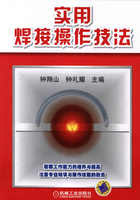
3.6 电弧焊的操作技术
焊条电弧焊是生产中应用最为广泛的焊接方法之一,它具有操作灵活、选择性强、适应性广等优点。根据焊接件的构成,其焊接形式可分为:板料焊接、管料焊接、管板焊接及构件的焊补等操作形式。
3.6.1 板材的焊接操作
根据板材焊件接缝所处的空间位置,其焊接位置分为平焊、立焊、横焊和仰焊四种形式。应该说明的是,板料的焊接操作应根据板料厚度(如厚板、薄板)有所不同。
1.厚板的焊接
对于厚度≥3mm的板料,其焊条电弧焊的操作可参照本书“3.5各种焊接位置的操作方法”来进行。
为保证焊件的焊接质量,对于较厚及重要的焊件应开设坡口。表3-23给出了选择焊缝坡口的基本形式,并给出了坡口尺寸。
表3-23 焊缝坡口的基本形式
(续)
2.薄板的焊接
由于电弧温度高,热量集中,焊接3mm以下的薄板时很容易产生烧穿现象,有时也产生气孔,因此焊接操作时,应采用小直径焊条和小电流,运条方法宜采用往复直线形。
对于厚度2mm以下的薄板焊件,最好用弯边焊接方法焊接,如图3-47所示。
焊接前,应先将焊件的直边用弯边机压制成弯边或在方钢上用锤子手工弯边,曲线弯边可利用专用模具在压力机上完成,然后将弯边焊件对齐修平进行定位焊。一般每隔50~100mm定位焊一次。越薄的板料,定位焊点应越密。
焊接时,最好采用直流反接,不留间隙,用2~3mm焊条快速短弧焊接,焊条沿焊缝作直线运动。如果焊缝较长,可固定在模具上焊接,以防变形。
除焊接各种容器外,在不影响质量的情况下,可采用断续焊接方法焊接薄板焊件,也可将焊件一端垫高12°~20°,如图3-48所示。但焊接时要防止熔渣流到熔池的前方造成夹渣及气孔等缺陷。
图3-47 薄板的弯边焊接
图3-48 薄板垫高一端的焊接
薄板的搭接焊比对接焊相对容易。薄板对接焊的注意事项如下:
1)装配间隙应越小越好,最大不要超过0.5mm。坡口边缘的切割熔渣与剪切毛刺应清除干净。
2)两块板装配时,对口处的上下错口不应超过板厚的1/3。对某些要求高的焊件,错口应不大于0.3mm。
3)应采用较小直径的焊条(φ2.0~φ3.2mm)进行定位焊及焊接。定位焊的间距应适当小一些,定位焊缝呈点状,在间隙较大处则定位焊的间距应更小些。例如在焊接1.5~2.0mm厚的薄板时,用φ2.0mm焊条,70~90A的电流进行定位焊,定位焊缝呈点状,焊点间距80~100mm。对缝两端定位焊缝长10mm左右。
4)焊接电流可比焊条说明书规定的大一些,一般应比表3-11所列的电流大10~20A,但焊速应稍高,以获得小尺寸的熔池。
5)焊接时应采用短弧、快速直线焊接,焊条不作摆动,以得到小熔池和整齐的焊缝表面。
6)对可移动的焊件,最好将其一头垫起,使之呈15°~20°角,进行下坡焊,如图3-48所示。这样可提高焊速和减小熔深,对防止薄板焊接时的烧穿和减小变形极为有效。
7)对不能移动的焊件,可采用灭弧的方法焊接,即焊接一段后发现熔池将要漏穿时立即灭弧,使焊接处温度降低,然后再进行焊接。也可采用直线前后往复焊接(向前时,将电弧稍提高一些)。
8)有条件时可采用立向下焊条进行薄板的焊接。由于立向下焊条焊接时熔深浅,焊速高,操作简便,不易烧穿,故对可移动的焊件应尽量放置在立焊位置进行向下立焊。对不能移动的焊件,其立焊缝或者斜立缝也可采用此种焊条。但平焊位置用此种焊条焊接成形不好,因此不宜采用。
3.焊缝衬垫
当要求焊缝全焊透且只能从接头的一面进行焊接时,除了采用单面焊双面成形焊接操作技术外,还可以采用焊缝背面加焊接衬垫的方法。使用焊接衬垫的目的是提供条件,使第一层金属熔敷在衬垫上,从而避免该层熔化金属从接头底层漏穿。
常用的衬垫有四种形式:衬条、铜衬垫、非金属衬垫和打底焊缝。
1)衬条。衬条是放在接头背面的金属条。第一条焊道使接头的两边结合在一起并与衬条相接。衬条如果不妨碍接头的使用特性,可保留在原位置上,否则应拆除掉。衬条需采用与所使用的母材和焊条在冶金上相配的材料制成。
2)铜衬垫。有时采用铜衬垫在接头底层支撑焊接熔池。它适用于平直对接焊缝。铜的热导率较高,有助于防止焊缝金属与衬垫熔合。
3)非金属衬垫。非金属衬垫是一种可伸缩的成形件,用夹具或压敏带贴紧在接头背面。它适用于空间曲面对接焊缝。焊条电弧焊有时也使用这种衬垫。使用时应遵循衬垫制造厂推荐的规范。
