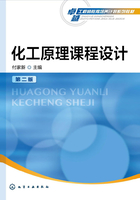
2.2 搅拌装置工艺设计
通常,搅拌装置的设计应遵循以下三个过程:①根据搅拌目的和物系性质进行搅拌装置的选型;②在选型的基础上进行工艺设计计算;③进行搅拌装置的机械设计与费用评价。搅拌装置设计中最重要的是搅拌功率与传热过程的计算。
2.2.1 搅拌功率工艺设计计算
2.2.1.1 搅拌功率特征数关联式
影响搅拌功率的因素来自于三个方面:①桨和槽的几何参数;②桨的操作参数;③被搅拌物系的物性参数。对于搅拌过程,一般可采用相似理论和量纲分析的方法得到其特征数关系式。为了简化分析过程,可假定桨、槽的几何参数均与搅拌器的直径有一定的比例关系,并将这些比值称为形状因子。对于特定尺寸的系统,形状因子一般为定值,故桨、槽的几何参数仅考虑搅拌器的直径。桨的操作参数主要指搅拌器的转速。物性参数主要包括被搅拌流体的密度和黏度。当搅拌发生打旋现象时,重力加速度也将影响搅拌功率。
通过量纲分析可得
Np=K0RexFry (2-1)
式中,,功率数或功率特征数;
,搅拌雷诺数,可衡量流体的流动状态;
,弗劳德数,表示流体惯性力与重力之比,用以衡量重力的影响;N为搅拌功率,W;d为搅拌器直径,m;ρ为流体的密度,kg/m3;μ为流体的黏度,Pa·s;n为搅拌转速,r/s;g为重力加速度,m/s2;K0为系数,量纲为1;x、y为指数,量纲为1。
若再令,称为功率因数,则
ф=K0Rex (2-2)
注意:功率因数ф与功率数Np是两个完全不同的概念。
从量纲分析法得到搅拌功率数的关系式后,可对一定形状的搅拌器进行一系列的实验,找出各流动范围内具体的经验公式或关系算图,则可解决搅拌功率的计算问题。
2.2.1.2 搅拌功率计算
关于搅拌功率计算的经验公式很多,研究最多的是均相系统,并以它为基础来研究非均相物系搅拌功率的计算。
Ⅰ.均相物系搅拌功率的计算
此处介绍均相物系搅拌功率的两种求算方法:拉什顿算图和永田进治公式。
(1)拉什顿(Rushton)算图
拉什顿的ф-Re关系曲线示于图2-2。图中以功率因数ф为纵坐标,雷诺数Re为横坐标,给出了8种不同桨型的搅拌器在有挡板或无挡板条件下的关系曲线。由图中曲线可看出:搅拌槽中流体的流动可根据Re的大小大致分为三个区域,即层流区、过渡区和湍流区。
当Re≤10时为层流区。在此区内搅拌时不会出现打旋现象,此时重力对流动几乎没有影响,即对搅拌功率没有影响。因此,反映重力影响的Fr可以忽略。
从图2-2还可以看出,在层流区内,不同搅拌器的ф与Re在对数坐标上为一组斜率相等的直线,其斜率均为-1。所以在此区域内有

图2-2 拉什顿的ф-Re关系算图
1—三叶推进式,s=d,N;2—三叶推进式,s=d,Y;3—三叶推进式,s=2d,N;4—三叶推进式,s=2d,Y;5—六片平直叶圆盘涡轮,N;6—六片平直叶圆盘涡轮,Y;7—六片弯叶圆盘涡轮,Y;8—六片箭叶圆盘涡轮,Y;9—八片折叶开启涡轮(45°),Y;10—双叶平桨,Y;11—六叶闭式涡轮,Y;12—六叶闭式涡轮(带有二十叶的静止导向器);s—桨叶螺距;d—搅拌器直径;Y—有挡板;N—无挡板
式中,K1为系数,量纲为1。
于是 N=фρn3d5=K1μn2d3 (2-3)
当Re=10~104时为过渡区,此时功率因数ф随Re的变化不再是直线,各种搅拌器的曲线也不大一致,这说明斜率不再是常数,它随Re而变化。当搅拌槽内无挡板并且Re>300时,液面中心处会出现漩涡,重力将影响搅拌功率,即Fr数对功率的影响不能忽略。此时有
(2-4)
经曲线变换得。
式中,ζ1、ζ2为与搅拌器型式有关的常数,量纲为1,其数值可从表2-5中查得。
表2-5 当300<Re<104时一些搅拌器的ζ1、ζ2值

