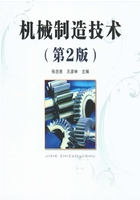
1.4 金属切削过程
金属切削过程是指将工件上多余的金属层,通过切削加工被刀具切除而形成切屑的过程。金属在切削过程中会产生的切削变形、切削力、切削热、积屑瘤和刀具磨损等物理现象,研究这些现象及变化规律,对于合理使用与设计刀具、夹具和机床,保证加工质量,减少能量消耗,提高生产率和促进生产技术发展都有很重要的意义。
1.切屑的形成与切削变形
大量的实验和理论分析证明,塑性金属切削过程中切屑的形成过程就是切削层金属的变形过程。根据切削实验时制作的金属切削层变形图片,可绘制出图1-19所示的金属切削过程中的滑移线和流线示意图。流线表明被切削金属中的某一点在切削过程中流动的轨迹。切削过程中,切削层金属的变形大致可划分为如下三个区域:
(1)第Ⅰ变形区:第Ⅰ变形区是切屑形成的主要区域(见图1-19中Ⅰ区),在刀具前面推挤下,切削层金属发生塑性变形。切削层金属所发生的塑性变形是从OA线开始,直到OM线结束。在这个区域内,被刀具前面推挤的工件的切削层金属完成了剪切滑移的塑性变形过程,金属的晶粒被显著地拉长。离开OM线之后,切削层金属已经变成了切屑,并沿着刀具前面流动。
(2)第Ⅱ变形区:切屑沿刀具前面流动时,进一步受到刀具前面的挤压,在刀具前面与切屑底层之间产生了剧烈摩擦,使切屑底层的金属晶粒纤维化,其方向基本上和刀具前面平行。这个变形区域(见图1-19中的Ⅱ区)称为第Ⅱ变形区。第Ⅱ变形区对切削过程也会产生较显著的影响。
(3)第Ⅲ变形区:切削层金属被刀具切削刃和前面从工件基体材料上剥离下来,进入第Ⅰ和第Ⅱ变形区;同时,工件基体上留下的材料表层经过刀具钝圆切削刃和刀具后面的挤压、摩擦,使表层金属产生纤维化和非晶质化,使其显微硬度提高;在刀具后面离开后,已加工表面的表层和深层金属都要产生回弹,从而产生表面残余应力,这些变形过程都是在第Ⅲ变形区(见图1-19中的Ⅲ区)内完成的,也是已加工表面形成的过程。第Ⅲ变形区内的摩擦与变形情况,直接影响着已加工表面的质量。
这三个变形区不是独立的,它们有紧密的内在联系并相互影响。

图1-19 金属切削过程中的滑移线和流线示意图
2.切屑的类型
由于工件材料以及切削条件不同,切削变形的程度也就不同,因而所产生的切屑形态也就多种多样。其基本类型,包括带状切屑、挤裂切屑、单元切屑和崩碎切屑四类,如图1-20所示。

