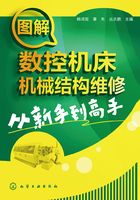
第3章 数控机床的主传动系统装调与维修
3.1 主轴调速系统的装调与维修
3.1.1 主轴变速方式
(1)无级变速
数控机床一般采用直流或交流主轴伺服电动机实现主轴无级变速,如图3-1所示。

图3-1 无级变速
(2)分段无级变速
有的数控机床在交流或直流电动机无级变速的基础上配以齿轮变速,使之成为分段无级变速,见图3-2。

图3-2 数控机床主传动的四种配置方式
① 分段无级变速的方式。
a.带有变速齿轮的主传动[图3-2(a)]。大中型数控机床较常采用的配置方式,通过少数几对齿轮传动,扩大变速范围。滑移齿轮的移位大都采用液压拨叉或直接由液压缸带动齿轮来实现。
b.通过带传动的主传动[图3-2(b)]。主要用于转速较高、变速范围不大的机床。适用于高速、低转矩特性的主轴。常用的是同步齿形带。
c.用两个电动机分别驱动主轴[图3-2(c)]。高速时由一个电动机通过带传动,低速时,由另一个电动机通过齿轮传动。两个电动机不能同时工作,也是一种浪费。
d.内装电动机主轴[电主轴,图3-2(d)]。电动机转子固定在机床主轴上,结构紧凑,但需要考虑电动机的散热。
② 分段无级变速机构。
a.液压拨叉变速机构。在带有齿轮传动的主传动系统中,齿轮的换挡主要都靠液压拨叉来完成,图3-3是三位液压拨叉的原理图。
通过改变不同的通油方式可以使三联齿轮块获得三个不同的变速位置。该机构除液压缸和活塞杆外,还增加了套筒4。当液压缸1通入压力油,而液压缸5卸压时[图3-3(a)],活塞杆2便带动拨叉3向左移动到极限位置,此时拨叉带动三联齿轮块移动到左端。当液压缸5通压力油,而液压缸1卸压时[图3-3(b)],活塞杆2和套筒4一起向右移动,在套筒4碰到油缸5的端部后,活塞杆2继续右移到极限位置,此时,三联齿轮块被拨叉3移动到右端。当压力油同时进入液压缸1和5时[图3-3(c)],由于活塞杆2的两端直径不同,使活塞杆处在中间位置。在设计活塞杆2和套筒4的截面直径时,应使套筒4的圆环面上的向右推力大于活塞杆2的向左的推力。液压拨叉换挡在主轴停车之后才能进行,但停车时拨叉带动齿轮块移动又可能产生“顶齿”现象,因此在这种主运动系统中通常设一台微电动机,无级变速的恒速交流电机驱动场合,通常需在传动链上安置一个微电机。正常工作时,离合器脱开,齿轮换挡时,主轴M1停止工作而离合器吸合,微电机M2工作,带动主轴慢速转动。同时,油缸移动齿轮,从而顺利啮合,如图3-4所示。

图3-3 三位液压拨叉工作原理图
1,5—液压缸;2—活塞杆;3—拨叉;4—套筒

图3-4 微电机工作齿轮变挡原理
图3-5为某分段变速箱液压变速机构。滑移齿轮的拨叉与变速液压缸的活塞杆相连接,三个液压缸都是差动液压缸,用Y型三位四通电磁阀来控制液压缸的通油。当液压缸左腔进油右腔回油、右腔进油左腔回油、左右两腔同时进油时,可使滑移齿轮块获得右、左、中三个位置,这样就可以获得所需要的齿轮啮合状态。在自动选速时,为了使齿轮顺利啮合而不发生顶齿现象,应使传动链在低速下运行。

图3-5 典型液压拨叉变速机构
b.电磁离合器变速。电磁离合器是应用电磁效应接通或切断运动的元件,由于它便于实现自动操作,并有现成的系列产品可供选用,因而它已成为自动装置中常用的操纵元件。电磁离合器用于数控机床的主传动时,能简化变速机构,通过若干个安装在各传动轴上的离合器的吸合和分离的不同组合来改变齿轮的传动路线,实现主轴的变速。如图3-6所示为THK6380型自动换刀数控铣镗床的主传动系统,该机床采用双速电机和六个电磁离合器完成18级变速。

