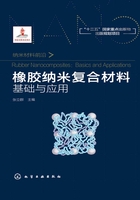
4.1.3 动态生热及低生热技术
4.1.3.1 动态生热机理
动态生热是橡胶材料的一种动态性能,它是外加机械能向热能的转化。任何材料的变形都可分为弹性成分和黏性成分,前者以弹簧表示,后者以黏壶表示。对(完全弹性的)弹簧施加周期性正弦应变,其应力与应变是同相位,而黏壶的应力正好与应变异相位(相差90°);当应变速率为最大值时,产生的应力值最大,而此时的应变为零。材料弹性成分和黏性成分力学行为的合效果即为材料实际应力,这导致其施加的应变产生一个相位角θ。
依据弹性、黏性和实际应力,分别定义了弹性模量、黏性模量以及复合模量(等于应力除以应变)。剪切过程中,这些模量分别用G′、G″以及G*表示;在压缩和拉伸过程中,用符号E代替G。由于黏性模量是与机械能损耗(机械能转化为热能)对应的黏性成分,因此黏性模量也称为损耗模量。此外动态性能可以用柔量表示,柔量随应力而变化,而不是随应变而变化。柔量用J(剪切)或D(压缩-拉伸)表示。复合柔量是复合模量的倒数。
若作出单个周期的应力-应变曲线,能得到一个滞后环。此闭合滞后环的面积称为滞后能密度,用H表示,它表示该周期内转化成热能的机械能。可由下式大致算出滞后能密度:
(4.2)
式中,DSA是应变幅值的两倍或是两峰值间的应变幅值,以变形前的百分率表示。
在DSA(恒应变)相同时比较胶料,发现胶料的滞后能密度与G′、tanδ或G″值成正比;而在等应力(恒应力)相同时比较胶料,则发现滞后能密度与损耗柔量J″成正比,此时:
(4.3)
经过简单的积分计算可得到单次加载周期内滞后能密度H的表达式,即式(4.3)。其中,σa是应力幅值;εa是应变幅值;ω是角频率;t是时间;δ是动态应力与动态应变之间的相位差;G″是损耗模量;J″是损耗柔量,J″=G″/(G*)2,G*是复合模量。在不同的加载方式(恒定应变、能量和应力)下,滞后能密度H有不同的表达式。Willett指出,在恒定应变幅值εa加载下,H与损耗模量G″成正比;在恒定应力幅值σa加载下,H与损耗柔量J″成正比;在恒定能量幅值σaεa加载下,H与损耗因子sinδ成正比,当相位角δ较小时,由于sinδ等价于tanδ,即可认为H与损耗因子tanδ成正比。热源的定义为单位时间单位体积内能量耗散量的大小,也称为生热速率Q·,滞后能密度H乘以频率f即得Q·。可见生热量与滞后能密度密切相关。
动态生热与节能是密切相关的,动态黏性损耗越高,生热就越大,动态服役的橡胶制品如轮胎的能量损耗也约大,也越不“节油”和“节能”。
如上所述,动态生热与橡胶制品所受到的应力及其所产生的变形有关,与动态服役时的频率、温度也有关系。其根源是动态黏性耗散,其本质则是大分子链间的动态摩擦、大分子链与纳米颗粒间的动态摩擦,以及纳米颗粒-纳米颗粒间的动态摩擦,如图4.18所示。

