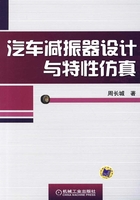
1.3 液压筒式减振器发展及研究状况
1.3.1 液压减振器发展状况
液压筒式减振器是汽车上最广泛使用的减振器,起初采用较多的是摇臂式液阻减振器。第二次世界大战期间,美军吉普车上采用了筒式液阻减振器并在战场上获得成功,此后筒式液阻减振器很快成为主流产品。它具有工艺简单、成本低、寿命长、质量轻等优点,主要零件采用了冲压、粉末冶金及精密拉管等高效工艺,适于大批量生产。
节流阀结构和特性对减振器的特性有决定性影响。筒式减振器有三种典型的阀结构,分别为板阀式、滑阀式和弹性阀片式。其中,板阀式和滑阀式多用于早期轿车减振器,通过改变弹簧刚度和弹簧预变形量调节。有关文献已对其节流特性进行了理论分析和实验研究。这两种阀的优点是结构简单,工作可靠,但由于板阀较小的升程就会形成较大的流通面积,因此导致减振器速度特性呈软非线性特性;而滑阀与导向座之间存在摩擦,导致阀运动响应滞后或不连续。
弹性阀片式节流阀的突出优点是,易于通过增减阀片数量和垫片等措施改变阀的节流特性;缺点是要求加工精度要求较高,使用过程中当阀片与阀座间存在杂质颗粒导致阀片关闭不严时,会造成减振器阻尼力的显著下降。这种节流阀最初多用于赛车减振器,随着制造技术的提高,目前已广泛应用于现代轿车。
作为在汽车上应用最多的筒式减振器,其设计开发技术也正经历着由基于经验设计-试验修正的传统设计方法,向着基于CAD/CAE技术的现代设计方法转变。但是据有关资料分析,先前,国内外尚无适合节流阀片精确设计的解析式,缺少准确、可靠的设计方法以及特性仿真模型,因此制约了现代设计技术的实现和应用。
1.3.2 节流阀片研究状况
1.阀片变形研究
对于汽车减振器节流阀片的变形,国内外已经很多学者进行了大量研究。大多是利用有限元分析软件,对阀片变形量进行数值分析。也有利用弹性力学原理,对阀片变形量进行分析研究,但是,只是通过阀片变形微分方程,利用边界条件列出一个通解,只表示节流阀片可利用弹性力学原理进行分析研究,而不能达到能实际应用的程度,没有创建一个可用于阀片厚度设计、变形计算的简单、准确、实用的解析式,难以在实际阀片设计中应用。
当今,弹性阀片变形计算方法有两种。一是利用《机械设计手册》的最大挠度系数和计算公式,二是利用现代流行的有限元分析软件,如ANSYS。其中,利用《机械设计手册》根据阀片外半径rb与内半径ra之比rb/ra,查得阀片最大挠度系数和计算公式,可粗略地计算在一定压力下阀片在外半径rb处的最大挠度。利用有限元分析软件,首先根据阀片的结构建立仿真分析模型,然后对模型划分有限元网格并施加载荷,最后利用仿真程序得到阀片变形量数值解。
以上两种计算方法对于阀片设计计算各有缺点。对于《机械设计手册》的最大挠度系数法,虽然具有计算解析式,可对阀片厚度进行粗略设计。但是,当实际阀片内、外半径比值在手册中没有给出时,就难以准确查得最大挠度系数。同时,该方法只能计算阀片在外半径rb处的最大挠度,而实际阀片设计时需要计算在阀口位置半径rk处的变形量。
对于有限元分析软件,虽然可以得到阀片在任意位置半径r处变形量的数值解,且比《机械设计手册》的最大挠度系数法精确。但是,由于该方法没有阀片变形量计算的解析式,不能对阀片厚度进行设计,只能对给定结构阀片进行变形量数值仿真验证。
因此,先前对阀片变形的两种计算方法,都不能满足对减振器参数进行精确设计、特性分析和仿真的要求。
2.叠加阀片研究现状
汽车减振器节流阀片大都是利用多片节流阀片叠加,以满足减振器不同的特性要求。叠加节流阀片与单片阀片相比具有很多优点。
