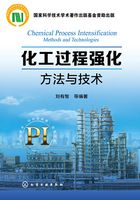
绪论
化学工业是国民经济的重要组成部分,与我们的生产和生活密切相关,医药、农药、化肥、塑料、橡胶、涂料、汽油、柴油、染料、火炸药等都是化学工业的产品。化学工业为国民经济发展作出了重要的贡献,促进了中国经济社会发展。但是,传统化工给人的印象是塔群林立,设备高耸,噪声刺耳,跑冒滴漏形成气味刺鼻、粉尘飘扬、液滴飞溅,造成严重的“三废”污染,其生产过程也造成资源浪费和能源的高消耗。由此带来的问题,对社会经济发展提出了挑战。因此,节能减排、低碳发展上升到重要的战略地位[1]。
低碳经济是指在可持续发展理念指导下,通过技术创新、制度创新、产业转型、新能源开发等多种手段,尽可能地减少煤炭石油等高碳能源消耗,减少温室气体排放,达到经济社会发展与生态环境保护双赢的一种经济发展形态。发展低碳经济是摒弃以往先污染后治理、先低端后高端、先粗放后集约的发展模式的现实途径,是实现经济发展与资源环境保护双赢的必然选择。低碳经济发展基于可持续发展的理念,就是要达到经济社会发展与生态环境保护齐推进,解决好“发展与污染”的矛盾。节能减排就是要节约物质资源和能量资源、减少废弃物和环境有害物排放。不难看出,节能减排是发展低碳经济的重要途径,并在很大程度上依赖于节能减排技术作为基本支撑[2]。
纵观近半个世纪的新技术发展和潜能,过程强化(Process Intensification,PI)技术是实现节能减排的重要手段之一,尤其是在“中国制造”的环境与背景下,催生、孕育和促进了新兴的化工过程强化技术基础的发展和工业示范、工程化技术推广进程,已取得显著的节能减排效果,潜能作用已显现。化工过程强化技术已成为实现化工过程的高效、安全、环境友好、密集生产,推动社会和经济可持续发展的新兴技术。
为此,本章概要介绍化工过程强化的概念、简史、方法及分类,阐述化工过程强化的特征及可持续发展的作用。
0.1 概述
近年来,化工发展的一个明显趋势是安全、清洁、高效的生产,其最终目标是将原材料全部转化为符合要求的最终产品,实现生产过程的零排放,减少对环境的污染。想要达到这一目标,可以从化学和化工两个方面着手。从化学反应本身着手,就是利用化学原理将反应物的原子全部转化为期望的最终产物,在制造和应用化学产品时应有效利用原料,消除废物和避免使用有毒的和危险的试剂和溶剂,通过采用新的催化剂和合成路线从源头上减少和消除工业生产对环境的污染;从化学工程出发,就是采用新的设备和技术,通过强化化工生产过程来实现节能减排、降低资源和能源消耗[3-5]。前者属于绿色化学的内容,侧重从化学反应本身来消除环境污染、充分利用资源、减少能源消耗;后者属于化工过程强化的范畴,强调在生产能力不变的情况下,在生产和加工过程中运用新技术和设备,极大地减小设备体积或者极大地提高设备的生产能力,显著地提升能量效率,大量地减少废物排放[6]。为此,本著作着重介绍化工过程强化方面的内容。
0.1.1 化工过程
何为过程?不同的学科对过程有着不同的解释。从哲学意义上讲,过程一般是指相互关联的一系列活动或变化,是事物的发展,是事情经历的经过,指的是客观事物从一个状态到另一个状态的变化。也可以把“过程”理解为是事物发展所经过的程序、阶段,也是将输入转化为输出的系统。
而对化工生产来讲,从原料开始到生产制造出期望得到的化学产品,要经过众多的化学和物理加工处理步骤,所涉及的每一个化学加工处理步骤、物理加工处理步骤、构成产品生产的一系列加工处理步骤(生产工艺)都称为化工过程,即化工过程也相应地包括化学过程和物理过程及其组成生产工艺过程,简称“过程”,这就是本著作中提及的“化工过程”或“过程”范畴。化学工业种类繁多、所用的加工制造方法各不相同,但如果将其制造过程加以整理,则可得到若干应用较广而为数不多的基本化学反应过程(例如氧化、还原、磺化、硝化、氯化等)和基本物理加工过程(例如吸收、加热、冷却、精馏等)。这些基本化学反应过程和物理加工过程(亦称单元操作)组成了各种化工产品的生产工艺(即生产过程)。因此,本著作中谈及的化工过程简称为“过程”,就是指这些化学反应过程、物理加工过程和化工生产的工艺过程。
