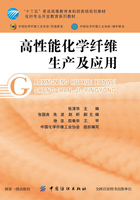
第三节 原丝碳化技术
一、PAN基原丝的碳化
PAN原丝的碳化过程主要包括放丝、预氧化、低温碳化、高温碳化、表面处理、上浆烘干、收丝卷绕等工序,基本工艺流程如图2-17所示。

图2-17 聚丙烯腈基碳纤维生产工艺流程示意图
1.预氧化
为了使聚丙烯腈线形大分子链转化为非塑性的耐热梯形结构,从而使纤维在高温下碳化不熔不燃,继续保持纤维形态,在原丝丝束碳化前要对其进行预氧化处理[39]。预氧化过程在整个碳纤维制备流程中耗时最长,预氧化时间一般为40~120min,碳化时间为几分钟到十几分钟,而石墨化时间则以秒计算,预氧化过程是决定碳纤维生产效率的关键环节[40]。
PAN原丝的预氧化,一般在180~300℃的空气中进行[41],随着温度的逐渐升高,原丝颜色由白色开始转变成淡黄色、黄色、棕色、棕黑和黑色。此过程中发生的化学反应相当复杂,包括氧化脱氮、脱氢环化和氰基环化反应等,经过预氧化后,PAN原丝中氢含量比例降低、氧含量上升,氮元素比例基本不变。
预氧化反应的原理是气固双扩散过程,氧由表及里向纤维芯部扩散,同时反应副产物由里向外扩散。预氧化炉内的流动空气作用有两个,一是提供预氧化反应所需要的氧,二是把反应热和反应副产物及时带出,促进双扩散过程向纤维内部发展。预氧化程度是影响碳纤维质量的重要因素,预氧化程度不足(氧含量<6%)即环化程度低,在碳化过程中释放出的分解产物多,将使碳纤维强度降低;预氧化程度过高(氧含量>12%),在梯形结构中结合的氧较多,在高温碳化时释放的热解产物多(如CO、CO2、H2O),将使碳纤维强度下降、碳率降低,最佳预氧化程度是生产工艺的关键控制指标[39]。
预氧化过程中的主要工艺参数包括:预氧化温度及其分布梯度、预氧化时间、张力牵伸等。预氧化工艺是否恰当决定了后续碳化过程的稳定性,甚至严重影响最终碳纤维的力学性能[40]。
预氧化过程在预氧化炉中完成,根据结构不同,预氧化炉有直线式炉、热风循环式炉、外热式预氧化炉、流化床式预氧化炉、导流板式炉等不同炉型[42]。
图2-18为直线式预氧化炉结构示意图,它由炉体、气室、走丝室、布风板等部件组成。经过滤的空气进入气室后被加热,热空气经布风板进入走丝室,及时将原丝在预氧化反应中放出的大量反应热带走并直接排出炉外。这种炉型具有结构简单、造价低的特点,但占地面积较大,走丝速度慢,能耗较高。

图2-18 直线式预氧化炉
近年来具有热风循环系统的预氧化炉在工业生产中得到大量应用。英国RK公司的热风循环式预氧化炉分为四个单元,图2-19是其中一个单元的结构示意图。该炉可实现热风循环使用,从预氧炉出来的含有分解及反应产物的热空气,一部分经焚化炉催化分解后放空,另一部分再循环到炉内,同时从进气口再补充一部分新鲜空气进入炉内。排放一部分,循环一部分,补充一部分,既可避免大量热能被排放气体带走,又可避免多次循环而使分解产物富集,对纤维造成污染[43]。

