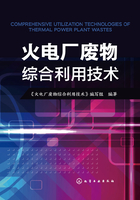
第1章 综 述
1.1 火力发电概况
电力工业发电方式包括火力发电、水力发电、核能发电、风力发电、太阳能发电、生物质能发电、地热发电、波浪能发电、海洋温差发电等。我国的发电装机结构和发电量结构中都以火力发电为主。2012年,全国发电装机容量、发电量分别为1146760MW时和49865×108kW·h。其中,火力发电分别占总装机容量的72%和占发电总量的79%。而在火力发电中又以燃煤发电为主,发电量比重约占火力发电的95%。
火力发电是通过化石燃料的燃烧将化学能转化为热能,通过动力机械将热能转换为机械能,再通过驱动发电机将机械能转换为电能的发电的技术。实现这种电能转换技术的工厂称为火力发电厂,其中,完成上述能量转换过程的设备组合称为火力发电机组。火力发电的燃料构成主要是自然界蕴藏量极丰富的化石燃料,包括固体燃料(主要为煤炭)、液体燃料(主要为原油及重油、柴油等石油制品)、气体燃料(主要是天然气、液化天然气、煤层气及由煤炭转换的各种煤气)。火力发电主要有蒸汽动力发电、内燃机发电、燃气轮机发电,以及燃气-蒸汽联合循环发电。在上述发电基础上发展起来的热电联产电厂,使火电机组既发电又供热,进一步提高了热能的利用率。
1.1.1 分类及特点
(1)分类
①按燃料划分 可划分为:燃煤发电机组,主要以煤炭作为燃料的发电机组;燃油发电机组,即以液体燃料(主要为原油、重油、柴油、渣油等石油制品)为燃料的发电机组;燃气发电机组,即以气体燃料(主要是天然气、液化天然气、煤层气及由煤炭转换的各种煤气等)为燃料的发电机组;余热发电机组,即用工业企业的各种余热进行发电的机组;还有利用垃圾及工业废料为燃料的发电机组。
②按蒸汽压力和温度划分 可分为:中低压发电机组(3.92MPa,450℃),高压发电机组(9.9MPa,540℃),超高压发电机组(13.83MPa,540℃),亚临界压力发电机组(16.77MPa,540℃),超临界压力发电机组(22.11MPa,550℃),超超临界压力发电机组(25~35MPa,580℃)。
③按发电机组装机容量划分 可分为:小容量发电机组(200MW以下),中容量发电机组[(200~600)MW,不含600MW],大容量发电机组(600MW及以上)。
④按原动机划分 可分为:凝汽式汽轮机发电机组、燃汽轮机发电机组、内燃机发电机组和蒸汽-燃汽轮机发电机组等。
⑤按输出能源划分 可分为:纯凝汽式发电,热电联产。
(2)主要特点
与水电站相比,火电厂具有如下特点:a.布局灵活,装机容量的大小可按需要决定;b.调度灵活,可根据电力需求调整机组负荷;c.建造工期短,一般为水电厂的1/2甚至更短;d.一次性建造投资较少,仅为水电厂的50%左右;e.生产成本较高,运行人员较多,煤耗量大,加上运煤费用和大量用水,其生产可变成本比水电要高出3~4倍;f.动力设备繁多,发电机组控制操作复杂,厂用电量和运行人员都多于水电厂,运行费用高;g.污染控制投入较大,排烟、排水、排灰渣等会造成环境污染,需加以控制。
