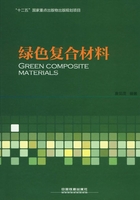
1.4 绿色复合材料发展现状及前景[27—30]
绿色复合材料是指组分材料中至少有一种是由天然资源获取并能完全降解的复合材料,也称为生物复合材料或生态复合材料(bio-composites or eco-composites)。从绿色环保和可持续发展的要求出发,绿色复合材料应包括两个内涵:
(1)以可再生生物质资源为原材料。例如,可全降解的生物高分子基体材料和天然植物纤维增强体,用专门的成型工艺复合而成的一类新型绿色材料,称为100%的绿色复合材料。它具有性能优异、环境友好、品种多样、附加值高、用途广泛等诸多优点,能最大限度地替代石化、矿产资源产品以及塑料、钢材、水泥等传统材料,是高性能复合材料的重要分支,也代表复合材料的发展方向。
(2)高性能复合材料的绿色化。用于航空航天等高端领域的高性能复合材料,目前以高性能纤维,主要是以碳纤维增强的树脂基复合材料为发展主流,目前还处于不可替代的地位,但高性能复合材料的高能耗、高投入、高环境负荷一直是困扰业界的主要问题。随着复合材料的大量应用,绿色化的发展就越来越成为关注的热点。所谓绿色化发展是指在复合材料的整个生命周期内,从设计、选材、成型制造、使用、直到产品退役、废弃物处理和回收再利用的整个过程中将环境的负荷降到最低,最大限度地提高使用性能和可循环再生率。20世纪90年代开始使用的复合材料低成本化技术,由“性能第一”向“性能和成本平衡”转型,可以认为是一种实现复合材料绿色化的努力。而现在这种趋势进展很快,如大型或超大型的复合材料制件非热压罐成型,在节能减排、降低成本及资源消耗等方面显示出巨大优势。
绿色复合材料属于树脂基复合材料的范畴,现在已发展成为复合材料的重要分支,应用研究和产业化发展都取得了很大进展,在新能源、汽车、轨道交通、基建、生物医用等领域得到越来越多的推广应用,并开始向航空航天高端领域应用发展。
与石化资源合成的生物树脂基体材料相比,绿色复合材料目前主要的问题是生物树脂基体的制备成本高,物理机械性能,如强度、耐热性、韧性不够好,这些问题是现在和将来绿色复合材料研究的重要内容。
1.4.1 绿色复合材料的研究现状
出于可持续发展的考虑,从20世纪80年代开始,人们开始了植物纤维自身的强度和韧性的研究以及纤维素纤维与热固性树脂复合化的研究,20世纪90年代木粉和热塑性树脂复合制备木塑复合材料的研究有很多报道。随后,以剑麻、黄麻、亚麻和竹原纤维等高强度的植物纤维为增强体,以热塑性树脂为基体的复合材料的研究不断增多,现在发展到用天然纤维与生物树脂基体复合,制备完全可降解的绿色复合材料。
从目前的发展现状看,绿色复合材料主要有以下几大类:木塑复合材料、生物树脂基复合材料、纳米纤维素生物基复合材料。
1.4.1.1 木塑复合材料[31,32]
木塑复合材料(wood-plastic composites,WPC)是以木质纤维素材料,如木粉、稻壳、秸秆等废弃植物纤维作为增强材料,以热塑性塑料,如聚乙烯(PE)、聚丙烯(PP)和聚氯乙烯(PVC)等作为基体材料,通过适当的方法复合而生产的一种新型材料。
木塑复合材料产业化于20世纪80年代起源于美国。其应用范围非常广泛,几乎可涵盖所有原木、塑料、塑钢、铝合金及其他类似复合材料的使用领域。不仅非常符合建筑业、家具业、物流业、包装业等领域的使用要求,同时也解决了塑料、木材行业废弃资源的再生利用问题。
木塑复合材料在建筑业具有广阔的发展前景,加拿大林产品创新研究院首席研究员戴春平在他的报告《北美木质复合材料研究现状和展望》中指出,当今世界上40%的能源和材料都用于建筑业,40%的固态垃圾从建筑中产生、34%的CO2是从建筑中产生,17%的水用于建筑业。而生物基复合材料中的木塑复合材料是目前最环保和最具再生利用优势的建筑材料。
近几年来,由于木塑复合材料的木质材料组成部分正在向各种其他植物纤维材料发展,因此,从更广泛意义上讲,木塑复合材料实质上已成为以各种植物纤维材料为增强体,与各种不同热塑性塑料复合形成的一类新型复合材料。
木塑复合材料既保持了木质材料原有的优良品质,又兼具热塑性高分子聚合物的一些特性,因而具有独特的性能特点,包括:
(1)良好的加工性能。木塑复合材料具有良好的制造和加工性能,可按要求制造出不同形状和尺寸的制件和产品,易于后续加工,可锯、可钉、可刨,使用木工器具即可完成。
(2)良好的机械性能。木塑复合材料由增强纤维与塑料基体复合,具有良好的抗压、抗弯曲等物理机械性能。硬度是木材的2~5倍。
(3)具有耐水、耐腐蚀性能,使用寿命长。木塑复合材料与一般木材相比,具有较强抗酸碱、耐水、耐腐蚀性能,使用寿命长,可达50年以上。
(4)性能易于调控。通过塑料基体的改性及调控增强体的比例和形态,可以提高复合材料的机械性能或获得某些特殊功能,如抗老化、防静电、阻燃等。
(5)原料来源广泛,可回收和再生。用生物树脂作基体的木塑复合材料,可回收或完全降解,是100%的绿色复合材料。
木塑复合材料在全球范围内发展很快,美国、欧洲、日本的年增长率超过10%,在我国近年来也得到快速发展,在建筑、家居、汽车、铁路交通领域的应用也在不断扩大。
木塑复合材料的发展应着重在以下几方面开展研究:
(1)提高资源利用率。扩大原料选用范围,多用木材、天然植物废弃物等制备木质纤维或其他形态的增强体,充分利用回收的石化废旧塑料重新加工和改性作为基体材料,用于木塑复合材料产品的加工制造。