图1-20 切屑的类型
1)带状切屑
带状切屑是加工塑性材料最常见的一种切屑。它的形状像一条连绵不断的带子,底部光滑,背部呈毛茸状,如图1-20(a)所示。一般加工塑性材料,当切削厚度较小、切削速度较高、刀具前角较大时,得到的切屑往往是带状切屑。形成这种切屑时,切削过程平稳,切削力波动较小,已加工表面粗糙度值较小,但带状切屑会缠绕工件、刀具等,需要采取断屑措施。
2)挤裂切屑
挤裂切屑又称节状切屑,是在加工塑性材料时较常见的一种切屑。其特征是内表面很光滑,外表面可见明显裂纹的连续带状切屑,如图1-20(b)所示。其产生的主要原因:切削过程中,由于被切材料在局部达到了破裂强度,使切屑在外表面产生了明显可见的裂纹,但在切屑厚度方向上不贯穿整个切屑,使切屑仍然保持了连续带状。采用较小的前角、较低的切削速度加工中等硬度的塑性材料时,容易得到这类切屑。这种切削过程,由于变形较大,切削力大,且有波动,加工后工件表面较粗糙。
3)单元切屑
单元切屑又称粒状切屑,是在加工塑性材料时较少见的一种切屑。其特征是切屑呈粒状,如图1-20(c)所示。其原因是在刀具的作用下,切屑在整个剪切面上受到的剪应力超过了材料的断裂极限,使切屑断裂而与基体分离。这种切削过程不平稳,振动较大,已加工表面粗糙度值较大,表面可见明显波纹。其产生条件与挤裂切屑相比切削速度、刀具前角进一步减小,切削厚度进一步增加。
4)崩碎切屑
崩碎切屑是加工脆性材料时常见的切屑。因被切材料在刀刃和前面的作用下,未经塑性变形就被挤裂而崩碎,从而形成不规则的碎块状切屑,如图1-20(d)所示。工件越硬脆,越容易产生这类切屑。产生崩碎切屑时,切削热和切削力都集中在主切削刃和刀尖附近,刀尖容易磨损,并产生振动,从而影响被加工件的表面粗糙度。
同一加工件,切屑的类型可以随切削条件的不同而改变,在生产中,常根据具体情况采取不同的措施来得到需要的切屑,以保证切削加工的顺利进行。例如,增大前角、提高切削速度或减小切削厚度可将挤裂切屑转变成带状切屑。
3.积屑瘤
在一定切削速度范围内,加工钢材、有色金属等塑性材料时,在刀具前面靠近刀刃的部位黏附着一小块很硬的金属,这块金属就是切削过程中产生的积屑瘤,或称刀瘤,如图1-21所示。

图1-21 积屑瘤
1)积屑瘤的形成
积屑瘤是由于切屑和前面剧烈的摩擦、黏结而形成的。当切屑沿刀具前面流出时,在高温和高压的作用下,切屑底层受到很大的摩擦阻力,致使这一层金属的流动速度降低,形成“滞流层”。当滞流层金属与刀具前面之间的摩擦力超过切屑本身分子间的结合力时,就会有一部分金属黏结在刀刃附近形成积屑瘤。积屑瘤形成后越来越高,达到一定高度又会破裂,从而被切屑带下或嵌附在工件表面上,影响表面粗糙度。上述过程是重复进行的。积屑瘤的形成主要取决于切削温度,如在300~380℃切削碳钢易产生积屑瘤。
2)积屑瘤对切削加工的影响
(1)对切削力的影响。积屑瘤黏结在刀具的前面上,增大了刀具的实际前角,可使切削力减小。但由于积屑瘤不稳定,导致了切削力的波动。
(2)对已加工表面粗糙度的影响。积屑瘤不稳定,易破裂,其碎片随机散落,可能会留在已加工表面上。另外,积屑瘤形成的刃口不光滑,使已加工表面变得粗糙。
(3)对刀具耐用度的影响。积屑瘤相对稳定时,可代替切削刃切削,减小了切屑与刀具前面的接触面积,提高刀具耐用度;积屑瘤不稳定时,破裂部分有可能引起硬质合金刀具的剥落,反而降低了刀具耐用度。
显然,积屑瘤有利有弊。粗加工时,对精度和表面粗糙度要求不高,如果积屑瘤能稳定生长,则可以代替刀具进行切削,保护刀具,同时减小切削变形。精加工时,则应避免积屑瘤的出现。
3)影响积屑瘤的主要因素
工件材料和切削速度是影响积屑瘤的主要因素。此外,接触面间的压力、粗糙程度、黏结强度等因素都与形成积屑瘤的条件有关。
(1)工件材料。塑性好的材料,切削时的塑性变形较大,容易产生积屑瘤。塑性差硬度较高的材料,产生积屑瘤的可能性相对较小。切削脆性材料时,形成的崩碎切屑与前面无摩擦,一般无积屑瘤产生。
(2)切削速度。切削速度较低(vc<3m/min)时,切屑流动较慢,切屑底面的金属被充分氧化,摩擦因数小,切削温度低,切屑金属分子间的结合力大于切屑底面与刀具前面之间的摩擦力,因而不会出现积屑瘤。切削速度在3~40m/min范围内时,切屑底面的金属与刀具前面间的摩擦因数较大,切削温度高,切屑金属分子间的结合力降低,因而容易产生积屑瘤。当切削速度较高(vc>40m/min)时,由于切削温度很高,切屑底面呈微熔状态,摩擦因数明显降低,亦不会产生积屑瘤。
此外,增大前角以减小切屑变形或用油石仔细打磨刀具前面以减小摩擦,或选用合适的切削液以降低切削温度和减小摩擦,都有助于防止积屑瘤的产生。
4.切削力
金属切削时,刀具切入工件,使工件材料产生变形成为切屑所需要的力称为切削力。切削力是计算切削功率、设计刀具、机床和机床夹具以及制订切削用量的重要依据。在自动化生产中,还可通过切削力来监控切削过程和刀具的工作状态。因此,研究和掌握切削力的规律和计算、实验方法,对生产实践有重要的实用意义。
1)切削力的来源及分解
(1)切削力的来源。切削时,使被加工材料发生变形成为切屑所需的力称为切削力。切削力来源于以下两个方面(见图1-22)。
①切屑形成过程中,弹性变形和塑性变形产生的抗力。
②切屑和刀具前面的摩擦阻力及工件和刀具后面的摩擦阻力。
(2)切削力的分解。总切削力F是一个空间力。为了便于测量和计算,以适应机床、刀具设计和工艺分析的需要,常将F分解为三个互相垂直的切削分力,如图1-23所示。