图2-19 热风循环式预氧化炉
目前国内外大型预氧化炉主要采用的是热风循环式结构,即将热风多次循环利用,达到充分利用余热的目的,该炉型节能效果很好,炉子结构如图2-20所示,炉内分层设置2~6个炉膛,每一个炉膛均连接一个热风炉,通过炉膛两侧设置的热风气流分布管送风,炉顶设置有空气预热管、废弃排放口及空气吹入口,纤维通过炉膛间的走丝狭缝运行。炉体顶部的废气口和进气口通过热交换使这种预氧化炉具有显著的节能降耗效果[44]。
预氧化炉膛内的热风流向可以与纤维平行,也可垂直。当平行流动的速度不太高时,反应热不易瞬时排除;流量太大时,热风耗量大;当垂直流动时,有利于反应热的排除,但平行运行的丝束对热风有阻流作用,且炉外空气易通过炉口进入炉内,使有效反应段减短[43]。
图2-21是装有导流板的预氧化炉,热风气流的流动轨迹是“之”字形,多次穿过纤维束,可有效带走反应热,显著缩短预氧化时间[45]。这种炉体结构的另一个优点是可以减少热风循环量,使热量得到充分利用,热风在这种炉膛内的流向兼备平行与垂直流向的综合优点。但这种预氧化炉的炉体结构较复杂,特别是导流板的凸与凹交替出现,给断丝处理和清理炉腔带来很大不便,仍需进一步完善和改进。

图2-20 外热式预氧化炉

图2-21 装有导流板的预氧化炉
2.碳化
碳化和石墨化是在高纯N2和Ar气保护下进行的固相热解反应。碳化过程伴随着材料的结构变化,原丝经预氧化后转变为耐热梯形结构预氧化丝,经低温碳化和高温碳化后转化为具有乱层石墨结构的碳纤维,随着碳化的进行,非碳原子逐步脱除,碳原子富集再结晶,含碳量高达92%以上。
(1)低温碳化。低温碳化可以使预氧化未反应的PAN进一步环化,分子链间脱水、脱氢交联以及侧链和末端基团热解,并伴有大量气体产物排出。低温碳化的温度区间在300~800℃,形成由低到高温度梯度,使热解过程循序渐进,可控可调。
低温碳化炉一般有五六个温区,内炉膛可用4~8mm耐热、耐蚀不锈钢板加工而成,其截面形状为上拱弧形。这种形状不仅可承受高温条件下不变形,而且上拱弧形可使焦油向两边流动,阻止焦油直接滴下污染纤维,造成断丝和影响连续生产[46]。内炉膛还可以用SiC材料制成,与不锈钢材料相比具有耐腐蚀、使用寿命长的特点,但加工制作较复杂,使用过程中易出现微裂纹。图2-22是国产低温碳化炉结构示意图,主要由炉体、炉膛、气封装置、氮气供给系统、废气排放装置、加热体及牵伸机构组成。

图2-22 低温碳化炉结构示意图
预氧丝经牵伸机构通过炉膛,炉膛下部设保护气体供给系统,氮气进入炉膛后,气流呈纤维运行垂直方向流过,携带碳化分解产物经设在低温端的排气口排出炉外。炉外安装引风机用于排除废气,并通过调节阀控制排风量大小,炉膛内部保持微正压。排出的废气集中收集处理,达标排放。为保证炉内气氛稳定,通入炉膛的氮气一般先进行预热。
(2)高温碳化。在高温碳化阶段,PAN产生芳构化反应,分子链间进行收缩、重排,非碳原子逐渐脱出,碳原子进一步环化和交联,形成具有乱层石墨结构的碳纤维。随着碳化的进行,纤维的拉伸强度和模量逐渐提高,断裂伸长率降低,纤维逐渐转化为脆性材料。
高温碳化温度一般在1000~2000℃,高温碳化炉多用石墨发热体作为热源,用低电压大电流变压器实施调控。在高温碳化过程中的主要副产物是N2,其次是HCN,这是小的碳网平面热缩聚为大的碳网平面的产物,合理的化学收缩是结构转化的必然规律。在此阶段,牵伸调控下的负牵伸是高温碳化的重要工艺参数之一[46]。
生产碳纤维的过程中,牵伸贯穿始终。牵伸有正牵伸(伸长)、零牵伸(定伸长)和负牵伸(收缩)。一般在预氧化工序正牵伸1%~5%或定伸长,需根据PAN原丝性能而定;在低温碳化工序一般为正牵伸,高温碳化工序为负牵伸[46]。
图2-23为高温碳化炉结构示意图,高温碳化炉主要由炉体、炉膛、加热体及气封装置组成。炉膛材料及加热体材料根据碳化炉工作温度确定,对于工作温度为1350℃以下的碳化炉,可选用SiC材料制作炉罐,选用SiC棒电热元件为发热体;对于1450℃以下的碳化炉,可选用刚玉材料炉罐及二硅化钼电热元件;对于1600℃以上碳化炉,必须选用石墨炉膛和石墨发热体。因高温碳化时间少于低温碳化时间,高温碳化炉的长度相应缩短。

