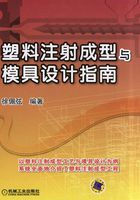
4.1 注射模具的结构
注射成型模具是用闭合和开启的型腔,成型一定形状和尺寸塑料制品的工具。本节介绍单分型面、双分型面和侧向分型抽芯三种典型的注射模结构。
4.1.1 注射模具的结构组成和分类
1.注射模的结构组成
凡是注射模,均可分为动模和定模两大部件。注射充模时,动模与定模闭合,构成型腔和浇注系统;开模时,动模与定模分离,取出制件。定模安装在注射机的固定板上;动模则安装在注射机的移动模板上。
图4-1为典型的单分型面注射模。根据模具上各个零部件的不同功能,可由以下七个系统机构组成。
图4-1 单分型面注射模
a)闭合充模 b)开模取件
1—定位环 2—主流道衬套 3—凹模 4—型芯 5—顶杆 6—拉料杆 7—顶出固定板 8—顶出板 9—动模座 10—回程杆 11—动模垫板 12—动模板 13—导柱 14—导套 15—冷却水管道 16—定模板 17—定模安装板
(1)成型零件 指构成型腔,直接与熔体相接触并成型塑料制件的零件。通常有凸模、型芯、成型杆、凹模、成型环、镶件等零件。在动模和定模闭合后,成型零件确定了注塑件的内部和外部轮廓和尺寸。图4-1所示模具的型腔是由凹模3、型芯4和动模板12构成的。
(2)浇注系统 将塑料熔体由注射机喷嘴引向型腔的流道称为浇注系统,由主流道、分流道、浇口和冷料井组成。图4-2为单分型面注射模上的浇注系统。
(3)导向与定位机构 为确保动模和定模闭合时,能准确导向和定位对中,通常分别在动模和定模上设置导柱和导套。深腔注射模还必须在主分型面上设有锥面定位。有时为保证脱模机构的准确运动和复位,顶出固定板7和顶出板8也设置导向零件。
(4)脱模机构 是指在开模过程的后期,将注塑件从模具中脱出的机构。图4-1中脱模机构由顶杆5、拉料杆6、顶出固定板7、顶出板8及回程杆10组成。
(5)侧向分型抽芯机构 带有侧凹或侧孔的注塑件,在被脱出模具之前,必须先进行侧向分型或拔出侧向凸模或抽出侧型芯。
(6)温度调节系统 为了满足注射工艺对模具温度的要求,模具设有冷却或加热的温度调节系统。模具冷却,一般在模板内开设冷却水道;加热则在模具内或周边安装电加热元件。有的注射模须配备模具温度自动调节装置。
(7)排气系统 为了在注射充模过程中将型腔内原有气体排出,常在分型面处开设排气槽。小型腔的排气量不大,可直接利用分型面排气,也可利用模具的顶杆或型芯与配合孔之间间隙排气。大型注射模必须设置专用排气槽。
图4-2 单分型面注射模的浇注系统
1—主流道 2—分流道 3—矩形浇口 4—冷料井
单分型面注射模也称两板式注射模,见图4-1。单分型面注射模的主流道设在定模一侧,分流道设在分型面上,开模后制件连同流道凝料一起留在动模一侧。动模上的脱模机构顶出制件和流道凝料,在打开的动模和定模之间,取走注塑件和流道凝料。在模具重新闭合时,一般有回程杆10使脱模机构复位。
2.注射模的分类
(1)按塑料品种分类 注射成型最早用于热塑性塑料制品加工,特别是大量地用于工程塑料的成型。目前,热固性塑料和橡胶也已大量应用注射模生产制品。它们需用专门的注射机进行塑化。物料注射至模具后,在较高的温度下进行交联固化定型。低发泡塑料注射成型,是在塑料中加入一定量的发泡剂,在低发泡注射模的型腔内发泡膨胀后固化成型。聚氨酯等几种塑料可用反应注射方法成型。流动性好的反应液在模具内固化迅速。反应注射模是一种成型周期短,生产率高的注射模。共注射模具是以不同塑料或不同着色,分先后二次注射于模具内。注射成型对各种黏流态塑料有良好的适应性。黏流态塑料有不同的流动性,在型腔内的物理和化学固化成型过程也不同。因此,各种物料的注射模的结构各有其特点。
