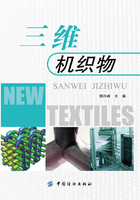
第一节 纺织复合材料
材料是人类生存和发展的物质基础,现代科技的发展,对材料的性能提出了高标准、多样化甚至是相互矛盾的要求,任何单一材料都难以满足这些要求,于是复合材料便应运而生。复合材料是材料领域的后起之秀,它的出现带来了材料领域的重大变革,从而形成了金属材料、无机材料、高分子材料和复合材料多角共存的局面。
复合材料是由两种或多种不同性能、不同形态的组分材料,通过复合工艺组合而成的、比其组成材料性能更优异的新材料。从复合材料的组成和结构来看,复合材料是由基体和增强材料两部分组成,基体是连续相,增强材料是分散相,被基体所包容。
一、复合材料的类型
(一)复合材料的类型
按照不同的标准和要求,复合材料通常有以下几种分类方法。
1.按使用性能不同分类
根据使用性能的不同,复合材料分为结构复合材料和功能复合材料。
利用复合材料的各种良好力学性能来制造结构的材料,称为结构复合材料,它主要由基体材料和增强材料两种组分组成。其中增强材料主要提供复合材料的强度和刚度,基本决定其力学性能;基体材料固定和保护增强纤维,传递纤维间载荷,并可改善复合材料的某些性能。
利用复合材料的物理、化学和生物学的功能作为主要用途的,称为功能复合材料。例如摩擦复合材料、隐身吸波复合材料、阻尼复合材料、压电复合材料、防热复合材料、磁性复合材料、导电复合材料、生物功能复合材料等,有些复合材料同时兼有多项功能,如耐热、透波、承载等。
2.按基体材料不同分类
按基体材料的不同,复合材料可分为聚合物基、金属基、无机非金属基复合材料。这三种复合材料中,以聚合物基复合材料应用最广、产量最大,约占复合材料总量的90%以上。
聚合物基复合材料是以有机聚合物(主要为热固性树脂、热塑性树脂及橡胶)为基体制成的复合材料。热固性树脂在固化前一般是流动的液体,相对分子质量不高,在成型过程中发生化学反应而交联固化,形成网状结构,固化后刚性大、硬度高,再加压加热也不能软化或流动,若温度过高则会分解或炭化。常用的热固性树脂有环氧树脂、不饱和聚酯树脂、酚醛树脂等。热塑性树脂在常温下为高分子量固体,在成型加工过程中,树脂经加压加热即软化和流动,不发生化学交联,可以在模具内赋形,经冷却定型制得所需形状的制品。与热固性复合材料相比,热塑性复合材料突出的优点是成型周期短,韧性好,可回收利用;但树脂熔体黏度高,在低沸点溶剂中溶解能力差或根本不溶解,给热塑性树脂浸渍纤维以及成型加工带来困难。以橡胶为基体可制成柔性复合材料,如轮胎、充气筏、传送带、矿山用导风筒、篷面材料等,织物与橡胶构成的纺织复合材料在柔性材料中占有相当大的比重。
金属基复合材料是以金属为基体制成的复合材料,如铝基复合材料、铁基复合材料、铜基复合材料、镁基复合材料等。
无机非金属基复合材料是以陶瓷、玻璃、水泥、碳材料为基体制成的复合材料。
3.按增强材料的形态分类
按增强材料的形态不同可分为颗粒增强复合材料、短纤维或晶须增强复合材料、片状材料增强复合材料、连续纤维增强复合材料和织物增强复合材料。
4.按增强纤维类型分类
按增强纤维的类型不同,可分为碳纤维复合材料、玻璃纤维复合材料、玄武岩纤维复合材料、芳纶复合材料、超高分子量聚乙烯纤维复合材料、硼纤维复合材料、陶瓷纤维复合材料等。
(二)复合材料的命名
复合材料的命名以其“相”为基础,将增强相(或分散相)材料放在前,基体相(或连续相)材料放在后,最后缀以“复合材料”。如由碳纤维和环氧树脂构成的复合材料称为“碳纤维环氧复合材料”。通常为了书写简便,可在增强相材料与基体相材料之间加符号“-”或“/”,再加“复合材料”,如上面的碳纤维环氧复合材料可写成“碳纤维-环氧复合材料”,更简化地写成“碳-环氧”或“碳/环氧”。
二、纺织结构复合材料
如果增强纤维是由经过纺织加工的纤维、纱线或织物构成,则称为纺织复合材料。
(一)纺织结构增强材料的类型
