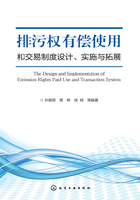
3.2 炼焦行业
3.2.1 行业概况
3.2.1.1 生产工艺
目前我国焦炭的主流生产工艺主要有水平室式常规机械化焦炉、捣固式热回收焦炉、直立炉生产工艺。
(1)水平室式常规机械化焦炉
机械化焦炉生产工艺已很成熟,其备煤、炼焦和煤气净化工艺流程见图3-3~图3-5。

图3-3 水平室式炼焦及焦处理工艺流程排污环节示意

图3-4 水平室式焦炉煤气净化氨分解工艺流程

图3-5 水平室式焦炉煤气净化硫铵工艺流程
(2)捣固式热回收焦炉
目前捣固式热回收焦炉以SJ—96型捣固式热回收焦炉和QRD—2000捣固式热回收捣固式焦炉为代表,前者是由山西三佳煤化有限公司开发研制,属冷装冷出工艺;后者由山西省焦化技术研究会和山西省化工设计院共同研发,属热装热出工艺;两者均已经过多年试生产运行。
①SJ-96型捣固式热回收焦炉(冷装冷出) SJ-96型捣固式热回收焦炉已通过山西省科技厅的技术鉴定,生产工艺流程见图3-6,其特点如下所述。

图3-6 冷装冷出捣固式热回收焦炉生产工艺流程
1)SJ-96型焦炉通过几年试产考验,证明在科学配煤、分层捣固情况下,可连续稳定生产出适应市场需求的不同品种的优质铸造焦、冶金焦。
2)SJ-96型焦炉负压操作、原料煤和焦炭冷装冷出、联体炉相邻炉引火、应用一次空气和二次空气燃烧技术及可调节装置。炉底建有严格防渗措施等,炼焦煤在充分隔绝空气下干馏,废气经充分燃烧后排放。吨焦耗煤较低[1.32t(煤)/t(焦)],焦炉无组织排放少、废气中BaP排放很小,熄焦用水闭路循环无渗漏。
3)SJ-96型焦炉结构合理、操作方便、焦炉投资低(包括焦炉、主烟道、烟囱、熄焦循环水系统,平均吨焦投资41.3元),经济效益好。
4)SJ-96型焦炉废气排放温度较高(800℃左右),可回收利用。
冷装冷出捣固式热回收焦炉工艺流程见图3-6,炉体结构示意见图3-7。

图3-7 冷装冷出捣固式热回收焦炉炉体示意
②QRD-2000捣固式热回收捣固机焦炉(热装热出) 该炉由炉顶、炉底、炭化室、四联拱燃烧室、主墙、机焦侧炉门及护炉铁件等组成。
1)焦炉箱式捣固侧装煤,炼焦炉负压操作,水平接焦,使得装煤炼焦推焦过程减少了烟尘外泄。
2)无煤气净化过程,生产过程只有熄焦水和脱硫除尘水,熄焦水闭路循环,脱硫除尘水经处理后回用于本环节。
3)捣固采用机械或液压捣固,液压捣固机噪声低,维修量小。同时煤饼表面平整,减少煤表面燃烧。
4)炼焦废气余热全部用于发电,实现了资源的综合利用。
5)炼焦煤中可配入大量弱黏结性煤,节约了炼焦煤资源,降低了炼焦成本。
6)投资低,建设速度快。动力消耗少,操作方便,工艺流程简单,操作方便。
QRD-2000捣固式热回收机焦炉工艺流程见图3-8,炉体结构示意见图3-9。