图2-23 高温碳化炉结构示意图
3.石墨化
碳纤维经高温碳化后,如要进一步提高其模量,需要在高纯氩气的保护下,在3000℃左右的高温下进行石墨化。石墨化的时间不宜过长,数秒至数十秒即可。石墨化设备和高温热处理技术是影响碳纤维石墨化的关键[47]。在国内外工业上普遍采用的碳纤维石墨化设备多为高温管式石墨化电阻炉。
除此之外,还有一些正在研制中的新型石墨化设备,图2-24所示为直接加热感应石墨化炉,该方法采用高频感应加热的方式使碳纤维直接加热到2500~3000℃,同时给纤维加载一个沿纤维轴向的牵伸张力而进行石墨化处理。整个设备主要包括高频发生器、耦合器、石英反应器和一个差速收放丝机构,借助差速收放丝机构形成牵伸张力预置,由线性电场感应直接使纤维达到工艺温度,完成石墨化处理[47]。

图2-24 直接加热感应石墨化炉
利用等离子体技术进行碳纤维石墨化是一项新的研究领域,日本的村井[47,48]发明了一种碳纤维连续石墨化热处理的装置。整个石墨化装置置于一密闭的真空容器内,通过真空泵进行真空置换,连续排除废气并注入惰性气体氦气和氮气,密闭容器内的碳纤维在3000℃左右的高温下进行连续石墨化处理而形成石墨纤维。但其温度场控制的不稳定且需在真空环境下操作,不便于工业化应用。
美国的Felix等[47,49]的一项发明中介绍了利用微波等离子技术和电磁辐射进行碳纤维碳化和石墨化的技术。碳纤维被置于真空石英管内,放在等离子体和电磁辐射场内,通过等离子体与电磁辐射的耦合,使电磁能被纤维利用,导致大量能量作用于纤维上而使碳纤维发生石墨化;该装置可大幅降低成本,使碳化、石墨化和表面处理一次完成。但其不能进行连续化生产限制了工业化生产推广。
4.碳纤维表面处理
碳纤维在高温惰性气体中碳化处理后,其表面活性、张力降低,与基体树脂的浸润性变差,为改善以上性能,需要对碳纤维进行表面处理。碳纤维表面处理有表面涂层改性法、气相氧化法、液相氧化法、阳极氧化法、等离子体法等[50]。
(1)表面涂层改性法的原理是将某种聚合物涂覆在碳纤维表面,改变复合材料界面层的结构与性能,使界面极性等与基体树脂相适应,以提高界面黏结强度,同时提供一个可消除界面内应力的可塑界面层[50]。
(2)气相氧化法使用的氧化剂有空气、氧气、臭氧等含氧气体。氧化处理后,碳纤维表面积增大,官能基团增多,可以提高复合材料界面的粘接强度和材料的力学性能[51]。
(3)液相氧化法是采用液相介质对碳纤维表面进行氧化的方法。常用的液相介质有浓硝酸、混合酸和强氧化剂等。液相氧化法相比气相氧化法较为温和,一般不使纤维产生过多的起坑和裂解,但是其处理时间较长,与碳纤维生产线匹配难,多用于间歇表面处理[50]。
(4)阳极氧化法,又称电化学氧化表面处理,这种方法大规模生产应用较多。该法就是把碳纤维作为电解池的阳极、石墨作为阴极,在电解水的过程中利用阳极生成的“氧”,氧化碳纤维表面的碳及其氧官能团,将其先氧化成羟基,之后逐步氧化成酮基、羧基和CO2的过程[50]。该工艺要求水的纯度高,此外电极必须是惰性的,不参加电化反应。阳极电解氧化法的典型流程如图2-25所示。

