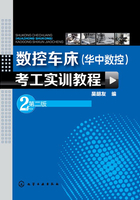
第1章 数控车床及其维护与保养
1.1 数控车床的功能特点
1.1.1 数控车床的分类
数控车床种类繁多、规格不一,有如下4种分类方法。
(1)按数控车床的档次分类
①简易数控车床。属于低档次数控车床,一般用单板机或单片机进行控制。机械部分由普通卧式车床略作改进而成;主轴电动机多用普通三相异步电动机;进给多采用步进电动机、开环控制、四刀位回转刀架。简易数控车床没有刀尖圆弧半径自动补偿功能,所以编程尺寸计算比较烦琐,加工精度较低,现在很少使用。
②经济型数控车床。属于中档次数控车床,一般有单色显示CRT、程序储存和编辑功能,多采用开环或半闭环控制。它的主轴电动机仍采用普通三相异步电动机,所以它的显著缺点是没有恒线速切削功能。
③多功能数控车床。属于较高档次的数控车床,主轴一般采用能调速的直流或交流主轴控制单元来驱动,进给采用伺服电动机、半闭环或闭环控制。多功能数控车床具有的功能很多,特别是具备恒线速度切削和刀尖圆弧半径自动补偿功能。
④高精度数控车床。主要用于加工类似磁鼓、磁盘的合金铝基板等需要镜面加工,并且形状、尺寸精度都要求很高的零部件,可以代替后续的磨削加工。这种车床的主轴采用超精密空气轴承,进给采用超精密空气静压导向面,主轴与驱动电动机之间采用磁性联轴器连接等。床身采用高刚性厚壁铸铁,中间填砂处理,支撑也釆用空气弹簧二点支撑。总之,为了进行高精度加工,在机床各方面均采取了多项措施。
⑤高效率数控车床。主要有一个主轴两个回转刀架及两个主轴两个回转刀架等形式。两个主轴和两个回转架能同时工作,提高了机床的加工效率。
⑥车削中心。在数控车床上增加刀库和C轴控制后,除了能车削、镗削外,还能对端面和圆周面任意进行钻、铣、攻螺纹等加工;而且在具有插补的情况下,还能铣削曲面,这样就构成了车削中心,如图1-1所示。它是在转盘式刀架的刀座上安装上驱动电动机,可进行回转驱动,主轴可以进行回转位置的控制(C轴控制)。车削中心可进行四轴(X、Y、Z、C)控制,而一般的数控车床只能两轴(X、Z)控制。

图1-1 车削中心
1—车床主机;2—刀库;3—自动换刀装置;4—刀架;5—工件装卸机械手;6—载料机
车削中心的主体是数控车床,再配上刀库和换刀机械手,与数控车床单机相比,显然自动选择和使用刀具数量大大增加。但是,卧式车削中心与数控车床的实质区别并不在刀库上,它还应具备如下两种先进功能:一种是动力刀具功能,即刀架上某一刀位或所有刀位可使用回转刀具,如铣刀和钻头。通过刀架内部结构,可使铣刀、钻头回转。
另一种是C轴位置控制功能。C轴是指以Z轴(对于车床是卡盘与工件的回转中心轴)为中心的旋转坐标轴。位置控制原有X、Z坐标,再加上C坐标,就使车床变成三坐标两联动轮廓控制。例如,圆柱铣刀轴向安装、X-C坐标联动就可以在工件端面铣削;圆柱铣刀径向安装、Z-C坐标联动,就可以在工件外径上铣削。这样,车削中心就能铣削出凸轮槽和螺旋槽,如图1-2所示。

图1-2 车削中心C轴加工能力
⑦FMC车床。实际上是一个由数控车床、机器人等构成的一个柔性加工单元。它除了具备车削中心的功能外,还能实现工件的搬运、装卸的自动化和加工调整准备的自动化,如图1-3所示。

图1-3 FMC车床
1—机器人控制柜;2—NC车床;3—卡爪;4—工件;5—机器人;6—NC控制柜
(2)按加工零件的基本类型分类
①卡盘式数控车床。未设置尾座,主要适用于车削盘类(含短轴类)零件,其夹紧方式多为电动液压控制。
②顶尖式数控车床。设置有普通尾座或数控尾座,主要适合车削较长的轴类零件及直径不太大的盘、套类零件。
(3)按数控车床主轴位置分类
①立式数控车床。主轴垂直于水平面,并有一个直径很大的圆形工作台,供装夹工件用。这类数控车床主要用于加工径向尺寸较大、轴向尺寸较小的大型复杂零件。
②卧式数控车床。主轴轴线处于水平位置,它的床身和导轨有多种布局形式,是应用最广泛的数控车床。
(4)按刀架数量分类
①单刀架数控车床。普通数控车床一般都配置有各种形式的单刀架,如四刀位卧式回转刀架[见图1-4(a)]、多刀位回转刀架[见图1-4(b)]。

图1-4 单刀架形式的自动回转刀架
②双刀架数控车床。双刀架的配置可以是平行交错结构,如图1-5(a)所示;也可以是同轨垂直交错结构,如图1-5(b)所示。各种刀架转换刀具的过程都是:接受转位指令→松开夹紧机构→分度转位→粗定位→精定位→锁紧→发出动作完成应答信号。驱动刀架工作的动力有电动和液压两类。

