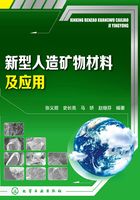
2.2 煤矸石灌浆材料
2.2.1 问题的提出
我国每年各类工程上注浆用材量极其巨大,以煤矿为例,每年一个大型矿用于注浆堵水的水泥就超过万吨。如果能把煤矸石用作注浆材料,无疑仅节约水泥一项就能获得巨大的经济效益。河南理工大学多年来一直从事煤矸石灌浆材料的研究,2003年该研究又列入河南省科技攻关计划,攻关题目是“煤矸石灌浆材料的研制”(0324210052)。项目下达后,现场试验点选在了永城煤电(集团)公司。在矿山的采掘过程中,该公司主采的二2煤层经常遇到一些破碎区、不良地质条件区,需对其进行注浆加固,还需对易燃区进行注浆防灭火,对受到二2煤层底板承压水威胁的区域进行注浆加固底板。以前的注浆材料多采用水泥浆液,成本较高。为了有效地解决注浆问题,节约注浆成本,急需开发一些利用工业废渣的廉价新型注浆材料。根据当地的条件,废渣有粉煤灰与煤矸石,为此,课题研究时扩大了其研究范围,改为“新型注浆材料的研发与应用”。项目对粉煤灰、煤矸石等一些工业废渣进行了全面系统的测试,优化注浆参数,开发出了多种新型廉价的注浆材料,提高了加固效果。
煤矸石根据来源,可分为露天开采剥离及采煤巷道掘进和开拓岩巷排出的矸(占总矸量的45%)、采煤过程中选出的普矸(占总矸量的35%)、选煤厂产生的选矸(占总矸量的15%)。煤矸石是多种矿岩组成的混合物,属沉积岩。主要岩石种类有黏土岩类、砂岩类、碳酸盐类和铝质岩类。黏土岩中主要矿物组分为黏土矿物,按其成分不同可分为高岭岩、伊利石、膨润土、高岭黏土等,还有植物化石、有机质、碳质等;砂岩类矿物多为石英、长石、云母,此外还含有植物化石和菱铁矿结核等;碳酸盐类的矿物组成为方解石、白云石、菱铁矿,并混有较多的黏土矿物、陆源碎屑矿物、有机物、黄铁矿等;铝质岩类均含有高铝矿物:三水铝矿、一水软铝石、一水硬铝石,还有石英、玉髓、褐铁矿、白云母、方解石等。
煤矸石的化学成分复杂,所含元素可以多达数十种,氧化铝和氧化硅是主要成分,如砂岩矸石SiO2含量高达70%,铝质岩石Al2O3含量大于40%,钙质岩石的CaO含量大于30%;还有氧化铁(Fe2O3)、氧化钙(CaO)、氧化镁(MgO)、氧化钠(Na2O)、氧化钾(K2O)、磷和硫的氧化物(P2O5、SO3)及微量的稀有金属元素(如钛、钒、钴、镓等的氧化物)[2,3]。
试验所用煤矸石取自某煤业公司矸石山上的白矸、普矸及洗煤厂产生的选矸,各取等量混合后放入球磨机,球磨1h后取出。激光粒度分析仪测试其粒度分布如图2-1所示。煤矸石化学成分测定结果见表2-1和图2-2。

