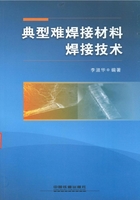
十、如何采用超声冲击处理技术提高铝合金焊接接头的强度?
目前,国内大多数企业生产过程中仍然采用氩弧焊作为焊接铝合金的主要焊接方法,由于该方法在焊接过程要输入大量的热,焊接件容易产生较大的焊接残余应力,同时焊缝两侧和填充材料经过焊接过程的重新熔化和冷却过程的再结晶,会在焊缝处形成铸态组织,焊缝也容易出现气孔、缩松等焊接缺陷,造成焊后接头强度降低,使其铝合金的应用受到了较大限制。
为改善高强铝合金焊接接头的力学行为,提高接头力学性能,国内外进行了大量的理论研究和试验研究,从力学角度和冶金角度开发出了多种强化焊接接头的方法。这些方法虽然能较好地提高铝合金焊接接头的强度,但均存在一定的不足。目前,有研究者研究了超声冲击处理技术,利用该技术处理焊接后的铝合金焊缝收到了较好的效果。超声冲击处理技术是近年来发展起来的提高焊接接头疲劳强度的方法,相对于传统的其他焊后处理技术,该技术在降低应力方面效果比较明显,处理后的焊缝强化层深度大,而且处理成本低、能耗少,尤其是该方法便于野外现场作业,因此是一种较为理想的改善焊接接头性能的方法。
例如,针对焊接基材板厚分别为6mm和4mm的2A12铝合金板材进行焊接和超声冲击处理,2A12铝合金板材为T4态,焊接用焊丝选用ER5356铝镁合金焊丝,焊丝直径为2.5mm。基材与焊丝的主要化学成分见表1-3。
表1-3 2A12铝合金和ER5356焊丝化学成分

焊接工艺采用手工交流氩弧焊(TIG),焊接过程采用无拘束双面焊接,焊接工艺参数见表1-4。
表1-4 焊接工艺参数

焊件的超声冲击处理是将焊后的试样平置于工作台上,使用ZJ-Ⅱ超声冲击设备沿焊接接头进行全覆盖冲击处理(处理过程如图1-4所示)。超声冲击处理的道次为3次。超声冲击处理设备工作的电流为0.8~1.0A,振动频率为20kHz,静压力为50N。

图1-4 超声冲击处理工艺过程
超声冲击处理前后焊接接头焊缝区的显微组织如图1-5所示。由图1-5(a)可见,未处理的焊缝主要为铸态的枝晶组织,这种铸态组织晶粒较粗大,而且晶粒大小很不均匀,组织也不致密,粗大的枝晶形结构弱化了晶界的连接,在外力作用下容易沿晶断裂,使焊接接头的拉伸性能变差。超声冲击处理后的组织如图1-5(b)所示,超声冲击处理中剧烈的塑性变形可致使焊缝表层的显微组织发生明显的变化,使晶粒尺寸大幅减小,组织更加致密。

图1-5 超声冲击处理前后焊缝区表层显微组织
理论上,由Hall-Petch公式可知,焊缝区组织的晶粒越细小,焊缝的强度就会越高。同时,晶粒细化还能有效改善焊缝的韧性。其主要原因是细小的晶粒可以使材料断裂前就能够承受更大程度的变形,使焊缝强度提高的同时韧性也得以提高。
在工程上,不少焊件是受静载荷作用的。为了解超声冲击处理对铝合金焊接接头静载力学性能的影响,有研究者对铝合金板材、超声冲击处理进行了静载荷拉伸试验。图1-6为6mm厚2A12铝合金母材试样拉伸应力-应变曲线。