图4.18 (a)聚合物-纳米颗粒相对滑移;(b)纳米颗粒-纳米颗粒相对滑移;(c)聚合物-聚合物相对滑移
一定范围内,动态服役的频率越高,内摩擦越大,动态生热越高,如图4.19所示[15]。固定频率下,动态应力或应变越大,纳米复合材料内的内摩擦也越大,黏性损耗也越大,动态生热也越高,如图4.20所示。值得指出的是,在应变非常小时,由于体系内纳米颗粒形成的网络结构没有遭到破坏,此时的网络结构充当着一个弹性网络的角色,体系的黏性耗散反而会降低,一旦当应变达到一定值时,体系内的网络结构开始解体,弹性功能丧失,黏性损耗将加剧(在前面的Payne效应部分已经有详细论述)。图4.20(a)中,不同炭黑用量填充的混炼胶的损耗因子随应变变化曲线出现交叉证明了这一观点。对于交联的橡胶体系,由于基体的黏性耗散大大下降,因此,随着炭黑用量的增加,损耗因子增加;随着应变的增大,体系内摩擦增大,损耗因子增加,但超过一个峰值后反而有所下降。对于纳米炭黑填充的交联橡胶,在大应变时,体系内部的颗粒聚集体基本处于解离状态,颗粒-颗粒网络结构解体,颗粒间摩擦大大下降。尽管如此,如果纳米颗粒高度分散而且与基体间有化学键合,例如白炭黑/橡胶纳米复合材料经过硅烷偶联剂实施界面偶合后,其损耗因子随应变增加会出现一个更为缓慢的增长,在更高的应变下才出现明显上升。因此对轮胎性能进行设计时,一般采用5%~10%应变区间内的损耗因子进行表达比较客观[16]。

图4.19 损耗因子对频率的依赖性
体系1为聚氨酯/AO80(100/50);体系2为聚氨酯

图4.20 ESBR/炭黑N115体系(N115的用量为变量)的损耗因子随应变的变化
(a)混炼胶;(b)硫化胶
4.1.3.2 橡胶纳米复合材料低生热技术
橡胶种类对复合材料的动态损耗具有明显的影响。一般来讲,橡胶材料的极性越大,相互作用力越强,分子间的动态摩擦就越大,动态损耗和生热就越高。例如在其他因素相同的情况下,NBR的动态生热就比SBR高,CR的动态生热比BR高。对通用的NR、SBR与BR来讲,BR的玻璃化转变温度最低,分子链最柔顺,分子间的摩擦最小;SBR由于苯环侧基的存在,玻璃化转变温度较高,分子间的摩擦较大,动态损耗较高。ESBR/BR、NR/BR并用复合材料硫化胶的损耗因子随应变的变化曲线如图4.21所示。从图4.21(a)可以看出,ESBR胶料的动态损耗最大,并用BR和NR后,硫化胶的动态损耗降低,NR/BR/ESBR的动态损耗最低,这也表明BR和NR的加入可以改善乳聚丁苯橡胶的生热性能。从图4.21(b)可以看出,NR/BR并用时,材料的动态损耗进一步降低,低于 NR/BR/ESBR的动态损耗[17]。

图4.21 硫化胶的tanδ-ε曲线
(a)丁苯胶与顺丁橡胶共混胶;(b)天然胶与顺丁橡胶共混胶
乳聚丁苯橡胶是丁苯橡胶的传统品种,大部分用于轮胎胎面,但其致命的缺点是弹性小、滞后损失大、行驶时滚动阻力大,从而造成生热高、耗油量大、废气排放量大,乳聚丁苯橡胶难以实现高湿抓着性与低滚动阻力的统一,而溶聚丁苯橡胶采用阴离子活性聚合,苯乙烯与丁二烯比例、丁二烯单元的微观结构、聚合物的宏观结构、单元组成的序列分布、相对分子质量及分布等都可任意进行控制,能满足分子设计的要求,使滚动阻力、抗湿滑性及耐磨性三者之间达到最佳平衡,如图4.22所示[18]。

图4.22 乳聚丁苯橡胶ESBR 1712、ESBR 1502和溶聚丁苯橡胶SSBR 2305损耗因子随温度的变化
1—ESBR 1712;2—ESBR 1502;3—SSBR 2305
偶联溶聚丁苯橡胶是新型溶聚丁苯橡胶,与未偶联溶聚丁苯橡胶相比,具有结合胶多,模量和强度高,内耗小,生热低等突出特点。如图4.23所示,偶联溶聚丁苯橡胶的0℃损耗因子高,60℃损耗因子低,证明其有优异的抗湿滑性能和低滚动阻力性能,在提高轮胎行驶安全性、降低能耗、节约能源等方面意义重大。