图3-6 THK6380型自动换刀数控铣镗床的主传动系统
图3-7是数控铣镗床主轴箱中使用的无滑环摩擦片式电磁离合器。传动齿轮1通过螺钉固定在连接件2的端面上,根据不同的传动结构,运动既可以从齿轮1输入,也可以从套筒3输入。连接件2的外周开有六条直槽,并与外摩擦片4上的六个花键齿相配,这样就把齿轮1的转动直接传递给外摩擦片4。套筒3的内孔和外圆都有花键,而且和挡环6用螺钉11连成一体。内摩擦片5通过内孔花键套装在套筒3上,并一起转动。当线圈8通电时,衔铁10被吸引右移,把内摩擦片5和外摩擦片4压紧在挡环6上,通过摩擦力矩把齿轮1与套筒3结合在一起。无滑环电磁离合器的线圈8和铁芯9是不转动的,在铁芯9的右侧均匀分布着六条键槽,用斜键将铁芯固定在变速箱的壁上。当线圈8断电时,外摩擦片4的弹性爪使衔铁10迅速恢复到原来位置,内、外摩擦片互相分离,运动被切断。这种离合器的优点在于省去了电刷,避免了磨损和接触不良带来的故障,因此比较适合于高速运转的主运动系统。由于采用摩擦片来传递转矩,所以允许不停车变速。但也带来了另外的缺点,这就是变速时将产生大量的摩擦热,还由于线圈和铁心是静止不动的,这就必须在旋转的套筒上装滚动轴承7,因而增加了离合器的径向尺寸。此外,这种摩擦离合器的磁力线通过钢质的摩擦片,在线圈断电之后会有剩磁,所以增加了离合器的分离时间。

图3-7 无集电环摩擦片式电磁离合器
1—传动齿轮;2—连接件;3—套筒;4—外摩擦片;5—内摩擦片;6—挡环;7—滚动轴承;8—线圈;9—铁芯;10—衔铁;11—螺钉
图3-8为啮合式电磁离合器,它是在摩擦面上做了一定的齿形,来提高传递的扭力。线圈1通电,带有端面齿的衔铁2又通过渐开线花键与定位环5相连,再通过螺钉7与传动件相连。磁轭内孔的花键送给另一个轴,这样,就使与螺钉7相连的轴与另一轴同时旋转。隔离环6是防止传动轴分离一部分磁力线,进而削弱电磁吸引力。衔铁采用渐开线花键与定位环5相连是为了保证同轴度。
这种离合器必须在低于1~2r/min的转速下变速。