图1-6 6mm厚2A12铝合金板材应力-应变曲线
由图1-6可见,载荷比较小时,试样伸长随载荷增加而增加,该过程为弹性变形阶段;当载荷超过A点后,拉伸曲线开始偏离直线,试样在继续产生弹性变形的同时将产生塑性变形,进入弹塑性变形阶段;当载荷上升至B点时,试样产生断裂。试样在拉伸过程中由弹性变形过渡到明显塑性变形,中间经历了屈服阶段,拉伸曲线上出现了平台(AB段)。试样从变形开始到断裂的全过程是由弹性变形、塑性变形和断裂3个阶段组成,断裂前出现明显的塑性变形,属于韧性断裂。试样的峰值应变在0.26~0.28之间,峰值应力在460~470MPa之间。经计算,6mm厚2A12铝合金板材的抗拉强度为465MPa,峰值应变为0.272。
超声冲击处理前后6mm和4mm铝板焊接接头在与母材同一加载形式下的拉伸应力-应变曲线如图1-7所示。由图1-7可见,未处理焊接接头试样主要由弹性变形和断裂2个阶段组成,断裂前塑性变形程度很小,属于脆性断裂,断裂前没有明显的征兆,此种情形危害性很大。经超声冲击处理的4mm铝板焊接接头试样从变形开始到断裂的全过程是由弹性变形、塑性变形和断裂3个阶段组成,断裂前也出现了较为明显的塑性变形阶段,拉伸曲线上出现了锯齿(如图1-7(d)中的CD段所示),但塑性变形阶段较短,属于韧性-脆性混合断裂。未经超声冲击处理的6mm和4mm试样的峰值应变在0.07~0.09之间,峰值应力在190~210MPa之间;超声冲击处理后试样的峰值应变在0.08~0.12之间,峰值应力在220~270MPa之间。计算结果表明,超声冲击处理后的6mm和4mm厚的2A12铝合金板材焊接接头的拉伸强度分别提高了17.4%和23.7%,延伸率提高了28%和44%。超声冲击处理同时提高了铝合金焊接接头的断裂强度及韧性,对于薄板焊接接头效果更为明显,可见该方法是一种较为理想的改善焊接接头力学性能的方法。
6mm厚铝合金母材经超声冲击处理前后焊接接头试样拉伸断裂宏观形貌如图1-8所示。从图1-8可以看出,母材试样拉伸断裂前都产生了明显的颈缩,断口呈现出剪切特征,剪切断裂面和拉伸载荷轴的夹角大约呈45°;未处理试样在焊趾部位萌生裂纹并基本上沿熔合线断裂;经超声冲击处理过的试样均断裂在焊缝部位。熔合区存在严重的物理和化学不均匀性,使得该区域成为焊接接头一个较薄弱的区域,所以未处理试样会在熔合区沿熔合线断裂,经超声冲击处理的试样断裂在焊缝区域。以上现象说明,超声冲击处理不但有效地强化了焊接接头薄弱的焊趾部位,而且还降低了焊趾部位的应力集中。但是,由于焊接接头余高的存在,使得焊缝中部断面较厚,超声冲击处理对焊缝芯部的作用就有所减弱,这也是造成有些焊接件超声冲击处理后在焊缝中部断裂的主要原因。

图1-7 超声冲击处理前后6mm和4mm铝板焊接接头在与母材同一加载形式下的拉伸应力-应变曲线

图1-8 6mm厚铝合金母材经超声冲击处理前后焊接接头拉伸断裂宏观形貌
焊接接头拉伸试样宏观断口形貌如图1-9所示。从图1-9可以看出,未经处理试样裂纹源位于焊缝中心夹杂处(如图1-9中箭头处所示),由裂纹源向四周扩展,存在明显的放射状区域,断口表面粗糙,属于典型的脆性断裂;经超声冲击处理试样无明显的放射线区域,裂纹不连续,而且多是局部扩展,断口表面相对细腻,没有发现粗大的棱线。未经处理的焊接接头的熔合区由于存在较多的焊接缺陷密集,使这个区域晶界的键合力被严重削弱,从而发生沿晶断裂。全覆盖超声冲击处理后,整个焊接接头的表层晶粒细化,组织结构更加均匀一致,使裂纹扩展方式发生改变,多为局部扩展。

图1-9 超声冲击处理与未超声冲击处理焊接接头拉伸试样宏观断口形貌
以上结果也说明焊接中2A12铝合金板材焊接工艺参数的选择也比较合理,焊后焊接接头的超声冲击处理工艺完全可以用来提高铝合金焊接接头的抗拉伸性能。未经超声冲击处理的焊接接头拉伸试样断裂发生在焊趾和熔合区,处理后断口均在焊缝中部断面,表明超声冲击处理使焊接接头薄弱的焊趾部位得到了有效强化。其中,超声冲击处理后焊接接头晶粒大幅细化、缺陷减少和组织致密化是提高铝合金焊接接头抗拉伸性能的主要原因。