(2)界面结合等基础研究。如研究复合材料的性能设计、原材料(塑料、木粉种类)的选择及组分比例的优化、组分材料的改性,提高界面相容性和结合力,提高复合材料强度、耐热性和抗冲击性能等。
(3)扩展成型工艺,降低制造成本。复合材料成型工艺有多种选择,根据产品性能需要,选择和开发新型成型工艺和制造技术,改变单一的螺杆挤出或模压成型工艺,开发专用设备,提高生产效率,降低制造成本。
(4)扩大应用领域,开发高性价比的产品。提高产品的性能和质量,扩大应用领域,向高端应用的方向发展。
1.4.1.2 生物树脂基复合材料[33—37]
生物树脂基复合材料是用生物树脂作基体制备的一类复合材料。生物树脂主要是指用天然资源通过化学合成制备的可降解生物高分子材料,也称生物塑料。它可以根据高分子化学理论来设计高分子主链结构,以控制或优化高分子材料的物理化学性能,而且可以充分利用自然界中提取或合成的各种小分子单体进行高分子聚合物的合成。
合成的方法主要有化学合成、微生物合成和最新研究的酶促合成高分子。目前,化学合成法研究得最多,化学合成的生物降解塑料大多是在分子结构中引入能被水解或微生物降解的含酯基结构的脂肪族生物聚酯,产品主要有聚乳酸(polylactic acid,PLA)、聚己内酯(polycap-rolacton,PCL)、聚丁二醇丁二酸酯(polybutylene succinate,PBS)等。
微生物合成制备的生物树脂目前主要是聚3羟基丁酸酯(poly-3-hydroxy butyrate,PHB)和聚3羟基戊酸酯(poly-3-hydroxy valerate,PHV),以及它们的共聚物聚3羟基丁酸/羟基戊酸酯(poly-3-hydroxy butyrate-co-3-hydroxy valerate,PHBV)。表1-2列出了这些生物树脂的主要性能以及与通用石化塑料的性能比较。这几种生物树脂的力学性能,如拉伸强度和弯曲强度都接近通用型的石化塑料,如聚乙烯、聚丙烯、聚酰胺等,实际应用时可作替代材料,突出的缺点是耐热性差、韧性低、脆性大、抗冲击性能不好、降解性能变化较大;另外,它们大多数是疏水性材料,影响到与亲水性植物纤维的界面结合;最后,生物树脂目前的价格普遍高于石化合成塑料,限制了它们作为塑料制品的使用。因此用天然纤维增强改性制备生物基复合材料是改进性能、降低成本、推广应用的有效途径。
表1-2 生物树脂基体性能比较

而天然纤维增强体主要是木材、竹材、棉、麻等直接提取原生纤维或用农业剩余物通过熔融纺丝制备再生纤维素纤维。如表1-3所示为天然纤维与其他纤维性能比较。
表1-3 天然纤维与其他纤维性能比较

由表1-3可知,麻纤维是目前性能最好的天然纤维增强体,品牌多,强度和模量高,密度与玻璃纤维接近,但拉伸强度和模量与玻璃纤维仍有相当大的差距,因此,天然植物纤维作为复合材料增强体,目前还局限于通用型的对强度要求不高的应用,要提高复合材料的性能,还有许多问题要继续研究。
生物树脂基复合材料的特点主要有:
(1)生物树脂基复合材料可完全降解,废弃后可以自行降解,最终变成CO2和H2O,重新回归到大自然循环,不会造成环境污染;
(2)天然植物纤维原料来源广泛,可以再生,材料成本低廉,与生物树脂复合可以降低复合材料的成本;
(3)生物树脂是一种生物高分子材料,来源于可再生的天然资源,可替代石化合成高分子材料,有利于可持续发展;
(4)用纤维增强改性,改善了生物高分子材料的性能,扩大了材料的应用范围;
(5)在一定的温度、湿度及微生物条件下,可实现生物降解,而在正常使用条件下,这种生物质材料自然降解,具有足够长的使用周期。
现在,全球范围内的相关研究进展较快,主要集中于生物树脂和天然增强纤维的开发应用和改性、复合工艺及成型加工技术、复合机理、复合材料生物降解特性及界面改性等方面。有的复合材料产品已实现商业化生产规模,在汽车、建筑、医疗、电子电气、家居中得到越来越多的应用。例如,欧洲汽车内饰件经历了由天然植物纤维材料替代玻璃纤维增强复合材料的发展历程。近几年,随着汽车废弃回收利用问题的压力和人们环保意识的增强,汽车内饰行业已经把天然纤维增强可生物降解材料的应用作为汽车内饰部件用塑料复合材料发展的必然方向。
虽然目前用作基体的生物降解塑料成本远高于普通石化塑料,生物质复合材料还没有得到大规模的应用。但是,随着可用石油资源的减少和人们环境保护意识的增强,可生物降解塑料的开发与应用将引起极大的关注与重视。天然纤维材料与完全可生物降解塑料复合制备新型的环境友好的生物质复合材料将显示广阔的发展前景。
1.4.1.3 纳米纤维素生物基复合材料[38—42]
纳米纤维素(nano-cellulose)是在再生纤维素基础上发展起来的一种新材料,是一种生物材料纳米技术,近年来成为绿色复合材料新的研究热点。
纳米纤维素主要是从植物纤维制取,植物纤维主要由纤维素、半纤维素、木质素、果胶及其他成分组成。纳米纤维素的制备过程大致是先将植物纤维制成浆料,分别采用硫酸水解法和阳离子交换树脂催化水解法将半纤维素和木质素等其他成分溶解分离,制备出纳米纤维素悬浮液,经过冷冻干燥后可制得粉末状的纳米纤维素。
纳米纤维素有时也称纤维素纳米纤维,是直径在纳米尺度的超微细纤维。纳米纤维素具有许多优良特性,如高结晶度、高纯度、高杨氏模量、高强度、高亲水性、超精细结构和高透明性等,加之具有天然纤维素轻质、可降解、生物相容及可再生等特性,因此,纳米纤维素的制备、结构、性能与应用的研究在绿色复合材料中占有非常重要的地位。