0.1.2 化工过程强化
化工过程强化技术是针对现有常用设备与技术相比而言,强调以化工原理和反应工程及相关物系平衡特性为基础,通过采用新设备和新工艺,显著提升传递过程速率或反应过程速率及其选择性,达到大幅度减小设备尺寸或提高产能、降低能耗及废物排放,形成高效节能、清洁、可持续发展的技术。
这里提及的“新设备和新工艺”是核心,是过程强化技术之所在,要靠方法创新、技术创新来实现。“新设备和新工艺”还说明了化工过程强化涉及两个方面的基本内容,即过程强化设备和过程强化(工艺)方法。
“显著提升过程速率”就是要成数倍乃至数十倍甚至更高比例地提升,是大幅度的提升或变化,这种“强化”本质上是创新性的、革命性的,而非渐进性的,带来的变化是巨大的。这是过程强化技术区别于一般技术改造或技术革新在原来的基础上挤出百分之几的根本所在。
Stankiewicz对过程强化给予了这样的描述,过程强化包括新型装备和技术,这些装备和技术与当今常用的装备和技术相比,可以显著地改进制造和加工过程,大幅度地提高设备产能,降低能耗或废物的产生,最终形成更廉价、更可持续发展的技术[7]。
由此看出,化工过程强化产生的效果是大幅度减小生产设备尺寸,简化工艺流程,减少装置数量,使工厂布局更加紧凑合理,单位能耗、废料、副产品显著减少[8,9]。实际上,化工过程强化带来的益处是多方面的。设备生产能力的显著提高,导致单位产品成本大幅降低。设备体积的微型化,将带来设备和基建投资及土地资源的节省。由于能充分利用能量、生产效率高,能耗将显著降低。大幅度减少化学物质的在线存量,提升安全等级。由于反应迅速、均匀,副反应少,从而大大减少了副产物的生成,污染环境的废物排放也会显著减少[10]。
在已研究和发展的20多种化工过程强化技术中,如整体催化技术、超重力强化技术和过程耦合强化技术等,因具有明显的平台技术特征和很好的工业应用前景,而备受化学和化工界的重视。化工过程强化是高效、安全、环境友好、密集生产,推动社会和经济可持续发展的新兴技术,将从整体上提升我国化学工业的绿色生产技术水平,被认为是解决化学工业“高能耗、高污染和高物耗”问题的有效技术手段,可望从根本上变革化学工业的面貌。
0.2 化工过程强化的发展及历史
单从“过程强化”这个短语来说,涉及的不但是过程工业范畴,而且还涉及非工业的过程领域,本书着重于过程工业尤其是化工过程来讨论“过程强化”。通俗地讲,化工生产的发展,充满了许许多多化工工艺及装备技术的进步。比如为了从食盐水中得到固体食盐,从最初靠阳光自然蒸发到人工强制加热,就是加快蒸发水分的过程速率;对气体中有害物质的吸收,从鼓泡吸收到填料塔吸收,也是提高吸收过程的速率和吸收效率[11];催化剂的开发,使得反应速率极慢的化学反应速率提高或使得通常不可能发生反应的化学反应变为可能;类似的例子很多,正是这样许许多多的例子,构成了现代的化工工艺及装备技术。在这里讲到的化工过程强化,不仅仅局限于此,正像前面介绍化工过程强化的概念一样,化工过程强化在这里赋予了可持续发展、效率倍增等本质内容。
