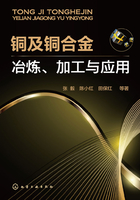
第4章 热处理
4.1 热处理基础
铜及铜合金的热处理通常有退火和时效两大类,退火包括去应力退火、再结晶退火、均匀化退火、固溶处理等,时效包括简单时效、复合时效等工艺。其理论基础分别是冷变形金属的回复与再结晶、过饱和固溶体的分解等理论,以及相关的位错理论、位错强化理论、时效析出与再结晶的相互作用理论等。国内外有关铜及铜合金的热处理原理和技术的论著和学术论文众多,既有教科书,也有学术专著和铜加工行业丛书和技术手册巨著等。本章撷其精髓,并结合有关研究进展进行介绍。
4.1.1 回复与再结晶
4.1.1.1 退火过程概述
(1)退火过程
经冷加工变形后,金属的显微组织和性能均发生变化,如晶粒拉长、形成纤维组织,强度、硬度提高,塑性降低等。同时,变形金属中还储存了一定的弹性畸变能,使变形金属处于热力学不稳定的亚稳状态。因此,经塑性变形的金属材料具有自发恢复到变形前低自由能状态的趋势。当加热冷变形金属时,它将通过发生回复、再结晶和晶粒长大等一系列过程逐渐恢复到变形前的状态。
根据不同温度下组织性能变化的特点,可将冷塑性变形金属材料的退火过程分为三个阶段,即较低温度下发生的回复,在一定温度范围发生的再结晶和再结晶完成后的晶粒长大。在实际加热过程中,上述三个过程相互重叠发生。回复是指较低退火温度或退火初始阶段发生的冷变形金属显微组织无明显变化,物理性能如导电率发生剧烈变化,力学性能轻微变化的过程。再结晶是指出现无畸变新晶粒逐步取代变形晶粒的过程;晶粒长大是指再结晶结束以后,无畸变新晶粒的继续长大。
图4-1为冷变形金属退火加热时显微组织的变化。回复阶段,光学显微镜下观察的组织几乎没有变化,仍然保持变形晶粒;再结晶阶段,首先是出现新的无畸变的再结晶晶粒核心,然后核心界面逐渐向周围扩展消耗周围的变形基体而长大,直到变形组织完全为新的无畸变的细小等轴晶粒取代为止;晶粒长大阶段,是在晶界能的驱动下,再结晶的新晶粒互相吞并而长大,以获得在该温度下较为稳定的晶粒尺寸。

图4-1 冷变形金属退火加热时显微组织的变化
图4-2为冷变形金属加热时某些性能随退火温度的变化。由图4-2可知,冷变形金属在退火加热时不同温度具有不同的变化规律。

图4-2 冷变形金属加热时某些性能随退火温度的变化
①强度与硬度 回复阶段的硬度变化很小,约占总变化的1/5,而再结晶阶段则下降较大。可以推断,强度具有与硬度相似的变化规律。上述情况主要与金属中的位错机制有关,即回复阶段时,变形金属仍保持很高的位错密度,而发生再结晶后,则由于位错密度显著降低,故强度与硬度明显下降。
②电阻 变形金属的电阻在回复阶段已表现明显的下降趋势。因为电阻率与晶体点阵中的点缺陷(如空位、间隙原子等)密切相关。点缺陷所引起的点阵畸变会使传导电子产生散射,提高电阻率。它的散射作用比位错、界面所引起的更为强烈。因此,在回复阶段电阻率的明显下降就标志着在此阶段点缺陷浓度有明显的减小。
③内应力 在回复阶段,大部或全部的宏观内应力可以消除,而微观内应力则只有通过再结晶方可全部消除。
④亚晶粒尺寸和晶粒尺寸 在回复的前期,亚晶粒尺寸变化不大,但在后期,尤其在接近再结晶时,亚晶粒尺寸就显著增大。再结晶结束后,继续提高退火温度,晶粒尺寸快速变大。
⑤密度 变形金属的密度在再结晶阶段发生急剧增高,显然,除与前期点缺陷数目减少有关外,主要是因再结晶阶段中位错密度显著降低所致。
⑥储能释放 当冷变形金属加热到足以引起应力松弛的温度时,储能就被释放出来。在恢复阶段,各种材料释放的储能量均较小,再结晶晶粒出现的温度对应于储能释放曲线的高峰处。
(2)回复过程
回复是冷变形金属在退火时发生组织性能变化的早期阶段,回复阶段的加热温度不同,冷变形金属的回复机制各异。
①低温回复 低温时,回复主要与点缺陷的迁移有关。冷变形时产生了大量点缺陷——空位和间隙原子,点缺陷运动所需的热激活能较低,因而可在较低温度时就可进行。它们可迁移至晶界(或金属表面),并通过空位与位错的交互作用、空位与间隙原子的重新结合,以及空位聚合起来形成空位对、空位群和空位片——崩塌成位错环而消失,从而使点缺陷密度明显下降。故对点缺陷很敏感的电阻率此时也明显下降。
②中温回复 加热温度稍高时,会发生位错运动和重新分布。回复的机制主要与位错的滑移有关:同一滑移面上异号位错可以相互吸引而抵消;位错偶极子的两条位错线相消等。
③高温回复
高温(约0.3Tm)时,刃型位错可获得足够的能量产生攀移。刃位错攀移的结果导致:a.使滑移面上不规则的位错重新分布,刃型位错垂直排列成墙,这种分布可显著降低位错的弹性畸变能,因此,可看到对应于此温度范围,有较大的应变能释放。b.沿垂直于滑移面方向排列并具有一定取向差的位错墙(小角度晶界),以及由此所产生的亚晶,即多边化结构(如图4-3所示)。

图4-3 位错在多边化过程中的重新分布
从上述回复机制可以理解,回复过程中电阻率的明显下降,主要是由于过量空位的减少和位错应变能的降低;内应力的降低主要是由于晶体内弹性应变的基本消除;硬度及强度下降不多则是由于位错密度下降不多,亚晶还较细小之故。因此,回复退火主要是用作去应力退火,使冷加工的金属在基本上保持加工硬化状态条件下降低其内应力,以避免变形并改善工件的耐蚀性,消除某些铜合金的应力腐蚀开裂倾向。
(3)再结晶
将冷变形后的金属加热到一定温度之后,在原变形组织中重新产生了无畸变的新晶粒,而性能也发生了明显的变化并恢复到变形前的状况,这个过程称之为再结晶。再结晶是一个显微组织重新改组的过程。再结晶的驱动力是变形金属经回复后未被释放的储存能(相当于变形总储能的90%)。通过再结晶退火可以消除冷加工的影响,故在实际生产中起着重要作用。
再结晶是一种形核和长大过程,即通过在变形组织的基体上产生新的无畸变再结晶晶核,通过逐渐长大形成等轴晶粒,从而取代全部变形组织的过程。
①形核 透射电镜观察表明,再结晶晶核是现存于局部高能量区域内的,以多边化形成的亚晶为基础形成再结晶核心。图4-4是三种再结晶形核方式示意图。

图4-4 三种再结晶形核方式示意图
图4-4中(a)和(b)这两种机制一般是在大的变形度下发生。当变形度较大时,晶体中位错不断增殖,由位错缠结组成的胞状结构,将在加热过程中发生胞壁平直化,并形成亚晶。借助亚晶作为再结晶的核心,其形核机制又可分为亚晶粒合并形核与亚晶粒界面迁移长大形核两种。
(a)亚晶粒合并形核。在回复阶段形成的亚晶,其相邻亚晶边界上的位错网络通过解离、拆散,以及位错的攀移与滑移,逐渐转移到周围其他亚晶界上,从而导致相邻亚晶边界的消失和亚晶的合并。合并后的亚晶,由于尺寸增大,以及亚晶界上位错密度的增加,使相邻亚晶的位向差相应增大,并逐渐转化为大角度晶界,它比小角度晶界具有大得多的迁移率,故可以迅速移动,清除其移动路程中存在的位错,在它后面留下无畸变的晶粒,从而构成再结晶核心。在变形程度较大且具有高层错能的金属中,多以这种亚晶合并机制形核。
(b)亚晶粒界面迁移长大形核。也称亚晶迁移机制。由于位错密度较高的亚晶界,其两侧亚晶的位向差较大,故在加热过程中容易发生迁移并逐渐变为大角度晶界,于是就可将它作为再结晶核心而长大。此机制易出现在变形度很大的低层错能金属中。铜合金的再结晶核心形成多以该机制进行。
上述两机制都是依靠亚晶粒的粗化来发展为再结晶核心的。
(c)晶界凸出形核。对于变形程度较小(一般小于20%)的金属,其再结晶核心多以晶界凸出方式形成,即应变诱导晶界移动,或称为凸出形核机制。
②长大 再结晶晶核形成之后,它就借界面的移动而向周围畸变区域长大。界面迁移的推动力是无畸变的新晶粒本身与周围畸变的母体(即旧晶粒)之间的应变能差,晶界总背离其曲率中心,向着畸变区域推进,直到全部形成无畸变的等轴晶粒为止,再结晶完成。这种再结晶也称为一次再结晶。
(4)再结晶晶粒长大和二次再结晶
再结晶结束后,材料通常得到细小等轴晶粒,若继续提高加热温度或延长加热时间,则将引起晶粒进一步长大。对晶粒长大而言,晶界移动的驱动力通常来自总的界面能的降低。晶粒长大按其特点可分为两类:正常晶粒长大与异常晶粒长大——二次再结晶,前者表现为大多数晶粒几乎同时逐渐均匀长大;而后者则为少数晶粒突发性的不均匀长大。
①晶粒的正常长大 再结晶完成后,晶粒长大是一自发过程。从整个系统而言,晶粒长大的驱动力是降低其总界面能。若就个别晶粒长大的微观过程来说,晶粒界面的不同曲率是造成晶界迁移的直接原因。实际上晶粒长大时,晶界总是向着曲率中心的方向移动,并不断平直化。因此,晶粒长大过程就是大晶粒不断长大,小晶粒不断消亡的过程,晶界由曲面逐渐变平的过程。在传统金相显微镜下,晶界平直且夹角为120°的六边形晶粒是二维晶粒的最稳定形状。
恒温下,再结晶晶粒正常长大时,平均晶粒直径Da与退火时间t之间存在Da=Ct1/2,即平均晶粒直径随退火时间的平方根而增大。但当金属中存在阻碍晶界迁移的因素(如杂质)时,t的指数项常小于1/2,所以一般可表示为Da=tn。
再结晶晶粒的正常长大是通过大角度晶界的迁移来进行的,因而所有影响晶界迁移的因素,如温度、分散相粒子、晶粒间位向差、杂质与微量元素等均对其有影响。
②二次再结晶 二次再结晶又称为异常晶粒长大、不连续晶粒长大,是一种特殊的晶粒长大现象。发生异常晶粒长大的基本条件是正常晶粒长大过程被分散相微粒、织构或表面的热蚀沟等所强烈阻碍。当晶粒细小的一次再结晶组织被继续加热时,上述阻碍正常晶粒长大的因素一旦开始消除时,少数特殊晶界将迅速迁移,这些晶粒一旦长到超过它周围的晶粒时,由于大晶粒的晶界总是凹向外侧的,因而晶界总是向外迁移而扩大,结果它就越长越大,直至互相接触为止,形成二次再结晶。图4-5为二维晶界示意图和晶界的移动方向。二维晶界的平衡状态为六边形,相邻晶界夹角为120°[图4-5(a)];当晶粒的晶界边数大于6时,晶界的曲率中心背离晶粒中心,在界面能的作用下有趋于平直的趋势,即晶粒长大;当晶粒的晶界边数小于6时,晶界的曲率中心指向晶粒中心,在界面能的作用下有趋于平直的趋势,即晶粒逐渐消亡。