1.1.2 主要系统及设备
1.1.2.1 系统概述
火力发电厂主要生产系统包括燃烧系统、汽水系统和发电系统。各系统基本情况如下。
(1)燃烧系统
燃烧系统是由输煤、磨煤、粗细分离、排粉、给粉、锅炉燃烧等组成。燃煤由皮带输送机从煤场,通过电磁铁、碎煤机然后送到煤仓间的煤斗内,再经过给煤机进入磨煤机进行磨粉,磨好的煤粉通过空气预热器来的热风,将煤粉打至粗细分离器,粗细分离器将合格的煤粉(不合格的煤粉送回磨煤机),经过排粉机送至粉仓,给粉机将煤粉打入喷燃器送到锅炉进行燃烧。燃烧产生的大块熔渣(约占总灰量的10%~20%),经水冷壁冷却形成固态渣由炉底排放,再经碎渣机破碎;燃烧产生的烟气由锅炉尾部的空气预热器出口排出后,经过除尘器,将烟气中的大部分细灰分离出来,排往除灰系统,以防止粉尘粒子对大气产生污染;为了减少SO2和NOx等有害气体对大气的污染,现代锅炉还设有烟气脱硫、脱硝装置,净化后的烟气经引风机排往烟囱。
(2)汽水系统
汽水系统是由锅炉、汽轮机、凝汽器、高低压加热器、凝结水泵和给水泵等组成,包括汽水循环、化学水处理和冷却系统等。水在锅炉中被加热成蒸汽,经过热器进一步加热后变成过热的蒸汽,再通过主蒸汽管道进入汽轮机。由于蒸汽不断膨胀,高速流动的蒸汽推动汽轮机的叶片转动从而带动发电机。为了进一步提高其热效率,一般都从汽轮机的某些中间级后抽出做过功的部分蒸汽,用以加热给水。在现代大型汽轮机组中都采用这种给水回热循环。在蒸汽不断做功的过程中,蒸汽压力和温度不断降低,最后排入凝汽器并被冷却水冷却,凝结成水。凝结水集中在凝汽器下部由凝结水泵打至低压加热器,再经过除氧气除氧,经给水泵送至高压加热器,经过加热后的热水打入锅炉,在过热器中把水已经加热到过热的蒸汽,送至汽轮机做功,循环做功。在汽水系统中的蒸汽和凝结水,由于经过管道很多并且还要经过许多的阀门设备,这样就难免产生跑、冒、滴、漏等现象,这些现象都会或多或少地造成水的损失,因此,必须不断地向系统中补充经过化学处理过的软化水,这些补给水一般都补入除氧器中。
(3)发电系统
发电系统是由副励磁机、励磁盘、主励磁机(备用励磁机)、发电机、变压器、高压断路器、升压站、配电装置等组成。发电是由副励磁机(永磁机)发出高频电流,经过励磁盘整流,再送到主励磁机,主励磁机发出电后经过调压器以及灭磁开关经过碳刷送到发电机转子,当发电机转子通过旋转其定子线圈便感应出电流,强大的电流通过发电机出线分两路,一路送至厂用电变压器,另一路则送到SF6高压断路器,由SF6高压断路器送至电网。
燃煤电厂生产流程示意如图1-1所示。