(2)按模具型腔容量分类 一般将模具型腔容积3000cm3以上,模具质量大于2t,需锁模载荷约600t以上的注射模称大型注射模。大型注射模的设计制造难度高,价格昂贵,必须慎重考虑塑料熔体流动性、模具的力学特性和温度调节系统。习惯上,又把模具型腔容积在100cm3以下的注射模划为小型。介于两者之间为中型注射模。
(3)按注射件尺寸精度分类 模塑过程中,注塑件成型收缩率很难稳定地控制。高精度的注塑件生产涉及众多因素,是综合性技术难题。近年来在大批量生产中,电子、电器、仪表、照相机等精密产品里,接插件、齿轮、支架板等塑料零件的精密注射技术有所进展。由此将中小型注射模中,成型精密级注塑件的模具称为精密注射模。这类模具能生产的精密注塑件,尺寸公差应达到SJ/T 10628—1995中的1~2级精度,达到GB/T 14486—2008中的MT2~MT3级精度(大致相当于金属件的公差配合标准GB/T 1800.2-2009中的IT8~9级精度)。精密注射模成型零件的加工精度达到IT6~7级,且型腔表面达到镜面。
(4)按注射模总体结构分类 最常用的分类方法是按注射模总体结构分类。注射模结构取决于注塑件的复杂程度及其浇注系统不同类型,主要有以下七种典型结构。
①单分型面注射模具;
②双分型面注射模具;
③带有活动镶件的注射模具;
④侧向分型抽芯注射模具;
⑤机动卸螺纹注射模具;
⑥热流道注射模具;
⑦叠式注射模具。
(5)按模具成型型腔数目分类 按模具成型型腔数目可分成单型腔和多型腔注射模。对小尺寸大批量生产的注塑件,一模多腔注射成型,成倍地提高生产率,已经实现一次成型32个或64个瓶盖制品注塑。另外,还有一次成型几个不同制品的多型腔注射模。
除上述五种分类方法外,还可按所安装注射机类型分成立式和卧式注射机用的注射模,或角式注射机上用的注射模。
4.1.2 双分型面注射模具
双分型面注射模系泛指浇注系统凝料和制品由不同分型面取出。此类注射模亦称三板式注射模,如图4-3所示。与单分型模具相比,在定模边增加了一块可往复移动的型腔板13。此板也称为型腔中间板或流道板,多用于针点浇口的单型腔或多型腔模具。开模A面分型时,型腔板与定模板作定距分离,供人工取出或自由下落浇注系统凝料;B面分型时,型腔板13与脱模板5相互分离,然后再由脱模机构顶出板9、顶杆11和脱模板5,将注塑件从型芯上脱出。
点浇口是直径1mm左右、长约0.6mm的塑料圆柱。采用点浇口可以把制品和浇注系统的凝料在模内分离。为此应该设计浇注系统凝料的脱出机构,保证将点浇口拉断,还要可靠地将浇注系统凝料从定模板或型腔板上脱离。
此种模具的结构较复杂,模板有顺序动作过程,而且浇注系统凝料较多。如果将流道加热,在定模中设置加热的流道板和顶针浇口的喷嘴,将演变成热流道注射模。
图4-3 双分型面注射模
a)闭合充模 b)开模取出塑件和浇道凝料
1—定距拉板 2—压缩弹簧 3—限位销钉 4—导柱 5—脱模板 6—型芯固定板 7—动模垫板 8—动模座 9—顶出板 10—顶出固定板 11—顶杆 12—导柱 13—型腔板 14—型芯 15—主流道衬套 16—定模板
4.1.3 侧向分型抽芯机构
侧向分型与抽芯机构简称为侧抽机构,用来成型具有外侧凸起、凹槽和孔的注塑件,成型壳体制品内侧的局部凸起、凹槽和盲孔。注射模侧抽机构的运动零件多,动作复杂。本节主要描述斜导柱机械力驱动的侧抽机构。
