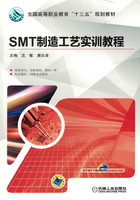
1.1 SMT概述
SMT是英文Surface Mounting Technology的缩写,中文意思是:表面贴装技术。它是相对于传统的贯通孔插件焊接技术(Through-HoleTechnology,THT)而发展起来的一种新的组装技术,也是目前电子组装行业里最流行的一种技术和工艺。SMT是在印制电路板(Printed Circuit Board,PCB)基础上进行加工的系列工艺流程的简称。
从广义上来讲,SMT是表面安装元件(Surface Mount Component,SMC)、表面安装器件(Surface Mount Device,SMD)、表面安装印制电路板(Surface Mount print circuit Board,SMB)以及普通混装印制电路板点胶、涂膏、表面安装设备、元器件取放、焊接和在线测试等技术过程的统称。
SMT是将表面组装元器件贴装到指定的涂覆了焊膏或粘合剂的印制电路板(PCB)焊盘上,然后经过回流焊接或波峰焊接方式使表面组装元器件与PCB焊盘之间建立可靠的机械和电气连接的技术。
如今电子行业飞速发展,电子产品追求小型化,以前使用的穿孔插件元器件已无法缩小。电子产品功能更完整,所采用的集成电路(IC)已无穿孔元器件,特别是大规模、高集成IC,不得不采用表面贴片元器件。产品批量化,生产自动化,厂方要以低成本高产量,出产优质产品以迎合顾客需求及加强市场竞争力。电子元器件的发展,集成电路(IC)的开发,半导体材料的多元应用促使电子科技革命势在必行,可以想象,在Intel、AMD等国际IC器件的生产商的生产工艺精进到20多纳米的情况下,SMT这种表面组装技术和工艺的发展也是不得以而为之的情况。
SMT贴片加工的优点:组装密度高、电子产品体积小、重量轻,贴片元件的体积和重量只有传统插装元器件的1/10左右,一般采用SMT之后,电子产品体积缩小40%~60%,重量减轻60%~80%;可靠性高、抗振能力强,焊点缺陷率低;高频特性好;减少了电磁和射频干扰;易于实现自动化,提高生产效率;降低成本达30%~50%;节省材料、能源、设备、人力和时间等。
1.1.1 SMT的特点
SMT是在THT基础上发展起来的,SMT与THT二者的比较详如图1-1所示。在图1-1a中,大多数元器件与其引脚都位于印制电路板(PrintedCircuitBoard,PCB)的同一面上,而在图1-1b中,元器件的引脚要穿过PCB,焊点与元器件位于PCB的不同面上。在PCB同一面上完成元器件引脚和PCB焊盘粘合的技术,就称为SMT,即表面贴装技术。

图1-1 SMT与THT的比较
a)SMT b)THT
表1-1较详细介绍了SMT与THT两种技术的特点。
表1-1 SMT与THT两种技术的特点比较

1.1.2 SMT的优点
(1)组装密度高
由于表面贴装元器件(SMC/SMD)在体积和重量上都大大减小,为此,PCB的单位面积上元器件数目自然也就增多了。
(2)可靠性高
由于片式元器件小而轻,抗振动能力强,自动化生产程度高,故贴装可靠性高。目前几乎所有中、高端电子产品都采用SMT工艺。
(3)高频特性好
由于片式元器件通常为无引线或短引线器件,因此在PCB设计方面,可降低寄生电容的影响,提高电路的高频特性。采用片式元器件设计的电路最高频率可达3GHz,而采用通孔元件仅为500MHz。
(4)降低成本
使用PCB的面积减小,一般为通孔PCB面积的1/12;PCB上钻孔数量减小,节约返修费用;频率特性提高,减少了电路调试费用;片式元器件体积小、重量轻,减少了包装、运输和储存费用。片式元器件发展快,成本迅速下降,价格也相当低。
(5)便于自动化生产
SMT采用自动贴片机的真空吸嘴吸放元件,真空吸嘴小于元件外形,为此可完全自动化生产;而穿孔安装印制板要实现完全自动化,则需扩大原PCB面积,这样才能使自动插件的插装头将元件插入,若没有足够的空间间隙,将碰坏零件。
(6)SMT的不足
厂家初始投资大,生产设备结构复杂,涉及技术面宽,费用昂贵;由于元器件微小,则电子产品维修工作困难,需专用工具;另外在加工过程中元器件与印制板之间热膨胀系数(CTE)要一致等。