图1-1 燃煤电厂生产流程示意
1.1.2.2 锅炉
(1)锅炉的容量、参数及其分类
①电站锅炉的蒸汽参数及容量 20世纪70年代以前,中国的火电机组单机容量在100MW以下,蒸汽参数以10MPa/540℃为主;20世纪80年代初期,我国自行设计和制造了单机容量为200MW的火电机组,配置主蒸汽参数为超高压,并具有中间再热系统的14MPa/540℃的锅炉机组。
20世纪80年代以后,我国的火电机组以引进技术国产化为主,建设了一批亚临界与超临界参数大容量发电机组。各种技术类型的300MW、500MW、600MW、800MW级亚临界与超临界参数锅炉机组相继投入运行。表1-1~表1-3是中国电站锅炉的蒸汽参数及容量。
表1-1 中国电站锅炉的蒸汽参数及容量

表1-2 亚临界压力自然循环及控制循环锅炉的参数及容量

续表

表1-3 超临界和超超临界锅炉的参数及容量

②锅炉的分类 按锅炉用途分类,分为电站锅炉(发电)、工业锅炉(工业生产工艺用汽或供暖)、热水锅炉(民用采暖或供热)。
按锅炉容量分类,随时代和技术进步,锅炉机组容量按大、中、小的排序和分类在不断演变,目前,300MW以上的机组配置的锅炉为大容量锅炉。
按燃煤方式分类,分为火床锅、煤粉炉(四角燃烧、对冲燃烧、W型火焰燃烧)、旋风炉、流化床锅炉。
按排渣方式分类,分为固态排渣锅炉和液态排渣锅炉。
按水汽流动方式分类,分为自然循环锅炉、强迫循环锅炉和直流锅炉。其中,自然循环锅炉的优点是可以将汽包内含杂质浓度较高的水连续排去一部分(连续排污),还可以在水冷壁下部定期放水,除去沉淀的水渣(定期排污),对给水质量要求稍低,自动调节系统较简单。强迫循环锅炉的汽压越高,饱和蒸汽与饱和水的密度就越接近,使炉水自然循环的动力也越小。如果设计、运行不当,就容易发生水循环不良,引发爆管事故;一般汽压超过16.6MPa(170atm)时可采用强迫循环锅炉。直流锅炉的特点是没有汽泡,水在给水泵的压力下,一直流过锅炉的蒸发部分,不往返循环;比较容易制造,钢材耗量少;缺点是不能排污,对水质要求高,自动调节也比较复杂。直流锅炉可用于任何蒸汽参数,特别适用于超高压以上的电厂。
(2)几类锅炉介绍
①固态排渣锅炉 炉膛和烟道由炉墙围成,整个炉膛是一个巨大的空间,炉膛的顶部倾斜,有利于烟气向水平烟道流动,中部由前墙、后墙和两侧墙围成煤粉燃烧的空间,称为燃烧室,简称炉膛。在炉墙的冷却作用下,呈熔化状态的灰分成为固态的炉渣,因此,这种锅炉称为固态排渣炉。
