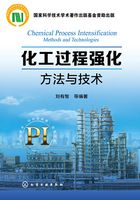
第3章 气-固过程超重力化工强化技术
气固过程是一个重要的化工单元操作,在一切伴有气固两相的生产过程中,它是不可缺少的一个环节,在化工、石油、煤炭、冶金、电力、化肥、水泥、纺织、食品、轻工等工业及环境保护工程中有着广泛的应用。大体可归纳为三类。
①获得洁净的气体。如煤气化过程中煤气的除尘,硫酸生产中硫铁矿焙烧制备的原料气脱除砷、硒等微粒,保证后序压缩、分离或反应工序能够顺利进行。在天然气进入合成氨厂的大型离心压缩机之前必须除净其中所含的微细粉尘,以保证压缩机的安全稳定运转。炼油厂催化裂化再生烟气的能量回收,需将高温烟气中大于10μm的颗粒除净,才能保证高温烟气轮机的长周期安全运行。
②净化废气保护环境。各国对于燃煤锅炉、炼钢炉、有色金属冶炼炉、矿烧结机、水泥窑以及炭黑生产、石灰锻炼、颜料、复合磷肥等生产中的尾气排放要求都有明确的规定,尤其是近年来大气污染越来越严重,对排放上限要求越来越严格,对大部分锅炉烟气实行超低排放。
③回收有用的物料。如各种流化床反应器内将催化剂回收返回床层;如在化肥、农药、颜料、洗涤剂及各种聚合物等的气流干燥过程中收集粉料产品,在有色金属冶炼过程中回收贵重的金属粉末等。
面对环保压力,国家相继出台或修订并通过了《中华人民共和国大气污染防治法》《大气污染防治行动计划》《烟气超低排放标准》等系列法律法规政策,如国家环保总局提出了超细粉尘达到超低排放的新要求(如排放烟气中的尘含量低于5mg/m3),工业过程节能降耗、污染物排放上限进一步降低,急切需要新的技术及其装备来强化气固过程,实现气固高效分离、过程节能降耗。因此,本章将从气-固过程强化技术着手,重点介绍超重力多相分离和离心流态化技术。
3.1 超重力多相分离
3.1.1 多相分离概述
气固分离可分为干法和湿法两大类。干法是利用气体与固体之间物理性质的差异(如密度、荷电性、表面性质等),依靠重力、惯性力、热聚力、扩散附着力、静电力等外力作用达到分离目的。干法分离设备主要有除尘器、惯性除尘器、旋风除尘器、过滤式除尘器、静电除尘器等[1-4]。湿法是利用液体对固体的浸润、包裹、湿润、聚集等性质,依靠分离设备对多相流之间产生的剪切作用而达到分离目的,涉及气、液、固三相,因而又称为多相分离。湿法分离设备主要有板式洗涤器、纤维填充洗涤器、喷雾式洗涤器、旋转式洗涤器、冲击式洗涤器、文丘里洗涤器和空塔喷淋等[5-7]。目前国内外工业上常用的除尘器类型与性能比较见表3-1。
表3-1 常用除尘器的类型与性能比较