纳米纤维素根据其制备方法、原料及结构等的不同可以分为三类,即微纤化纤维素(microfibrillated cellulose,MFC)、纳米微晶纤维素(nano microcrystalline cellulose,NCC)、细菌纳米纤维素(bacterial nanocellulose,BNC)(见表1-4)。
表1-4 纳米纤维素的分类

表1-4中的纳米纤维因为来源、制备方法的差异,在结构和性能上也不相同,如前两类纳米纤维主要来自植物纤维,分别通过机械粉碎、强酸水解,将纤维素中的非纤维素成分分离、脱除,形成纳米尺度的微纤或纳米微晶纤维。由于植物纤维能快速生长、天然合成、原料丰富、成本低廉,因此这两类纳米纤维具有非常好的资源优势和发展前景。
用纳米纤维素作为绿色复合材料的增强体,具有其他增强体无可比拟的优点:
(1)具有优异的生物降解性和再生性,通过光合作用或酶解作用,可完全返回到自然界的碳循环中;
(2)具有高强度,杨式模数和抗张强度比普通植物纤维素成倍增加,用作增强体,比例分数可调,用低含量(质量分数≤5%)即可得到高性能的复合材料;
(3)具有纳米材料的多种效应,如表面效应、小尺寸效应、量子尺寸效应、宏观量子隧道效应。在化学、物理(热、光、电磁等)性质方面表现出特异性,可制备出多种功能的复合材料。
纳米纤维素与PLA、PHB和PBS复合可制备能满足不同性能要求的生物基复合材料。
作为一种新型的复合材料的增强材料,纳米纤维素还有一些问题需要继续研究,包括高性能、高质量的高效和低成本制备方法,与生物基体的复合效应,复合材料成型工艺,以及热、光、生物降解机理等。
1.4.2 绿色复合材料发展前景[43—46]
用天然植物纤维增强石化合成高分子材料,制备木塑复合材料起步于20世纪80年代,主要用于汽车、建筑、机械、家居等方面,这种复合材料从20世纪90年代开始得到迅速发展,到21世纪初,产量已达数百万吨,平均年增长率达到15%~20%。
绿色复合材料的发展方向主要集中在以下几个方面:
(1)拓展原材料供应链。开发新型的生物树脂基体和纤维增强体,一是在现有研究基础上继续提高原材料的性能,逐步向高端应用的复合材料方向发展;二是充分利用资源,利用不与粮食作物和经济作物竞争的可再生植物资源,或城市、工业废弃物、造纸和纺织等副产物开发生物树脂基体材料和再生纤维素纤维增强材料。
(2)开发新型高效低成本的复合工艺和成型制造技术。在现有挤出、模压等工艺基础上,扩展到高性能复合材料的一些高度数字化和自动化成型制造工艺,如树脂传递模塑、自动铺丝/自动铺带、大型制件的非热压罐成型、双真空袋成型等,提高工效、降低成本,实现绿色复合材料大尺寸的制件成型。
(3)扩大应用范围。提高绿色复合材料的性能和质量,降低成本,实现产品的多规格化和多功能化,推动绿色复合材料向航空航天等高端应用发展。
1.4.3 高性能复合材料绿色化技术
绿色化是材料技术发展的一种必然趋势,涉及多方面的内容,最终目的是要实现在材料产品的整个生命周期内,从设计、选材、成型、使用、回收、再利用的各个阶段对环境影响减到最小。
高性能复合材料的发展主流是用高性能纤维(碳纤维、玻璃纤维、芳纶)与高性能树脂基体(环氧树脂、双马来酰亚胺树脂、聚酰亚胺树脂)复合而成的树脂基复合材料,由于其优异的缩合性能,目前在航空航天等高端领域的应用还处于不可替代的地位,但高性能复合材料是高投入、高成本、高能耗的新材料,近年来绿色化的发展倍受关注,开展了大量的研究。
高性能复合材料绿色化技术包括设计、材料、成型和使用回收等方面的内容。
1.4.3.1 绿色化设计技术[47—49]
在工业化进程中,产品开发一直是沿用“串行式”的设计理念,这种理念下的工作模式是设计、选材、制造、使用、维护是相对独立、互相封闭的,一个阶段工作完成后把结果交给下一部门。但人们发现,这种设计方式有诸多弊端,因为各个环节缺少交流和配合,设计主要考虑产品形状、尺寸和性能等,而很少考虑下游的制造、装配、使用、检测、维修等环节的要求,制造出来的产品,往往还要多次返回进行设计修改,从而造成资源浪费,增加产品成本,延长产品生命周期。
20世纪90年代,出于可持续发展的需要,新型的“并行式”设计理念得到开发和推广,这种方法的核心思想是要求一开始就考虑产品整个生命周期中所有的影响因素,包括质量、成本、资源、能耗、进度、环境和用户要求。这种模式要求设计、制造、产品服务等相关部门协调配合,最终制定最优化的产品开发方案。
设计是复合材料开发应用的第一个重要环节,依据并行式的设计模式,充分利用复合材料性能的可设计性、材料设计与结构设计一体化及大型构件整体成型等优点,综合考虑选材、成型制造、使用维护、成本、环保等因素,实现结构效率、性能、功能与成本的综合优化。
并行工程设计是实现复合材料设计绿色化的切实可行的途径,主要有面向制造和装配(design for manufacturing and assembly,DFMA),此外还有面向环境设计(design for environment,DFE)、面向回收设计(design for recycling,DFR)等,用得最多的是DFMA。
