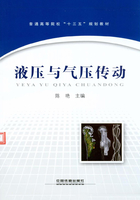
2.3 叶片泵
叶片泵输出流量均匀,脉动小,噪声小,但结构较复杂,对油液的污染比较敏感。它可分为单作用叶片泵和双作用叶片泵两种。单作用叶片泵转子旋转一周进行一次吸油、压油,并且流量可调节,故又称为变量泵。由于其主要零件在工作时要受到径向不平衡力的作用,因而工作情况较差。双作用叶片泵转子旋转一周进行两次吸油、压油,并且流量不可调节,故又称为定量泵。由于其主要零件在工作时受径向力平衡的作用,因而工作情况较好,应用较广。
2.3.1 单作用叶片泵
1.工作原理
如图2.12所示为单作用叶片泵的工作原理。它由转子、定子、叶片和配油盘等组成。定子3的工作表面是一个圆柱表面,定子3与转子2不同心安装,有一偏心距e。叶片4装在转子槽内可灵活滑动。转子回转时,叶片在离心力和叶片底部压力油的作用下,使其顶部贴紧在定子内表面上。在转子2、定子3、叶片4和两侧配油盘1之间就形成了若干个密封腔。当转子2按图2.12中的方向旋转时,右侧的叶片逐渐伸出,密封腔容积逐渐增大,产生局部真空,于是油箱中的油液在大气压力作用下,经配油盘的吸油口进入密封腔,这就是吸油过程。反之,左侧的叶片被定子内表面压入转子槽内,密封腔容积逐渐减小,其内部的油液受到压缩,经配油盘的压油口压出,这就是压油过程。这种泵在转子转一圈的过程中,吸油、压油各一次,故称单作用叶片泵。

图2.12 单作用叶片泵的工作原理
1—配油盘;2—转子;3—定子;4—叶片
2.排量和流量的计算
单作用叶片泵的排量应由泵中密封腔数目和每个密封腔在压油时容积的变化量的乘积来决定。如图2.13所示,设单作用叶片泵每个密封腔在转子旋转一圈中的容积变化量为ΔV,近似等于扇形体积V1和V2之差,即



式中:B——定子的宽度(mm);
β——相邻两叶片间的夹角(°);
z——叶片数;
R——定子的内半径(mm);
r——转子的半径(mm);
e——定子相对转子的偏心距。

图2.13 单作用叶片泵排量的计算简图
因此,单作用叶片泵的排量为
V=zΔV=4πReB
若单作用叶片泵的转速为n,容积效率为ηv,其实际流量为
q=Vnηv=4πReBnηv
由上面两个式子可以看出,改变单作用叶片泵转子和定子的偏心距e,便可改变泵的排量V和流量q,根据理论分析,单作用叶片泵的叶片数越多,流量的脉动率越小,叶片数为奇数的单作用叶片泵的脉动率比叶片数为偶数的单作用叶片泵的脉动率小,所以叶片数一般取z=13或z=15。
3.限压式变量叶片泵的变量原理
图2.14为限压式变量叶片泵的结构图,图2.15(a)为限压式变量叶片泵的简化原理图。如图所示,在定子的左侧作用有一弹簧10(刚度为K,预压缩量为x0);右侧有一控制活塞6(作用面积为A),控制活塞油室常通泵的出口油液压力为p。作用在控制活塞上的液压力F=pA与弹簧力Ft=Kx0相比较,当F<Ft时,定子处于右极限位置,偏心距最大,即e=emax,泵输出最大流量,若泵的出口压力p因工作负载增大,导致F>Ft时,定子将向偏心减小的方向移动,位移为x。定子的位移,—方面使泵的排量(流量)减小,另一方面使左侧的弹簧进一步受压缩,弹簧力增大为Ft=K(x0+x)。当液压力与弹簧力相等时,定子平衡在某一个偏心距(e=emax-x)下工作,泵输出一定的流量。泵的出口压力越高,定子的偏心距越小,泵输出的流量越小。其压力流量特性曲线如图2.15(b)所示。
在图2.15(b)所示的特性曲线中,B点为拐点,对应的压力pB=Kx0/A;C点为极限压力点。pC=K(x0+emax)/A。在AB段,作用在控制活塞上的液压力小于弹簧的预压缩力,定子偏心距e=emax,泵输出最大流量。(因为随着压力增高,泵的泄漏量增加,泵的实际输出流量减小,因此线段AB略向下倾斜。)拐点B之后,泵输出流量随出口压力的升高而自动减小,如曲线BC所示,曲线BC的斜率与弹簧的刚度有关。到C点,泵的输出流量为零。
调节图2.14中的压力调节螺钉11可以改变弹簧的预压缩量x0,即改变特性曲线中拐点B的压力pB的大小,曲线BC沿水平方向平移。调节定子右边的最大流量调节螺钉8,可以改变定子的最大偏心距emax,即改变泵的最大流量,使曲线AB上下移动。由于泵的出口压力升至C点压力pC时,泵的流量等于零,压力不会再增加,泵的最高压力为pC,因此将其命名为限压式变量泵。