图2-1 煤矸石粒度分布图

图2-2 煤矸石XRD图
表2-1 煤矸石的主要化学成分 单位:%

由表2-1可以看出此种煤矸石样品烧失量达42.82%,含碳量很高,如果直接加入水泥作为掺合料将大大降低浆体的固结强度,必须经过燃烧降低含碳量。另外,两种主要成分为SiO2和Al2O3,且CaO含量较低,总体化学成分含量与粉煤灰类似,同属于CaO-SiO2-Al2O3系统。
2.2.2 煤矸石的活性概述
煤矸石要想掺入水泥中作为注浆材料必须具有活性SiO2和活性Al2O3。无机材料的化学反应活性的高低主要取决于它的结构稳定性。一般而言,微观结构缺陷多、晶体的晶格畸变多或呈无定形状态的材料,其化学反应活性高。从晶体化学观点来看,即要求混合材料有裂解或可裂解的硅氧四面体骨架,以及可以和硅氧四面体分离的铝氧四面体[4]。
煤矸石可作为水泥掺合料用于注浆材料,其原因在于黏土类煤矸石矿物,加热到一定温度(一般为700~900℃)时,原来的结晶相分解破坏,变成无定形的非结晶体,使煤矸石具有活性。活性的大小和煤矸石的物相组成和煅烧温度等有关[5]。
(1) 矿物组成对煤矸石活性的影响 研究表明,煤矸石中的黏土类矿物和云母类矿物的受热分解与玻璃化是煤矸石活性的主要来源。未燃煤矸石中黏土类矿物占有相当大的比例,此类煤矸石中的高岭石矿物在煅烧过程中发生分解,生成了无定形的SiO2和Al2O3,这是煅烧煤矸石具有活性的根本原因。因而,通过物理和化学的方法使煤矸石中矿物的晶体结构发生畸变,可提高其化学反应活性,使之成为有用的胶凝材料。
(2) 煤矸石活性与内部结构的关系 在自然界中,煤矸石以新鲜矸石(风化矸石)和自燃矸石两种形态存在,这两种矸石在内部结构上有很大的区别,因而活性的表现程度也不一。
新鲜矸石(风化矸石)是指经过堆放,在自然条件下经风吹、雨淋,使块状结构分解成粉末状的煤矸石。该种煤矸石由于在地表下经过若干年缓慢沉积,其结构的晶型比较稳定,其原子、离子、分子等质点都按一定的规律有序排列,活性也很低或基本上没有活性。
自燃矸石是指经过堆放、在一定条件下自行燃烧后的煤矸石,自燃矸石一般呈陶红色,又称红矸。自燃矸石含碳量大大减少,氧化硅和氧化铝含量较未燃矸石明显增加,与火山渣、浮石、粉煤灰等材料相似,也是一种火山灰质材料。自燃矸石的矿物组成与未燃矸石有较大差别,原有高岭石、水云母等黏土类矿物脱水、分解、高温熔融及重结晶而形成新的物相,如赤铁矿等,尤其生成的无定形SiO2和Al2O3,使自燃煤矸石本身就具有一定的火山灰活性。
2.2.3 煤矸石活性激发方法及试验
自燃矸石中由于存在无定形的SiO2和Al2O3,具有一定的火山灰活性,属于活性混合材料,常温下与水、石灰化合反应,生成不溶、安定的硅铝酸钙盐。一般而言,自燃矸石通过机械磨细及超细磨来激发其活性。实际上大量存在和未能充分利用的还是未燃矸石,通过X射线衍射结构分析得知,此类矸石中几乎没有活性的SiO2和Al2O3。为此,如何在外界条件作用下破坏其完整晶体结构,使SiO2和Al2O3以活性组分存在成为激发煤矸石活性的关键。常用的方法有热活化、机械活化、化学活化及复合活化(多种活化方法的优化组合),其中热活化及复合活化最为普遍和重要。
(1)热活化 煤矸石结构中的SiO2、Al2O3通常以[SiO4]四面体和[AlO4]四面体存在,Si—O键和Al—O键结合能很大,结晶程度很高,甚至在其内部结构某个区域形成SiO2和Al2O3富集区,覆盖在矸石颗粒表面,形成保护层,使颗粒内部本来不多的可溶性SiO2、Al2O3很难溶出。因此,煤矸石若作为灌浆材料,必须采取措施充分激发其潜在的火山灰活性。
针对煤矸石的特性,提高其活性须从以下3方面入手:
1)增加煤矸石中玻璃体的含量,尤其是玻璃体中活性SiO2和Al2O3的含量。
2)破坏表面和
网络构成的保护层,使内部更多的可溶性活性SiO2、Al2O3释放出来。
3)将网络聚集体解聚、瓦解,使[SiO4]、[AlO4]四面体形成的三维连续高聚合度网络解聚成四面体短链,然后进一步解聚成[SiO4]、[AlO4]等单体或双聚体活性物,为下一步反应提供活化分子。
热活化的试验如下:煤矸石经破碎成一定粒度后,置于炉中煅烧,然后取出物料立即急冷,参照廉慧珍等提出的活性率Kα测定实验方法[6],可测得活性SiO2、Al2O3含量。低温煅烧试验流程如图2-3所示。因煤矸石活性受煅烧温度、保温时间、升温速度等多方面因素影响,试验中煅烧温度T所示选择700℃、750℃、800℃、850℃;而保温时间t则选择0.5h、1h、1.5h、2h,并保持升温速度在7.9℃/min左右,安排见表2-2,结果见表2-3。