图4.23 溶聚丁苯橡胶偶联对(a)低温与(b)高温损耗因子的影响[19,20]
橡胶分子经交联后,弹性增加。随着交联密度的增加,材料的模量增加,变形能力降低,内摩擦下降,动态损耗降低,生热下降。硫黄用量对炭黑增强天然橡胶复合材料动态损耗和压缩生热的影响分别如图4.24和表4.1所示。从图4.24可以看出,随着硫黄用量的增加(交联密度增加),橡胶复合材料的动态损耗呈下降的趋势;从表4.1中数据可以看出,随着硫黄用量的增加,胶料的压缩温升逐渐降低,说明配方中硫黄用量越高,胶料的生热越低。这与图4.24中胶料的动态损耗的结果是相符的[21]。

图4.24 硫黄用量对炭黑增强天然橡胶动态损耗的影响
表4.1 不同硫黄用量对天然橡胶复合材料压缩温升影响

另外,除了橡胶种类与交联程度,纳米颗粒用量对复合体系动态生热影响也很大。理论上分析,纳米颗粒用量越多,纳米颗粒与分子链界面面积越大,其界面摩擦增大,生热增加;同时纳米颗粒用量越多,纳米颗粒与纳米颗粒之间接触概率也相应增加,导致纳米颗粒-纳米颗粒间摩擦增加,动态生热增加(如图4.25所示)。关于纳米颗粒尺寸对动态损耗的影响,可参考本章4.2.2.1节。

图4.25 炭黑用量对橡胶动态损耗的影响随着炭黑用量的增加,60℃的损耗因子明显提高
值得强调的是,如果单纯增加分散时间和分散能耗,随着分散程度的增加,动态生热下降[图4.26(a)与(b)]。分散剂处理只是提高了分散程度,但界面间仍然是物理作用,因此动态生热比不处理时低,但与偶联剂处理相比会有差距。偶联剂处理后,不但改善了分散,减少了颗粒-颗粒间摩擦,而且有了化学键接,显著增大了交联密度,也减少了界面摩擦,因此动态生热降低最为明显[图4.27(a)与(b)]。

图4.26 混炼时间对天然橡胶/白炭黑体系(白炭黑50phr)性能的影响
(a)储能模量随应变的变化;(b)损耗因子随应变的变化

图4.27 三种体系(天然橡胶/纯白炭黑硫化胶、天然橡胶/硅烷偶联剂改性白炭黑硫化胶与天然橡胶/分散助剂改性白炭黑硫化胶,白炭黑均为70phr)的(a)储能模量随应变的变化及(b)损耗因子随应变的变化
欧盟数据表明,近五年来交通运输能耗约占世界总能耗的20%以上,而其中轮胎油耗为汽车油耗的20%~30%;全球18%的CO2排放与道路交通有关,道路车辆排放的CO2的24%与轮胎有关。另有数据显示,2015年英国由于轮胎故障造成的交通事故总计921起,造成17人丧生、147人受重伤。为顺应轮胎节油、安全、高性能的发展要求,欧盟于2009年推出了轮胎强制标签法,对轮胎的滚动阻力系数和湿抓地指数做了分级(A~G)。据测算,轮胎滚动阻力每降低20%,可节油5%,即使用B级绿色轮胎每年可节省200亿升汽油,减少5000万吨CO2排放;使用A级轮胎,相较于使用G级轮胎,湿路面刹车距离可缩短18m,极大提高了安全性。
如何进一步降低轮胎的油耗,传统的橡胶纳米复合材料设计理念与制备似乎走到了瓶颈。为了突破这一瓶颈,刘军和张立群教授等提出了新结构的概念。他们采用分子模拟设计了理想型橡胶纳米复合材料,如图4.28(a)所示。通过对分子链末端进行官能化(绿色表示),再与纳米颗粒(蓝色表示)表面进行化学接枝,构造了由等长分子链连接纳米颗粒的网络结构。纳米颗粒在体系中分布均匀,被等长分子链隔开。在这种结构中,纳米颗粒高度分散,因为橡胶分子链末端与纳米颗粒间为化学键合,而且由于是等长链连接结构,动态生热很低,拉伸取向更高。图4.29(a)是模拟体系的拉伸应力-应变曲线。可以看出,理想结构与传统共混结构相比,分子链更容易拉伸取向,呈现出高的应力-应变行为,且理想型橡胶纳米复合材料表现出最低的动态滞后损失(dynamic hysteresis loss,DHL)。