此时搅拌功率的计算式为
(2-5)
在过渡区,无挡板且Re<300,或有挡板并且符合全挡板条件及Re>300时,流体内不会出现大的旋涡,Fr数的影响可以忽略。这时搅拌功率仍可用式(2-3)进行计算,计算时可直接由Re数在Rushton算图中查得ф值。
在搅拌湍流区,即Re>104时,一般均采用全挡板条件,消除了打旋现象,故重力的影响可以忽略不计。在Rushton算图中表现为:ф值几乎不受Re和Fr的影响而成为一条水平直线,即
ф=Np=K2
因此 N=K2ρn3d5 (2-6)
式中,K2为系数,量纲为1。该式表明:在湍流区全挡板条件下ф=Np=K2=定值,流体的黏度对搅拌器的功率不再产生影响。
采用Rushton算图计算搅拌功率是一种很简便的方法,在使用时一定要注意每条曲线的应用条件。只有符合几何相似条件,才可根据搅拌器直径d、搅拌器转速n和流体密度ρ、黏度μ值计算出搅拌Re数,并在算图中相应桨型的功率因数曲线上查得ф值,再根据流动状态分别选用式(2-3)~式(2-6)来求得搅拌器的搅拌功率。
(2)永田进治公式
①无挡板时的搅拌功率 日本永田进治等根据在无挡板直立圆槽中搅拌时“圆柱状回转区”半径的大小及桨叶所受的流体阻力进行了理论推导,并结合实验结果确定了一些系数而得出双叶搅拌器功率的计算公式。
(2-7)
(2-8)
(2-9)
(2-10)
式中,A、B为系数;p为指数;b为桨叶的宽度,m;D为搅拌槽内径,m;H为槽内流体的深度,m;θ为桨叶的折叶角,对于平桨θ=90°。
现就永田进治公式作几点讨论。
·当b/D≤0.3时,式(2-10)中的第四项7(b/D)4与其他项相比很小,可以忽略不计,而目前所使用的桨式搅拌器大多都能满足这一要求。
·对于高黏度流体,搅拌的Re数较小,属于层流,式(2-7)中右边第一项占支配地位,第二项与其相比很小,可以忽略不计。因此式(2-7)可简化为
(2-7a)
该式结果与式(2-3)是完全一致的。
·对于低黏度流体的搅拌,Re数较大,搅拌处于湍流区。此时式(2-7)中的第一项很小,可以忽略不计,第二项中的几何参数对于一定的桨型都是常数,B和ф值也是常数。于是式(2-7)可简化为
(2-7b)
式中,B'为系数,量纲为1。即在湍流区时,Np近似为常数,而与Re的大小无关,这一结论与式(2-6)是一致的。
·在湍流区,当搅拌器的桨径相同且桨叶宽度b和桨叶数量z的乘积相等,则它们的搅拌功率就相等。如果装有多层桨叶,只要符合桨叶宽度b与桨叶数量z的乘积相等这一条件,则它们的搅拌功率也相等。
·永田进治公式可近似用于桨式、多叶开启涡轮、圆盘涡轮等常用桨型无挡板湍流区搅拌功率的计算。
②全挡板条件下的搅拌功率 将湍流区全挡板条件下的ф线沿水平线向左延长,与层流区向下延长的ф线有一交点,此交点可看做是湍流区和层流区的转变点,对应于此点的雷诺数称为临界雷诺数,以Rec表示。将Rec值代入式(2-7)中,便可求得全挡板条件下的搅拌功率。Rec的数值与搅拌器的型式有关。对于不同尺寸的平直叶双桨搅拌器,Rec值可由下式计算,即
(2-11)
式中,Rec为临界雷诺数,量纲为1。
③高黏度流体的搅拌功率 高黏度流体搅拌功率的计算可参考有关文献。
Ⅱ.非均相物系搅拌功率的计算
(1)不互溶液-液相搅拌的搅拌功率
在计算液-液相搅拌功率时,首先求出两相的平均密度ρm,然后再按均相物系搅拌功率的计算方法求解。液-液相物系的平均密度为
ρm=xvρd+(1-xv)ρc (2-12)
式中,ρm为两相的平均密度,kg/m3;ρd为分散相的密度,kg/m3;ρc为连续相的密度,kg/m3;xv为分散相的体积分数,量纲为1。
当两相液体的黏度都较小时,其平均黏度μm可采用下式计算
(2-13)
式中,μm为两相的平均黏度,Pa·s;μd为分散相的黏度,Pa·s;μc为连续相的黏度,Pa·s。
(2)气-液相搅拌的搅拌功率
当向液体通入气体并进行搅拌时,通气搅拌的功率Ng要比均相系液体的搅拌功率N低。Ng/N的数值取决于通气系数Na的大小。通气系数Na依下式计算
(2-14)
式中,Qg为通气速率,m3/s;Na为通气系数,量纲为1。
一些搅拌器的通气搅拌功率Ng与均相系搅拌功率N之比和通气系数Na的实验关系曲线如图2-3所示(图中Z为搅拌器距槽底的高度,m)。一般Na越小,气泡在搅拌槽内越容易分散均匀,所以从图2-3上可看出当Ng/N在0.6以上时,Na是比较合适的。

