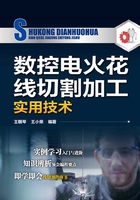
1.1.3 线切割机床的组成
电火花线切割机床主要由3大部分组成,分别是机床主体、脉冲电源和控制器。如图1-4(a)为高速走丝线切割机床,图1-4(b)为低速走丝线切割机床。
图1-4 电火花线切割机床
1.1.3.1 机床主体
机床主体是电火花线切割机床的主要部分,由X、Y坐标工作台、储丝走丝机构、丝架、导轮、床身和工作液循环系统组成。
(1)X、Y坐标工作台
工作台起装夹工件的作用,主要由上下托板、导轨、丝杠传动副和齿轮副4部分组成。控制器控制步进电机将动力通过齿轮变速机构传递给丝杠螺母副,再由丝杠螺母副控制托板作X、Y方向运动,从而获得指定的工作加工轨迹。
① 托板 托板主要由下托板、中托板、上托板(工作台)组成。通常下托板与床身固定连接;中托板置于下托板之上,运动方向为坐标Y方向;上托板置于中托板之上,运动方向为坐标X方向。其中上、中托板一端呈悬臂形式,以放置步进电动机。
为在减轻质量的条件下,增加托板的结合面,提高工作台的刚度和强度,应使上托板在全行程中不伸出中托板,中托板不伸出下托板。这种结构使坐标工作台所占面积较大,通常电机置于托板下面,增加了维修的难度。
② 导轨 坐标工作台的纵、横托板是沿着导轨往复移动的。因此,对导轨的精度、刚度和耐磨性有较高的要求。此外,导轨应使托板运动灵活、平稳。
线切割机床常选用滚动导轨。因为滚动导轨可以减少导轨间的摩擦阻力,便于工作台实现精确和微量移动,且润滑方法简单。缺点是接触面之间不易保持油膜,抗振能力较差。滚动导轨有滚珠导轨、滚柱导轨和滚针导轨等几种形式。在滚珠导轨中,滚珠与导轨是点接触,承载能力不能过大。在滚柱导轨和滚针导轨中,滚动体与导轨是线接触,因此有较大承载能力。为了保证导轨精度,各滚动体的直径误差一般不应大于0.001mm。
在线切割机床中,常用的滚动导轨有以下两种。
a.力封式滚动导轨 力封式是借助运动件的重力将导轨副封闭而实现给定运动的结构形式。图1-5是力封式滚动导轨结构简图,承导件有两根V形导轨。运动件上两根与承导件相对应的导轨中,一根是V形导轨,另一根是平导轨。这种结构具有较好的工艺性,制造、装配、调整都比较方便;同时,导轨与滚珠的接触面也较大,受力较均匀,润滑条件较好(因V形面朝上,易于储油)。缺点是托板可能在外力作用下,向上抬起,并因此破坏传动。当搬运具有这种导轨形式的机床时,必须将移动件夹紧在床身上。对于滚柱、滚针导轨,也常采用上述组合方式,因此在大、中型线切割机床中得到广泛使用。
图1-5 力封式滚动导轨结构简图
b.自封式滚动导轨 图1-6是自封式滚动导轨结构简图。自封式是指由承导件保证运动件按给定要求运动的结构形式。其优点是运动受外力影响,防尘条件好。但结构复杂,每个V形槽两侧面受力不均,工艺性比较差。
此外,还有“角尺”型滚珠寻轨、弧型导轨等组合结构。
图1-6 自封式滚动导轨结构简图
在大、中型线切割机床上,也有用导向导轨和承载导轨的。导向导轨配置在切割加工区域内,两侧有承载导轨。导向导轨与承载导轨皆为精密滚针导轨,有预应力的滚针镶嵌在淬硬、磨光的钢条上。这种结构的导轨精度高、刚度好、承载支点跨距大;同时热变形对称、直线性好、横向剪切力不变。
工作台导轨一般采用镶件式。由于滚珠、滚柱和滚针与导轨是点接触或线接触。导轨单位面积上承受的压力很大,同时滚珠、滚柱和滚针硬度较高,所以导轨应有较高的硬度。为了保证运动件运动的灵活性和准确性,导轨的表面粗糙度Ra值应在0.8μm以下,工作面的平面度应为0.005/400mm。导轨的材料一般采用合金工具钢(如CrWMn、GCr15等)。为了最大限度地消除导轨在使用中的变形,导轨应进行冰冷处理和低温时效。