图4.28 (a)分子链末端官能化化学接枝纳米颗粒构造理想型橡胶纳米复合材料;(b)热塑性弹性体SBS自组装形貌(TEM图);(c)热塑性聚氨酯TPU自组装形貌(AFM图)

图4.29 四种体系(a)拉伸应力-应变行为的对比及(b)动态滞后损失的对比
实际上该理想网络结构类似于热塑性弹性体的自组装结构,均匀分散的纳米颗粒类似于自组装形成的均匀分布的硬相微区[4.28(b)与(c)]。图4.30显示了单根分子链连接相邻纳米颗粒的拉伸-回复示意图。进一步针对如下4种体系: SBS、TPU、天然橡胶/白炭黑体系、天然橡胶/炭黑体系,对比研究其动态力学性能。相对于共混纳米颗粒体系,自组装复合材料呈现出了非常低的损耗因子。在大应变下,由于微相分离的结构被破坏,分子链间的内摩擦呈现明显的上升趋势[图4.31(a)]。为反映轮胎的滞后损失,一般采用7%应变下的损耗因子,相对于共混体系,自组装体系均表现出很低的滞后损失。进一步做成小轮子——天然橡胶小轮子与聚氨酯小轮子。在50kg载荷与800r/min下,监测轮子的温升与功率损耗,自组装体系均表现出了更好的性能 (图4.32)。但由于一般的热塑性弹性体耐温性不好,高温下结构发生破坏,限制了其在轮胎工业上的应用。关于如何设计超级弹性体,来解决魔三角的问题,参见第12章12.3节[22]。

图4.30 单根分子链连接相邻纳米颗粒的拉伸-回复示意图

图4.31 (a)SBS、TPU、天然橡胶/白炭黑体系与天然橡胶/炭黑体系损耗因子随应变的变化;(b)4种体系的7%应变时的损耗因子对比

图4.32 (a) 天然橡胶小轮子;(b)聚氨酯小轮子;50kg载荷、800r/min下(c)小轮子的温升与(d)小轮子的功率损耗 [22]
4.1.3.3 纳米弹簧对滞后损失影响的分子模拟研究
北京化工大学先进弹性体材料研究中心首次提出了采用纳米弹簧来调整橡胶材料黏弹性的概念,模拟了碳纳米弹簧的引入对橡胶基体黏弹性的影响[图4.33(a)]。碳纳米弹簧具有力学可回复变形性,与橡胶复合后,可用前一节的黏弹性模型来描述,即两个弹簧与一个黏壶的并联[图4.33(b)]。通过对其拉伸回复过程的模拟,发现体系动态滞后损失随着碳纳米弹簧弹性系数的增加而逐渐减小,其原因是随着碳纳米弹簧弹性系数的增大,拉伸过程中储存的能量增加,在回复过程中能更有效地带动周围橡胶分子链的运动,降低体系内摩擦与滞后损失。该发现为工业上制备低滞后损失的轮胎提供了新的思路,也为碳纳米材料的大规模工业化应用提供了新的途径。

图4.33 (a)碳纳米弹簧、碳纳米环与单片石墨烯力学可回复变形示意图;(b) 碳纳米弹簧填充橡胶体系黏弹性模型示意图;(c) 碳纳米弹簧填充橡胶体系拉伸回复过程示意图
进一步采用分子动力学模拟的方法,系统研究可发生回复变形的大尺寸碳纳米填料——碳纳米管和石墨烯带填充的顺丁橡胶纳米复合材料,以及填料对复合材料黏弹性的影响[23]。
(1)碳纳米管填充的顺丁橡胶纳米复合材料
将碳纳米管与顺丁橡胶共混,制备纳米复合材料,如图4.34(a)所示。碳纳米管的填充分数w=12.0%,顺丁橡胶的交联密度ρ1=0.0011mol/cm3。采用体系的快照图观察复合材料变形过程中碳纳米管的变化情况,如图4.34(b)和图4.34(c)所示。结果表明,复合材料单轴拉伸的方向不一样,碳纳米管的变形方式也不一样。当复合材料沿z方向拉伸时,碳纳米管会被逐渐拉直;当材料沿x方向拉伸时,碳纳米管的弯曲程度会逐渐增加;总之,当体系回复时,碳纳米管会逐渐回复到变形前的形态。基于这一结果,可以利用柔性碳纳米材料在加载过程中改变形态,吸收一部分能量,在卸载过程中逐渐回复初始形态,释放出能量,从而降低材料的损耗能量,减少滞后损失。