先前,国内外已有学者采用有限元分析软件对叠加阀片进行初步研究,并得到了有价值的结论,例如,叠加阀片不等于各叠加阀片厚度之和,叠加阀片变形量不能用单片厚度等于叠加阀片厚度之和的阀片代替,叠加阀片变形量与叠加顺序无关等。
但是,这些研究没有解决叠加阀片设计中的关键问题,不能满足减振器实际设计和生产的需要,如多片阀片叠加的等效厚度问题、叠加阀片厚度和应力之间关系问题、设计厚度阀片拆分设计为叠加阀片问题及叠加阀片最大厚度问题等。目前,山东理工大学已对叠加阀片进行研究解决了上述问题,并建立了叠加阀片设计原则。
1.3.3 流体阻尼研究状况
流体阻尼技术早已应用于很多领域,直到最近二三十年才在理论上形成新的学科。目前,流体阻尼的机理普遍被认为是耦连的机械结构和流体之间相对运动而耗损能量。小孔阻尼的能量损失实际包括了黏滞损耗和涡流损耗两部分。实际上,减振器阻尼产生的环境非常复杂,引起阻尼特性变化的原因有以下几点:
1)活塞上下表面对流体的压力阻尼,活塞周边与油缸之间的薄膜阻尼力。
2)小孔节流引起的黏滞阻力与压力阻尼。
3)油缸壁与流体的黏滞阻尼,活塞杆壁与密封圈之间的密封阻尼。
4)特殊工况下活塞杆的振动引起的振动阻尼。
5)油液中的气泡与涡流引起的功耗。
6)油路突然扩大、缩小以及改变方向所产生的局部阻力损失。
1994年,Koenraad Reybrouck所发表的论文标志着国外汽车减振器技术领域的理论研究最新动向。文中提出了处理减振器高非线性行为的一般方法,涉及一系列正弦激励信号下阻尼力的测量,所提出的减振器模型对两个问题作了解答:
1)行驶中汽车的行为不仅与减振器特性参数的大小有关,而且还与减振器特性曲线(示功图)的形状有关。
2)减振器阻尼力不仅是速度的函数,而且还是位移、加速度和温度的函数。
但该减振器模型没有考虑局部阻力损失,例如,油液流动方向改变、流道突然扩大和缩小等,同时,油液流动只考虑了紊流,没有考虑在低速时的层流流动。因此,该模型限制了在低速度下的准确性,也限制了参数设计和特性仿真的准确性。
1.3.4 设计方法研究现状
汽车减振器阀系参数严重影响减振器的特性,因此,国内外有很多学者一直致力减振器阀系参数设计研究。目前,减振器阀系参数设计方法有两类。
(1)利用《机械设计手册》提供的最大挠度系数和公式进行设计 利用开阀前速度点,根据节流压力和流量之间的关系,对常通节流孔面积进行设计;利用开阀后速度点,对阀片厚度进行设计。减振器阻力特性是非线性的,不同速度点设计得到的参数值不同。因此,对减振器阀系参数大都是凭经验确定一个速度点进行设计,先前,国内外对单个阀系参数只能实现单速度点设计。
(2)利用计算机和软件对减振器进行计算机辅助设计(CAD)先前对节流阀片缺少精确设计的解析式,对减振器阀系参数缺少准确、可靠的设计方法,因此,也难以保证CAD软件的准确性和可靠性,制约了现代设计技术的推广和应用。
以上两种设计方法存在的缺点为
1)所采样的阀片变形计算公式是一个粗略计算公式,半径和内半径阀片不同时,最大挠度系数难以准确确定,对阀片变形量计算不准确。
2)利用该方法计算得到的是阀片在外半径rb处的最大挠度,不是阀片在阀口位置的变形量,而实际节流阀开度是由节流阀片在阀口位置的变形量所决定的,利用阀片最外半径rb处的变形量,代替阀口位置半径rk处的变形量,将对参数设计产生很大误差。
3)阻尼力是非线性的,利用不同速度设计点得到的设计参数不同。即使对设计速度点进行调整,但是,当减振器参数发生变化时,速度点也将变化。
以上两种传统设计方法,因没有阀片开度精确计算公式,没有可靠的设计理论和方法,因此难以获得准确、可靠的设计参数。