图1-22 切削力的来源

图1-23 总切削力的分解
①主切削力Fc:主切削力是总切削力F在主运动方向上的分力,又称切向力。主切削力是三个分力中最大的,消耗的机床功率也最多(95%以上),是计算机床动力和主传动系统零件(如主轴箱内的轴和齿轮)强度和刚度的主要依据。
②进给力Ff:进给力是总切削力F在进给运动方向上的分力,车削外圆时与主轴轴线方向一致,又称轴向力。进给力一般只消耗总功率的1%~5%,是计算进给系统零件强度和刚度的重要依据。
③背向力Fp:背向力是总切削力F在垂直于进给运动方向上的分力,又称径向力或吃刀抗力。因为切削时在此方向上的运动速度为零,所以Fp不做功,但会使工件弯曲变形,还会引起工件振动,对表面粗糙度产生不利影响。
总切削力F与三个分力Fc、Ff、Fp的关系

据实验,当κr=45°、λs=0°、γo=15°时,Fc、Fp、Ff之间有以下近似关系
Fp=(0.4~0.5)Fz
Ff=(0.3~0.4)Fz
代入式(1-22)得
Fc=(1.12~1.18)Fz
随着刀具几何参数、切削用量、工件材料和刀具磨损等情况的不同,Fc、Fp、Ff之间的比例也不同。
2)切削力、切削功率的计算
(1)切削力的计算。很多研究人员曾用计算机对切削力做了大量的理论分析,以期从理论上获得计算切削力的理论公式,服务于生产。但由于切削过程非常复杂,影响因素很多,迄今还未能得出与实测结果相吻合的理论公式。因而生产实践中仍采用通过实验方法所建立的切削力实验公式。它是通过大量实验,由测力仪测得切削力后,将所得数据用数学方法进行处理而得出的。
现有的切削力实验公式有两类:
①经验公式:由于切削过程十分复杂,影响因素较多,生产中常采用经验公式计算,即
Fc=KcAD=Kcapf (1-23)
式中:Fc——切削力(N);
Kc——切削层单位面积切削力(N/mm2);
AD——切削层公称横截面积(mm2)。
Kc与工件材料、热处理方法、硬度等因素有关,其数值可查切削手册。
②指数公式

