopt soft water.
10 Water-cooled parts in reheating furnace must be provided with thermal insulation measures,hearth water pipe(or water beam)must be wrapped,which may adopt double layer insulating structure with anchor.
3.7.2 Hearth water cooling pipe design for pusher type reheating furnace should comply with the following:
1 Optimization shall be done for hearth water cooling pipe design by adopting rational distance of lengthways pipe and transverse pipe and applying counter-moment on the both sides of T type column or transverse pipe.
2 Arearatio value between water cooling pipe and furnace hearth shall be maintained at 0.20-0.30 for miniature reheating furnace,0.30-0.45 for medium reheating furnace,and less than 0.55 for steel ingot reheating furnace.
3 Tensile strength can be the following for hearth pipe calculation.
1)No higher than or equal to 140N/mm2 for water cooling type.
2)No higher than or equal to 140N/mm2 for evapouration cooling type.
Note:Flexivity between alternate supports should not be greater than 1/500.
4 Hearth pipes shall be made of hot rolled boiler pipes with wall thickness no less than 10mm,and material 20# quality carbon steel.
5 Transverse water pipe must be made of the same steel pipe;lengthways water pipe should also reduce the number of welding seam.
3.7.3 Longitudinal beams layout for walking beam reheating furnace should satisfy with the following provisions:
1 The number of longitudinal beam and supporting column should be reduced under the premises of smooth billet movement in furnace.
2 Longitudinal beam in billet discharging zone can adopt staggered skids and staggered beams.
3 Billet layout and jibarm length for wire and bar reheating furnace should be according to the third paragraph of article 3.3.3 of the current code.
3.7.4 Structure of walking beam and fixed beam should comply with the following provisions:
1 Design of longitudinal water beam for walking beam reheating furnace should be of twin-pipe structure.
2 When the length of single longitudinal water beam is not greater than 12mm,the supporting column should be pre-inclined in design,with inclination value being calculated according to different coolingdown method.
3 The length of single longitudinal water beam should not be greater than 25mm;otherwise design for it shall be in sections.
4 In calculating longitudinal water beam strength,permissible stress value should be 100 N/mm2.
5 Distance for fixed supporting column should be 2-4m.
6 Longitudinal water beams and supporting columns for reheating furnaces with steam pressure of evaporation cooling system no greater than 2.5MPa can be made from thick wall seamless steel pipe made of 20# quality carbon steel.
3.7.5 Spacer design for walking beam reheating furnace should comply with the following provisions:
1 Spacer shape and connection method with longitudinal beam should be based on furnace type,shape and size of billet,black spot requirement,spacer material type and price,and so on.
2 The strip welded spacer size can be 150-250mm(length)×25-50mm(width)×60-120mm(height);and the strip rider spacer size can be 100-120mm(length)×40-100mm(width)×60-150mm(height).
3 Average billet/slab bearing pressure on spacer surface for fixed beam or walking beam should be 1.0-2.0MPa when the reheating furnace is used for reheating carbon steel.
4 Spacer in low-temperature zone can adopt welding type semi-hot slide-way;high-temperature zone can adopt rider hot skid rail,material for which should be appropriate high-temperature alloy according to furnace temperature.
3.7.6 The longitudinal beam welding of walking beam reheating furnace should satisfy he following provisions:
1 Factory-length of longitudinal beam parts should be 8-12m,combined welding shall be done after they have been transported to site;forms and welding requirements of various weld seams must be marked clearly.
2 Thick wall pipe welding for longitudinal beam should use the U-shaped back sealing weld,and argon-arc welding as backing welding.After welding,X ray film examination shall be conducted in accordance with current national standard"metal melting welding joint radiography"GB/T 3323,with each welding seam should be filmed no less than two times to make sure 30% of welding seams should be gradeⅠwelding seams and the rest should be gradeⅡ.