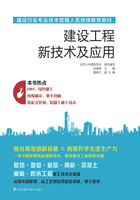
第四节 水泥粉煤灰碎石桩(CFG)复合地基技术
一、技术原理及技术特点
1)基本概念
水泥粉煤灰碎石桩复合地基是由水泥、粉煤灰、碎石、石屑或砂加水拌合形成的高黏结强度桩(简称CFG桩),通过在基底和桩顶之间设置一定厚度的褥垫层以保证桩、土共同承担荷载,使桩、桩间土和褥垫层一起构成复合地基。桩端持力层应选择承载力相对较高的土层。水泥粉煤灰碎石桩复合地基具有承载力提高幅度大、地基变形小、适用范围广等特点。
2)技术特点
根据工程地质条件不同,CFG桩一般可采用长螺旋钻孔管内泵压灌注成桩工艺和振动沉管灌注成桩工艺。CFG成桩的主要施工工艺是长螺旋钻孔管内泵压灌注成桩,属排土成桩工艺。该工艺具有穿透能力强、无泥浆污染、无振动、低噪声、适用地质条件广、施工效率高及质量容易控制等特点。当地基土是松散的饱和粉细砂、粉土时,以消除液化和提高地基承载力为目的,可选择振动沉管成桩施工工艺。但该工艺用在难以穿透较厚的硬土层、砂层和卵石层,在饱和黏性土中成桩会造成地表隆起及挤断已成桩,存在振动噪声污染及扰民等缺点。
二、主要技术指标
根据工程实际情况,水泥粉煤灰碎石桩可选用水泥粉煤灰碎石桩常用的施工工艺,包括长螺旋钻孔、管内泵压混合料成桩、振动沉管灌注成桩及长螺旋钻孔灌注成桩四种施工工艺。主要技术指标为:
①桩径宜取350~600mm。
②桩端持力层应选择承载力相对较高的地层。
③桩间距宜取3~5倍桩径。
④桩身混凝土强度满足设计要求,通常不小于C15。
⑤桩垂直度不大于1.5%。
⑥褥垫层宜用中砂、粗砂、碎石或级配砂石等,不宜选用卵石,最大粒径不宜大于30mm。厚度150~300mm,夯填度不大于0.9。
实际工程中,以上参数根据场地岩土工程条件、基础类型、结构类型、地基承载力和变形要求等条件或现场试验确定。
对于市政、公路、高速公路、铁路等地基处理工程,当基础刚度较弱时宜在桩顶增加桩帽或在桩顶采用碎石+土工格栅、碎石+钢板网等方式调整桩土荷载分担比例,提高桩的承载能力。
三、施工技术应用
1.技术应用范围
适用于处理黏性土、粉土、砂土和自重固结的素填土等地基。对淤泥质土应按当地经验或通过现场试验确定其适用性。就基础形式而言,既可用于条形基础、独立基础,又可用于箱形基础、筏形基础。采取适当技术措施后亦可应用于刚度较弱的基础以及柔性基础。
①长螺旋钻孔灌注成桩,适用于地下水位以上的黏性土、粉土、素填土、中等密实以上的砂土。
②长螺旋钻孔、管内泵压混合料灌注成桩,适用于黏性土、粉土、砂土,粒径不大于60mm、土层厚度不大于4m的卵石(卵石含量不大于30%),以及对噪声或泥浆污染要求严格的场地。
③振动沉管灌注成桩,适用于粉土、黏性土及素填土地基。
④泥浆护壁成孔灌注成桩,适用土性应满足《建筑桩基技术规范》(JGJ94—2008)的有关规定。对桩长范围和桩端有承压水的土层,应首选该工艺。
⑤锤击、静压预制桩,适用土性应满足《建筑桩基技术规范》(JGJ94—2008)的有关规定。
2.施工设计要点
水泥粉煤灰碎石桩的设计应符合下列规定:
①水泥粉煤灰碎石桩应选择承载力相对较高的土层作为桩端持力层。
②桩径:长螺旋钻孔中心压灌、干成孔和振动沉管成桩宜取350~600mm;泥浆护壁钻孔灌注素混凝土成桩宜取600~800mm;钢筋混凝土预制桩宜取300~600mm。
③桩距应根据基础形式、设计要求的复合地基承载力和复合地基变形、土性、施工工艺确定。箱形基础、筏形基础和独立基础,桩距宜取3~5倍桩径;墙下条形基础单排布桩宜取3~6倍桩径。桩长范围内有饱和粉土、粉细砂、淤泥、淤泥质土层,采用长螺旋钻中心压灌成桩施工中可能发生串孔时宜采用大桩距或采用跳打措施。
④水泥粉煤灰碎石桩可只在基础内布桩,应根据建筑物荷载分布、基础形式、地基土性状,合理确定布桩参数:
对框架核心筒结构形式,核心筒部位布桩,宜减小桩距、增加桩长或加大桩径,提高复合地基承载力和模量。
对设有沉降缝或抗震缝的建筑物,宜在沉降缝或抗震缝部位,采用减小桩距、增加桩长或加大桩径布桩,以防止建筑物发生较大相向变形。
对相邻柱荷载水平相差较大的独立基础,应按变形控制进行复合地基设计,荷载水平高的宜采用较高承载力确定布桩参数。
对筏形基础、筏板厚度与跨距之比小于1/6,梁板式基础、梁的高跨之比大于1/6以及板的厚跨比(筏板厚度与梁的中心距之比)小于1/6时,基底压力不满足线性分布,不宜采用均匀布桩,应主要在柱边(平板式筏形基础)和梁边(梁板式筏形基础)外扩2.5倍板厚的面积范围布桩。
墙下条形基础、当荷载水平不高时,可采用墙下单排布桩。
⑤桩顶和基础之间应设置褥垫层,褥垫层厚度宜取0.4~0.6倍桩径。褥垫材料宜用中砂、粗砂、级配砂石和碎石等,最大粒径不宜大于30mm。
⑥水泥粉煤灰碎石桩复合地基承载力特征值,应通过现场复合地基载荷试验确定,初步设计时也可按下式估算:
复合地基承载力特征值:

式中fspk——复合地基承载力特征值(kPa);
m——面积置换率;
Ra——单桩竖向承载力特征值(kN);
Ap——桩的截面积(m2);
β——桩间土承载力折减系数,宜按地区经验取值,如无经验时可取0.75~0.95,天然地基承载力较高时取大值;
λ——单桩承载力发挥系数,宜按当地经验取值,无经验值可取0.7~0.9;
fs k——处理后桩间土承载力特征值(k Pa),宜按当地经验取值,如无经验时,可取天然地基承载力特征值。
⑦单桩竖向承载力特征值Ra的取值,应符合下列规定:
当采用单桩载荷试验时,应将单桩竖向极限承载力除以安全系数2;
当无单桩载荷试验资料时,可按下式估算:
单桩承载力特征值:

式中up——桩身周长(m);
n——桩长范围内所划分的土层;
qsi、qp——桩周第i层土的侧阻力、桩端端阻力特征值(k Pa),可按现行国家标准《建筑地基基础设计规范》(GB50007—2011)的有关规定确定;
li——第i层土的厚度(m)。
⑧桩体试块抗压强度平均值应满足下式要求:

式中fcu——桩体混合料试块(边长150mm立方体)标准养护28d,立方体抗压强度平均值(kPa)。
⑨地基处理后的变形计算应按现行国家标准《建筑地基基础设计规范》(GB50007—2011)的有关规定执行。复合土层的分层与天然地基相同,各复合土层的压缩模等于该天然地基压缩模量的ζ倍,ζ值可按下式确定:

式中fak——基础底面下天然地基承载力特征值(kPa)。
3.施工技术要点
1)材料要求
(1)水泥
宜选用42.5级普通硅酸盐水泥,使用前送验复试。
(2)碎石
碎石粒径为20~50mm,松散密度为1.39t/m3,杂质含量小于5%。
(3)石屑或砂
石屑粒径为2.5~10.0m,松散密度为1.47t/m3,杂质含量小于5%。
砂为中砂或粗砂,含泥量不大于5%。
(4)粉煤灰
宜选用Ⅰ级或Ⅱ级粉煤灰,细度分别不大于12%和20%。
(5)外加剂
多为泵送剂、早强剂、减水剂等,掺量通过试验确定。
2)配合比
根据拟加固场地的土质情况及加固后要求达到的承载力而定。水泥、粉煤灰、碎石混合料按抗压强度相当于C7~C1.2低强度等级混凝土,密度大于2000kg/m3,掺加最佳石屑率(石屑质量与碎石和砂总质量之比)约为25%的情况下,当W/C(水与水泥用量之比)为1.01~1.47, F/C(粉煤灰与水泥质量之比)为1.02~1.65,混凝土抗压强度约为8.8~14.2 MPa。
3)主要施工机具
桩成孔、灌注一般采用振动式沉管打桩机架,配DZJ90型变矩式振动锤,亦可采用长螺旋钻机。此外,配备混凝土搅拌机、混凝土输送泵和连接混凝土输送泵与钻机的钢管、高强柔性管以及长短棒式振捣器、机动翻斗车、小推车等。
4)施工要点
(1)按CFG桩位平面图测设桩位轴线
基坑内施工时,边坡(离桩边)应外扩不小于1.0m,以利边角桩施工。
(2)采用振动式沉管打桩机施工
①桩施工程序为:桩机就位→沉管至设计深度→停振下料→振动捣实后拔管→留振→振动拔管、复打。应考虑隔排隔桩跳打,新打桩与已打桩间隔时间不应少于7d。桩施工工艺流程,如图2-5所示。