式中:Fc、Fp、Ff——分别为主切削力、背向力、进给力;
、
、
——分别为上述三个分力的系数,其大小决定于被加工材料和切削条件(可查手册);
、
、
、
、
、
、
、
、
——分别为三个分力公式中,背吃刀量aP、进给量f和切削速度vc的指数(可查手册)。
(2)切削功率的计算。消耗在切削过程中的功率称为切削功率Pc,是Fc、Ff所消耗功率之和。Fp方向没有位移,不消耗功率。而Ff相对于Fc所消耗的功率来说一般很小,可略去不计。因而切削功率Pc可按下式计算
Pc=Fcvc10-3 (1-25)
(3)机床电动机功率。在设计机床选择电动机功率PE时,应按下式计算

式中:ηc——机床传动效率,一般取0.75~0.85。
5.影响切削力的因素
1)工件材料的影响
工件材料的强度、硬度越高,虽然切屑变形略有减小,但总的切削力还是增大的。强度、硬度相近的材料,塑性大,则与刀具的摩擦因数也较大,故切削力增大。加工脆性材料,因塑性变形小,切屑与刀具前面摩擦小,切削力较小。
2)切削用量的影响
(1)背吃刀量和进给量。当进给量f和背吃刀量ap增加时,切削面积增大,切削力也增加,但两者的影响程度不同。在车削时,当背吃刀量ap增大一倍时,切削力约增大一倍;而进给量f加大一倍时,切削力只增大68%~86%。
(2)切削速度。积屑瘤的存在与否,决定着切削速度对切削力的影响情况:在积屑瘤生长阶段,vc增加,积屑瘤高度增加,变形程度减小,切削力减小;反之,在积屑瘤减小阶段,切削力则逐渐增大。在无积屑瘤阶段,随着切削速度vc的提高,切削温度增高,刀具前面摩擦减小,变形程度减小,切削力减小,如图1-24所示。因此生产中常用高速切削来提高生产效率。

图1-24 切削速度对切削力的影响
在切削脆性金属工件材料时,因塑性变形很小,刀具前面的摩擦也很小,所以切削速度vc对切削力无明显的影响。
3)刀具几何参数的影响
(1)前角。前角对切削力影响最大。当切削塑性金属时,前角增大,能使被切层材料所受挤压变形和摩擦减小,排屑顺畅,总切削力减小。加工脆性金属时前角对切削力影响不明显。
(2)负倒棱。在锋利的切削刃上磨出负倒棱(见图1-25),可以提高刃口强度,从而提高刀具使用寿命,但此时被切削金属的变形加大,切削力增加。

图1-25 负倒棱对切削力的影响
(3)主偏角。主偏角对切削力的影响主要是通过切削厚度和刀尖圆弧曲线长度的变化来影响变形,从而影响切削力的。主偏角对切削分力Fc、Fp、Ff的影响较小,但对背向力Fp和进给力Ff的影响明显,主偏角κr增大,背向力Fp减小,进给力Ff增大。因此,生产中常用主偏角为75°的车刀加工。
4)其他因素的影响
刀具、工件材料之间的摩擦因数因影响摩擦力而影响切削力的大小。在同样的切削条件下,高速钢刀具的切削力最大,硬质合金次之,陶瓷刀具最小。在切削过程中使用切削液,可以降低切削力。并且切削液的润滑性能越高,切削力的降低越显著。刀具后面磨损越严重,摩擦越剧烈,切削力越大。
6.切削热与切削温度
切削热和由它产生的切削温度,会使加工工艺系统产生热变形,不但影响刀具的磨损和耐用度,而且影响工件的加工精度和表面质量。因此,研究切削热和切削温度的产生及其变化规律有很重要的意义。
1)切削热的来源与传导
在切削过程中,由于切削层金属的弹性变形、塑性变形以及摩擦而产生的热,称为切削热。切削热通过切屑、工件、刀具以及周围的介质传导出去,如图1-26所示。在第Ⅰ变形区内切削热主要由切屑和工件传导出去,在第Ⅱ变形区内切削热主要由切屑和刀具传导出去,在第Ⅲ变形区内切削热主要由工件和刀具传出。加工方式不同,切削热的传导情况也不同。不用切削液时,切削热的50%~86%由切屑带走,40%~10%传入工件,9%~3%传入刀具,1%左右传入空气。