DFMA的主要目的是要提高制件的可制造性和可装配性,提高工效,缩短制造周期,降低成本。而复合材料的材料与结构设计和制造一体化的特点为DFMA提供了广阔的空间,DFMA的主要原则包括:
(1)尽量减少零件数;
(2)减少机械紧固件和连接件;
(3)减少装配方向;
(4)零件易于插装和对准;
(5)使零件易于配合;
(6)使用模块化设计。
现在,DFMA的设计理念和相关产品已广泛应用于汽车、飞机制造、航空和国防等行业。在复合材料设计和制造方面,随着计算机数字化技术的发展,用计算机模拟和仿真技术应用于复合材料的DFMA,已成功地开发出各种专家系统和设计软件,用于各种复合材料的结构设计。大量研究表明,数字化模拟和仿真的各种理论模型可以不同程度地与实际情况相符合。有的技术已发展到非常成熟的阶段,对复合材料设计、优化工艺参数、提高工效、降低成本、保证产品性能和质量发挥具有重要的作用。
1.4.3.2 绿色化材料技术
1.发展可回收的热塑性树脂基复合材料[50—52]
航空航天应用的高性能复合材料,针对热固性树脂,如环氧树脂、双马聚酰亚胺树脂等不能回收和降解的弊端,从20世纪90年代,陆续开发了系列化的高性能热塑性树脂,如聚醚醚酮系列(PEEK)、聚醚砜(PES)、聚苯硫醚(PPS)、聚醚酰亚胺(PEI)等与连续纤维或长纤维复合,制备的复合材料既具有热固性复合材料良好的综合力学性能,又在材料韧性、耐腐蚀性、耐磨性及耐温性方面有明显的优势,在工艺上还具有良好的二次或多次成型和易于回收的特性,有利于资源充分利用和减少环境压力,具有良好的发展和应用前景。目前主要在民航上应用开发。空客在这方面处于领先位置,已从次承力结构件向主承力结构件发展,如空客A-380就采用了玻璃纤维增强的PPS热塑性复合材料制造机翼前沿。
在其他应用领域,有代表性的是长纤维增强的热塑性复合材料(long fiber thermoplastic composites,LFT),具有轻质、高强、抗冲击、耐腐蚀、工艺性能优良、可设计与重复回收利用、绿色环保等卓越性能。在汽车上的应用取得很大进展,主要被用于制作结构和半结构部件,如前端模块、保险杠大梁、仪表盘骨架、电池托架、备用轮胎仓、座椅骨架、脚踏板及整体底板等。长纤维增强聚丙烯被用于轿车的发动机罩、仪表板骨架、蓄电池托架、座椅骨架、轿车前端模块、保险杠、行李架、备胎盘、挡泥板、风扇叶片、发动机底盘、车顶棚衬架等;长纤维增强的聚酰胺(尼龙)被进一步扩展到引擎盖内,高玻璃纤维含量使其热膨胀系数几乎与金属相同,能承受引擎带来的高温。
2.开发可降解的热固性树脂[53,54]
用作高性能复合材料的热固性树脂主要是环氧树脂,具有黏接强度高、耐热性好、抗腐蚀、固化物尺寸稳定、工艺性能好,数十年来,一直是用得最多的复合材料的基体材料,环氧树脂的最高使用温度可达150℃,因此很适合用于民用飞机复合材料结构件的制造,如波音的B-787梦想客机和空客的A-350XWB超宽体客机,复合材料结构用量分别为50%和52%,都是采用环氧树脂作基体材料。
环氧树脂固化物是高交联密度的三维网状分子结构体,不溶、不熔,成为回收再利用的难题。随着大量的使用,环氧复合材料的回收和再生受到更多的关注。
由于环氧树脂在高性能复合材料的作用和地位目前还不能被取代,所以近年来开始了可降解环氧树脂(也称生物环氧树脂)的研究。
实际上,生物环氧树脂的开发可以看成是对环氧树脂进行可降解的改性研究,目前可分为两种方法,一是物理共混,二是化学合成。
物理共混是在环氧树脂中加入可降解的生物高分子材料,如淀粉、天然植物油脂、可生物降解的聚酯等,共混型技术含量较低,树脂最终不能完全降解,但因成本低,目前还有许多应用。
化学合成是将可降解的官能基团引入到环氧分子链中,形成共聚化合物。按机理可分为热降解、光降解和生物降解。
生物降解是目前的研究重点,是将环氧官能团引入可生物降解的聚合物结构中。此类树脂基体中具有被微生物分解的结构,因此易被微生物消化吸收。常用的可生物降解的聚合物有:
(1)聚乙二醇(PEG)。既溶于水又溶于有机溶剂,有较好的生物相容性和端基反应性,分子量范围广、选择余地大,可用于修饰生物降解型聚酯。环氧基封端的聚乙二醇即可作为热固性环氧树脂。
(2)生物降解聚酯。热稳定性和机械性较差。将环氧官能团引入聚酯分子结构,既能保持一定的机械强度,又能被生物降解。合成这类环氧树脂时,环氧官能团数量可以人为控制。酯基易于水解,生成可降解的小分子片段,最后完全降解。
(3)聚氨酯。具有优良的力学强度、高弹性、耐磨性、润滑性、耐疲劳性、生物相容性,是生产可生物降解材料的理想原料。以聚乙二醇、羟基封端的聚己内酯为起始原料合成的聚氨酯型环氧树脂,具有较好的生物降解性能。
可降解环氧的研究近年来取得了实质性进展,如美国复合材料技术服务公司(CTS)开发出用可降解固化剂制备的生物基环氧树脂(bio-based epoxy resin),对碳纤维具有良好的浸润性,用它制成的新一代碳纤维预浸料具有很好的工艺性能,适用于树脂传递模塑、拉挤、纤维缠绕等工艺,制成的复合材料,具有很好的韧性、抗冲击性和剪切性能,可在航空航天、汽车、新能源风电叶片等领域得到应用。
可降解环氧树脂要完全替代高性能的环氧基体作为复合材料的基体,还需要继续研究。
3.高效低成本碳纤维制备新技术[55—60]