1.短纤维
将短切纤维与树脂混合,经复合后可制成各种复合材料制品。这种复合材料构件不宜用于承力较大的场合,因纤维不连续,相互间的结合较差,排列方向也不确定,但制造工艺比较简单,生产效率高,生产成本低,适合大规模生产,因而近年来应用很广。
片状模塑料(SMC)是用短纤维与不饱和聚酯树脂、填料等混合制成的片状半成品,在使用时只需撕掉两面的聚乙烯薄膜,按成品相应尺寸裁剪、叠层,然后放入模具中加热加压固化,即得到需要的复合材料制品。块状模塑料(BMC)是在不饱和聚酯树脂中加入短纤维和填料制成的块状半成品,因成型流动性好,可采用高效率的注射工艺成型小型电器元件。块状模塑料和片状模塑料在成分上没有多少差异,只是块状模塑料的纤维含量和纤维长度比片状模塑料的小,而且块状模塑料在制造过程中的纤维损伤较严重,故其制品的力学性能要比片状模塑料低。
用吸附法将短纤维制成与复合材料制品的结构、形状和尺寸相似的预成型坯,然后在模具内与树脂混合,在一定的温度和压力下压制成型。这种方法适用于批量生产大型、高强、异形,尤其是深拉制品的制造,材料成本低,容易实现自动化。
2.纱线
为使短纤纱具有一定的强力,克服纤维间的滑移,通常都对其施加一定的黏度;长丝纱可以加捻,也可以不加捻。两根或多根单纱再通过合股加工,可以得到股线。纱线的捻度和合股数影响纱线的性能,Hearle给出了纱线模量Ey、纤维模量Ef和捻角θ之间的关系。
捻角系指纤维在纱线中的倾斜方向与纱线轴线的夹角。由公式可以看出,当捻度增加、捻角增大时,纱线的模量会降低。表1-1是纱线捻度和合股数对弹力玻璃纱性能的影响,实验采用734tex的弹力玻璃纤维单股纱。从表中可以看出,随着纱线捻度和合股数的增加,纱线的强度和模量均会相应降低。这是由于捻度增加后,当纱线承受拉伸力作用时,因为纤维间侧向分力的存在,使纤维的强度利用率降低。纱线中股数的增多,增加了纱线承受外力时纤维受力的不均匀性,亦即纤维不能同时承受外力,因此降低了纤维的强度利用率。
表1-1 捻度及合股数对弹力玻璃纱性能的影响
续表
鉴于加捻对纤维强度的利用造成不利影响,复合材料常采用无捻或弱捻长丝纱与树脂浸渍、固化成复合材料制品。例如,缠绕工艺将浸渍过树脂的长丝通过缠绕方法制造管道和容器,拉挤成型工艺牵引浸渍过树脂的长丝纱通过模具,经固化后得到各种截面的实心棒材或空心管材(工形、方形、圆形等)。
连续长丝具有高的线性度,纤维强度利用程度高,使复合材料在纤维方向上具有很高的强度和模量,适合于承受拉力的场合。但复合材料在垂直于纤维方向的强度和模量较低,易发生横向开裂和脱层问题,所以拉挤工艺常采用纤维毡、布带和三维织物来提高横向强度。由布带拉挤成型的复合材料制品,其拉伸强度、横向强度都非常好,但成本较高。将三维织物用于拉挤工艺,不仅克服了传统增强纤维制品层间剪切强度低、易于分层等缺点,其层间性能也相当理想。
3.平面织物
按照纱线加工成织物原理的不同,用作增强复合材料的平面结构织物有机织物、针织物、编织物和非织造布等。
目前,用于复合材料的增强织物大多数为机织物,它由经纱和纬纱以90°相互交织而成,常用的织物组织有平纹组织、方平组织、斜纹组织和缎纹组织等。机织物具有良好的结构可设计性,在经向、纬向稳定性好。但机织物的面内抗剪切能力差,各向异性,纱线的屈曲降低了纱线与织物拉伸强度的转化系数。
针织物具有相互穿套的纱圈结构,根据织物中纱线的走向和线圈的结构,针织物可分为经编织物和纬编织物两类。针织物的纱圈结构为其在各方向提供了相当大的延伸性,使其比机织物具有较大的成形范围,因此,能很好地适应于深冲压成型的复合材料。针织物可以在纵向和横向置入呈直线状态的衬经纱和衬纬纱,衬经和衬纬起增强作用,提高了织物尺寸和结构的稳定性。进一步在织物的倾斜方向引入一组或多组纱线,可以获得多轴向针织物,织物的抗剪切性能好。