图1-26 切削热的来源与传导
2)切削温度及影响因素
切削温度一般指切屑与刀具前面接触区域的平均温度。切削温度可用仪器测定,也可通过切屑的颜色大致判断。例如切削碳素钢时,切屑的颜色从银白色、黄色、紫色到蓝色,则表明切削温度从低到高。切削温度的高低,取决于该处产生热量的多少和传散热量的快慢。因此,凡是影响切削热产生与传出的因素都影响切削温度的高低。
(1)工件材料。对切削温度影响较大的是材料的强度、硬度及热导率。材料的强度和硬度越高,单位切削力越大,切削时所消耗的功率就越大,产生的切削热越多,切削温度就越高。热传导率越小,传导的热越少,切削区的切削温度就越高。
(2)刀具几何参数。刀具的前角和主偏角对切削温度影响较大。增大前角,可使切削变形及切屑与前面的摩擦减小,产生的切削热减少,切削温度下降。但前角过大(γo≥20°)时,刀头的散热面积减小,反而使切削温度升高。减小主偏角,可增加切削刃的工作长度(见图1-27),增大刀头的散热面积,降低切削温度。

图1-27 主偏角与刀刃工作长度
(3)切削用量。增大切削用量,单位时间内切除的金属量增多,产生的切削热也相应增多,致使切削温度上升。由于切削速度、进给量和吃刀量的变化对切削热的产生与传导的影响不同,所以对切削温度的影响也不相同。其中,吃刀量对切削温度的影响最小,进给量次之,切削速度的影响最大。因此,从控制切削温度的角度出发,在机床条件允许的情况下,选用较大的吃刀量和进给量比选用大的切削速度更有利。
(4)其他因素。刀具后面磨损增大时,加剧了刀具与工件间的摩擦,使切削温度升高。切削速度越高,刀具磨损对切削温度的影响越明显。可利用切削液的润滑功能降低摩擦因数,减少切削热的产生,同时切削液也可带走一部分切削热,所以采用切削液是降低切削温度的重要方法。
3)切削热对切削加工的影响
传入切屑及介质中的热对加工没有影响;传入刀头的热量虽然不多,但由于刀头体积小,特别是高速切削时切屑与刀具前面发生连续而强烈的摩擦,刀头上切削温度可达1000℃以上,会加速刀具磨损,降低刀具使用寿命;传入工件的切削热会引起工件变形,影响加工精度,特别是加工细长轴、薄壁套以及精密零件时,更需注意热变形的影响。所以,切削加工中应设法减少切削热的产生,改善散热条件。
7.刀具磨损与刀具耐用度
切削时刀具在高温条件下,受到工件、切屑的摩擦作用,刀具材料被逐渐磨耗或出现其他形式的破坏。当磨损量达到一定程度时,切削力加大,切削温度上升,切屑形状和颜色改变,甚至产生振动,不能继续正常切削。因此,刀具磨损直接影响加工效率、质量和成本。
1)刀具磨损的形态
刀具磨损是指刀具与工件或切屑的接触面上,刀具材料的微粒被切屑或工件带走的现象。这种磨损现象称为正常磨损。若由于冲击、振动、热效应等原因使刀具崩刃、碎裂而损坏,称为非正常磨损。刀具正常磨损有以下三种形式:
(1)前面磨损(月牙洼磨损)。切削塑性材料,当切削厚度较大时,刀具前面承受巨大的压力和摩擦力,而且切削温度很高,使前面产生月牙洼磨损,如图1-28所示。随着磨损的加剧,月牙洼逐渐加深加宽,当接近刃口时,会使刃口突然破损。刀具前面磨损量的大小,用月牙洼的宽度KB和深度KT表示。
(2)后面磨损。刀具后面虽然有后角,但由于切削刃不是理想的锋利,而有一定的钝圆,因此,刀具后面与工件实际上是面接触,磨损就发生在这个接触面上。在切削铸铁等脆性金属或以较低的切削速度、较小的切削厚度切削塑性金属时,由于刀具前面上的压力和摩擦力不大,主要发生刀具后面磨损,如图1-28所示。由于切削刃各点工作条件不同,其刀具后面磨损带是不均匀的。C区和N区磨损严重,中间B区磨损较均匀,其平均磨损宽度以VB表示。

