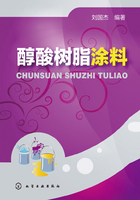
第二节 醇酸树脂涂料制造
一、醇酸树脂清漆
醇酸树脂清漆是按要求的固体分[如50%(质量分数)],将中油度或长油度亚麻油、豆油醇酸树脂溶于选定的溶剂中,加入催干剂,充分搅拌均匀,然后过滤净化制成。醇酸树脂清漆在过去一般也不用铅催干剂,因为醇酸树脂中游离的苯二甲酸酐能结合铅盐析出,从而使清漆发浑。醇酸树脂清漆中应加入防结皮剂,松节油亦有防结皮作用。
将4个不同油度(50%、55%、60%和66%)的醇酸树脂分别加入催干剂和溶剂配成清漆,干燥7d,测得其涂膜的力学性能,见表4-11。
表4-11 4个醇酸树脂清漆涂膜的力学性能

从表4-11中可以看出,干燥时间随油度的降低而缩短,附着力、拉伸强度等力学性能则随油度的降低而增强。综合考虑,醇酸树脂清漆主要品种有C01-1(中油度醇酸树脂)和C01-7(长油度醇酸树脂)两类,参考配方见表4-12。
表4-12 醇酸树脂清漆配方

续表

①对应第三章中的亚麻油、甘油、苯酐的中油度醇酸树脂。
②对应第三章中的62%季戊四醇、豆油、苯酐的醇酸树脂。
③原配方是用铅催干剂,用稀土催干剂代替,用量可以调整。
④原配方中溶剂是用二甲苯,要用低毒溶剂(如含氧溶剂)代替。
表4-12列出典型的中油度、长油度醇酸树脂配制清漆出厂的质量指标,二者差别不大,只是颜色与催干剂稍有不同。醇酸树脂清漆技术标准实行多年后,修订为化工行业标准HG 2453—1993,产品技术要求分为Ⅰ类和Ⅱ类。前者又分为优等品、一等品和合格品,颜色分别为8号、10号和12号(铁钴比色);实干时间分别为10h、12h和15h;耐水时间分别为18h、12h和6h。Ⅱ类醇酸树脂清漆耐水性要求18h。另外增加耐候性一项:广州地区天然曝晒一年,失光和裂纹均为2级,生锈为0级。成膜物是长油度醇酸树脂,相当于表4-12中的C01-7长油度醇酸树脂清漆。经过多年运行,醇酸树脂清漆产品标准经过修订,并把醇酸树脂清漆、色漆合并为一个标准,升为国家级的推荐标准,2010年开始实行GB/T 25251—2010,适用于金属、木质等表面的保护和装饰。GB/T 25251—2010中醇酸树脂清漆技术要求见表4-13。室内装饰装修用溶剂型醇酸树脂木器涂料专有一个标准GB/T 23995—2009。
表4-13 醇酸树脂清漆技术要求(GB/T 25251—2010)

续表

二、醇酸树脂色漆
1.色漆配方设计基础——颜料在涂膜中体积浓度
(1)颜料体积浓度
涂膜中颜料和填料的含量要涉及颜料体积浓度(PVC)的概念,PVC是颜料体积浓度的英文pigment volume concentration的缩写,是指色漆中颜料、体质颜料及其他固体粒子与不挥发物的总体积之比值,通常以百分数(%)表示。PVC可以用下式表达:
或
干色漆涂膜中PVC的参考数量见表4-14。
表4-14 醇酸树脂干色漆涂膜中PVC的参考数量