图3-8 啮合式电磁离合器
1—线圈;2—衔铁;3—螺钉;4—弹簧;5—定位环;6—隔离环;7—连接螺钉;8—旋转集电环;9—磁轭
与其他形式的电磁离合器相比,啮合式电磁离合器能够传递更大的转矩,因而相应地减小了离合器的径向和轴向尺寸,使主轴箱的结构更为紧凑。啮合过程无滑动是它的另一个优点,这样不但使摩擦热减少,有助于改善数控机床主轴箱的热变形,而且还可以在有严格要求的传动比的传动链中使用。但这种离合器带有旋转集电环8,电刷与滑环之间有摩擦,影响了变速的可靠性,而且还应避免在很高的转速下工作。另一方面,离合器必须在低于1~2r/min的转速下变速,这将给自动变速带来不便。根据上述特点,啮合式电磁离合器较适宜于在要求温升小和结构紧凑的数控机床上使用。
3.1.2 高速主轴结构
当今世界各国都竞相发展自己的高速加工技术,并成功应用,产生了巨大的经济效益。要发展和应用高速加工技术,首先必须有性能良好的数控机床,而数控机床性能的好坏则首先取决于高速主轴。高速主轴单元影响加工系统的精度、稳定性及应用范围,其动力学性能及稳定性对高速加工起着关键的作用。高速主轴是电动机转子装在主轴上,主轴就是电动机轴,多用在小型加工中心机床上。这也是近来高速加工中心主轴发展的一种趋势。
(1)高速主轴结构组成
数控机床的高速主轴单元包括动力源、主轴、轴承和机架(图3-9)等几个部分。高速主轴单元的类型有电主轴、气动主轴、水动主轴等。不同类型的高速主轴单元输出功率相差较大。高速加工机床要求在极短的时间内实现升降速,并在指定位置快速准停。这就需要主轴有较高的角减速度和角加速度。如果通过传动带等中间环节,不仅会在高速状态下打滑,产生振动和噪声,而且增加转动惯量,给机床快速准停造成困难。目前,随着电气传动技术的迅速发展和日趋完善,高速数控机床主传动系统的机械结构已得到极大的简化,基本上取消了带传动和齿轮传动。机床主轴由内装式电动机直接驱动,从而把机床主传动链的长度缩短为零,实现了机床的“零传动”。这种主轴电动机与机床主轴“合二为一”的传动结构形式,使主轴部件从机床的主传动系统和整体结构中相对独立出来,因此可做成“主轴单元”,俗称“电主轴”。由于当前电主轴主要采用的是交流高频电动机,故也称为“高频主轴”。由于没有中间传动环节,有时又称它为“直接传动主轴”。电主轴是一种智能型功能部件,它采用无外壳电动机,将带有冷却套的电动机定子装配在主轴单元的壳体内,转子和机床主轴的旋转部件做成一体,主轴的变速范围完全由变频交流电动机控制,使变频电动机和机床主轴合二为一。电主轴具有结构紧凑、重量轻、惯性小、振动小、噪声低、响应快等优点,不但转速高、功率大,还具有一系列控制主轴温升与振动等机床运行参数的功能,以确保其高速运转的可靠性与安全性。使用电主轴可以减少带传动和齿轮传动,简化机床设计,易于实现主轴定位,是高速主轴单元中的一种理想结构。

图3-9 高速主轴
(2)电主轴结构
电主轴基本结构如图3-10所示。用于大型加工中心的内装式电主轴单元由主轴轴系1、内装式电动机2、支撑及其润滑系统3、冷却系统4、松拉刀机构5、轴承自动卸载系统6、编码器安装调整系统7组成。

图3-10 加工中心用电主轴结构简图
1—主轴轴系;2—内装式电动机;3—支撑及其润滑系统;4—冷却系统;5—松拉刀机构;6—轴承自动卸载系统;7—编码器安装调整系统
(3)高速主轴维护
① 电主轴的润滑。电动机内置于主轴部件后,发热不可避免,从而需要设计专门用于冷却电动机的油冷或水冷系统。滚动轴承在高速运转时要给予正确的润滑,否则会造成轴承因过热而烧坏。
a.油气润滑方式(图3-11)。用压缩空气把小油滴送进轴承空隙中,油量大小可达最佳值,压缩空气有散热作用,润滑油可回收,不污染周围空气。根据轴承供油量的要求,定时器的循环时间可从1~99min定时。

图3-11 油气润滑
b.喷注润滑方式(图3-12)。用较大流量的恒温油(每个轴承3~4L/min)喷注到主轴轴承,以达到冷却润滑的目的。回油则不是自然回流,而是用两台排油液压泵强制排油。

图3-12 喷注润滑系统
c.凸入滚道式润滑方式(图3-13)。润滑油的进油口在内滚道附近,利用高速轴承的泵效应,把润滑油吸入滚道。若进油口较高,则泵效应差,当进油接近外滚道时则成为排放口了,油液将不能进入轴承内部。