1.外侧分型
外侧分型注射模是以两个对合滑块,来成型注塑件整个侧向外形,也称瓣合模。图4-4是一组典型的外侧分型注射制品。
图4-4上所示的外形对称的注塑件,侧向分型面必须经过中心线。瓣合模成型的注塑件在外形上会留下拼合缝。因此在模具的使用期内,应保证侧滑块的拼合精度和足够的侧向压力。螺纹管接头制件上明显的拼合缝影响旋合联接功能。对笔套类塑件,唯一可取的侧向分型面必须设在弹性夹头的最高凸起处。
如图4-5所示,斜导柱驱动的侧向分型机构由斜导柱、滑块、导滑槽、定位装置和锁紧楔组成。在动模一侧的成型滑块,装在动模板上的导滑槽内,滑块上的导轨在导滑槽内可精确地往复运动。在定模边固定有与开模方向成倾角α的斜导柱,它与滑块上的斜孔成大间隙动配合。开模时滑块在斜导柱上滑动,由侧向分力驱动滑块进行侧向分型。滑块脱离斜导柱后,定位装置对滑块起定位和固定作用,以使斜导柱在合模时能再次对准插入。在合模中,斜导柱有一与前相反的复位分力,驱使滑块回复。斜导柱不能承受熔体充模时很大的侧压力,故要用锁紧楔紧压滑块于成型位置,保证注塑件的尺寸精度,防止产生溢料。斜导柱与斜孔有较大间隙,在合模时便于插入;在注射时避免与锁紧楔干涉;在开模时让锁紧楔先行脱离与滑块斜面的接触。
图4-4 需外侧分型的注塑件
a)管接头 b)方形骨架 c)螺纹管接头 d)圆筒骨架 e)接头 f)管轴杆 g)蛋杯 h)带轮 i)笔套
图4-5 斜导柱驱动的侧向分型注射模
a)合模状态 b)开模过程 c)开模终止 1—斜导柱 2—侧向成型滑块 3—导滑槽 4—定位装置 5—锁紧楔 6—圆筒骨架注射件 7—动模
在开模时,滑块以速度v沿斜导柱轴线方向运动。它是动模于开模方向的牵连运动va,和滑块在动模导滑槽中相对运动vr的合速度,如图4-5b所示。其v和va速度矢量的夹角为斜导柱的安装倾角α,故滑块侧向抽拔速度
vr=va tanα (4-1)
又如图4-5所示,侧滑块的抽拔距是指从成型位置起始,到滑块移至的不妨碍注塑件脱模顶出的位置。临界抽拔距Sc定义为:侧滑块与注塑件外形在模板上的投影不相重合的移动距离。而实际抽拔距S,应计入安全余量和误差补偿量2~3mm。
随着斜导柱安装倾角α增大,抽拔距S增大,但是所需的开模力和斜导柱受到的法向作用力也随之增大,会造成模具无法开启,并存在斜导柱折断的危险;此时抽拔速度过快,还会损伤注塑件。然而,倾角α过小,会使斜导柱机构处于自锁状态而不能开模。所以斜导柱倾角α在12°~25°比较适宜。
斜导柱驱动的侧向分型与抽芯机构由五个零部件所组成。它们是滑块、导滑槽、斜导柱、定位装置和锁紧楔。
(1)滑块和导滑槽 滑块上的成型表面是型腔的组成部分,应该用优质塑料模具钢制成并经抛光。小型滑块可采用整体式;但较大滑块大多用组合式结构。
滑块常用T型槽导向,加工方便且刚性好。构成导滑槽的压板或导轨以采用组合式为佳,这样便于使用高硬度淬火钢。摩擦表面应有40HRC以上的硬度。滑块的导轨和导滑槽应有足够的制造精度,保证滑块在使用期限内运动平稳,无上下窜动和卡滞现象。滑块在抽拔后,滑块外伸于导滑槽外过长,会因自重产生歪斜,影响闭模时斜导柱插入。所以滑块停留在导滑槽内的长度,应大于滑块导轨长度的三分之二。
(2)斜导柱 斜导柱由滑动段和固定段组成,紧固在定模板中。斜导柱安装倾角α和滑动段长度决定了侧向抽拔距。注射机的开模方向行程距离要保证滑块脱离斜导柱。斜导柱用高碳钢淬火保证硬度,并有足够直径保证弯曲强度。
