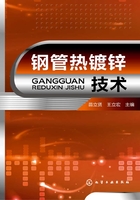
第六节 钢制品的热浸镀锌生产操作
由于目前国内热浸镀锌企业均面临一个较大的难题,就是客户提供的钢板材成分及类型千差万别,这就对热浸镀锌操作提出了较高的要求。不同成分及类型的钢板材需要采用不同的热浸镀锌操作工艺。适当的热浸镀锌操作对获得良好的镀锌层质量及较低的生产成本是非常关键的。热浸镀锌操作主要是对锌液温度、浸入速度、浸锌时间、提升速度以及刮灰、捞渣等操作步骤进行有效控制及实施;对于钢管热浸镀锌来讲,主要看外、内抹拭的技术,用以减少锌的消耗,提高镀层的外观质量。
一、锌液温度的控制
传统的Q195、Q215、Q235、Q275等低碳、低硅钢热镀锌时温度宜采用440~465℃之间。高碳、高硅钢宜在高温区间热镀锌,采用480~530℃温度镀锌,此时需要向锌液中添加含有铝(Al)的稀土铝锡锌多元合金,其铝含量约在0.03%~0.05%,可以获得光亮镀层,并可防止因高温镀锌件离开锌液后δ1相仍继续生长,在镀件表面上形成δ1与η相的混合组织,镀层呈灰暗色。此时铁在锌液中的溶解极限为0.30%,不采取措施去除铁离子将可能使镀层厚度较温度在450℃情况下增加1倍。但镀锌锅应选用耐高温的陶瓷型;若在低温区热镀锌,可将锌液温度设定在440~428℃之间,并在锌液中添加含锡的锌铝稀土合金元素,增加锌液流动性。
二、钢制品浸锌时间的确定
浸锌时间将直接影响镀锌层的厚度、表面质量。不同的钢制工件、材质、重量、厚薄等,热浸镀的时间是不一样的。应区别对待。锌液温度低时浸锌时间应长些,温度高浸锌时间应短些;管材质厚比薄的时间要长些;材质差的比材质优的时间要短些;熔锌量多比熔锌量少时,时间要短些;钢制工件本身温度高比温度低时,时间要短些等,其基本原则就是要使钢制件热得透,镀层才能粘得牢,不漏镀(铁)。
三、钢制件进入、离开锌液的速度
1.工件进入速度
工件的提升速度是根据牛顿内摩擦定律,导出锌液在工件表面上自由流动时的速度,实际上要比自由流动的速度慢些。钢制工件进入、离开锌液的速度过慢、过快都不好。钢制工件入锌液速度慢,将导致钢制工件在浸入锌液前表面助镀剂过早熔化失效,使失效部分的钢铁暴露在空气中,发生氧化,从而影响铁锌反应的进行,还可能出现表面缺陷。提升速度过快,结晶在钢制工件表面助镀盐没有足够的反应时间熔化分解、还原的钢材表面的残余氧化物和锌液表面上的氧化锌,部分尚未分解的残余助镀剂盐会随工件夹带如锌锅,增加了镀锌层表面出现的残留助镀盐产生的黑斑(也有叫作溶剂斑)缺陷的危险性。同时镀锌后的钢制工件提出锌液的速度过快将导致镀锌锌层的增厚。
钢制工件的浸入时间与取出时间(不是指工件在锌液中的时间)对镀层的厚度有很大的关系,这主要是指浸入和取出过程的速度所占用的时间。钢制工件浸入锌液的速度要适中,通常认为,钢制工件进入锌液时,应当采用稍快的速度。
(1)钢制工件浸入锌液的速度过慢产生的缺陷
①进入锌液速度过慢或发生中途停顿,可能会造成助镀剂膜层局部烧损失效,出现漏镀现象。
②钢制工件进入锌液速度过慢,会使钢制工件因受热时间的差异产生翘曲现象,快速进入锌液通常变形较小。
③对于长形钢制工件,当以竖直进入锌液时,两端的浸镀时间有明显的差异,会造成沿长度方向上的镀层厚度差别较大。
④进入锌液速度慢会减低生产效率。
(2)进入锌液速度过快会产生的缺陷
①当钢制工件干燥不彻底,或对干燥程度出现意想不到的情况,浸镀时会加重锌液飞溅或爆炸现象,危害人身安全,也会破坏锌锅内壁的合金保护层,降低锌锅的使用寿命。
②浸入锌液速度不应高于钢制工件靠自重落入锌液的速度,所以不宜过快。