碳纤维自20世纪60年代成功用于高性能复合材料增强体以来,轻质高强的优异性能使它一直处于不可替代的地位,但碳纤维是一种高投入、高能耗、高污染的高技术产业,其居高不下的成本一直是困扰业界的主要问题。21世纪初对碳纤维的低成本和绿色化的制备开展了多方面的研究,目前已取得了不少进展,主要有以下几个方面:
(1)开发新型的碳纤维前驱体,也称原丝(precursor),包括造纸副产物的木质纤维素、乙醇生产过程中的副产物等,用以替代高价格的聚丙烯腈原丝。
如美国能源部的橡树岭国家实验室(ORNL)于2007年首次从纤维素乙醇副产物中提取的α-纤维素,通过熔纺和碳化而制备成低成本碳纤维,这种碳纤维就是木质素碳纤维,但迄今尚未产业化。日本森林综合研究所与北海道大学农学研究院成功地开发出由杉树等针叶林的木质素制备碳纤维的技术,木质素碳纤维的抗拉强度可达到以往以石油为原料的通用级碳纤维的水平,制造成本也大体相同。用木质纤维素作原丝,还可解决石化资源日益短缺的问题。这一技术在形成规模化的产业方面,还在继续研究。
用聚烯烃废旧饮料瓶为原料制取原丝已获得突破性进展,有望使成本降低2/3。此外沥青基原丝、腈纶基原丝都可以降低碳纤维成本,其中沥青基碳纤维已经实现产业化规模,具有优异的性能,刚度为钢铁的4.5倍,导热性为铜的2倍,而质量只有铝的2/3,密度为1.7~2.2g/cm3。沥青基原料可取自石化、煤化及造纸的副产物,日本、美国等已形成年产达数百吨至上千吨的规模。
(2)开发低成本的碳纤维制备新工艺。采用干喷湿纺,与传统湿法纺丝相比,干喷湿纺多了一个在空气层中高分子溶液的拉伸步骤,这一改进使高倍的喷丝头拉伸成为可能,同等条件下纺丝速度大幅提高,产量可提高3倍以上,且产品质量也可得到提高。
原丝生产速度的大幅度提高是降低成本最有效的手段,在高纺速的干湿法纺丝工艺基础上,采用特殊相对分子质量组成的聚合体,获得更大倍数的高倍喷丝头拉伸倍数的原液与可稳定经受更高饱和蒸汽拉伸倍数的凝胶体原丝,来达到高速度和高稳定性的原丝制备。
(3)开发大丝束品种。通常每束单丝数大于48000(简称48K)的碳纤维称为大丝束,现在已发展到480K。大丝束能大幅提高纤维的铺放速度,对于大尺寸复合材料制件,如风电叶片,能大幅提高工作效率,缩短生产周期,降低成本。
(4)开发各种新技术。包括从源头的原液聚合、纺丝成型、预氧化、碳化等各个环节,采用新技术能有效提高生产效率,降低能耗和成本。如碳化技术的改进,碳化是制备高性能碳纤维的关键工序,在高性能碳纤维成本中占25%~30%,而且对最终产品的性能有极大的影响。一种新技术是采用微波碳化和石墨化替代上千度的高温加热,大大减少热能的消耗。另外还有预氧化碳化废气零能耗处理和热能回收技术——将预氧化炉和碳化炉内的废气合并进入焚烧炉,在氧气氛围中自主式高温焚烧后的排放气体达到排放标准后排放,同时回收热能,减少了碳排放。
1.4.3.3 绿色化制造技术[61-68]
绿色制造是材料科学和工程发展的必然趋势,是综合考虑环境影响和资源消耗的现代制造模式,其目标是使得产品在制造过程中对环境影响最小,资源利用率最高,使经济效益和社会效益协调优化。
高性能复合材料对制件的性能和质量要求非常严格,必须用专门的设备与方法进行复合材料的成型和制造。成型和制造是关系到复合材料设计思想、复合效应及性能优势能否充分体现的关键,同时也是复合材料高投入、高能耗和高成本的主要原因。数据分析表明,复合材料的制造成本占总成本的50%以上,包括专门设备投入和运作成本、人工成本以及成型过程中高能耗和各种工序引起的成本等。
例如,热压罐成型一直是航空航天复合材料结构的主要成型技术,至今仍在广泛应用。但热压罐设备成本高,如美国航天局(NASA)为固化直径10m的复合材料运载火箭桶身状壳体,专门建造了直径为12m、长度为24m的热压罐,其设备制造、运输、安装耗资超过1亿美元。另外,热压罐成型能耗大。高温型环氧树脂的固化温度在200℃以上,而双马来酰亚胺树脂为250~300℃,聚酰亚胺树脂为350~400℃,固化时间周期为5~8h,后固化处理时间为6h,另外固化过程中要用氮气加压到30~40MPa。此外,设备利用率不高,热压罐一次只能成型一个制件,工效不高,不适合批量生产。
面对居高不下的成本,20世纪90年代开始了复合材料发展的转型,即由“性能第一”转向“性能/成本平衡”,开始实施各种低成本计划,其中最重要的一个方面就是降低制造成本,以树脂传递模塑(RTM)为代表的各种低成本成型技术得到开发和推广应用。其他的低成本化技术还包括低温固化复合材料技术、电子束和微波固化技术、自动铺丝/自动铺带技术等。值得一提的是,为适应复合材料制件向大型化和超大型化发展的趋势,自20世纪90年代开发了一种新的成型技术,即非热压罐成型(out of autoclave,OoA)。
经过20年的技术储备和发展,OoA制备的复合材料大型构件都已满足航空航天结构复合材料的要求。在航天方面,如图1-6所示的大型复合材料低温燃料储罐已成功完成地面试验,超大尺寸储罐的研发也在计划之中。另外,美国NASA更多地采用OoA制造航天器大型复合材料构件,如复合材料乘员舱(composite crew module,CCM)、直径达10m的太空发射系统(space launch syste,SLS)的有效载荷整流罩(payload fairing)等,标志着OoA在航天应用中已进入成熟阶段。
在航空方面,OoA也取得了重要进展。如由洛克希德马丁公司制造的先进复合材料运输机Dornier328,其19.8m长的全复合材料机身的上下蒙皮,波音新一代无人机“幻影眼”(Phantom Eye)制造出11.6m长的翼梁验证件,都用OoA成型。