③ 丝杠传动副 丝杠传动副的作用是将传动电动机的旋转运动变为托板的直线运动。要使丝杠副传动精确,丝杠与螺母就必须精确,一般应保证6级或高于6级的精度。
丝杠副的传动齿形一般分三角普通螺纹、梯形螺纹和圆弧形螺纹三种。三角普通螺纹和梯形螺纹结构简单、制造方便、精度易于保证。因此,在中、小型线切割机床的丝杠传动副中得到广泛应用。这种丝杠副传动为滑动摩擦,传动效率较高。大、中型线切割机床常采用圆弧形螺纹滚珠丝杠;滚珠丝杠传动副目前广泛用于线切割机床坐标工作台托板的运动传动结构中,滚珠丝杠传动副能够有效地消除丝杠与螺母间的配合间隙,可使托板的往复运动灵活、精确。
丝杠和螺母之间不应有传动间隙,以防止转动方向改变时出现空程现象,造成加工误差。所以,一方面要保证丝杠和螺母齿形与螺距等方面的加工精度;另一方面要消除丝杠和螺母间的配合间隙,通常有以下两种方法。
a.轴向调节法 利用双螺母、弹簧消除丝杠副传动间隙的方法是简便易行的(图1-7)。当丝杠正转时,带动螺母1和托板一起移动;当丝杠反转时,则推动副螺母3,通过弹簧2和螺母1,使托板反向移动。装配和调整时,弹簧的压缩状态要适当。弹力过大,会增加丝杠对螺母和副螺母之间的摩擦力,影响传动的灵活性和使用寿命;弹力过小,在副螺母受丝杠推动时,弹簧推动不了托板,不能起到消除间隙的作用。
图1-7 双螺母弹簧消除间隙的结构
1—螺母;2—弹簧;3—副螺母
b.径向调节法 图1-8为径向丝杠副间隙的结构。螺母一端的外表面呈圆锥形,沿径向铣出三个凸槽,颈部壁厚较薄,以保证螺母在径向收缩时带有弹性。圆锥底部处的外圆柱面上有螺纹,用带有锥孔的调整螺母与之配合,使螺母三爪径向压向或离开丝杠,消除螺母的径向和轴向间隙。
图1-8 径向丝杠副间隙的结构
④ 齿轮副 步进电动机与丝杠间的传动通常采用齿轮副来实现。由于齿侧间隙、轴和轴承之间的间隙及传动链中的弹性变形的影响,当步进电动机主轴上的主动齿轮改变转动方向时,会出现传动空程。为了减少和消除齿轮传动空程,应当采取以下措施:
a.采用尽量少的齿轮减速级数,力求从结构上减少齿轮传动精度的误差。
b.采用齿轮副中心距可调整结构,通过改变步进电机的固定位置来实现。
c.将被动齿轮或介轮沿轴向剖分为双轮的形式。装配时应保证两轮齿廓分别与主动轮齿廓的两侧面接触,当步进电动机变换旋转方向时,丝杠能迅速得到相应反应。
步进电动机的安装位置有两种:一种是置于托板的一侧端部;另一种是固定在可移动托板的下面,齿轮传动副也固定在托板下面的相应位置上。步进电动机的固定位置对托板的结构方式有着很大的影响。
(2)储丝走丝机构
高速走丝机构主要用来带动电极丝按一定线速度移动,并将电极丝整齐地排在储丝筒上。
① 对高速走丝机构的要求
a.高速走丝机构的储丝筒转动时,还要进行相应的轴向移动,以保证电极丝在储丝筒上整齐排绕。
b.储丝筒的径向跳动和轴向窜动量要小。
c.储丝筒能正反向旋转,电极丝的走丝速度在7~10m/s内无级或有级可调,或恒速运转。
d.走丝机构最好与床身相互绝缘。
e.传动齿轮副、丝杠副应具备润滑措施。
② 高速走丝机构的结构及特点 高速走丝机构由储丝筒组合件、上下托板、齿轮副、丝杠副、换向装置和绝缘件等部分组成。
储丝筒组合件主要结构如图1-9所示,储丝筒1由电动机2通过简单型弹性圆柱销联轴器3带动,以1450r/min的转速正反向转动。储丝筒另一端通过三对齿轮减速后带动丝杠4。储丝筒、电动机、齿轮都安装在两个支架5及6上。支架及丝杠则安装在托板7上,螺母9装在底座8上,托板在底座上来回移动。螺母具有消除间隙的副螺母及弹簧,齿轮及丝杠螺距的搭配使滚筒每旋转一周托板移动0.20mm。所以,该储筒适用于f0.19mm以下的钼丝。
图1-9 储丝筒组合件