图4-5 二维晶界示意图和晶界的移动方向
因此,二次再结晶的驱动力来自界面能的降低,而不是来自应变能。它不是靠重新产生新的晶核,而是以一次再结晶后的某些特殊晶粒作为基础而长大的。二次再结晶形成的粗大晶粒恶化金属材料的加工性能和使用性能,实践中应尽量加以避免。
4.1.1.2 回复与再结晶理论
(1)晶界移动的驱动力和阻力
回复与再结晶过程是亚晶界和再结晶晶界扫过高密度位错区域的过程。界面两侧位向差在10°~13°的晶界通常由位错墙构成,称为小角度晶界。相邻晶粒或亚晶粒的位向差越大,界面区域原子排列混乱程度和原子间距越大,这种大角度界面的迁移仅需要少数原子的迁移,比小角度晶界的位错墙需要整体移动来说相对容易。
晶界移动的驱动力主要来源于两方面,对冷变形金属来说主要是塑性变形晶粒与再结晶晶粒的体积自由能差,对完成再结晶的金属来说主要是细晶粒和粗大晶粒的界面能差。
冷变形金属的储存能主要与位错密度有关,位错的线能量正比于Gb2,冷加工金属的位错密度一般为1012/cm2,其界面迁移驱动力约为104N/cm2,这是再结晶的主要驱动力。
当合金中存在分散相粒子,其对晶界迁移有一定阻力,由于分散颗粒对晶界的阻碍作用,从而使晶粒长大速度降低。假设第二相粒子为球形,其半径为r,单位面积的晶界能为γb,当第二相粒子与晶界的相对位置如图4-6(a)所示时,其晶界面积减小pr2,晶界能则减小pr2γb,从而处于晶界能最小状态,同时此时粒子与晶界是处于力学平衡的位置。当晶界右移至图4-6(b)所示的位置时,不但因为晶界面积增大而增加了晶界能,此外在晶界表面张力的作用下,与粒子相接触处晶界还会发生弯曲,以使晶界与粒子表面相垂直。若以θ表示与粒子接触处晶界表面张力的作用方向和晶界平衡位置间的夹角,则晶界右移至此位置时,晶界沿其移动方向对粒子所施的拉力
F=2πrcosθ·γb sinθ=πrγb sin2θ (4-1)

图4-6 移动中的晶界与分散相粒子的交互作用示意图
根据牛顿第二定律,此力也等于在晶界移动的相反方向粒子对晶界移动所施的阻力,当θ=45°时,此阻力为最大,即
Fmax=πrγb (4-2)
实际上,由于在合金基体上均匀分布着许多第二相颗粒,因此,晶界迁移能力及其所决定的晶粒长大速度,不仅与分散相粒子的尺寸有关,而且单位体积中第二相粒子的数量也具有重要影响。通常,在第二相颗粒所占体积分数一定的条件下,颗粒越细,其数量越多,则晶界迁移所受到的阻力也越大,故晶粒长大速度随第二相颗粒的细化而减小。当晶界能所提供的晶界迁移驱动力正好与分散相粒子对晶界迁移所施加的阻力相等时,晶粒的正常长大即行停止。此时的晶粒平均直径称为极限的晶粒平均直径Dlim。存在下列关系:
(4-3)
式中,f为分散相粒子所占的体积分数。在f一定时,粒子越小,极限的晶粒平均直径越小。
(2)再结晶动力学
再结晶过程进行的快慢通常用再结晶速度来描述。与许多化学反应一样,再结晶过程也是一个热激活过程,无论是回复阶段位错的重排多边化,还是亚晶界的迁移、亚晶粒的合并长大和晶界的移动,均符合扩散性相变的典型S曲线特征,虽然再结晶过程并不伴随晶体结构的改变。图4-7为经98%冷轧的纯铜在不同温度下的等温再结晶曲线。

图4-7 经98%冷轧的纯铜(99.999%Cu)在不同温度下的等温再结晶曲线
再结晶速度取决于再结晶核心形核率和长大速率的大小。通常用Johnson-Mehl方程描述已经再结晶的体积分数fR与再结晶时间t,形核率N和长大速率G的关系:
(4-4)
等温再结晶时,形核率随时间呈指数关系衰减,因此通常用Avrami方程进行描述:
fR=1-exp(-BtK) (4-5)
或 (4-6)
式中,B和K均为常数,作图,直线的斜率为K值,截距为lgB。
4.1.2 影响回复与再结晶的因素
由于回复与再结晶在一定温度范围内进行,为便于讨论,一般把冷变形金属开始进行再结晶的最低温度称为再结晶温度,它可用金相法或硬度法测定,即以显微镜中出现第一颗新晶粒时的温度或以硬度下降50%所对应的温度,定为再结晶温度。在工业生产中,则通常以经过大变形量(约70%以上)的冷变形金属,经1h退火能完成再结晶(fR≥95%)所对应的温度,定为再结晶温度。也有的将在上述相同条件下开始再结晶的温度定义为再结晶温度,通常将按上述两个定义的再结晶温度分别称为再结晶终了温度和再结晶开始温度。显然两者在温度数据上是有差别的,在条件相同时,再结晶终了温度总是高于再结晶开始温度。我国目前习惯采用后者,若未注明,再结晶温度一般均指再结晶开始温度。
影响再结晶温度的因素很多,凡是提高再结晶形核速率N和长大速率G的因素都会降低再结晶温度。金属材料的结晶温度并不是一个物理常数,它不仅随材料成分而改变,同一材料其冷变形程度、原始晶粒尺寸、固溶原子、弥散颗粒、加工状态和退火工艺等因素也影响着再结晶温度。
4.1.2.1 合金的组成与组织
(1)固溶原子
金属中的杂质和微量合金元素可显著提高再结晶温度。表4-1为一些金属和合金的再结晶开始温度。表4-1表明,金属纯度不同,再结晶温度相差很大。
表4-1 某些有色金属和合金的再结晶温度近似值

图4-8示出13种合金元素对铜的再结晶温度的影响。由图4-8可见,不同合金元素对铜的再结晶温度的影响程度有明显差别。在添加量相同的情况下,合金元素以置换原子形式固溶于铜基体晶格内,溶质元素与铜之间原子尺寸差别越大(即在铜中的极限固溶度越小),则提高再结晶温度的作用越显著。其原因是溶质与溶剂原子的尺寸、晶格类型及电负性相差较大时,溶质原子与晶体缺陷的交互作用能越大,对缺陷运动的阻碍效应越大,并影响回复多边化过程和再结晶核心在加热时的形核和长大,从而显著提高再结晶温度。

图4-8 铜中13种合金元素的添加量与再结晶温度的关系
(2)弥散颗粒
弥散分布的第二相一般情况下可提高再结晶温度,弥散度愈大效果愈显著,但也存在弥散相促进再结晶核心形成的研究报道,这主要取决于弥散相粒子的大小及分布。当弥散颗粒尺寸较大时,间距较宽,如大于1μm,再结晶核心可在其表面形成;当弥散相颗粒尺寸很小且又较密集时,则会阻碍再结晶过程的进行。Al2O3、ZrO2和TiB2等弥散颗粒能显著提高铜的再结晶温度,以机械合金化法制备的Cu-3% TiB2复合材料,其软化温度高达980℃,接近铜的熔点。另外,弥散的稀土氧化物能提高钨、钼的再结晶温度。但应指出,当第二相数量不多且弥散度不大时,也有可能使再结晶温度降低。
(3)过饱和固溶体合金的退火析出与再结晶的交互作用
过饱和固溶体合金经过冷变形加工以后进行退火,由于合金的析出行为和再结晶行为都是热激活过程,因此在一定加热温度范围内合金第二相析出与再结晶过程存在重叠,存在相互竞争相互影响的现象,称为合金析出与再结晶的交互作用。
图4-9为合金析出与再结晶行为的交互作用示意图。再结晶和析出均有一定的孕育期,析出过程的孕育期tp与析出激活能Qp有一定联系;相类似,再结晶孕育期tR与再结晶激活能QR有关。图4-9(a)可知,具有Co成分的固溶体经冷变形后在不同温度加热具有不同的析出动力学特征。图4-9(b)根据退火加热温度不同分为三个区。温度高于T1,在该区为单相固溶体区,不存在析出行为,再结晶可以在析出开始之前完成,合金内溶质元素的偏析对再结晶过程存在影响;温度T1和T2之间为第二区,在这里虽然再结晶先开始,但在再结晶过程中存在析出现象,析出第二相对再结晶过程的继续进行产生影响;T2温度以下为第三区,合金的析出行为在再结晶开始之前出现,因此析出行为会阻碍合金回复时位错的移动、再结晶核心的形成以及晶界的迁移。