图4.34 碳纳米管填充的顺丁橡胶纳米复合材料
(a)碳纳米管在聚合物基体中的分散;(b)、(c)复合材料单轴拉伸方向对碳纳米管微观形态的影响:(b)z方向拉伸,(c) x方向拉伸蓝色小球代表碳纳米管,红色小点代表聚合物基体;为了方便观察,只显示出其中一根碳纳米管
接下来分析界面作用对复合材料黏弹性的影响。采用界面交联密度表征碳纳米管与橡胶基体的界面作用。界面交联键个数依次为0、50、100和150,对应的界面交联密度ρ2分别为0、0.0016mmol/m2、0.0032mmol/m2和0.0048mmol/m2。随着界面交联密度逐渐升高,材料的力学性能显著增强,如图4.35(a)所示。拉伸应变为200%时,界面交联密度为0.0048mmol/m2的材料的应力是界面交联密度为0的材料的7倍。同时,随着界面交联密度增加,复合材料的永久变形z逐渐减小。这是因为界面作用增强了分子链与碳纳米管之间的协同运动能力,即碳纳米管的运动带动了分子链的运动。为了表征在形变过程中,界面作用对分子链与碳纳米管之间协同作用的影响,表征了纯体系和碳纳米管填充体系中分子链的取向程度,如图4.35(c)所示。很明显,随着界面交联密度的升高,回复后复合材料中的分子链取向程度逐渐接近于分子链的初始态,表明柔性碳纳米管在变形过程中可以带动分子链运动,即分子链与碳纳米管的协同运动。此外,探讨了压缩模式下,界面交联密度对复合材料应力-应变的影响,如图4.35(b)所示。与拉伸模式一致,随着界面交联密度升高,复合材料的力学性能增强,永久变形减小。为了更直观、更具体的体现交联密度对体系黏弹性的影响,计算了复合材料的滞后损失,如图4.35(d)和(e)所示。可以看到,随着界面交联密度升高,在拉伸-回复、压缩-回复两种模式下,材料的滞后损失均逐渐减小。在拉伸-回复模式下,当界面交联密度ρ2=0.0048mmol/m2时,复合材料的滞后损失为31%,明显高于界面交联密度为0时复合材料的滞后损失(61%)。从上面的讨论可知,界面交联密度对复合材料滞后损失的影响与对永久变形的影响规律一致。

图4.35 碳纳米管(w=12.0%)填充的纳米复合材料(ρ1=0.0011 mol/cm3,ρ2单位为mmol/m2)
(a)、(b)界面交联密度对复合材料应力-应变性能的影响:(a)拉伸-回复模式,(b)压缩-回复模式;(c)界面交联密度对分子链取向程度的影响;(d)、(e)交联密度对碳纳米管填充纳米复合材料滞后损失的影响:(d)拉伸-回复模式,(e)压缩-回复模式
除了界面作用以外,我们还研究了在强界面作用下,碳纳米管填充分数对复合材料黏弹性的影响。在模拟体系中,碳纳米管的填充个数依次为6、12、18和24,对应的质量分数w= 6.4%、12.0%、16.9%和21.4%,界面交联键的个数依次为25、50、75和100,以保证在模拟体系中界面交联密度一致(ρ2=0.0016mmol/m2)。研究结果如图4.36所示。