编织物是由三根或多根纱线,从一端开始各自按一定的规律同时运动,从而实现相互交叉编织形成织物。传统的二维编织机分立式和卧式两种,编织物有扁形和圆形。由于二维编织机所能控制的纱线根数有限,一般不宜生产像机织、针织那样幅宽较大的织物,主要生产绳、带、管等织物,如扁形编织带常用于服装装饰,圆形编织物用作鞋带、电线外包的绝缘布、套管的骨架织物等。由于复合材料发展的需要,编织技术特别是三维编织技术得到迅速发展,除了能生产绳、带、管等类型的织物外,还可以生产各种异形织物,即所谓的预成型织物,也称零件织物。
适用于复合材料应用的非织造布包括纤维毡、缝编和黏合织物等,非织造布具有良好的各向同性,但短纤维增强强力较低。
4.三维织物(3D织物)
对三维织物的大量需求来自于20世纪60年代的航空航天领域。为了克服传统层合板复合材料层间强度低、层间产生剥离或开裂的问题,需要采用层间也存在纤维或纱线的三维整体织物作增强材料。三维织物的生产技术推动了纺织技术的发展,目前三维织物已成为纺织复合材料、特别是高性能复合材料制造技术的发展方向。由于三维织物中纤维连续且多方向连接,使构件的整体性和可靠性大大提高,层间剥离现象不易产生。
尽管对三维织物的研究和应用已有多年,但一直还没有一个明确的定义。在2008年的第一届三维织物国际会上,三维织物被定义为“由多层纱线构成的高厚度织物,或具有复杂形状的中空结构或三维薄壳结构织物”。按照织造方法的不同,三维织物可分成三维机织物、三维编织物、三维针织物、三维缝合织物等,本书讨论的是三维机织物。图1-1是一种三维机织物的结构图,它由多层的经纱1和多层的纬纱2与穿过织物厚度方向的接结纱3相互交织而成。
图1-1 三维机织物结构图
1—经纱 2—纬纱 3—接结纱
(二)纺织复合材料的特点
1.比强度高、比模量大
复合材料的最大优点是比强度高、比模量大。比强度是指材料的强度与密度之比,比模量为材料的模量与密度之比。例如碳纤维增强环氧树脂复合材料的比强度比钢高5倍,比铝合金高4倍,比钛合金高3.5倍,比模量是钢、铝、钛的4倍。比强度、比模量说明了复合材料在“轻质高强”方面的优越性,它意味着可制成性能好而又质量轻的结构,对于航空航天的结构部件和汽车、火车、舰艇等的运动结构有重要意义。
2.材料性能具有可设计性
复合材料的力学、热、光、电、防腐、抗老化等物理、化学性能,都可按照使用要求和环境条件要求,通过组分材料的选择和匹配、铺层设计和界面控制等手段,最大限度地达到预期目的,以满足工程设备的使用性能。例如,通过安排纤维的排列方向、层数和次序,使复合材料达到设计的强度,这是金属材料所不能比拟的;通过综合发挥各种组成材料的优点,使一种材料具有多种材料的性能,比如玻纤/环氧复合材料,达到强度似钢材、耐腐蚀性似塑料的目的。
3.抗疲劳性能好
疲劳破坏是材料在交变载荷作用下,由于微观裂纹的形成和扩展而造成的低应力破坏。金属材料的疲劳破坏是由里向外突然发展的,往往事先无征兆;而纤维复合材料中纤维与基体的界面能阻止裂纹的扩展,其疲劳破坏总是从材料的薄弱环节开始,逐渐扩展,破坏前有明显的征兆。大多数金属材料的疲劳极限是其拉伸强度的40%~50%,碳纤维复合材料则达70%~80%。
4.减震性能好
复合材料中的纤维与树脂基体界面有较大的吸振能力,致使材料的振动阻尼高,可避免共振引起的破坏。曾对形状、尺寸相同的铝合金梁和碳纤维/环氧复合材料梁做过振动试验,前者需9s才停止振动,后者仅需2.5s。
5.耐化学腐蚀性好
常见的玻璃纤维增强热固性树脂基复合材料(俗称热固性玻璃钢),一般都耐酸、稀碱、盐、有机溶剂、海水并耐湿。玻璃纤维增强热塑性树脂基复合材料(俗称热塑性玻璃钢)的耐化学腐蚀性较热固性好,一般而言,耐化学腐蚀性主要决定于基体。
6.成型工艺性优越
可根据产品的结构和使用要求及生产数量,灵活合理地选择原辅材料及成型工艺。由于制品与需要的最终产品接近,复合材料不需或仅需极少的后加工,与金属产品比较,能减少零部件的数量,避免多次加工,降低制造成本。