OoA的目标是不用热压罐而能得到与热压罐成型具有同等性能和质量的复合材料制件,体现出节能的世袭效益,同时还能缩短制造周期,工序简单,灵活方便,能大幅减少工装和运作费用。特别是对于大型或超大型复合材料制件,OoA具有多方面的优势。从绿色化制造发展看,OoA将来也许会打破高性能航空航天复合材料热压罐成型的格局,引发复合材料产业性的变革。
大型或超大型复合材料制件的OoA成型是一种集成化的技术,需要有相关的材料技术、制造技术配套支撑,包括适合于OoA的树脂体系和薄层预浸料、自动铺丝/自动铺带技术、双真空袋成型技术等。
1.4.3.4 绿色化回收再生技术[69—78]
高性能复合材料所用的碳纤维是一种高成本高价位产品,据估算,制备1t碳纤维平均需要至少耗资1万英镑,随着碳纤维的大量使用以及越来越多的退役制件和废弃物的产生,用掩埋或焚烧处理不仅造成资源极大浪费,而且带来极大的环境影响,因此,绿色化的回收和再利用日益受到关注。
21世纪初,美国波音公司、日本东丽公司、英国诺丁汉大学(Nottingham University)和其他材料供应商,包括先进复合材料集团(ACG)、陶氏化学汽车(Dow Automotive)、福特汽车公司(Ford Motor Company)等都实施相关计划,开展碳纤维的回收与再利用的研发。我国中科院宁波材料技术与工程研究所近年来也开展了相关研究,取得了不少进展。
热塑树脂基复合材料的回收相对简单,热塑性树脂的熔/固转换是可逆的,通过加热树脂变成熔融流体就能使纤维分离,这也是今后要加大开发应用热塑性复合材料的重要原因之一。
热塑性树脂基复合材料的回收再生有以下三种方法:
(1)熔融再生法。直接将回收的热塑性树脂基复合材料清洁造粒后重熔,若有必要则加入硅烷等偶联剂,然后用注模压成新的复合材料。
(2)溶解再生法。采用适当的溶剂使热塑性树脂基复合材料废料得以溶解,然后加入沉淀剂分离出聚合物和增强相,过滤后就得到再生材料。
(3)热解法。只需少量的热量及催化剂即可将材料基体转化为低分子量碳氢化合物,以气体形式逸出纤维得以回收。这种方法对回收碳纤维等贵重纤维有良好效果,基本上能保持纤维原有的性能和质量。
相对而言,热固性树脂基复合材料的回收要困难得多,这是因为热固性树脂固化物是一种不溶、不熔的坚实固体,且性能稳定,不易降解。因此,绿色化回收技术的研究主要是针对热固性复合材料。
目前,热固性复合材料的回收和再生主要有:
(1)物理法。机械粉碎回收法作为较早被研究的一种物理回收方法,主要依靠机械设备,通过机械力将热固性树脂及其复合材料碾碎、压碎或切碎等方式,获得尺寸不一的块体颗粒、短纤等物质,具有工艺简单、不产生污染物等优点。如用机械碾压从玻纤增强聚酯基、环氧基、环氧/芳纶纤维复合材料中获得不同长度的纤维,将回收得到的纤维重新与树脂复合,回收纤维复合材料具有很好的力学性能。机械粉碎回收法操作简单,可回收不同长度的短纤及复合材料粒子,但是纤维在回收过程中受到的破坏较大,无法得到长纤维。
(2)热解法。热解法是在空气或惰性气体环境中利用热量使热固性树脂分解成小分子气体逸出的方法。从而得到填料颗粒和表面干净的纤维。这种方法的优点是操作简便,不需要复杂专门的设备,能较好地保持纤维的形态和性能,缺点是能耗较大,树脂裂解产生的低分子气体对环境有污染。
热解法分高温热解、流化床热解和微波热解,这几种方法原理相似,都是通过高温的作用使树脂基体分解,由于高温的作用,回收得到的纤维机械强度降低幅度较大,同时树脂分解产生的小分子气体对环境有影响。在如何降低能耗、充分利用剩余热能、降低污染、保护纤维性能等方面还需继续研究。
(3)超临界流体法。超临界流体法是指流体的温度和压力分别超过其固有的临界温度和临界压力时所处的特殊状态。处于超临界状态的流体具有类似液体的密度和溶解能力,类似气体的黏度和扩散系数,所以超临界流体在一定条件下可以渗入多孔固体材料和溶解有机材料。超临界流体强大的溶解能力可将碳纤维复合材料废弃物的树脂基体分解,从而得到干净的碳纤维,而且能够很好地保留碳纤维的原始性能。工艺条件,包括温度、时间、催化剂、树脂/流体的原料比和压力等因素对回收过程都有影响。
超临界流体法作为一种新的回收方法,具有原料廉价、回收过程清洁无污染,且回收得到的碳纤维表面干净且性能较为优异等优势;但是超临界条件要求比较苛刻,大部分超临界流体要求高温高压,对反应设备的要求比较高,且造价昂贵,安全系数低。目前,超临界流体技术回收热固性树脂复合材料还需要继续研究,实现产业化规模尚存在诸多问题。
综上所述,对于碳纤维增强的热固性树脂基复合材料,绿色化回收及循环再生既要能够把树脂基体从碳纤维上分离开来,保证原纤维的性能和质量不受严重损坏,以利于开发新的应用,同时又要做到整个回收过程的能耗和环境影响降到最低。
每种回收方法都有其优点,也有不可回避的缺点。由于复合材料结构各异,所用树脂基体也千差万别,没有任何一种方法能适合所有复合材料的回收,因此,必须根据复合材料本身的特点,开发合适的回收技术。总体上看,复合材料的回收必然向着绿色环保、低能耗、低污染的方向发展,且要求回收产物具有再利用的价值,满足可持续发展的要求。
参考文献
[1]唐见茂.高性能纤维复合材料[M].北京:化学工业出版社,2013.