图2-25 阳极电解氧化法的装置图
(5)等离子体法主要是通过等离子体撞击碳纤维表面,从而刻蚀碳纤维表层,使其表面的粗糙度增加,表面积也相应增加。由于等离子体粒子一般具有几到几十电子伏特的能量,使得碳纤维表面发生自由基反应,并引入含氧极性基团。等离子体法还有可能使碳纤维表面微晶晶格遭到破坏,从而减小其微晶尺寸[52]。
5.上浆
碳纤维是一种脆性材料,极易在加工过程中产生毛丝,需要对碳丝表面上浆处理。上浆剂主要有以下几个作用:提高碳纤维的集束性和耐磨性,保护碳纤维表面;提高纤维与树脂的浸润性;改善复合材料的界面性能,提高层间剪切强度。
目前多采用乳液型上浆剂,以一种树脂为主体,配以一定量的乳化剂,少量交联剂,以及为提高界面黏合性的助剂。碳纤维的上浆剂多采用环氧树脂,环氧树脂种类繁多,但作为主上浆剂多采用双酚A环氧树脂,是一种产量大,应用广泛的主流上浆剂。
上浆后的碳纤维要求每根单丝表面均匀上浆而形成薄膜,以满足在后续深加工过程中的集束性、耐磨性、开纤性和扩幅性。同时,上浆后的碳纤维要求具有良好的悬垂值、润湿性和平度等性能。目前碳纤维普遍采用的上浆方法有转移法、浸渍法和喷涂法等,其中浸渍法最为常用。
6.PAN基碳纤维预氧化、碳化控制系统实例[53]
控制系统可采用可编程计算机控制器(PCC)技术,以PP281触摸屏为核心,配以4个PowerLink分站,实现温度、传动、开关量的集中显示与控制。整条生产线由10台预氧炉、1台中温碳化炉、1台高温碳化炉组成,共有55个控温点、30个测温点,牵伸系统采用15台变频器进行调速。系统输入/输出模块采用B&R2003系统模块,其中温度模块采用AT664,数字量输出模块采用DO720,数字量输入模块采用DI439,模拟量输出模块采用AO352。
温度加热采用固态继电器PWM调功方式;变频器采用DO(数字量输出)信号启动,模拟量调速,为提高控制精度,变频器安装编码器模块,在电机侧安装增量式旋转编码器,构成闭环控制。
PP281集触摸屏功能与PLC功能于一体,采用Automation Studio软件,C语言编程,实现温度PID调节控制、变频调速控制、温度/牵伸比的实时显示、气体监测、实时与历史报警记录等功能,界面友好,操作简单。
(1)温度PID控制。由于预氧化设定温度较低(190~280℃),而且预氧化过程中会有放热反应,为避免温度到达设定值时的过冲现象,选择适合的碳纤维预氧化温度控制策略尤为重要,如图2-26所示。

图2-26 预氧炉温度控制策略
预氧炉温度控制采用混合控制策略。温度低于设定值30℃时,采用全功率升温控制策略,当温度在接近设定值30℃以内时,采用高精度PID调节的升温速度控温策略,达到设定值后,转换为单纯的高精度PID调节。采用此种控制策略,既可以根据不同炉子的特性实现快速升温,又可靠保证在预氧化温度达到设定值时,不会出现温度过冲现象[54,55]。
温度的PID控制采用贝加莱的智能PID模块,有着新的积分部分和更好的饱和度,利用PCC分时序、多任务的特点,可同时进行所有控温点的PID控制及PID参数优化,而各区参数的独立性及准确性保证了温度参数的精度,可将其误差控制在1℃的偏差范围内。温度控制及PID参数画面分别如图2-27和图2-28所示。
(2)牵伸控制。牵伸控制采用15台具有矢量控制功能的ABB变频器,闭环控制,PP281通过DO信号控制变频器启停,通过模拟量调速。牵伸控制功能如图2-29所示。