图2.14 限压式变量叶片泵的结构
1—滚针;2—滑块;3—定子;4—转子;5—叶片;6—控制活塞;7—传动轴;8—最大流量调节螺钉;9—弹簧座;10—弹簧;11—压力调节螺钉

图2.15 限压式变量泵原理
1—控制活塞;2—弹簧
4.结构特点
(1)存在困油现象。配流盘的吸、排油窗口间的密封角略大于两相邻叶片间的夹角,而单作用叶片泵的定子不存在与转子同心的圆弧段,因此,在吸、排油过渡区,当两叶片间的密封容积发生变化时,会产生与齿轮泵类似的困油现象,通常,通过在配流盘排油窗口边缘开三角卸荷槽的方法来消除困油现象。
(2)叶片沿旋转方向向后倾斜。叶片仅靠离心力紧贴定子表面,考虑到叶片上还受哥氏力和摩擦力的作用,为了使叶片所受的合力与叶片的滑动方向一致,保证叶片更容易地从叶片槽滑出,叶片槽常加工成沿旋转方向向后倾斜一个角度。
(3)叶片根部的容积不影响泵的流量。由于叶片头部和底部同时处在排油区或吸油区中,所以叶片厚度对泵的流量没有影响。
(4)转子承受径向液压力。单作用叶片泵转子上的径向液压力不平衡,轴承负荷较大。这使泵的工作压力和排量的提高均受到限制。
2.3.2 双作用叶片泵
1.工作原理
如图2.16所示为双作用叶片泵的工作原理。它由转子、定子、叶片和配油盘等组成。转子3和定子2是同心的,定子2内表面是由两段长半径圆弧、两段短半径圆弧和四段过渡曲线组成。当转子3旋转时,叶片1在离心力和通往叶片底部压力油的作用下紧贴在定子的内表面上,在相邻叶片之间形成密封腔。显然,右上角和左下角的密封腔的容积逐渐变大,它们所在的区域是吸油腔,左上角和右下角的密封腔的容积逐渐变小,它们所在的区域是压油腔。在吸油腔和压油腔上,配油机构提供了相应的吸油口和压油口,并用封油区将吸油腔和压油腔隔开。

图2.16 双作用叶片泵的工作原理
1—叶片;2—定子;3—转子;4—配油盘
2.排量和流量的计算
双作用叶片泵平均流量的计算方法和单作用叶片泵相同,也可以近似化为环状体积来计算。图2.17为双作用叶片泵平均流量计算原理图。当两叶片从a、b位置转到c、d位置时,排出容积为M的油液,从c、d转到e、f时,吸进了容积为M的油液。从e、f转到g、h时又排出了容积为M的油液;再从g、h转回到a、b时又吸进了容积为M的油掖。这样转子转一周,两叶片间吸油两次,排油两次,每次容积为M。当叶片数为z时,转子转一周。所有叶片的排量为2z个M容积,若不计叶片几何尺寸,此值正好为环状体积的两倍。所以,双作用叶片泵的理论排量为
V=2π(R2-r2)B
式中 R——定子长半径;
r——定子短半径;
B——转子厚度。
双作用叶片泵的平均实际流量为
q=2π(R2-r2)Bnην (2.1)
式(2.1)是不考虑叶片几何尺寸时的平均流量计算公式。一般双作用叶片泵在叶片底部都通压力油,并且在设计中保证高、低压腔叶片底部总容积变化量为零,也就是说叶片底部容积不参加泵的吸油和排油,因此在排油腔,叶片缩进时转子槽的容积变化,对泵的流量有影响,在精确计算叶片泵的平均流量时,还应该考虑叶片容积对流量的影响,每转不参加排油的叶片总容积为