从表3-1中看出,对细小颗粒物脱除效率较高的有袋式除尘器、静电除尘器和高能文丘里除尘器。但袋式除尘器具有滤料易损坏、清灰时效率下降明显、占地面积大等缺点;电除尘器除尘效率高,但基建费较高,占地面积大,且其对0.1~2μm的细颗粒物脱除效率很低,容易产生二次飞灰,不能有效地控制细颗粒物的排放浓度;文丘里除尘器可以脱除粒径大于0.5μm的颗粒物,但其压降过高,甚至达到5000Pa以上,想要脱除亚微米级颗粒物则压降更大(大于10000Pa),阻力损失严重。综合来看,目前国内外还没有适宜的高精度净化气体除尘技术,随着国家对大气环境保护要求越来越严格,深度净化细颗粒的技术研发迫在眉睫。因而,研发一种低成本、低能耗、高效率的细小颗粒物净化技术成为当务之急。
超重力多相分离技术正符合这一需求,即低成本、低投入、高效率地深度脱除工业气体中的细颗粒物。
3.1.2 超重力多相分离原理与特点
超重力场下,气-固分离过程是在气-液接触型超重力装置中,将气体中的固体(尘或尘粒)快速转移到液相中,即超重力多相分离过程是将水膜浸润与捕获、离心沉降、过滤、机械旋转碰撞和惯性碰撞、扩散等多种除尘机制集于一体的复合除尘,最终利用密度差异而达到分离的目的[8]。
浸润与捕获机制:在超重力场作用,液体被旋转的填料剪切分割成极薄的液膜、细小的液滴和液丝,并在填料层内多次快速地凝并与分散,使得气-液-固接触面积和表面更新速率得到极大提高,强化液体对粉尘的浸润和捕获,对气体中的微细粉尘形成了极强的捕获能力。
离心沉降机制:当含尘气体通过超重力转子时,被高速旋转的填料层加速,随填料层一起旋转,其中较大颗粒粉尘或是被液体润湿聚并的粉尘在离心力作用下实现离心沉降分离。
碰撞机制:当含有较大粒度粉尘的气体在运动时遇到液滴和填料时,尘粒自身的惯性会使它们不能沿流线绕过液滴或填料,而碰撞到液滴或填料表面而被液滴或填料捕集,即粉尘与液体、填料间都形成了快速的碰撞接触,粉尘的惯性沉降能力增强,进而强化气-固分离过程。
过滤机制:当含尘气体通过转子时,填料层中弯曲狭窄复杂的孔道、液滴、液膜对粉尘形成良好的过滤而实现气固分离。
布朗扩散机制:含尘气体经过转子时,其中较小粒度粉尘在气流夹带的作用下围绕液滴、液丝和润湿的填料运动过程受到布朗扩散作用导致尘粒沉积在液滴、液膜上而被分离。因旋转填料极大地提高了相界面积,从而可以强化布朗扩散作用。
超重力多相分离技术正是耦合了上述多种除尘机制作用,使得其具有切割粒径小、净化效率和除尘精度高、液气比小、压降低、能耗低等优点。因而,人们利用超重力技术进行了除尘净化研究。
张海峰[9]对超重力旋转填料床的除尘效果进行了实验考察,结果表明,旋转填料床的除尘效率随着液量和转速的增大而增大,在最佳参数下,旋转床对灰尘的捕集效率达到99%以上,能够完全除去3μm以上的颗粒。张艳辉[10]等采用逆流旋转填料床,利用燃煤飞灰模拟含尘气体,进行了超重力湿法除尘研究,结果表明,除尘效率可达99.9%以上,出口含尘浓度一般小于50mg/m3,设备压降约在600~1250Pa之间。同时考察了转速、液气比对除尘效率的影响,发现除尘效率随着转速、液气比的增大而提高,且液气比仅为0.21L/m3。柳巍[11]分别采用了并流、逆流旋转填料床处理燃煤飞灰,考察了液量和转速对出口粉尘浓度的影响。结果表明,并流旋转填料床的总除尘效率高于逆流旋转填料床,而旋转填料床在最佳条件下对1μm以下粉尘的脱除效率仍达99%以上。进口气体粉尘浓度对总的除尘效率影响不大,但进口气体所含粉尘的粒径分布会影响除尘的分级效率。宋云华[12]等采用燃煤飞灰模拟的粉尘平均粒径为2.55μm进行脱除实验,结果表明,旋转填料床切割粒径达到0.02~0.3μm,与袋式除尘器的切割粒径相当,出口气体的含尘浓度小于100mg/m3,除尘率高于99%,且旋转填料床的压降小于3000Pa。黄德斌[13]对多级雾化旋转填料床进行了改进,考察转速、液量、轴向的平面丝网层数对除尘效率的影响,结果表明,3层平面丝网的效率远高于1层平面丝网。
通过大量研究和工程应用结果表明,超重力多相分离技术具有如下特点:
①切割粒径小、净化效率和除尘精度高。因超重力多相分离过程耦合了多种除尘机制,对微细粉尘具备协同作用,切割粒径达到0.02~0.3μm。
②液气比小。由于旋转的填料对液体具有高度分散、聚并作用,使得相界面积和界面更新速率得到极大的提高。
③有效防止填料结垢、堵塞。由于在超重力场下,液体随填料层高速旋转而对填料具有良好的冲涮和清洗作用,即液体对填料层内捕集到的粉尘具有极强的“携带”和“清洗”作用,使得粉尘、泥等污染物不易在填料上结垢或结疤等。
④气相压降减小,能耗低。因超重力装置中的填料层高度仅为0.2~0.3m,即气体通过填料层的路径短,其气相阻力极小,一般对原有管路和风机影响不大,可以不另增设风机。
⑤设备体积小、开停车时间短,易于安装、操作、检修。超重力强化气液固的传递作用显著,传递速率一般是塔设备的1~3个数量级,因而超重力装置体积大幅度缩小。
⑥适用范围广泛,操作弹性大。气体负荷可在20%~150%范围内波动,气体流量波动对净化效率影响较小;既适合于新建厂,也适合于老厂改造;可用于原料气深度净化,也可用于排放尾气的深度净化和超低排放要求。
总的来讲,超重力多相分离技术具有气体净化度高、操作弹性大、能耗低、设备体积小、易于安装和维护、适用范围宽等优势。
3.1.3 超重力多相分离性能研究
细颗粒物是指空气动力学直径小于2.5μm的粉尘,又称PM2.5,具有极大的比表面积,能够吸附各种重金属、多环芳烃等有毒、有害物质,并沉积在人体肺部,导致心脑血管疾病和肺癌,严重危害人体健康。同时,细颗粒物还是降低大气能见度,导致“雾霾”现象的罪魁祸首,给交通带来了很大的影响。细颗粒物的来源主要是人为排放:各种燃料燃烧,如发电、冶金、石油、化学、纺织印染等工业过程、供热过程中燃煤与燃气或燃油排放的烟尘和机动车尾气等。相对于石油和天然气等清洁燃料,我国现阶段仍然以煤炭为主,燃煤发电、取暖等过程排放的可吸入颗粒物占排放总量的30%以上。因此,从源头治理工业含尘气体,对于减小细颗粒物的排放,缓解大气污染,具有重要的现实意义。为此,国家针对燃煤烟气实行超低排放,即燃煤机组在完成治理之后的烟气排放达到天然气机组标准(SO2不超过35mg/m3、NOx不超过50mg/m3、烟尘不超过5mg/m3),现有技术难以经济地满足此要求,必须开发新的方法及装备,突破现有除尘方法及装备的局限,耦合多种除尘机制。
中北大学付加等[14-17]以太原第二热电厂的粉煤灰来模拟粉尘[使用激光粒度分布仪对进口粉尘的粒度分布(数量分散度)进行测量,粒度分布见表3-2,其粒径集中分布在1~3μm,平均粒径为2.25μm],对转子规模相近的错流与逆流旋转填料床脱除细颗粒物进行了研究,分别对二者的总除尘效率和分级除尘效率进行了系统研究,并进行了对比分析。通过对超重力多相分离工艺参数——气体含尘浓度、超重力因子、液体喷淋密度、气速、液体循环时间对除尘效率影响的研究,确定适宜工艺条件。
表3-2 模拟粉尘的粒度分布

3.1.3.1 超重力多相分离流程
超重力多相分离流程如图3-1所示。烘干后的粉煤灰由小型螺杆加料机3以一定流量挤出到离心风机1的入口处,再与由风机吸入的定量空气混合,在管道内形成一定浓度的均匀含尘气体。同时,储液槽中的水由液泵5输送至错流或逆流旋转填料床4,在填料内部被剪切与聚并成液滴、液丝和液膜,捕集尘粒后排出进入储液槽,循环使用。

图3-1 超重力气-固分离除尘性能实验流程
1—风机;2—气体流量计;3—螺杆加料机;4—逆流/错流旋转填料床; 5—液泵;6—液体流量计;7—储液槽;8—U形管压差计
实验过程中使用TFC-30s型双通道粉尘采样仪对进、出口气体进行采样分析:即采样前在采样仪的双通道内分别放入干燥后的过氯乙烯滤膜,取样过程中,分别调节采样仪的双通道流量计,使其对进、出口气体进行同时采样,粉尘过滤在滤膜上,一定时间后,关闭采样仪,取下滤膜;然后将滤膜融入10mL乙酸丁酯溶剂中,使用激光粒度分布仪对粉尘的粒度分布进行分析,即得到粉尘的数量频率。同时,使用LB-FC手持式智能粉尘烟尘检测仪对旋转填料床进、出口的含尘浓度进行实时在线测量。
3.1.3.2 超重力的多相分离性能
(1)错流旋转填料床的分离性能
错流旋转填料床的分离性能如图3-2~图3-9所示,分别是总除尘效率和分级除尘效率随超重力因子、空床气速、液体喷淋密度、气体含尘浓度(或粉尘粒度)的变化规律。