将旋转用于分离和化学反应已有近百年的历史,但是,这个方面的研究在1979~1983年期间得到了新的发展。在此期间,英国帝国化学工业公司(Imperial Chemical Industries,ICI)新科学小组的Colin Ramshaw教授等先后提出了在旋转填料床(Rotating Packed Bed,RPB;可产生离心加速度达200g~1000g)内进行化工分离操作,名为“Higee”的一系列技术专利。1983年Colin Ramshaw教授发表的论文中报道了工业规模的超重机(旋转填料外径800mm,内径300mm,厚度300mm)平行于传统板式塔进行乙醇与异丙醇和苯与环己烷分离,成功运转数千小时的情况,肯定了这一新技术的工程与工艺可行性[12,13]。它的传质单元高度仅为1~3cm,较传统填料塔的1~2m下降了两个数量级,它极大地降低了投资和能耗,显示出十分重大的经济价值和广阔的应用前景。因此,谈及过程强化,则以1983年Colin Ramshaw教授发表的论文为标志。几个月后,有关过程强化学术会议在曼彻斯特理工大学(University of Manchester Institute of Science and Technology,UMIST)召开。可以说最早的过程强化定义(或者说是一种描述)出现在上述Ramshaw的论文和UMIST会议的报告中。Ramshaw认为过程强化就是“设计极其紧凑的化工厂,降低主要设备和安装费用”。
在20世纪70年代到80年代初,ICI的过程强化思想是基于Colin Ramshaw和他的研究小组成员在取得数个技术发展基础上形成的,包括“Higee”旋转填料床气液接触器、印刷电路热交换器、Rotex吸收热泵、聚合物膜紧凑热交换器等技术的发展。直到20世纪90年代初期,过程强化仍然只是一个限于英国的学科,主要涉及四个领域:离心场的应用、紧凑高效换热、强化混合和组合技术。
然而当时这个具有十分重大的经济价值和广阔的应用前景的化工过程强化技术已成为一个国际热点,许多国家的研究机构已经涉足该领域。1983年汪家鼎院士在国内化学工程会议上介绍了ICI所开发的超重力新技术的情况。北京化工大学郑冲教授于1988年与美国Case Western Reserve大学合作,开始进行旋转填料床的应用。得到原化工部和国家科委的高度重视和大力支持,经论证,被列为国家1989年度和“八五”重点科技攻关项目,也得到了中国自然科学基金委对这项高新技术的基础研究的支持。
需要指出的是,1983年ICI公司作出判断,认为超重力技术不可能建造更大规模的连续工艺系统,因此ICI公司放弃了对超重力技术的进一步研究。这个技术转让给了美国专门从事填料塔吸收系统制造设计的Glitsch公司。很快Glitsch公司启动了数个工程项目,包括天然气除臭、地下水净化修复等,而且证明了超重力装置在机械上的可靠性和达到设计要求。到1990年,Glitsch公司也从该市场领域退出;很久以后,美国陶氏公司开创了超重力用于次氯酸制造的应用,示范装置成功运行,随后有几台超重力装置安装使用,达到了设计规范和要求。
英国于1995年1月在伦敦举办了第一届国际过程强化会议,会议上Ramshaw再次提出:化工过程强化是指在生产能力不变的情况下,能够显著减小化工厂体积的措施。
各国的专家和学者也组织了过程强化网,积极开展学术交流和科技合作。其中,以Colin Ramshaw为首席,于1999年1月1日在英国纽卡斯尔成立了过程强化网(Process Intensification Network,PIN),吸引了众多的工业界和学术界的参与者,并于当年4月份举行了首届PIN学术会议,有64位成员参加[14]。此后该学术交流会议每年举办1~2次,到2016年6月21日,在英国纽卡斯尔大学召开了第24届PIN会议。荷兰也建立了类似的网络。
2000年以来,国内学者对化工过程强化认识达到了前所未有的高度,发表了大量化工过程强化的论文,举办了多种形式的学术交流会议、产学研合作会议等,政府和企业也给予了高度的关注和支持,有力地推进了化工过程强化技术的研究和应用进展。
2006年,为促进我国化学工业向能源资源节约型和环境友好型生产模式转变,国家科技部将化工反应过程强化技术项目列入“十一五”国家“863”计划,开发对化学反应过程有显著强化效果的关键共性技术。