图4-9 合金析出与再结晶行为的交互作用
tR—再结晶开始;tP—未变形固溶体析出开始;t'R—受析出影响的再结晶开始;t'P—冷变形固溶体析出开始
一定情况下,再结晶前的析出行为也有利于再结晶过程。如合金析出完成后固溶体内溶质原子减少,溶质原子对变形基体的再结晶的阻碍作用会明显减弱。这时析出物的间距较大,不会明显阻碍晶界迁移,综合作用效果达到析出行为促进再结晶过程的目的。
(4)原始晶粒大小
在其他条件相同的情况下,金属的原始晶粒细小,冷变形时加工硬化率大,变形抗力越大,基体储能越高,故再结晶温度较低。此外,晶界往往成为再结晶核心形核部位,因此细晶粒金属的再结晶形核率和长大速率均增加,所形成的新晶粒更细小,再结晶温度将降低。图4-10为H70黄铜的原始晶粒大小对再结晶后晶粒尺寸的影响。可见在原始晶粒尺寸相同条件下,形变量越大,再结晶后的晶粒尺寸越小。

图4-10 H70黄铜的原始晶粒大小对再结晶后晶粒尺寸的影响
4.1.2.2 加工状态与退火工艺
(1)加工状态
金属材料的加工状态和加工程度——冷变形程度对再结晶温度有较大影响。随变形程度增加,再结晶温度降低。但冷变形使金属储能增加有一个上限,因此,当冷变形达到一定程度(变形量>70%)后,再结晶温度基本上不再随冷变形度的增加而改变,达到最低值。通常将变形程度在60%~70%以上,退火1~2h的最低开始再结晶温度TR称为再结晶门槛,一般用它来代表金属的再结晶温度。
对于工业纯金属,再结晶门槛温度与熔点之间存在以下关系:
TR=(0.3~0.4)Tm (4-7)
式中,TR、Tm分别为绝对温标表示的最低再结晶开始温度及熔点。对于特别纯的金属为:
TR=(0.25~0.3)Tm (4-8)
对于单相合金,TR要大得多(有时达到0.6 Tm),并随成分而变化。对弥散强化铜合金,如Al2O3弥散铜,其TR=(0.75~0.9)Tm。
在实际铜加工中,通常对铜合金进行热轧或热挤压加工,以分别获得板材或管棒材,在材料的不同加工部位发生不同的再结晶,如在热轧和热挤压变形区发生动态回复与再结晶,在冷却区发生静态再结晶,如图4-11所示。

图4-11 低层错能铜合金类金属材料热轧(a)、热挤压(b)变形区的动态回复与动态再结晶和冷却区的再结晶示意图
(2)退火工艺
退火工艺包括退火加热速度、加热时间和退火温度。
退火加热速度过慢或过快都有提高再结晶温度的趋势。加热速度过慢,回复过程比较充分,降低了储能,减小了再结晶驱动力;加热速度过快,在各温度下停留的时间太短,来不及再结晶形核和核心长大,故需加热到更高温才能进行再结晶。
在其他条件相同时,延长退火加热时间将降低再结晶温度。
退火温度越高,再结晶完成时间越短。从表4-1可以看出,铜及铜合金的再结晶温度通常为120~390℃,在流水式铜加工生产线上通常通过提高再结晶退火温度和缩短退火时间来提高生产效率,如在气垫连续退火炉中对铜合金薄板带进行440℃退火加热保温4min即可完成再结晶。
4.1.3 常用材料的退火组织及其控制
4.1.3.1 纯铜的退火
工业纯铜(即紫铜)一般只进行再结晶退火,其目的是为了消除内应力,使金属软化或改变晶粒度。退火温度一般为500~700℃。表4-2为纯铜的退火加热规范。图4-12为T2铜的力学性能及电阻率与退火温度的关系。
表4-2 纯铜的热加工与热处理规范


图4-12 T2铜的力学性能及电阻率与退火温度的关系
为了防止发生氢病,退火前必须将工件认真清洗干净,对于含氧铜,特别是含氧量大于0.02%的铜的退火,不能在木炭或其他还原性气氛保护下进行,只能在微氧化性气氛(例如燃烧完全的煤气炉)或真空气氛中进行,或将退火温度降低到500℃以下。经验表明,在500℃以下由于氢、碳等元素在固态铜中扩散慢,与铜中氧的(还原)反应进行很慢,氢病不容易发生。退火完毕,应迅速将制品转入气氛保护冷却区或冷水中冷却,以减少氧化。
再结晶退火后铜的晶粒度决定于退火温度和保温时间。实验表明,退火温度低时(550℃以下),保温时间的影响较小;若退火温度高则保温时间对晶粒度影响颇大。所以在高温下退火应尽量缩短保温时间,以避免粗大晶粒。
为了避免出现再结晶织构,退火前的冷变形度不应大于40%~60%,退火温度不应超过700℃。冷变形度越大,退火温度越高,再结晶织构越明显。
4.1.3.2 黄铜的退火
黄铜的主要热处理是退火,分为再结晶退火及去应力退火。
(1)再结晶退火
再结晶退火包括加工工序之间的中间退火和产品的最终退火,其目的是消除加工硬化,恢复塑性和获得细晶粒组织。黄铜的再结晶温度随合金成分及杂质含量的不同,大多在300~400℃之间;再结晶退火多在600~700℃进行。退火温度对黄铜H70性能的影响如图4-13所示。各种黄铜的具体退火温度见表4-3。

图4-13 退火温度对黄铜H70性能的影响
表4-3 各种黄铜的退火温度

退火温度过高会引起晶粒长大,使材料的性能下降。如图4-13所示。例如,HFe62-0.4黄铜,正确退火获得细晶粒组织时抗拉强度σb为415MPa,δ为34.5%,若加热温度过高,引起晶粒长大,则σb降至290MPa。

图4-14 α+β黄铜的再结晶温度与时间的关系
(a)变形量<40%,显示α不连续、β连续析出;(b) 变形量>70%,显示α与β不连续析出、成分均匀化区
黄铜的晶粒度对材料冷加工性能有很大影响。细晶粒组织的强度高,加工成形后质量好,但变形抗力较大,较难成形。粗晶粒组织则容易加工,但冲压件表面质量不好,甚至形成橘皮,疲劳性能也较差。因此,用于压力加工的黄铜进行再结晶退火时,必须根据需要,很好控制晶粒度。晶粒度是衡量黄铜退火质量的主要标准,不同晶粒度等级所适用的冷加工类型见表4-4。由表可见,变形越强烈,要求的晶粒度越大,但不能太大。
表4-4 适用于不同冷加工的退火铜合金的晶粒度

α黄铜退火后的冷却方式对性能影响不大,可用空冷或水冷。水冷可使工件表面的氧化皮脱落,获得光洁表面。
对于(α+β)黄铜,由于冷却过程中发生β→α相变,冷却越快,析出的针状α越细,硬度稍高。若要求塑性高,应采用缓慢冷却。反之,若为改善切削加工性能要求较高的硬度,可采用较快冷却。
Mader等的研究表明,变形量低于40%时,形变(α+β)黄铜退火加热时首先发生β相的连续再结晶,其次是α相的不连续再结晶,如图4-14(a)所示。通常情况下,相界面的位错密度较高优先成为再结晶核心形成的位置。变形量在70%以上时,500℃以上退火,形变α相和β相发生不连续再结晶,如图4-14(b)所示。500℃以下退火,fcc-α相与形变bcc-β相的成分发生均匀化,在相界面附近同时发生α相、β相的析出和再结晶。
(2)去应力退火
加工黄铜,特别是含锌量较高的黄铜,应力腐蚀破裂倾向很严重,其冷变形产品(包括成品和半成品)必须进行去应力退火,以消除变形过程中产生的残余内应力,防止自裂。去应力退火的温度,一般比再结晶温度低30~100℃,约为230~300℃。成分复杂的黄铜去应力退火温度约为300~350℃(见表4-3)。退火保温时间约为0.5~1h。
(3)退火硬化现象
α黄铜冷变形后于再结晶温度以下退火(或长期存放),其硬度不但不降低,反而有所升高(与此同时,电阻有所降低)。例如,三七黄铜(H63),冷变形50%后在235℃去应力退火1h,其抗拉强度不但不降低,反而升高约30MPa,伸长率则降低约2%。实验表明,含锌量大于10%的黄铜、含铝量大于4%的铝青铜、含锰量大于6%的锰青铜和含镍量大于30%的白铜都有这种退火异常硬化现象。这种现象也可称为变形时效,对于这种现象曾有过许多研究和解释。但对Cu-Zn及Cu-Al合金来说,主要是由于合金发生有序化转变,晶格的一些部分收缩,引起相的应变硬化所致。合金经过冷变形或淬火,促进了有序化过程的进行,有序化程度越发展,相应的应变越严重,硬化也越显著;此外,溶质原子在晶格缺陷上偏聚,从而增大了对位错运动的阻力,也是硬化的部分原因。薄膜透射电镜分析表明,发生退火异常硬化现象的合金组织中无沉淀相(或中间过渡相)形成。
利用上述退火异常硬化现象,对许多铜合金弹性材料进行低温退火,可提高其弹性性能。
4.1.3.3 其他铜合金的退火与热处理
铜及铜合金的完全退火一般用作中间退火及获得软制品的成品退火。中间退火是指冷变形过程中的退火,目的是消除前阶段冷变形造成的加工硬化,恢复材料塑性,以利于进一步冷变形。中间退火和成品退火工艺基本相同,但一般情况下前者的退火温度稍高,控制也不如成品退火那么严格。退火工艺的主要参数是退火温度和时间。对于铜及其合金而言,完全退火温度一般比再结晶温度高250~350℃。大多数黄铜和青铜的再结晶开始温度在300~400℃之间;含镍量大于10%的白铜及某些耐热铜合金则在400~500℃以上。因此,各种铜合金的退火温度有较大差异。
铝青铜具有自退火现象。从Cu-Al二元合金相图可以看出,Al含量为12%的Cu-Al合金的β相缓慢冷却在565℃发生共析转变β→(α+γ2),得到粗大(α+γ2)共析组织,材料发生脆化,性能恶化。若固溶处理后快冷发生马氏体转变,而后进行500℃退火处理,可以得到细小的α+γ2混合组织,合金得到强韧化。另外,通过添加少量Fe、Ni、Mn也可有效避免上述共析反应。常用铜合金的退火规程可参考表4-5。
表4-5 常用铜合金的退火规程