(3)锁紧楔 又称压紧楔。它在注射过程中,使侧滑块将型腔紧密闭合,所以要求有足够的刚性。它可利用定模板直接加工出锁紧楔(例如图4-5注射模上的锁紧楔),称整体式。它能承受较大侧压力,但需要大厚度的定模板,切削耗钢多。如图4-7注射模上的锁紧楔,镶嵌在定模板中,结构紧凑且牢靠,刚性也好。它应该用淬硬钢制造,但需要较大的定模板面积。装配式的锁紧楔依靠螺钉和定位销固定,螺钉承受很大拉力。其加工和修配容易,但刚性差,易松动。为此,有时采用里外双重锁紧来保证刚性。锁紧楔的许用变形量小于0.05mm。锁紧楔角α′应大于斜导柱的安装倾角α,α′=α+(2°~3°)。以使在开模瞬时,先脱离侧滑块。
(4)定位装置 为保证滑块在抽拔后停留在准确位置上,机构必须有定位装置。该装置如图4-5和图4-7所示,常用挡块、钢珠或球头柱销定位。定位后还需用弹簧或自重来固定滑块。定位表面应有较高的硬度和精度。
2.外侧抽芯和局部型腔成型
图4-6上所示为具有侧面孔、凸起或凹槽的各种塑件。其中a~f注塑件必须从侧向抽出成型型芯。其临界抽拔距Sc等于孔的深度。其侧向抽拔力可用8.3节薄壁或厚壁注塑件脱模力计算式求得。图f注塑件侧面凸起数字和图g塑件侧面凹槽,必须用侧滑块从外侧局部成型。其Sc等于凸起高度或槽的深度。
图4-6 需外侧抽芯和局部型腔成型的注塑件
a)侧圆孔 b)侧槽支架 c)盒盖支承侧孔 d)长锥孔 e)筒侧孔 f)盒侧壁上凸字 g)盒侧壁上凹槽
图4-7所示是最常见的斜导柱驱动的外侧抽芯或局部型腔成型的注射模。斜导柱固装在定模上,滑块装在动模上。侧抽芯机构必须在开模方向,圆筒注塑件脱模之前完成抽拔动作,还必须在闭模过程中让机构复位。在模具的侧滑块领先复位过程中,顶杆或顶管还尚未退到闭模位置,以致滑块与它们相撞产生干涉现象。当然,可让顶出零件安排在不干涉的位置,由回程杆与定模相碰后,驱动顶杆等脱模机构零件复回。但有时无法避免两者在主分型面上投影的重合。
图4-7 斜导柱驱动外侧抽芯的注射模
a)合模状态 b)开模侧抽芯和顶出状态
1—斜导柱 2—侧向抽芯滑块 3—锁紧楔 4—定位装置 5—导滑槽 6—顶杆 7—动模
图4-8所示为产生干涉的几何条件。所示的复位位置是侧型芯与某个顶杆在同一侧平面上。Δl为侧型芯与顶杆在主分型面上重合的侧向距离。Δh是顶杆端面与侧型芯在开模方向的最近距离。当
Δl>Δhtanα (4-2)
时会产生干涉。两者重合距离Δl过大,侧型芯过低即Δh较小,容易发生干涉。在判断会产生干涉现象时,则须采用先复位机构。弹簧式先复位机构将压缩弹簧安装在顶杆固定板和动模底面之间。顶出注塑件时弹簧受压。一旦合模,在弹簧力作用下脱模机构立即复位。但弹簧力作用有限,仅适用于立式和小型注射模。较大的注射模,须利用装在顶杆固定板上的铰链、杠杆或三角滑块,合模时定模给以碰撞压力,迫使脱模机构领先侧抽滑块复位。
图4-8 产生干涉的几何条件
3.内侧局部型腔成型
注塑件内表面上的凸起、凹槽和盲孔,依靠向内侧抽拔的滑销或滑块成型。它们是成型型芯的一部分,但其运动受到空间条件限制。图4-9所示是直线机动顶出注塑件,而后由人工侧拉脱模。这种侧向抽拔,只适用于内侧表面单向的局部成型要求。图a为内滑销成型,在开模时侧拉注塑件,在制品的内侧面上有拼合缝。图b为用内滑块成型单侧内表面凸凹槽全长,拼合缝在另外两个内侧面上。在开模时将镶块与注塑件一起从动模上取出。在模外的侧向抽芯,镶块返回模具。另一种是注塑件圆孔中整个周边均有凸或凹槽时,在设计注塑件时就应考虑强制脱模。因为这类注塑件不能内侧抽。
图4-9 机动顶出后人工侧拉