续表

①还有一种封闭底漆,具有较低黏度,能对其下面的涂层(腻子)或底材有较强的渗透能力,对底材的缺陷或可能有的外渗物(如木材中的单宁酸)起封闭作用。封闭底漆常常使用低颜料体积浓度的着色颜料和体质颜料,使其能充分流动,渗入和强化底材表面,涂膜又具有适当的固体体积,能有效地成膜。这样能起到封闭层和底漆的双重作用。
②面漆干膜中PVC和面漆涂膜的光泽要求是相对应的,随成膜物种类及颜料的品种而不同。就一种成膜物而言,要求面漆的光泽越低,PVC也越高。表4-14中是以中油度醇酸树脂配制有光醇酸磁漆为例的。成膜物不同会有细微差别,需要配方师在生产实践中逐渐摸索试验,逐步掌握。
(2)颜料临界体积浓度
前面已解释了干色漆涂膜中颜料体积浓度(PVC)的概念,这是色漆配方设计的基础,当选定了合适组分之后,决定颜料和基料的相对数量,实现产品的最佳性能的最重要因素就是颜料体积浓度了。
在色漆涂膜中PVC的高低是有限度的,颜填料颗粒分散在基料的过程中,如果PVC适宜,成膜物分子湿润颗粒表面置换粒子表面的空气层,进而包裹每颗颜填料粒子,颜料颗粒之间被基料隔离,颗粒间隙也被基料填充。使颜填料粒子能稳定分散在基料中,这就是色漆稳定分散的要求。这种涂料能对应形成连续致密的干涂膜,能正常发挥涂膜各种物化性能。随着色漆涂膜中PVC的提高,达到某一特定值时,颜填料颗粒间的基料会逐步减少,涂膜的多孔性也随着逐渐增加,许多与多孔性质相关的涂膜性能,如渗透性、光泽、起泡性和防锈性也逐渐变化。这一特定的PVC值称为临界颜料体积浓度(CPVC)。
临界颜料体积浓度(critical pigment volume concentration,CPVC)定义为:漆基正好名义理论上填充互相接触的固体粒子(主要是颜料及体质颜料)之间的空隙时的颜料体积浓度的特定值。超过或未达到此值时,某些性能将会明显地改变。
因此设计色漆配方确定PVC时总是以PVC值和其相应的CPVC值之间的关系进行考虑的。也就是当两种不同的颜料组成其各自的色漆配方,如果二者在各自的配方中PVC值是相同的,但是由于这两种颜料的CPVC值彼此不同,其涂膜性能也可能不同。
显然,颜填料的CPVC值和其吸油量值是相关的,影响颜料吸油量的因素对CPVC同样起作用。可用下式表示:
式中 OA——颜料的吸油量(对于混合颜料应是其实测值),g/100g;
ρ——颜料的密度,g/cm3;
93.5——精制亚麻油的密度×100,g/cm3。
例如,氧化锌的密度为5.6g/cm3,用规定的方法测得的吸油量为19g/100g,计算其CPVC。依据上式得:
在式中可看出,吸油量大的颜填料,其CPVC相对要小。
(3)PVC对色漆性能的影响
色漆中PVC及其相应的CPVC之间的相对关系对色漆涂膜的影响很大。所以在色漆配方设计时,将PVC和CPVC的相互比例安排在一个适当的范围内是十分重要的。通常耐久性要求高的面漆一般都采用低PVC(15%~20%)的配方,因为基料多容易获得连续而致密性好的涂膜,能获得所需的光泽和户外耐久性。随着PVC的增加,涂膜的光泽也随之下降,可以得到半光磁漆、无光磁漆。当需要减少光泽又必须控制PVC和其CPVC的相互比例,以保证涂膜其他性能时,可借助消光剂来调整光泽。
在工业漆和防锈漆中,当PVC低于其CPVC时,涂膜空隙率低,腐蚀因子不易侵入涂膜,防锈性能好。而PVC值超过CPVC值时,腐蚀介质易于透过涂膜侵蚀物体,金属容易生锈,涂膜容易被沾污,故而一般情况下配制色漆时PVC总是低于CPVC。例如,一般工业漆PVC/CPVC=0.8~0.9,防锈漆PVC/CPVC=0.7~0.8,二道底漆为便于砂纸打磨一般为1.05~1.15,同时,由于二道底漆涂膜中PVC大于CPVC,底漆涂膜空隙多,有利于第一道面漆涂层的渗入,可以提高层间结合力。
表4-11中四个不同油度(66%、60%、55%、50%)的4种醇酸树脂,以不同PVC(0~60%)制成色漆,在碳钢板上制得厚度为35~40μm的涂膜,干燥7d,测定涂膜在碳钢板上的附着力,则PVC与附着力的关系如图4-1所示。