烟道是烟气流通的途径,在其中布置着吸收烟气热量的过热器、再热器、省煤器及空气预热器等作为受热面。固态排渣煤粉锅炉炉膛和烟道结构布置示意如图1-2所示。

图1-2 锅炉炉膛结构示意
②液态排渣锅炉 燃料燃烧后生成的炉渣在熔渣室的高温下熔化成液态从炉膛排出的锅炉,其特点如下:a.适合燃用低挥发分或低灰熔点的煤种,避免了固态排渣炉燃用此煤种时存在的燃烧不完全及灰渣结焦问题;b.由于具有独特的排渣方式,可不需要一般锅炉所设计的贮灰场,从而既节省了灰场投资又节约了大量冲灰用水;c.熔融灰在炉膛内的被捕获概率大大高于固态灰渣,捕渣率可达70%以上,而一般煤粉炉则仅为20%左右;由于飞灰量的减少,大幅度降低了除尘器入口浓度;d.灰渣利于综合利用。为使液态渣排出流畅,对于燃烧灰熔点稍高或不太稳定的煤种时,在燃料中加入适量的石灰石,不仅降低了煤的灰熔点,改善了流渣条件,而且还降低烟气SO2浓度,并为灰渣的综合利用提供了有利条件,并以此获得综合利用效益。液态排渣炉的增钙渣和飞灰在生产建筑材料、直接生产岩棉、生产多元素复合肥等方面更优于固态渣灰。由于增钙渣的成分与岩棉的成分十分相似,而液态排渣过程又为制造生产岩棉提供了有利条件,即省去了一般生产岩棉用的加热熔化炉。
③W型火焰锅炉
a.W型火焰锅炉是固态排渣煤粉炉的一类,适用于燃烧低挥发分的煤。目前,W型火焰锅炉已在一些国家广泛应用于燃烧无烟煤。
b.通常国内外将可燃基挥发分Vdaf<10%的煤列为无烟煤。无烟煤具有含碳量多、挥发分低、机械强度高、质硬、密度大、不易研磨、挥发分析出温度高、着火困难等特点,因此,在无烟煤的燃烧中要着重解决着火、稳燃、燃烬三个主要问题。
c.国内电站锅炉燃无烟煤时主要选用固态排渣煤粉炉并采用直流燃烧器四角切圆燃烧方式,但在实际运行中普遍存在着火不好、燃烧不稳定、燃料灰熔点低时易结渣等问题。国内外围绕此类问题做了大量工作,研制出许多新型燃烧器和预燃室,如煤粉旋流预燃室燃烧器、钝体燃烧器、浓淡燃烧器、大速差同向射流燃烧器、PAX型燃烧器等,但仍存在一些问题。故美国一些公司对于劣质煤,特别是低挥发分的无烟煤,大都倾向于采用U型、W型火焰燃烧技术。
W型火焰锅炉由下部拱型着火燃烧室和上部辐射燃烧室组成。着火燃烧室敷设卫燃带,以改善无烟煤的燃烧工况。燃烧室的前后拱上布置燃烧器。一、二次风向下喷出,着火的煤粉气流向下形成W型火焰再向上进入辐射燃烧室。W型火焰锅炉工艺示意如图1-3所示。

