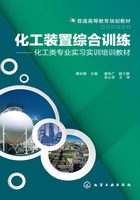
2.3 均酐工艺生产原理
2.3.1 均四甲苯气相氧化法制均酐的生产原理
均四甲苯气相氧化工艺采用固体的均四甲苯和空气为主要原料。均四甲苯经蒸汽加热溶化、与热空气混合汽化后,进入固定床氧化反应器中,采用五氧化二钒为催化剂,在反应器中发生非均相催化氧化反应(反应物为气相,催化剂为固相)生成均酐及副产物。从反应器中出来的混合气体经换热冷却后在捕集器中凝华捕集得到均酐粗产品。均酐粗产品经过水解结晶后得到粗均苯四甲酸,再将粗均苯四甲酸经脱水和升华结晶后最终得到均酐的产品。如果欲生产均苯四甲酸产品,将粗均苯四甲酸经干燥处理后即可得。
生产过程共分为5个工段:氧化工段、水解工段、脱水工段、升华结晶工段以及干燥工段。均苯四甲酸二酐生产流程框图如图2-1所示。

图2-1 均苯四甲酸二酐生产流程框图
2.3.1.1 氧化工段
氧化工段是固体的均四甲苯经蒸汽加热溶化、汽化与热空气混合后,在固定床氧化反应器中,催化氧化生成均酐及副产物,经换热冷却在捕集器中凝华捕集得到均酐粗产品。由均四甲苯气相氧化制取PMDA是一个复杂的多相催化过程,产物是一种范围很宽的含氧化合物的混合物,其中包括酐类、醛类和醇类化合物。由均四甲苯气相氧化化学转化的反应网络如图2-2所示。

图2-2 均四甲苯气相氧化化学转化的反应网络
其中:C1为1,2,4,5-四甲苯;C2为2,4,5-三甲基苯甲醛;C3为2,5-二甲基对苯二甲醛;C4为4,5-二甲基-2-苯甲醛;C5为甲基偏苯三甲酸;C6为均苯四甲酸及二苯酞;C7为均苯四甲酸二酐;C8为4-和5-甲基苯酞;C9为二氧化碳;C10为4,5-二甲基苯酐;C11为苯酞;C12为偏苯三甲酸。
由图2-2的反应网络可看出,均四甲苯气相氧化反应产物较多,因此反应选择性较低需要进一步研究气相氧化催化剂,提高反应选择性。
(1)反应机理
在V-O系催化剂上芳烃氧化反应机理主要有以下两种看法。
①烃分子夺取催化剂晶格中氧而氧化。
还原态催化剂+O2氧化钛催化剂
氧化态催化剂+烃氧化产物+还原态催化剂
②烃是被吸附的氧离子氧化。氧吸附在催化剂表面,从催化剂夺取电子,形成吸附氧离子:
烃吸附在催化剂表面,将电子供给催化剂而形成正烃离子:
RHRH+(吸附)
正烃离子与吸附的氧离子作用,形成中间配合物,进一步氧化为产物。
均四甲苯与空气的反应,为热力学不可逆反应,不受化学平衡限制。从上述反应方程可知,主、副反应均为强放热反应,氧化深度越大,放出反应热越多。
控制温度及时移出反应热非常重要,为抑制副反应及防止均酐的深度氧化,必须使用性能良好的催化剂。
主反应:
副反应:
(2)主要工艺影响因素
均四甲苯氧化制均苯四甲酸二酐的反应目前都在常压下进行,主要工艺影响因素有反应温度、原料空速、均四甲苯与空气的配比等。
①反应温度。由于主副反应均为强放热反应,尤其完全氧化反应在热力学上有很强的竞争性,高温必然导致完全氧化反应的进行,其结果放出更多的热量,使催化剂床层温度难以控制,甚至产生“飞温”现象,烧坏催化剂。因此,通常反应温度的控制必须限定在所对应的催化剂使用温度范围内,催化剂的类型不同,反应温度有所差别,通常均四甲苯氧化制均苯四甲酸二酐的反应要严格控制反应温度在435~445℃。
②原料空速。空速(空间速度)是指单位体积催化剂上通过的原料气的标准体积流量,或单位时间、单位体积催化剂上通过原料的标准立方米数,通常用m3/[m3(催化剂)·h]表示或用h-1表示。
由于在反应过程中不仅原料均四甲苯可直接氧化成大量一氧化碳和二氧化碳,而且产物均酐也能进一步氧化生成一氧化碳和二氧化碳,因此,空速的合理控制显得尤为重要。—般情况下,空速增加(即停留时间缩短),可减少深度氧化副反应的发生,提高反应的选择性。由于单位时间通过床层的气量增加,在一定范围内可使均酐生产能力增加;有利于反应热的移出和床层温度控制。
当然,空速也不能太大,空速太大,反应物在催化剂床层中的停留时间过短,就会导致反应物还没来得及反应就被移出了反应器,这样进入反应器中的原料中参与反应的反应物数量减少,反应放出的热量就会减少,最终导致整个反应系统的温度下降,严重的还会导致反应的停止。
因此,在实际工业生产中,通过反应器的原料空速的选择,通常根据所用催化剂的活性和选择性以及反应器的结构、输送原料的动力消耗等因素,一般控制在4500~6000h-1。
③均四甲苯与空气的配比。由于均四甲苯氧化反应属于强放热反应,且均四甲苯与空气的混合物在一定浓度范围具有爆炸的危险,因此,均四甲苯与空气的配比选择,首要条件是安全,即均四甲苯与空气的混合物浓度必须处在爆炸浓度范围之外。由相关资料可知,均四甲苯在空气中的爆炸浓度范围为0.840%~0.758%(摩尔分数),与之相当的均四甲苯与空气的摩尔比为1∶(118~131),换算为每立方米空气中均四甲苯的质量为45.67~50.70g,可见浓度相当的低。
实际生产过程中,对于强氧化放热反应大多采用低浓度之外的安全浓度区进行生产操作,这样做的目的是便于控制反应器中催化剂床层的温度。均四甲苯氧化制均苯四甲酸二酐的反应就是利用此方法进行实际生产操作的,气流中均四甲苯的浓度较低为0.126%~0.190%(摩尔分数),相当于7.6~11.4g/m3空气。
2.3.1.2 水解工段
氧化工段得到的是均酐的粗产品,里面含有大量的副产物,不是最终的产品。鉴于均酐和均苯四甲酸容易相互转化,粗酐需要先到水解工段水解结晶后得到均苯四甲酸的晶体。结晶作为工业生产经常用到的一种提纯手段,可将产品均酐(均苯四甲酸)的纯度得到很大的提高。在水解工段,粗的均酐产品在水解釜中加一定量的水和活性炭,加热水解后,经热过滤除去活性炭,冷却结晶再经过离心机甩干,得到均苯四甲酸粗产品,废液送污水装置处理。粗均酐与软水在95℃下水解生成均苯甲酸反应如下。
(1)水解反应
可见水解反应为吸热反应,因此在实际生产过程中需向水解釜提供热量维持水解反应在一定温度下进行,通常采用0.3MPa的低压蒸汽加热水解釜,维护水解反应在95℃左右。
(2)水解过程
由氧化工段生成的均酐粗产品,其水解过程通常在水解釜中进行。为了保证水解反应的顺利进行,水解过程需做到以下几点:
①加入的软水量一定要大于生成均苯四甲酸完全溶解所需的水量,其值可通过表2-5的溶解度数据进行定量计算;
②为了使生成的均酐产品中尽可能不含有色杂质,水解时需加入一定量的活性炭进行脱色,水解结束后,再经热过滤器除去活性炭;
③由水解反应可知,水解过程是吸热过程,因此,水解时需连续补充热量,通常采用0.3MPa的低压蒸汽加热水解釜,维护水解反应在95℃左右。
(3)结晶原理
均苯四甲酸在水中的溶解度如表2-5所示。
表2-5 均苯四甲酸在水中的溶解度

