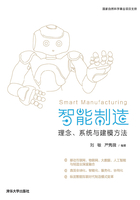
2.1 “工业4.0”的智能制造技术
按照德国学术界和产业界解释,“工业4.0”是继机械化(“工业1.0”,蒸汽动力机械设备应用于生产)、电气化(“工业2.0”,电机发明和电能使用,大规模流水线生产)、自动化和信息化(“工业3.0”,应用IT技术实现自动化生产)之后,以智能制造为主导的第四次工业革命(“工业4.0”),通过移动互联网、物联网、人工智能、云计算、工业互联网和大数据等新兴信息技术,实现智能制造。
“工业4.0”从嵌入式系统向CPS进化,利用CPS对制造过程的组织管理模式进行革命性变革,通过工业软件、智能器件实现制造过程的智能化、虚拟化,力图在制造工厂这一德国的传统优势领域保持领导地位。在设备层面,通过智能器件和控件的小型化、自主化实现设备的智能化;在工厂层面,通过工业软件整合设备资源,实现制造过程的智能化,打造智能工厂;在生产与市场的整合方面,把设计、生产计划、制造过程管控、产品运营维护等全生命周期信息进行整合,在智能工厂内实现端到端集成,并最终实现制造模式的变革——智能制造。智能工厂作为未来第四次工业革命的标志,不断向实现实物、数据以及服务等元素的无缝连接(物联网、大数据和服务互联网)的方向发展。
2.1.1 智能工厂的概念
智能工厂作为智能制造重要的实践领域,正引起了制造企业的广泛关注和各级政府的高度重视。智能工厂的概念起源于早期的智慧工厂/数字化工厂模型。
1.智慧工厂/数字化工厂的概念模型
智慧工厂/数字化工厂概念首先由美国ARC顾问集团(ARC Advisory Group)于2006年提出,智慧工厂/数字化工厂实现了以制造为中心的数字制造、以设计为中心的数字制造和以管理为中心的数字制造,并考虑了原材料、能源供应、产品销售的销售供应,提出从工程(面向产品全生命周期的设计和技术支持)、生产制造(生产和经营)和供应链这3个维度描述。智慧工厂全部的协同制造与管理活动(Collaborative Manufacturing Management,CMM)[7]如图2-1所示。

图2-1 早期智慧工厂的概念模型(来源于美国ARC提出的智慧工厂/数字化工厂模型)
CPM—Collaborative Production Management;PLM/D/S—Product Lifecycle Management Design/Service ERP—Enterprise Resource Planning
数字工厂作为支撑“工业4.0”现有的最重要国际标准之一,是IEC(国际电工委员会)/TC65(65技术委员会:工业过程测量、控制和自动化)的重要议题。
2011年6月,IEC/TC65成立WG16“数字工厂”工作组,西门子、施耐德电气、罗克韦尔自动化、横河等国际自动化企业,以及我国机械工业仪器仪表综合技术经济研究所等研究机构都参与了IEC/TR 62794:2012数字工厂标准的制定。为更好地指导国内企业开展数字工厂建设,全国工业过程测量控制和自动化标准化委员会(SAC/TC124)组织国内相关单位,将该标准等同转化为我国国家标准《工业过程测量、控制和自动化生产设施表示用参考模型(数字工厂)》(GB/Z 32235—2015,2015年12月发布)。
IEC词汇库给出的定义是:数字工厂是数字模型、方法和工具的综合网络(包括仿真和3D虚拟现实可视化),通过连续的、没有中断的数据管理集成在一起。它是以产品全生命周期的相关数据为基础,在计算机虚拟环境中对整个生产过程进行仿真、评估和优化,并进一步扩展到整个产品生命周期的新型生产组织方式。
IEC数字工厂的概念模型分为图2-2所示的3个层次:底层是包含产品构件(如汽车车灯、发动机、轮胎等)和工厂生产资源(如传感器、控制器和执行器等)的实物层;第二层是虚拟层,对实物层的物理实体进行语义化描述,转化为可被计算机解析的“镜像”数据,同时建立数字产品资源库和数字工厂资源库的联系;第三层是涉及产品全生命周期过程的工具应用层,包括设计、仿真、工程应用、资产管理、物流等各个环节。