a)滑销内侧成型 b)滑块内侧成型
图4-10 斜顶杆与铰链联接的内侧抽机构
1—顶出板 2—滑座 3—顶出固定板 4—斜顶杆 5—复位杆 6—动模垫板 7—动模主型芯 8—型芯固定板
如果几个方向有多个内侧成型,必须用倾斜运动的斜顶杆或滑块来实现完全机动的侧向抽拔。此种机构复杂,设计制造困难。
图4-10为较常见的一种内侧抽芯的斜顶机构,称为斜顶杆与铰链联接的内侧抽机构。如图4-10所示,斜顶杆4的头部有成型制品的内侧凹。斜顶杆安装在主型芯7中开设的斜孔内。斜顶杆下部装有铰链。在脱模顶出过程中,由铰链座的推顶,使斜顶杆的头部向模具中心靠拢。注塑件在脱离主型芯的同时完成斜顶杆头部的侧抽动作。铰链座夹固在顶出板和顶出固定板之间。有的在斜顶杆的头下端装滚柱。
4.1.4 型腔压力分析
型腔压力是注射模设计时各项计算的依据。在浇注系统设计、模腔壁厚和垫板的强度与刚度计算、型芯的偏移和变形计算、所需锁模力校核等运算中,要将型腔压力作为已知条件。型腔压力大小会影响开模力和脱模力,是决定注塑件质量的重要因素。型腔压力的分布和变化与温度一起,将决定固化后注塑件的密度和密度分布。借助注射模CAE/CAD的有限元分析软件进行型腔压力的计算机模拟;借助模具型腔压力的测定进行注射机参量的自动调节控制,能实现理想的注射成型工艺。但是由于昂贵的设备和技术难度,难以普遍实行。
1.型腔压力要求
1)注射充模时,要保证熔体具有合理的剪切速率。塑料熔体在模具的通道间隙中剪切速率应为102~104s-1。过低充模速率会使熔体流动性变差;过高的剪切速率,在型腔内会出现湍流或涡流,会产生熔体喷射并且破碎,将成型废次的注塑件。熔体在模内流动应是雷诺数很低的层流。
2)要保证型腔的充模压力。塑料熔体的压力传递能力较差,经各流程的流道和浇口,压力逐渐下降,会使注射到注塑件型腔的熔体压力不足。进入型腔的熔体压力应有(250~500)×105 Pa。为此,一方面浇注系统的流道要有足够的截面尺寸;另一方面注塑件型腔流程不能太长太窄,致使料流末端压力不足,造成塑料制品密度低、收缩率大,严重的甚至不能注满,因此,必须由各种塑料熔体的流程比来校核塑件的壁厚。
图4-11 型腔压力分布链示意图
a)单分型面注射模 b)双分型面注射模 c)柱塞式料筒与单分型面注射模
2.型腔压力分布
广义的型腔压力是模内塑料熔体流经位置和时间的函数。型腔压力分布链的位置状态,如图4-11所示。主流道末端具有最大的分型面上的压力pA。浇口处具有注塑件型腔的最大压力pB(两处常是压力测定点)。喷嘴出口处的压力pZ,是模具浇注系统压力的源头。在双分型注射模的型腔板上,浇注系统较复杂且流程长。从pZ至pB有较大浇注系统压力降Δpr。熔流末端压力pc倘若过低则会影响注塑件质量,甚至不能注满,故熔体末端压力pc≥10~25MPa。注塑件型腔的压力从pZ降至pc为模腔压力降Δpc。若型腔流程的截面较简单,可用流变学压力降公式估算。
型腔压力的源头是注射压力p0,它可由每台注射机的油压表上读出的最大值pi换算得到
式中 p0——调用的注射压力(MPa);
D——注射液压缸活塞直径(mm);
dS——注射螺杆或柱塞直径(mm);
pmax——注射机的最大注射压力(MPa);
p′——注射机液压泵的额定油压(MPa);
pi——注射过程中油压表上的最大值,即表压(MPa)。
由图4-11a和b图可知,螺杆头处p0至喷嘴pZ间存在压力降ΔpZ。ΔpZ是圆管中的非牛顿流变的压力降,按照第2章式(2-18b),喷嘴为圆柱孔道,其压力降计算式为