图1-3 W型火焰锅炉工艺示意
④循环流化床锅炉 循环流化床锅炉(简称CFB锅炉)是基于流态化基本原理的一种集气固两相流动、燃烧、传热、传质等复杂过程于一体的实用化的锅炉技术。CFB锅炉与老式鼓泡床相比,在炉膛出口增加颗粒分离装置(一般为旋风分离器),将气流夹带的较大粒度颗粒分离下来,并经由物料回送系统(返料器)送回炉膛反复燃烧,只有细小的颗粒随气流进到尾部烟道。由于分离装置的存在,流化速度可以选得比较高,物料的循环携带作用使得燃料热量的释放和吸收在整个炉膛包括循环回路进行,解决了受热面布置的问题,飞灰,特别是炉渣的可燃物含量可以控制得较低。CFB锅炉工艺示意如图1-4所示。

图1-4 CFB锅炉工艺示意
固体燃料在炉膛内以一种特殊的气固流动方式——流态化方式运动,炉膛内固体颗粒的浓度高,燃烧、传质、传热剧烈,温度分布均匀。强烈湍流带来的强烈物料掺混,为循环流化床内燃料颗粒的燃烧创造了良好的条件。CFB锅炉炉内添加石灰石可以实现炉内干法脱(固)硫。其技术特点如下。
a.燃烧效率高。循环流化床物料循环流动沿床高(包括分离器和物料循环回路)有足够高且均匀的温度分布,以及强烈湍流带来的强烈物料掺混,为循环流化床内燃料颗粒的燃烧创造了良好的条件。因此,虽然CFB锅炉炉膛温度通常只有900℃左右,但CFB锅炉仍然可以达到与煤粉锅炉相当的燃烧效率(97%~99%)。
b.良好的换热效果。物料浓度对CFB锅炉传热特性有明显的影响。CFB锅炉炉膛内物料浓度是常规煤粉炉的几十倍,因此,其传热系数很高,在炉膛温度比煤粉炉低很多的情况下也可以得到很好的换热效果。
c.可烧劣质燃料。CFB锅炉炉膛内存在大量炙热惰性床料,使得CFB锅炉燃烧过程非常稳定,仅相当于百分之几床料的燃料进入炉内,即使是高灰分低热值的劣质燃料,也不会对炉内的稳定燃烧造成大的冲击。因此,CFB锅炉几乎可以燃烧各种劣质燃料(贫煤、无烟煤、褐煤、煤矸石、油页岩、石油焦、城市垃圾等)。
d.洁净煤燃烧。CFB锅炉炉膛内一般维持900℃左右的低温燃烧,加入1mm以下的石灰石粉,就可以在炉内燃烧过程中实现80%以上硫的脱除率。同时,低温燃烧使CFB锅炉NOx的排放也很低(通常200mg/m3以下)。因此,CFB锅炉被认为是一种洁净煤技术,具有良好的环保特性。
e.负荷调节比大。由于CFB锅炉燃烧的稳定,不会轻易发生灭火现象。CFB锅炉可以很容易实现40%额定负荷下不投油稳定燃烧,其负荷调节比大。CFB锅炉燃料的入炉粒径为0~10mm(实际有的锅炉由于破碎系统问题,入炉煤粒度甚至达到50mm,CFB锅炉也基本能维持运行),因此,原煤通常只需要经破碎而无需磨制即可满足要求。
f.灰渣活性高。CFB锅炉燃烧温度低,其底渣和飞灰活性高,用于生产水泥、建筑材料、筑路等更有优越性。
g.CFB锅炉不利的特点主要是其烟风阻力大(存在布风板、床料、分离器阻力损失),导致CFB锅炉虽然不需要煤粉制备系统,但其厂用电仍然较煤粉炉偏高。目前,国内投运的10×104kW及以上的CFB锅炉,厂用电率普遍为6%~8%。其中,布风板阻力设计过高、风机选型过大等是直接的原因。
1.1.2.3 汽轮机
(1)汽轮机基本组成
汽轮机是将蒸汽能量转化为机械功的旋转式动力机械,本体由转动部分(转子)和固定部分(静子)组成,如图1-5所示。转动部分包括动叶栅、叶轮(或转鼓)、主轴、联轴器等;固定部分包括气缸、蒸汽室、喷嘴室、隔板、隔板套(或静叶持环)、汽封、轴承、轴承座、机座、滑销系统等。

