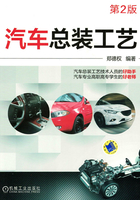
第二节 工艺相关术语
一、工艺术语
(1)工艺 使各种原材料、半成品成为产品的方法和过程;是利用生产工具对原材料、毛坯、半成品进行加工,改变其几何形状、外形尺寸、表面状态和内部组织的方法。
(2)总装工艺 是汽车全部制造工艺过程的最终环节,是把经检验合格的数以千万计的各类零件,按规定的精度标准和技术要求组合成分总成、总成、整车,并经严格检测程序,确认其是否合格的整个工艺过程。
(3)机械制造工艺 各种机械的制造方法和过程的总称。
(4)汽车制造工艺 汽车在成为产品的过程中所运用的制造方法和生产过程。
(5)典型工艺 根据零件的结构和工艺特征进行分类、分组,对同组零件制订的统一加工方法和过程。
(6)产品结构工艺性 所设计的产品在能满足使用要求的前提下,制造、维修的可行性和经济性。
(7)零件结构工艺性 所设计的零件在能满足使用要求的前提下,制造的可行性和经济性。
(8)工艺性分析 在产品技术设计阶段,工艺人员对产品结构工艺性进行分析和评价的过程。
(9)可加工性 在一定生产条件下,材料加工的难易程度。
(10)生产过程 将原材料转变为产品的全过程。
(11)工艺过程 改变生产对象的形状、尺寸、相对位置和性质等,使其成为成品或半成品的过程。
(12)工艺文件 指导工人操作和用于生产、工艺管理的各种技术文件。
(13)工艺方案 根据产品设计要求、生产类型和企业生产能力,提出工艺技术准备工作具体任务和措施的指导性文件。
(14)工艺路线 产品或零部件在生产过程中,由毛坯准备到成品包装入库,经过企业各有关部门或工序的先后顺序。
(15)工艺规程 规定产品或零部件制造工艺过程和操作方法等的工艺文件。
(16)工艺设计 编制各种工艺文件和设计工艺装备等的过程。
(17)工艺要素 与工艺过程有关的主要因素。
(18)工艺规范 对工艺过程中有关技术要求所做的一系列统一规定。
(19)工艺参数 为了达到预期的技术指标,工艺过程中所需选用或控制的有关量。
(20)工艺准备 产品投产前所进行的一系列工艺工作的总称。其主要内容包括:对产品图样进行工艺性分析和审查;拟订工艺方案;编制各种工艺文件;设计、制造和调整工艺装备;设计合理的生产组织形式等。
(21)工艺试验 为考查工艺方法、工艺参数的可行性或材料的可加工性等而进行的试验。
(22)工艺验证 通过试生产,检验工艺设计的合理性。
(23)工艺管理 科学地计划、组织和控制各项工艺工作的全过程。
(24)生产纲领 企业在计划期内应当生产的产品量和进度计划。
(25)生产类型 企业生产专业化程度的分类。一般分为大批量生产、成批生产和单件生产三种类型。
(26)生产批量 一次投入或产出的同一产品或零件的数量。
(27)生产周期 生产某一产品或零件时,从原材料投入到出产品一个循环所经过的日历时间。
二、生产对象
(1)原材料 投入生产过程以创造新产品的物质。
(2)主要材料 构成产品实体的材料。
(3)辅助材料 在生产中起辅助作用而不构成产品实体的材料。
(4)毛坯 根据零件(或产品)所要求的形状、工艺尺寸等制成的供进一步加工用的生产对象。
(5)工件 加工过程中的生产对象。
(6)外协件 由本企业提供设计图样资料,委托其他企业完成部分或全部制造工序的零部件。
(7)在制品 在一个企业的生产过程中,正在进行加工、装配或待检查验收的制品。
(8)半成品 在一个企业的生产过程中,已完成一个或几个生产阶段,经检验合格入库尚待继续加工或装配的制品。
(9)成品 在一个企业内完成全部生产过程,可供销售的制品。
(10)合格品 通过检验质量特性符合标准要求的制品。
(11)不合格品 通过检验质量特性不符合标准要求的制品。
(12)废品 不能修复又不能降级使用的不合格品。
三、工艺方法
(1)铆接 借助铆钉形成的不可拆连接。
(2)粘接 借助粘结剂形成的连接。
(3)装配 按规定的技术要求,将零件或部件进行配合和连接,使之成为半成品或成品的工艺过程。
四、工艺要素
(1)工序 一个或一组工人,在一个工作地对同一个或同时对几个工件所连续完成的那一部分工艺过程。
(2)安装 工件(或装配单元)经一次装夹后所完成的那一部分工序。
(3)工步 在加工表面(或装配时的连接)和加工(或装配)工具不变的情况下,所连续完成的那一部分工序。
(4)工位 为了完成一定的工序部分,一次装夹工件后,工件(或装配单元)与夹具或设备的可动部分一起相对刀具或设备的固定部分所占据的每一个位置。
(5)基准 用来确定生产对象上几何要素间的几何关系所依据的那些点、线、面。
(6)设计基准 设计图样上所采用的基准。
(7)工艺基准 在工艺过程中所采用的基准。
(8)工序基准 在工序图上用来确定本工序所加工表面加工后的尺寸、形状、位置的基准。
(9)定位基准 在加工中用作定位的基准。
(10)测量基准 测量时所采用的基准。
(11)装配基准 装配时用来确定零件或部件在产品中的相对位置所采用的基准。