式中 ΔpZ——塑料熔体流经注射机喷嘴的压力降(Pa);
n——塑料熔体非牛顿指数,n<1;
K′——熔体剪切黏度系数(N·s/cm2);
Q——熔体流经喷嘴的体积流量(cm3/s);
LZ——喷嘴长度(cm);
RZ——喷嘴半径(cm)。
[例]PP熔体的温度Tm=240℃,注射时计量容积V=427cm3,注射时间t=2.4s。经注射机喷嘴的剪切速率。喷嘴内半径RZ=0.275cm、长LZ=2.0cm。计算PP熔体流过喷嘴的压力降ΔpZ。
[解]流经喷嘴的熔体体积流量
代入已知条件计算得Q=178cm3/s。又由表2-5查得牌号为J340的PP的n=0.13,K′=6.04N·s/cm2。代入式(4-4)得熔体流经喷嘴的压力降为
由实验曲线可知,螺杆式注射装置中的压力降为
Δpe=p0-pz=(2.0~2.5)Δpz (4-6)
此式中的放大系数,系指活塞和螺杆等运动件的摩擦阻抗,以及螺杆头前剩余熔体段的压力降。通常螺杆式注射装置中的压力降Δpe=10~20MPa,但注射高黏度熔体,或是使用高阻抗喷嘴,如阀式喷嘴,Δpe会更大,需作计算预测或专门的测量。此外,在型腔压力估算时,所使用的注射压力p0必须小于注射机的最大注射压力pmax,为注射车间现场留有充分调节注射压力的余地。
若将非牛顿塑料熔体,视为短时间恒温状态,且在各流段中处于恒剪切速率,则可用牛顿流体计算式计算压力降。对于圆管道有
且按定义
式中 L和R——圆管长和半径(cm);
ηa——塑料熔体表观黏度(N·s/cm2);
τ——剪切应力(N/cm2);
Δp——圆管道两端的压力降(N/cm2,1N/cm2=104 Pa)。
由式(4-8)计算该段流程中剪切速率γ·。从上例中数据,可得
然后在PP塑料流动曲线的图上,查到对应剪切应力τ。也可代入式(4-7)得到
由式(4-8)有压力损失
计算结果与上述数值相差很小。此种计算方法称之为塑料熔体压力降的工程计算法。
柱塞式注射装置有与螺杆式注射装置不同的塑化原理和结构。由于粒料区的作用,装置内压力阻抗较大。不过,柱塞式注射装置常见公称注射量均在60cm3以下。经实验测得,柱塞式注射装置中的压力降为
Δpe=p0-pr=30MPa+(0.1~0.2)p0 (4-9)
式中,第一项30MPa压降是加热室和喷嘴的黏流区的压力损失;第二项是被压缩的粒料区的压力损失,它与柱塞压力p0成正比。其折算系数与注射加工时的注射量有关,当注射量较大时取大值。
3.型腔压力变化
将型腔压力变化对注射成型时间进程作图,就得到型腔压力周期图,如图4-12所示。(对应图4-11b双分型面注射模的浇道、浇口和型腔各位置的压力对时间的变化)。
图4-12所示t0~t1称注射时间。塑料熔体进入型腔,并达到最远处,而且压力得到急剧升高。t1~t2为保压时间,也称压实补缩阶段,螺杆作少量推进,以维持一定压力。在时间t1,模内物料温度明显下降。在时间t2螺杆后撤。喷嘴口压力pZ下降最快。t2~t3为倒流时间。时间t3是注射模中内浇口的冻结时间。螺杆后撤时,内浇口尚未冻结,型腔内熔体回头倒流至浇道。t3~t4是静态冷却时间。t4是模具打开时间。pr为该时间的型腔内的残余压力。
在注射保压阶段,在分型面上,型腔压力pA决定了锁模力。锁模力不足或分型面不平整,会产生塑料熔体溢料。也注意到位于料流未端型腔压力pc较低,在该位置的分型面上设置有排气槽。
图4-12 注射成型型腔压力周期图
p0—注射压力 pZ—喷嘴压力 pA—料流进入型腔压力 pB—型腔压力 pC—料流末端型腔压力