由表2-5可知,随着水温的降低,均苯四甲酸的溶解度明显下降。因此,实际生产过程中将温度较高(95℃)的水解液通过结晶釜降温,使水解生产的均苯四甲酸结晶析出,从而实现重新将其与水分离的目的。
(4)结晶过程
加热水解后的水解液,需冷却才能将其中的均苯四甲酸结晶析出。工业生产中,水解液的冷却结晶可在结晶釜或结晶槽中进行。
对于第一捕集器出料后的水解液,通常采用在结晶釜内进行结晶。用结晶釜结晶,优点是生产效率高,单位时间内产量大,但需消耗冷却水,生产成本相对较高。
对于第二捕集器或第三捕集器料的水解液,通常采用在结晶槽内进行自然冷却结晶。此法无需消耗冷却水,生产成本相对较低,但结晶槽内的自然结晶速率较慢,生产能力较低,且需若干个结晶槽,占地面积大。
不管采用结晶釜结晶,还是在结晶槽内进行结晶,最终的结晶溶液均需通过离心机甩干,得到含有一定水分和少量杂质的均苯四甲酸粗产品。
2.3.1.3 脱水工段
在脱水工段,将水解工段得到的均苯四甲酸粗产品放入脱水釜中,在高温和真空的条件下,除去粗产品中的游离水和分子水生成均酐,同时除去低沸点的副产物。反应方程式如下:
2.3.1.4 升华结晶工段
升华结晶工段发生的是物理过程。升华是指物质直接从固态变成气态的过程,反升华则是气态物质直接凝结为固态的过程。升华结晶过程包括这两步,以实现把一个升华组分从含其他不升华组分的混合物中分离出来。在升华工段,将脱水工段得到的粗酐放入升华釜中,在高温和真空的条件下,使均酐升华结晶,进一步提高纯度,得到均酐的最终产品。
2.3.1.5 干燥工段
通过氧化工段、水解工段、脱水工段和升华结晶工段可得到均酐产品。如果要生产均苯四甲酸产品,将水解工段得到的均苯四甲酸粗产品到干燥工段通过干燥操作,脱去均苯四甲酸表面附着的水,得到均苯四甲酸最终产品。干燥工段采用两种干燥手段,一种是采用气流干燥(闪蒸),利用高速流动的热空气,使物料悬浮于空气中,在气力输送状态下完成干燥过程;另一种是采用真空干燥,通过蒸汽加热,在一定真空度和一定温度条件下,粗均苯四甲酸在真空圆锥体内靠筒身的转动,不断翻滚物料,湿物料吸热后蒸发的水汽通过真空系统(泵)抽出筒外,从而达到物料的干燥。