图3-8 QRD-2000捣固式热回收机焦炉生产工艺流程

图3-9 QRD-2000捣固式热回收机焦炉立面
1—炉底;2—四联拱燃烧室;3—炭化室;4—主墙;5—炉顶
(3)直立炭化炉
半焦(兰炭)炭化炉是以不黏煤、弱黏煤、长焰煤等为原料,在炭化温度750℃以下进行低温干馏,以生产半焦(兰炭)为主的生产装置。加热方式分内热式和外热式。其生产工艺主要包括备煤车间、炼焦制气车间、污水处理、煤气储备及输送部分。
半焦生产工艺简介:合格的入炉煤用胶带机卸入炉组上部的储煤仓,经带送机再经放煤旋塞和辅助煤箱装入直立炭化炉内。根据生产工艺要求,每隔一段时间打开放煤旋塞向直立炭化炉内自动加煤一次。加入炉内的块煤自上而下移落,与燃烧室送入的高温气体逆流接触。炭化室上部为预热段,块煤在此被预热到360~400℃;接着进入炭化室中部的炭化段,块煤在此段被加热到680~720℃,并被炭化为半焦;半焦通过炭化室下部的冷却段时,经排焦箱与炉底水封槽内产生的水蒸气换热冷却至200~160℃,最后被推焦机推入炉底水封槽内被冷却到50℃左右由刮焦机连续刮出,通过刮焦机尾部时经烘干装置烘干后落入半焦料仓后进入筛焦运焦系统。煤料炭化过程产生的荒煤气与进入炭化室的高温废气混合后,经上升管、桥管进入集气槽,120℃左右的混合气体在桥管和集气槽内经循环氨水喷洒被冷却至80℃左右。混合气体和冷凝液送至煤气净化工段。其工艺流程见图3-10,生产工艺流程简图见图3-11。

图3-10 直立炉生产工艺流程

图3-11 直立炉工艺流程简图
直立焦炉以SH-2007型内热式直立炭化炉为例,单座产能1.0×105t/a,其特点如下:
a.炉体结构简单,造价低;高效内燃;低温干馏;半焦、中温煤焦油和煤气质量有保障;b.炉体结构由内部耐火砖布气花墙、耐火砖内墙、中心隔墙、保温隔热层和炉体墙组成;c.炉顶部安装布料集气装置;d.炉上、中、下部和出焦口均装有测温装置;e.供给炉内的加热煤气和空气均设计有计量装置和燃气混合器装置;f.采用连续上煤定时自动布料、水封密闭出焦;g.采用多项密封隔热保温措施,保证直立炭化炉炉体严密性,防止高温烟气外逸,提高炭化炉热工效率。
3.2.1.2 污染物排放
(1)水平室式常规机械化焦炉
①大气主要污染物 机械化焦炉大气主要污染物排放来自装煤、推焦、熄焦、脱硫等环节。
1)焦炉装煤烟气。焦炉在装煤过程中产生的烟气主要来自于3个方面:a.煤料装入炭化室占据炭化室空间排出的热空气;b.煤料装入炭化室后与高温炉墙接触,煤中部分挥发分裂解产生的荒煤气;c.煤中水分汽化生成的水蒸气。炉内热空气上升及煤裂解产生的荒煤气和水蒸气从装煤孔、炉门等处冒出,同时带出大量烟、粉尘,在无控制措施情况下,大量烟、粉尘排入大气,严重污染环境。据资料介绍,短时间内装煤产生的烟尘是正常结焦阶段的7倍,所排放的污染物占整个炼焦过程污染物排放总量的50%~60%。
2)推焦。推焦过程中,随着炉门打开、焦炭的推出,大量的烟尘外逸。焦炉在推焦过程污染排放特点主要是点多、面广、分散,污染物种类多、危害性大、难治理。
3)熄焦。目前熄焦工艺分为湿法熄焦和干法熄焦两种。干法熄焦是目前国家推广的技术。湿法熄焦是焦炭被送入熄焦塔内(一般为36m高),水与赤热的焦炭接触,期间伴有大量的熄焦水蒸发和污染物逸散。干法熄焦是用惰性气体作热载体,由循环风机鼓入冷却室内,吸收焦炭显热,流经余热锅炉后回到冷却室,如此循环将焦炭冷却至250℃以下。
湿法熄焦目前采用塔内设置折流板的抑尘方式,减少熄焦过程焦尘外排。干熄焦除尘系统包括工艺除尘和环境除尘。工艺除尘分为两次除尘:一次除尘设在干熄炉出口、余热锅炉入口,其主要作用是将循环气体中的大颗粒粉尘除去,以保护余热锅炉炉管;二次除尘设在余热锅炉出口,循环风机入口,其主要作用是将循环气体中的小颗粒粉尘除去,以保护循环风机叶轮。
环境除尘包括装焦除尘、排焦除尘和焦炭运输除尘三部分。
常规的湿法熄焦除了与干法熄焦相比存在着不能回收焦炭显热等缺点外,还存在熄焦后焦炭水分不均匀及大量逸散物污染环境等缺点。但是由于常规湿法熄焦具有工艺简单、投资少等优点,仍在我国乃至世界各国普遍使用。有些采用干法熄焦的工厂,还将湿熄焦塔作为干熄焦大修或故障时的备用设备。因此,世界各国焦化科技工作者为了克服湿法熄焦的缺点,发挥其优势,研究开发出一些新型湿法熄焦工艺,并取得了较显著的成果,如美钢联的低水分熄焦和德国蒂森克虏伯公司的稳定熄焦又叫集水式熄焦,低水分熄焦已成功用于我国的邯钢和鞍钢等焦化厂。
所谓低水分熄焦就是熄焦水在设定压力下经过巧妙排列的水喷嘴以大水流喷射到熄焦车内的红焦表面,获得水分低且均匀的焦炭熄焦过程。该工艺一般与定点接焦的熄焦车相配合,以获得更理想的熄焦效果。
所谓稳定熄焦就是定点接焦的熄焦车接焦后开到熄焦塔下定位后不再移动,大量的水经管道进入特制的熄焦车下部的倾斜夹层中通过斜底上分布的出水口由下至上喷水获得水分低且均匀稳定的焦炭的熄焦过程。
表3-15和表3-16分别为湿法熄焦和干法熄焦工艺污染物排放量的统计结果。
表3-15 湿法熄焦与干法熄焦污染物排放量的比较