图4-1 0~60%PVC对不同油度铁红醇酸树脂涂料附着力的影响(1kgf/cm2=98.0665kPa)
1—50%油度醇酸树脂;2—55%油度醇酸树脂;3—60%油度醇酸树脂;4—66%油度醇酸树脂
由图4-1可以看出,油度下降,聚合物分子上的极性基团如羟基、羧基和酯基增加,这些基团提供了涂膜的附着力。油度增加,涂膜在干燥过程中交联密度增加,导致内应力增加和涂膜收缩,因而附着力下降。加入颜料可以提高附着力。随树脂不同,达到某一颜料体积浓度时,附着力达到最高值,越过此点,颜料再多加,则附着力下降。
上述66%、60%、55%、50%油度的4种醇酸树脂和氧化铁红分别制成的色漆,其最大附着力及CPVC为:
油度/% 66 60 55 50
CPVC/% 45 38 30 25
附着力(最大值)/MPa 24.51 30.40 32.36 35.30
高于或低于CPVC,则附着力急剧下降。但此CPVC值低于按吸“醇酸树脂”量法测得的CPVC值。氧化铁红醇酸树脂漆,虽在CPVC时达到最高值,但涂膜的拉伸强度与坚韧度很差,正确选择颜料的用量以达到涂膜的各项性能都符合要求。
2.颜基比——简化色漆设计工序的参数
如上所述,颜料体积浓度PVC是色漆配方设计的依据,但计算不如颜料与基料的质量比简便直观,故在醇酸色漆的配方计算中常用颜基比法。
颜料与基料的质量比简称颜基比。它可以定义为在色漆配方中颜料(包括体质颜料)的质量与基料(涂料中非挥发的液体部分)的质量之比。即:
颜基比=颜料质量∶基料质量
对常用的色漆配方进行分析可以看出,用途不同的色漆,配方中采用不同的颜基比,一般面漆的颜基比为(0.25~0.9)∶1,底漆的颜基比为(2.0~4.0)∶1。
3.醇酸树脂面漆的PVC和颜基比范围
(1)不同醇酸树脂面漆的PVC范围
醇酸树脂漆的品种有清漆、磁漆、调合漆、底漆、二道底漆、防锈漆、腻子等品种。按涂膜光泽又分为高光、亚光、无光等。设计醇酸树脂色漆的配方,其PVC与涂膜光泽度对应的关系大致为:
PVC/% 涂膜光泽度/%
3~20 有光在85以上
40~55 亚光20~30
55~60 无光在5以下
(2)醇酸磁漆
在醇酸树脂色漆中,醇酸磁漆是非常成熟、应用很广的一种面漆。它的PVC较低,一般为3%~20%,不加或加极少量的填料(如作消光用),这也是和醇酸调合漆的主要差别(另外,醇酸树脂指标也不同)。醇酸磁漆具有良好的装饰性和户外耐久性,既可常温干燥,也可烘干,既是一种通用的民用漆,也可制成各种工业漆,如卡车、农机、建筑机械等。在醇酸磁漆的基础上,通过增大PVC或加入消光剂可以生产出亚光漆或无光漆。有代表性的中油度醇酸树脂磁漆(牌号C04-2)配方列于表4-15。
表4-15 C04-2醇酸磁漆配方