图2-27 温度PID控制功能

图2-28 温度PID参数优化功能

图2-29 牵伸控制功能
(3)气体监测。PP281通过RS485接口与露点仪和微量氧分析仪通讯,可实时监测保护气体中的水分含量和氧含量,并设定最大量程和报警上下限[56],如图2-30所示。
(4)系统设置。系统设置功能可以管理多个用户的密码、保存和提取工艺参数、时间设定以及进行触摸屏校正,如图2-31所示。

图2-30 气体监测功能

图2-31 系统功能
2007年12月该控制系统在某单位成功运行,结果显示该控制系统不仅升温速度快,控温精度高,并且传动平稳可靠,控制灵活,完全满足了碳纤维生产的需求。
7.碳纤维生产辅助系统
(1)丙烯腈精制及回收系统。一般工业用丙烯腈含有阻聚剂或少量杂质,而高性能碳纤维原丝的制备必须配备高纯度的原料,丙烯腈精馏和回收系统是必不可少的装备。以市场采购的丙烯腈为原料,其典型成分组成丙烯腈≥98%、水≤0.5%,微量阻聚剂、微量盐。精馏后的丙烯腈纯度≥99.5%。
为了满足工艺要求,需对丙烯腈进行提纯。原料经进料泵进入精馏塔,中部进料,落入塔釜的物料经立式热虹吸式再沸器加热汽化后上升进入精馏塔,精馏塔里装有高效填料,气液在精馏塔里进行传质交换,进入冷凝器的气体经循环冷冻水实现相变,冷却成为液体进入回流罐,液体物料经控制回流泵,一部分回流回塔,一步法经产品冷却器采出合格产品进入界区外成品储罐。釜底为重组分及少量丙烯腈,经釜液采出泵间歇定时排出。
整个精馏系统中,设备是关键,要求如下:与物料接触材料均采用SUS316L,壳体内壁抛光处理;丙烯腈为高度危害介质,连接法兰均采用凹凸面密封,阀门均采用优质球阀,垫片均采用F4材料,以保证安全;精馏塔采用填料塔,内装表面洁净的金属散堆填料;分布器采用操作弹性大、压降低、分布效果良好的气液收集分布器,精馏塔外壁保温;再沸器采用立式热虹吸式再沸器,壳程循环热水加热;冷凝器卧置成一定倾角安装,物料走壳程,冷冻水走管程;产品冷却器卧置安装,双管程,物料走管程,冷冻水走壳程;回流罐、真空缓冲罐均采用立式椭圆双封头;真空捕集器竖立安装,物料走管程,冷冻水走壳程,用于捕集未凝汽;真空泵采用喷射泵,以保证安全稳定;热水浴配套蒸汽加热,温度可调可控,配套水循环泵系统。
因丙烯腈为高毒化学品,生产和使用丙烯腈者要掌握中毒的急救方法,车间要备有急救药品和氧气呼吸器,生产设备、管线要加强维修,进入容器清理或进行其他操作前必须进行充分通风,使用有效防护用品,并有专人在容器外进行监护,禁止单人在危险地区操作,工作场所严禁进食、吸烟,丙烯腈泄漏时要及时撤离危险区,切断火源,处理人员戴好正压自给式呼吸器,穿化学防护服,收集漏液入密封容器内,用砂土或其他惰性材料吸收残液并转移到安全场所,再用氯漂白液中和残液。若大量泄漏利用围堤收容,然后收集、回收或无害处理后废弃,用大量的清水冲洗,并将冲洗水放入废水系统中。
(2)溶剂回收系统。在碳纤维原丝制备过程中,凝固浴液不断积累,需要回收提纯后继续使用,溶剂回收是一个重要工序。一般而言,回收凝固浴液体中溶剂的浓度(DMSO)在40%左右,水在60%左右,外加微量杂质。回收处理后溶剂指标要达到99.9%。