图3-2 超重力因子β对总除尘效率的影响

图3-3 超重力因子β对分级效率的影响

图3-4 空床气速对总除尘效率的影响

图3-5 空床气速对分级效率的影响

图3-6 液体喷淋密度对总除尘效率的影响

图3-7 液体喷淋密度对分级效率的影响

图3-8 气体含尘浓度对总除尘效率的影响

图3-9 粉尘粒度对分级效率的影响
对研究结果分析发现,错流旋转填料床的总除尘效率和分级除尘效率均随着超重力因子、液体喷淋密度、空床气速的增大而增大;粉尘粒度越大越易脱除,粒度为2.0μm的脱除度达99%,切割粒径达0.08μm;适宜的工艺参数:超重力因子160,液体喷淋密度为6.3m3/(m2·h),空床气速为2.6m/s;对于进口气体中含尘浓度低于16g/m3的总除尘效率可稳定在99.5%以上,若气体含尘浓度较高,可以采用两级或多级来处理,以达到超低排放要求。
(2)错流与逆流旋转填料床的分离性能对比
在相近工艺条件下,对比研究了超重力因子β、液体喷淋密度q和空床气速u等参数对错流和逆流旋转填料床的总除尘效率和分级效率的影响。
①总除尘效率对比 表3-3是错流与逆流旋转填料床分别在各自的适宜操作条件的总除尘效率。
表3-3 错流与逆流旋转填料床的总除尘效率对比

对比结果说明,逆流旋转填料床可以在更小的超重力因子和液体喷淋密度条件下,达到更高的除尘效率。
②分级除尘效率对比 图3-10是错流床与逆流旋转填料床在各自适宜操作条件下的分级效率。

图3-10 错流与逆流旋转填料床的分级效率对比
对比研究结果知,逆流旋转填料床的分级效率略高于错流床,但对于大于2.5μm的粉尘,二者的脱除率都超过99.8%,即错流床和逆流床对2.5μm粉尘的分级效率分别可以达到99.87%和99.9%,对0.25μm粉尘的分级效率η0.25分别为70.1%和75.7%,均高于现有除尘器,且逆流床的分级效率更高。
(3)分级效率拟合
W.Licht等[18]研究发现,大多数除尘器的分级效率与粉尘粒径的关系可以用下式表示:
(3-1)
式中,m、n为特性系数。其中,m反映分级除尘效率大小,m越大,除尘器的分级效率越高;系数n反映粉尘粒度对该除尘器分级效的率影响,n越小,分级效率曲线越平坦,除尘器对细微颗粒物的分级效率越高。
对错流旋转填料床在超重力因子为163,喷淋密度为6.3m3/(m2·h),气速为2.6m/s时的分级效率数据进行回归分析得出,m=1.72,n=0.51,拟合度R2=0.96,拟合结果良好,如图3-11所示。

图3-11 错流旋转填料床分级效率拟合曲线
表3-4是几种常见除尘器的分级效率特性系数。对比发现,旋转填料床的分级效率大于一般湿式除尘器,与静电除尘器相近,可以高效脱除气体中的细颗粒物。逆流旋转床的m值大于错流床,说明逆流床的分级效率高于错流床;二者的n值相近,说明错流床与逆流床对细微颗粒物的脱除效率相当。
表3-4 不同除尘器的分级效率特性系数

通过对超重力多相分离工艺参数的优化研究,得出以下结论:错流旋转填料床的除尘效率均随着转速、液气比、空床气速的增大而增大,且在相同操作条件下,逆流旋转填料床的除尘效率略高于错流旋转填料床,且对于粒径为0.25μm粒子的去除率达99.5%以上,可以高效率地脱除气体中的细颗粒物。
3.1.4 超重力湿法净化气体中细颗粒物技术应用实例
我国近年来频繁地出现长时间,大范围的“雾霾”天气,引起国家高度重视,出台政策强调,必须从源头治理雾霾。因而,高效脱除工业气体中细颗粒物技术的工业应用,对于缓解大气污染具有重要的现实意义。下面结合超低排放需求介绍几个典型的应用案例。
3.1.4.1 治理复合肥烟囱含尘尾气中的应用
山西某集团是我国最大的硝基复合肥生产基地,复合肥二厂利用硝酸磷肥副产硝酸钙生产硝酸铵钙的过程中,因操作温度和压力的不稳定使转鼓流化床造粒机和转鼓流化床冷却机产生大量的造粒尾气,气量为43000m3/h,其含尘约3000mg/m3的硝酸铵钙产品,直接排放对环境污染大。该尾气存在尘粒径细小,且含尘浓度高,常规方法无法高效脱除,且极易堵塞除尘设备,难以长期稳定运行;同时,富铵钙生产装置在22m高的平台上,空间位置十分有限(厂房内高度仅有5m),传统除尘设备因除尘效率与空间布置问题而不能实施,导致多年无法治理。
中北大学针对此难题,开发了超重力湿法回收富铵钙尾气治理工艺及装备,建立了示范工程,于2003年10月投入使用。项目中超重力装置直径1.6m、高3.5m,安装在生产现场狭小空间内,满足了厂房内布置的特殊限制。经过10多年运行结果表明超重力多相分离技术除尘效果良好,出口气体中含尘量仅为5mg/m3,除尘效率达到了99%以上,循环用水量仅为8~12t/h,用水量仅为普通湿法除尘的20%~40%,且除尘效率更高。吸收粉尘后的液体进入生产工序,既治理了污染,又回收了产品。
3.1.4.2 治理高浓度硫酸铵尾气中的应用
贵州某厂是中国规模最大、工艺技术最先进的磷化工企业,在国内外磷化工行业具有举足轻重的地位。2012年贵州地区硫酸铵粉尘排放标准:从700mg/m3降低到250mg/m3,原有的麻石除尘器因效率低,且除尘率不稳定,随入口气体中尘含量的变化波动较大,已无法满足此要求。据实地监测,尾气中硫酸铵高达5000~8000mg/m3,不仅对周围环境造成极大污染,也造成了资源浪费。含硫酸铵的尾气工况见表3-5。
表3-5 含硫酸铵的尾气工况