图1-5 某汽轮机本体结构示意
①汽轮机组 汽轮机的级由喷嘴叶栅(或静叶栅)和与它相配合的动叶栅组成。喷嘴的作用是把蒸汽的热能转变成动能,也就是使蒸汽膨胀降压增加流速,按一定的方向喷射出去,进入动叶栅中做功。喷嘴直接安装在喷嘴室和隔板中,如图1-6所示。

图1-6 汽轮机通流部分结构示意
叶片按用途可分为动叶片和静叶片(又称喷嘴叶片)两种。动叶片安装在转子叶轮(冲动式汽轮机)或转鼓(反动式汽轮机)上。静叶片安装在隔板或气缸上,起喷嘴作用;在双列速度调节级中,第二列静叶做导向叶片,使气流改变方向,引导蒸汽进入动叶片。
②汽轮机转子 汽轮机中所有转动部件的组合叫作转子,它是汽轮机最重要的部件之一,担负着工质能量转换及扭矩传递的重任。转子由主轴、轴套、叶轮、叶片、联轴器、轴封套(汽封套)等部件组成,有些转子还包括带动主油泵和调速器的附加轴。
③汽轮机汽缸与隔板 汽缸的主要作用是将汽轮机的通流部分与外界隔开,保证蒸汽在汽轮机内完成做功过程。此外,它还要支撑汽轮机的一些静止部件(隔板、喷嘴室、汽封套等)。汽缸通常制成具有水平接合面的对分形式,上半部叫上汽缸,下半部叫下汽缸。上、下汽缸之间用法兰螺栓连接在一起。为了减小汽缸应力,现代汽轮机也有采用无水平接合面汽缸的。
多级汽轮机调节级后的各压力级是在不同的压力下工作的。为了保持各级前后的压力差、安装静叶片和阻止级间漏气,汽缸上装设有多个隔板,它可以直接安装在汽缸内壁的隔板槽中,也可以借助隔板套安装在汽缸上。隔板通常做成水平对分形式,其内圆孔处安装有隔板汽封。反动式汽轮机没有隔板,但会在汽缸上安装支撑静叶的持环。
④汽封 汽轮机运转时,转子高速旋转,汽缸、隔板(或静叶环)等静止不动。因此,转子和静止部件之间需留有适当的间隔,防止相互碰磨。然而间隙的存在会导致蒸汽泄漏,这不仅会降低机组效率,还会影响机组安全运行。为了减少蒸汽泄漏和防止空气漏入,采用了汽封装置。汽封按其安装位置的不同,可分为叶顶汽封、隔板(或静叶环)汽封、轴端汽封以及径向汽封等。反动式汽轮机还装有平衡活塞汽封。汽封主要形式有梳齿、蜂窝、刷式等。
为了防止和减少漏气以及回收漏气,很多汽轮机设有由轴端汽封加上与之相连接的管道、阀门及附属设备组成的轴封蒸汽调整系统,并配置自动调节装置。
⑤汽轮机轴承 汽轮机轴承包括径向支撑轴承和推力轴承,主要采用滑动轴承。径向支撑轴承承担转子的质量和旋转动反力,并保证转子的径向位置。推力轴承承受蒸汽作用在转子上的部分轴向推力,保持转子工作时的轴向位置,以保证通流部分动静轴向间隙。推力轴承的工作面是转子相对于汽缸的定位点,称为汽轮机转子对静子的相对死点。
⑥联轴器 联轴器是汽轮机各转子间、汽轮机转子和发电机转子间的连接件。通过联轴器把汽轮机转子的转动力矩传递给发电机。汽轮机电机组主要联轴器多采用刚性联轴器。
⑦盘车装置 汽轮机冲转前和停机后,要使转子连续转动一段时间,以保证转子均匀受热和冷却。带动转子转动的装置称为盘车装置,它可以自动投入和切除。汽轮机的盘车分为低速盘车(3~5r/min)和高速盘车(40~70r/min)两种。汽轮机启动时,为减小盘车电动机功率,采用高压油顶轴装置,在盘车装置投入前用压力油将转子顶起以减少启动转矩。
⑧汽轮机控制与保护系统 汽轮机控制系统的主要作用是:当发电机负载变化时,使主气阀和调节气阀改变进汽量,调节汽轮机的输出功率,使其与外界负荷相适应,维持汽轮机转速在规定范围内,保证电能质量。供热汽轮机还具备供热蒸汽压力自动调节系统。