图2-3 通气系数与功率比的关系
搅拌条件:d=D/3,H=D,Z=D/3,全挡板 1—八片平直叶圆盘涡轮;2—八片平直叶上侧圆盘涡轮;3—十六片平直叶上侧圆盘涡轮;4—六片平直叶圆盘涡轮;5—平直叶双桨
当采用六片平直叶圆盘涡轮式搅拌器进行气相分散搅拌时,搅拌功率的比值Ng/N可由下式计算
(2-15)
(3)固-液相搅拌的搅拌功率
当固体颗粒的体积分数不大,并且颗粒的直径也不很大时,可近似地看做是均匀的悬浮状态,这时可取平均密度ρm和黏度μm来代替原液相的密度和黏度,以ρm、μm作为搅拌介质的物性,然后按均一液相搅拌来求得搅拌功率。固-液相悬浮液的平均密度ρm为
ρm=xvsρs+ρ(1-xvs) (2-16)
式中,ρm为固-液相悬浮液的平均密度,kg/m3;ρs为固体颗粒的密度,kg/m3;ρ为液相的密度,kg/m3;xvs为固体颗粒的体积分数,量纲为1。
当悬浮液中固体颗粒与液体的体积比ψ≤1时
μm=μ(1+2.5ψ) (2-17)
当ψ>1时,则 μm=μ(1+4.5ψ) (2-18)
式中,μm为固-液相悬浮液的平均黏度,Pa·s;μ为液相的黏度,Pa·s;ψ为固体颗粒与液体的体积比,量纲为1。
固-液相的搅拌功率与固体颗粒的大小有很大的关系,当固体颗粒直径在0.074mm(200目)以上时,采用上述方法所计算的搅拌功率比实际值偏小。
2.2.2 搅拌器工程放大
2.2.2.1 放大基本原则
根据相似理论,要放大推广实验参数,就必须使两个系统具有相似性,如:
几何相似——实验模型与生产设备的相应几何尺寸的比例都相等;
运动相似——几何相似系统中,对应位置上流体的运动速度之比相等;
动力相似——两几何相似和运动相似的系统中,对应位置上所受力的比值相等;
热相似——两系统除符合上述三个相似的要求外,对应位置上的温差之比也相等。
由于相似条件很多,有些条件对同一个过程还可能有矛盾的影响,因此,在放大过程中,要做到所有的条件都相似是不可能的。这就要根据具体的搅拌过程,以达到生产任务的要求为前提条件,寻求对该过程最有影响的相似条件,而舍弃次要因素,即要将复杂的范畴变成相当单纯的范畴。两系统几何相似是相似放大的基本要求。
应予指出,动力相似的条件是两个系统中对应点上力的比值相等,即其无量纲特征数必相等。
若搅拌系统中不止一个相,则混合时还要克服界面之间的抗拒力,即界面张力σ,于是还要考虑表示施加力与界面张力之比的特征数(韦伯数)对搅拌功率的影响,韦伯数定义为:。此时搅拌功率特征数关系式应改写为
Np=f(Re,Fr,We)
在两个几何相似的系统中搅拌同一种液体时,若实现这两个系统动力相似,必须同时满足下列关系(下标1、2分别代表两个相似系统)
当Re1=Re2时,;当Fr1=Fr2时,
;当We1=We2时,
。
对于同一种流体而言,物性常数ρ、μ和σ在两个系统中均为定值,因此上述三等式不可能同时满足。补救的办法是尽量抑制或消除重力和界面张力因素的影响,从而减少相似条件。
2.2.2.2 放大方法
搅拌器的放大,一般可分为两大类:一类是按功率数放大,另一类是按工艺过程结果放大。
(1)按功率数放大
若两个搅拌系统的构型相同,不管其尺寸大小如何,它们可以使用同一功率曲线。
如果两个搅拌系统的构型相同,搅拌槽具有全挡板条件,则搅拌时不会产生打旋现象,再若被搅拌的流体又为单一相的条件,两个系统的功率特征数关系式可简化为
Np=f(Re)
这样通过测量小型设备的搅拌功率便可推算出生产设备的搅拌功率。
(2)按工艺过程结果放大
在几何相似系统中,要取得相同的工艺过程结果,有下列放大判据可供参考(对同一种液体,ρ、μ和σ不变,下标1代表实验设备,2代表生产设备)。
①保持雷诺数不变,要求
;
②保持弗劳德数不变,要求
;
③保持韦伯数不变,要求
;
④保持叶端线速度uT=nπd不变,要求n1d1=n2d2;
⑤保持单位流体体积的搅拌功率N/V不变,要求。
对于一个具体的搅拌过程,究竟选择哪个放大判据需要通过放大实验来确定。
2.2.3 搅拌器中的传热
2.2.3.1 传热方式
在搅拌槽中对被搅拌的液体进行加热或冷却是经常遇到的重要操作。尤其是伴有化学反应的搅拌过程,对被搅拌的液体进行加热或冷却可以维持最佳工艺条件,促进化学反应,取得良好反应效果。对于有的反应,如果不能及时移出热量,则容易产生局部爆炸或反应物分解等。因此,被搅拌液体进行化学反应时搅拌更为重要。
被搅拌液体的加热或冷却方式有多种。可在容器外部或内部设置供加热或冷却用的换热装置。例如,在搅拌槽外部设置夹套,在搅拌槽内部设置蛇管等。一般用得最普遍的是采用夹套传热的方式。
(1)夹套传热
夹套一般由普通碳钢制成(见图2-4),它是一个套在反应器筒体外面能形成密封空间的容器,既简单又方便。夹套上设有水蒸气、冷却水或其他加热、冷却介质的进出口。目前,空心夹套已很少用,为了强化传热,常采用螺旋导流板夹套、半管螺旋夹套等形式。如果加热介质是水蒸气,为了提高传热效率,在夹套上端开有不凝性气体排除口。