4.1.3.4 退火脆性和中温脆性
(1)退火脆性
冷加工后的α相铜合金进行退火处理有时会发生材料开裂的现象,称为退火脆性。佐藤等研究了铝黄铜和H70黄铜的退火脆性行为。外径70mm,壁厚15mm的铝黄铜管挤出后,进行10%~30%的拉伸,在600℃或400℃退火处理均会发生显著的脆性开裂现象,制品表面出现退火龟裂纹。H70黄铜也存在同样的现象。显微组织分析表明,脆化是由于再结晶前的晶界产生微空洞导致的。这与蠕变拉伸试验的空洞化现象类似。这种退火脆性与冷加工后的残留应力、退火加热温度条件、加热速度以及温度波动范围和保温时间,晶粒大小和加工变形量明显相关。作为对策,可以通过细化晶粒防止退火脆性,也可以通过快速加热尽快消除残余应变来避免。
(2)中温脆性
铜及铜合金在高温进行塑性变形时,在500℃前后的中温阶段通常出现如图4-15所示的合金的断面收缩率和冲击韧性等塑性、韧性降低的变形温度范围,这种脆性称为中温脆性。

图4-15 Cu-Zn 二元合金的中温脆性
(a)断面收缩率(b)冲击韧性
研究发现这种铜及铜合金的中温脆化原因,与合金杂质原子影响、三叉晶界开裂、晶界开裂、应变速率、晶粒直径等有关。
杂质原子在晶界平衡偏析可以降低界面能,对铜基体而言,杂质元素含量:Bi(0.6mg/kg以上)、Sb(0.3%~0.4%以上,H70黄铜0.01%以上)、Te(1mg/kg以上)、Se(>4mg/kg)、S(>10mg/kg)、Pb(>2mg/kg)、Sn(0.01%~1.2%以上)均会发生中温脆性。
井形和堀等通过三种粒径16μm、54μm、104μm无氧铜的高温拉伸研究发现,材料的断裂应变εf与最大拉伸载荷对应的应变εu的差值εf-εu、温度、应变速率、粒径的变化与加工硬化指数n和应变硬化指数m存在相关性。细化晶粒可以有效防止中温脆性。
4.1.3.5 低温退火硬化
图4-16为Cu-63.67%Zn α相合金的退火处理与抗拉强度、塑性、硬度、断裂强度等力学性能的关系曲线,可见α相铜合金200℃退火后,强度和硬度明显高于加工态,出现明显的低温硬化现象。

图4-16 Cu-63.67%Zn α相合金的退火处理与力学性能的关系(50%冷轧,退火3h)
1kp/mm2=9.81MPa
通常,冷加工后进行低温退火,会发生加工硬化的回复,材料出现软化。而图4-16这种情况与之相反,出现材料的抗拉强度、硬度、弹性极限出现升高的现象,称为低温退火硬化,对加工硬化型弹性合金、磷青铜、白铜具有实际意义。黄铜的中间退火温度为400~450℃,通过进行适当的冷加工变形量与200~250℃的低温退火配合可以提高弹性极限值。图4-17为不同温度下退火时间对HPb60-2.5-0.5-0.2黄铜棒显微硬度的影响,在该合金中也出现了明显的低温退火硬化现象。

图4-17 不同温度下退火时间对HPb60-2.5-0.5-0.2黄铜棒显微硬度的影响
α相铜合金的低温退火硬化机制主要有以下几种。
①Cu78-Ni-20-Al2合金经95%冷变形,进行400℃退火,其抗拉强度达到655MPa,其低温硬化机制为溶质原子的短程有序化。
②Cu55.26-Zn26.87-Ni17.70合金,经过类似处理,XRD发现合金形成超结构,即有序强化为其主要原因。
③微细GP.区颗粒的析出。
④铃木化学作用使Zn原子在层错上偏析,从而钉扎位错。
上述几种机制,通过XRD分析、中子衍射分析、比热测定等对比研究,第④种机制较为合理。
4.1.3.6 再结晶织构
具有变形织构的金属经再结晶后往往仍具有择扰取向,称再结晶织构。再结晶织构位向和原形变织构往往有一定的取向关系,但不完全相同。例如冷轧H70黄铜的织构在退火前后都是{113}<211>,而冷轧铜板的变形织构为{110}<112>,在350℃以上退火后得到的再结晶织构却变成立方体织构{100}<001>。
再结晶织构的形成机理有两种。
①定向形核理论 该理论认为由于变形基体中已经具有很强的择扰取向,再结晶形核时晶核本身也具有择优取向,晶核长大后就形成再结晶织构。
②定向生长理论 在再结晶开始阶段,存在着任意取向的晶核,但只有那些取向有利的晶核的晶界才能获得最快的迁移速率,例如fcc金属中,两晶粒的位向差相对于<111>轴为30°~40°时,其晶界迁移速率最快,于是这些晶核优先长大,而其他取向的晶核生长受到抑制,从而形成为取向接近的再结晶织构。透射电镜选区衍射的实验结果支持定向生长理论在再结晶织构形成过程中起主导作用的观点。
再结晶织构的影响因素较复杂:(a)化学成分对再结晶织构影响很大,甚至微量元素都表现出明显作用。例如,在铜中加入微量铝(0.2%)和镉(0.1%)能促进立方织构的形成,加入极微量的磷,则可阻止再结晶立方织构的出现。(b)原始组织也有影响,在一定冷轧变形率条件下,原始组织愈细,愈容易获得明显的立方织构(图4-18)。(c)退火工艺也是影响再结晶织构的因素。实验表明,很多金属在较低温度退火或快速加热至高温短时保温,再结晶织构与变形织构相同或基本相同。升高退火温度或延长保温时间,某些位向的晶粒择扰生长而使再结晶织构发生重大改变。(d)退火前的冷变形程度对不同合金影响不同,较难预测。

图4-18 铜的立方织构生成范围
4.1.3.7 再结晶晶粒的调控
再结晶晶粒度对材料的屈服强度影响较大,符合Hall-Petch关系。通过退火前冷变形量、退火温度、退火时间的合理协调,可以获得所需要的晶粒度。将变形程度、退火温度和再结晶后的晶粒大小的关系在一个图上表示就构成再结晶图。图4-19为H68黄铜的再结晶图,图4-20为Cu-63%Zn α黄铜退火3h的再结晶图。部分合金的再结晶图可在有关手册和文献中查阅。再结晶图是制定金属加工变形量和退火温度的重要依据。

图4-19 H68黄铜的再结晶图

图4-20 Cu-63%Zn α黄铜的再结晶图(退火3h)
4.1.4 时效处理
将双相合金加热到单相区成分均匀化后快速冷却可以得到过饱和的固溶体。这些溶质原子在高温都具有较大的溶解度(如图4-21中虚线所示合金),如果快速冷到室温,使β相来不及析出,将得到过饱和固溶体,会大大增加固溶强化作用。这种热处理工艺称为固溶处理也有称此过程为淬火。过饱和固溶体的过饱和溶质成为析出第二相的驱动力。对过饱和固溶体在固溶度变化曲线双相区适当温度下进行加热,发生过饱和固溶体的分解析出第二相,使合金的强度、硬度升高的热处理工艺称为时效。时效硬化的本质是从过饱和固溶体中析出弥散第二相。过饱和固溶体在室温长久放置产生的时效称为自然时效,而加热到室温以上某一温度进行的时效,则称为人工时效,就是通常所说的时效处理。

