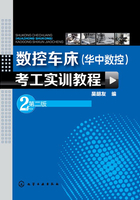
第2章 数控车削工艺设计
2.1 数控车削加工工艺分析
2.1.1 数控车削加工工艺概述
(1)数控车削加工的主要对象
数控车削是数控加工中用得最多的加工方法之一。由于数控车床具有加工精度高、能作直线和圆弧插补(高档车床数控系统还有非圆曲线插补功能)以及在加工过程中能自动变速等特点,因此其工艺范围较普通车床宽得多。针对数控车床的特点,下列几种零件最适合数控车削加工。
①轮廓形状特别复杂或难于控制尺寸的回转体零件。由于数控车床具有直线和圆弧插补功能,部分车床数控装置还有某些非圆曲线插补功能,所以可以车削由任意直线和平面曲线组成的形状复杂的回转体零件和难于控制尺寸的零件,如具有封闭内成形面的壳体零件。图2-1所示的壳体零件封闭内腔的成形面——口小肚大,在普通车床上是无法加工的,而在数控车床上则很容易加工出来。组成零件轮廓的曲线可以是数学方程式描述的曲线,也可以是列表曲线。对于由直线或圆弧组成的轮廓,直接利用机床的直线或圆弧插补功能。对于由非圆曲线组成的轮廓,可以用非圆曲线插补功能;若所选机床没有非圆曲线插补功能,则应先用直线或圆弧去逼近,然后再用直线或圆弧插补功能进行插补切削。

图2-1 成形内腔壳体零件示例
②精度要求高的回转体零件。零件的精度要求主要指尺寸、形状、位置和表面等精度要求,其中表面精度主要指表面粗糙度。例如:尺寸精度高(达0.001mm或更小)的零件;圆柱度要求高的圆柱体零件;素线直线度、圆度和倾斜度均要求高的圆锥体零件;线轮廓度要求高的零件(其轮廓形状精度可超过用数控线切割加工的样板精度);在特种精密数控车床上,还可加工出几何轮廓精度极高(达0.0001mm)、表面粗糙度数值极小(Ra达0.02mm)的超精零件(如复印机中的回转鼓及激光打印机上的多面反射体等),以及通过恒线速度切削功能,加工表面精度要求高的各种变径表面类零件等。
③带特殊螺纹的回转体零件。普通车床所能车削的螺纹相当有限,它只能车等导程的直、锥面公制(米制)或英制螺纹,而且一台车床只能限定加工若干种导程的螺纹。数控车床不但能车削任何等导程的直、锥螺纹和端面螺纹,而且能车增导程、减导程及要求等导程与变导程之间平滑过渡的螺纹,还可以车高精度的模数螺旋零件(如圆柱、圆弧蜗杆)和端面(盘形)螺旋零件等。数控车床可以配备精密螺纹切削功能,再加上一般采用硬质合金成形刀具以及可以使用较高的转速,所以车削出来的螺纹精度高、表面粗糙度小。
(2)数控车削加工工艺的基本特点
工艺规程是工人在加工时的指导性文件。由于普通车床受控于操作工人,因此在普通车床上用的工艺规程实际上只是一个工艺过程卡,车床的切削用量、走刀路线、工序的工步等往往都是由操作工人自行选定。数控车床加工的程序是数控车床的指令性文件。数控车床受控于程序指令,加工的全过程都是按程序指令自动进行的。因此,数控车床加工程序与普通车床工艺规程有较大差别,涉及的内容也较广。数控车床加工程序不仅要包括零件的工艺过程,而且要包括切削用量、走刀路线、刀具尺寸以及车床的运动过程。因此,要求编程人员对数控车床的性能、特点、运动方式、刀具系统、切削规范以及工件的装夹方法都要非常熟悉。工艺方案不仅会影响车床效率的发挥,而且将直接影响到零件的加工质量。
(3)数控车削加工工艺的主要内容
①选择适合在数控车床上加工的零件,确定工序内容。
②分析被加工零件的图样,明确加工内容及技术要求。
③确定零件的加工方案,制订数控加工工艺路线,如划分工序、安排加工顺序、处理与非数控加工工序的衔接等。
④加工工序的设计,如选取零件的定位基准、装夹方案的确定、工步划分、刀具选择和确定切削用量等。
⑤数控加工程序的调整,如选取对刀点和换刀点、确定刀具补偿及确定加工路线等。
2.1.2 数控加工工艺文件
编写数控加工工艺文件是数控加工工艺设计的内容之一。这些工艺文件既是数控加工和产品验收的依据,也是操作人员必须遵守和执行的规程。不同的数控机床和加工要求,工艺文件的内容和格式有所不同。目前尚无统一的国家标准,各企业可根据自身特点制订出相应的工艺文件。下面介绍企业中常用的几种主要工艺文件。
(1)数控加工工序卡
数控加工工序卡与普通机械加工工序卡有较大区别。数控加工一般采用工序集中,每一加工工序可划分为多个工步。工序卡不仅应包含每一工步的加工内容,还应包含其所用刀具号、刀具规格、主轴转速、进给速度及切削用量等内容。它不仅是编程人员编制程序时必须遵循的基本工艺文件,也是指导操作人员进行数控机床操作和加工的主要资料。不同的数控机床,数控加工工序卡可采用不同的格式和内容。
(2)数控加工刀具卡
数控加工刀具卡主要反映使用刀具的规格名称、编号、刀长和半径补偿值以及所加工表面等内容,它是调刀人员准备和调整刀具、机床操作人员输入刀补参数的主要依据。
(3)数控加工走刀路线图
一般用数控加工走刀路线图来反映刀具进给路线,该图应准确描述刀具从起刀点开始,直到加工结束返回终点的轨迹。它不仅是程序编制的基本依据,也便于机床操作人员了解刀具运动路线(如从哪里进刀、从哪里抬刀等),计划好夹紧位置及控制夹紧元件的高度,以避免碰撞事故发生。走刀路线图一般可用统一约定的符号来表示,不同的机床可以采用不同的图例与格式。
(4)数控加工程序单
数控加工程序单是编程人员根据工艺分析情况,经过数值计算,按照数控机床的程序格式和指令代码编制的。它是记录数控加工工艺过程、工艺参数、位移数据的清单,同时可帮助操作人员正确理解加工程序内容。表2-1是数控车床加工程序单的格式。
表2-1 数控加工程序单