图2-3 低温煅烧试验流程图
表2-2 低温煅烧煤矸石煅烧制度全分析试验安排

表2-3 不同煅烧制度下煤矸石的活性率 单位:%

结合实际情况,选取活性率Kα作为本次试验的最终考核指标。可用下式计算:
(2-1)
式中,Kα为活性率;ω'为在饱和石灰水中反应的SiO2和Al2O3的总量;ω0为原样初始成分全分析中的SiO2和Al2O3总量。
图2-4所示为活性率Kα与煅烧温度的关系,图2-5所示为活性率与保温时间的关系。从表2-3、图2-4和图2-5可看出,煅烧后的煤矸石活性均比没煅烧的要高,当煅烧保温时间在0.5~2h时,随煅烧温度提高,低于800℃时煤矸石的活性率Kα逐渐增大,而大于800℃时在逐渐减小;当低于750℃时,随煅烧保温时间的延长,Kα逐渐增大;在850℃时则呈现相反的变化,随煅烧保温时间延长,Kα却逐渐在减小;在800℃温度点处则表现出保温时间1h时煤矸石的Kα最高,达63.32%。究其原因,煤矸石中含有大量的高岭石矿物,当加热到550~710℃时,煤矸石含水高岭石矿物中的羟基结构水则缓慢脱除而分解为易反应的无水偏高岭土及部分可溶性SiO2和Al2O3而产生活性,反应式如下:

图2-4 活性率Kα与煅烧温度的关系

图2-5 活性率Kα与保温时间的关系
至800~1000℃时残余晶格水全排除,但脱水后的产物在925℃时就会开始转化为新的物相——铝硅尖晶石、似莫来石,最终产物是莫来石和方石英等,结构稳定性提高,导致活性降低甚至失去,反应方程式如下:

根据以上分析,在煅烧过程中,煤矸石微粒中的原子在高温下产生剧烈的热运动,结果使硅氧四面体和铝氧三角体只能形成短链,不可能充分地聚合成长链,即熔体中的硅氧链和铝氧链具有较多的断裂点,相当于具有较多的自由端。而且在煅烧过程中,煤矸石也会自行生成一些活性矿物,如硅酸一钙(CaO·SiO2)、硅酸二钙(2CaO·SiO2)等,这样煅烧过后矸石就会具有较高的活性。800℃、1h煅烧制度下矸石的XRD图谱(图2-6)分析证明了经过煅烧后煤矸石中确实有活性矿物存在;同时还可看出,若煅烧温度过高或保温时间过长,由于煤矸石被烧死(过烧),烧渣中有一部分γ-Al2O3(有很强的活性)转变成α-Al2O3,无定形SiO2则转变成其他稳定晶体,导致Kα减小。同样,若煅烧温度过低或保温时间过短,却又不能充分地激发其活性,Kα也较低。综合以上试验结果及理论分析知,采取煅烧温度800℃、保温时间为0.5~1h的煤矸石活性激发效果最好。