图2-4 夹套传热
夹套同器身的间距视容器公称直径的大小采用不同的数值,一般取25~100mm。夹套的高度取决于传热面积,而传热面积是由工艺要求决定的。但须注意的是,夹套高度一般不应低于料液的高度,应比器内液面高度高出50~100mm,以保证充分传热。通常夹套内的压力不超过1.0MPa。夹套传热的优点是结构简单、耐腐蚀、适应性广。
(2)蛇管传热
当需要的传热面积较大,而夹套传热在允许的反应时间内尚不能满足要求时,或者是壳体内衬有橡胶、耐火砖等隔热材料而不能采用夹套传热时,可采用蛇管传热(见图2-5)。蛇管沉浸在物料中,热量损失小,传热效果好。排列密集的蛇管能起到导流筒和挡板的作用。

图2-5 蛇管传热
蛇管中对流传热系数较直管大,但蛇管过长时,管内流体阻力较大,能量消耗多,因此,蛇管不宜过长。通常采用管径25~70mm的管子。用蒸汽加热时,管长和管径的比值可参考表2-6。
表2-6 管长和管径的比值

用蛇管可以使传热面积增加很多,有时可以完全取消夹套。蛇管的传热系数比夹套的大,而且可以采用较高压力的传热介质。
此外,还有诸如回流冷凝法、料浆循环法等其他传热方式。
2.2.3.2 热载体侧对流传热系数
搅拌过程中流体的传热主要是热传导和强制对流。传热速率取决于被搅拌流体和加热或冷却介质的物理性质、容器的几何形状、容器壁的材料和厚度以及搅拌的程度。
(1)蛇管中流体对管壁的对流传热系数
当Re>10000时,直管中的流体对管壁的对流传热系数用下式计算
(2-19)
式中,,表示对流传热系数的特征数,量纲为1;
,表示物性对传热系数影响的特征数,量纲为1;
,流体在主体温度下的黏度与在壁温下的黏度之比,量纲为1;α为直管中的流体对管壁的对流传热系数,W/(m2·℃);De为当量直径,m;λ为热导率,W/(m·℃);Cp为液体的比热容,J/(kg·℃);μ为流体在主体温度下的黏度,Pa·s;μw为流体在壁温度下的黏度,Pa·s。
流体在蛇管中流动时,由于流体对管壁的冲刷作用,所以,蛇管中的对流传热系数等于由式(2-19)算得的结果乘上一个大于1的校正因子,即
(2-20)
式中,Dc为蛇管轮的平均轮径,m。
当Re<2100时,即流体在层流区域时,蛇管中流体对管壁的对流传热系数用下式计算
(2-21)
式中,L为蛇管长度,m。
当2100<Re<10000时,即流体在过渡流区域时,可用式(2-19)计算出Nu,再乘上一个系数Φ,Φ值由表2-7决定。
表2-7 校正系数