2.1.3 零件的工艺分析
工艺分析是数控车削加工的前期工艺准备工作。工艺制订得合理与否,对程序编制、机床的加工效率和零件的加工精度都有重要影响。因此,应遵循一般的工艺原则并结合数控车床的特点,认真而详细地制订好零件的数控车削加工工艺。其主要内容有分析零件图样、确定工件在车床上的装夹方式、各表面的加工顺序和刀具的进给路线以及刀具、夹具和切削用量的选择等。
(1)零件图分析
零件图分析是制订数控车削工艺的首要工作,主要包括以下内容。
①尺寸标注方法分析。零件图上尺寸标注方法应适应数控车床加工的特点(见图2-2),应以同一基准标注尺寸或直接给出坐标尺寸。这种标注方法既便于编程,又有利于设计基准、工艺基准、测量基准和编程原点的统一。

图2-2 零件尺寸标注分析
②轮廓几何要素分析。在手工编程时,要计算每个节点坐标;在自动编程时,要对构成零件轮廓的所有几何元素进行定义。因此在分析零件图时,要分析几何元素的给定条件是否充分。如图2-3所示的几何要素中,根据图示尺寸计算,圆弧与斜线相交而并非相切。又如图2-4所示的几何要素,图样上给定几何条件自相矛盾,总长不等于各段长度之和。