图4.36 碳纳米管填充的纳米复合材料(ρ1=0.0011mol/cm3,界面交联密度ρ2=0.0016mmol/m2)
填充分数对复合材料应力-应变行为的影响:(a)拉伸-回复模式,(b)压缩-回复模式;(c)、(d)填充分数对复合材料滞后损失的影响:(c)拉伸-回复模式,(d)压缩-回复模式
由图4.36(a)可以看出,在拉伸模式、强界面作用下,随着碳纳米管填充分数的增加,复合材料的力学性能显著增强,永久变形逐渐减小。在压缩模式下,也能得到相同的规律,如图4.36(b)所示。计算不同填充分数下材料的滞后损失,结果如图4.36(c)和(d)所示。可以看到,随着填充分数的增加,复合材料的滞后损失逐渐减小。原因如下:在强界面作用下,碳纳米管在聚合物基体中均匀分散。在形变过程中,碳纳米管会协同周围分子链一起运动。填充分数越高,协同运动的分子链越多,复合材料内部的分子链摩擦会逐渐减小,因此复合材料的滞后损失逐渐减小。值得指出的是,在真实的纳米复合材料体系中,由于填充浓度高会导致粒子分散不均匀而形成网络结构,Payne效应增大,因此,即使粒子与基体间存在化学键合,一般也表现为填充浓度越高,损耗因子越大。
(2)石墨带填充的顺丁橡胶纳米复合材料
图4.37显示了石墨带填充纳米复合材料在拉伸-回复过程中,纳米带的变形-回复情况。

图4.37 石墨带填充的顺丁橡胶纳米复合材料的快照图,石墨带填充分数w=12.0%,顺丁橡胶本体交联密度ρ1=0.0011mol/cm3
(a)石墨带在聚合物基体中的分散;复合材料单轴拉伸方向对石墨带微观形态的影响:(b)z方向拉伸,(c)x方向拉伸蓝色小球代表石墨带,红色小点代表聚合物基体;为了方便观察,只显示出其中一根石墨带
由图4.37(a)可以看出,在纳米复合材料中,石墨带处于弯曲状态;当复合材料沿z方向拉伸时,石墨带会被逐渐拉直,如图4.37(b)所示;当复合材料沿x方向拉伸时,石墨带弯曲程度会逐渐增加,如图4.37(c)所示;最终,当复合材料回复时,石墨带都能回复到初始状态。
图4.38显示了界面作用对石墨带填充顺丁橡胶纳米复合材料黏弹性的影响。由图可知,随着界面交联密度增加,即界面作用逐渐增强,复合材料的力学性能显著增强,永久变形显著减小,如图4.38(a)所示;在压缩模式下,也能得到一样规律,如图4.38(b)所示。此外,计算了复合材料的滞后损失,如图4.38(c)和(d)所示;在拉伸-回复、压缩-回复两种模式下,随着界面作用的增强,复合材料的滞后损失均逐渐减小。说明石墨带也能像碳纳米管一样,调控顺丁橡胶的黏弹性。


图4.38 石墨带填充顺丁橡胶纳米复合材料,石墨带填充份数w=12.0%,顺丁橡胶本体交联密度ρ1=0.0011 mol/cm3
界面交联密度ρ2(mmol/m2)对复合材料应力-应变性能的影响:(a)拉伸-回复模式,(b)压缩-回复模式;界面交联密度ρ2(mmol/m2)对碳纳米管填充纳米复合材料滞后损失的影响:(c)拉伸-回复模式,(d)压缩-回复模式
最后,探讨石墨带尺寸对复合材料黏弹性的影响。固定石墨带的宽度,改变石墨带的长度。随着石墨带长度的增加,石墨带所含的碳原子数逐渐增多。研究结果如图4.39所示。由图4.39(a)可以看出,在拉伸模式下,石墨带的力学增强效果存在一个最佳的尺寸;然而,在压缩模式下,随着石墨带尺寸的增加,复合材料的力学性能一直增强,如图4.39(b)所示。计算石墨带尺寸对滞后损失的影响,研究结果如图4.39(c)和图4.39(d)所示。在两种模式下,随着石墨带尺寸的增加,复合材料的滞后损失均逐渐减小。

图4.39 石墨带填充顺丁橡胶纳米复合材料,石墨带填充分数w=12.0%,顺丁橡胶本体交联密度ρ1=0.0011 mol/cm3,界面交联密度ρ2=0.0032 mmol/m2
石墨带尺寸对复合材料应力-应变性能的影响:(a)拉伸-回复模式,(b)压缩-回复模式;石墨带尺寸对纳米复合材料滞后损失的影响:(c)拉伸-回复模式,(d)压缩-回复模式