此外,为保证运行安全,汽轮机还设有各种保护装置,如超速保护、轴向位移保护及低油压保护等。当这些参数超出安全范围时,保护系统自动切断汽轮机进汽,停止设备运转,避免事故发生与扩大。
(2)汽轮机的分类
根据做功原理、热力过程特性、参数水平的差异等可以将汽轮机进行以下分类。
①按做功原理分类
a.冲动式汽轮机。按冲动原理做功的级构成的汽轮机叫冲动式汽轮机。为了提高效率,冲动式汽轮机级均带有一定反动度,习惯上仍称为冲动式汽轮机。
b.反动式汽轮机。按反动式原理做功的级构成的汽轮机叫反动式汽轮机。现代反动式汽轮机常以冲动级(单列级或复速级)做调节级,但习惯上仍称为反动式汽轮机。
②按热力过程特性分类
a.凝汽式汽轮机。进入汽轮机的蒸汽在流经汽轮机各级后,除少量漏气外全部进入凝汽器,这种汽轮机叫作凝汽式汽轮机。现代汽轮机为提高循环热效率,一般都采用若干段回热抽气加热给水,这类汽轮机习惯上仍成为凝汽式汽轮机。
b.背压式汽轮机。进入汽轮机的蒸汽流经各级做功后,在高于大气压力的情况下排出,以供工业或生活之用。这种汽轮机成为背压式汽轮机。
c.调整抽气式汽轮机。从汽轮机中间某个几级后抽出一定参数、一定质量流量的蒸汽,供给工业或生活之用,其余的蒸汽流入凝汽器,这种汽轮机称为调整抽气式汽轮机。调整抽气式汽轮机和背压式汽轮机统称为供热式汽轮机。
d.中间再热式汽轮机。将在汽轮机若干级中做过功的蒸汽(如高压汽缸的排汽)引入锅炉再次加热,然后又回到汽轮机后面的一些级(如中低压汽缸)内继续膨胀做功,乏汽进入凝汽器,这种汽轮机叫作中间再热式汽轮机。
③按蒸汽压力分类
a.低压汽轮机。新汽压力为1.2~2.0MPa(例如,新汽压力为1.3MPa,温度为340℃)。
b.中压汽轮机。新汽压力为2.1~4.0MPa(例如,新汽压力为3.43MPa,温度为435℃)。
c.高压汽轮机。新汽压力为8.1~12.5MPa(例如,新汽压力为9.0MPa,温度为535℃)。
d.超高压汽轮机。新汽压力为12.6~15.0MPa(例如,新汽压力为13.0MPa或13.5MPa、温度为535℃或550℃,再热温度为535℃或550℃)。
e.亚临界压力汽轮机。新汽压力为15.1~22.5MPa(例如,新汽压力为16.5MPa、温度为535℃,再热温度为535℃)。
f.超临界压力汽轮机。新汽压力大于22.1MPa。例如,国内某600MW超临界压力汽轮机参数为:新汽压力为23.8MPa,温度为566℃,再热温度为566℃。
g.超超临界压力汽轮机。新汽压力在27MPa以上蒸汽温度达到600℃/620℃以上的汽轮机。例如,国内某900MW超超临界压力汽轮机参数为:新汽压力为26.25MPa,温度为600℃,再热温度为600℃。
此外,按汽缸数可以分为单缸汽轮机和多缸汽轮机;按机组转轴数可以分为单轴汽轮机和双轴汽轮机;按工况可以分为固定式汽轮机和移动式汽轮机等。
(3)汽轮机的型号
汽轮机型号虽然随着制造商的习惯不同而不同,但是一般都包含了汽轮的形式、容量、新蒸汽参数和再热蒸汽参数等信息,供热汽轮机型号还包括供热蒸汽参数。因此,从汽轮机的型号可以基本判断出汽轮机的主要特征。
我国制造的汽轮机的型号大多包含三部分信息。第一部分信息由汉语拼音字母表示汽轮机的形式(见表1-4);由数字表示汽轮的容量,即额定功率(MW);第二部分信息用几组由斜线分隔的数字分别表示新蒸汽参数、再热蒸汽参数、供热蒸汽参数等(见表1-5)。功率单位为MW,蒸汽压力参数的单位为MPa,温度参数的单位为℃;第三部分为厂家设计序号。
表1-4 汉语拼音代号