2009年11月首届“精细化工过程强化技术交流大会”在南京成功召开,成立了全国化工过程强化技术指导委员会,此后,“化工过程强化技术交流大会”陆续举行。2010年9月,第二届全国精细化工过程强化技术交流大会在杭州召开。2011年11月,第三届全国精细化工过程强化技术交流大会在青岛召开。2014年11月,第四届全国化工过程强化技术交流大会在青岛召开。会上专家作报告,众多化工企业参加,会下企业与专家面对面,交流化工过程强化技术,结合生产实际和需求,解决问题,在推动了化工过程强化技术在企业落地开花的同时,企业也提出了新要求,进一步促进了化工过程强化技术的发展。
2011年6月,“面向可持续发展化学工业的过程强化技术国际会议”(International Conference on Process Intensification for Sustainable Chemical Industries)在北京国家会议中心召开。会议由中国化工学会主办,北京化工大学承办,得到了国家自然科学基金的资助。会议顺应了当代国际化工科技发展潮流,促进了国内外的学术交流和科研合作,对推动我国在化工过程强化与绿色过程领域的技术进步,实现化工行业的节能减排具有重要作用。
2013年9月,2013北化国际系列论坛——“化工过程强化与绿色技术国际研讨会”(International Symposium on Chemical Process Intensification and Green Technology)主要讨论了化工过程强化、化工过程强化(流体混合专场)、材料化学工程、绿色化工技术四个主题,旨在加强国际间合作。
2015年中国化工学会年会就以“创新驱动,绿色发展”为主题,揭示了化工产业可持续发展的方向和实现路径,体现了化工行业转型发展的新理念、新方向,是学术、科技、产业界的共同盛会。
中国化工企业管理协会于2016年3月在杭州市举办“2016绿色化工暨化工工艺技术创新研讨会”。为紧随科学技术的脚步,传统的化工行业需要通过技术创新来推动化工行业发展,全方位推进节能减排,强化化工行业绿色制造,加快工艺技术升级。
2000年以来,化工过程强化技术得到国家自然科学基金持续多个方面的资助。
近些年来,我国“制造大国”总体环境,对化工清洁生产、环境友好、可持续发展提出了新要求,为化工过程强化技术的发展提供了发展的空间和市场,化工过程强化技术受到人们更多的关注,化工过程强化技术与绿色化工紧密结合、与节能减排相关联,必将达到可持续发展的要求。
0.3 化工过程强化的原理及方法
0.3.1 化工过程强化的思路及基本原理
过程速率是指物理或化学变化过程在单位时间内的变化率。一般用单位时间过程进行的变化量表示过程的速率。如传热过程速率用单位时间传递过的热量,或用单位时间单位面积传递过的热量表示;传质过程速率用单位时间单位面积传递过的质量表示。
单纯从生产的产品数量看,在现有技术条件下,可以通过扩大规模或延长生产时间来实现,显然这个不是我们在这里要讨论的问题。众所周知,过程进行的速率决定设备的生产能力,过程速率越大,意味着单位时间设备生产能力也越大,或在同样产量时所需的设备尺寸越小。需要特别指出的是,往往过程速率的提高还不仅仅是一个简单的生产能力问题,过程速率的提高往往涉及化学反应的有效调控,会产生在通常条件下难以实现目标产物的高产率、低副产物的情况,甚至获得意想不到的化学反应结果,达到理想的期盼。如采用撞击流-旋转填料床(Impinging Stream-Rotating Packed Bed,IS-RPB)作为反应器,氯化镁与氢氧化钠反应生成氢氧化镁结晶,沉降速率加大提高。因此,过程速率的提高,意味着在完成同样任务的条件下,运行时间缩短,目标产物的转化率提高(成品率提高,副产物和污染物的排量减少)、设备的体积缩小(占地面积较小,安装空间节省,投资减小,运行费用降低)、生产在线的化学物料量减少(对化工易燃易爆的特点,意味着提高了生产安全性)。