2012年中北大学在生产现场原有的除尘装置后增设了超重力湿法净化硫酸铵尾气装置,进行了工业试验和参数优化工作。进口尘含量对除尘率的影响情况如图3-12所示。

图3-12 进口尘含量与除尘率的关系
从结果看出,超重力除尘装置的除尘率随进口尘含量的增加而增加,特别是浓度在0.4~0.5mg/m3除尘率增加显著,从35%快速增加到70%。工艺参数优化后,在液气比为0.6L/m3左右,超重力因子为65,停止原麻石除尘装置进水的情况下,除尘率达99.7%,即从入口尘含量7000mg/m3左右脱除到240mg/m3以下,达到了当地排放标准。表明超重力多相分离技术同样适用于高浓度粉尘气体的净化,且循环水量仅为原麻石除尘的1/3。
3.1.4.3 深度净化半水煤气中的应用
贵州某集团年产20万吨/年合成氨项目合成车间压缩机进口半水煤气含有硫膏、粉尘、焦油等杂质,经常堵塞压缩机活门而导致压缩机停车、清洗以及长期点天灯的现象,严重影响装置的正常稳定运行、浪费煤气资源和污染环境。
2011年12月~2012年3月中北大学进行了超重力湿法净化半水煤气工程的设计及实施。超重力设备直径1600mm,高度3200mm,最高转速600r/min,装机功率18.5kW,半水煤气进口压力为10~45kPa,煤气流量21000m3/h,洗涤水流量10m3/h,净化后的煤气含粉尘及焦油浓度降低到了5mg/m3以下,气相压力损失低于800Pa。连续运行30天后,压缩机的活门没有焦油和粉尘的积结与堵塞。项目实施后,压缩机连续稳定运行了半年以上,极大地缓解了压缩机堵塞和停车的情况,提高了生产效率,有效地回收了煤气,结束了多年点天灯的资源浪费现象,减少了环境污染。
3.1.4.4 深度净化煤锁气中的应用
新疆某有限公司合成氨造气车间的煤锁气尽管经过水洗涤塔和旋风除尘器除去了大部分的粒尘和部分焦油,但仍然含有大量的微细颗粒物及焦油等杂质,经常导致压缩机的活门结疤、堵塞而停运,煤锁气只能去点火炬烧掉,不仅导致煤气浪费,而且污染环境。为此,2013年1月,引入中北大学超重力多相分离技术,在煤气进入压缩机前安装超重力多相分离装置,利用超重力旋转填料床湿法深度净化气体技术将煤气中的粉尘、焦油等杂物进一步脱除,以利后续压缩机正常运行。
处理煤气量20700m3/h;煤气温度约40℃;压力约3.4kPa;
压缩机进口压力要求≥2.0kPa;气体含有微量焦油、尘、氨等杂质。
因压缩机进口处原有旋风除尘器,故在该项目中省去了气液分离器,经超重力装置除尘后的煤气沿切线进入旋风分离器,将夹带的少量液体去除后,进入压缩机。
该项目2013年7月投入运行,压缩机可连续稳定运行6个月以上,结束原来只有连续1~2周的限制。经过连续1个月的监测结果表明,超重力多相分离技术的除油率、除尘率和除氨率分别达到90%、95%和88%以上,为压缩机长期稳定运行创造了条件。解决了煤锁气火炬燃烧排放造成的环境污染和资源浪费的行业难题。
3.1.5 超重力除尘装置与传统除尘设备性能比较
多年工业应用表明,超重力多相分离技术具有效率高、压降低、体积小、能耗低、适应范围宽等特点,且切割粒径小,特别适用于细颗粒物的脱除,将是从源头治理雾霾的利器。表3-6给出超重力装置与传统设备性能对比数据。
表3-6 旋转填料床与传统工业除尘器性能对比

总的来讲,超重力多相分离技术与传统技术相比具备以下特点。
①利用超重力强化气液传递,并耦合多种除尘机制的特性,极大地提高除尘效率和净化度,实现超低排放,对于亲水或非亲水性粉尘,一次除尘效率达到99%以上。
②液气比小,约为传统的1/4左右,较小液气比意味着液体循环量的减少,从而减小循环泵的功率,降低后处理过程投资和运行费用。
③适用范围广,与传统除尘机制相比,超重力场除尘更具有良好适应性,能够适用于多种来源的含尘气体处理,包括亲水、憎水、高浓度、低浓度、飘尘、颗粒、油烟、焦油等体系。
④压力损失小,与传统除尘设备相比,超重力装置压力损失小,在低液气比情况下,其压降小于200Pa,在高的液气比条件下,其压降在800Pa以下,而文丘里洗涤器、填料塔的压降高于500~1000Pa。超重力场对于气相压力要求不高,多数场合不需要增加风机。
⑤占地面积小,超重力装置单位体积处理能力大,设备体积最小,相应的投资少、占地省。
面对国家提倡的工业过程节能减排、超低排放等需求,超重力多相分技术可以广泛适用于工业气体的深度净化,实现过程工业的节能、减排、高效、绿色发展。
3.2 离心流态化
相对于传统重力流化床及其不足,20世纪60年代初前苏联学者提出了离心流化床(CFBD)概念。由于该技术可通过调节超重力因子(即离心力场)使颗粒在理想的气速下进行流化操作,因而比之于传统流化床,该技术具有许多独特的优势:流化气速可调,操作弹性较大,操作范围比传统流化床宽;由于颗粒在超重力场下有效重力增加,因而流化时气固之间的相互作用极大地增强,这不仅使其传质传热速率远高于传统流化床,而且还有助于限制或减小气泡的生成、颗粒的聚团倾向和阻止颗粒的扬析,促进聚式流态化向散式化的转变,从而改善颗粒尤其是超细颗粒的流化质量;此外,离心流化床表面积较小、设备紧凑、空间布置灵活并能够在重力场外(如太空)和晃动条件下操作。所以该技术一提出,人们便认识到了它潜在的广阔应用前景,并进行了大量的研究工作。
3.2.1 离心流化床的工作原理
离心流态化是相对于传统重力流态化的一种新型气-固接触技术。如图3-13所示,在一刚性的、壁上均匀、有气体分布孔的圆形转鼓内装入固体物料,然后使转鼓以一定的转速旋转,由于受到离心力的作用,物料将均匀分布在转鼓内壁上,形成环状固定床。此时,由转鼓外侧经壁孔通入气体,床层中的物料将受到离心力及与离心力方向相反的气体作用力。当气速增加到最小流化速度时,内层物料所受的离心力与气体作用力达到平衡,开始流化。随着气速的进一步增加,床层内物料由内开始向外逐层流化至完全流化状态。

