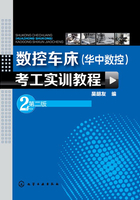
1.3 编程方法及步骤
1.3.1 编程的目的
编制数控加工程序时,要把加工零件的工艺过程、运动轨迹、工艺参数和辅助操作等信息,按一定的文字和格式记录在程序载体上,通过输入装置,将控制信息输入到数控系统中,使数控车床进行自动加工。从分析零件图样开始到获得正确的程序载体为止的全过程,称为零件加工程序的编制,以后也简称为编程。简而言之,就是为了驱动数控车床把零件加工出来。
1.3.2 编程的方法
数控加工的编程方法主要有手工编程和自动编程两类。
(1)手工编程
编制程序的过程,即从分析零件图样、制订工艺路线、选用工艺参数到进行数值计算等都是由人工完成的,这种编程方法称为手工编程。对于点位加工或几何形状简单的零件,不需要经过复杂的计算,程序段不多,此时使用手工编程方法较为合适。但对于形状复杂、工序较长的零件,需要进行烦琐的计算,程序段很多,出错也难于校核,此时尽可能采用自动编程。
(2)自动编程
自动编程时,程序员根据零件图样和工艺要求,使用有关CAD/CAM软件(包括Master CAM、Cimatron、Pro/ENGINEER、UG、CATIA、I-DEAS、Solid Works、CAXA等),首先利用CAD功能模块进行造型,然后利用CAM模块产生刀具路径,进而再用后置处理程序产生NC代码(与手工编程一样的数控程序),就可以通过DNC传输软件(现在数控系统的计算机带有硬盘,存储空间足够大,直接把数控代码复制到数控系统的硬盘下,不需要传输软件),传给数控机床,实现边传边加工。由此可见,自动编程与手工编程比较,具有编程时间短、减少编程人员劳动强度、出错机会少、编程效率高等优点。详细内容参考相关CAD/CAM软件的教程。
1.3.3 常用的数控车床自动编程软件介绍
(1)Master CAM
美国CNC Software公司的Master CAM软件是在微机档次上开发的,在使用线框造型方面较有代表性,而且它又是侧重于数控加工方面的软件,这样的软件在数控加工领域内占重要地位,有较高的推广价值。Master CAM的主要功能是:2D/3D图形设计、编辑;3维复杂曲面设计;自动尺寸标注、修改;各种外设驱动;5种字体的字符输入;可直接调用AutoCAD、CADKEY、SURFCAM、UNIMOD等;设有多种零件库、图形库、刀具库;2~5轴数控铣削加工;车削数控加工;线切割数控加工;钣金、冲压数控加工;加工时间预估和切削路径显示,过切检测及消除;可直接连接300多种数控机床。该软件主要CAM功能有:
①2D外形铣削挖槽和钻孔,2D挖槽残料加工,实体刀具模拟。
②2~5D单一曲面粗加工、精加工、沿面加工、投影加工。
③2~5D直纹曲面、扫描曲面、旋转曲面加工。
④3D多重曲面粗加工、精加工。
⑤3D固定Z轴插削加工。
⑥3D沿面夹角清角加工。
⑦3D多曲面沿面切削等。
(2)CAXA
CAXA制造工程师是由北京海尔软件有限公司开发的全中文CAD/CAM软件。CAXA的主要CAM功能有:
①支持2~5轴铣削加工,提供轮廓、区域以及3轴、4轴和5轴加工功能。
②支持车削加工,具有轮廓粗车、精车、切槽、钻中心孔、车螺纹等功能;可以用参数修改功能对轨迹的各种参数进行修改,以生成新的加工轨迹;
③支持线切割加工,具有快、慢走丝切割功能,可输出3B或G代码的后置格式。
1.3.4 编程的内容和步骤
以手工编程为例来说明编程内容和步骤。
(1)分析零件图样
通过对零件的材料、形状、尺寸和精度、表面质量、毛坯情况和热处理等要求进行分析,确定该零件是否适合在数控车床上加工。
(2)确定工艺过程