4)打底焊缝。打底焊缝是在单面坡口焊接接头中的一道或多道的背面焊道。这种焊缝是在坡口正面熔敷第一道焊缝之前在接头背面熔敷的。完成打底焊缝之后,所有的其余焊道均从正面在坡口内完成。
3.6.2 管材的焊接操作
管材在各类装置和设备中应用数量很大。管材焊接质量的好坏,直接影响着装置或设备的正常运转。管材按照焊接放置位置的不同,可分为:转动焊接、水平固定的焊接、垂直固定的焊接和倾斜固定的焊接等。
1.管道的转动焊接(管材水平放置)
管道采用转动焊接,操作简便,能保证质量,而且生产效率高,所以在预制场大量使用。各类装置或设备上的联系管道及工艺管道干线应尽量提高预制装配程度,减少固定焊口。
(1)对口及定位焊 管道的焊接要求坡口端面的不平齐度小于0.5mm,焊口拼装错口不得大于1mm,对口处的弯曲度不得大于1/400。定位焊时,对于管径小的(φ≤70mm),只需在管材对称的两侧进行定位焊就可以了。管径大的可定位焊三点或对更多的点进行定位焊(图3-49)。定位焊焊肉的尺寸应适宜,通常当管壁厚度小于或等于5mm时,定位焊焊肉厚度可与管壁齐平;若管壁厚度大于5mm时,则定位焊焊肉厚度约为5mm,定位焊长度为20~30mm。为便于接头熔透,定位焊焊肉的两个端都必须修成缓坡形。
(2)根部的焊接 不带垫圈管材的转动焊接,为了使根部容易熔透,运条范围选择在立焊部位,如图3-50所示。操作手法采用直线形或稍加摆动的小月牙形。如果对口间隙较大时,可采用灭弧方法焊接。
图3-49 定位焊数量及位置
图3-50 管材转动焊接的立焊部位
A—起焊点 S—焊段终点
对于厚壁管,为防止转动时由于振动使焊口根部出现裂纹并便于操作,在对口前应将管材放在平整的转动台或滚杠上。焊接时,最好每一焊段焊接两层后再转动,同时定位焊焊缝必须有足够的强度。靠近焊口两个支点的距离最好是管径的1.5~2倍,如图3-51所示。
(3)多层焊的其他各层焊接方法 对于转动焊接的多层焊接,运条范围是选择在平焊部位,如图3-52所示。
图3-51 滚动支点的布置
图3-52 多层焊的运条位置
操作时,焊条应在垂直中心线两边15°~20°范围内运条,焊条与垂直中心线成30°角,采用月牙形手法,压住电弧作横向摆动,这样可得到整齐美观的焊缝。或仍选用斜立焊部位进行焊接,这种方法适用于现场无转动台的转动焊接。
2.水平固定管的焊接
水平固定管的焊接具有以下特点:
1)施焊过程中焊条位置变化很大,操作比较困难。
2)熔化金属在仰焊位置有向下(向焊道外)坠落的趋势,而在立焊及过渡到平焊位置时,则有向管材内部滴落的倾向,因而有透度不匀及外观不整齐的现象。
3)仰缝施焊时,主要依赖电弧的吹力使熔化金属熔化到坡口中去,并与母材很好地接合在一起。若电弧吹力不够,则熔滴输送到熔池的力量就会减弱,所以只有增大电流强度才能使电弧吹力增加。但电流过大,熔池面积增加,熔化金属容易下坠。由于焊件温度随着焊接过程的进行而升高,所以为了防止熔化金属下坠,必须使用合适的电流。
4)焊接根部时,仰焊及平焊部位比较难于操作,通常仰焊部位背面出现焊不透或容易产生凹陷,表面因熔化金属下坠出现焊瘤、咬口和夹渣等缺陷。平焊部位容易产生焊不透以及因熔化金属下坠而形成的焊瘤。
5)自立焊部位至平焊部位这一段焊缝,往往由于操作不当等原因,常产生气孔和裂纹等缺陷。
根据上述特点,在操作时应针对性的采取以下措施:
(1)对口要求及定位焊 组对时,管材轴线必须对正,以免形成弯折的接头;同时考虑到焊缝冷却时会引起对口间隙的收缩,所以对较大直径的管材,有必要于焊接前使平焊部位的对口间隙大于仰焊部位。
定位焊基本上与转动焊接相同。
(2)根部施焊 在施工现场,常见的为不带垫圈的V形坡口对接焊,其焊接方法基本上与钢板的焊接方法相似。
焊法有两种:第一种是分两半焊接,此法应用广泛;第二种是顺着管材圆周焊接。
1)两半焊接法。两半焊接的施焊程序为:仰焊+立焊+平焊,此法能保证熔化金属和熔渣很好地分离,透度比较容易控制。
该操作方法是沿垂直中心线将管材截面分成相等的两半,各进行仰、立、平三种位置的焊接。在仰焊及平焊处形成的两个接头如图3-53所示。