由此可见,化工过程强化实质上就是要提升过程速率,而且要大幅度提升这个速率。这个就是解决问题的出发点和落脚点,是解决问题的根本所在,这就是化工过程强化的思路。
化工过程强化的基本原理就是综合运用物系内部和物系(多相流)之间的传递原理和反应原理及相关平衡特性,通过新设备和新工艺,提高过程速率。
传递现象是自然界和化工生产中普遍存在的现象,只要物系内部或物系之间存在速度、温度、浓度梯度,即可发生动量、热量、质量传递,直到平衡为止。由此看来,不平衡的存在是传递的前提条件,平衡特性是化工过程强化必须考虑的关键因素。以化工过程强化来提升过程速率,实际上是加快达到这样的平衡。因此,尽管在工程方面,考虑过程的速率问题往往比物系的平衡问题重要,但平衡问题在一定程度上显得更重要。改变平衡特性也是过程强化的内容,超临界流体和离子液体等就是典型的例子。
实际上,化工过程主要涉及多相流之间发生的化学反应和传递过程,包括动量传递、热量传递和质量传递以及相互间的作用,即“三传一反”。研究化工过程速率问题,就是研究化学反应速率和传递速率,化学反应速率往往受到传递速率的影响。
化工过程涉及的“三传”问题,可以用“现象方程”加以描述,这个在化工传递学中已经描述得很清楚。传递速率等于传递的动力与传递的阻力之比,即符合现象方程:
通量=-扩散系数×浓度梯度
这里浓度梯度是传递的动力,扩散系数的倒数即为传递的阻力,可以将现象方程写成:
这里的推动力和阻力不一定是物体之间的相互作用,而是广义的力,其推动力应该理解为促使过程加快进行的外界作用,而阻力应该理解为影响过程进行的外界作用。
对于不同过程的研究,总是以提高过程的速率为目的。要提高传递速率的方法,不外乎要么加大传递的动力、要么减小传递的阻力,或同时加大传递动力和减小传递阻力。加大传递的动力是必然要增加能耗,一般不予采取;在推动力一定的条件下,过程的速率提高又必须以削弱过程的阻力为前提。减小传递阻力表现在改变和控制多相流的流动形态、尺度、流动形式和接触方式,加大多相流的相际面积等。
化学反应不仅受到反应动力学的限制,往往动量传递(流体力学及混合)、传热和传质过程决定着整个反应过程。如果利用化工过程强化技术能有效消除“三传”的限制,或者将传递过程速率提高到远比反应动力学速率快得多的程度,这将使得反应过程强化接近或达到化学反应动力学极限,这时化学动力学完全可以控制反应过程目标。从化学角度看,化工过程强化给了每个分子相同的过程经历。
这里的推动力和阻力不一定是物体之间的相互作用,而是广义的力,其推动力应该理解为促使过程加快进行的外界作用,而阻力应该理解为阻碍过程进行的外界作用,这个影响还与物质本身的某种特性——物性参数有关,即物质的物性参数影响过程进行的快慢。
0.3.2 化工过程强化的方法及分类
如前所述,化工过程强化主要是基于新设备和新工艺两个方面,即化工过程强化技术包括过程强化设备(硬件)和过程强化方法(软件)两个方面。需要指出的是,在一些情况下,两个方面是相互联系、相互渗透和交叉的,在创新的过程中,往往研究新的强化方法通常需要开发新设备,反之亦然。
设备强化的方法与分类,可以依据是否涉及化学反应分为反应器和单元操作设备;也可以依据设备从事的具体化工操作进一步分类,如混合器、萃取器、吸收装置、蒸发设备;也可以依据外场作用(离心场、超声波、微波、电场等)分类,如超重力反应器、超重力精馏装置、超声波设备、微波反应器等;也可以依据流体的流动状态进行分类,如静态混合器、静态反应器、动态混合器、撞击流混合器等;也可以依据设备的体积分类,如微混合器、微(化工)反应器等[7]。