图3-13 离心流化床的原理图
3.2.2 离心流化床的分类
离心流化床按结构特点可分为立式和卧式两种。
立式离心流化床的转鼓轴线处于垂直位置(图3-14),流态化时受重力的影响,不易均匀流态化,特别是对于大颗粒、湿含量高的物料难以控制。故一般用于颗粒较小,密度较低,表面水分高的物料的干燥。干燥的时间可以很短,且出料方便。

图3-14 立式离心流化床设备结构示意图
1—螺旋进料器;2—电动机;3—搅拌及分布器轴; 4—空心轴;5—轴承;6—物料分布器;7—干燥转鼓; 8—搅拌齿;9—排风管;10—物料分离器
卧式离心流化床的转鼓轴线处于水平位置,物料流化时受重力的影响相对较小,因而适合处理颗粒大、密度高、湿含量也高的物料,能获得较好的流化质量。同时,其干燥时间也可加以控制。
图3-15所示是前苏联学者设计的带有窄的固相出料口和迷宫密封的离心流化床示意图。在这个结构中,进料是通过中空的旋转轴,但出料是通过转鼓的一端和出料室之间窄的出料口流出的。

图3-15 一个床层的设备示意图
1—外壳;2—转鼓;3—反射板;4—空心轴;5—迷宫式密封
图3-16所示为连续进料的多层床层的示意图。转鼓为锥形结构。物料通过中空的旋转轴进入,首先在转鼓的最内层流化,当物料层高度超过层与层之间的物料导管高度时,在离心力作用下进入第二层进行流化,依次进行。(a)、(b)结构上不同之处在于出料方式的不同:(a)中物料经转鼓最外层的窄的出料口流入出料室;(b)中转鼓最外层有一导管与中空的旋转轴相连,最终的物料在气体曳力作用下经导管沿中空的旋转轴流出。

图3-16 具有固相循环的多层床设备
图3-17所示为连续进料的单层转鼓的结构示意图。(a)中在转鼓内设有一系列径向挡板,物料经中空旋转轴进入,依次在挡板与挡板之间流化,最终在气流曳力作用下沿旋转轴流出;(b)中在转鼓内部径向贯穿一系列螺旋形的挡板,物料经中空旋转轴进入,依次沿着螺旋形的挡板流到转鼓另一端,在气流曳力作用下沿旋转轴流出。(a)、(b)这样的结构便于形成一定的浓度梯度和温度梯度。

图3-17 固体循环的单床层设备
美国学者P.F.Hanni等在D.F.Farkas的装置基础上,设计出适用大规模生产的卧式连续离心流化床干燥器。转鼓直径为254mm,长度为2540mm,干燥表面积可达1.953m3,孔直径为2.4mm孔间距为9.6mm,开孔率为45%。转鼓采用皮带传动,速度可达350r/min。图3-18为进料、进风端的示意图。物料由转鼓一端通过压缩空气进入。在空气进口端设有一系列逆流叶片,便于在0~45°之间调节空气的流向。图3-19所示为物料流和排出室的示意图。物料经转鼓另一端的出料口卸出,排出室内设有一挡板以调节出料速度。整个转鼓有一个支架可以在0~6°的范围内调节以便于控制物料的停留时间。

图3-18 进料、进风端的示意图
1—压缩空气进料器;2—空气室;3—干燥器; 4—倾斜装置;5—折叶密封

图3-19 物料流和排出室示意图
1—物料入口;2—干燥器;3—空气室; 4—出料口;5—可调斜形支撑;6—导流叶片; 7—密封挡板;8—出料口
中国王喜忠、阎红等在研究离心流化床干燥器流体力学性能时设计了卧式连续离心流化床干燥器。该装置干燥转鼓的内径和长度均为150mm。转鼓孔径为12mm错列;转鼓内衬有40目不锈钢丝网;转鼓的总开孔率为28.2%。在转鼓开口一侧,用法兰连接一内径为110mm的中空滑动轴,主要作用是:①支撑转鼓旋转;②相当于堰,限定床层的最大高度为20mm,必要时还可改变堰高,以调节床层中物料厚度。
CFBD按进风方式,可分为全角度进风和半角度进风两种。图3-20为全角度进风CFBD的结构示意图。热风从各个角度沿转筒径向吹入干燥器内,床层内的物料在各个角度上均受到离心力(超重力)和与其相反的气体作用力。特点是物料流化均匀,床层稳定,有清晰的流化界面,对物料的磨损小。图3-21为半角度进风CFBD的结构示意图,床层物料在进风的一侧受到离心力和方向相反的气体作用力而流化,而在出风的一侧,物料受到方向相同的上述两个力的作用,变为固定床。这种方式的特点是:气体通过床层的压力较小,物料在转筒内的运动类似活塞流,并且由于气体二次通过床层,热效率高,但物料和转筒间的碰撞严重,流化也不均匀,不稳定。因此,为获得较好的流化质量,采用全角度进风方式的设备较多。