表1-5 型号中蒸汽参数表示法

(4)汽轮机的凝汽系统及设备
发电厂用的汽轮机组绝大部分是凝汽式汽轮机。在火电厂中,蒸汽循环做功主要有四大过程:蒸汽在锅炉中的定压吸热过程,蒸汽在汽轮机中膨胀做功过程,汽轮机排汽在凝汽器中定压放热过程,凝结水在给水泵中的升压过程。可见,凝汽系统及设备是汽轮机组的重要组成部分,其设计、运行性能将直接影响到整个汽轮机组的经济性和安全性。
①凝汽系统的工作原理 图1-7是汽轮机凝汽系统示意,系统由凝汽器、抽气设备、循环水泵、凝结水泵以及相连的管着、阀门等组成。

图1-7 汽轮机凝汽系统示意
1—汽轮机;2—发电机;3—凝汽器;4—抽汽设备;5—循环水泵;6—凝结水泵
在凝汽式汽轮机组整个热力循环中,凝汽系统的任务可以归纳为以下四点。
一是在汽轮机末级排汽口建立并维持规定的真空。从热力学第二定律的观点,完整的动力循环必须要有一个冷源,凝汽系统在蒸汽动力循环中起着冷源的作用,通过降低排汽压力和排汽温度来提高循环热效率。
二是汽轮机的工质是经过严格化学处理的水蒸气,凝汽器将汽轮机排汽凝结成水,凝结水经回热抽汽加热、除氧后,作为锅炉给水重复使用。
三是起到真空除氧作用,利用热力除氧原理除去凝结水中的溶解气体(主要为氧气),从而提高凝结水品质,防止热力系统低压回路管道、阀门等腐蚀。
四是起到热力系统蓄水作用,凝汽器既是汇集和贮存凝结水、热力系统中的各种疏水、排汽和化学补水的场所,又是缓解运行中机组流量的急剧变化,从而起到热力系统稳定调节作用的缓冲器。
为了完成上述任务,仅有凝汽器是不够的。要保证凝汽器的正常工作,必须随时维持三个平衡:一是热量平衡,汽轮机排汽放出的热量等于冷却水(又称循环水)带走的热量,故在凝汽系统中必须设置循环水泵;二是质量平衡,汽轮机排汽流量等于抽出的凝结水流量,所以在凝汽系统中必须设置凝结水泵;三是空气平衡,在凝汽器和汽轮机低压部分漏入的空气量等于抽出的空气量,因此,必须设置抽气设备。
凝汽器内的真空是通过蒸汽凝结过程形成的。当汽轮机末级排汽进入凝汽器后,受到冷却水的冷却而凝结成凝结水,放出汽化潜热。由于蒸汽凝结成水的过程中,体积骤然缩小,这样就在凝汽器容积内形成了高度真空。其压力为凝汽器内温度对应的蒸汽饱和压力,温度越低,真空越高。为了保持所形成的真空,通过抽气设备把漏入凝汽器内的不凝结气体抽出,以免其在凝汽器内逐渐积累,恶化凝汽器真空。
②水冷凝汽系统 水的传热系统比较大,因此,发电厂大多采用水冷凝汽系统。水冷凝汽系统的冷却方式又可以分为直流供水方式(也称开式循环水系统)和循环供水方式(也称闭式循环水系统)两种。直接供水方式是以江、河、湖、海的天然水源作为冷却水源。通常,凝汽系统的取水口布置在江河的上游,排水口选在下游。直流供水方式凝汽系统广泛应用于建在大江、大海附近的发电厂。循环供水方式是需要专用的冷却塔,冷却水吸收凝汽器中排汽的热量后,送入冷却塔中进行冷却,冷却后的冷却水重新进入凝汽器中工作,如此往复循环。一般只需要补充少量冷却水来补充循环中的水损失,因此,闭式供水方式适合于水源不足的地区采用。
③空冷凝汽系统 空冷凝汽系统是指用空气带走汽轮机排汽热量的凝汽系统。采用空冷凝汽系统,不需要冷却水,所以在发电厂厂址选择上就不会受到冷却水源的限制,特别是厂址选在煤炭产地的坑口电厂,采用空冷凝汽系统,更有显著意义。空冷凝汽系统可以分为直接空冷和间接空冷两种方式。
a.直接空冷凝汽系统。图1-8所示为直接空冷凝汽系统的示意,汽轮机排汽送到空冷凝器的翅片管束中,冷空气通过风机的输送,在翅片管外流动,将管内流动的汽轮机排汽冷却、凝结、凝结水由凝结水泵送至回热系统后,作为锅炉给水重复使用。

图1-8 直接空冷凝汽系统的示意
1—汽轮机;2—空冷凝汽器;3—凝结水泵;4—发电机
直接空冷凝汽系统的优点是:一是不需要冷却水等中间冷却介质,适合于严重缺水区域使用;二是传热温差较大,可获得较低的排汽压力。缺点是:一是由于空气的传热系数低于水的传热系数,导致空冷凝器体积比水冷凝器的体积要大得多,所以对凝汽器的安装场地有更多的要求,也更容易泄漏;二是直接空冷凝汽系统大多采用强制通风方式,增加了发电厂的厂用电量,也增加了环境噪声。
b.间接空冷凝汽系统。间接空冷凝汽系统如图1-9所示,汽轮机排汽进入混合式凝汽器后,与从空气冷却器来的冷却水混合凝结为凝结水。凝汽器出来的凝结水与冷却水的混合水流,小部分(约3%)作为锅炉的给水,其余大部分循环水泵打入空气冷却器,构成一个封闭型间接空冷凝汽系统。水轮机用于调节混合凝汽器喷水压力,同时回收部分能量,比如同轴驱动水泵。这种间接空冷凝汽系统克服了直接空冷凝汽系统的缺点,具有凝汽器体积小、设备投资省等优点。缺点是整个凝汽系统复杂、设备多、布置也比较困难。

图1-9 间接空冷凝汽系统示意
1—汽轮机;2—发电机;3—混合式凝汽器;4—抽汽设备;5—水轮机;6—空气冷却器;7—循环水泵;8—给水泵