图2-5 水泥粉煤灰碎石桩施工工艺流程
(a)打入管桩;(b)、(c)灌水泥粉煤灰碎石、振动、拔管;(d)成桩1—桩管;2—水泥粉煤灰碎石桩
②桩机就位须平整、稳固,沉管与地面保持垂直。如带预制混凝土桩尖,需埋入地面以下300mm。
③混合料应按设计配合比配制,投入搅拌机加水拌合,搅拌时间不少于2min,加水量由混合料坍落度控制,一般坍落度为30~50mm;成桩后桩顶浮浆厚度一般不超过200mm。
④在沉管过程中用料斗向桩管内投料,待沉管至设计标高后,须继续尽快投料,直至混合料与钢管上部投料口齐平。如上料量不够,可在拔管过程中继续投料,以保证成桩标高及密实度的要求。
⑤当混合料加至与钢管投料口齐平后,沉管在原地留振10s左右,即可边振动边拔管,拔管速度控制在1.2~1.5m/min,每提升1.5~2.0m,留振20s。桩管拔出地面确认成桩符合设计要求后,用粒状材料或黏土封顶,移机进行下一根桩施工。
⑥为使桩与桩间土更好地共同工作,在基础下宜铺一层150~300mm厚的碎石或灰土垫层。
(3)采用长螺旋钻机施工
①工艺流程:桩机就位→钻孔→混凝土配制、运送及泵送→压灌混凝土成桩→成桩验收。
②桩机就位时,必须保持平稳,不发生倾斜、移位。为准确控制造孔深度,应在桩架上或桩管上做出控制的标尺,以便于在施工中观测、记录。
③应根据桩长来安装钻塔及钻杆。每施工2~3根桩后,应对钻杆连接处进行紧固。
④钻进速度应根据土层情况确定:杂填土、黏性土、砂卵石层为0.2~0.5m/min;素填土、黏性土、粉土、砂层为1.0~1.5m/min。
钻到桩底设计标高,验孔后,进行压灌混凝土。
⑤混凝土地泵位置应与钻机的施工顺序相配合,两者距离一般在60m以内为宜,尽量减少弯道。
⑥泵送前采用水泥砂浆进行润湿,但不得倒入泵孔内。泵送时,应保持料斗内混凝土的高度,不得低于400mm,以防吸进空气造成堵管。
当钻机移位时,地泵料斗内混凝土应连续搅拌。
混凝土的原材料、配合比强度等级应符合设计要求。
⑦成桩施工各工序应连续进行。
⑧钻杆的提升速度应与混凝土泵送量相一致,其充盈系数不小于1.0。应通过试桩确定提升速度及何时停止泵送。遇到饱和砂土或饱和粉土层,不得停泵待料,并减慢提升速度。成桩过程中应经常检查排气阀是否工作正常。
⑨成桩后必要时,应对桩顶3~5m范围内进行振捣。
4.施工注意事项
①冬季施工时,混合料入孔温度不得低于5℃,对桩头和桩间土应采取保温措施。
②清土和截桩时,应采取措施防止桩顶标高以下桩身断裂和桩间土扰动。
③褥垫层铺设宜采用静力压实法,当基础底面下桩间土的含水量较小时,也可采用动力夯实法,夯填度(夯实后的褥垫层厚度与虚铺厚度的比值)不得大于0.9。
④施工垂直度偏差不应大于1%;对满堂布桩基础,桩位偏差不应大于0.4倍桩径;对条形基础,柱位偏差不应大于0.25倍桩径,对单排布桩桩位偏差不应大于60mm。
⑤桩施工完毕,经7d达到一定强度后,方可进行基坑开挖。
⑥设计桩顶标高不深(小于1.5m),宜采用人工开挖;大于1.5m时可采用机械开挖,但下部宜预留500mm用人工开挖,以避免损坏桩头部位。
⑦水泥粉煤灰碎石桩宜用于提高地基承载力和减少变形的桩基,不宜用于挤密松散砂性土为主的地基。
⑧施工前,应进行试桩,确定配合比、桩体强度和工艺参数,符合设计要求后方可施工。
5.施工质量检验
1)施工期质量检验应包括以下内容
①水泥、粉煤灰、砂及碎石等原材料应符合设计要求。
②施工中应检查施工记录、桩数、桩位偏差、混合料的配合比、坍落度、提拔钻杆速度(或提拔套管速度)、成孔深度、混合料灌入量、褥垫层厚度、夯填度和桩体试块抗压强度等。
2)竣工后质量验收
竣工后质量检验应包括以下内容:
①施工结束后,应对桩顶标高、桩位、桩体质量、地基承载力以及褥垫层的质量做检查。
②水泥粉煤灰碎石桩复合地基,其承载能力检验应采用复合地基荷载试验,宜在施工结束后28d后进行。试验数量宜为总桩数的0.5%~1%,且每个单体工程的试验数量不应少于3点。
③应抽取不少于总桩数10%的桩进行低应变动力试验,检测桩身完整性。
④水泥粉煤灰碎石桩复合地基的质量检验标准应符合表2-1的规定。
表2-1 水泥粉煤灰碎石桩复合地基的质量检验标准

注:1.夯填度指夯实后的褥垫层厚度与虚体厚度的比值。
2.桩径允许偏差负值是指个别断面。