图3-20 全角度进风CFBD的结构示意图

图3-21 半角度进风CFBD的示意图
3.2.3 离心流化的流体力学性能研究
3.2.3.1 离心流化床的压降及流化速度关联式
CFBD的压降公式是通过流化床层物料受力分析得到的,其压力降公式如下:
(3-2)
式中,Δp为床层压降,mmH2O;M为床层中物料的质量流量,kg/s;Ap为床层中颗粒物料的总外表面积,m2;ac为离心加速度,m/s2;Fc为离心因子rω2/g;g为重力加速度,m/s2;r为转鼓半径,m;ω为转筒角速度,1/s。
在可比的条件下,离心流化床的床层压降是普通流化床床层压降的Fc倍。式子形式简单,计算方便,而且易于和重力流化床比较。但其计算的压降值和实测的压降值相差较大。造成这种误差的原因有以下几点:①推导时没有考虑离心流化床物料流化时的特点,即由于离心流化心力的存在,不论气体的运动还是床层物料的运动都和重力流化床中的有所不同,未充分考虑气体的流型和床层物料的运动,所造成的影响势必带来误差;②推导时忽略了重力场的影响,重力的影响是存在的,造成床层物料流化的不均匀性,是造成误差主要原因。因此,式(3-2)有必要进行研究与修正。
Fan等(1985)提出的CFBD中的压降及临界流化速度关联式适用性也较广。他在考虑了圆柱状转鼓的“曲率效应”影响的前提下作了下列假设:
①当流体对物料的曳力与整个床层物料的有效重量相等时,物料开始流化;
②流体的径向速度相等。
推导出的压降关联式如下:
(3-3)
式中,Δp为床层压降,mmH2O;ϕ1为压降方程系数;u0为基于外半径的表观流化气速,m/s;r0为转鼓外半径,m;r1为转鼓内半径,m;ϕ2为压降方程系数;ρg为气体密度,kg/m3;ω为转筒角速度,1/s。
当u0=u0c时,床层的压降达到了最大值Δpmax。
(3-4)
式中,u0c为临界流化速度,m/s。
临界流化速度的关联式如下:
(3-5)
式中,ρs为物料密度,kg/m3。
其中
(3-6)
(3-7)
式中,ε为床层孔隙率;dp为床层中颗粒粒径,m;μg为气体黏度,Pa·s。
关于CFBD的临界流化速度的关联式,大多是借用重力流化床的关联式直接外推而得到的经验或半经验式。目前运用最广泛的是Gelperni通过修正重力场的关系式得到的:
(3-8)
(3-9)
(3-10)
(3-11)
式中,Ar'是用离心因子Fc修正的阿基米德数;Re是最小流态化速度时的雷诺数;ρf为液体密度;K、L与床层空隙率相关。
D.F.Farkas等对上式进行验证,指出该式仅对球形颗粒有较好的准确性,且需有准确dp和ε值。对非球形颗粒则需要校正为球形颗粒。由于床层中的ε值不易准确测取,该式的应用受到了限制。因而需要另外的特征数关联式,在这种关联式中不含有孔隙率ε,或找出一种可以间接估算ε的方法,这一方面的工作还需要进一步加强。
3.2.3.2 离心流化床的床层压降与流化速度的关系
关于压降与气速的关系,中外学者中存在着两种不同的观点。分别以两种不同的压降-气速曲线加以说明。
一种观点如图3-22所示,曲线(1)代表了Kroger(1979)[19],Metcalfe(1977)[20],Levy(1978)[21],Demirean(1978)[22],Y-Men-Chen(1987)[23]等的实验结果。