式中 Vb——不参加排油的叶片总容积;
b——叶片厚度;
z——叶片数;
φ——叶片相对于转子半径的倾角(°)。
双作用叶片泵精确流量计算公式为

对于特殊结构的双作用叶片泵,如双叶片结构、弹簧叶片结构,其叶片底部和单作用叶片泵一样也参加泵的吸油和排油,其平均流量计算方法仍采用式(2.1)。

图2.17 双作用叶片泵平均流量计算原理图
3.结构特点
(1)因配流盘的两个吸油窗口和两个压油窗口对称布置,因此作用在转子和定子上的液压径向力平衡,轴承承受的径向力小,寿命长。
(2)定子内表面曲线由两段大圆弧和两段小圆弧即四段过渡曲线组成,过渡曲线采用等加速等减速曲线。叶片对定子曲线冲击较小。另外,叶片在受到离心力的作用而和定子内表面不脱空的条件下,该曲线所允许的定子半径比R/r较大,这使叶片泵在同样体积下采用该曲线的流量较大。
(3)为了减小叶片对转子槽侧面的压紧力和磨损。将叶片相对转子旋转方向向前倾斜一角度θ,通常取θ=13°。
(4)为保证叶片在转子叶片槽内自由滑动并始终紧贴定子内环,双作用叶片泵一般采用叶片槽根部全部通压油腔的办法。采取这种措施后,位于吸油区的叶片便受到一个不平衡的液压力,转子高速旋转时,叶片顶部在该力的作用下刮到定子的吸油腔部,从而造成磨损,影响泵的寿命和额定压力的提高。要提高双作用叶片泵的额定压力,必须采取措施,保证作用在叶片上的不平衡液压力不因额定压力的提高而随之增大,具体的措施有:
①采用双叶片结构。如图2.18所示,各转子槽内装有两个经过倒角的叶片。叶片底部不与高压油腔相通,两叶片的倒角部分构成从叶片底部通向头部的V形油道,因而作用在叶片底部、头部的液压力相等,合理设计叶片头部的形状,使叶片头部承压面积略小于叶片底部承压面积,这个承压面积的差值就形成叶片对定子内表面的接触力。也就是说,这个接触力是能够通过叶片头部的形状来控制的,以便既保证叶片与定子紧密接触,又不至于使接触应力过大,同时,槽内两个叶片可以相互滑动,以保证在任何位置,两个叶片的头部和定子内表面紧密接触。
②采用弹簧叶片结构,如图2.19所示。叶片在头部及两侧开有半圆形槽,在叶片的底面上开有三个弹簧孔。通过叶片头部和底部相连的小孔及侧面的半圆槽使叶片底面与头部沟通,这样,叶片在转子槽中滑动时,头部和底部的压力完全平衡。叶片和定子内表面的接触压力仅为叶片的离心力、惯性力和弹簧力,故接触力较小。不过,弹簧在工作过程中频繁受交变压缩,易引起疲劳损坏。

图2.18 双叶片结构原理

图2.19 弹簧叶片结构
③采用母子叶片结构。如图2.20所示,在转子叶片槽中装有母叶片和子叶片,母、子叶片能自由地相对滑动,为了使母叶片和定子的接触力压力适当,须正确选择子叶片和母叶片的宽度尺寸之比。转子上的压力平衡孔使母叶片的头部和底部液压力相等,泵的排油压力经过配流盘、转子槽通到母、子叶片之间的中间压力腔,如不考虑离心力和惯性力,叶片作用在定子上的力为F=bt(p2-p1),只要适当选择t和b的大小,就能控制接触应力。在排油区叶片仅靠离心力与定子接触,为防止叶片的脱空,在联通中间压力腔的油道上设置适当的节流阻尼,使叶片运动时中间油腔的压力高于作用在母叶片头部的压力,保证叶片在排油区时与定子紧密贴合。

图2.20 母子叶片结构
④采用阶梯叶片结构,如图2.21所示,叶片做成阶梯形式,转子上的叶片槽亦具有相应的形状,它们之间的中间油腔经配流盘上的槽与压力油相通,转子上的压力平衡油道把叶片头部的压力油引入叶片底部。与母子叶片结构相似,在压力油引入中间油腔之前,设置节流阻尼,使叶片向内缩进时,此腔保持足够的压力,保证叶片紧贴定子内表面。这种结构由于叶片及槽的形状较为复杂,加工工艺性较差,应用较少。

图2.21 阶梯叶片结构