式(2-19)~式(2-21)适用于圆管,对于非圆管,采用当量直径。
(2)夹套中热载体对搅拌釜壁的对流传热系数
不同方式的夹套的传热计算基本相同,按Re的不同分别用式(2-20)、式(2-21)和表2-7计算,与计算管中流体传热不同的是其当量直径De,计算流速u时的流通面积Ax和传热面积S取值另有规定,见表2-8。
表2-8 三种夹套的对流传热系数算法

注:E—夹套环隙宽度,m;P—螺距,m;Ax—流通面积,m2;S—传热面积,m2;dci—蛇管内径,m;Dji—夹套内径,m;Djo—夹套外径,m。
2.2.3.3 被搅拌液体侧的对流传热系数
(1)对流传热系数关联式
搅拌液体侧的对流传热系数大致可分成两大类:一类是蛇管外壁的对流传热系数;另一类为有夹套的容器内壁对流传热系数αj。通过大量实验工作,得到了一些搅拌液体侧的对流传热系数关联式。比较常用的有佐野雄二推荐的关联式。
佐野雄二给出的桨式或涡轮式搅拌器的对流传热系数关联式如下
(2-22)
(2-23)
式中,,表示被搅拌液体对有夹套容器内壁面的对流传热系数的特征数,量纲为1;
,表示被搅拌液体对内冷蛇管外壁面的对流传热系数的特征数,量纲为1;
,表示物性对传热系数影响的特征数,量纲为1;dco为内冷蛇管外径,m;ε为单位质量被搅拌液体消耗的搅拌功率,W/kg;ν为被搅拌液体的运动黏度,m2/s。
计算物性时,一般以流体的平均温度作为定性温度。
上两式的特点是既能用于有挡板槽,也可用于无挡板槽,而且蛇管设置与否、叶轮型式、叶轮安装高度、叶轮上的叶片数和叶片倾角等的变化对关联式的系数无影响,这使关联式的应用范围很广。
另外,永田进治也推荐了一些适用范围广泛的对流传热系数关联式。实验的搅拌槽内装入了冷却管,搅拌器主要为桨式、涡轮式,对牛顿型流体进行了实验,应用时可参阅相关文献。
(2)传热系数K的计算
传热系数K又称总传热系数,是评价搅拌反应器的重要技术指标。它对搅拌反应器的生产能力、产品质量、产品成本、动力消耗都有很大影响。
对于间壁两边都是变温的冷、热两流体间的实际传热过程,热流体的温度为T,冷流体的温度为t,间壁厚度为δ2,间壁材料的热导率为λ2。在间壁两边生有垢层,其厚度各为δ1及δ3,热导率为λ1及λ3。传热过程由热流体对壁面的对流传热、在垢层和金属壁间的热传导和壁面对冷流体的对流传热组成。
对于定态传热,选用传热面积的平均值Sm,并应用热阻串联原理,可得
(2-24)
(2-25)
式中,Q为传热速率,W;(T-t)m为平均温度差,℃。
在通常情况下,金属热导率比垢层热导率大得多,所以一般可忽略不计。
为了方便,暂不考虑垢层对传热的影响,总的热阻必来自料液与容器壁间的热阻1/α1和夹套内传热介质与容器壁间的热阻1/α2。工程上采取各种有效措施提高α1和α2,以强化传热。
为了强化α1,常采用加设挡板或设置立式蛇管,有时也采用小搅拌器高转速。对于高黏度流体或非牛顿型流体,往往1/α1比其他热阻要大得多,故实际上总的热阻由此层热阻控制。为了提高α1值,采用近壁或刮壁式搅拌器。对高黏度的拟塑性物料,采用刮壁搅拌器可提高K值4~5倍。
为了提高α2值常采用下列几种方法。
①夹套中加螺旋导流板,可以增加冷却水流速。螺旋导流板一般焊在容器壁上,与夹套壁有0~3mm的间隙。
②加扰流喷嘴。在夹套的不同高度按等距安装喷嘴。冷却水主要仍从夹套底部进水口进入夹套,在喷嘴中注入一定数量的冷却水,使冷却水主流呈湍流状态,可以大幅度提高α2。
③夹套多点切向进水。在夹套的不同高度切向进水,可提高α2值,其作用同扰流喷嘴相似。
当夹套内的介质为饱和水蒸气或过热度不大的过热蒸汽加热时,由于水蒸气的相变使α2高达10000以上,在此情况下总阻力集中在搅拌槽一侧。
搅拌器的总传热系数K值可通过式(2-25)求出。其经验值列于表2-9,供设计时参考。
表2-9 搅拌器的总传热系数K的参考数据