工艺方法强化方法与分类,可以依据反应与分离耦合方法分类,如膜反应器、反应精馏、反应萃取等;也可以依据分离方法耦合进行分类,如膜蒸馏、吸附蒸馏、膜萃取等;也可以依据外场作用(离心场、超声波、微波、电场等)分类,如超重力技术、超声波技术、等离子技术等;也可以依据流体状态分类,如超临界流体技术、离子液体等[3,15-18]。
过程强化技术的分类见图0-1所示,具体细节在后续的相关章节进行详细讨论。

图0-1 化工过程强化方法及分类
0.4 化工过程强化技术特征
化工过程强化的技术特征,可以简要概括为平台技术、效率倍增、可持续发展的特征。
0.4.1 平台技术特征
化工过程强化技术是方法创新,不是基于某一个问题而提出的,也不是简单的就事论事。化工过程强化是一个方法创新和技术创新的结合,这本身就决定了化工过程强化技术具有平台技术特点。例如超重力化工技术、超声波化工技术、微化工技术等均可以广泛应用于诸多的化工单元操作和化学反应。因此,化工过程强化技术打造的是一个个平台技术,基于这样的一个平台,可以派生不同的专项技术。从现在的情况看,这些平台技术在逐渐趋于成熟,得到广泛的工程应用与推广,大量的专利授权、专著出版,逐渐在形成真正的“平台”,“平台技术”效应正在发挥作用。因此,化工过程强化技术平台技术的特征更加突显。
0.4.2 效率倍增特征
化工过程强化技术不是在原有技术基础上的改进,挤出百分之几的效率,而是成数倍或数十倍地提高,是一场革命性的变化。化工过程强化技术的“强化”本质上是创新性的、革命性的,而非渐进性的,带来的变化是巨大的,这就是化工过程强化技术的最重要的特征。如静态混合器的发明和引入,打破了搅拌槽技术在流体混合方面的主导地位,就是现代过程强化最好的例子。我们要特别关注的是,静态混合器带来的技术突破不是对传统搅拌本身的改善,而是方法创新开辟新途径,从根本上摒弃了机械搅拌这一流体混合的方法!
0.4.3 可持续发展特征
化工过程强化技术节能减排的效果,符合绿色发展的思路,其可持续发展特征可以简要概括为更紧凑、更经济、更环保、更节能、更安全。
(1)更紧凑
设备体积大幅度减小,安装空间和占地面积节省,设备与生产线布置更紧凑,单元操作的集成化,管网和土建工程减少。
(2)更经济
指的是设备尺寸减小、流程紧凑而带来的设备造价降低、管网和土建工程量减少而减小投资、节省土地、成本降低、运行和能耗费用降低等。还需要说明的是设备尺寸缩小数十倍,意味着原先贵重金属或价格昂贵材料制作的设备造价将大幅度降低,以往投资偏大的设备现在成了常规价格,甚至比常规设备的价格还低。从这个意义上讲,化工过程强化带来的是原来的“不可能”成为了可能。设备的生产效率提高,设备台数减少,运行费用削减。
(3)更环保
设备显著减小带来设备制造所用钢材量节省,本身含有间接低碳效应;强化技术的高效率,副产物少,减排效果显著。
(4)更节能
设备效率提高,能量得到充分利用;设备体积缩小,特别是高度降低,减少了用于液体的输送能量。
(5)更安全
设备大幅度减小,使得过程得到很好的控制,同时生产过程的在线物料存量陡然缩小,反应器内物料滞留量非常小,即便发生爆炸,泄漏量也是微不足道的,想必也不会造成严重后果,本质安全能力显著提升。反应热效应实时快速控制,副反应受到抑制,使危险化学品的生产也能做到生产线的本质安全。
0.5 化工过程强化技术是可持续发展的新兴技术
可持续发展实际上就是对资源的持续循环利用,强调环境与经济的和谐。从化工可持续发展的角度看,我们应该着重从以下三个方面来认识和审视问题。
在分子和化学合成层面,应更多地考虑绿色化学的研究。即研究化学反应本身的绿色化途径,在原子经济性和可持续发展的基础上研究合成化学和催化的基础问题,侧重从化学反应本身来消除环境污染、充分利用资源,通过采用绿色合成和绿色催化、选择合适的原料和合成路线,从源头上制止污染物的生成。