图2-2 数字工厂概念的示意图
数字工厂概念的最大贡献是实现虚拟(设计与仿真)到现实(资源分配与生产)。通过连通产品组件与生产系统,将用户需求和产品设计通过语义描述输入资源库,再传递给生产要素资源库,制造信息也可以反馈给产品资源库,从而打通产品设计和产品制造之间的“鸿沟”。更进一步,实现了全网络统筹优化生产过程的各项资源,在改进质量的同时减少设计时间,缩短产品开发周期。
2.虚实结合的智能工厂概念模型
随着信息技术和数据库技术的发展,数字工厂的概念和功能有了扩展。
德国的专家和教授基于制造立国和制造强国的理念,把CPS运用于生产制造,提出了信息物理生产系统(Cyber Physical Production System,CPPS),以CPPS为模型构建智能工厂(smart factory)或者数字化工厂。2012年,德国政府制定和大力推行“工业4.0”,而且强调“工业4.0”的特征是工业自动化和信息的紧密结合,它建立在CPS的基础之上。这就为智能工厂的实现指明了一条具有现实可行性的途径。于是,德国为数众多的、与制造相关的企业从跨国超大型企业(如Siemens、SAP等)到各类自动化产品的中小企业,都在考虑和酝酿如何应对这一发展的大趋势。
CPS深度融合了3C(计算、通信和控制)能力,在对物理设施深度感知的基础上,构建安全、可靠、高效、实时的工程系统。通过计算进程和物理进程实时相互反馈循环,实现信息世界和物理世界的完全融合,从而改变人类构建工程物理系统的方式。因此,智能工厂可以看作是图2-3所示的物理工厂+虚拟工厂的结合体[8]。在这个模型中,依靠自动化生产设备构建而成的物理工厂是智能制造的基础,也是绝大多数的中国制造工厂现阶段转型提升的重点和关键,即实现生产过程的自动化和数字化;在数字化的基础上,通过大数据分析及新一代人工智能技术,实现工厂的智能化分析和应用。

图2-3 智能工厂=物理工厂+虚拟工厂
智能生产:当今市场瞬息万变,为了能够应对与日俱增的市场竞争压力,更好地满足市场需求,企业生产模式也由以往的大规模生产向大规模定制和更高级的个性化定制转变,这就要求工厂的生产线具备模块组合能力;在模块组合生产中,借助物联网技术,对生产模块中混线生产的个性化定制半成品、成品进行实时追踪、组合配置与调度,实现工厂的柔性化生产,并解决大规模生产向定制化生产转型带来的不确定性、多样性和复杂性问题。
产品质量控制:为更好地响应市场需求,追求成本最优,绝大多数公司会设立多家自有工厂或者使用代工厂。因此,虽然是同样的制造工艺及生产流程,但不同的供应商存在原材料差异,且生产工艺易受气候、温湿度等众多因素影响,在这种情况下,如何确保在任何工厂和同一工厂的任何时间按照同样生产工艺流程制造的产品保持同一、优质的产品特性,成为质量工程师和工艺工程师的一道难题。
设备预测性维护:为适应客户的不同需求,现在越来越多的制造业工厂同时拥有面向大批量生产的连续型流水线工艺设备、面向定制化需求的离散型多机台工艺设备,以及管线型动力设备、区域型值守物流设备等。对于不同的设备类型,如何建立差异化的运维与保障策略,实现对生产工艺、产品质量的有效保障(图2-4),已经成为大型生产制造企业普遍面临的难题。

图2-4 基于物联网和大数据的设备预测性维修
智能物流管控:车间物流的智能化管理与控制。
能耗智能管理:企业能源管理是构建智慧工厂的重要环节,优先对企业能源实现智能管理是智慧工厂建设的重要步骤。
3.通用电器(GE)智慧工厂的概念模型
2015年2月14日,GE公司在印度Pune建设的智慧工厂(brilliant factory)揭幕。区别于传统大型制造厂,这间工厂具备超强的灵活性,可以根据GE公司在全球不同地区的需要,在同一厂房内加工生产飞机发动机、风机、水处理设备、内燃机车组件等看似完全不相干的产品。
GE公司的智慧工厂结合工业互联网和先进制造技术,用数据主线打通设计、工艺、制造、供应链、分销渠道、售后服务,并形成一个内聚、连贯的智能系统。该工厂雇用的1500名工人共同分享使用生产线,包括3D打印机和激光检测设备。这里,工厂的设备和计算机相互“沟通交流”、共享信息,并且为保证质量和预防设备故障采取措施。而且,工厂的生产线通过数字化的方式与供应商、服务商、物流系统相连接用来优化生产。
GE智慧工厂[9]的理念基于两个概念:数字主线(digital thread)和数字孪生(digital twin),其理念是通过数字主线驱动智慧工厂(图2-5),在企业各阶段实现经营目标。