操作要点为:首先对正定位焊焊口,在仰焊缝的坡口边上引弧至焊缝间隙内,用长弧烤热起焊处(时间3~5s)。预热以后,迅速压短电弧熔穿根部间隙施焊。在仰焊至斜仰焊位置运条时,必须保证半打穿状态;至斜立焊及平焊位置,可运用顶弧焊接。其运条角度变化过程及位置如图3-54所示。
图3-53 两半焊接法示意图
图3-54 两半焊接法运条位置
为了便于仰焊及平焊接头,焊接管材前一半时,在仰焊位置的起焊点及平焊部位的终焊点都必须超过管材的半周(超越中心线5~10mm),如图3-55所示。
为了使根部透度均匀,焊条在仰焊及斜仰焊位置时,尽可能不作或少作横向摆动,而在立焊及平焊位置时,可作幅度不大的反半月形横向摆动。
当运条至定位焊焊缝接头处时,应减慢焊条的前移速度,以便熔穿接头处的根部间隙,使接头部分能充分熔透。当运条至平焊部位时,必须填满熔池后再熄弧。
焊接环形焊缝后一半的运条方法基本上与前一半相同,但运条至仰焊及平焊接头处时必须多加注意。
各种接头施焊时,应注意以下几点:
第一,仰焊接头方法。由于起焊处容易产生气孔和未焊透等缺陷,故接头时应把起焊处的原焊缝用电弧割去一部分(约10mm长),这样既割除了可能有缺陷的焊缝,又可以形成缓坡形割槽,也便于接头。其操作方法如下:首先用长弧烤热接头部分,稍微压短电弧,此时弧长约等于两倍焊条直径;从超越接头中心约10mm的焊波上开始焊接,此时电弧不宜压短,也不作横向摆动,一旦运条至接头中心时,立即拉平焊条压住熔化金属向后推送,未凝固的熔化金属即被割除而形成一条缓坡形的割槽;焊条随即回到原始位置(约30°),从割槽的后端开始焊接;运条至接头中心时,切勿灭弧,必须将焊条向上顶一下,以打穿未熔化的根部,使接头完全熔合,如图3-56所示。
图3-55 管材前一半的焊接
a—起焊点 b—终焊点
图3-56 仰焊接头操作示意图
a)电弧预热之后开始用长弧焊接(不摆动) b)拉平焊条准备割槽 c)焊条向后推送形成割槽 d)焊条回到正常位置并从割槽后端起焊
对于重要管道或使用低氢型焊条的焊接,可用凿、锉等手工加工方式修理接头处,把仰焊接头处修理为缓坡形,然后再施焊。
第二,平焊接头方法。平焊接头时,应先修理接头处,使其成一缓坡形。选用适中的电流值,当运条至斜立焊(立平焊)位置时,焊条前倾,保持顶弧焊,并稍作横向摆动(图3-57)。当距接头处尚有3~5mm间隙(即将封闭)时,绝不可灭弧。接头封闭的时候,需把焊条向里稍为压一下(此时可听到电弧打穿根部而产生的“啪喇”声),并在接头处来回摆动以延长停留时间,从而保证充分的熔合。熄弧之前必须填满熔池,然后将电弧引至坡口一侧熄灭。
图3-57 平焊接头用顶弧焊法
第三,定位焊缝和换焊条时的接头操作方法。定位焊缝和平焊处的接头施焊方法相似,其要点在于首先修理定位焊焊缝,使其成为具有两个缓坡形的焊点。在与定位焊焊缝的一端开始连接时,必须用电弧熔穿根部间隙,使其充分熔合。当运条至定位焊缝的另一端时,焊条在接头处稍停,使接头熔合。
换焊条时有两种接头方法:第一种是当熔池尚保持红热状态时就迅速地从熔池前面引弧至熔池中心接头(图3-58),此法接头比较平整,但运条要灵活,动作要敏捷;第二种方法是由于某种原因,如换焊条动作缓慢或焊缝冷却速度太快等,以致熔池完全冷凝,这时焊缝终端由于冷却收缩时常形成较深的凹坑,并且也常产生气孔和裂纹等缺陷,因此必须用电弧割槽或手工修理后,方可施焊。
2)沿管周施焊。沿管周施焊主要用在对质量要求不高的薄壁管的焊接。操作方法是:以斜立焊位置作为起焊点(图3-59),在自上而下的运条过程中最好不要灭弧,焊条端部托住熔化金属使用顶弧焊接。在平焊→立焊→斜仰焊这几段焊接过程中,焊条几乎与管周成切线位置,在由斜仰焊至仰焊这一段,焊条位置可以稍偏于垂直。在仰焊→立焊→平焊位置运条过程中,施焊方法与“两半焊接法”相同。整个环形焊缝最后在斜立焊位置闭合。
图3-58 红热状态时的接头方法
图3-59 沿管周施焊方式示意图
a)起焊点(A点) b)沿管周施焊
此方法由于有一半是自上而下运条,熔化金属及熔渣有向下坠落的趋势,所以熔深不大,透度不易控制,熔化金属与熔渣不易分离,焊缝容易产生夹渣等缺陷。但由于运条速度快,能提高焊接生产率。
(3)其他各层的焊接 其他各层也分两半进行仰焊→立焊→平焊的施焊方法,操作要领基本上与相应位置的钢板焊接法相似,但还必须注意以下几点:
1)为了消除底层焊缝中存在的隐藏缺陷,在其外层焊缝施焊时,应选用较大的电流值,并适当控制运条,达到既不产生严重咬边又能熔化掉底层焊缝中隐藏缺陷的目的。
2)为了使焊缝成形美观,当焊接外部第二层焊道时,仰焊部位的运条速度要快,使形成厚度较薄、中部下凹的焊缝(图3-60a);平焊部位的运条速度应该缓慢,使形成略为肥厚而中央稍有凸起的焊缝(图3-60b)。必要时,在平焊部位可以补焊一道焊肉(图3-60c),以达到整个环形焊缝高度一致的目的。
3)当对口间隙不宽时,仰焊部位的起焊点可以选择在焊道中央;如果对口间隙很宽,则宜从坡口的一侧起焊。
图3-60 外部第二层焊道良好成形图
当采用从焊道中央起焊时,其接头方法为:首先应在越过中线10~15mm处引弧预热,起焊时电弧不宜压短,需作直线运条,速度稍快,至中线(接头中心)处开始逐渐作横向摆动(图3-61)。
图3-61 仰焊部位的起焊运条方式(从焊道中心起焊)
在焊接管周的另一半时,首先在接近于A点的对称部位A′点引弧预热,接头起焊时电弧较长,运条速度稍快,坡口两侧停留时间比焊缝中央为长,接头处的焊波应该薄些,避免形成焊瘤。
当采用从坡口一侧起焊时,其接头方法为:起焊和接头的基本要求与上面方法相似,只是起焊点在坡口的一侧,接头处的焊波是斜交的,如图3-62所示。
图3-62 从坡口一侧的起焊方法
3.垂直固定管的焊接
垂直固定管的焊接特点与钢板的横焊基本相似。其操作要点主要有以下几点:
(1)对口要求及定位焊 当对口两侧管径不等时(错口),可以将直径较小的管材置于下方,并且保证沿圆周方向的错口数值均等;绝对避免偏于一侧集中错口,因为当错口值很大时将不可能熔透,在根部必然产生咬口缺陷,这种缺陷会由于应力集中而导致焊缝根部破裂(图3-63)。
图3-63 错口接头(箭头指处为咬口缺陷)
错口大于2mm时则必须通过加工使内径相同,其加工坡度为1∶5(图3-64)。
为了使焊口对正,管材端面应垂直于管材轴线。焊接之前,坡口及其两侧10mm范围内应清除锈污,直至显露金属光泽为止。
定位焊及焊点的修理都与钢板横焊的定位焊相似。当管径直径φ较小(φ≤70mm)时,只需在管材对称的两侧定位焊两点就行。管材较大时,可定位焊三点或更多的焊点。
(2)根部焊接 根部焊接同横焊基本操作法。
(3)多层焊接 多层焊接同横焊基本操作法。
(4)单人焊接大直径管道的方法 当焊接直径较大的管道时,如果沿着圆周连续运条,则变形量较大,必须应用“逆向分段跳焊法”来焊接,如图3-65所示。
图3-64 管材内圆加工示意图
图3-65 逆向分段跳焊法
多层焊时,每层焊道的接头应错开20~30mm。
4.倾斜固定管的焊接
倾斜固定管的焊接可以看成是水平固定管焊接和垂直固定管焊接的结合,其根部焊接与水平固定管焊接相似。多层焊时,若管材倾斜角小于45°,可运用垂直固定管焊接的方法(图3-66a);当倾斜角大于45°时,可用水平固定管焊接方法(图3-66b)。但这种焊接形式难以获得美观的外表,尤其是焊缝接头处。
倾斜固定管的焊接操作要点主要有以下几点:
(1)对口要求及定位焊 与水平固定管焊接相同。
(2)根部施焊 根部施焊可分成两半焊成。由于管材是倾斜的,熔化金属有从坡口上侧坠落到下侧的趋向,所以在施焊中焊条应该偏于垂直位置(图3-67)。其余注意事项与水平固定管焊接相同。
图3-66 管材斜焊方式
图3-67 管材斜焊根部运条方式
(3)多层焊接 当管材倾斜角小于45°时,可运用多层多道焊,分两半焊成。每道焊缝运条方式与根部焊接相似,但可略作水平方向的横向摆动;如果管材倾斜角大于45°,则可与水平固定管焊接相似,运用单道焊法。但由于横向摆动的幅度较大,为了不使熔化金属下坠,焊条在坡口下侧的停留时间应比上侧略长,即图3-68中的a侧焊条停留时间应比b侧长。
(4)仰焊接头的施焊 在焊接过程中,对仰焊接头的施焊可采用以下方式:起焊点越过管材半周(以接头中心OY线为准,见图3-69)10~20mm。横向摆动的幅度自仰焊至立焊部位越来越小。在接近平焊处摆幅再度增大。为了防止熔化金属偏坠,折线运条方向也需随之改变。
图3-68 多层焊时单道焊法的运条方式
图3-69 管材斜焊时的仰焊部位接头方式
OY—接头中心 OC—焊缝中心
接头时,从A′起焊,电弧略长,摆幅自A′点至A点逐渐变大(图3-70)。