①原配方中的中铬黄要用低毒的颜料代替,参见本章第一节有关部分。
②氧化铅主要起催干作用,可用氧化锆代替。
③铅催干剂可用稀土催干剂代替。
④溶剂适量,要用低毒溶剂取代。
从表4-15可以看出,醇酸磁漆的颜色由深至浅,其PVC从低至高变化(2.69%~16.4%),颜基比是(0.15∶1.0)~(0.77∶1.0)。配方中不用填料,白色颜料不用锐钛型钛白粉和立德粉,而用耐久性好的金红石型钛白粉,都是“吃的细粮”,才能保证醇酸磁漆的性能优良。这是20世纪80~90年代设计和使用的配方,对原料选择考虑环保要求少一些。
传统的C04-64醇酸半光磁漆的光泽度为30%±10%,PVC为30%~40%;而C04-83醇酸无光磁漆的光泽度小于10%,PVC为40%~50%。
其他醇酸色漆,如长油度醇酸色漆,醇酸树脂质量分数在70%以上,颜料含量较低,PVC在10%左右。醇酸底漆,如铁红醇酸底漆,通常用中油度醇酸树脂,质量分数在35%左右,PVC在40%左右。
醇酸二道底漆,特点是颜料少而填料多,应用于底漆之上,以填充底漆的孔隙。PVC为45%~50%。
醇酸腻子,刮涂施工,以滑石粉、碳酸钙等填料为主,PVC在70%以上。
水性醇酸树脂漆和用醇酸树脂制备的硝基漆、氨基漆等,将在后面章节中叙述。
(3)醇酸调合漆
醇酸磁漆综合性能好,是醇酸树脂涂料中的主流产品。但只用着色颜料,一般不用填料,树脂只用双漂植物油(精制油)或纯度高的脂肪酸和其他化工单体,成本较高。为降低醇酸树脂面漆成本,在20世纪80年代,醇酸树脂涂料制造者逐渐尝试在面漆中添加一些填料,使价格高的着色颜料在涂料中尽量减少,这势必要提高颜基比,使面漆光泽度、硬度等达不到醇酸磁漆的质量水平,特别是耐久性逊于醇酸磁漆较多,但却大大优于酯胶调合漆。由于成本降低,又易于施工,受到市场特别是住房建筑业的青睐,逐渐在业内发展成为一大类产品,取名为“醇酸调合漆”,制定了行业标准。最早用典型的干性油中油度醇酸树脂制造醇酸调合漆的参考配方列于表4-16。
表4-16 各色醇酸调合漆配方

从表4-16中可以看出,用填料(硫酸钡和碳酸钙),最少是灰色漆只用填料6%,因用了20%遮盖力弱的、便宜的立德粉,不便再多用填料。深色漆(黑色、红色、蓝色)用填料最多,达到20%以上。即使白色漆用钛白粉,也是性能差的锐钛型钛白粉。原料质量低,肯定影响涂膜性能。加上醇酸调合漆配方中颜基比高[(0.73~0.88)∶1.0],说明其涂膜中决定性能的醇酸树脂成膜物相对比例少,耐久性比醇酸磁漆要差很多。
表4-16所列配方是20世纪80年代前期所用的配方,使用标准的质量较好的干性油中油度醇酸树脂,算是第一代醇酸调合漆。当时,松香和植物油相比要便宜得多,采用松香代替植物油制醇酸调合树脂,松香用量为5%~10%,甚至更高,虽然对涂膜物理机械性能影响不大,但影响耐久性。后来,松香价格一路上涨,一度价格超过了干性油。为降低成本的醇酸调合树脂肯定是不能用松香了,另找一些化工副产物,如涤纶废丝、C5~C9石油树脂等。使醇酸调合树脂品种五花八门,如质量控制不当,会影响醇酸调合漆的质量。
(4)醇酸树脂底漆
醇酸树脂底漆是用途最广的底漆,C06牌号包括铁红醇酸底漆和防锈漆,主要性能是附着力好、防锈性强(以耐盐水性为标志),参考配方与性能要求见表4-17、表4-18。
表4-17 醇酸底漆、防锈漆配方

①这个品种使用历史久,但红丹(四氧化三铅)有剧毒,早已要求代用和禁用。锌黄含铅铬金属,也是要求代用和禁用的品种,这在本章第一节中已介绍。
②铁红醇酸底漆用中油度亚麻油和桐油(质量比1∶1)、苯酐、甘油醇酸树脂;醇酸防锈漆用季戊四醇、苯酐、亚麻油或梓油的长油度醇酸树脂。
表4-18 醇酸底漆、防锈漆性能要求