①仅为熄焦过程的排放量,不含焦运输和焦处理过程。
表3-16 湿法熄焦与干法熄焦污染物排放统计结果

①表中焦尘排放量的最大值为德国的规定指标。
4)煤气脱硫
炼焦过程中煤中约有30%的硫进入焦炉煤气,95%的硫以H2S的形式存在。焦炉煤气中一般含有H2S 6~8g/m3、HCN 1.5~2g/m3,若不事先脱除,将会有50%的HCN和10%~40%H2S进入氨、苯回收系统,加剧了设备的腐蚀。焦炉煤气净化工艺流程的选择,主要取决于脱氨和脱硫的方法。近十几年来,我国已基本掌握了具有世界先进水平的各种脱氨、脱硫新工艺,可以根据用户的不同要求组合各种焦炉煤气净化流程。
②废水主要污染物 焦化废水是由配煤所含水分和炼焦生产的化合水组成,主要源自煤气的冷却和化工产品回收过程产生的废水。
焦化废水来源主要包括以下几类。
1)剩余氨水或蒸氨废水。由装炉表面的湿存水、镁干馏产生的化合水以及焦炉上升管、集气管喷射的蒸汽和冷凝工段清扫管道的蒸汽组成。该废水是焦化厂最重要的酚氰水来源,其水量占焦化废水总量的1/2以上。废水含酚600~1200mg/L,COD约为3000mg/L,氨氮200~300mg/L。
2)煤气冷却水。在进行煤气的最终冷却时,煤气中一定数量的酚、萘、氰化物、硫化物及吡啶盐基等进入冷却水中。为保证煤气的最终冷却温度和减轻脱苯蒸馏设备的腐蚀,终冷循环水需部分更换,而排出一定量的酚氰废水。废水中含酚约150mg/L,氰化物80~150mg/L,COD约1500mg/L,并有少量硫化物。
3)油加工和粗苯精制过程中产生的废水。在焦化产品粗、精制过程中的水蒸气冷凝水和焦化产品沉降分离产物,以及各储槽定期或由事故排出的废水。该类废水主要含芳香烃类、酸、碱、盐等。
(2)捣固式热回收焦炉
捣固式热回收焦炉装煤、推焦、熄焦过程排污环节与水平室式机械化焦炉相同,但该炉型生产过程中焦炉煤气全部燃烧,热回收利用。因此,不存在煤气净化环节,不产生焦化废水,无相应排污环节。
(3)直立焦炉
直立炭化炉生产半焦过程中排污环节与传统机焦炉相同,所不同的是由于该炉型为立式,由焦炉顶部装煤、从底部出焦。煤气净化与机焦炉完全相同。产生污染环境的烟、尘、液、渣及噪声等,废水中含有酚和氰化物等有害物质,废气中主要有害物质有SO2、氮氧化物、苯并[a]芘(BaP)、氰化氢等。
半焦车间废气、粉尘污染源治理措施:一是防止废气、粉尘产生;二是避免废气、粉尘飞扬。煤、焦堆场配有喷洒水系统,减少粉尘排放;堆场周围设挡墙,防止大风扬尘。选用热稳定性较好的块煤入炉,采用皮带通廊、转运站等封闭建筑上煤。煤气管道必须严密,防止泄露。半焦排出采用湿法出焦,防止粉尘外冒。破碎、筛分室设布袋除尘进行机械除尘等。