图2-3 几何要素缺陷示例一

图2-4 几何要素缺陷示例二
③精度及技术要求分析。对被加工零件的精度及技术要求进行分析,是零件工艺性分析的重要内容。只有在分析零件尺寸精度和表面粗糙度的基础上,才能正确合理地选择加工方法、装夹方式、刀具及切削用量等。精度及技术要求分析的主要内容如下。
a.分析精度及各项技术要求是否齐全、是否合理。
b.分析本工序的数控车削加工精度能否达到图样要求。若达不到而需采取其他措施(如磨削)弥补,则应给后续工序留有余量。
c.找出图样上有位置精度要求的表面,这些表面应在一次安装下完成。
d.对表面粗糙度要求较高的表面,应确定用恒线速切削。
(2)结构工艺性分析
零件的结构工艺性是指零件对加工方法的适应性,即所设计的零件结构应便于加工成形。在数控车床上加工零件时,应根据数控车削的特点,认真审视零件结构的合理性。例如图2-5(a)所示零件,需用三把不同宽度的切槽刀切槽,如无特殊需要,显然是不合理的。若改成图2-5(b)所示结构,只需一把刀即可切出三个槽,既减少了刀具数量,少占了刀架刀位,又节省了换刀时间。在结构分析时,若发现问题应向设计人员或有关部门提出修改意见。

图2-5 结构工艺性示例
(3)零件安装方式的选择
在数控车床上零件的安装方式与普通车床一样,要合理选择定位基准和夹紧方案,主要注意以下两点。
①力求设计、工艺与编程计算的基准统一,这样有利于提高编程时数值计算的简便性和精确性。
②尽量减少装夹次数,尽可能在一次装夹后,加工出全部待加工面。
2.1.4 零件数控加工工艺路线的拟定
由于生产规模的差异,对于同一零件的车削工艺方案是有所不同的,应根据具体条件,选择经济、合理的车削工艺方案。
(1)加工方法的选择
在数控车床上,能够完成内外回转体表面的车削、钻孔、镗孔、铰孔和攻螺纹等加工操作,具体选择时应根据零件的加工精度、表面粗糙度、材料、结构形状、尺寸及生产类型等因素,选用相应的加工方法和加工方案。
(2)加工工序划分
在数控机床上加工零件,工序可以比较集中,一次装夹应尽可能完成全部工序。与普通机床加工相比,加工工序划分有其自己的特点,常用的工序划分原则有以下两种。
①保持精度原则。数控加工要求工序尽可能集中。通常粗、精加工在一次装夹下完成,为减少热变形和切削力变形对工件的形状、位置精度、尺寸精度和表面粗糙度的影响,应将粗、精加工分开进行。对轴类或盘类零件,将待加工面先粗加工,留少量余量精加工,来保证表面质量要求。对轴上有孔、螺纹加工的工件,应先加工表面而后加工孔、螺纹。
②提高生产效率的原则。数控加工中,为减少换刀次数、节省换刀时间,应将需用同一把刀加工的加工部位全部完成后,再换另一把刀来加工其他部位。同时应尽量减少空行程,用同一把刀加工工件的多个部位时,应以最短的路线到达各加工部位。实际生产中,数控加工工序的划分要根据具体零件的结构特点、技术要求等情况综合考虑。
(3)加工路线的确定
在数控加工中,刀具(严格说是刀位点)相对于工件的运动轨迹和方向称为加工路线,即刀具从对刀点开始运动起,直至加工结束所经过的路径,包括切削加工的路径及刀具引入、返回等非切削空行程。加工路线的确定首先必须保持被加工零件的尺寸精度和表面质量,其次考虑数值计算简单、走刀路线尽量短、效率较高等。由于精加工的进给路线基本上都是沿其零件轮廓顺序进行的,因此确定进给路线的工作重点是确定粗加工及空行程的进给路线。下面举例分析数控车削加工零件时常用的加工路线。
①车圆锥的加工路线分析。在车床上车外圆锥时可以分为车正锥和车倒锥两种情况,而每一种情况又有两种加工路线。图2-6所示为车正锥的两种加工路线。按图2-6(a)车正锥时,需要计算终刀距S。假设圆锥大径为D,小径为d,锥长为L,背吃刀量为ap,则由相似三角形可得
(D-d)/(2L)=ap/S (2-1)

图2-6 车正锥的两种加工路线
则S=2Lap/(D-d),按此种加工路线,刀具切削运动的距离较短。
当按图2-6(b)的走刀路线车正锥时,则不需要计算终刀距S,只要确定背吃刀量ap,即可车出圆锥轮廓,编程方便。但在每次切削中,背吃刀量是变化的,而且切削运动的路线较长。图2-7(a)、(b)为车倒锥的两种加工路线,分别与图2-6(a)、(b)相对应,其车锥原理与正锥相同。