综上所述,浸入锌液速度应根据钢制工件的形状尺寸特点灵活掌握。
(3)浸入锌液操作要点
①工件浸入锌液前,应先将锌液面的浮渣和锌灰打净,这样做的目的是:
a.使钢制工件与锌液充分接触,否则钢制工件表面的助镀剂与锌灰首先接触,会延缓化学反应的进行;
b.钢制工件浸入后,容易观察锌液面化学反应的进行情况;
c.可为最后打灰操作创造有利条件,更容易得到光亮的锌液表面。
②钢制工件浸没后应反复提动工件,以促进钢制工件上的助镀剂与锌液充分接触,使反应物尽快浮出。钢制工件的最佳浸入锌液位置是沉入液面以下100mm左右。
③浸入钢制工件时操作人员应戴防护面具,并离开锌锅一定距离,以防发生意外,被飞溅的锌液烫伤。
④浸入的钢制工件应尽量不要触及锌锅底部渣层,以避免底渣被搅动。
2.钢制工件的取出速率
钢制工件镀锌后取出速率对镀层的影响是很明显的。取出速率将对浸镀外观质量和镀锌层厚度(主要是纯锌层)产生重要影响,随着速率的增大而增厚,因此对镀锌后的钢制工件去除速率要注意以下几点。
(1)当钢制工件从锌液中取出后,仅依靠锌液的重力自然流淌方式形成纯锌层时,应遵守以下原则。
取出速率应与锌液在重力作用下沿工件表面流淌的速率相匹配,对简单形状的长形零件(杆、管及型材)有以下引出方式。
a.钢制工件垂直于锌液面引出,在常规镀锌温度下(445~465℃)可采用2.5~4.0m/min的取出速率;工件在锌液中呈水平状态,并与锌液面呈某一倾斜角度(称为引出角θ)取出时,其取出速度太小,见表3-9。对于热镀锌钢管来说,钢管的提升、向上爬升角度不低于16°为宜。
表3-9 引出角θ与取出速率的关系

b.取出速度与锌液的黏度密切相关,而锌液黏度与锌液中的合金成分及铁含量与锌液温度及环境温度相关。所以取出速率应根据工艺条件的不同,灵活掌握。
c.必须考虑工件的形状特点,如果是组合件应以保证镀件主要工作面上的锌液流动情况处于良好状态,此时工件悬挂方位的合理性显得格外重要。如果取出速率过快,工件上的锌液未能充分回锌锅,浸镀后纯锌层必须增厚,并出现锌瘤和锌的堆积。
d.确定取出速率时,还要考虑到镀件的化学成分对镀层质量的影响。对含硅镇静钢而言,如果取出速率过慢,必须延长在锌液及空气中的停留时间,合金层厚度会增加。此时,可以采用较快的取出速率,以缩短在空气中停留的时间,以得到光亮镀层。
(2)当钢制工件从锌液取出后,采用吹抹、离心等方法,去除工件表面余锌时,可采用2~8m/min提升速率。有条件时可采用变频调速技术,设置4~6个速度档次,使操作过程简捷、灵活,并提高生产效率。调速范围可从5~60Hz连续可调,这样可以更好地满足不同产品对升降速度的不同要求。
(3)钢制工件镀锌后从锌液中取出时的操作要做到以下几点。
①必须将锌液面上的锌灰彻底清除,呈现明亮锌液表面时,方可将工件提出。
②对形状复杂的工件,随着工件的引出,可以增大引出角度,以利于锌液的流淌。并用刮灰板或专用工具,在最适当的时间内将工件底部未能自行淌回的锌液刮除。
③钢制工件全部离开锌液时,应将钢制工件最底部的余锌刮除干净,并进行适当的敲击振动,使余锌落入锌锅。
④当浸镀大批量的小型零件时,应注意是否有散落到锌锅中的工件,并应及时检查打捞,避免产生不必要的锌耗。
⑤对于较长的钢制件,提升速度慢会导致较长的操作时间,为了维持相当的生产量,需要采用较快的提升速度,但必须使提出的速度和锌液的自由流动速度基本上一致,以便得到均匀的纯锌层。
对于钢管、钢带、钢丝、电焊钢丝网热镀锌的生产,其热镀走线速度则另当别论。可见有关连续热镀锌钢管、钢带、钢丝、电焊钢丝网论述。