图3-13 凸入滚道润滑用特种轴承
② 电主轴的冷却。为了尽快使高速运行的电主轴散热,通常对电主轴的外壁通以循环冷却剂,而冷却剂的温度通过冷却装置来保持。高速电主轴的冷却系统主要依靠冷却液的循环流动来实现,而且流动的冷却压缩空气能起到一定的冷却作用,如图3-14所示为某型号电主轴油水热交换循环冷却系统示意图,为了保证安全,对定子采用连续、大流量循环油冷。其输入端为冷却油,将电动机产生的热量从输出端带出,然后流经逆流式冷却交换器,将油温降到接近室温并回到油箱,再经压力泵增压输入到主轴输入端从而实现电主轴的循环冷却。图3-15为冷却油流经路线。

图3-14 电主轴油水热交换循环冷却系统

图3-15 电主轴冷却液流经路线
③ 高速主轴的动平衡。高速主轴的最高转速一般在10000r/min以上,有的高达60000~100000r/min,主轴运转部分微小的不平衡量,都会引起巨大的离心力,造成机床的振动,导致加工精度和表面质量下降。因此,首先电主轴应严格遵循对称设计的原则,其次,要采取相应的一些工艺措施使转子在装配后达到动平衡,甚至设计专门的自动平衡系统来实现主轴的动平衡。
a.高速机床刀具系统的动平衡方法。
方法1:在制造阶段对刀具和刀柄分别进行动平衡,动平衡包括各种圆柱铣刀、盘铣刀等加工中心用的刀具和刀柄。平衡的方法是用动平衡机检测不平衡量和偏移位置,然后在相反的位置切去相应的量。这一工作应该由刀具和刀柄生产厂家完成。高速加工中心的用户应该尽可能选用平衡指标满足要求的刀具和刀柄。
方法2:采用可调平衡刀柄。尽管已经使用分别经过动平衡的刀具和刀柄,但在实际加工中,由于刀具要夹紧在刀柄上,然后由拉杆拉紧在主轴锥孔里。由于有多个中间装配环节的影响,往往会出现总体不平衡量满足不了加工质量要求的情况。这时,需要对“刀具-刀柄”的总体组合检测其不平衡量,然后调整可调平衡刀柄,最后达到总体平衡的要求。
常用的可调平衡刀柄是在标准刀柄上增加可调平衡的部件。一种是在刀柄的外端面上钻出一系列平行于轴线的螺纹孔,用固定螺钉进行调节,根据所需要的平衡量旋入或退出螺钉,也就是调整刀柄的径向重心位置。在刀具和刀柄装在一起后在动平衡机上检测不平衡量,然后手动调整。另一种是采用带有平衡调整环的刀柄。美国肯纳金属公司采用这种可调平衡刀柄,如图3-16所示。