图2-7 车倒锥的两种加工路线
②车圆弧的加工路线分析。应用G02(或G03)指令车圆弧,若用一刀就把圆弧加工出来,这样吃刀量太大,容易打刀。所以实际切削时,需要多刀加工,首先将大部分余量切除,最后才车得所需圆弧。图2-8所示为车圆弧的车圆法切削路线。即用不同半径的圆来车削,最后将所需圆弧加工出来。此方法在确定了每次背吃刀量后,对90°圆弧的起点、终点坐标较易确定。图2-8(a)的走刀路线较短,但图2-8(b)加工的空行程时间较长。此方法数值计算简单,编程方便,常用于加工较复杂的圆弧。图2-9所示为车圆弧的车锥法切削路线,即先车一个圆锥,再车圆弧。但要注意车锥时的起点和终点的确定。若确定不好,则可能损坏圆弧表面,也可能将余量留得过大。确定方法是连接OB交圆弧于D,过D点作圆弧的切线AC。由几何关系得
(2-2)

图2-8 车圆法切削路线

图2-9 车锥法切削路线
此为车锥时的最大切削余量,即车锥时,加工路线不能超过AC线。由BD与ΔABC的关系,可得
(2-3)
这样可以确定出车锥时的起点和终点。当R不太大时,可取AB=CB=0.5R。此法数值计算较繁,但其刀具切削路线较短。
③轮廓粗车加工路线分析。切削进给路线最短,可有效提高生产效率,降低刀具损耗。安排最短切削进给路线时,应同时兼顾工件的刚性和加工工艺性等要求,不要顾此失彼。图2-10给出了三种不同的轮廓粗车切削进给路线,其中图2-10(a)表示利用数控系统具有封闭式复合循环功能控制车刀沿着工件轮廓线进行进给的路线;图2-10(b)为三角形循环进给路线;图2-10(c)为矩形循环进给路线,其路线总长最短,因此在同等切削条件下的切削时间最短,刀具损耗最少。

图2-10 粗车切削进给路线示例
④车螺纹时的轴向进给距离分析。在数控车床上车螺纹时,沿螺距方向的Z向进给应和车床主轴的旋转保持严格的速比关系,因此应避免在进给机构加速或减速的过程中切削。为此要有引入距离δ1和超越距离δ2。如图2-11所示,δ1和δ2的数值与车床拖动系统的动态特性、螺纹的螺距和精度有关。一般δ1为2~5mm,对大螺距和高精度的螺纹取大值;δ2一般为1~2mm。这样在切削螺纹时,能保证在升速后使刀具接触工件,刀具离开工件后再降速。

图2-11 车螺纹时的引入距离和超越距离
(4)车削加工顺序的安排
制订零件车削加工顺序一般遵循下列原则。
①先粗后精。按照粗车→半精车→精车的顺序进行,逐步提高加工精度。粗车将在较短的时间内将工件表面上的大部分加工余量(如图2-12中的双点画线内所示部分)切掉,一方面提高金属切除率,另一方面满足精车的余量均匀性要求。若粗车后所留余量的均匀性满足不了精加工的要求,则要安排半精车,以此为精车作准备。精车要保证加工精度,按图样尺寸一刀切出零件轮廓。

图2-12 先粗后精示例
②先近后远。在一般情况下,离对刀点近的部位先加工,离对刀点远的部位后加工,以便缩短刀具移动距离,缩短空行程时间。对于车削而言,先近后远还有利于保持坯件或半成品的刚性,改善其切削条件。例如,加工图2-13所示零件时,若第一刀吃刀量未超限,则应该按ф34mm→ф36mm→ф38mm的次序先近后远地安排车削顺序。

图2-13 先近后远示例
③内外交叉。对既有内表面(内型腔)又有外表面需加工的零件,安排加工顺序时,应先进行内外表面粗加工,后进行内外表面精加工。切不可将零件上一部分表面(外表面或内表面)加工完毕后,再加工其他表面(内表面或外表面)。
④基面先行原则。用作精基准的表面应优先加工出来,因为定位基准的表面越精确,装夹误差就越小。例如,轴类零件加工时,总是先加工中心孔,再以中心孔为精基准加工外圆表面和端面。