[2]MAZUMDAR S K.Composite manufacturing:materials product and process engineering[M].LLC,USA:CRCPress,2002.
[3]朱和国,张爱文.复合材料原理[M].北京:国防工业出版社,2013.
[4]成来飞、殷小玮、张立同.复合材料原理[M].西北工业大学出版社,2016.
[5]MILTON G W.The Theory of Composites[M].UK:Cambridge University Press,2004.
[6]陈祥宝,张宝艳,邢丽英.先进树脂基复合材料技术发展及应用现状[J],中国材料进展,2009,28(6):1-12.
[7]TANG JIAN MAO.Review and prospect of carbon fiber resin matrix composites[J].Spacecraft Environment Engineering,2010,27(3):269-280.
[8]郭玉明,冯志海,王金明.高性能PAN基碳纤维及其复合材料在航天领域的应用[J].高科技纤维与应用,2007,32(5):1-8.
[9]TANG JIANMAO,STEPHEN K L LEE.Recent progress of applications of advanced composite materials in aerospace industry[J].Spacecraft Environment Engineering,2010,27(5):552-557.
[10]STEITZ D E.NASA tests game changing composite cryogenic fuel tank[R/OL],http://www.nasa.gov/press/2013/july.
[11]JEFF SLOAN.AFP/ATL evolution[J/OL].High-Performance Composites,2014-3,http://www.compositesworld.com/articles/afpatl-evolution.
[12]Northrop Grumman & ATK Complete James Webb Backplane Testing[R/OL],http://www.compos-itestoday.com/2014/07/northrop-grumman-atk-complete-james-webb-backplane-testing.
[13]陈绍杰.先进复合材料在汽车领域的应用[J].高科技纤维与应用,2011,36(1):18-24.
[14]蒋鞠慧,陈敬菊.复合材料在轨道交通上的应用与发展[J].玻璃钢/复合材料,2009,(6):81-85.
[15]邹志华,曾竟成,刘钧.高速列车及其用复合材料的发展[J].材料导报A:综述篇,2011,(21):112-1185.
[16]牟书香,陈淳,邱桂杰.碳纤维复合材料在风电叶片中的应用[J].新材料产业,2012,(2):32-36.
[17]孙正军,任海青.先进生物质复合材料在风电叶片中的应用[J].复合材料学报,2006,23(3):127-129.
[18]施军,黄卓.复合材料在海洋船舶中的应用[J].玻璃钢/复合材料,2012,(11):275-279.
[19]代志双,宋平娜,高志涛.纤维复合材料在海洋油气开发中的应用[J].海洋工程装备与技术,2014,(3):65-69.
[20]彭福明,郝际平,岳清瑞.碳纤维增强复合材料(CFRP)加固修复损伤钢结构[J].工业建筑,2003,(9):7-10.
[21]ROUISON D,SAIN M,COUTURIER M.Resin transfer molding of hemp fibercomposites:optimization of the process and mechanical properties of the materials[J].Composites Science and Technology,2006,66(78):895-906.
[22]ROUISON D,SAIN M,COUTURIER M.Resin-transfer molding of natural fiber–reinforced plastic.I.Kinetic study of an unsaturated polyester resin containing an inhibitor and various promoters[J].Journal of Applied Polymer Science,2003,89(9):2553-2561.
[23]BROSIUS D.Out-of-autoclave manufacturing:The green solution [J/OL],High-Performance Composites,2014-01.
[24]PICKERING S J.Recycling technologies for thermoset composite materials——current status[J].Composites:Part A,2006,(37):1206-1215.
[25]PATEL V.Composites recycling:market opportunity analysis[J].FRP Today,2010,(4):23-27.
[26]RUSHS.Carbonfiber:Life Beyond the Landfill[J/OL].High-Performance Composites,2007-5-1.http://www.compositesworld.com/articles/carbon-fiber-life-beyond-the-landfill.
[27]THAKURV K.Greencomposites:polymer composites and the environment[M].New York:CRC Press,2005:5-15.
[28]THAKURVK.Green composites from natural resources[M].New York:CRCPress,2013:2-15.
[29]TICOALU A,ARAVINTHAN T,CARDONA F.A review of current development in natural fiber composites for structural and infrastructure applications[J].Proceedings of the Southern Region Engineering Conference,2010:1(5):11-12.
[30]曹勇,合田公一,陈鹤梅.绿色复合材料的研究进展[J].材料研究学报,2007,21(2):119-125.
[31]李光哲.木塑复合材料的研究热点及发展趋势[J].木材加工机械,2010,(2):41-44.
[32]刘涛,何慧,洪浩群,等.木塑复合材料研究进展[J].绝缘材料,2008,41(2):38-41.
[33]欧阳平凯,姜岷,李振江,等.生物基高分子材料[M].北京:化学工业出版社,2012.
[34]李坚.生物质复合材料学[M].北京:科学出版社,2008.
[35]封硕.生物可降解高分子材料研究综述[J].中山大学研究生学刊,2012,31(1):29-32.
[36]PICKERING K.Properties and performance of natural fiber composites[M].Oxford:Woodhead Publishingin Materials,2008.
[37]GAULT ML.Bio-composites update:Beyond eco-branding[J/OL].Composites Technology,2013,06,http://www.compositesworld.com/articles/biocomposites-update-beyond-eco-branding.
[38]董凤霞,刘文,刘红峰.纳米纤维素的制备及应用[J].中国造纸学报2012,增刊:466-472.
[39]范子千,袁晔,沈青.纳米纤维素研究及应用进展[J].高分子通报,2010,(3):40-60.
[40]周素坤,毛键贞,许凤,等.微纤化纤维素的制备及应用[J].化学进展,2014,26(10):1752-1762.
[41]卿彦,蔡智勇,吴义强.纤维素纳米纤丝研究进展[J].林业科学,2012.48(7):145-152.
[42]李勍,陈文帅,于海鹏.纤维素纳米纤维增强聚合物复合材料研究进展[J].林业科学,2013,49(8):145-152.