图2-5 数字主线驱动的智慧工厂
(1)数字主线:描述一束连接(贯穿)着产品生命周期里各阶段过程的数据(图2-6),如喷漆发动机的传感器链接着供应商等。

图2-6 数字主线
洛克希德•马丁在21世纪初研制F-35时,为大幅度提高产品质量、缩短研制周期和降低成本,构建了集成产品和过程研发(Integrated Product and Precess Development, IPPD)平台,提出了digital thread的概念,强调数字主线贯穿于产品全生命周期(digital thread throughout life-cycle),在F-35研制中取得了很好的效果,此后被大家广泛认可。
在2005年F-35的评审中提到:整个F-35团队通过IPPD能共享数字工程模型,其效果是非凡的,使我们能基于设计/工程/制造软件CATIA的计算机模型制作产品部件。当部件交付时,非常令人满意地看到它们完美地匹配计算机模型。这种方法创造了奇迹,如澳大利亚制造的用于F-35自主物流项目的发动机输送车,可以精确地与发动机匹配。
GE数字主线的核心框架(图2-7):将企业的运营数据转变为有效的客户化定制方案。

图2-7 GE数字主线的核心框架
(2)数字孪生(图2-8):是指每件物质资产的数字模型(虚拟),包括设计和工程细节,描述其集合形状、材料、组件和行为,以及特定物理资产的制造和操作数据,最初由国防高级研究计划署(Defense Advanced Research Projects Agency,DARPA)提出。

图2-8 发动机的数字孪生模型
数字孪生的概念模型由3个主要部分构成:真实世界的实物产品(physical products in real space)、虚拟世界的虚拟产品、虚拟产品和实物产品间关联的数据和信息连接。
数字孪生革新了工程模拟过程(图2-9),可帮助公司分析和优化产品在实际操作条件下的性能。

图2-9 工程模拟的数字孪生模型
数字孪生革新了产品生产过程,可以改进物理工厂的操作监控及资产管理(图2-10)。

图2-10 工厂的孪生模型(虚拟工厂和物理工厂)
数字孪生的本质是根据物理工厂创建一个资产的运营数字模型(虚拟工厂),因此,数字孪生和数据主线成为“工业4.0”成功的关键技术。
(3)GE智慧工厂的理念是将设计、工程、制造、供应链、分销和服务链接到一个智能系统中,因此,现代制造就是从云到车间的过程(图2-11)。

图2-11 GE智慧工厂
2.1.2 “工业4.0”的核心特征
在“工业4.0”框架(图2-12)中,物联网和服务互联网分别位于智能工厂三层信息技术基础架构的底层和顶层。最顶层中包含与生产计划、物流、能耗和经营管理相关的ERP、SCM、CRM等,和产品设计、技术相关的PLM也处在最顶层,与服务互联网紧密相连。中间一层通过信息处理系统实现与生产设备的连接和生产线控制、调度等相关功能,从智能物料的供应到智能产品的产出,贯穿整个产品生命周期管理。最底层通过物联网实现控制、执行、传感,最终实现智能生产。