在化工操作和流程方面,应更多地从过程强化的角度思考问题。即研究开发节能降耗的高效率的新装备和工艺技术,通过强化化工生产过程更有效地解决生产过程的高效、安全、清洁、环境友好等问题。
在更大区域(如工厂、园区、地域、国家和全球),应更多从循环经济和生态化工的角度去认识和解决问题。从循环经济角度看,在经济发展中,实现废物减量化、资源化和无害化,使经济系统和自然生态系统的物质和谐循环,维护自然生态平衡,是以资源的高效利用和循环利用为核心,以“减量化、再利用、资源化”为原则,符合可持续发展理念的经济增长模式。从生态化工的角度看,要做到资源利用、加工和产品的生态化。即产品源于那些可以再生的资源,甚至源于废弃物资源;生产工艺是环境友好的,低污染甚至是无污染;产品本身及在使用过程中不会产生生态污染。
我国化学工业迫切需要以循环经济模式为指导,以生态化工要求为目标,向资源节约型和环境友好型发展模式转变,而针对复杂化工体系利用过程强化技术来推动和促进这一转变过程则是化学工业的必由之路。通过过程强化技术开发新型、高效的生产工艺,或对传统工艺进行改造和升级,使过程的能耗、物耗和废物排放大幅度减少,必将从根本上变革化学工业的面貌。
过程强化是国内外化工界长期奋斗的目标,也是化学科学和工程研究的主要成果之一。化工过程强化的可持续发展的特征,已经表明了化工过程强化目前已成为实现化工过程的高效、安全、环境友好、密集生产,推动社会和经济可持续发展的新兴技术。
0.6 化工过程强化技术展望与愿景
在高度追求生产规模化和提升产能的年代,什么样的设备和技术是先进的?往往是看设备的大小和产能,设备大代表着规模水平,似乎也代表着先进技术,这就是在规模化生产前提下的评价原则和发展理念;因为在初始发展阶段,物质产品需求是第一追求,由此而产生的资源和能源的高消耗、环境污染等都不是主要问题。在那个物质缺乏的年代,就是一门心思去追求大规模,更是无暇顾及技术创新,不愿采用新技术而冒险,生怕耽误了生产和影响规模化发展。这种粗放型的经济发展方式是以高投入、高消耗、高污染、高排放为前提,换来的却是较低的经济效益。随着我国快速的工业化进程,化工行业面临可持续发展的压力和挑战更加突出。
不过,化工过程强化技术的出现正在改变这种情况。化工过程强化目前已成为实现化工过程的高效、安全、环境友好、密集生产,推动社会和经济可持续发展的新兴技术。
随着社会的发展,人们更看重的是生产装置的高效率,从以往的“我的设备最大”向“我的设备最有效”转变,比的是更有效、更节能、更环保。就像电子管与晶体管做比较一样,是以晶体管的体积小、低能耗、更有效、更稳定而得到发展。化工过程强化本质就是正在从“电子管”式的化工装置,走向“晶体管”式的化工装置的过程,大量的“晶体管式化工装置”正在兴起,如微反应器、超重力化工装置等,由此建立的化工工艺及生产线也正在悄然走入化工生产的序列,在支持着化工的可持续发展。
如果提到化工厂,人们一般想到的是宽敞的厂房,高高的烟囱。然而在不久的将来,这样的情景在某些地方将变成历史。化工过程强化带来的装置设备小型化、高效率,使得化工生产设备更紧凑、流程简化,设备体积缩小数十倍,高大耸立的装备变得小型化和微型化;人们由此而设想,一种微型化的化工厂将取代庞大、复杂的传统化工厂。期盼着化工生产线也能进入到“蔬菜大棚式”的厂房内,实现花园式工厂,憧憬着共同的期盼——美丽化工。
化工过程强化带来的是投资小,易建设。“晶体管式的化工装置”有各种规格,可以非常方便地被运往目的地。它们也可以按照计划好的模式组装成工艺生产线,从而完成一系列化工产品的生产。对于这些装置的控制也可以实现全自动化,或者通过控制中心进行无线遥控。更有甚者,微反应系统的模块结构可真正实现工厂的便携化,实现因地制宜的“建厂开工”,并且可通过增加通道数或更换模块来调节生产,实现弹性操作。这样,有望实现哪里需要使用化学品,就在哪里建厂的诉求。这不仅很好地解决了危险物料的运输问题,而且使分散的资源得到了有效利用,还能大大减少人员开支和经营费用,所生产的化工产品也可以直接运到顾客群附近。另外,化学品长途运输量将会减少,危化品的运输安全得到彻底改善。