半焦生产过程中产生的酚氰废水,由于其属高浓度有机废水,常常采用焚烧工艺,即污水经预处理后用焦炉煤气作燃料在焚烧炉内进行焚烧,污水中有机物在高温下变成CO2和H2O,使COD、酚类、CN等从根本上得以治理,产生热废气经余热锅炉换热,产生蒸汽,供熄焦使用。
3.2.2 主要污染物控制措施
(1)焦炉装煤烟气治理
装煤过程产生的烟气量一般在(6~9)×104m3,烟气中的污染物主要有烟尘、SO2和苯并芘。烟气中SO2主要是通过降低入炉煤的硫分进行控制,一般一级冶金焦入炉煤的硫分为≤0.6%,二级冶金焦入炉煤的硫分为≤0.7%。
目前世界上主要的焦炉装煤烟尘控制技术有高压氨水喷射、双集气管及跨越管式消烟、夏尔克(Schalke)装煤烟尘净化、湿式地面站烟尘净化、车载式湿法洗涤烟尘净化、燃烧法干式地面站烟尘净化、非燃烧法干式地面站烟尘净化、车载式干法烟尘净化以及上述各种技术的组合方式等。
表3-17给出了以上几种装煤烟气净化措施的捕集率、净化效率、排放浓度和能耗指标。侧导管和夏尔克属于无烟装煤方案,其余属除尘装煤方案。其中燃烧干式地面站、非燃烧干式地面站、干式车载除尘,捕集率较高、烟尘净化效果好、排放浓度低、耗电少、无废水产生。燃烧干式地面站可以有效去除烟气中的苯并芘等苯系物,但由于增加了燃烧装置,装煤车结构复杂化、车体加重、投资增加,同时操作时有爆鸣等,危险程度大。非燃烧干式地面站,系统较为完善,净化率可达99.5%,应用较普遍。存在的问题:一是需采用布袋预喷涂,延长布袋的使用寿命;二是占地面积较大;三是操作费用较夏尔克装煤车高。湿式地面站和湿式车载除尘车,前者捕集率高、排放浓度低,但电耗和水耗均较高,后者捕集率较差、排放浓度高、电耗低,有一定的水耗;两者设备腐蚀程度均较高,且有潜在的二次水污染问题。侧导管和夏尔克一方面采用高压氨水喷射,将大量烟气抽入集气管,另一方面采用顺序装煤,既保证烟气有一个畅通的气道,同时也缩短装煤时间,这样,在烟气导走的同时,通过缩短装煤时间,加强煤车与炉口的密封,保证烟气无外溢。跨越管、侧导管在我国正在应用推广,夏尔克装煤车由于投资较高在国内尚无运行实例。
表3-17 焦炉装煤烟气治理技术比较

表3-18是国内较普遍采用的几种装煤烟气治理工艺,通过比较可以看出,方案四投资和运行费用较低,但排尘浓度较高,其余方案排尘浓度均可小于50mg/m3。
表3-18 国内现行普遍采用的几种装煤烟气治理方案的技术和经济指标

(2)推焦烟气治理
推焦过程产生的烟气量很大,一般在(1.0~1.4)×105m3。烟气中主要有颗粒物和SO2。表3-19为推焦过程各种净化方案的效果比较。目前应用最多的治理技术主要是推焦湿式地面站除尘系统、推焦干式地面除尘站。
表3-19 国内现行的推焦烟气治理技术比较