图4-21 具有时效硬化特性的二元合金相图示意图
只要具有溶解度变化的合金理论上都可以用时效的方法提高其强度和硬度。绝大多数铁基合金和非铁基合金都具有时效特性。但作为一种强化手段,对非铁基合金进行时效的意义更大:这是因为多数非铁基合金不具有多形性转变,固溶和时效是通过热处理提高其强度的唯一手段。
4.1.4.1 时效析出理论
(1)析出过程概述
合金平衡相图显示的第二相为平衡相,过饱和固溶体在时效过程中的分解是从低温开始首先析出与合金基体保持共格关系的G.P.区——溶质原子富集区,其次析出过渡中间相,最终转变为平衡相的系列过程。时效析出相的种类、大小、体积分数、分布状态、析出速度等显微组织特征对合金的宏观性能、特殊的力学性能密切相关,在工业上对合金的显微组织控制与调控具有重要意义。时效硬化类合金的化学成分、微量元素、固溶处理、加热速度、时效温度与时间、时效前的冷加工条件对时效过程均有显著影响。上述诸因素的控制是调控时效硬化合金显微组织和析出相结构的重要措施,这也是时效热处理的关键。
在固态相变中,新相和母相之间的相界面具有三种结构。
①共格界面。当两相晶体结构和晶格常数比较接近时,容易在有利的晶面上保持共格相界面。此时,在界面处晶格是连续的。一般情况下,新相与母相晶格常数或面间距不相同,因此在形成共格界面时,两相的晶格要产生一定的应变才能完全匹配。这样在界面附近,晶格常数较大的相就受到压应力,晶格常数较小的相就受到拉应力。对于共格界面,因晶格连续过渡,所以界面能很低,但弹性能较高,其程度决定于两相晶格常数和弹性模量的差异以及第二相的形状等因素。为减少弹性应变能,新相以片状或碟状形式生核和长大最为有利。
②非共格界面。相当于一般大角度晶界,如果新相与母相的比容相差不大,弹性应变能将很小,可以忽略不计。这时界面能γ成为了新相形成的决定因素。为了降低两相之间的界面能,新相晶核趋向于以球形出现,这样可以做到界面面积最小。如果两相晶体结构差别很大,γ值就会很高,此时即使表面积为最小(即新相晶核呈球形),而总界面能值仍然很大,相变将难以进行。
③半共格界面。介于上述两种界面之间,相界面由共格区和位错网络构成。当新相与母相的晶体结构及晶格常数大小相差较大时,如果形成共格界面,弹性应变能将会很高,这样就可以以局部共格的界面出现,中间隔以位错,这种界面称为半共格界面。
根据上述简略的能量关系分析,就很容易理解下面要讨论的Al-4%Cu合金的析出过程:先形成结构相同并保持共格关系的溶质原子富集区,即G.P.区;随后过渡到成分及结构与θ相近的θ″相和θ'相,同时共格关系逐渐破坏,最后形成非共格的具有正方结构的θ相。
时效析出过程有两种机制。
①溶质原子扩散为基础的第二相形成机制,即形核-长大机制。
②调幅分解机制。基于空位扩散的置换原子扩散机制与间隙原子扩散机制不同,对时效硬化型铜合金和铝合金等面心立方结构的合金来说,空位扩散更为重要,特别是G.P.区的形成与固溶处理的冻结空位紧密相关。
调幅分解的析出相分布很均匀。而最常见的形核-长大机制,在母相固溶体内自发均匀形核和均匀析出非常少见,形核部位通常为位错、层错、亚晶界、晶界、相界面等晶体缺陷处有限形核,导致非均匀析出。非均匀形核的析出相分布不均匀及析出相的粗大对合金的力学性能损害较大。特别是铜合金的晶界反应型不连续析出较易出现。
(2)过饱和固溶体的分解
通常过饱和固溶体的分解是通过形核、长大机制进行的,相变驱动力是两相自由焓差。固态相变同液相中的结晶不同,在能量关系中,弹性能一项占据比较重要的位置,因而相变需在更大的过冷条件下进行,有时还要经过某些中间过渡阶段。另外,在相界面结构上,新相形态和晶体取向上也需保持适
当的对应关系,以降低表面能和弹性应变能,使相变过程易于进行。
以Al-Cu合金为例,从体积自由焓角度来看,过饱和α固溶体中以直接析出平衡相θ最有利,因为此时能量落差最大,如图4-22所示。但由于θ相和α相基体在成分及晶体结构上相差较大,新相形核和长大需要克服很大的能垒,在时效温度较低的情况下,要完成这一过程比较困难。若先形成某些预沉淀产物和过渡相,如G.P.区、θ″相、θ'相等,则相变所需激活能较低,从动力学角度来说,这样显然比较有利。

图4-22 Al-Cu合金中不同沉淀产物相应的体积自由焓-成分关系曲线
(3)G.P.区的形成与消失
G.P.区在室温即可形成。固溶处理后15min在Al-Cu合金单晶体的摆动法X射线照片上,就会出现二维衍射效应,即在{110}面上出现窄带状的衍射星芒,但必须时效1天后星芒才能变得很清楚。这种带状星芒的出现,说明铜原子在铝晶格的六面体{100}上聚集,如图4-23(a)所示,形成了圆片状的析出区,或称作G.P.区。G.P.区没有独立的晶体结构,而是完全保持母相的晶格,并与母相共格。只是铜原子半径比铝原子小,G.P.区产生一定的弹性收缩,如图4-23所示。

图4-23 G.P.区示意图(a)和Al-Cu合金中GP区的共格应变示意图(b)
G.P.区的厚度只有几个原子,直径随时效温度的变化而有所不同,一般不超过100Å。Al-Cu合金室温时效时G.P.区很小,直径约50Å,密度为1014~1015mm-3,G.P.区之间的距离约为20~40Å。130℃时效15h后,G.P.区直径长大到90Å,厚约4~6Å。温度再高,G.P.区数目开始减少,200℃即不再生成G.P.区。
G.P.区的界面能很低、形核功很小,因而在母相中各处皆可生核,这与部分共格的过渡相不同。
在Cu-2%Be合金经800℃固溶处理后的低温时效中也观察到G.P.区的形成,研究认为过饱和固溶体的冻结空位和空位聚集形成的位错环促进G.P.区的形成。
(4)G.P.区、中间相、平衡相与析出相的关系
将Al-Cu合金在较高的温度下进行时效,G.P.区的直径急剧长大,而且铜原子和铝原子逐渐形成规则的排列,即所谓的正方有序化结构。这种结构的x、y两轴的晶格常数相等(a=b=4.04Å),z轴的晶格常数为7.68Å,一般称作θ″相(或G.P.Ⅱ区)。过渡相θ″在基体的{100}面上形成圆片状组织,厚度为8~20Å,直径为150~400Å。过渡相θ″与基体完全共格,但在z轴方向的晶格常数比基体的晶格常数的两倍略小一些(2cAl=8.08Å),因而产生约4%的错配度。因此,在过渡相θ″附近形成一个弹性共格应变场,或晶格畸变区。这种由过渡相θ″造成的应变场引起的应力场,也可以从电镜照片衬度反差效应上显示出来。如时效时间继续增加,过渡相θ″密度不断提高,使基体内产生大量畸变区,从而对位错运动的阻碍作用不断加大,使合金的硬度、强度,尤其是屈服强度显著提高。
继续增加时效时间或提高时效温度,例如将Al-4Cu合金时效温度提高到200℃、时效12h后,过渡相θ″即转变为过渡相θ'。过渡相θ'属于正方点阵,其中a=b=4.04Å,c=5.80Å,名义成分为CuAl2。
θ'过渡相的晶体取向关系为:(001)θ'//(001)Al,[110]θ'//[110]Al。其大小决定于时效时间和温度,直径约为100~6,000Å,厚度为100~150Å,密度为108mm-3。由于在z轴方向的错配度过大(约30%),造成(010)和(100)面上的共格关系遭到部分破坏,在过渡相θ'与基体间的界面上存在位错环,形成了半共格界面。过渡相θ'与基体局部失去共格,界面处的应力场就会减小。这种应变能的减小,意味着晶格畸变的减小,合金的硬度和强度下降,开始进入过时效阶段。
进一步提高时效温度和延长时效时间,θ'相即过渡到平衡相θ(CuAl2)。θ相属于体心正方有序化结构,因为其与基体完全失去共格关系,故θ相的出现,意味着合金的硬度和强度显著下降。
以上是Al-4Cu合金在时效过程中,过饱和固溶体的各个沉淀阶段,其沉淀序列概括为:
α过饱和→GP区→θ″过渡相→θ'过渡相→θ(CuAl2)稳定相
沉淀过程与合金成分及时效参数有关,而且不同沉淀阶段之间相互重叠、交叉进行,往往有一种以上的中间过渡相同时存在。例如Al-4Cu合金在130℃以下时效时,以G.P.区为主,但也可能出现过渡θ″相和过渡相θ';在150~170℃以过渡相θ″为主;在225~250℃以过渡相θ'为主;高于250℃以后,即以θ相为主,接近退火组织。表4-6列出了不同Al-Cu合金在不同时效温度下的主要沉淀相。
表4-6 不同时效温度下Al-Cu合金沉淀产物

(5)析出相晶核的形成与生长
图4-24表示了Al-4Cu合金在130℃和190℃时效过程中硬度的变化。由图4-24可以看出,G.P.区所造成的硬度增加到一定程度即达到饱和状态,随着θ″相的出现造成硬度的重新上升并达到峰值;当组织中出现θ'相时,硬度开始降低,这种现象称为过时效;如形成了稳定相θ,则合金完全软化。因而,合金在时效过程中随时效时间的增加,其硬度先增加后降低,有一个最佳时效时间使其硬度最高。

图4-24 Al-4 Cu合金时效硬化曲线
时效过程的基本规律总结为:先由固溶处理获得双重过饱和的空位和固溶体;时效初期,由于空位的作用,使溶质原子以极大的速度进行重聚形成G.P.区;随着提高时效温度和增加时效时间,G.P.区转变为过渡相,最后形成稳定相。此外,在晶体内的某些缺陷地带也会直接由过饱和固溶体形成过渡相或稳定相。如表4-7所示。
表4-7 时效硬化型铜合金系形成G.P.区、调幅结构、析出相的特征与固溶度