图2-6 800℃、1h煅烧制度下矸石的XRD图谱
(2)机械活化 机械活化是指把物料置在粉碎设备中通过研磨介质在高速旋转的情况下给料以冲击,使其与固体碰撞或引起颗粒间相互碰撞,物料颗粒在粉磨过程中因在外力作用下,克服内聚力被粉碎。从外观上看,颗粒变小,比表面积增大,事实上内部结构还会产生类似晶体缺陷等一系列物理、化学性能的变化。它具体有以下两个方面作用:一方面是将粗大多孔的玻璃体粉碎,可解除玻璃颗粒黏结,改善其表面特性,而活性较好的球形颗粒由于很难磨碎保持了原来的形状,由此可以改善其颗粒级配,减少配合料在混合过程的摩擦,并可以提高其物理活性(如颗粒效应、微集料效应等);另一方面,破坏了粗大玻璃体尤其是多孔颗粒的粘连结体以及玻璃体表面坚固的保护膜,从而使内部更多的可溶性活性SiO2、Al2O3溶出,同时硅氧四面体、铝氧三角体在强烈机械力作用下,晶格无序化、畸变,形成晶格缺陷,甚至可能使Si—O键、Al—O键折断,成为无定形物,比表面积增大,从而使表面出现许多活化中心。整个颗粒表面活化过程可用如图2-7所示的活化点分布模型表示,假设物料颗粒是球形,黑点表示活化点,它开始分布在表面,然后集中于局部区域,最后均匀地分布于整体,则活化点可认为是机械力化学的。

图2-7 活化点分布模型
图2-8所示为将煤矸石进行粉磨后的X射线衍射图,与如图2-6所示的仅经煅烧但没有粉磨的X射线图相比,衍射线变宽、弥散,说明有无定形物质生成,因此改变了矸石的性质,降低了反应活化能,从而使反应得以快速进行。而且,通过粉磨可将煤矸石颗粒原有的棱角磨圆或被磨掉,浑圆的颗粒却能起到滚动润滑作用,有利灌浆。但矿粉超过一定的细度,对复合材料的综合性能技术指标并不利。基于此,从材料使用性能和能耗两方面考虑,分别粉磨15min、30min、45min、60min,然后使用激光粒度仪测定不同粉磨时间颗粒的粒径分布。有试验资料表明,对于用类似粉煤灰的火山灰质材料研制的胶凝材料强度,在寻求火山灰质材料最佳颗粒级配时,应尽量提高小于30μm颗粒含量,限制30~45μm颗粒含量,减少大于45μm颗粒含量。经测定,煤矸石在粉磨30min后,小于30μm颗粒质量分数已达到60.35%,大于45μm颗粒质量分数仅有17.58%。若粉磨时间增加一倍,小于30μm颗粒仅增加10个百分点左右。综合考虑,煤矸石经粉磨30min后作为灌浆材料性价比最佳。

图2-8 磨细煤矸石的XRD图谱
(3) 化学活化 所谓化学活化,实质就是通过加入一些称为激发剂的物质,促进系统充分水化,提高浆材的性能。试验采用74.5%的煤矸石、21.3%的石灰、4.2%的石膏,将自行研制的ZGW复合激发剂掺入其中进行化学活化。
ZGW复合激发剂是利用减水剂、膨胀剂、早强剂进行正交试验来确定的。经对浆液黏度、3d的抗压强度、7d的抗压强度、28d的抗压强度等指标的分析,得出ZGW复合激发剂的最佳配比下的指标见表2-4。
表2-4 基于ZGW复合激发剂的试验结果

(4)晶种活化 胶凝材料水化是一个矿物的溶解同时产物在液相
中结晶的过程,即水化产物同时在液相中不断析晶的过程。研究表明,要使液体变成晶体,首先必须产生晶核,然后使晶核进一步长大成为晶体(晶化)。在成核过程中,需克服一成核势垒ΔGr,只有这样晶核才能长大,若假设新生相为球形(图2-9),成核势垒ΔGr则可以写为
(2-2)