化工过程强化装置设备小型化、高效率,使得化工生产中的在线物料量极大减少,即使危险化学品的生产也能做到生产线的本质安全,这点是多年从事危化品生产人员的共同期盼。
参考文献
[1] 孙宏伟,陈建峰.我国化工过程强化技术理论与应用研究进展[J].化工进展, 2011, 30(1): 1-15.
[2] 费维扬.发展低碳经济、推动节能减排.中国化工学会2009年年会暨第三届全国石油和化工行业节能节水减排技术论坛会议论文集(下)[C].广州: 中国化工学会, 2009: 1.
[3] 张永强, 闵恩泽, 杨克勇 等.化工过程强化对未来化学工业的影响[J].石油炼制与化工, 2001, 32(6): 1-6.
[4] 费维扬.化工过程强化呈现新特点[N].中国化工报, 2002-05-23A04.
[5] 褚秀玲,仇汝臣.化工过程强化的理论与实践初探[J].化工生产与技术, 2010, 17(1): 9-14,7.
[6] 张明国.面向节能减排的化工过程强化技术研究.第三届全国科技哲学专家专题论坛“在为国服务中发展自然辩证法”学术研讨会论文集[C].北京: 中国自然辩证法研究会, 2010: 3.
[7] Stankiewicz A J, Moulijn J A.Process intensification: transforming chemical engineering[J].Chem Eng Prog,2000, (2): 22-34.
[8] 方向晨, 黎元生, 刘全杰.化工过程强化技术是节能降耗的有效手段[J].当代化工, 2008, 37(1): 1-4,34.
[9] 李昕桐, 赵壮, 华恩乐.我国化工过程强化技术理论与应用研究进展[J].化工设计通讯, 2016, 42(1): 46.
[10] 路勇.化工过程强化与微反应技术——构筑高效、节能、清洁的未来化工厂的新技术[J].世界科学, 2006, (3): 20-21.
[11] 费维扬.国外化工塔器的若干最新进展[J].化工进展, 1996, (6): 40-44.
[12] 陈建峰, 邹海魁, 初广文 等.超重力技术及其工业化应用[J].硫磷设计与粉体工程, 2012, (1): 6-10,5.
[13] Ramshaw C.Higee distillation—An example of process intensification[J].Chemical Engineer, 1983, 389(2): 13-14.
[14] Ramshaw C.Process intensification by miniature mass transfer[J].Process Engineering, 1983, 64(1): 29.
[15] 李敬生, 沈琴, 昌庆 等.超声波对化工过程的强化作用[J].西安建筑科技大学学报(自然科学版), 2007, 39(4): 563-568.
[16] 秦炜, 原永辉, 戴猷元.超声场对化工分离过程的强化[J].化工进展, 1995, (1): 1-5.
[17] 闵恩泽, 孟祥堃, 温朗友.新催化材料和化工过程强化——非晶态合金/磁稳定床反应器和负载型杂多酸/悬浮床催化蒸馏[J].石油炼制与化工, 2001, 32(9): 1-6.
[18] 费维扬, 王德华, 尹晔东.化工分离技术的若干新进展[J].化学工程, 2002, 30(1): 63-66,5.