(6)调幅分解
调幅分解,也称为增幅分解,是指过饱和固溶体在一定温度下分解成结构相同、成分不同两个相的过程。
1)调幅分解的热力学条件
图4-25(a)为具有溶解度变化的A-B合金相图。成分为x0的合金在t1温度固溶处理后快冷至t2温度时,处于过饱和状态的亚稳相α将分解为成分x1的α1和成分x2的α2两相。在t2温度下固溶体的自由能-成分曲线如图4-25(b)所示。曲线上的拐点(d2G/dx2=0)与相图中虚线上的P,Q两点相对应,虚线为不同温度下拐点的轨迹,称为拐点线。合金成分处于拐点线之内(d2G/dx2=0)的固溶体,当存在任何微量的成分起伏时都将会分解为富A和富B的两相,都会引起体积自由能的下降。例如成分为x0的合金,在t2温度时的自由能为G0,分解为两相后的自由能为G1,显然G1<G0,即分解后体系自由能下降,d2G/dx2<0,也就是相变驱动力ΔGv<0。成分在拐点线之外(d2G/dx2>0)的固溶体,例如图中x'0,当出现微量的成分起伏时,将导致体系自由能升高,只有通过形核长大才会发生析出分解。

图4-25 调幅分解的驱动力分析
需要指出,即使固溶体的成分位于拐点以内,也不一定发生调幅分解,还要看梯度能和应变能两项阻力的大小。梯度能是由于微区之间的浓度梯度影响了原子间的化学键,使化学位升高而增加的能量。应变能是指固溶体内成分波动,点阵常数变化,而为了保证微区之间的共格结合所产生的应变能。这两项能量的增值都是调幅分解的阻力。可见,调幅分解能否发生,要由两个因素决定:一是起始成分必须在两个化学拐点之间;二是每个原子应具有足够的相变驱动力ΔG,以克服所增加的阻力。
2)调幅分解的特点
①调幅分解过程的成分变化是通过上坡扩散来实现的。如图4-26(a)所示,首先是出现微区的成分起伏,随后通过溶质原子从低浓度区向高浓度区扩散,使成分起伏不断增幅(富A的继续富A,富B的继续富B),直至分解为成分x1的α1和成分x2的α2两平衡相为止,故此又称为增幅分解。
②调幅分解不经历形核阶段,因此不会出现另一种晶体结构。也不存在明显的相界面。若忽略畸变能,单从化学自由能考虑,调幅分解不需要形核功也就不需要克服热力学能垒。所以分解速度很快。而通常的形核-长大过程,其晶核的长大是通过如图4-26(b)所示的正常扩散(下坡扩散)进行的,且晶胚一旦产生就具有最大的浓度,新相与基体之间始终存在明显的界面。

图4-26 两种固溶体分解方式转变时成分变化
现已发现许多二元系、三元系合金或陶瓷都会发生调幅分解,如Au-Pt、Al-Ag、Cu-Ti、Cu-Ni-Sn、Fe-Ni-Al、SiO2-BaO、SiO2-Na2B8O12等。
由于调幅分解后形成共格型的溶质原子贫、富区,对合金的强度和磁性有一定的影响。例如Al-Ni-Co型永磁合金应用调幅分解可获得高的硬磁特性。
利用调幅分解可以制备超细显微结构的金属材料,材料硬度得到显著提高。郝新江等对Cu-30Ni-25Fe合金,采用变形和热处理的方法获得了不同的晶粒度和失稳分解组织(图4-27),结果表明,合金发生失稳分解后,其硬度和晶粒直径的关系仍符合Hall-Petch关系式,在各种晶粒度下失稳分解后的硬度均大于固溶态,但当分解后的两相尺寸与晶粒尺寸相比约小两个数量级时,失稳分解的相界强化作用消失。

图4-27 Cu-30Ni-25Fe合金时效后的失稳分解组织
(7)晶界反应析出
除过饱和固溶体的析出相是在晶粒内部形成的,随着析出过程的进行,合金基体的溶质浓度连续减少外,平衡相在晶界附近析出的同时且基体溶质的平衡浓度较低时,均可发生过饱和固溶体的分解,上述两种情况分别称为连续析出和不连续析出。实际上这属于固态相变中的胞区分解,又叫不连续相变的三种类型之一的胞区沉淀(另两种为共晶凝固、共析分解)或胞状析出。
胞区沉淀与共析分解的机制很相似。其差别主要在:共析分解产物中约两相都和母相结构不同,而胞区沉淀产物的两相中有一相和母相结构不同,另一相和母相结构相同,但具有平衡相的成分,一般说来它和母相也不共格。胞区分解之初,新相多以非均匀成核的方式在母相的晶界上出现,但是成核的具体细节则可能因系统而异。
对于胞区沉淀反应α'→α+β的成核过程,史密斯描述为:最初一个β相核心在过饱和母相α'中晶粒1与晶粒2之间的界面上靠近晶粒1的一侧生成。从形核势垒来考虑,此核心一定与晶粒1有较好的取向匹配关系。若β相中溶质原子浓度高于母相,那么β核心附近便出现了溶质原子贫化,这便是平衡α相出现的条件。β核心连带着旁边的平衡α相有两种选择,要么长入晶粒1,要么长入晶粒2。相比之下,长入晶粒2更为有利,因为晶界提供了一个很好的扩散通道,而且晶界随新相的长大而推移,构成了永不消失的反应前沿。这一过程的示意见图4-28。它可以解释为什么胞区沉淀相总是长入界面一侧的晶粒,而且是长入与新相匹配较差的晶粒。

图4-28 胞区沉淀在母相晶界上形核并随界面推移而长大的示意图
胞区分解是受溶质原子的长程扩散控制的。产物的分散度,例如片状组织的片间距则取决于扩散路径的长度与总界面面积的大小这两个因素的竞争与协调。大的片间距可使总界面能下降,但维持转变所需的原子扩散路程要相应地增大。小的片间距可以使扩散路程缩短,但总界面能却要增大。
铜合金中的胞区分解,特别是固溶后进行形变加工的铜合金的胞区沉淀又称为不连续析出,这是一种较特殊的时效析出情况,它与再结晶相互关联,因此又称为晶界再结晶反应,是一种特殊的晶界反应。晶界反应析出的出现导致合金显著软化,对工业用铜合金而言避免晶界反应析出的出现是非常重要的。图4-29是Cu-3%Ti合金的晶界反应析出TEM特征,具有明显的胞状组织特征。Cu-Be合金的时效也具有晶界反应析出机制。

图4-29 Cu-3%Ti合金的晶界反应析出TEM像(375℃,104min时效)
(8)晶体缺陷对过饱和固溶体分解方式的影响
晶体缺陷在过饱和固溶体分解中具有重要影响,对第二相析出方式,特别是对形核过程的影响要高于对第二相核心长大过程的影响。根据第二相析出时合金基体溶质成分变化和晶格常数变化的连续性通常将时效析出分为连续析出和不连续析出两类。
①连续析出 连续析出是过饱和固溶体最重要的析出方式,其基本特点是析出反应在整个体积内各部分均可进行。另外,各析出相晶核长大时,周围基体的浓度连续降低,其点阵常数也发生连续变化,而且在整个转变过程中,原固溶体基体晶粒的外形和位向基本保持不变。
根据显微组织特征,连续析出又可分为普遍析出和局部析出。
普遍析出:在整个固溶体中普遍发生析出并析出均匀分布的析出产物。通常,普遍析出对力学性能有利,它使合金具有较高的疲劳强度,并减轻合金晶间腐蚀和应力腐蚀敏感性。
局部析出:在普遍析出前,在晶界、滑移带、夹杂物界面及其他晶体缺陷处优先形核,使该地区较早地出现析出相质点。局部析出往往是在过冷度较小(即时效温度较高)的条件下发生的,随着过冷度的增加,析出驱动力增大,晶界或其他晶体缺陷处将失去优先形核的优越性,从而有利于普遍析出。局部析出无论对力学性能还是耐蚀性能均有不利影响,要尽量避免。
②不连续析出 不连续析出可用图4-30示意说明,将成分的α相过冷至t1温度,首先在晶界上形成一小颗胞状析出产物,随后向α基体中长大,如图4-30(b)所示。胞状析出物是由α相和β相交替组成,通常为片层状。β片的成分几乎总是平衡成分,以Cβ表示;α相的成分为
,一般稍大于平衡成分α0。胞状区与基体间有明晰的界面,在界面处α相的成分发生突变,即由基体
突然变化为胞状区的
,因而界面处α相的晶格常数也呈不连续变化。

图4-30 不连续析出示意图
不连续析出时,析出胞与基体间的界面是非共格界面,析出胞内的α片和β片都与原始α基体形成非共格界面。析出胞大多在晶界处形核,故不连续析出又称为晶界反应。析出胞形核后,胞壁(晶界)会向毗邻的一个原始晶粒内部推进[图4-30(b)],只要反应的同时不发生连续析出,则各析出胞会继续长大,直到相互接触为止。
不连续析出是时效硬化铜合金中的一个较普遍的现象,在Cu-Be、Cu-Ti、Cu-In、Cu-Mg、Cu-Sb、Cu-Cd、Cu-Ag、Cu-Ni-Co、Cu-Ni-Sn、Cu-Ni-Al等合金系中均存在。一般认为,不连续析出所形成的粗大析出物对强化不利,会削弱晶界,应尽量避免。
析出时可能只发生连续析出,也有可能不连续析出和连续析出在同一合金中同时发生。合金在析出时显微组织的变化,可能有不同的形式,可用图4-31来说明。