图2-9 掺入晶种后成核模型
式中 γLS——液-固界面能(假定没方向);
ΔGV——液-固相变时,不考虑界面能时单位体积自由焓的变化;
ΔGr——相变活化能,用来描述相变发生时形成临界晶核所必须克服的势垒。其值越小,成核过程越容易。
当引入微小颗粒作为晶种在新相形成体系时,新生相成核将受影响,晶核将在这些晶种上优先寄生、成核。
通过上述理论,引入钙矾石、水化硅酸钙、水化铝酸钙等微小颗粒作晶种,以促进煤矸石水化。试验采用已充分水化过的煤矸石胶凝水化产物,经磨细过4900孔筛作晶种,测定其对抗压强度和凝结时间的影响见表2-5。
由表2-5知,掺入晶种后,使新生相体系成核过程需要克服的势垒有所降低,缩短了成核过程,促进了胶凝材快速水化,为煤矸石结构的解体提供了更有利的外部条件。表征为:晶种掺量在1%~3%内随着掺量的增加,凝结时间明显缩短,3d、7d强度略有增加,28d强度影响不大。当进一步增加掺量时,凝结时间虽进一步缩短,但是因成核过多,结构虽致密,而晶体却无法长大,使整个系统晶/胶比过低,造成阻裂能力、强度下降,故晶种的适宜掺量为3%。
表2-5 晶种掺量的影响

(5) 碱与硫酸盐双重激发煤矸石活性试验 低温煅烧过的煤矸石与粉煤灰具有相似的化学组成,同属于CaO-SiO2-Al2O3系统,但煤矸石中的CaO含量远低于粉煤灰,因此活性较粉煤灰差。受粉煤灰-石灰-硫酸盐基本系统的启发,以煤矸石-石灰-硫酸盐为基本系统,采用了碱与硫酸盐双重激发煤矸石的活性。
1)试验方案 试验采用煤矸石-石灰-硫酸盐基本系统,原料为低温煅烧粉磨后的煤矸石粉、生石灰及元明粉,试验中共有3种组分,当另两种组分用量确定,第三种组分用量也随之确定,故以生石灰和元明粉两因素三水平,选择可容纳四因素三水平L9(34)的正交表来安排9组试验(表2-6、表2-7)。
表2-6 因素水平表 单位:%

表2-7 煤矸石活性激发试验结果 单位:MPa

2)试验数据分析及结论 从表2-7中可以看出,3d强度第5组分和第6组分较为突出,第6组分略大于第5组分;到7d强度上,两组分强度还是比较突出,但第5组分强度开始高于第6组分,成为9组试验中最优配比;到28d时,第5组仍然是9组中强度最高的一组。所以从试验结果直接观察可知,第5组(生石灰29.2%,元明粉3%)为煤矸石活性激发的最佳激发剂配方。煤矸石试验结果极差分析见表2-8。
表2-8 煤矸石试验结果极差分析

