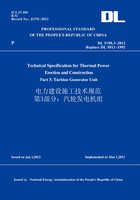
6 Regulation and Protection Device and Oil System
6.1 General Provisions
6.1.1 This Chapter is applicable to works of turbine main oil pump,governor mechanism,steam valve and driving mechanism,protecting devices,lubricating oil system,hydrogen-cooled generator sealing oil system,oil purifier and electro-hydraulic regulation and protection system.
6.1.2 Except for equipment that must not be disassembled as specified by manufacturer,equipment in oil system shall be disassembled to check their cleanness,and unclean parts and components shall be thoroughly cleaned,to ensure cleanness inside the system.
6.1.3 The disassembling,inspection and assembling of regulation and protection device and oil system parts shall comply with the following provisions in addition to the relevant provision sin 3.3 hereof:
1 The disassembling inspection and assembling of regulation and protection components shall be performed in a dedicated clean area.
2 The disassembling,safe-keeping and assembling of main components shall be under the charge by designated personnel.
3 For adjustable main parts such as nuts,screws,linkages,springs and butterfly valves,the original data of their dimensions and gaps shall be measured and recorded before disassembling,and assembling shall be done on these bases.When any disassembling record does not agree with ex-works records or requirements on drawings,it shall be confirmed by manufacturer and be adjusted again,and a final assembling record shall be made.For assembling,the steel stamp marks of all parts shall agree with those at disassembling.
4 Precision parts shall be cleaned with environmental protection detergent not corrosive to equipment,and be kept properly after being cleaned.
5 Parts shall be checked against drawings,and the number of holes and passages,positions and sections shall be correct and through.
6 Springs shall be free of crack,rust,damage or deformation,and the ends shall be flat.
7 At the time of assembling,sliding parts shall be flexible in movement over the full travel,and the pin shafts of connecting parts shall not become loose or jammed.Rotating parts such as rolling bearings and pump shafts shall be flexible when turned.
8 Pins and dowels,securing washers,split pins,lock nuts and screws for connection shall be set to place and locked.Split pins shall be free of crack and securing washers shall have no crack after edge curling.
9 The joint surfaces,sliding faces,engaged faces,connection joints,bearings and bolts in the oil flowing section shall be coated with lubricating oil.
10 The joint surfaces and sealing surfaces shall be in good contact,free of through groove and trace,the threaded connections shall be tight without leakage,and correct packing and coating materials shall be selected,refer to Appendix C.
11 Parts not to be assembled for a time being shall be protected against damage and pollution and sealed up for storage.
6.1.4 The construction of oil system piping shall comply with the following provisions in addition to those in Part 5"Piping and system"of this specification:
1 Flange connection should not be used for oil piping,and welds shall be minimized,before welding of piping,frequent inspection shall be made,to ensure the inside of piping is clean.
2 Argon arc welding shall be used for oil pipes up to DN50mm,and argon arc backing welding shall be used for all oil pipes.The groove types,weld gap and welding inspection for weld seams shall be in accordancewith"Codeofweldingforfossilfuelpowerplants"DL/T869and"Code of welding for conventional island in nuclear power plants"DL/T 1118.
3 Oil inlet pipes shall have a sloping of 1/1000 towards the oil pump,and the sloping of oil return pipe towards the oil tank shall be no less than 5/1000.
4 Regulating oil pipes shall be free of blind section or humping section in the middle.
5 Expansion spacing shall be provided for oil pipes from foundation,equipment,piping or other facilities,to ensure that thermal expansion of turbine and oil pipes themselves will not be affected in operation;small oil pipes connected with equipment parts and pipes with expansion displacement shall comply with provisions for expansion compensation.
6 Outer wall of oil pipes shall have a net spacing no less than 150mm from the steam pipes insulation layer outer surface,and thermal insulation plate shall be added if this spacing cannot be satisfied.Oil pipes with static oil during operation shall have a net spacing no less than 200mm,and flanges and flexible connectors should not be provided for oil pipes close to main steam pipes and valves.
7 Oil pipe connectors must not carry the loads of pipes and valves.
8 Male and female face flanges shall be used for oil pipes,dense packing materials resisting to oil and heat shall be used at joint surfaces,refer to Appendix C.Gaskets shall be clean and flat,free of fold trace,with inner diameter 2mm-3mm larger than the flange inner diameter,and the outer diameter shall be close to the dimensions of flange joint surfaces outer edge.
9 Oil flange connections must not be aligned with force,and the flange bolts shall be tightened symmetrically and homogeneously.
10 In installing pipes for oil system,enclosing provision shall be made for oil pipe openings.
11 For oil casing pipes pre-fabricated and assembled in factory,the cleanness of inside of parts shall be checked before installation,to ensure the inside is clean and free of sundries,and the supports and clamps inside the sleeve shall be checked for firm fixing.
12 Insulation shall be provided for turbo-generator parts requiring isolation from shaft current when they are connected with oil pipe,and before assembling,the insulation shall be checked for freedom of damage and correct installation.To facilitate insulation measurement,double insulated flanges can be fitted.
13 For oil pipes in stainless steel,stainless steel shims or non-metal gaskets with chlorine ion content not exceeding 500ppm shall be used as isolation where the pipe wall is in contact with ferrite supports and hangers.
14 Oil pipes connected with unions shall comply with the following provisions:
1)Welded lock nut unions must not be used.
2)Spherical lock nut unions must be subject to coloring inspection and the contact shall be tight.
3)Flat lock nut unions shall be fitted with annealed red copper shim,at a thickness of preferably 1.0mm.
4)Pipe unions shall be in a free state,and there shall be surplus threads for lock nut after connection.
15 The installation direction of expansion joint shall be correct.
6.1.5 Inspection and installation of oil pipe valves shall comply with the following provisions:
1 Valves shall be made of steel with external screw nut,no reverse valve shall be used,and the opening and closing directions shall be clearly marked.
2 The valve stem shall be in horizontal or downward arrangement.
3 Two manual valves shall be provided for emergency oil drain pipe.The emergency drain valve shall have a distance greater than 5m from the oil tank,and there shall be two or more passages.The hand wheel of emergency oil drain valve shall be provided with a glass protection hood with clear mark,and it must not be locked.
4 For special valves such as pressure reducing valve,oil overflow valve,over pressure valve and check valve,the gap,travel and dimensions of parts shall be checked according to the requirements of manufacturer technical documents and recorded,and leakage test shall be performed for valves.
5 Teflon bowl sealing gasket should be used for stem packing.
6.1.6 Inner wall of oil pipes must be cleaned thoroughly,and must be free of welding slag,rusty dirt,fiber or moisture,no drilling,gas cutting or welding shall be done on any oil pipe after cleaning or enclosing,otherwise it shall be cleaned,checked and enclosed again.
6.1.7 The materials and fabrication of piping and fittings of oil system pipes shall comply with the following provisions:
1 Hot pressed bends shall be used for large diameter pipes,cold bending pipes shall be used for pipes up to DN50mm,and pipe must not be hot bent by filling sand.
2 Reducers shall be forged or moulded types,and large diameter reducers can be welded with steel plate;reducers fabricated on-site with sliding out process must not be used.
3 Tees up to DN25mm should be machine made,and for prepared tees,sundries such as welding slag,overlap and flux coating shall be removed.
4 Seamless steel pipes shall be used for pressure oil pipes.
5 Unions should not be used for connection unless it is necessary for connection with equipment.