(3)煤气脱硫
焦炉的热源为燃烧净化后的焦炉煤气,废气经焦炉烟囱排出。污染物排放情况与焦炉煤气净化效果密切相关。焦炉煤气经冷鼓、电捕焦油、脱硫、洗脱苯、脱氨等工序净化后用于焦炉加热、粗苯管式炉等。
目前焦炉煤气脱硫的方法大致分两种:一种是湿式氧化工艺;另一种是湿式吸收工艺。我国已建成投产的湿式氧化工艺有以氨为碱源TH法、FRC法、HPF法、PDS+栲胶和以碳酸钠为碱源的改良ADA法。已建成的湿式吸收工艺有以单乙醇胺为吸收剂的索尔菲班法(Sulfiban法)和以氨水为吸收剂AS循环洗涤法。
当前国内外焦炉煤气净化技术发展趋势如下。
1)焦炉煤气脱硫脱氰装置设置在终冷和洗苯前,使煤气尽可能地在终冷前除去大部分杂质,以减轻对水质和大气环境的污染。
2)利用煤气中的氨为碱源,脱除煤气中的H2S和HCN,既不需外加化学品,也有利于综合利用。
表3-20对以上6种脱硫工艺从脱硫、脱氰效率、脱硫废液处理、投资、运行成本等方面进行了技术和经济指标的比较,湿式氧化法和湿式吸收法一般都分为以碳酸钠为碱源和以焦炉煤气中的氨为碱源两种,但无论从脱硫装置本身的经济效益来看,还是从解决整个焦炉煤气净化系统设备和管道腐蚀问题来看,调研结果表明,采用以氨为碱源的脱硫方法是焦炉煤气脱硫的最佳选择。
表3-20 各种焦炉煤气脱硫工艺的技术经济指标比较

(4)焦化废水处理
目前水平室式机械化焦炉焦化废水常见的A/O、A/O2、A2/O、A2/O2等处理方法,直立式焦炉采用高浓度酚氰废水焚烧及焚烧+生化处理的方法。焦化废水经A2/O工艺处理后,COD可降至50~250mg/L,氨氮可降至0~25mg/L。图3-12为A2/O污水处理工艺。表3-21为A/O、A/O2处理焦化废水效果的对比。