四、锌液中的其他成分对镀锌层的影响
为了降低镀锌层厚度,现在一些厂家普遍注意往锌液中添加一定量的低熔点锌合金。关于锌合金可以分为两类,其中的一类是以铝为主要成分的三元或多元合金,其主要作用为增加表面光泽亮度,见表3-10。
表3-10 Zn-5% Al-RE合金化学成分

1.合金的种类和作用
一类是单纯的锌铝稀土合金,以含铝元素为主,作用是增加光亮度。熔炼较好、铝含量合适的铝合金,有抑制合金层生长的作用,因而对镀锌层有部分减薄作用。另一类合金是锌、锡、铋、铝和混合稀土组成的多元合金,具有降低锌的熔点和表面张力的作用,在镀锌过程中,锌液温度控制在435~450℃范围内,就可以满足热镀Q235的型材和部分Q345型材。通过几年来国内对热镀锌的工件、要求变形较小的扁、长、宽的钢制件尤为合适,如电缆桥架等。
另一类是以镍为主的有少量铝、镁、锌、镍合金,其镍含量一般为2%、1%、0.5%三种,2%镍合金不但有减少色差、抑制圣德林现象的发生,同时具有对未有加锌镍合金镀层厚度将减薄15%~30%,而且将减少锌灰的产生,延长锌锅使用寿命等优点。其中以共晶成分的锌0.5%镍的使用较为好用,但用量较大,价格不太便宜,而使用厂家较少;而2%镍含量合金,由于价格偏低,添加量少,受到厂家的好评,但在使用前后,需按一定的操作工艺,如静止锌液、沉淀锌渣后捞渣等,要需一定的时间。在这方面,国内现在已有较为成熟的应用经验。
2.锌液中的铝与铁的关系
铁在锌液中的溶解度随着锌液温度和铝含量两大因素的变化而变化,总体趋势是随着温度的升高而升高,随着铝含量的增加而下降。在镀锌常见温度460℃时,铁的溶解度随着铝含量变化的曲线如图3-8。

图3-8 锌液460℃时铁在锌液中的溶解与析出的平衡组织
从图3-8上可以看出铝含量为0.10%和0.135%是两个临界点。铝含量低于0.1%时,铁的溶解度随铝含量的增加以较大的斜率减小,而在0.1%和0.135%之间,铁的溶解度随铝含量的增加缓慢下降,当铝含量超过0.135%时,随铝含量的增加铁的溶解度又以很快的速度下降。这是因为,在不同的铝含量下,铁饱和以后所形成的金属化合物不同,在铝含量<0.10%时,近似于镀纯锌层,铁饱和以后铁与锌反应生成FeZn13是一种锌含量较高的底渣,在锌含量为0.10%~0.135%之间,铁饱和以后铁与锌反应生成FeZn7,是一种最常见的底渣,而当锌含量超过0.135%时,铝参与反应,铁与铝和锌反应生成的化合物是Fe2Al5Znx,就是锌锅顶上的浮渣。这几种情况如表3-11。
表3-11 锌液460℃时不同铝含量下铁锌平衡反应锌渣组成

从理论上讲,若能达到平衡状态的话,有效铝含量低于0.135%则全部形成底渣,而有效铝高于0.135%则全部形成浮渣,当铝含量在0.135%左右的话,则有可能产生底渣,也有可能产生浮渣。当然,生产实际的情况是千变万化的,不会像理论分析一样有截然不同的界限,但大体趋势毕竟如此,这一理论为锌锅中有效铝的含量确定和无底渣操作提供了理论上的依据。
3.锌铝合金的使用量
在非连续热镀锌工艺生产中,使用铝合金时,锌液中含铝至0.007%的范围内就可以获得满意效果,锌液中铝含量连续增加,其有效性就会降低。还可以导致漏镀等缺陷,这是由于锌液表面形成的氧化铝保护层在工件浸镀时通过与助镀盐(氯化锌+氯化铵)反应生成挥发性氯化铝而实现分解的。最近有报道称:对含0.09%(质量)Si的活性钢热镀锌时,在锌液中添加锰含量小于0.5%(质量)的Zn-Mn合金后,可以使镀锌层不同程度地减薄。