图4-31 合金时效析出时显微组织变化的示意图
(a)固溶组织;(b)连续析出;(c)析出相粗化;(B)连续析出+晶界无沉淀带;(d)不连续析出(胞状沉淀);(e)胞状组织;(D)连续析出+不连续析出;(E)均匀沉淀组织+胞状组织
图4-31中(a)→(b)→(c)表示连续析出时显微组织的变化;(a)→(B)→(c)也是连续析出的情况,但由于发生局部析出而出现了晶界无沉淀带。(a)→(d)→(e)表示不连续析出时组织的变化,(a)→(D)→(E)则代表同时发生连续析出和不连续析出时显微组织的变化。
4.1.4.2 时效析出对性能的影响
合金经过固溶处理后,所得过饱和固溶体在随后进行的时效处理过程中,便会依照上述析出沉淀过程发生第二相的析出,其显微组织和性能(如电阻率、强度和硬度、塑性等)也随之发生相应变化。
一般情况下,时效处理会使合金的强度、硬度升高,但塑性和抗蚀性下降。其强化效果决定于合金的成分、固溶体的本性、过饱和度、分解特性和强化相的本性等,因而有的合金系时效强化效果较大,有的合金系时效强化效果较小。
对同一成分的合金而言,影响其时效强化效果的主要工艺参数有固溶加热温度和冷却速度、时效处理温度和时间、加热速度以及时效前的塑性变形等。
(1)电阻的变化
电磁学古典理论认为金属中电流的产生是其中自由电子在外电场作用下定向漂移的结果,自由电子在运动过程中与晶格上原子实体相撞,造成对电子定向运动的破坏,从而产生电阻和电流热效应。依据古典电子论,金属电导率可由以下公式表示:
(4-9)
式中,为金属电导率;n为金属中自由电子(价电子)数密度;λ为自由电子平均自由程;e、m、V分别为自由电子的电量、质量和平均运动速度。
古典电子论可以很好地解释许多物理现象,如欧姆定律等,但它在几个问题上遇到了无法解决的困难。最大的困难是实验测得的电子平均自由程比古典电子论预计值要大一个数量级,因此必须引入量子力学和固体理论来描述金属中的导电过程。由能带理论导出的金属电导率表达式为:
(4-10)
式中,τF为费米面附近电子两次散射的间隔时间;为单位体积中参加导电的电子数密度。由于参加导电的电子是靠近费米面的电子,只是价电子的一部分,因此这里的
是小于公式(4-9)中
值的。
由金属电子理论可知,绝对零度时,当电子波通过理想晶体点阵时,将不产生散射,此时电阻为零。在晶体点阵完整性遭到破坏的地方,电子波会受到散射,这就是电阻的产生原因。由温度引起的晶格离子热振动、晶体中异类原子、位错、空位、晶界和相界均会使理想点阵的周期性遭受破坏,降低金属的导电性。合金元素对铜合金导电性的影响主要包括两方面,首先是固溶于铜基体中的合金元素将引起铜合金的导电率下降,固溶原子对铜合金电导率的影响是很复杂的,但主要影响是异类原子引起铜基体晶格发生畸变而增加对电子散射作用的结果。在低固溶条件下,电阻率符合马提申(Matthissen)定则:
(4-11)
式中,代表固溶体的电阻率;
代表纯铜的电阻率,它仅是温度的函数,当
时,
;
为固溶体中溶质元素的浓度;ζ为单位溶质元素固溶体残余电阻。由此公式可见,固溶合金元素对合金导电性的影响与其浓度呈正比,这与试验结果图4-32相一致,因此固溶元素对铜合金的导电性影响较大。

图4-32 合金元素对铜合金导电性的影响
加工硬化会增大铜晶格的畸变程度,同时冷加工可改变铜原子间结合力并导致原子间距增大,因此加工硬化后铜合金电导率低于退火态材料的电导率。细化晶粒后的铜合金和铜基原位复合材料中,晶界(界面)引起的晶格畸变比较严重,材料电导率也因此有所下降。总体来看,位错、晶界和界面的存在对铜合金导电率影响不是很大。
在时效强化和弥散强化型铜合金中,通常情况下,时效强化和弥散强化型铜合金电导率可近似由数相电导率的算术相加而求得。因此,时效、弥散强化型铜合金中,当第二相体积分数较小时,如能通过生产工艺控制析出相尺寸使之远远偏离电子平均自由程,则材料往往能实现较高电导率。时效强化铜合金中,析出相与基体相互作用而引起晶格畸变,由此导致的导电性的变化,可由下式表示:
(4-12)
式中,为铜基体的电导率,
为铜合金的电导率,f为第二相颗粒的体积百分数,
为第二相颗粒的电导率,
。对于时效强化铜合金,
,
,代入上式可得:σ=98.5%σ0。因此,每1%体积分数的析出相颗粒对铜合金导电率的影响在1.5%IACS以下。表明析出强化对材料的导电率的影响较小。然而,当析出相颗粒的尺寸在1nm数量级时,也即颗粒尺寸达到与电子波长同一数量级时,由于电子波在此析出相上发生附加散射,对电子产生最大的散射作用,此时合金的导电率会发生明显下降,将对材料导电性产生较大的影响,大约在10%~15%IACS。
对时效硬化铜合金而言,固溶和时效处理可促进铜合金基体溶质原子以第二相形式析出,合金的电阻率随之下降。图4-33为Cu-2%Be-0.2%Co合金G.P.区的形成、比电阻的变化与添加微量元素的关系,图中B-未添加,3Z、3M和3E分别添加类0.1at.%的Zn、Mg和Ce。4种合金经780℃水冷固溶处理后,分别进行250℃和350℃的等温时效处理后的显微硬度和比电阻(R/R0)的变化。250℃时效的4种合金的比电阻均先增加到极大值后再逐渐下降,研究表明合金时效前期比电阻的增加与G.P.区的形成有关,G.P.区越大相同条件下传导电子的波长越大。对不同含量的Al-Zn合金研究表明,每个G.P.区对电子的平均散射能随G.P.区的尺寸增加而单调增加,另外G.P.区的数量随析出相的粗化而逐渐减少。两者综合作用在某个时效时间导致电阻值出现极大值。

图4-33 Cu-2%Be-0.2%Co合金GP区的形成、比电阻变化与添加元素的关系
(图中B-未添加,3Z-0.1%Zn(体积),3M-0.1%Mg(体积),3E-0.1%Ce(体积))
(2)析出强化机制和强韧化措施
①概述 金属与合金的强化主要是其显微组织和化学成分(溶质、杂质原子)阻碍位错运动引起的。因此,对位错运动的阻碍会导致位错在障碍物(如各种界面、第二相、偏析等缺陷等)前堆积导致应力集中产生,发生局部开裂出现微裂纹,微裂纹的传播发展导致材料宏观断裂。其强韧化措施主要在于通过调控金属的显微组织阻止位错的运动,从而避免在材料特定场合产生应力集中。
时效析出型合金的强化机制可采用的主要有固溶强化、加工硬化、析出强化和颗粒弥散强化、细晶粒和超细晶粒强化等,断裂主要与后三种机制有关。上述几种强化机制在合金中不可避免存在若干机制的组合。
固溶强化对固溶度较高的合金具有重要意义,溶质和溶剂原子尺寸差越大,固溶效果越大。对时效析出合金而言,过饱和固溶体分解后产生时效硬化,固溶体基体残留的溶质原子的固溶强化效果较小,很多场合难以利用。而加工硬化与时效析出组合的利用对强化效果提高更有效。
时效硬化合金的强化以析出强化与粒子弥散强化为主,粒子大小、粒子间距和共格程度、颗粒强度等对其强化效果均具有重要影响。
②切过强化 切过强化主要发生在G.P.区尺寸较小且与基体共格,以及微细析出粒子与合金基体保持共格的情况下。位错遇到上述可变形G.P.区或微细析出粒子,可沿滑移面切过,使之同基体一起产生变形,由此也能提高屈服强度。这是由于质点与基体间晶格错排及位错线切过第二相质点产生新的界面需要做功等原因造成的。这类质点的强化效果与粒子本身的性质、数量及其与基体的结合情况有关。Courtney将该类分为三部分:共格强化τcoh、弹模强化τGp和化学强化τchem。
共格强化是由于析出粒子与基体晶格参数不匹配引起的,其表达式为:
(4-13)
式中,εcoh为析出粒子与基体共格晶面的错配度,;ap和am分别为共格界面上粒子和基体晶格常数;b为位错柏氏矢量;f为粒子体积分数;r为粒子半径。
弹模强化是由于析出粒子与基体剪切弹性模量不一致引起的,其表达式为:
(4-14)
式中,εGp为析出粒子与基体剪切弹性模量的差值,εGp=Gp-Gm,Gp和Gm分别为粒子和基体的剪切弹性模量。
化学强化由于析出粒子与基体化学成分不同引起的,其表达式为:
(4-15)
式中,γs为析出粒子与基体相界面能;G为相界面的剪切弹性模量。
位错切过变形粒子的强化效应总和τdp为:
(4-16)
③绕过强化 当析出粒子尺寸较大或强度较高,钉扎在位错滑移面上而不能被位错切过时,根据位错理论,位错线只能绕过不可变形的第二相质点,为此,必须克服弯曲位错的线张力。塑性变形时,位错线不能直接切过第二相粒子,但在外力作用下,位错线可以环绕第二相粒子发生弯曲,最后在第二相粒子周围留下一个位错环而让位错通过。位错线的弯曲将会增加位错影响区的晶格畸变能,这就增加了位错线运动的阻力,使滑移抗力增大。该种强化机制又称为奥罗万(Orowan)强化机制。
弯曲位错的线张力与相邻质点的间距有关,故含有不可变形第二相质点的金属材料,其屈服强度与流变应力决定于第二相质点之间的间距。绕过质点的位错线在质点周围留下位错环。随着绕过质点的位错数量增加,留下的位错环增多,相当于质点的间距减小,流变应力就越高。对不可变形的第二相质点,当体积分数一定时,减小质点尺寸,则质点数量增加,间距减小,强度提高。图4-34为奥罗万强化示意图。