3d强度的极差:
7d强度的极差:
28d强度的极差:
总体上看,生石灰是影响体系强度的主要因素,这也可以从煤矸石的化学成分推断的相一致,“缺钙”是粉煤灰、煤矸石等工业废渣活性的瓶颈。
方差分析如下。
3d强度:
9次强度平均值
方差S生石灰=(4.21-4.74)2+(5.91-4.74)2+(4.11-4.74)2=2.05
S元明粉=(4.11-4.74)2+(4.92-4.74)2+(5.19-4.74)2=0.65
S生石灰>S元明粉
7d强度:
9次强度平均值
S生石灰<S元明粉
28d强度:
9次强度平均值
S生石灰>S元明粉
从3d强度的分析可以看出,生石灰在2水平和元明粉在3水平时具有较高的抗压强度,其对应的组分是生石灰掺量29.2%和元明粉掺量4%;而7d与28d强度的趋势图却发生了变化,这两个龄期的较高强度在生石灰和元明粉两因素的2水平,对应的是生石灰29.2%和元明粉3%。出现这种现象的原因是元明粉首先溶解在水中电离出S与煤矸石本身所含的CaO反应,这部分CaO高度分散在煤矸石中,比后加入的CaO与S
反应快得多,生成钙矾石,形成早期强度;随着龄期的增大,生石灰慢慢参与反应,使中后期强度得到了保证,成为影响中后期强度的主要因素。
综上所述,大的元明粉掺量有助于体系早期强度的形成,过量则对中后期强度和体系安定性有很大的影响;生石灰掺量也要适量,掺量过少则为体系提供不了足够的Ca2+生成钙矾石,过量生石灰只充当填料的作用,早期几乎不与煤矸石发生反应,对早期强度没有贡献,后期还会发生体积膨胀,对后期强度的发展有害无益。体系各组分的比例见表2-9。
表2-9 煤矸石-石灰-硫酸盐体系组成及各龄期强度

2.2.4 电子显微(SEM)分析
为进一步研究煤矸石与碱激发剂、硫酸盐激发剂的相互作用,了解生成何种矿物以及其在微观上的排列方式,分别对煤矸石的两组样品进行了扫描电镜分析。测试样品配方:煤矸石75.44%、生石灰22.09%、元明粉2.27%。图2-10所示为样品的SEM照片。

图2-10 样品的SEM照片
从图2-10中可以看到,大量层片状氢氧化钙晶体,少量的方型石英晶体,小堆状的蒙脱石,极少量的长4~5μm的针状钙矾石开始生长,较大的孔隙没有填充。由于煤矸石烧失量高达48.82%,含有较多的有机碳质,虽经800℃、1h的低温煅烧,急冷后呈灰黑色,仍含有较多的碳质,由于碳质属于“惰性”物质,极少与其他矿物发生化学反应,只是作为填料,影响了其强度的增长。
2.2.5 水泥-煤矸石注浆材料
煤矸石经过粉碎、低温煅烧和粉磨后,具有了一定的活性,能够作为水泥混合料,其含有的活性物质能与水泥水化产物发生反应,生成具有胶凝强度的产物。通过试验,可确定煤矸石的掺量多少具有最好的强度、施工性能和经济效益。
(1)试验安排 煤矸石掺量为10%~60%,测试水灰比为1∶0.5、1∶0.6和1∶0.8,测试参数为浆液黏度、凝结时间、抗折抗压强度及结石率。
(2)试验结果及分析 见表2-10、图2-11。
表2-10 煤矸石单掺试验结果


图2-11 煤矸石掺量、水灰比与抗压强度的关系
从图2-11中可以看出,当煤矸石掺量30%以内时,强度随着掺量的增大有增大的趋势;当掺量继续增大时,各龄期强度都有所下降。3d强度不到1MPa,后期强度增长较快,这是因为煤矸石代替了一部分水泥后,水泥-煤矸石浆体体系中水泥比例减少,控制水泥水化速率的有效水灰比增大,使溶液中的Ca2+浓度降低,水泥-煤矸石体系的水化速率减慢,生成的水化产物颗粒之间连接不够紧密,相应地降低了早期强度;在28d时由于煤矸石的火山灰效应以及煤矸石细小颗粒的填充效应和微集料效应,使得浆体的结构比较致密,水化产物之间的相互交叉和连接程度较好,导致其强度的增长较快。
从图2-12中可以看出,掺入煤矸石后,黏度随着煤矸石掺量的增大而增大,凝结时间也随之延长。煤矸石具有较为疏松的结构,颗粒之间能够“储存”水分的空间相对较大,导致了浆液流动性降低。

图2-12 煤矸石掺量、水灰比与黏度、凝结时间之间的关系
综合以上分析,选择水泥单掺30%的煤矸石较为适宜,材料组分与工艺参数见表2-11。
表2-11 煤矸石注浆材料优选组分与性能