图1-5 双刀架形式的自动回转刀架
1.1.2 数控车床的布局
数控车床的主轴、尾座等部件相对床身的布局形式与普通卧式车床基本一致,但刀架和床身导轨的布局形式发生了根本的变化。这是因为它不仅影响机床的结构和外观,还直接影响数控车床的使用性能,如刀具和工件的装夹、切削的清理以及机床的防护和维修等。床身导轨与水平面的相对位置有以下四种布局形式。
①水平床身[见图1-6(a)]。工艺性好,便于导轨面的加工。配上水平放置的刀架可提高刀架的运动精度。但水平刀架增加了机床宽度方向的结构尺寸,且床身下部排屑空间小,排屑困难。

图1-6 数控车床的布局形式
②水平床身斜刀架[见图1-6(b)]。配上倾斜放置的刀架滑板,这种布局形式的床身工艺性好,机床宽度方向的尺寸也较水平配置滑板的要小且排屑方便。
③斜床身[见图1-6(c)]。导轨倾斜角度分别为30°、45°、75°。它和水平床身斜刀架滑板都因有排屑容易、操作方便、机床占地面积小、外形美观等优点,而被中小型数控车床普遍采用。
④立床身[见图1-6(d)]。从排屑的角度来看,该床身布局最好,切屑可以自由落下,不易损伤导轨面,导轨的维护与防护也较简单,但机床的精度不如其他三种布局形式的精度高,故运用较少。
1.1.3 数控车床的功能与结构特点
(1)功能
数控车床(CNC车床)能自动地完成对轴类与盘类零件内外圆柱面、圆锥面、圆弧面、螺纹等切削加工,并能进行切槽、钻孔、扩孔和铰孔等工作。数控车床具有加工精度稳定性好、加工灵活、通用性强的特点,并且能适应多品种、小批量生产自动化的要求,特别适合加工形状复杂的轴类或盘类零件。
(2)结构特点
数控车床由主轴箱、刀架、进给系统、床身以及液压、冷却、润滑系统等部分组成,数控车床的进给系统与普通卧式车床的进给系统在结构上有本质的区别。卧式车床的进给运动是经过交换齿轮架、进给箱、溜板箱传到刀架实现纵向和横向进给运动的;数控车床是采用伺服电动机经滚珠丝杠传到滑板和刀架,而实现Z向(纵向)和X向(横向)进给运动的,其结构较卧式车床大为简化。
图1-7为数控车床的结构示意图。由于数控车床刀架的两个方向运动分别由两台伺服电动机驱动,所以它的传动链短,不必使用交换齿轮、光杠等传动部件。伺服电动机可以直接与丝杠连接带动刀架运动,也可以用同步齿形带连接。多功能数控车床一般采用直流或交流主轴控制单元来驱动主轴,按控制指令作无级变速,所以数控车床变轴箱内的结构比卧式车床简单得多。

图1-7 数控车床的结构示意图
在数控车床上增加刀库和C轴控制,可使它除了能车削、镗削外,还能进行端面和圆周面上任意部位的钻、铣、攻螺纹,而且在具有插补功能的情况下,还能铣削曲面,这样就构成了车削中心,如图1-8所示。

图1-8 车削中心结构示意图
综上所述,数控车床的机械结构特点如下。
①采用高性能的主轴部件,具有传递功率大、刚度高、抗振性好及热变形小等优点。
②进给伺服传动一般采用滚珠丝杠副、直线滚动导轨副等高性能传动件,具有传动链短、结构简单、传动精度高等特点。
③高档数控车床具有较完善的刀具自动交换和管理系统。工件在数控车床上一次安装后,能自动地完成工件多道加工工序。
1.1.4 数控车床的选择配置与机械结构组成
图1-9为典型数控车床的选择配置与机械结构组成。包括主轴传动机构、进给传动机构、刀架、床身、辅助装置(刀具自动交换机构、润滑与切削液装置、排屑、过载限位)等部分。

图1-9 典型数控车床的选择配置与机械结构组成
1.1.5 数控车床的主要技术参数
本书采用的数控车床是济南第一机床厂生产的CK6136i型,配有华中数控系统。数控车床的主要技术参数如下。
①床身上最大工件回转直径 ф360mm
②滑板上最大工件回转直径 ф160mm
③最大工件车削直径 ф360mm
④定尖距 1000mm
⑤最大工件加工长度 855mm
⑥Z轴最大行程 970mm
⑦X轴最大行程 240mm
⑧Z轴快速移动速度 8m/min
⑨X轴快速移动速度 6m/min
⑩Z轴滚珠丝杠(直径×螺距) ф32mm×6mm
X轴滚珠丝杠(直径×螺距) ф20mm×4mm
Z轴进给电动机(AC) 0.9kW
X轴进给电动机(AC) 0.5kW
主轴电动机(变频电动机) 5.5kW
主轴转速(无级变频调速) 200~1050~300r/min
主轴头 A2-5
主轴通孔直径 ф40mm
主轴孔锥度 MT 5#
液压卡盘直径/棒料通过直径 6in/ф28mm
刀架 六工位电动刀架
刀架分度时间 单步2s(电动回转刀架)
全步刀位4s(电动回转刀架)
刀具规格尺寸 车刀:20mm×20mm
镗刀:ф25mm
尾架 手动尾架
尾架套筒直径/行程 ф60mm/120mm
尾架套筒内孔锥度 MT 4#
润滑装置 a.间歇时间 15min
b.排量 5.5mL/次
c.油箱容积 1.8L
d.排油压力 0.3MPa
冷却装置 a.泵电动机 电压380V、50/60Hz
b.流量 25L/min
c.扬程 6m
d.水箱容积 45L
液压装置 a.电动机 2HP-4-220/380
b.系统压力 3.5MPa
c.最大流量 16L/min
d.油箱容量度 60L
机床工作灯(型号:FAC21080GM) 交流110V/20W
机床外形尺寸 2600mm×1205mm×1725mm