(5)平焊接头的施焊 平焊接头比仰焊接头容易操作。为了防止咬边,应选用较小电流,焊条在坡口上侧的停留时间略长,如图3-71所示。
图3-70 管材斜焊焊缝外貌图
图3-71 管材斜焊平焊接头方式
5.管材焊接注意事项
在焊接管材时,应注意以下事项:
(1)大直径管材的焊接 对直径很大的管材,因轧制无缝钢管比较困难,可用钢板卷圆,然后焊接成管。在焊接纵向焊缝时,为了防止变形,可采用分段逆向跳焊法(参见图3-65)。
图3-72中数字表示分段施焊的次序,每段长为150~300mm。多层焊时,上下两层的焊段接头应该错开。
(2)对口焊 进行对口焊时,相邻两管段的纵向焊缝应错开一段距离l,且l应大于200mm,如图3-73所示。
图3-72 纵向焊缝的分段逆向跳焊法
图3-73 焊制管道对接方式
为了减小变形和提高劳动生产率,尽可能采用两人对称焊或转动管材进行焊接。如果要取得良好的根部质量,最好在管材内壁再补焊一道焊肉。
(3)刚性对口的焊接 安装管道时,时常会使焊口处于刚性状态。对于此种焊口或冷拉焊口进行焊接时的特点就是易产生裂纹,故应注意以下事项:
1)根部焊缝应焊得肥厚些,使它具有一定的强度;焊接过程尽可能不中断。
2)最好在焊接之前对焊口进行预热,必要时(如焊合金钢)在施焊过程中可以保持预热温度。
3)根部焊完之后应检查有无裂纹,若发现有裂纹则需彻底清除。
4)尽可能利用多层焊法以改善接头质量。
5)表层焊肉不得有咬边(咬肉)现象,如有,应该补焊。
6)焊后应退火,以消除残留应力。
7)用以拉紧焊件的冷拉工具必须等焊口焊完并且热处理冷却之后方可松去。
(4)低温下的焊接 在低温下焊接时,由于焊缝冷却速度很快,因而产生较大的焊接应力,焊缝容易破裂。另外,熔化金属的快速冷却阻碍了气体的析出,故焊缝中易产生气孔。当温度很低时,焊工易疲劳,也影响工作质量。为此,应注意以下方面:
1)焊接场所尽可能保持在零度以上,可以用遮风、雨、雪棚,并配置暖气、火炉或电炉来调节温度和取暖。
2)必须扫清焊件内外及焊接场所的积雪和冰块,焊缝附近的水分应擦干或烤干。
3)低温下焊接时必须严格按照规程要求,对焊缝进行预热及退火。
4)在坡口内定位焊时,定位焊焊缝的尺寸不能太小。若在合金钢管坡口内定位焊时,定位焊前应进行预热。此外,还应避免管材的强力对正;不得敲打和弯折定位焊焊缝;焊接前必须仔细检查焊点有无裂纹,并且要把焊点两个端部修理成缓坡形;定位焊后应立即施焊。
5)低温焊接时要重视热处理规范,可通过焊前预热、焊接过程中加热、增加电流或采用保温方法以降低焊缝区的温度梯度。
3.6.3 管道向下立焊的操作
管道全位置焊接时,熔化的金属容易下淌,使焊缝成形差。传统的焊接方法采用减小焊接电流和向上立焊来克服。焊条电弧焊向下立焊的操作是指在焊接结构中的立焊位置时用立向下焊条,由上向下运条进行施焊的一种操作方法。由于采用的立向下焊条在其药皮中配制了提高熔渣熔点及粘度的物质,从而使焊条适宜在立焊时由上向下焊接。采用此操作方法焊接时,坡口应留有一定的均匀钝边,根部留一定间隙,采用大焊接电流,宜使用带引弧电流的弧焊电源,电弧吹力强,熔深大,不宜摆动。可由多个焊工组成连续操作的流水作业班组,这种方式特别适用于长距离大口径管线的焊接施工。它与传统的上向焊接比较,具有焊接质量好,焊接速度快,生产效率高(比使用一般焊条由下向上焊接的效率能提高两倍以上,节省焊条约30%)等优点。
1.管道向下立焊技术要点
采用向下立焊,其焊接技术要点主要有以下几点:
(1)坡口形式及尺寸 管道向下立焊采用单面V形坡口,单面焊双面成形,坡口形式如图3-74所示。管道向下立焊对接焊缝的尺寸要求见表3-24。
图3-74 管道向下立焊坡口示意图
表3-24 管道向下立焊对接缝尺寸的要求
(2)管道向下立焊参数 管道向下立焊参数的确定主要有以下内容:
1)管道向下立焊遵循多层多道焊的原则。焊接层数根据管壁厚度确定,不同壁厚要求的焊接层数见表3-25,焊接顺序如图3-75所示。
表3-25 不同壁厚要求焊接层数
2)焊接材料应根据不同的管材和输送介质选择不同的焊条。输气管线原则上选用低氢型立向下焊条,输油和水管线选用纤维素型立向下焊条。向下立焊均采用直流电源反极性接法。纤维素型立向下焊条的焊接参数见表3-26,低氢型立向下焊条的焊接参数见表3-27。