如在带钢连续热镀锌中,当采用气体还原法时,一般应向锌液中添加一定量的铝,才能获得好的镀板质量,根据经验,锌液中应保持0.16%~0.20%铝的含量,此时铝元素将悬浮在锌液的偏上面,将与锌液中的铁元素化合而生成浮渣(铝含量为4%~7%)漂浮在锌液上面,仅及时打捞这部分浮渣,实行这样的工艺在锌锅底部产生的锌渣很少(亦叫无底渣工艺技术)。而实际铝的消耗量为0.35%左右,因此在添加铝合金时,要考虑这个因素,据生产实践计算:在锌层重量为300g/m2的情况下,为使锌液中铝的浓度提高0.01%,则加入锌液的铝含量应该提高0.05%~0.08%。关于锌液中铝的含量高低,还应根据带钢的运行速度和锌层重量,带钢运行速度越低,锌层重量越小,则加入锌液中的合金铝含量也应该高一些。当采用溶剂法带钢热镀锌时,锌液中铝的含量应低于采用气体还原法时的铝含量,根据实际经验,当采用氯化锌、氯化铵复合溶剂浓度为1.4~1.6时,铝含量约为0.02%~0.04%为宜。且添加锌铝合金时应在锌锅中部或带钢出口处添加,避免因在带钢入口处添加而出现的漏镀问题和非与沉没辊接触面的镀锌层不光滑现象。
国际上对成型钢件热镀锌的镀层特性和测试方法的标准ISO 1461中规定,锌锅中的杂质成分(参见ISO 752或EN 1179中的规定)不包括铁和锡元素以外的其他杂质,即铅、镉、铜、铝、的总含量不能超过1.50%。实际上实用传统锌液化学成分:(最大限量)Pb 1.20%,Fe 0.035%,Cd 0.30%,Cu 0.07%,Sn 0.30%,Al 0.005%,Zn余量。
五、扒锌灰和捞锌渣
在热镀锌过程中,因锌液表面的暴露、锌液面上的空气流动、钢丝上面的氯化铵溶剂等因素,锌液上面会出现锌灰。锌灰的成分比较复杂,一般情况下其成分含有氧化锌、氯化锌和铝、铁的氧化物等。它的产生主要是锌液与空气中的氧气反应产物、钢丝上面黏附的溶剂盐与锌液接触时,发生反应所产生的氧化锌、氯化锌等物质。其成分一般为6.5%Al2O3+39.3%ZnO+16%ZnCl2+5.0%Fe+33.2%Zn(金属颗粒)。锌灰的生成量通常约占钢丝镀锌总消耗量的25%~32%。
因此,在镀件从锌液表面提出来之前,锌液表面的锌灰必须去除,才能获得光滑的表面的制件。可以用专用的刮灰板将表面的锌灰轻轻地扒到锌锅边或两端,扒锌灰时应注意不要用力过大,使锌液面产生较大的搅动,这样容易使锌锅内壁形成的锌铁合金保护层脱落,加速锌锅的腐蚀损坏。
在镀锌过程中,会不断地形成锌渣。锌渣在静止的情况下会沉到锌锅的底部,在制件浸锌时应尽量不要搅动它,以免将大量的锌渣搅到锌液中,使镀层表面因粘上锌渣出现颗粒,影响镀件外观质量,以使锌耗增加。应定期打捞锌渣,以免锌锅底部的锌渣过厚,容易随工件表面带出,另外过厚的锌渣将影响导热性能,使锌锅壁局部过热,加速锌液对锌锅的腐蚀,将减少锌锅的使用寿命,严重时可能产生锌锅穿孔而漏锌液。可根据生产产量的实际情况,用专用带ф20~25mm的孔眼工具定期捞锌渣,或一周、半个月捞一次。
六、空气、水冷却
将热镀锌后的钢制件在经过数秒钟时间的空气冷却,去除锌瘤后,应立即将其进入水中,防止因空冷时间过长而使其镀层表面出现灰暗层等现象。钢制工件进入冷却水时,除较短的工件竖直进入水中外,较长钢制工件应倾斜进入水中,以防止弯曲变形等缺陷的产生。水温亦控制在25~45℃之间,水温不宜超过50℃。往往在刚开始热镀锌时因水温过低,则使镀锌后的工件易变形,在冬天热镀锌时应提前将冷却水温度提高到适宜温度。水温过高则使镀锌件镀锌层表面变暗。并应时常检查其pH值,有条件的地方应保持流动的清水。
对于紧固件热镀锌,经离心机对紧固件镀锌层甩锌后,应注意调整进行水冷却时间,以防止镀锌层脱锌皮的问题。