目前,碳纤维原丝生产大多采用DMSO作为溶剂。其回收一般采用三塔连续负压精馏工艺,塔一主要除去大量的水,塔二除去所有水分和其他前馏分,塔三出产品DMSO,釜底为高沸物。基本物料流程如下:
①将纺丝工序送回的稀溶剂通过进料泵输送,经换热器换热后进入预处理塔中部,塔内物料经再沸器加热后变成蒸汽上升,上升到塔顶的蒸汽经换热器和冷凝器冷凝后进入回流罐,罐内物料经过回流泵输送,一部分物料回流返回预处理塔内,与塔内上升蒸汽进行热质传递,另一部分物料进入水接收罐,塔釜内的物料通过塔釜出料泵进入釜液接收罐。
②将釜液接收罐内的物料通过下级进料泵输送,进入精馏塔中部,塔内物料经再沸器加热后变成蒸汽上升,上升到塔顶的蒸汽经冷凝器冷凝后进入本塔回流罐,罐内物料经过本塔的回流泵输送,一部分物料回流返回精馏塔内,与塔内上升蒸汽进行热质传递,另一部分物料进入前馏罐,塔釜内的物料通过本塔釜出料泵进入本塔釜液接收罐。
③将精馏塔釜液接收罐内的物料通过塔三进料泵输送,进入精馏塔三中部,本塔内物料经再沸器加热后变成蒸汽上升,上升到塔顶的蒸汽经本塔冷凝器冷凝后进入本塔回流罐,罐内物料经过本塔回流泵输送,一部分物料回流返回本精馏塔内,与塔内上升蒸汽进行热质传递,另一部分物料经产品冷却器冷却后,进入产品接收罐,本塔釜内的物料通过溢流进入本塔釜液接收罐,得到成品回收的溶剂。
溶剂回收的主设备包括:预处理塔、原料储罐、釜液接收罐、回流罐、水接收罐、真空缓冲罐、真空泵、换热器、冷凝器等设备,配套真空及输送系统控制系统,实现回收功能。
(3)高纯水制备系统。在碳纤维制备过程中,特别是在原丝制备过程中,大量用到高纯水,如配制凝固浴、初生纤维水洗浴、上浆剂等,水质直接影响碳纤维原丝质量。目前为了制备高纯度稳定水,一般取自来水为水源,经过处理后制备高纯工艺水,水质要求电阻率≥15MΩ/cm。其制水工艺分为预处理系统、反渗透系统、精处理(EDI)系统。在使用过程中,用户需根据管道供水水质选择适当的预过滤保护装置,主要净化功能为降低污泥指数,降低余氯含量,降低水硬度;超纯水系统安装在尽可能洁净的室内,以确保其超纯水不被二次污染。
(4)在碳纤维原丝制备过程中,多个工段需要高纯氮气保护,如丙烯腈存储、聚合反应保护气体;在低温碳化和高温碳化工艺中,需要氮气保护,并且对氮气消耗量大,且纯度要求高,对氧含量和水含量控制苛刻。碳化时,要求氮气纯度氧含量一般≤1mg/kg,水含量要求露点低于-70℃。
在碳纤维制备工程中,为了控制成本和质量,一般采用深冷制氮模式制备高纯氮气。整个流程由空气压缩净化、空气分离、液氮汽化三部分组成。首先,空气经过滤器除去灰尘及杂质后,进入空气压缩机逐级压缩冷却,然后进入预冷系统进行空气降温后进入净化器,空气中的水分、二氧化碳及大部分碳氢化合物等得以清除;其次,净化后的空气进入主热交换器与返流的氮和废气进行热交换后进入精馏塔的底部。经精馏塔分离后顶部得到氮气,这些氮气被冷凝成液氮,另一部分经主换热器回收后作为产品废气排出塔外;精馏塔底部为液态空气,液态空气从塔底抽出经冷却器节流进入主冷凝蒸发器,与氮气换热后成废气,部分进入膨胀机膨胀制冷,膨胀后的废气再返回主热交换器与其余废气汇合后排出塔外。最后,由空分塔出来的液氮进液氮贮槽贮存,汽化后得到高纯氮气产品。