在分析零件图样的基础上,确定零件的加工工艺(如决定定位方式,选用工夹具等)和加工路线(如确定对刀点、走刀路线等),并确定加工余量、切削用量(如切削宽度、进给速度、主轴转速等)。
(3)数值计算
根据零件图样和走刀路线计算刀具中心运动轨迹。对于外形较复杂的零件,要充分利用数控系统的插补功能和刀具补偿功能来简化计算。对于列表曲线、自由曲面等程序编制,数学处理复杂,需要借助计算机使用专门软件进行计算。
(4)编写加工程序
根据工艺过程、数值计算结果以及辅助操作要求,按照数控系统规定的程序指令及格式编写出加工程序。
(5)把加工程序输入数控系统
把编写好的程序,输入到数控系统中,具体的输入方法有以下3种。
①在数控车床操作面板上进行手工输入。
②利用DNC(数据传输)功能,首先把程序录入计算机,然后由专用的CNC传输软件把加工程序输入数控系统,最后调出执行。如果程序太长,就采用DNC(边传边加工)的方法进行加工。
③直接复制到数控系统计算机硬盘上。
(6)首件试切
在开始切削前必须先对程序进行校验,确定没有错误后,才能进行首件试切。常用的校验方法有以下3种。
①利用空运行进行校验,该法只能校验程序格式、代码是否正确,校验不出加工轨迹是否正确。
②利用数控系统在操作面板的屏幕上显示图形,检查刀具运动轨迹的图形,以及刀具与夹头、尾座等是否相撞。
③用其他材料(如木材、尼龙、塑料)来代替毛坯进行试切,确定程序和工件加工轨迹无误后进入正式首件试切阶段。检查完毕后,可进行首件试切。只有首件通过检验,符合零件的质量要求后,才可认为数控加工程序无误,正式投入生产使用。
1.3.5 图形的数学处理
用适当的方法,将数控车床程序编制所需的有关数据计算出来的过程,称为数值计算。编程时的数值计算包括工件轮廓的基点坐标计算和节点坐标计算。由于数控车床一般以加工平面直线和圆弧的轮廓为主,所以数值计算的主要任务是求各基点的坐标。
(1)基点的概念
构成工件轮廓的不同几何素线的交点或切点称为基点,如直线与直线的交点、直线与圆弧的交点或切点、圆弧与圆弧的交点或切点等。基点主要直接用于编程时运动轨迹的起点或终点。图2-16中A~K各点都是该工件轮廓上的基点。基点计算的主要内容有:每条运动轨迹(线段)的起点和终点在选定坐标系中的坐标值和圆弧运动轨迹的圆心坐标值。
(2)基点计算的方法
①手工法。根据零件图样上给定的尺寸,运用数学方面的有关知识,计算出数值。例如要车削如图1-16所示的工件,在编程时必须要知道各基点的坐标,根据图中给定的几何尺寸,对其中的一些基点坐标很快就能找出,如A~E点等,但I点的坐标必须通过基点计算才能确定。作出图示辅助线,从几何关系可以看出,只要确定IM的距离,那么I点的X坐标就可确定。

图1-16 工件轮廓上的基点计算
I点的X坐标(直径)为36-2IM=(36-6)mm=30mm,即I点的坐标为I(30,-50)。
注意:在计算时要将小数点后面的位数留够,以保证足够的精度。对数控车床来说,其最小脉冲当量为0.001mm,所以计算时将小数点保留3位。
②自动法。利用CAD软件从图中查取。大多数的图形绘制都是在AutoCAD或其他绘图软件中完成;在AutoCAD软件中绘图时,可以利用它的一些功能,把某些点的坐标直接标出。当要通过计算或其他方法确定坐标值的基点数较少时(如图1-17中,只有A点的坐标不能直接得到),可以用DIMLINEAR(线性标注)的命令,把A点的坐标值标注出来;当要确定的基点数较多时,首先用UCS命令把CAD中的用户坐标系移至所作图的工件坐标系O点处;然后利用DIMORDINTE(坐标标注)命令,把所需要标注基点的坐标值标注出来。具体操作可参见有关AutoCAD的教程。

图1-17 工件的基点坐标值AutoCAD标注法