图3-16 具有平衡环的可调平衡刀柄
调整平衡的过程如下(图3-17)。

图3-17 平衡环调整示意图
?把刀具和刀柄连接并锁紧。
?调整环相隔180°布置并锁紧定位螺钉。
?把装配好的刀具刀柄放在动平衡机上测量不平衡量和方位。
?在刀柄上标出不平衡点的位置,并从平衡调整表中查出平衡环的调整角度。
?按照表中角度旋转带刻度的调整环,并锁紧螺钉。
?再在动平衡机上检查调整结果。
?若不满足,重复上述步骤继续调整。调整标准可用G等级标准,也可以根据实际要求确定。
下面举例说明调整方法。已知刀具质量2.75kg,主轴转速12000r/min,采用平衡等级G2.5。
首先由式
式中 G——G等级量,g·mm/kg;
m——刀具质量;
n——主轴转速。
计算出G2.5的不平衡量U=5.47g·mm。
在动平衡机上测量出不平衡量是25g·mm,重心在60°位置处。
根据刀柄平衡调整后列出的不平衡量调整参数表,查出对应的调整角度,设调整环直径为50~60mm,查出的调整角度为112°。
用六角扳手把上下调整环分别向相反方向转112°,锁紧定位螺钉。
然后再放在动平衡机上检测不平衡量,若是等于或小于5g·mm,即为满足要求。
方法3:仅仅调整刀具和刀柄的平衡往往还不够,不平衡的主轴也会使原本平衡的刀柄发挥不了它应有的潜力。平衡刀柄系统应该能够针对各种主轴转速自动调节平衡。为了更精确地调整平衡,最好的方法是把刀具装在主轴上,在工作转速下测量和调整平衡。美国肯纳金属公司最近开发出一种可以调节主轴系统自动平衡的刀柄系统(Total Automatic Balancing System),简称TABS刀柄,也称全自动平衡刀柄。刀柄和测量控制调整装置一起组成了刀具自动平衡系统。
自动调整系统由TABS刀柄、微机控制器、测量支架、测振传感器和固定调整线圈组成。测量支架、测振传感器和固定调整线圈装在机床工作台上,测振传感器有两个,成90°安装,分别测量两个方向的刀具振动。调整线圈安装在支架上,线圈和传感器均连接到计算机上。计算机配备有测量和计算不平衡量的程序,能够在PC机上显示主轴转速,计算振动量和平衡量,并且向调整线圈发出调整控制信号。
TABS刀柄的基本工作原理是在刀柄的平衡环中装有永磁体,可对有两个平衡块的转子进行定位。在计算机测量出不平衡量和位置时,向线圈发出脉冲信号,由线圈中产生的电磁量改变刀柄中永磁体的位置,达到消除不平衡量的目的。
调整时,将装有TABS刀柄的主轴移动到线圈中心,开动机床。在计算机控制下,几秒钟内即可完成自动调整。
b.主轴动平衡。主轴动平衡系统有不同的类型,如图3-18所示是一种机电动平衡系统,整个系统装在高速主轴内,包含有两个内装电子驱动元件,并有两个可在轴上做相对转动的平衡重块。
该系统的平衡块在断电时仍保持在原位置上不动,所以停机后重新启动时主轴的平衡状态不会发生变化。

图3-18 机电动平衡系统
1—信号无线输送单元;2—紧固法兰;3—内装电子驱动元件的平衡块;4—磨床主轴
④ 主轴的防尘与密封。电主轴是精密部件,在高速运转情况下,任何微尘进入主轴轴承,都可能引起振动,甚至使主轴轴承咬死。由于电主轴电动机为内置式,过分潮湿会使电动机绕组绝缘变差,甚至失效,以致烧坏电动机。因此,电主轴必须防尘与防潮。由于电主轴定子采用循环冷却剂冷却,主轴轴承可能采用油-气润滑,因此,防止冷却及润滑介质进入电动机内部非常重要。另外,还要防止高速切削时的切削液进入主轴轴承,因此,必须做好主轴的密封工作。
(4)电主轴的选用
电主轴选用的一般原则:首先,要熟悉和了解电主轴的结构特点、基本性能、主要参数、润滑和冷却的要求等基本内容;其次,结合目前具备的条件,如机床的类型及特点、电源条件、润滑气源条件、冷却条件、加工产品特点等诸多因素来考虑如何正确选择适宜的电主轴。
实际上,选用电主轴最重要的是选定其最高转速、额定功率、转矩和转矩与转速的关系。主要应该注意以下几点。
① 从实际需要出发,切忌“贪高(高转速)求大(大功率)”,以免造成性能冗余、资金浪费、维护费事,以致后患无穷。
② 根据实际可行的切削规范,对多个典型工件的多个典型工序多做计算。
③ 不要单纯依靠样本来选用,而应多与供应商的销售服务专家深入交谈,多听他们的有益建议。
④ 注意正确选择轴承类型与润滑方式。在满足需求的条件下,应尽量选用陶瓷球混合轴承与永久性油润滑的组合,这样可省去润滑部件并方便维护。
3.1.3 传动带
带传动是传统的传动方式,常见的有V带、平带、多联V带、多楔带和齿形带。为了定位准确,常用多楔带和齿形带。
(1)多联V带
多联V带又称复合V带(如图3-19所示),有双联和三联两种,每种都有3种不同的截面,横断面呈楔形,如图3-20所示,楔角为40°。多联V带是一次成形,不会因长度不一致而受力不均,因而承载能力比多根V带(截面积之和相同)高。同样的承载能力,多联V带的截面积比多根V带小,因而重量较轻,耐挠曲性能高,允许的带轮最小直径小,线速度高。多联V带传递负载主要靠强力层。强力层中有多根钢丝绳或涤纶绳,具有伸长率小和较大的抗拉强度和抗弯疲劳强度。带的基底及缓冲楔部分采用橡胶或聚氨酯。