(3)管道向下立焊注意事项 管道向下立焊时应注意以下事项:
1)管材采用内对口器对口时,去掉对口器前必须完成全部根部焊道的焊接;采用外对口器对口时,去掉对口器前必须完成50%以上的根部焊道的焊接,并且焊完的每段长度近似相等,且分布于圆周上的每段间距也应均匀。
图3-75 焊接顺序
1—根部焊道 2—热焊焊道 3、4—填充层焊道 5—盖面层焊道
表3-26 纤维素型立向下焊条的焊接参数
①适用于焊接壁厚较薄或管直径较小的管材。
表3-27 低氢型立向下焊条的焊接参数
①适用于焊接壁厚较薄或管直径较小的管材。
2)更换焊条要快,应在熔池熔渣未冷却前换完焊条并再引弧。若工作间断后再焊,应先清除接头处的渣壳再引弧焊接。每相邻两层焊道更换焊条接头处应错开30~50mm,避免相互重叠。
3)根部焊道要保证全部焊透,背面成形稍有凸起,凸起的高度以1.0mm±0.5mm为宜。
4)根部焊道完成后,要尽快焊接第二层焊道(热焊),一般要求根部焊道与热焊道的间隔时间不超过5min。
5)每根焊条引弧后应一次连续焊完,焊接面每边一般应一次连续焊完,中间不要中断。
2.管道向下立焊操作方法
管道向下立焊多采用纤维素型立向下焊条。焊接时,要求采用单面焊双面成形,背面焊缝要求焊波均匀、表面光滑并略有凸起。因此根部焊道是保证背面成形良好的关键。管道向下立焊操作方法主要分为:根焊、热焊、填充焊和盖面焊四个过程。
1)根焊。指焊接根部第一层焊道。焊接时从管顶中部略超过中心线5~10mm处起焊,从坡口表面上引弧,然后将电弧引至起焊处。电弧在起焊处稍作停留,待钝边熔透后沿焊缝直拖向下,采用短弧操作。焊条倾角的变化如图3-76a所示。根部焊道焊完后,应彻底清除表面焊渣,尤其是焊缝与坡口表面交界处应仔细清除干净,以免在下层焊道焊接时产生夹渣。
2)热焊。根部焊道焊完后应立即焊接第二层焊道,即热焊。进行热焊时,与根焊时间的间隔不宜太长(最长10min),焊条直径可与根焊时相同或略大,运条时一般直拖向下或稍作摆动,但摆动时电弧长度要适中,保持短弧焊接,焊条倾角与根焊时相同。
3)填充焊。填充焊道是为了给盖面焊接打基础。焊道要求均匀、饱满,两侧熔合良好且不能破坏坡口。焊条直径和焊接电流可大些,采用直线运条或稍作摆动,保持短弧焊接,焊条倾角与根焊时基本相同。
图3-76 管道向下立焊的焊条倾角
a)焊根部焊道的焊条倾角 b)焊盖面焊道的焊条倾角
4)盖面焊。盖面焊道是保证焊缝尺寸及外观的关键工序。焊条直径可以与填充焊道的焊条相同或更大,但焊接电流不宜太大。采用直线稍加摆动运条,摆动幅度要适当,以压两侧坡口1.5~2.0mm为宜。收弧时,焊条要慢慢抬起,以保证焊道均匀过渡。焊接时焊条倾角的变化如图3-76b所示。
3.6.4 管板的焊接操作
管板的焊接结构是常见的焊接构件形式。根据管板固定形式及施焊位置的不同,主要有平角焊、仰角焊及管板水平固定焊几种,采用焊条电弧焊时,其操作可按以下步骤进行。
1.平角焊位置的操作
管板的焊接操作分为三步,即打底焊、填充焊和盖面焊。
(1)打底焊 打底焊主要保证根部焊透,底板与立管坡口熔合良好,背面成形无缺陷。焊接时,首先在左侧的定位焊缝上引弧,稍加预热后开始由左向右移动焊条,当电弧移到定位焊缝的前端时开始压低电弧,向坡口根部的间隙处送焊条,等形成熔孔后,保持短弧并作小幅度的锯齿形摆动,电弧在坡口两侧稍加停留。打底焊时,焊接电弧的大部分覆盖在熔池上,另一部分保持在熔孔处,保证熔孔大小一致,如果控制不好电弧,容易产生烧穿或熔合不好。平角焊打底焊的焊条角度如图3-77所示。
图3-77 平角焊打底焊的焊条角度
焊接过程中,由于焊接位置不断发生变化,因此要求焊工手臂和手腕要相互配合,保证合适的焊条角度,并控制熔池的形状和大小。打底焊的接头一般采用热接法,因为打底焊时的熔池较小,凝固速度快,因此一定要注意接头速度和接头位置。如果采用冷接法,一定要将接头处处理成斜面后再接头。焊最后的封闭接头时,要保证焊缝有10mm左右的重叠,填满弧坑后再熄弧。
(2)填充焊 填充焊前,要将打底层焊道的熔渣清理干净,处理好焊接有缺陷的地方。焊接时,要保证地板与管的坡口处熔合良好。填充层的焊缝不能太宽、太高,焊缝表面要保持平整。填充层的焊条角度如图3-78所示。