1—储丝筒;2—电动机;3—联轴器;4—丝杠;5,6—支架;7—托板;8—底座;9—螺母
储丝筒运转时应平稳,无不正常振动。滚筒外圆振摆应小于0.03mm,反向间隙应小于0.05mm,轴向窜动应彻底消除。
高频电源的负端通过炭刷送到储丝筒轴的尾部,然后传到钼丝上。炭刷应保持良好接触,防止机油或其他脏物进入接触区。
储丝筒本身作高速正反向转动,电动机、滚筒及丝杠的轴承应定期拆洗并加润滑脂,换油期限可根据使用情况具体决定。其余中间轴、齿轮、燕尾导轨及丝杠、螺母等每班应注润滑油一次。随机附有摇手把一只,可插入滚筒尾部的齿轮槽中摇动储丝筒,以便绕丝。
a.储丝筒旋转组合件 储丝筒旋转组合件主要由储丝筒、联轴器和轴承座组成。
·储丝筒。储丝筒是电极丝稳定移动和整齐排绕的关键部件之一,一般用45钢制造。为减小转动惯量,筒壁应尽量薄,按机床规格不同,选用范围为1.5~5mm。为进一步降低转动惯量,也可选用铝镁合金材料制造。储丝筒壁厚要均匀,工作表面要有较好的表面粗糙度,一般Ra为0.8μm。为保证丝筒组合件动态平衡,应严格控制内孔、外圆对支承部分的同轴度。
储丝筒与主轴装配后的径向跳动量不大于0.01mm。一般装配后,以轴的两端为中心孔定位,重磨储丝筒外圆与轴承配合的轴径。
·联轴器。走丝机构中运动组合件的电动机轴与储丝筒中心轴,一般不采用整体的长轴,而是利用联轴器将二者连在一起。由于储丝筒运行时频繁换向,联轴器瞬间受到正反剪切力很大,因此多用弹性联轴器和摩擦锥式联轴器。
弹性联轴器:弹性联轴器结构简单,惯性力矩小,换向较平稳,无金属撞击声,可减小对储丝筒中心轴的冲击。弹性材料采用橡胶、塑料或皮革。这种联轴器的优点是允许电动机轴与储丝筒轴稍有不同心和不平行(如最大不同心允许为0.2~0.5mm,最大不平行为1°),缺点是由它连接的两根轴在传递扭矩时会有相对转动。
摩擦锥式联轴器:摩擦锥式联轴器可带动转动惯量较大的大、中型机床储丝筒旋转组合件。此种联轴器可传递较大的转矩,同时在传动负荷超载时,摩擦面之间的滑动还可起到过载保护作用。因为锥形摩擦面会对电动机和储丝筒产生轴向力,所以在电机主轴的滚动支承中,应选用向心止推轴承和单列圆锥滚子轴承。另外,还要正确选用弹簧规格。弹力过小,摩擦面打滑,使传动不稳定或摩擦面过热烧伤;弹力过大,会增大轴向力,影响中心轴的正常转动。
b.上下托板 走丝机构的上下托板多采用下面两种滑动导轨。
·燕尾型导轨。这种导轨结构紧凑,调整方便。旋转调整杆带动塞铁,可改变导轨副的配合间隙。但该结构制造和检验比较复杂,刚性较差,传动中摩擦损失也较大。
·三角、矩形组合式导轨。图1-10为三角、矩形组合式导轨结构。导轨的配合间隙由螺钉和垫片组成的调整环来调节。
图1-10 三角、矩形组合式导轨结构
由于储丝筒走丝机构的上托板一边装有运丝电动机,储丝筒轴向两边负荷差较大。为保证上托板能平稳地往复移动,应把下托板设计得较长以使走丝机构工作时,上托板部分可始终不滑出下托板,从而保持托板的刚度、机构的稳定性及运动精度。
c.齿轮副与丝杠副 走丝机构上托板的传动链是由2~3级减速齿轮副和1级丝杠副组成的。它使储丝筒在转动的同时,作相应的轴向位移,保证电极丝整齐地排绕在储丝筒上。在大、中型线切割机床中,走丝机构常常通过配换齿轮改变储丝筒的排丝筒的排丝距离,以适应排绕不同直径电极丝的要求。丝杠副一般采用轴向调节法来消除螺纹配合间隙。为防止走丝电动机换向装置失灵,导致丝杠副和齿轮副损坏,在齿轮副中,可选用尼龙齿轮代替部分金属齿轮。这不但可在电动机换向装置失灵时,由于尼龙齿轮先损坏,保护丝杠副与走丝电动机,还可减少振动和噪声。
d.绝缘、润滑方式
·走丝机构的绝缘一般采用绝缘垫圈和绝缘垫块,方法简单易行。在一些机床中,也有用绝缘材料制成连接储丝筒和轴的定位板实现储丝筒与床身绝缘的。这种方法的缺点是,储丝筒组合件装卸时精度易改变。