图2-12 “工业4.0”框架
“工业4.0”的核心在于工业、产品和服务的全面交叉渗透,这种渗透借助于软件,通过在互联网和其他网络上实现产品及服务的网络化而实现。“工业4.0”重点关注两方面内容:产品开发与生产过程。“工业4.0”实施建议中,进一步提出“工业4.0”的3个核心特征:
•通过价值链及网络实现企业间的横向集成,将各种不同制造阶段和商业计划的IT系统集成在一起,强调产品的价值流(增值过程)集成,既包括一个公司内部的材料、能源和信息的配置(如原材料物流、生产过程、产品外出物流、市场营销等),也包括不同公司间的配置(形成价值网络)。
•企业内部灵活可重组的网络化制造系统的纵向集成,将各种不同层面的自动化与IT系统集成在一起(如传感器和执行器、控制、生产管理、制造执行、企业计划等各种不同层面),强调生产信息流的集成,包括订单、生产调度、程序代码、工作指令、工艺和控制参数等信息的下行传递,以及生产现场的工况、设备状态、测量参数等信息的上行传递。
•全生命周期管理及端到端系统工程,通过集成CAD/CAM/CAPP、PLM、ERP、SCM、CRM、MES等软件/系统,实现用户参与设计(个性化),并通过虚拟设计、虚拟评估和虚拟制造,更好地把用户需求同生产制造完美地结合起来,并涉及产品直到维护服务的全生命周期,随时将用户意见反馈给前端的设计阶段,动态提升产品质量。
智能工厂的横向集成(图2-13):网络协同制造的企业通过价值链以及信息网络所实现的信息共享与资源整合,确保各企业间紧密合作,提供实时产品和服务,实现产品开发、生产制造、经营管理等在不同企业间的信息共享和业务协同,主要体现在网络协同合作上,从企业集成过渡到企业间的集成,进而走向产业链、企业集团,甚至跨国集团间基于企业业务管理系统的集成,产生全新的价值链和商业模式。

图2-13 智能工厂的横向集成
智能工厂的纵向集成(图2-14):基于智能工厂中网络化的制造体系,实现贯穿企业内部管理、运行、控制及现场等多个层级的企业内部业务流程集成,是实现柔性生产、绿色生产的途径,主要体现在工厂内的科学管理从侧重于产品的设计和制造过程,走向产品全生命周期的集成过程,最终建立有效的纵向生产体系。

图2-14 智能工厂的纵向集成
智能工厂的端到端集成(图2-15):贯穿整个价值链的工程化信息集成,以保障大规模个性化定制的实施。端到端集成是基于满足用户需求的价值链的集成,通过价值链上不同企业间及每个企业内部的资源的整合及协作,是实现个性化定制服务的根本途径。端到端集成可以是企业内部的纵向集成,可以是产业链中的横向集成,也可以是两者的交互融合。

图2-15 智能工厂的端到端集成
在“工业4.0”中,对供应商而言,动态商业模式和工程流程使生产和交付变得更加灵活,而且对于生产中断和故障可以灵活反应。现在工业制造在制造流程中已经能够提供端到端的透明化,以促进选择决策的制定。安全和安保是智能制造系统成功的关键(图2-16),设备和产品中包含的信息特别需要被保护,以防止这些信息被滥用或者在未被授权的情况下使用。这将对安全和安保的架构和特殊识别码的集成调用产生更高的要求。

图2-16 基于云安全网络的智慧工厂流程
企业从信息集成、过程集成、企业集成不断向智能发展的集成阶段迈进,在智能工厂的横向集成、纵向集成和端到端集成3项核心特征的基础上,智能制造将推动企业内部、企业与网络协同合作企业之间以及企业与顾客之间的全方位整合,形成共享、互联的未来制造平台。另外,这3个集成实际上为我们指明了实现“工业4.0”的技术方向。
2.1.3 “工业4.0”的基本特征
互联:把设备、生产线、工厂、供应商、成品及客户紧密地联接在一起,将无处不在的传感器、嵌入式终端系统、智能控制系统、通信设施通过CPS形成一个智能网络,使得产品和生产设备之间、不同的生产设备之间以及数字世界和物理世界之间能够互联,使得机器、功能部件、系统以及人类通过网络持续地保持数字信息的交流。
数据:在“工业4.0”时代,制造企业的数据将会呈现爆炸式增长态势。数据包括产品数据、运营数据、价值链数据、外部数据。
创新:“工业4.0”的实施过程就是制造业创新发展的过程,制造技术(新型传感器、集成电路、人工智能、移动互联、大数据等信息技术,传统制造技术,传统工业与信息技术融合,如信息物理空间、智能工厂等)、产品(“全面感知+可靠通信+智能”的产品以及智能装备从单机智能向智能生产线、智能车间和智能工厂演进)、模式(全新的生产模式:基于CPS的智能工厂和智能制造模式;商业模式:网络众包、异地协同设计、大规模个性化定制、精准供应链管理等)、业态、组织(开放创新、协同创新、用户创新)、转型(从大规模生产向个性化定制转型、从生产型制造向服务型制造转型、从要素驱动向创新驱动转型)等方面的创新将会层出不穷。
集成:上面3项的集成。