(3)盖面焊 盖面焊有两道焊缝,焊接前同样要将填充层焊道的焊渣清理干净,处理好局部缺陷。焊接下面的盖面焊道时,电弧要对准填充层焊道的下沿,保证底板熔合良好;焊接上面的盖面焊道时,电弧要对准填充焊道的上沿,该焊道应覆盖下面焊道的一半以上,以保证与立管熔合良好。盖面焊时的焊条角度如图3-79所示。
图3-78 填充层的焊条角度
图3-79 盖面焊的焊条角度
2.仰角焊位置的操作
管板仰角焊的焊接操作也分为三步,即打底焊、填充焊和盖面焊。
(1)打底焊 打底焊的作用是要保证坡口根部与底板熔合良好。焊接时,引燃电弧后对始焊端先预热,然后将电弧压低,待形成熔孔后,开始小幅度锯齿形横向摆动,进入正常焊接。操作时,电弧尽量控制的短些,保证底板与立管坡口熔合良好。打底层焊道的焊条角度如图3-80所示。
(2)填充焊 填充焊的操作要领与打底焊基本相同,填充焊道的表面不能有局部突出的现象,还需保证焊道的两侧熔合良好。盖面焊有两道焊道,先焊上面的焊道,后焊下面的焊道。焊上面的焊道时,摆幅略加大,焊道的下沿要覆盖填充焊道的一半以上。焊下面的焊道时,焊道上沿与上面的焊道要熔合良好,保证两条盖面焊道圆滑过渡,从而使焊缝外形成形良好。
图3-80 打底层焊道的焊条角度
(3)盖面焊 盖面焊时,其焊条的角度如图3-81所示。
图3-81 盖面焊道的焊条角度
3.管板水平固定焊的操作
管板水平固定全位置焊要求对平焊、立焊和仰焊的操作技能都要熟练。焊接过程中,焊条的角度随着焊接位置的不同而不断发生变化,各位置焊时的焊条角度如图3-82所示。
管板水平固定全位置焊的焊接操作步骤分打底焊、填充焊和盖面焊三步。
(1)打底焊 焊接时,采用左右两半圈进行焊接,先焊右半圈,后焊左半圈。
焊右半圈时,应在时钟4点到6点之间进行引弧,引燃电弧后,迅速将电弧移到6点至7点之间,对工件稍加预热后压低电弧,等管板根部充分熔合形成熔池和熔孔后开始向右焊接,在6点至7点处的焊缝尽量薄些,以利于左半圈焊接时连接平整。在时钟6点至5点之间时,为了避免产生焊瘤,操作时可采用短弧焊接和斜锯齿形运条,向斜下方摆动要快,向斜上方摆动相对要慢,并在两侧稍加停留。焊接时钟5点至2点之间时,焊条向工件里面送得要相对浅些,有时为了更好地控制熔池形状和温度,可采用间断灭弧焊或挑弧焊法熄弧焊接。采用间断灭弧焊时,如果熔池出现下坠,可横向摆动焊条且在两侧加以停留,扩大熔池面积,以使焊缝成形平整。焊接时钟2点至0点位置时,应将焊条端部偏向底板一侧作短弧锯齿形运条,并使电弧在底板处停留时间稍长些。
左半圈焊接前,应先将右半圈焊缝的开始和末尾处的焊渣清理干净。如果时钟6点至7点处焊道过高或有焊瘤、飞溅,必须清理干净。焊接开始时,先在时钟8点处引弧,引燃电弧后,快速将电弧移到始焊端(时钟6点处)进行预热,然后压低电弧,以快速斜锯齿形运条,由6点向7点处进行焊接。左半圈的焊接除方向不同外,其余与右半圈相同。当焊至0点处与右半圈焊道相连时,采用挑弧焊或间断灭弧焊,等弧坑填满后,熄弧停止焊接。
图3-82 各位置焊时的焊条角度
注:α1=75°~85°;α2=90°~105°;α3=100°~110°;α4=110°~120°;α5=30°;α6=45°;α7=35°~45°
(2)填充焊 填充焊的焊条角度和焊接步骤与打底焊相同,但焊条的摆动幅度比打底焊时略大些,摆动间隙也稍大。填充层的焊道尽量要薄些,将管材一侧的坡口填满,底板一侧要比管材坡口一侧宽出1.5~2mm,使焊道形成一斜面,以利于盖面焊的焊接。
(3)盖面焊 焊右半圈时,应从填充焊道上5点到6点的位置引弧,然后迅速将电弧移到6点至7点之间,预热后压低电弧,采用直线形运条法施焊,焊道尽量要薄,以利于左半圈焊道连接平整。6点至7点处的焊接采用锯齿形运条法,操作方法和焊条角度与填充焊相同。焊接5点至2点时可采用间断灭弧焊。焊接2点至12点时,由于熔敷金属在重力作用下易向管壁侧聚集,使得处于焊道上方的底板侧容易产生咬边,如果操作不当则很难达到所要求的焊脚尺寸。因此操作时可采用间断灭弧焊,当焊到12点的位置时,将焊条端部靠在填充焊道的管壁处,以直线形运条到12点与11点之间收弧,同时为左半圈的焊接打好基础。