图3-12 A2/O法酚氰污水处理站工艺流程
表3-21 A/O2和A/O工艺处理焦化废水的结果对比

随着环保要求的不断提高,加之水资源的短缺,要求焦化废水零排放的要求呼声越来越高。“焦化废水零排放”是指将处理后的焦化废水全部回用于厂内,其关键在于处理后的废水在满足达标的前提下,符合回用水的要求。要实现焦化废水的零排放,需根据企业性质,对不同的回用用户采用相应的处理工艺,使处理后焦化废水资源得到最大限度的合理利用。
1)联合钢铁企业,处理后焦化废水除了回用于焦化厂外,还可以用于钢铁企业浊循环水系统中。这样废水处理达到《钢铁工业污染物排放标准》(GB 13456—92)中的一级标准满足要求。
2)煤焦联合企业,处理后焦化废水除了可用于焦化厂外,还可送往洗煤厂,用作洗煤补充水,同样需要达到《污水综合排放标准》(GB 8978—1996)中的一级标准。
3)独立焦化厂,如果采用湿法熄焦工艺,处理后焦化废水应该达到《污水综合排放标准》(GB 8978—1996)中的一级标准;如果不允许外排,必须控制进废水处理站的稀释水量,并以熄焦水量来控制稀释水量。
4)独立焦化厂,如果采用干法熄焦工艺,同时环保部门又不允许外排的,即使不考虑其他水量,仅蒸氨废水一项靠焦化厂本身是消耗不掉的。必须采用深度处理工艺,如砂滤、生物滤池、混凝处理、活性炭过滤、超滤、反渗透、化学氧化等,同时尽量减少废水处理的稀释水用量,使深度处理的产水用于生产净循环水补充水;少量的浓缩液可以喷洒到煤场或作为泡沫除尘的补充水。
5)要求零排放的,仅靠焦化厂本身是消耗不掉处理后的焦化废水,必须采用深度处理工艺,使深度处理的产水用于生产净循环水补充水。
3.2.3 初始权核定方法
分析炼焦行业主要污染物产排污情况和污染控制措施,可以得出以下结论。
①炼焦过程中的二氧化硫主要产生在装煤、炼焦炉和推焦这3个工序,但最终二氧化硫的排放量取决于焦炉煤气的净化程度,污染物排放量与治污设施运行情况直接相关,因此,炼焦企业的二氧化硫初始排污权核定可采用排放绩效法;
②通过对炼焦行业氮氧化物排放现状进行分析得出:氮氧化物吨产品排放量与企业总产能、炉型的关系较小,根据这一特点,氮氧化物初始排污权核定方法可选用排放绩效法。
③根据炼焦生产过程产排污分析结果,焦炭生产过程中排放颗粒物的工序较多,且由于目前无法收集到各工序污染物的排放量,各工序污染物排放量无法与最终产品对应,因此无法准确得出炼焦行业粉尘、烟尘的排放绩效值,炼焦企业的烟尘、工业粉尘初始排污权核定方法选用排放标准法,即按照现有的国家行业污染物排放标准中规定的废气排放标准为依据确定企业初始排污权。
应用排放绩效法进行初始排污权核定的计算公式如下。
Mi=AiGPSi·10
式中 Mi——第i个炼焦企业的二氧化硫、氮氧化物初始排污权核定量,t/a;
Ai——第i个炼焦企业的焦炭生产能力,104t/a;
GPSi——第i个企业的排放绩效值,kg/t(焦)。
应用标准法进行初始排污权核定的计算公式如下。
Mi=BiCi·10-9
式中 Mi——第i个炼焦企业在达标排放情况下的初始排污权核定量,t/a;
Bi——第i个炼焦企业满负荷条件下的废气排放量,m3/t(焦);
Ci——炼焦行业废气执行排放浓度,mg/m3。
Bi=AiBi0/Ai0
式中 Ai——第i个炼焦企业焦炭产能,t/a;
Bi0——第i个炼焦现状废气排放量,m3/t(焦);
Ai0——第i个炼焦企业焦炭产量,t/a。
由于“十二五”期间山西省内要求焦化行业实现废水零排放,因此对炼焦企业不予核定化学需氧量、氨氮初始排污权。
3.2.4 初始权核定示例
以焦化大省山西为例进行焦化行业初始排污权核定案例研究。
3.2.4.1 基本情况
山西省是全国最大的炼焦用煤资源基地,依托丰富的焦煤资源,山西省目前已成为国内乃至全球焦炭产量最大、输出量最多的生产基地。虽然“十一五”期间焦化行业大力实施淘汰落后产能工作,但炼焦产能仍由2005年的1.2×108t增加至1.6×108t,未能实现《“山西省焦化工业十一五”发展规划》中产能控制在1.2×108t的目标。由于全国乃至全球焦炭需求的日益饱和以及经济危机的影响,导致“十一五”期间全省焦化行业整体低迷,焦炭产量并没有随着焦炭产能的增加而大幅增加,仅由2005年的7.981×107t增加至2010年的8.502×107t。但全省焦炭产能素质得到明显提升,单台焦炉产能明显扩大,2010年全省焦化企业焦炉单台产能情况见表3-22。可以看出,全省炼焦炉以捣固型为主,其产能占全省焦炭产能的64%,单炉产能所占比例最大的依次为6.0×105t/座4.0×105t/座以下和(4~6)×105t/座的焦炉,其比例分别为28%、23%和20%。顶装型焦炉产能占全省焦炭产能的26%,清洁热回收型焦炉产能占全省焦炭产能的10%。
表3-22 2010年山西省炼焦行业焦炉单台产能情况

3.2.4.2 排污控制现状
2008年山西省人民政府发布了《关于进一步深化焦化行业清理整顿做好污染减排工作的通知》,其中要求炼焦炉必须全部建设脱硫设施,2010年山西省所有焦炉全部建有脱硫设施。
“十一五”期间全省积极推进焦化废水零排放,并将焦化行业废水零排放写进《山西省环境保护“十二五”规划》中。根据2010年山西省污染源普查更新数据,截至2010年全省63%的焦化企业已实现废水零排放。
3.2.4.3 焦化行业初始排污权核定关键参数
按照3.2.3部分确定的方法,焦化行业初始排污权核定的关键参数包括二氧化硫、氮氧化物排放绩效值和烟尘、工业粉尘等排放标准限值。
(1)现状参数情况
将全省炼焦企业分别按照企业总产能、焦炉单机产能分类,进行二氧化硫、氮氧化物、烟尘、工业粉尘和废气排放量的吨产品排放量分析,结果见表3-23、图3-13、表3-24及图3-14。
表3-23 山西省炼焦企业主要污染物吨产品排放情况按企业总产能分类统计结果