(12)辅助基准 为满足工艺需要,在工件上专门设计的定位面。
(13)工艺孔 为满足工艺(加工、测量、装配)的需要而在工件上增设的孔。
(14)工艺凸台 为满足工艺的需要而在工件上增设的凸台。
(15)工艺尺寸 根据加工的需要,在工艺附图或工艺规程中所给出的尺寸。
(16)工序尺寸 某工序加工应达到的尺寸。
(17)尺寸链 互相联系且按一定顺序排列的封闭尺寸组合。
(18)工艺尺寸链 在加工过程中的各有关工艺尺寸所组成的尺寸链。
(19)材料消耗工艺定额 在一定生产条件下,生产单位产品或零件所需消耗的材料总质量。
(20)材料工艺性消耗 产品或零件在制造过程中,由于工艺需要而损耗的材料。
(21)材料利用率 产品或零件的净重占其材料消耗工艺定额的百分比。
(22)设备负荷率 设备的实际工作时间占其台时基数的百分比。
(23)加工误差 零件加工后的实际几何参数(尺寸、形状和位置)对理想几何参数的偏离程度。
(24)加工精度 零件加工后的实际几何参数(尺寸、形状和位置)与理想几何参数的符合程度。
(25)加工经济精度 在正常加工条件下(采用符合质量标准的设备、工艺装备和标准技术等级的工人,不延长加工时间)所能保证的加工精度。
(26)表面粗糙度 加工表面上具有的较小间隙和峰谷所组成的微观几何形状特性,一般由所采用的加工方法和其他因素形成。
(27)工序能力 工序处于稳定状态时,加工误差正常波动的幅度。通常用6倍质量特性值分布的标准偏差表示。
五、装配与试验术语
(1)配套 将待装配产品的所有零、部件配备齐全。
(2)部装 把零件装配成部件的过程。
(3)总装 把零件和部件装配成最终产品的过程。
(4)吊装 对大型零、部件,借助于起吊装置进行的装配。
(5)试装 为保证产品总装质量而进行的各连接部位的局部试验性装配。
(6)装配尺寸链 各有关装配尺寸所组成的尺寸链。
(7)预载 对某些产品或零部件在使用前所需预加的载荷。
(8)静平衡试验 调整产品或零部件使其达到静态平衡的过程。
(9)动平衡试验 对旋转的零部件,在动平衡试验机上进行试验和调整,使其达到动态平衡的过程。
(10)试车 整车装配后,按技术要求进行的动态试验。
(11)性能试验 为测定产品或其零部件的性能参数而进行的各种试验。
(12)寿命试验 按照规定的使用条件(或模拟其使用条件)和要求,对产品或其零部件的寿命指标所进行的试验。
(13)噪声试验 按规定的条件和要求,对产品所产生的噪声大小进行测定的试验。
六、工艺装备与工件装夹
(1)工艺装备(工装) 产品制造过程中所用的各种工具总体;包括刀具、夹具、模具、量具、检)具、辅具、钳工工具和工位器具等。
(2)通用工艺装备 能为几种产品所共用的工艺装备。
(3)标准工艺装备 已纳入标准的工艺装备。
(4)专用工艺装备 专为某一产品所用的工艺装备。
(5)成组工艺装备 根据成组技术的原理,专对一组或一族相似零件进行设计的、由基础部分和可换调整部分组成的、用于成组加工的工艺装备。
(6)可调工艺装备 通过调整或更换工艺装备零、部件,以适用于几种产品零、部件加工的工艺装备。
(7)组合工艺装备 由可以循环使用的标准零、部件(必要时可配用部分专用件)组装成易于连接和拆卸的工艺装备。
(8)跨产品借用工艺装备 被同品种不同型号的产品借用的专用工艺装备。
(9)组合夹具 由可以循环使用的标准夹具元件、合件配套组成;根据工艺要求能组装成容易连接和拆卸的夹具。
(10)专用工艺装备设计任务书 由工艺人员根据工艺要求,对专用工艺装备设计提出的一种指示性文件,作为工艺装备设计人员进行工艺装备设计的依据。
(11)工艺装备验证 工艺装备制造完毕后,通过试验、检验、试用,考核其合理性的过程。
(12)工艺装备验证书 记载新工艺装备验证结果的一种工艺文件。
(13)工艺装备通过系数 工艺装备通用的产品零、部件种数与工艺装备种数的比值。
(14)工艺装备利用率 实际使用的工艺装备种数与为保证产品生产大纲所必需的工艺装备设计种数的比值。
(15)工艺装备负荷率 在产品生产计划期内,工艺装备实际工作时与总的有效时间的比值。
(16)工艺装备计算消耗费用 按工艺装备设计、制造定额计算的成本费用。
(17)工艺装备额定消耗费用 在产品的试制阶段和正式生产阶段所规定的工艺装备设计、制造费用。
(18)专用工艺装备系数 产品专用工艺装备种数与产品专用件种数的比值。
(19)工艺装备复杂系数 表示工艺装备复杂程度的数值。以其成本、件数、精度以及保证产品尺寸要求的计算尺寸数目和总体尺寸等诸因素来确定。
(20)工艺装备复杂等级 表示工艺装备复杂程度的级别,是对工艺装备进行技术经济评价,完善工艺装备设计、制造、使用过程的管理。一般可依据复杂系数划分为A级、B级、C级等。
(21)装夹 将工件在机床上或夹具中定位夹紧的过程。
(22)定位 确定工件在机床上或夹具中占有正确位置的过程。
(23)夹紧 工件定位后将其固定,使其在加工中保持定位位置不变的操作。