(5)醇酸树脂涂料技术标准
原化工部1967年确定,1975年和1982年两次修改,将涂料按成膜物树脂分成17大类,外加辅料1大类,这就是涂料行业实行30多年的18大类的分类标准。醇酸树脂涂料被列为第五类,品种牌号以汉语拼音的C为前冠,前面出现的C01-1、C01-7、C06-1、C02-4等是代表醇酸树脂清漆、底漆、磁漆的品种牌号。按成膜物为基础划分18大类的分类方法沿用了30多年,为行业核算统计、计划制定发挥了历史性作用,但随着科技的发展,人民生活水平的提高,涂料品种发展日新月异。一个品种包括几种成膜物是很普遍的,并且产品在不断地更新换代,高性能、低污染、功能性涂料迅速发展,有些传统的溶剂型涂料VOC含量高、污染重、质量低,逐步被淘汰。显然,18大类的分类方法是不适应涂料品种新发展形势的。这个分类标准现已废止。
根据涂料品种新发展形势,有关部门制定和颁布了涂料品种新的分类方法标准GB/T 2705—2003,将主要涂料产品类型分为建筑涂料、工业涂料、通用涂料及辅助材料,主要内容列为该标准的附录A(规范性附录),而原来18大类分类方法中的17大类列为附表B.2,18大类中的辅助材料大类列为附表B.3。新的分类方法标准实际包括了原来18大类分类标准中的主要分类的内容,只是主要分类方法显得合理一些。
在近二三十年,我国涂料的生产和技术得到迅速发展,2009年涂料产量跃居世界首位,自然带动了量大面广的醇酸树脂涂料迅速发展。尽管产品标准制修订工作一般是滞后于生产与技术的发展,醇酸树脂涂料的生产与技术发展也推动其产品技术标准的制修订工作不断发展。醇酸树脂涂料产品应用广泛,品种有数十种之多,按原来18大类的分类的牌号分别制定的醇酸树脂涂料产品的技术标准,比较复杂。在20世纪90年代,经过整合、修订形成醇酸树脂涂料化工行业系列标准,分为底漆(HG/T 2009—1991的C06-1铁红醇酸底漆)、调合漆(HG/T 2455—1993各色醇酸调合漆)、磁漆(HG/T 2576—1994各色醇酸磁漆)、防锈漆(HG/T 3345—1999红丹醇酸防锈漆)等。简化了不少。
为适应新的发展,醇酸树脂涂料产品进一步整合与修订,联合醇酸清漆、色漆(底漆、防锈漆、调合漆和磁漆)一起合并为一个综合性醇酸树脂涂料标准,并升格为国家标准GB/T 25251—2010,2010年颁布并实行。这个标准简练合理,包括面较广,大大简化了以往标准的繁杂性,给执行带来许多方便。不管是用什么醇酸树脂、颜料,不管原料组成如何,只要达到标准要求就行。如防锈漆,红丹已禁用,可用其他低毒性防锈颜料(得到权威认证)达到防锈漆的标准要求,就是醇酸防锈漆,执行该标准。醇酸树脂色漆质量指标要求见表4-19。
表4-19 醇酸树脂色漆质量指标要求(GB/T 25251—2010)