·润滑方式有人工润滑和自动润滑两种。人工润滑是操作者用油壶和油枪周期地向相应运动副加油的润滑方式;自动润滑为采用灯芯润滑、油池润滑或油泵供油的集中润滑系统。采取润滑措施,能减少齿轮副、丝杠副、导轨副和滚动轴承等运动件的磨损,保持传动精度;同时能减少摩擦面之间的摩擦阻力及其引起的能量损失。此外,还有润滑接触面和防锈的作用。
(3)丝架、导轮部件的结构
丝架与走丝机构组成了电极丝的运动系统。丝架的主要功用是在电极丝按给定线速度运动时,对电极丝起支撑作用,并随电极丝工作部分与工作台平面保持一定的几何角度。
对丝架的要求是:
·具有足够的刚度和强度。在电极丝运动(特别是高速走丝)时不应出现振动和变形。
·丝架的导轮有较高的运动精度,径向偏摆和轴向窜动不超过5μm。
·导轮与丝架本体、丝架与床身之间有良好的绝缘性能。
·导轮运动组合件有密封措施,可防止带有大量放电产物和杂质的工作液进入导轮轴承。
·丝架不但能保证电极丝垂直于工作台平面,在具有锥度切割功能的机床上,还具备能使电极丝按给定要求保持与工作台平面呈一定角度的功能。
丝架按功能可分为固定式、升降式和偏移式三种类型。按结构可分为悬臂式和龙门式两种类型。
① 丝架本体结构 目前,中、小型线切割机床的丝架本体常采用单柱支撑、双臂悬梁式结构。由于支撑电极丝的导轮位于悬臂的端部,同时电极丝保持一定张力,因此应加强丝架本体的刚度和强度,可使丝架的上下悬臂在电极丝运动时不至振动和变形。
为了进一步提高刚度和强度,在上下悬臂间增加加强筋的结构。大型线切割机床的丝架本体有的采用龙门结构。这时,工作台托板只沿一个坐标方向运动,另一个坐标方向的运动通过架在横梁上的丝架托板来实现。
此外,针对不同厚度的工件,还可采用丝臂张开高度可调的分离式结构(图1-11)。活动上臂在导轨上滑动,上下移动的距离由丝杠副调节。松开固定螺钉时,旋转丝杠带动固定于上臂体的丝母,使上臂移动。调整完毕后,拧紧固定螺钉,上臂位置便固定下来;为了适应丝架丝臂张开高度的变化,在丝架上下部分应增设副导轮(图1-12)。
图1-11 可调式丝架本体结构示意图
图1-12 可移动丝臂走丝示意图
② 导轮部件结构
a.对导轮运动组合件的要求
·导轮V形槽面应有较高的精度。V形槽底的圆弧半径必须小于选用的电极丝半径,保证电极丝在导轮槽内运动时不产生轴向移动。
·在满足一定强度要求下,应尽量减轻导轮质量,以减少电极丝换向时电极丝与导轮间的滑动摩擦。导轮槽工作面应有足够的硬度,以提高其耐磨性。
·导轮装配后转动应轻便灵活,尽量减少轴向窜动和径向跳动。
·进行有效的密封,以保证轴承的正常工作条件。
b.导轮运动组合件的结构 导轮运动组合件结构主要有三种;悬臂支承结构、双支承结构和双轴尖支承结构。
悬臂支承结构简单,上丝方便。但因悬臂支承,张紧的电极丝运动的稳定性较差,难于维持较高的运动精度,同时也影响导轮和轴承的使用寿命。
双支承结构为导轮居中,两端用轴承支承,结构较复杂,上丝较麻烦。但此结构的运动稳定性较好,刚度较高,不易发生变形及跳动。
双轴尖支承结构。导轮两端加工成30°的锥形轴尖,硬度在60HRC以上。轴承由红宝石或锡磷古铜制成。该结构易于保证导轮运动组合件的同轴度,导轮轴向窜动和径向跳动量可控制在较小的范围内。缺点是轴尖运动副摩擦力大,易于发热和磨损。为补偿轴尖运动副的磨损,利用弹簧的作用力使运动副良好接触。
此外,导轮支承有的还采用滑动支承结构。
c.导轮的材料 为了保证导轮轴径与导向槽的同轴度,一般采用整体结构。导轮要求用硬度高、耐磨性好的材料制成(如GCr15、W18Cr4V),也可选用硬质合金或陶瓷材料制造导轮的镶件来增强导轮V形工作面的耐磨性和耐蚀性。