图1-28 刀具的磨损形态
(3)刀具前面和后面同时磨损。这是一种兼有上述两种情况的磨损形式。在切削塑性金属时,若切削厚度适中,经常会发生这种磨损。
2)刀具磨损的主要原因
刀具磨损的原因很复杂,主要有以下几个方面:
(1)硬质点磨损。硬质点磨损是由于工件材料中的硬质点或积屑瘤碎片在刀具表面产生的机械划伤,从而使刀具磨损。各种刀具都会产生硬质点磨损,但对于硬度较低的刀具材料,或低速刀具,如高速钢刀具及手工刀具等,硬质点磨损是刀具的主要磨损形式。
(2)黏结磨损。黏结磨损是指刀具与工件(或切屑)的接触面在足够的压力和温度作用下,达到原子间距离而产生黏结的现象。因相对运动,黏结点的晶粒或晶粒群受剪或受拉被对方带走而造成磨损。黏结点的分离面通常在硬度较低的一方,即工件上。但也会造成刀具材料组织不均匀,产生内应力以及疲劳微裂纹等缺陷。
(3)扩散磨损。扩散磨损是指刀具表面与被切出的工件新鲜表面接触,在高温下,两个摩擦面的化学元素获得足够的能量,相互扩散,改变了接触面双方的化学成分,降低了刀具材料的性能,从而造成刀具磨损。例如,硬质合金车刀加工钢料时,在800~1000℃高温时,硬质合金中的Co、W和C等元素迅速扩散到切屑、工件中去;工件中的Fe元素则向硬质合金表层扩散,使硬质合金形成新的低硬度高脆性的复合化合物层,从而加剧刀具磨损。刀具扩散磨损与化学成分有关,并随着温度的升高而加剧。
(4)化学磨损。化学磨损又称为氧化磨损,指刀具材料与周围介质(如空气中的O,切削液中的极压添加剂S、Cl等),在一定的温度下发生化学反应,在刀具表面形成硬度低、耐磨性差的化合物,加速刀具的磨损。化学磨损的强弱取决于刀具材料中元素的化学稳定性以及温度的高低。
(5)相变磨损。指工具钢在切削温度超过相变温度时,刀具材料中的金相组织发生变化,硬度显著下降而引起的磨损。
(6)热电磨损。切削时,刀具与工件构成一自然热电偶,产生热电势,工艺系统自成回路,热电流在刀具和工件中通过,使碳离子发生迁移或从刀具移至工件,或从工件移至刀具,都将使刀具表面层的组织变得脆弱而加剧刀具磨损。
对于不同的刀具材料,在不同的切削条件下,加工不同的工件材料时,其主要磨损原因可能属于上述磨损原因中的一、两种。如硬质合金刀具高速切削钢料时,主要是扩散磨损,并伴随有黏结磨损和化学磨损等;对一定刀具和工件材料,起主导作用的是切削温度,低温时以机械磨损为主,高温时以热、化学、黏结、扩散磨损为主;合理的选择刀具材料、几何参数、切削用量、切削液,控制切削温度,有利于减少刀具磨损。
3)刀具磨损过程及磨钝标准
(1)刀具的磨损过程。在正常条件下,随着刀具的切削时间增大,刀具的磨损量将增加。通过实验得到图1-29所示的刀具后面磨损量VB与切削时间的关系曲线。由图1-29所示的坐标可知,刀具磨损过程可分为三个阶段。