续表

①含片状颜料和效应颜料,如铝粉、云母氧化铁、玻璃鳞片、珠光粉等的产品除外。
②含铝粉颜料的产品除外。
在醇酸树脂清漆中已介绍,表4-19所列的醇酸树脂色漆适用于木质、金属表面的保护和装饰。另外,强制性标准GB 18581—2009中规定,用于室内装饰装修用溶剂型醇酸树脂涂料,VOC≤500g/L,苯≤0.3g/L,二甲苯等苯类溶剂总量≤5g/L,对甲醛、重金属的含量都做了规定。是涉及醇酸树脂涂料的第一个强制性标准。
4.色漆的配制——配色和色浆发展
上面讨论了以PVC为基础的颜基比计算色漆配方,方法简便,适用一般色漆。对于单色漆,如果其颜色是红、黄、蓝、白、黑、金属光泽等几种颜色中的某一种单色,在选定了颜基比后,那只要采用选定量的对应的那种颜色的颜料即可。如白色漆,采用一种钛白粉颜料就可达到要求。如果是复色漆,如驼色、米黄色、中灰色等,在选定颜基比后,在颜料用量中,按配色要求,确定用两种以上的彩色颜料的相对比例调配才可达到要求。
非彩色之间只有明度的差别,彩色之间则有色调、明度和饱和度的差别。两种彩色板如果色调、明度和饱和度都相同,这两种样板所使用的颜料是完全相同的。如果这三个特性中的任何一个有差别,则两种彩色也是不同的。将两个颜色调节到视觉上相同或等同的方法称为颜色匹配。具体到涂料制造过程,便是彩色漆的配制,简称配色。
传统的配色方法,指的是国内涂料企业曾广泛应用的用色卡或标准颜色样板表示颜色,以人工目测的方法进行色差评定的彩色漆配制方法。首先结合工艺配方了解欲配制的颜色(以标准色卡、标准颜色样板或漆样)的色调范围,了解由哪几种颜料组成,哪种是主色,哪种是副色,色与色之间的关系如何,各占比例多少。一些彩色漆所用各种彩色颜料的相对比例也有经验数据的总结,在有关涂料制造专著中可以查到。在调色时,本着先调深浅、后调色调的原则细心调制。
例如,调制草绿色磁漆时,研磨漆浆中以铬黄浆为主,加入铁蓝浆调成暗绿色,逐渐调入铁蓝浆时色调渐深。如黑色调不够,在一定程度时补加少量炭黑浆(注意,因黑色加入铬黄浆中,也出现黑绿色,导致绿色加深),如能逐渐出现所需的草绿色,就不必使用其他色浆,有时若红色调不足,可以用少许铁红浆补调红色调,直至要求的颜色。所用色浆一般是企业自制,这种手工配色方法现已很少采用,基本多采用电脑配色。
色浆特别是水性乳胶涂料用的色浆已有专业化生产,配合电脑配色,大大提高色漆生产过程中配色效率。有关技术与方法在专门文献中已有介绍,这里不重复。水性色浆是将彩色颜料分散于水性乳胶涂料用的助剂中制成的,因水性乳胶涂料用的助剂通用性较强,适合制造水性乳胶涂料用的色浆,但这种方法不适合溶剂型工业涂料,故工业涂料用的色浆难以产业化。近来也有进展,醇酸、聚酯、丙烯酸、聚氨酯、环氧、硝基、氯化橡胶等溶剂型工业涂料用色浆均有专业厂家提供,正在行业内推广,工业涂料(溶剂型和非溶剂型)色漆生产工序可以大为简化。
5.醇酸树脂色漆制造工艺
(1)颜料在醇酸树脂中的分散
颜料在醇酸树脂漆料中均匀分散要经过润湿、分散与稳定分散的过程。涂料生产企业购进的颜料,其粒子大小是原级粒子、附聚的粒子(团粒)的混合体,研磨分散的设备是利用剪切力将团聚的颜料粒子打碎,使颜料粒径尽可能地接近其原级粒径(一般不易完全达到),而不是将颜料粒子继续粉碎成比原级粒径更小的颜料粒子。颜料分散的第一步是润湿。按配方将醇酸树脂、颜料、溶剂、助剂投入混料槽,在混料中借助搅拌的剪切力使树脂液和颜料粒子充分接触,树脂和溶剂分子逐步向颜料团粒内渗透,使颜料粒子表面存在的空气和潮气被树脂和溶剂置换,由原有的固/气界面(颜料颗粒/空气或潮气)转变为固/液界面[颜料颗粒/树脂或溶剂(或水)体系]。这个过程称为“润湿”,这是颜料在树脂中分散的重要的第一步。在研磨过程中,通过机械能(剪切力和冲击力)进一步使颜料团粒(附聚体)破碎,并使树脂或溶剂分子充分润湿颜料颗粒,形成更为细小的颜料分散体。通过润湿作用,颜料团粒逐步打散,树脂体系对颜料粒子表面逐步形成一个包覆层(图4-2)。

图4-2 颜料颗粒的分散与润湿过程
润湿、分散进行得较好,颜料粒子会被树脂(或溶剂)包覆层隔离开,由于位阻作用,阻止颜料粒子间团聚,可使颜料稳定分散在树脂体系中(图4-3)。

图4-3 空间位阻效应
也可利用特种助剂增强颜料颗粒表面电荷,无机颜料是添加阴离子分散助剂,使颜料粒子表面带负电层,进而使颜料颗粒表面都包围着一个双层离子电荷。当两个颜料颗粒彼此接近时,库仑排斥力占优势,从而改变它们的运行轨迹以避免更接近(图4-4)。有机颜料就要添加阳离子分散助剂,其作用相同。