图3-22 两种压降对气速关系曲线
由图3-22中曲线(1)可以看出,CFBD的压降与其表观气速的关系分为三个阶段。第一阶段,即固定床阶段,此时,us=ubf,曲线呈直线,表明压降随气速的增加而线性增加;第二阶段,半流化阶段,此时,ubf≤us<u0c曲线呈圆弧状,表明压降随气速的增加与固定床时的相比,增加幅度下降;到第三阶段,完全流化阶段,us≥u0c,此时压降恒定不变,为常数。其中us为气体表观速率;ubf为起始流化速度;u0c为临界流化速度。
另一种观点的主要分歧在第三阶段,研究者认为当us≥u0c,时,压降随气速的增加而减小,如图3-23中曲线(2)所示。这种观点的主要代表人有Fan(1955)、Takahashi等。
Chen提出CFB的分层流化机理来解释曲线(1)的趋势,认为当us≥ubf时,Δp基本上为一常数,与重力流化床的相似,其基本方程式是根据动量平衡提出的,表明其结论的关系式如下:
压降方程系数
(3-12)
(3-13)
式中,us为表观操作气速,m/s;ϕs为球形度。
ε由下式确定:
(3-14)
(3-15)
r由下式确定:
(3-16)
式中,M为床层中物料质量流量,kg/s;L为转鼓长度,m。
令人感兴趣的是方程式(3-14)在式(3-16)的限制下,方程式(3-16)的M为床层中粒子的总质量,是一个常数。方程式(3-14)右端第一项也是一个常数,第二项远小于第一项,所以当气速超过临界流化气速以后,压力降呈现一段平稳值。
T.Takahahsi等经过研究认为,离心流化床的压降曲线不同于重力流化床的,在达到临界流化速度时床层压降为一最大值,此后压降将减小,而不是一常数。最大值为式(3-17)。
(3-17)
临界流化速度u0c为:
(3-18)
(3-19)
(3-20)
式中,Δpmax为床层最大压降,Pa。
J.Kao等对Chen的分层流化机理进行了验证,并对Chen和Takahashi的实验结果差异作了解释。他所作的预测如下:当气速大于最小流化速度后,有式:
(3-21)
上式可解释为当床层厚度增加时,内部空气的曳力大于床层表面的离心力,致使表面粒子被带出床层,压降减小,从而导致曲线(2)的趋势。
3.2.3.3 床层混合与夹带
(1)床层中的颗粒混合
虽然对CFBD流体力学性质的一些理论研究已日趋成熟,但对CFBD中物料的具体混合情况,近几年才见报道。
Menon和Durian(1997)用分波器(DWS)对普通重力流化床中的粒子运动进行观察[24],结果表明:一些细小的气泡是床层中粒子混合的原因;流化床的壁面效应是促成粒子环状流的原因;在初始流化后,气泡生成前,才可能有均匀一致的流态化;随气速的增加,气泡的生成促使粒子做轴向或径向的对流运动。Kroger等[25](1980)曾研究过CFBD中粒子混合情况。他们的研究表明气泡是Gekdert-B和Gekdert-D粒子径向混合的最主要动力,然而他们没有观察Gekdert-A粒子的混合情况。Gui Hua Qian[26]等用频闪观测器记录两层颜色不同的Gekdert-A粒子在CFBD中的混合情况。他们的结论表明,临界流化速度后气泡的生成是促使相同材料、不同颜色的两层粒子混合的原因。对于密度不同的两种Gekdert-A粒子,混合性质决定于靠近分布板的是哪种粒子,若密度较大的粒子靠近分布数,混合情况则与同种密度的两种粒子的混合情况一致。若密度较小的粒子靠近分布板,由于两层粒子的密度差及流化特性的不同,在气泡生成之前,两层粒子已完全混合。
在传统流化床中,最小气泡生成速度umb依赖于粒子的尺寸及密度,而在CFBD中由于离心力的存在,粒子加速度比普通流化床中的粒子加速度大,而且没有明显的壁面效应造成环状流。因此决定umb的因素比较复杂,目前还没有文献报道。
(2)夹带
Gelperin等曾就CFBD的床层厚度与夹带的情况进行研究,发现床层厚度增大,夹带增大。R.Chevery等[27]研究了CFBD中的气泡动力学和颗粒夹带情况,指出离心力和Coriolis力能减少气泡的生成量、气泡的尺寸以及物料的夹带量,提高流化质量。E.K.Levy等[28]、T.Takahashi等[29]、V.A.Borodulya等[30]均就CFBD中物料的夹带及其影响因素进行过研究,得出一些可供参考的结论。T.Takahashi等还研究了卧式CFBD中物料的轴向混合情况,并得到了经验关联式。
3.2.4 离心流化床传热传质的研究
CFBD中气固运动和热质传递过程非常复杂,再加上测试手段的局限性,关于CFBD在传热、传质方面的研究比较少,还没有发现具有普遍意义的规律性,甚至是半经验半理论的关联式也很少见。
Gelperin等采用砂和硅胶对在CFBD中的传热、传质特性作过一些研究。得出,在CFBD中同样存在着传递作用高度,颗粒与流化介质之间传热、传质只在离气体分布网不大的距离ha(称稳定带)内完成,对于dp=0.2mm的沙子,在距离气体分布网4mm处已达到恒定温度。验证了热量衡算用于传热计算的可靠性。并用硅胶吸附水分的实验,关联了传质系数与Re的关系,如式(3-22):
(3-22)
其中:
(3-23)
(3-24)
式中,c为任意时刻颗粒内湿分的平均浓度;k为传质系数。
(3-25)
(3-26)
(3-27)
式中,Ar为阿基米德数。
得出CFBD的传热、传质速率高于重力流化床。但是Gelperin的研究涉及的物料少,Re的范围窄,且未考虑其他因素的影响,因而没有普遍性。
联邦德国的F.Alstetter[31]采用传递单元数模型(NUT模型)关联低密度、小颗粒湿物料与热空气间传热、传质特性,得出和关联式如下:
(3-28)
传热时
(3-29)
传质时
(3-30)
式中,Tgout为床层出口温度, ℃;Ts为床层温度, ℃;Tgin为床层进口温度, ℃;NTU为传质单元数;Ap为床层中颗粒物料的总外表面积,m2;cpg为气体定压比热容,kJ/(kg·℃);Mg为空气的质量流量,kg/s;Nu为努塞尔数;dp为颗粒直径m;L为转鼓长度,m;Pe为贝克莱数。
此模型完全地描述了流体和相界面之间接触时由显热向潜热的转换,但只限于小颗粒、低密度的物料。
前苏联的V.A.Borodulya等[30]用耐酸灰和砂进行了CFBD的传热研究,将传热特征数Nu与床层空隙率ε、Re、Pr、床高H及颗粒直径dp进行关联,稍后,V.A.Borodulya[32]进一步研究了CFBD的传质特性,得到了Sh与Re和床高与颗粒直径之比的特征数关联式,肯定了CFBD强化了气固间的热质传递,但未关联超重力因子,而且物料种类少,代表性不强。
东南大学的郝英立、施明恒[33,34]引入连续介质方法将固体颗粒看作是与流体相相互作用的流体,建立了CFBD中气固两相运动和热质传递的物理模型,如式(3-31)~式(3-36)所示。
连续性方程
气相:
(3-31)
固相:
(3-32)
式中,u为绝对速度矢量;v为相对速度矢量。
动量方程
气相:
(3-33)
固相:
(3-34)
式中,Ω为运动坐标系旋转速度矢量;r为流体质点的相对矢径;β为相间动量传递系数;τs为固体黏性应力张量,τf为气体黏性应力张量;ρs为固体密度;ρf为液相密度;D为虚拟质量系数,对于离散的球形颗粒可取1/2。
能量方程
气相:
(3-35)
固相:
(3-36)
式中,cV,s为固体定容比热容;cV,f为液体定容比热容;ks为固相热导率;kf为气相热导率;Ts为固相温度;Tf为液相温度。
3.3 离心流化的工业应用前景
3.3.1 医药、食品行业热敏性物质的快速干燥
离心流态化技术比之于传统流态化技术的最大优势是具有快速干燥能力,但在生产规模和操作连续化方面不如传统流化床,因此离心流态化技术应用于气固体系最有前景的是对干燥时间和强度有严格要求的高附加值产品的干燥。另一方面,虽然国内对于离心流态化干燥中的传质传热过程进行了理论和实验研究工作,但在这些研究中尚未有人从生产实际出发考虑工业设备的结构问题,商业化离心流化床干燥机在国内还属空白。因此,针对特定领域、以设备开发为目标进行必要的操作工艺研究和装备结构研究,可望尽快取得创新性成果。
3.3.2 煤的液化
利用煤的间接或直接加氢可以使煤转化为液态烃。这一转化过程通常是在高温(537.8℃)和高压下(6.8MPa)进行。为了最大程度地取得液体产物,氢的接触时间必须小于1s,而煤亦需尽快加热到反应温度并在该温度下维持数秒钟,所得产物宜迅速冷却以避免液体产物的进一步裂解,传统重力流化床难以胜任这一过程。由于离心流化床存在着相当高的离心力场,因此可以使用较大的气体速度,并由此导致较高的传热系数和传质系数。这样一来,短的接触时间以及使用较细粉煤等要求亦易于实现[35]。目前仅见国外报道,该项研究作为高新技术研究,可在实验机内进行相关实验工作,一旦取得实效,将是创新成果,在能源应用领域将产生历史性的革命,有着非常重要的市场价值。
3.3.3 超细粉体 (Geldart C类颗粒) 的流化
超细粉流态化具有重要的经济价值和技术价值,因此目前国内外都在积极开展超细粉流态化技术的研究,采用了表面改性、增加添加剂、外加声场、高压操作等方法,但效果有限。采用超重力技术流化超细粉的研究目前仅见国外报道,且取得了良好的效果。该项研究主要作为高新技术研究,可在干燥实验机内进行相关实验工作,一旦取得实效,将是创新成果,有重要的市场价值。
3.3.4 离心流化燃烧方面的研究
另一广泛的应用是用于燃料的燃烧。英国学者C.I.Metcalfe等对丙烷在离心流化中的燃烧进行实验研究,通过实验观察到丙烷能够在CFB中快速、稳定地燃烧,而且燃烧集中、加料便利。所用的实验设备如图3-23所示。