以上介绍的是液-液系统,如在鼓泡搅拌器中,传热问题可与不通气时一样处理。关于加热时间的计算及高黏度液体的传热,可参阅有关资料或专著。
2.2.4 搅拌器主要附件
为了达到混合所需的流动状态,在某些情况下搅拌槽内需要安装搅拌附件,常用的搅拌附件有挡板和导流筒。
2.2.4.1 挡板
加装挡板可消除搅拌釜内液体的打旋现象,抑制釜内液体的快速圆周运动,迫使被搅拌的液体上下翻腾,强化湍动。加装挡板有两种形式——壁挡板和底挡板。壁挡板(见图2-6)是在槽壁上均匀地安装若干纵向挡板,以创造全挡板条件。在固体悬浮操作时,还可在槽底上安装横向挡板——底挡板(见图2-7),以促进固体的悬浮。

图2-6 壁挡板

图2-7 底挡板
纵向挡板主要是将切向流动转化为轴向流动和径向流动,对于槽内流体的主体对流扩散、轴向流动和径向流动都是有效的,同时增大被搅拌流体的湍动程度,从而改善搅拌效果。实验证明:纵向挡板的宽度W、数量nb以及安装方式等都将影响流体的流动状态,也必将影响搅拌功率。当纵向挡板的条件符合
(2-26)
此时搅拌器的功率最大,这种挡板条件叫做全挡板条件。纵向挡板的宽度W一般取为:W=(1/12~1/10)D,对于高黏度流体,可减小到(1/20)D。纵向挡板的数量nb取决于搅拌槽直径的大小。对于小直径的搅拌槽,一般安装2~4块挡板,对于大直径的搅拌槽,一般安装4~8块,以4块或6块居多,若继续增加挡板的数目并不会明显增加搅拌器的功率,此时已接近于全挡板条件。
搅拌槽内设置的其他能阻碍水平回转流动的附件,也能起到挡板的作用,如搅拌槽中的传热盘管可以部分甚至全部代替挡板,装有垂直换热管后,一般可不再设置挡板。
2.2.4.2 导流筒
在需要控制流体的流动方向和速度以确定某一特定流型时,可在搅拌槽中安装导流筒(见图2-8)。导流筒主要用于推进式、螺杆式及涡轮式搅拌器。推进式或螺杆式搅拌器的导流筒是安装在搅拌器的外面,而涡轮式搅拌器的导流筒则安装在叶轮的上方。导流筒的作用是:一方面它提高了对筒内流体的搅拌程度,加强了搅拌器对流体的直接机械剪切作用,同时又确立了充分循环的流型,使搅拌槽内所有的物料均可通过导流筒内的强烈混合区,提高混合效率。另外,导流筒还限定了循环路径,减少短路的机会。导流筒的尺寸需要根据具体生产过程的要求决定。一般情况下,导流筒需将搅拌槽截面分成面积相等的两部分,即导流筒的直径约为搅拌槽直径的70%。

图2-8 导流筒
导流筒置于搅拌槽内,是上下开口的圆筒,在搅拌混合中起导流作用。通常导流筒的上端都低于静液面,且在筒身上开有槽或孔,当生产中液面降落时流体仍可从槽或孔进入。推进式搅拌桨可位于导流筒内或略低于导流筒的下端[见图2-8(a)和(b)];涡轮式或桨式搅拌桨常置于导流筒的下端[见图2-8(c)]。当搅拌桨置于导流筒之下,且筒直径又较大时,筒的下端直径应缩小,使下部开口小于搅拌桨直径。