图4-34 奥罗万强化示意图
(a)滑移面上位错线与不可变形颗粒相遇;(b)位错线弯曲;(c)位错线绕过,继续在滑移面上运动,在每个粒子周围留下一个位错环
位错弯曲的最大剪切强度τB,表达式为:
(4-17)
式中,(L-2r)为粒子间距;G为基体的剪切弹性模量;b为柏氏矢量。可以看出,(L-2r)越大,奥罗万强化强化效应越大,因此,析出粒子越分散,强化效果越大。
④细晶强化 细晶强化是在浇铸时采用快速凝固措施或采用热处理手段来获得细小的晶粒,也可以加入某种微量合金元素来细化晶粒。晶粒尺寸减小,合金强度提高。晶粒细化引起的界面增多对导电率影响不大。所以细晶强化也成为铜合金主要强化手段之一。一般情况下,多晶体强度及其晶粒尺寸间关系符合Hall-Petch公式[19]:
σs=σi+kd1/2 (4-18)
式中,σs为多晶体的屈服强度;σi为晶格摩擦力;k为常数;d为平均晶粒直径。可见,通过添加化学元素或采用冷变形+再结晶退火工艺细化加工硬化铜合金晶粒后,材料强度可以得到提高。细晶强化的突出优点是在提高材料强度的同时可以提高材料的塑性。这是由于晶粒细化后,材料变形时晶界处位错塞积所造成的应力集中可以得到有效缓解,推迟了裂纹的萌生,材料断裂前可以实现较大的变形量。细晶粒特别是超细晶粒的调控和制备技术也正是由于这一优点而得到了广泛应用。
4.1.4.3 析出强化型合金的热处理方法及影响因素
析出强化型合金的热处理方法主要一般时效处理和形变时效两大类。一般时效热处理包括固溶处理+时效处理,形变时效热处理是把时效强化和加工硬化互相叠加的处理方法,即热机械处理。
(1)一般时效热处理
①固溶加热 固溶处理由加热和淬火冷却两部分组成。固溶加热温度根据合金平衡相图确定,通常在相图的固相线与固溶线之间温度进行。例如铍青铜(Cu-1.9%Be-0.2%Ni或Co)的固溶温度为790℃,固溶时间按照材料壁厚1h/25.4mm确定。固溶温度越低,固溶越不充分。要特别注意固溶温度不要高于共晶温度。固溶加热过程合金局部熔化和吸入氢是合金塑性和韧性变差的部分原因。
②淬火冷却 合金固溶加热后进行淬火冷却是获得过饱和固溶体的重要工序,通常浸入室温水中进行快速冷却。合金加热后不进行快速冷却也能在冷却过程中避免第二相析出的合金称为易固溶淬冷合金。合金的淬冷特性受其均匀化固溶处理温度和微量添加合金元素的影响。图4-35为Sn添加量对Cu-Cr合金的T-T-P曲线的影响,可以看出,添加微量Sn对Cu-Cr合金850℃和500℃等温析出转变T-T-P曲线的鼻尖温度并没有改变。添加不同Sn含量500℃鼻尖温度下的析出孕育期基本不变,而对850℃鼻尖温度下的析出孕育期影响较大,添加少量Sn明显抑制Cr相高温等温析出。Cu-Cr合金等温析出转变T-T-P曲线具有850℃和500℃两个鼻尖易析出温度区与Cr在铜中的固溶度变化较大有关。研究发现,Cu-(0.3%~1.5%)Cr合金1,000℃均匀化处理后,其实际固溶度为0.37%~0.41%Cr,因此Cr含量在0.56%以上的Cu-Cr合金固溶处理后合金基体中总是存在一定数量的残留Cr质点,850℃高温下易作为过饱和固溶体分解析出Cr相的形核部位,容易得到粗大的析出相。因此,Cr含量较高的Cu-Cr合金时效处理时要快速冷却避开850℃鼻温区,而要选择过冷度较大的500℃鼻温区附近进行时效,以获得微细均匀析出Cr相。

图4-35 Sn添加量对Cu-Cr合金的T-T-P曲线的影响
③时效处理 过饱和固溶体分解是得到G.P.区强化还是中间相强化主要是由不同合金系分别选择适合的时效温度和时间来决定的。低温时效和高温时效的区别在于前者形成G.P.区而后者形成中间相。与铝合金不同,铜合金在室温下不能发生自然时效。一般工业时效以高温时效为主。除特殊的合金系外,要采取措施避免晶界反应时效产生粗大析出相,以及过时效产生较大粒子间距的奥罗万强化机制的出现。对有些合金在G.P.区和中间相共存时效,以及存在G.P.区向中间相转变的析出过程,可以进行第一阶段低温时效形成G.P.区,第二阶段形成中间相的两步时效或分级时效(two-step ageing,split ageing)。国内外对铝合金的分级时效研究较详细,国内对铜合金的分级时效研究也相继得到清华大学、中南大学、南昌大学、河南科技大学、上海理工大学等高校、北京有色金属研究总院等研究机构以及中铝洛阳铜业等大型企业的很多关注,其中河南科技大学高性能铜合金创新团队和上海理工大学电功能材料研究所在时效强化电子铜合金的形变-分级时效(复合时效)等方面做了大量工作,取得一些研究成果。
表4-8为常用时效强化铜合金的强化相分类与时效组织示意图。CuSnMg合金的时效强化以不连续析出强化为主,阻碍其强度的进一步提高。
表4-8 常用时效强化铜合金的强化相分类与时效组织

(2)微量元素对时效析出的影响
时效析出强化的基本原理是,在铜中加入溶解度随温度降低而明显减小合金元素,通过高温固溶处理形成过饱和固溶体,固溶体的强度与纯铜相比有所提高。而后通过时效,使过饱和固溶体分解,合金元素以沉淀相的形式析出弥散分布在基体中。沉淀相能有效地阻止晶界和位错的移动,从而大大提高合金强度。产生析出强化的合金元素应具备以下两个条件:一是高温和低温下在铜中的固溶度相差较大,以便时效时能产生足够多的析出相;二是室温时在铜中的固溶度极小,以保证基体的高导电性。按这一原理开发的高强高导铜合金有Cu-Cr、Cu-Zr、Cu-Cr-Zr、Cu-Fe、Cu-Fe-Ti、Cu-Ni-Be等系列,而以Cu-Cr、Cu-Zr系合金的发展最为迅速,应用最为广泛。
析出强化型合金的屈服强度不仅与析出相粒子的种类、大小、数量有关,还同粒子与基体的界面结构有关。通过优化固溶-时效工艺,形成合适的析出相组态,即可获得不同强度级别的合金。固溶体脱溶过程中,铜基体中溶质浓度减小,成分接近纯铜,基体电阻率急剧下降;同时,析出粒子的出现会对电子产生附加散射,增大合金电阻率,但时效析出的第二相引起的点阵畸变对电子的散射作用要比铜基体中固溶原子引起的散射作用小得多,因而在总体上,脱溶过程后合金能获得较高的导电率。
在铜合金中,为产生时效析出强化效果而加入的元素有Ti、Co、P、Ni、Si、Mg、Cr、Zr、Be、Fe等。其中以Cu-Be合金最为著名,有关其时效强化的研究也起步很早。时效析出强化的优点是在大幅度提高材料强度的同时,对电导率损害很小,通过分析几十种集成电路用铜合金材料成分及性能,引入的强化相对强度与电导率的综合影响因数见表4-9第5列数据,其数值是强化相元素所引起的强度升高与电导率下降数值之比。此因数的物理意义为引入析出强化相,每提高1MPa强度所引起铜合金电导率下降的数值。可以看出当各种强化相在铜中析出时,使铜合金抗拉强度每升高1MPa对电导率的降低仅为0.03%~0.08%IACS。
表4-9 形成强化相元素对铜合金强度和电导率综合影响

(3)形变时效热处理
形变时效热处理,又称为加工热处理,简称TMT或TMP(thermomechanical treatment or processing),是一种值得重视的热加工技术。
TMT的加工温度选择适当,在析出粒子存在或开始析出的情况下进行加工,可以获得均匀分布的微细析出相粒子与稳定的位错结构组态共存,在提高强度的同时获得优良的塑韧性。基于对时效硬化铝合金开发的各种形变时效热处理工艺曲线示意图如图4-36所示。图中,(a)的加工温度很高而(b)为冷加工,这两种TMT处理方法常用。(c)的加工温度与高温时效温度相同,称为温加工,在形变过程中开始析出。(d)和(e)为低温时效后进行形变,分别为冷加工和温加工。(f)为低温时效后进行温加工变形,加工温度与高温时效相当。(g)为固溶处理后在较高温度同时进行温加工和形变与时效析出。(h)为Al-Zn-Mg合金的TMT曲线实例。铜合金一般采用(b)和(d),特别是(b)的应用最为广泛。

图4-36 各种形变热处理示意图
TF—熔化温度;t.a.—室温;S—固溶处理;P—热加工/高温形变;T—水冷淬火;A—时效处理;A1—低温时效/一次时效;A2—高温时效/二次时效;H—室温加工/冷加工;Hc—中间温度加工/温加工
佐治等研究了Cu-4%Ti合金的形变时效热处理工艺,采用固溶处理-冷轧-时效工艺,研究了变形量、时效温度与时间不同组合对其显微组织的影响,得到四种不同的组织形貌。主要结论如下。
①变形量、时效温度与时间的不同组合分别得到四类组织:具有晶格缺陷的调幅结构、微细的两相混合组织、不连续析出的胞状组织、魏氏组织。
②加工后时效初期产生包含位错、层错和微观孪晶等晶体缺陷的调幅结构,富含Ti原子的亚稳相周期排列。这种组织强韧性优良。
③微细两相混合组织由1μm以下尺寸的微细α-Cu再结晶晶粒与三叉晶界上析出的微细β'-Cu3Ti粒子组成。这种组织在高变形量合金,约95%以上的区域均可观察到,在中等变形量合金的变形带中可形成。微细两相混合对加工材中位错胞的形成具有重要作用。低温时效初期,富Ti区的形成抑制了再结晶,后期平衡相β'-Cu3Ti的不均匀析出促进附近富集区的溶解,从而促进再结晶的进行。
④不连续析出的胞状组织在中、低变形量的加工材经较低的低温时效形成。形变促进了不连续析出相的形核与长大。变形量越大,两相混合组织对基体的分割作用增强,胞状组织形成趋势降低。
⑤魏氏组织在低变形量的加工材经750℃时效形成。