[43]PANDEYJK,AHNLS H,LEECS,et al.Recent advances in the application of natural fiber based composites[J].Macromolecular Materials and Engineering,2010,295(11):975-989.
[44]SHAH D U.Developing plant fibre composites for structural applications by optimising composite parameters:a critical review[J].2013,48(18):6083-6107.
[45]ZAMIR A,SALIT M S,TAHIR S M,et al.A review of current development in natural fiber composites in automotive applications[J].Applied Mechanics and Materials,2014,(564):3-7.
[46]DAVID B.Critical review of recent publications on use of natural composites in infrastructure[J].Com-posites Part A:Applied Science and Manufacturing,2012,43(8):1419-1429.
[47]布斯劳.面向制造与装配的产品设计[M].北京:机械工业出版社,1999.
[48]王咏梅.浅谈国内复合材料设计制造一体化技术[J].航空制造技术2012,(18):41-44.
[49]马瑛剑,宫少波,齐德胜.复合材料部件设计制造一体化研究[J].化学与粘合,2010,(2):30-34.
[50]王兴刚,于洋,李树茂,等.先进热塑性树脂基复合材料在航天航空上的应用[J].纤维复合材料,2011,27(2):4447.
[51]BLACK S.Reinforced thermoplastics in aircraft primary[J/OL].High-Performance Composites,2011,(5):http://www.compositesworld.com/articles/reinforced-thermoplastics-in-aircraft-primary-structure.
[52]马鸣图,魏莉霞,朱丽娟.塑料复合材料在汽车轻量化中的应用[J].化工新型材料,2011,39(11):1-3.
[53]王新波,黄龙男.降解型环氧树脂[J].化学进展,2009,21(12):2704-2711.
[54]杨萍.降解型环氧树脂用于可持续碳纤维复合材料[J].玻璃钢,2013(4):42-46.
[55]Composite Technical Services,LTD.Bio-based epoxy resin for next generation epoxy prepregs[N/OL],www.azom.com/news.aspx?newsID=30774.
[56]MA S,LIU X,FAN L,et al.Synthesis and properties of a bio-based epoxy resin with high epoxyvalue and low viscosity[J].Chem Sus Chem,2014,7(2):555-562.
[57]BAKER D A,RIALST G.Recent advances in low-cost carbon fiber manufacture from lignin[J].Journal of Applied Polymer Science,2013,130(2):713-728.
[58]WARREN C.Low-cost carbon fiber:Real or just wishful thinking?[J/OL].Composites Technology,2003,12,http://www.compositesworld.com/columns/low-cost-carbon-fiber-real-or-just-wishful-thinking.
[59]梁燕,金亮,潘鼎.碳纤维低成本制备技术[J].高科技纤维与应用,2011,36(2):39-44.
[60]韩克清,严斌,余木火.碳纤维及其复合材料高效低成本制备技术进展[J].中国材料进展,2012,31(10):30-36.
[61]包建文.高效低成本复合材料及其制造技术[M].北京:国防工业出版社,2012.
[62]GARDINER.Out-of-prepregs:hype or revolution?[J/OL].High-Performance Composites,2011-01-01,http://www.compositesworld.com/articles/out-of-autoclave-prepregs-hype-or-revolution.
[63]DALE B.Out-of-autoclave manufacturing:the green solution,[J/OL].High-Performance Composites,2014-01-01,http://www.compositesworld.com/articles/out-of-autoclave-manufacturing-the-green-solution.
[64]North Thin Ply Technology.Prepreg materials [R/OL].2014-11-16.http://www.thinplytechnology.com/prepreg-materials.php.
[65]JEFF S.AFP/ATL evolution[J/OL].High-Performance Composites,2014-03-4.http://www.com-positesworld.com/articles/afpatl-evolution.
[66]HOUT H,JENSENB J.Evaluation of double-vacuum-bag process for composite fabrication[J/OL].2013-11-30,http://www.researchgate.net/publication/250043379_Evaluation_of_Double-Vacuum-Bag_Process_For_Composite_Fabrication.
[67]罗云烽,彭公秋,曹正华.航空用热压罐外固化预浸料复合材料的应用[J].航空制造技术,2012(18):26-31.
[68]唐见茂.航空航天复合材料非热压罐成型研究进展[J].航天器环境工程,2014,31(6):572-583.
[69]PIMENTA S,PINHO S T.Recycling carbon fiber reinforced polymers for structural applications:Technology review and market outlook[J].Waste Management,2011,(31):378-392.
[70]段志军,段望春,张瑞庆.国内外复合材料回收再利用现状[J].塑料工业,2011,39(1):14-18.
[71]YANG Y,BOOM R,HEERDEN D J V,et al.Recycling of composite materials[J].Chemical Engineering and Processing,2012,(51):53-68.
[72]张东致,万怡灶,罗红林.碳纤维复合材料的回收与再利用现状[J].中国塑料,2013,27(2):1-6.
[73]BOURMAUD A.Investigations on the recycling of hemp and sisal fibre reinforced polypropylene composites[J].Polymer Degradation and Stability,2007,92(6):1034-1045.
[74]MISHRA R,BEHERA B,MILITKY J,et al.Recycling of textile waste into green composites:Performance characterization[J].Polymer Composites,2014,35(10):1960-1967.
[75]PINERO-HERNANZ R,GARCÍA-SERNAA J,DODDS C,et al.Chemical recycling of carbon fibre composites using alcohols under subcritical and supercritical conditions[J].The Journal of Supercritical Fluids,2008,46(1):83-92.
[76]罗益锋.碳纤维复合材料废弃物的回收与再利用技术发展[J].纺织导报,2013(12):36-39.
[77]ASMATULU E,TWOMEY J,OVERCASH M.Recycling of fiber-reinforced composites and direct structural composite recycling concept[J].Journal of Composite Materials,2014,48(5):593-608.
[78]徐平来,李娟,李晓倩.热固性树脂基复合材料的回收方法研究进展[J].工程塑料应用,2013,41(1):100-104.