(5)污水处理系统。在碳纤维生产过程中,会产生大量废水,废水中BOD、COD含量较高,需要进行集中处理后才能排放,一般碳纤维工厂水中COD≤600mg/L、BOD≤300mg/L、SS≤250mg/L、氨氮≤300mg/L,经过处理后出水污染物最高浓度要求达到《污水综合排放标准》(GB 8978—1996)二级排放标准。
目前碳纤维生产厂污水处理一般采用“A—O生物脱氮工艺”,实施该工艺时,在进水前端设格栅和调节池,以隔除大尺寸杂质,调节水量和水质;厌氧处理单元设置水解酸化池;好氧处理单元采用传统活性炭污泥法;剩余污泥排入污泥浓缩池消化处置,浓缩污泥利用箱式压滤机脱水外运。在设备运行阶段,一般1~2年清掏一次污泥,每4~5年更换一次过滤材料,以保证污水处理站正常稳定运行。
二、沥青基碳纤维原丝的碳化
1.沥青纤维的不熔化(预氧化)处理
沥青纤维必须通过碳化,充分除去其中的非碳原子,最终保留碳元素所固有的特性;但由于沥青的可溶性和黏性,在刚开始加温时就会黏在一起,不能形成单丝,所以必须先进行预氧化处理。另外,预氧化还可以提高沥青纤维的力学性能,增加炭化前的抗拉强度[57,58]。沥青纤维在氧化过程中分子之间产生了交联,使纤维具有不溶解、不熔融的性能。
2.沥青基碳纤维的碳化和石墨化
不熔化后沥青纤维送到惰性气氛中进行炭化或石墨化处理,以提高最终力学性能。不熔化纤维在低温碳化时,其含氧官能团以CO和CO2脱离,单分子间产生缩聚,在600℃以上时有脱氢、脱甲烷、脱水反应,非碳原子不断脱除,最终纤维的碳含量达到92%以上,碳的固有特性得到展现,单丝的拉伸强度和初始模量增加[57,58]。
三、黏胶基碳纤维原丝的碳化
1.黏胶纤维的后处理
黏胶基碳纤维的制造工艺包括多个环节,即加捻、稳定化浸渍、干燥、预氧化、卷绕、高温碳化、表面处理、碳纤维成品。
和PAN基碳纤维相比,由于黏胶纤维含水量较多,增加了加捻、稳定化处理工序,稳定化工序中加入无机和有机系催化剂,以降低热裂解热和活化能,缓和热裂解和脱水反应,便于生产工艺参数的控制,有利于碳纤维强度的提高。
在催化剂作用下,白色黏胶纤维经过脱水、热裂解和结构的转化,变为黑色的预氧化纤维,提高了耐热性。高温碳化在一个衬石墨的碳化炉中进行,温度在1400~2400℃,可获得含碳量为90%~99%的碳纤维。
2.黏胶纤维的碳化机理
黏胶纤维的脱水、热裂解和碳化过程非常复杂,物理化学反应主要发生在700℃之前,可大致归纳为四个阶段。
开始阶段:黏胶纤维中物理吸附水解脱,在90~150℃低温除水。
第二阶段:温度接近240℃,纤维素葡萄糖残基发生分子内脱水化学反应,羟基消除,碳双键生成。
第三阶段:残基的糖苷环发生热裂解,在240~400℃下,纤维素环基深层次裂解成含有双键的碳四残链。
第四阶段:在400~700℃高温下发生芳构化反应,使碳四残链横向聚集合并、纵向交联缩聚为六碳原子的石墨层结构,如果在张力下进行石墨化处理,可提高层面间的取向,转化为乱层石墨结构,从而提高碳纤维的强度和模量。