图3-23 离心流化燃烧实验设备
1—风机;2—丙烷流量计;3—空气流量计; 4—旋转密封;5—空心驱动轴;6—通气入口; 7—通气室;8—气体分布板
另外,CFB也被用于二元固体分离、气体脱硫、除尘[36]、核反应[37]以及不均匀催化反应。
CFB由于其理论研究的不足,开发的设备形式种类很少,许多工作只处于探索阶段,所以阻碍了它的工业应用。基于CFB的适用性和经济性,预计其商业前景是广阔的,这就迫切地要求加快、深入地研究出能指导实践的可靠理论,进而以适应该技术的推广和适用。CFB干燥理论模型化的研究中也将存在巨大困难:一是实验设备上获得的动力学结果在大型工业化干燥设备能否重现;二是干燥过程中需要微观测量及瞬间测量的技术还不完善,而测试技术是揭示流态化内部机理的一把钥匙。由于流体中存在着运动的颗粒,给测试工作带来许多困难,造成较大误差。因此,不同的作者对同一问题用不同的测试手段进行研究,会得出差别很大的结果,流化床传热系数的研究就是一例。
目前,需要解决的测试方法有:无接触的测试、运动着的固体颗粒温度的测试、床层中空隙率的测试、颗粒速度的测试、床层中颗粒的取样技术、物料湿含量的瞬间测试等。解决这些测试手段的问题,对CFB的研究和了解将是一个飞跃。
参考文献
[1] 李永胜.提高高炉煤气重力除尘器除尘率的方法 [D].鞍山:辽宁科技大学, 2006.
[2] 张殿印,顾海根.回流式惯性除尘器技术新进展[J].环境科学与技术,2000,(3):45-48.
[3] 张艳辉,刘有智.旋风除尘器的研究进展[J].华北工学院学报,1998,19(4):324-328.
[4] 高坚,张卫东,郝新敏.空气除尘设备及技术的发展[J].现代化工,2003,23(10):49-53.
[5] 向洪滨.新型湿法除尘器介绍[J].纯碱工业,1981,06:48-49.
[6] 周艳民,孙中宁,谷海峰,苗壮.文丘里洗涤器去除气溶胶特性实验研究[A]∥中国核学会核能动力分会反应堆热工流体专业委员会.第十四届全国反应堆热工流体学术会议暨中核核反应堆热工水力技术重点实验室2015年度学术年会论文集[C].中国核学会核能动力分会反应堆热工流体专业委员会,2015:4.
[7] 魏光.高效空塔喷淋技术在烟气脱硫装置中的应用[J].化学工程与装备,2011,7:230-233.
[8] 刘有智.超重力化工过程与技术[M].北京:国防工业出版社,2009.
[9] 张海峰.旋转床除尘技术的研究[D].北京:北京化工大学,1996.
[10] 张艳辉,柳来栓,刘有智.超重力旋转床用于烟气除尘的实验研究[J].环境工程,2003,21(6):42-43.
[11] 柳巍.超重力并流除尘技术的研究[D].北京:北京化工大学,2004.
[12] 宋云华,陈建铭,付继文等.旋转填充床除尘技术的研究[J].化工进展,2003,22(5):499-502.
[13] 黄德斌,邓先和,田东磊等.超重力旋转床脱除微米级粉尘的实验研究[J].化学工程,2011,39(3):42-45.
[14] 付加.超重力湿法除尘技术研究[D].太原:中北大学,2015.
[15] 李俊华,刘有智.超重力法烟气除尘机理及试验[J].化工生产与技术,2007,14(2):35-37.
[16] 付加,祁贵生,刘有智等.超重力湿法脱除气体中细颗粒物研究[J].化学工程,2015,43(4):6-10.
[17] 付加,祁贵生,刘有智等.错流旋转填料床脱除气体中细颗粒物的研究[J].化工进展,2015,34(3):680-683.
[18] Licht W.Air pollution control engineering:Basic calculations for particulate collection[M].CRC Press,1988.
[19] Kroger D G,Abdelnour G,Levy E K,Chen J.Flow characteristics in Packed and Rotating Beds[J].Powder Technol,1979,24:9.
[20] Metcalfe C I,Howard J R.Fluidization and Gas Combustion in a Rotating Fluidized Bed[J].PPI Enegry,1977,3:65.
[21] Levy E,Martin N,Chen J,Minimum Fluidization∥Kearins D L,ed.Fluidization[M].Cmabridge:Cambridge Univ Press,1978;71.
[22] Demirean N,Gibbs B H,Swithenbakn J, Taylor D S.Rotating Fluidized Bed Combustor∥Dvaidson J F,Kaims D L,eds.Fluidization[M].Cmabridge :Cmabridge Univ Press,1978:270.
[23] Y M Chen.FundamentalsofaCentrifugalFluidizedBed[J].AIChE Journal,1987,33(5):722-728.
[24] Menon N,D J Durian,et al.Practice Motions in a Gas-Fluidized bed of sand[J].Phy Rev Lett,1997,79:3407.
[25] Kroger D G,Abdelnour G,Levy E K,et al.Particle Distribution and Mixing in a Centrifugal Fluidized Bed[M].Fluidization.Springer US,1980:349-356.
[26] Gui-Hua Qian,John G Steven S,et al.Particle Mixing in a Rotating Fluidized Beds; inferences about the Fluidized State[J].AIChE Journal,1999,45(1):1401-1410.
[27] R Chevery,Y M Chen,et al.AIChE Journal,1980,26,(1);26,(3).
[28] E K Levy,W J Shakespeare,et al.Particle Elutriation from Centrifugal Fluidized Beds[J].AIChE Symp osium Series,1981,7792050:86-95.
[29] T Takahashi,S Kaseno,et al.Lateral Solid Particles Mixing in a Centrifugal Fluidized Bed[J].Journal of Chemical Engineering of Japan,1988,21(S):493-497.
[30] V A Borodulya,A I Podberezskii et al.Entrainment of Fluidized Material from Vertical Rotary Apparatus[J].Vestsi Akad Navuk BSSR,Ser Fiz-Energ,Navuk,1984,(4):79-82.
[31] F Alstetter.Fluidized Bed in a Centrifugal Field and It’s Use in Drying Technology[J].VDI-Ber,1986,607(1):611-644.
[32] V A Borodulya,A I Podebryozskii,G I Zhuravskii.Mass transfer in a centrifugal fluidized bed∥Heat and Mass Transfer:from Theory to Practice[in Russian],ITMO im A V.Lykova AN BSSR,Minsk,1984:31-34.
[33] 郝英立,施明恒.离心流化床的连续介质模型[J].东南大学学报,1997,26(2):18-23.
[34] 郝英立,施明恒.离心流化床中气固传热特性的实验研究[J].化工学报,1996,47(1):22-28.
[35] 卢天雄.流化床反应器[M].北京:化学工业出版社,1986.
[36] Brookhaven National Laboratoyr.BNL50990[R],1978.
[37] Brookhvaen National Laboratoyr.BNL50362[R],1972.