图4-4 电荷稳定作用
(2)醇酸树脂涂料制造工艺
溶剂型涂料制造工艺过程是指将原料和半成品加工成色漆成品的过程,基本是物理过程。工序包括配料混合、研磨分散、调漆、过滤、包装、成品入库等。另外,要和仓储、运输、计量等工艺手段有机组合,确定整个工艺流程。
以白色醇酸磁漆制造工艺为例,其配方组成(质量分数)为:季戊四醇豆油醇酸树脂(固体分50%)82%,金红石型钛白粉25%,溶剂4.85%,催干剂、防结皮剂若干。颜料/基料≈0.6/1。其制造工艺如下。
①配料与混合 按配方规定的醇酸漆料和溶剂分别加入配料预混合罐中(按工艺要求,一般要预留部分漆料和溶剂),用高速分散机将其混合均匀,然后在搅拌下逐渐加入配方量的钛白粉颜料,提高高速分散机的转速,进行充分润湿和预分散,制得待研磨分散的白色漆浆。
②研磨 分散设备有球磨机、辊磨机、砂磨机等,但以砂磨机使用最多,砂磨机型号也较多,有立式密闭型、卧式、棒销式、篮式,各有优缺点,根据具体情况选用。将预混合好的白色的醇酸漆浆用砂磨机分散至细度合格(一般细度要求在20μm以下),即得合格的白色研磨醇酸漆浆,置于漆浆槽中贮存备用。这是一种基本调色漆浆,调入其他副色漆浆,可制备多种颜色磁漆产品。因为是制备白色醇酸磁漆,研磨好的醇酸漆浆置于可移动的容器中(一般是拉缸),继续进行后面的工序。
③调漆 将拉缸中的白色漆浆,通过手工移动或泵送的方式,加入调漆罐中。边搅拌边加入配方工艺中规定预留的部分漆料及催干剂、防结皮剂,混匀后加入预留溶剂调整黏度合格(如果是生产复色漆,就要按配色要求加入其他颜色的色浆调色合格)。
④过滤包装 经检验合格的色漆成品,经振动筛过滤后,进行计量包装、入库。
白色醇酸磁漆制造工艺流程如图4-5所示。

图4-5 白色醇酸磁漆制造工艺流程
图4-5是以白色醇酸磁漆为代表的制造工艺,其他的涂料(包括其他的面漆和底漆)的制造工艺是相似的。这是一种间歇式、半封闭式、半自动化的生产工艺,在加料、物料传送、中控等中手工操作较多,生产不连续,混料、拉缸、分散、调漆等工序多不密闭。是国内涂料企业普遍采用的醇酸树脂涂料传统生产工艺。
6.全自动、全密闭、连续化溶剂型涂料生产工艺
传统的溶剂型涂料生产工艺有溶剂挥发,造成溶剂损失,污染环境,劳动强度大,生产效率低,不适合大规模生产。国外早就推广全密闭、连续化、自动化溶剂型涂料生产工艺。笔者在20世纪90年代随团考察日本一家工厂就采用类似这样的生产工艺。车间年产量约3万吨,产品以生产聚酯和醇酸树脂漆为主,三班生产,自动控制,整个车间只有8名工人。
前几年国内有乳胶漆的全密闭、自动化、连续化生产工艺的报道,据说溶剂型涂料的全密闭、自动化的生产工艺也正在业内推广。曾有报道介绍了欧洲某涂料公司一个全密闭、连续化、自动化溶剂型涂料生产工艺。该工厂以单班生产计,年产量为2万吨,其中60%为乳胶漆,40%为溶剂型醇酸树脂漆,产品的80%为白色漆,另外20%用以制备各种彩色漆。因此该工厂还在另外地方配套生产400t/a的着色剂。全部工艺流程中,将各种原料贮存入仓(或罐)以后,则产品制造的全部过程完全可以按电脑设定的程序,在密闭容器内自动进行。故全厂(包括原料准备及成品仓库管理)只有52人。全自动化色漆生产工艺流程如图4-6所示。

图4-6 全自动化色漆生产工艺流程
1—溶剂槽罐车;2—溶剂贮罐;3—助剂贮罐;4—电子秤;5—溶剂型树脂贮罐;6—砂磨机;7—密闭式配料预混合罐;8—粉料计量秤;9—颜(填)料贮槽;10—着色剂贮罐;11—颜(填)料散装运车;12—袋装粉料倒袋机;13—乳液贮罐;14—乳液运输罐车;15—振动筛;16—灌装机;17—调色罐;18—调漆罐