图3-19 多联V带(一)

图3-20 多联V带(二)
(2)多楔带
如图3-21所示,多楔带综合了V带和平带的优点。运转时振动小,发热少,运转平稳,重量轻。因此在40m/s的线速度下来使用。此外,多楔带与带轮的接触好,负载分配均匀,即使瞬时超载,也不会产生打滑,而传动功率比V带大20%~30%。因此,能够满足加工中心主轴传动的要求。在高速、大转矩下也不会打滑。多楔形带安装时需要较大的张紧力,因此,使主轴和电动机承受了较大的径向负载。

图3-21 多楔带的结构
多楔带有H型、J型、K型、L型、M型等,数控机床上常用的多楔带有J型齿距为2.4mm、L型齿距为4.8mm、M型齿距为9.5mm三种规格。根据图3-22可大致选出所需的型号。

图3-22 多楔带型号选择
(3)齿形带
① 齿形带简介。齿形带又称为同步齿形带,根据齿形不同又分为梯形同步齿带和圆弧齿同步带,如图3-23所示。图示是两种齿形带的纵断面,其结构与材质和楔形带相似,但在齿面上覆盖了一层尼龙帆布,用以减少传动齿与带轮的啮合摩擦。梯形齿同步带在传递功率时,由于应力集中在齿根部位,使功率传递能力下降。同时由于与带轮是圆弧形接触,当带轮直径较小时,将使齿变形,影响了与带轮齿的啮合,不仅受力情况不好,而且在速度很高时,会产生较大的噪声与振动,这对于主传动来说是不利的。因此,在加工中心的主传动中很少采用,一般仅在转速不高的运动传动或小功率的动力传动中使用。而圆弧齿同步带克服了梯形齿同步带的缺点,均化了应力,改善了啮合。因此,在加工中心上,无论是主传动还是伺服进给传动,当需要用带传动时,总是优先考虑采用圆弧齿形同步带。

图3-23 同步齿形带
1—强力层;2—带齿;3—带背
同步齿形带具有带传动和链传动的优点,与一般的带传动相比,它不会打滑,且不需要很大的张紧力,减少或消除了轴的静态径向力;传动效率高达98%~99.5%;可用于60~80m/s的高速传动。但是在高速使用时,由于带轮必须设置轮缘,因此在设计时要考虑轮齿槽的排气,以免产生“啸叫”。
同步齿形带的规格是以相邻两齿的节距来表示的(与齿轮的模数相似),主轴功率为3~10kW的加工中心多用节距为5mm或8mm的圆弧齿形带,型号为5M或8M。根据图3-24可大致选出所需的型号。

图3-24 同步齿形带型号选择
② 应用齿形带的注意事项。
a.为了使转动惯量小,带轮由密度小的材料制成。带轮所允许的最小直径,根据有效齿数及平带包角,由齿形带厂确定。
b.为了避免离合器引起的附加转动惯量,在驱动轴上的带轮应直接安装在电动机轴上。
c.为了对齿形带长度的制造公差进行补偿并防止间隙,同步齿形带必须预加载。预加载的方法可以是电动机的径向位移或是安装张力轮。
d.对较长的自由齿形带(大于带宽9倍),为衰减带振动常用张力轮。
张力轮可以是安装在齿形带内部的牙轮,但是更好的方式是在齿形带外部采用圆筒形滚轮,这种方式使齿形带的包角增大,有利于传动。为了减少运动噪声,应使用背面抛光的齿形带。