d.导轮组合件的装配 导轮组合件装配的关键是消除滚动轴承中的间隙,避免滚动体与套环工作表面在负荷作用下产生弹性变形,以及由此引起的轴向窜动和径向跳动。因此,常用对轴承施加预负荷的方法来解决。通常是在两个支承轴承的外环间放置一定厚度的定位环来获得轴承的预负荷。预加负荷必须适当选择,若轴承受预加负荷过大,在运转时会产生急剧磨损。同时,轴承必须消洗得很洁净,并在显微镜下检查滚道内是否有金属粉末、碳化物等。轴承经清洗、干燥后,填以高速润滑脂,起润滑和密封作用。
③ 电极丝保持器 保持器主要是对电极丝往复运动起限位作用,以提高位置精度。当保持器用于保证电极丝顺序排绕时,一般置于上、下丝臂靠近储丝筒的一端(图1-13),使上、下保持器左右相对偏移。保持器的定位圆柱面应从相应中心位置对称地左右调节,使电极丝走向与导轮V形槽夹角尽量小,有利于导轮的正常使用。图1-14的V形宝石架用于保持电极丝运动的位置精度时,不应对电极丝产生较大的压力。圆柱式保持器可以用硬质合金和红宝石、蓝宝石制成。目前使用的有圆弧形、V形、#形等方式。
图1-13 硬质合金保持器
1—储丝筒;2—钼丝;3—硬质合金块
图1-14 V形宝石架
1—保持器架;2—V形宝石保持器
(4)工作液系统
在电火花线切割加工过程中,需要稳定地供给有一定绝缘性能的工作介质——工作液,以冷却电极丝和工件,排除电蚀产物等,这样才能保证放电持续进行。一般线切割机床的工作液系统包括:工作液箱、工作液泵、流量控制阀、进液管、回液管及过滤网罩等,如图1-15所示。
图1-15 线切割机床工作液系统
1—过滤网;2—回液管;3—工作台;4—下丝臂进液管;5—上丝臂进液管;6—流量控制阀;7—进液管;8—工作液泵;9—工作液箱
工作液过滤装置:工作液的质量及清洁程度在某种意义上对线切割工作起着很大的作用,如图1-16所示,用过的工作液经管道流到漏斗5,再经过磁钢2、泡沫塑料3、纱布1流入水池中。这时基本上已将电腐蚀物过滤掉,再流经二块隔墙4、铜网布6、磁钢2,工作液得到过滤复原。此种过滤装置不需要特殊设备,方法简单,可靠实用,设备费用低。
图1-16 工作液过滤网
1—纱布;2—磁钢;3—泡沫塑料;4—隔墙;5—漏斗;6—铜网布;7—工作液泵
此外,必须注意水箱内不能涂漆,要镀锌处理。工作液的黏度要小一些,否则泡沫塑料会堵塞,水泵的进水口要装铜丝网。
坐标工作台的回水系统装有射流吸水装置,如图1-17所示。在进水管中装一个分流,流进回水管,使回水管具有一定的流速,造成负压,台面的工作液在大气压下畅通流入管而不外溢。
图1-17 射流吸水装置示意图
1.1.3.2 脉冲电源
电火花线切割脉冲电源又称高频电源,是电火花线切割机床的重要组成部分,主要由主振电路、脉宽调节电路、间隔调节电路、功率放大电路和整流电源5部分组成,如图1-18所示。
图1-18 线切割脉冲电源组成示意图
为了满足电火花线切割加工条件和加工工艺要求,电火花线切割机床所采用的脉冲电源应满足以下要求:
① 脉冲电源的峰值电流不能太大,一般控制在10~25A,且易于调节。
② 脉冲宽度能够调窄,实际加工时脉冲宽度控制在0.5~0.64μs。
③ 脉冲重复频率能够调高,一般控制在5~500kHz。
④ 脉冲电源应具有对电极丝损耗小的性能,这也是衡量脉冲电源好坏的重要参数之一。正常情况下,电极丝切割10000mm2面积后,其损耗小于0.001mm。
⑤ 脉冲电源能输出单向脉冲。
⑥ 脉冲电源输出的脉冲波形在前沿和后沿应陡些。
⑦ 脉冲参数能在较宽的范围内调节。
1.1.3.3 控制器
电火花线切割控制器是电火花线切割机床的重要组成部分,它控制着X、Y方向工作台的运动及锥度切割装置的U、V坐标的移动,并合成工作切割轨迹,目前大部分控制器都已经实现数字控制或微机控制。