左半圈焊接前,应先将右半圈焊缝的开始和末尾处的焊渣清理干净。如果接头处焊道过高或有焊瘤、飞溅,必须处理平整。焊接开始时,一般在8点左右的填充焊缝上引弧,然后将电弧拉至6点处的焊缝起始端预热,并压低电弧开始焊接。6点到7点之间一般采用直线形运条,同时保证连接处光滑平整。当焊至12点的位置时,一般作几次挑弧动作,将熔池填满后收弧。左半圈其他部位的操作可参照右半圈的焊接方法。
3.6.5 焊条电弧焊的补焊
焊条电弧焊在生产中除用于焊接外,还用于焊补加工。对于不同的泄露形式,应有针对性地采用不同的止漏方案和补焊方案,而焊补过程中,正确地选择焊接规范并运用合适的操作方法则又是在确定止漏方案后能否堵漏成功的关键。
1.泄漏原因分析
要确定正确的堵漏方案,首先要分析找出发生泄漏的原因。一般设备泄漏处的介质都为蒸汽,因此观察泄漏点介质喷出的形状可初步确定泄露的原因。
若喷出的介质成束状或气柱状,则说明是砂眼;若成扇状,则说明缺陷是本体材料内部的夹渣或松散组织。用焊工刨锤尖部轻微敲打距泄漏点50mm的远本体并逐渐接近泄漏点,若声音由脆变哑,则说明缺陷大都是由腐蚀引起的。有条件的应对泄漏处附近进行测厚,若壁厚<2mm,不得采用直焊法堵漏。
2.堵漏方案的确定
通过对泄漏处的介质进行检查和判断后,便可确定正确的堵漏方案。
对砂眼可以采取捻缝后补焊法。捻打时必须用专门的头部呈球形的冲子,以锤子轻微敲打砂眼四周金属,通过使金属产生塑性变形来缩小砂眼而止漏。在捻打砂眼止漏后,必须进行补焊。在补焊时运条慢、熔池过深和裂纹未收严也都会产生砂眼。因此要注意控制熔深,运条动作不宜太慢,引弧点应在收严的裂纹上,熄弧时需填满弧坑。补焊前要仔细检查裂纹,引弧点应在收严的范围内,发现裂纹中有异物应清除干净。补焊能使裂纹自然收严一小段后,才能采用分段逆向焊法。
在管道、容器及阀体上,通常会在原有焊缝及应力集中处产生裂纹。对本体裂纹的带压堵漏,一般采用分段逆向焊法,即在焊缝起点引弧,向裂纹反方向运条,在原焊缝金属上熄弧,使裂纹起始段由于裂纹收缩而收紧。再在已收严的一小段裂纹末端引弧,反向运条熄弧。采用分段逆向焊法能保证焊接电弧、熔池及熄弧点都避开喷出的介质。
对泄漏介质为易燃、易爆物的焊件不应采用补焊法,对于压力不高的可燃介质可进行带引流阀门的加强板补焊法止漏。
对于由各种原因引起的本体局部腐蚀或流体冲刷减薄的管壁,在补焊时可以采取引流阀门、加补强板及上下引流阀门套箱等方法止漏。引流阀门应注意选择相应压力等级的闸阀,加强补焊时则必须采用壁厚足够的优质钢板。在套箱成形焊接时也可以采取分段逆向焊法。
3.补焊工艺的确定
补焊工艺的确定主要是根据被修复件的材质、补焊部位和要求制订合理的工艺。一般应注意以下问题:
1)坡口形式。坡口形式要根据待补焊部位的几何形状制订坡口的加工方法,以能保证缺陷全部被清除为标准。坡口形式的确定以损坏部件易焊透且尽量少消耗焊条为目的,另外还要考虑焊后的加工和焊件的变形。
2)焊接材料。应根据被焊母材的需要选用相匹配的焊接材料,此外,还要根据现场的焊接设备情况和母材的材质,考虑选用酸性或碱性焊条。一般情况下应选用碱性低氢型焊条,因为此焊条的黏性较大,熔池内的熔化金属不易被吹走。焊接电流比正常情况下焊接各位置的电流要高出35%~60%,以增强电弧吹力,提高熔合性,提高熔池和母材的温度。
3)在补焊工作量不大时,尽量采用小直径焊条进行补焊。
4)在保证焊接修复时能够焊透、熔合良好及不产生夹渣的情况下尽量选择焊接电流的下限,以防止温度过高产生变形、飞溅、咬边和气孔缺陷等。为了防止产生缺陷,焊接时电弧不要拉起过长或把电弧压得太低,应根据具体情况,以电弧能正常燃烧为准。
5)根据焊接修复时坡口的形式和焊后加工的要求,在保证熔合良好的情况下,焊接速度要根据焊件灵活控制。补焊时,一般采用多层多道的焊接,因为多层多道的焊接能起到预热和缓冷的作用,且有利于提高焊缝金属的塑性和韧性。
6)焊接电源采用直流或交流电焊机均可。在采用直流电焊机时应正接,宜选择φ2.5~φ3.2mm的焊条,引弧时应采用接触法。对于捻打后较小的针孔状砂眼,补焊时可先在周围以较长的电弧轻微预热,此时熔滴金属较细,并不形成熔池。当温度升高后,应迅速而准确地将焊条引向缺陷点。当孔眼被堵住后,应马上熄弧。采用分段逆向焊法时,电弧长度应尽量控制在2~4mm,不能在裂纹上熄弧,熔池深度要低于工件厚度的1/2。
7)根据具体要求选择合理的热处理工艺。