图3-13 山西省炼焦企业主要污染物吨产品排放量按企业总产能(R)分类结果
由图3-13可以看出,二氧化硫、工业粉尘的吨产品排放量与企业总产能有明显的相关性,即随着企业总产能的增加,二氧化硫、工业粉尘的吨产品排放量减小;氮氧化物、烟尘的吨产品排放量与企业总产能的相关性不明显,特别是氮氧化物,其吨产品排放量不随企业总产能发生变化,为0.5kg/t左右。
表3-24 山西省炼焦企业主要污染物吨产品排放情况按焦炉单台产能分类统计结果


图3-14 山西省炼焦企业主要污染物吨产品排放量按炼焦炉型分类结果
由图3-14可以看出,炼焦行业主要污染物吨产品排放量与焦炉类型相关,其中清洁型热回收焦炉的二氧化硫、烟尘排放吨产品排放量较捣固型、顶装型焦炉高,捣固型焦炉的工业粉尘吨产品排放量较其他两类焦炉的值高,3种炉型的氮氧化物吨产品排放量差别不大。
(2)不同控制要求下参数情况的分析
2012年《炼焦化学工业污染物排放标准》(GB 16171—2012)正式颁布实施,对炼焦生产过程各工序的二氧化硫、氮氧化物和颗粒物的排放浓度限值做出新的规定,具体限值见表3-25。依据排放浓度限值计算得出的炼焦企业主要污染物排放绩效值见表3-26。根据全省炼焦企业污染物排放现状分析结果,吨焦废气排放量取0.5×104m3。
表3-25 炼焦企业大气污染物排放浓度限值

①机焦、半机焦;②热回收焦炉。
根据《山西省主要污染物总量控制“十二五”规划》,“十二五”期间要求全省所有炼焦炉实施焦炉煤气精脱硫,H2S的浓度小于50mg/m3,同时颗粒物排放浓度不得大于30mg/m3;要求所有焦化企业实现废水零排放。依据规划要求计算得出的炼焦企业主要污染物排放绩效值见表3-26,其中根据全省炼焦企业污染物排放现状分析结果,吨焦废气排放量取0.5×104m3。《“十二五”主要污染物总量减排核算细则》中对“十二五”期间核算炼焦行业新增产能的单位产品二氧化硫、氮氧化物排放系数做出规定,具体绩效值见表3-26。
按照以上不同污染控制要求计算得出的炼焦企业主要污染物排放绩效值见表3-26。
表3-26 炼焦企业主要污染物排放绩效值计算结果

分析表3-26,可得出以下结论。
1)减排核算细则中规定的二氧化硫绩效值明显大于全省炼焦企业二氧化硫现状平均绩效值,大于全省捣固型、顶装型焦炉二氧化硫现状绩效值。全省各种类型焦炉的二氧化硫现状绩效水平高于炼焦行业排放标准要求。
2)由于目前尚未出台炼焦行业氮氧化物控制要求,炼焦行业氮氧化物排放要求较宽松,排放标准要求折算出的氮氧化物绩效值明显高于全省炼焦企业氮氧化物现状平均绩效水平。减排核算细则规定的炼焦企业氮氧化物绩效值小于全省炼焦企业氮氧化物现状平均绩效水平。
(3)关键参数的确定
根据“从严控制”核定原则,山西省炼焦行业排放绩效值在现状绩效值、排放标准折算值、减排核算细则规定值中选取最小值,作为炼焦行业二氧化硫、氮氧化物初始排污权核定的排放绩效值,结果如表3-27所列。
表3-27 山西省炼焦行业主要污染物初始排污权核定排放绩效值

炼焦行业烟尘和工业粉尘等排放浓度执行《炼焦化学工业污染物排放标准》(GB 16171—2012)中规定浓度限值,具体取值见表3-28。
表3-28 山西省炼焦行业主要污染物初始排污权核定排放浓度值