图1-29 刀具的磨损过程
①初期磨损阶段:初期磨损阶段的特点是磨损快,时间短。一把新刃磨的刀具表面尖峰突出,在与切屑摩擦过程中,峰点的压强很大,造成尖峰很快被磨损,使压强趋于均衡,磨损速度减慢。
②正常磨损阶段:经过初期磨损阶段之后,刀具表面峰点基本被磨平,表面的压强趋于均衡,刀具的磨损量VB随着时间的延长而均匀地增加,经历的切削时间较长。这就是正常磨损阶段,也是刀具的有效工作阶段。
③急剧磨损阶段:当刀具磨损量达到一定程度,切削刃已变钝,切削力、切削温度急剧升高,磨损量VB剧增,刀具很快失效。为合理使用刀具及保证加工质量,应在此阶段之前及时更换刀具。
(2)刀具的磨钝标准。刀具磨损后将影响切削力、切削温度和加工质量,因此必须根据加工情况规定一个最大的允许磨损值,这就是刀具的磨钝标准。国际标准ISO统一规定以1/2背吃刀量处后面磨损宽度VB作为刀具的磨钝标准。磨钝标准的具体数值可查阅有关手册。表1-2所示为高速钢车刀与硬质合金车刀的磨钝标准。
表1-2 高速钢车刀与硬质合金车刀的磨钝标准

4)刀具磨损限度和刀具耐用度
在实际生产中,不可能经常停机测量刀具后面上的VB值以确定是否达到磨钝标准,而是采用与磨钝标准相对应的切削时间,即刀具耐用度来表示。刀具耐用度是指刃磨后的刀具自开始切削直到磨损量达到刀具的磨钝标准所经过的净切削时间,用T表示,单位为s(或min)。刀具耐用度T值越大,表示刀具磨损越慢。常用刀具的耐用度如表1-3所示。
表1-3 刀具耐用度T参考值

(1)刀具磨损限度。在正常磨损阶段后期、急剧磨损阶段之前换刀或重磨,既可保证加工质量,又能充分利用刀具材料。在大多数情况下,后面都有磨损,而且测量也较容易,故通常以后面的磨损宽度VB作为刀具磨损限度。
(2)刀具耐用度(刀具寿命)。刀具耐用度(又称刀具寿命)是指两次刃磨之间实际进行切削的时间,以T表示,单位为min。在实际生产中,不可能经常测量VB的宽度,而是通过确定刀具耐用度,作为衡量刀具磨损限度的标准。因此,刀具耐用度的数值应规定得合理。对于制造和刃磨比较简单、成本不高的刀具,耐用度可定得低些;对于制造和刃磨比较复杂、成本较高的刀具,耐用度可定得高些。通常,硬质合金车刀T为60~90min;高速钢钻头T为80~120min;齿轮滚刀T为200~300min。
(3)影响刀具耐用度的因素。影响刀具耐用度的因素很多,主要有工件材料、刀具材料、刀具几何角度、切削用量以及是否使用切削液等。切削用量中切削速度的影响最大。所以,为了保证各种刀具所规定的耐用度,必须合理地选择切削速度。
5)刀具的破损
刀具破损也是刀具损坏的主要形式之一。以脆性大的刀具材料制成的刀具进行断续切削,或加工高硬度的工件材料时,刀具的破损最为严重。
(1)破损的形式。刀具破损的形式包括脆性破损和塑性破损两种。
①脆性破损:硬质合金和陶瓷刀具切削时,在机械和热冲击作用下,刀具前、后面尚未发生明显的磨损前,就在切削刃处出现崩刃、碎断、剥落、裂纹等。
②塑性破损:切削时,由于高温、高压作用,有时在刀具前、后面和切屑、工件的接触层上,刀具表层材料发生塑性流动而失去切削能力。
(2)破损的原因。在生产实际中,工件的表面层无论其几何形状,还是材料的物理、机械性能,都不是规则和均匀的。例如毛坯几何形状不规则,加工余量不均匀,表面硬度不均匀,以及工件表面有沟、槽、孔等,都使切削或多或少带有断续切削的性质;至于铣、刨更属断续切削之列。在断续切削条件下,伴随着强烈的机械和热冲击,加以硬质合金和陶瓷刀具等硬度高、脆性大的特点,粉末烧结材料的组织可能不均匀,且存在着空隙等缺陷,因而很容易使刀具由于冲击,机械疲劳、热疲劳而破损。
(3)防止或减小破损。防止或减小刀具破损的措施包括提高刀具材料的强度和抗热振性能;选用抗破损能力大的刀具几何形状;采用合理的切削条件。