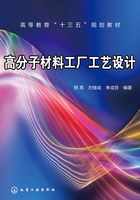
3.1 物料计算
通过物料计算,可以深入地分析和研究生产过程,得出生产过程中所涉及的各种物料的数量和组成,从而使设计由定性转入定量。在整个工艺设计中,物料计算是最先进行的一个计算项目,其结果是后续的能量计算、设备选型或工艺设计、车间布置设计、管道设计等各单项设计的依据,因此,物料衡算结果的正确与否直接关系到整个工艺设计的可靠程度。
物料计算的依据是工艺流程框图以及为物料计算收集的有关资料。虽然工艺流程框图只是定性地给出了物料的来龙去脉,但它决定了应对哪些过程或设备进行物料计算,以及这些过程或设备所涉及的物料,使之既不遗漏,也不重复。可见,工艺流程框图对物料计算起着重要的指导作用。
3.1.1 物料计算的基本知识
(1)基本概念
转化率:生成目标产物的反应物数量占参加反应的反应物起始数量的百分比。
单程转化率是以反应器为体系,总转化率是以整个过程为体系。
选择性:反应物反应生成目的产物所消耗的量占反应物反应掉的量的百分数。
单程收率:指生成为目的产物的反应物数量占反应物(通常指限制反应物)起始数量的百分比。
回收率:指副产物或未参加反应的反应物经处理后可以重新利用的百分比。
流量:指单位时间内物料流过设备的数量。可以是质量流量(物料衡算中用),也可以是体积流量(设备体积计算、管径计算中用)。
产量:指单位时间内生产装置生产出产品的数量,有年产量、月产量、日产量等。
消耗量:指生产单位数量产品所需原材料的数量。
损失量:指生产单位数量产品损失掉原料的数量。
纯度:指物料中含主要成分的百分比。
浓度:指单位体积溶液中含溶质的数量(质量浓度、摩尔浓度)。
配料比:指进入生产装置的各种原料之间的比例关系(质量比、摩尔比)。
限制反应物:化学反应原料不按化学计量比配料时,其中以最小化学计量数存在的反应物称为限制反应物。
过量反应物:不按化学计量比配料的原料中,某种反应物的量超过限制反应物完全反应所需的理论量,该反应物称为过量反应物。
过量百分数:过量反应物超过限制反应物所需理论量的部分占所需理论量的百分数。
(2)理论依据
高分子材料的生产过程是一个既有量变又有质变的一系列转变过程。为了正确地指导生产的各个过程,必须对质和量的变化进行分析。物料计算就是确定生产过程中物料比例和物料转变的定量关系的过程。物料计算意味着设计工作由定性转向定量。
物料计算的基础是物料衡算,它是“质量守恒定律”的一种表现形式。通常,物料衡算有两种情况,一种是对已有的生产设备或装置,利用实际测定的数据,算出另一些不能直接测定的物料量,用此计算结果,对生产情况进行分析、做出判断、提出改进措施。另一种是设计一种新的设备或装置,根据设计任务,先作物料衡算,求出进出各设备的物料量,然后再作能量衡算,求出设备或过程的热负荷,从而确定设备尺寸及整个工艺流程。
进行物料衡算时,必须先确定衡算的体系。根据质量守恒定律,在某一个生产过程中,进入的物料量应该等于排出物料量与过程积累量之和。或者说,进入某一设备进行操作的物料量必须等于操作后所得产物的重量加上物料损失。可用下面方程式表示。
(3-1)
式中 ∑G——输入物料量的总和;
∑G'——输出物料量的总和;
∑Gloss——物料损失量总和。
物料衡算可以以主要产品的单位质量(kg、t)或以过程的单位时间(h、d)的输入、输出的物料量进行计算。输入和输出的量可以根据式(3-2)将固相、液相、气相物料分别列出。
(3-2)
一个过程不一定总是包含所有的相或只含有一个相的物料。因此式(3-2)可根据情况写成一个简单式或更复杂的形式。
如果体系内发生化学反应,则对任一个组分或任一种元素作衡算时,必须把反应消耗或生成的量亦考虑在内。
理论的物料衡算可以通过化学方程式来计算。实际的物料衡算则需要考虑到起始物料组成和最终产品的组成、每种组分的余量、转化率、原料和产品的损失量等。
3.1.2 物料计算的一般步骤及结果处理
在进行物料衡算,特别是做那些复杂的物料衡算时,为了能顺利地解题,避免错误,必须掌握解题技巧,按正确的解题方法和步骤进行。一般须遵循下面的计算步骤。
1)画出物料衡算示意图
注上与物料衡算有关的数据。最简单的物料衡算示意图如图3-1所示。

图3-1 物料衡算示意图
2)写出化学反应方程式
包括主、副反应。只属于物理过程的,此步骤可免去。
3)确定计算任务
如年产量、年工作日、日生产能力、纯度、产率、制成率或损耗等。
4)选定计算基准
在物料计算和能量计算过程中,恰当的选择计算基准可以使计算简化,缩小计算误差。常用的计算基准有。
①时间基准 对于连续生产,以1段时间间隔,如1s、1h、1d等的投料量或生产产品量为计算基准。这种基准可以联系到生产规模和设备计算,如,年产3000t的PP树脂,年工作日为300d,平均产量可计为10t·d-1,或417kg·h-1。
对间歇生产,常常以加入设备的一批原料或一批料的生产周期作为基准。选批次作为基准时的单位为kg·B-1、m3·B-1等
②单位重量、单位体积或单位摩尔量的原料或产品 如1kg、1000kg等作为基准。若每千克产品消耗原料1.012kg,则可计为1.012kg·kg-1,或1012kg·t-1。
对液、固物料进行衡算时常选用重量基准,气体物料选用体积基准,若物料为一系列的化合物,或者由已知组成百分数和组分分子量的多组分组成,用物质的量(摩尔)作为基准更为方便。
对于不同化工过程,采用什么基准适宜,需视具体情况而定,不能作硬性规定。
5)选择物理化学及工艺常数以及计算所必要的数据
如临界参数、密度或比体积、状态方程参数、蒸气压、气液平衡常数或平衡关系、黏度、扩散参数等。
6)由已知数据,根据式(3-1)和式(3-2)进行物料衡算
7)将物料衡算结果列出物料衡算表,必要时画出物料衡算图
物料衡算表的表格形式看参考表3-1。
表3-1 ××阶段物料衡算表

通过生产过程中各阶段的物料衡算就可以得出以下内容。
①生产1吨100%半成品或成品的原料消耗定额;
②生产1吨100%成品所产生的排出,包括副产品、废水、废弃、废物等。排出物量在多数情况下是同热量计算有关,物料计算所得的排出物只是其中一部分。
再经过各种系数的转换和计算工作,最后得出原材料消耗综合表和排出物综合表。表格形式看参考表3-2和表3-3。
表3-2 原料消耗综合表

表3-3 排出物综合表

3.1.3 物料计算举例
【例3-1】 采用蒸发方法将浓度为10%NaOH及10%NaCl的水溶液进行浓缩。蒸发时只有部分水分汽化成为水蒸气而逸出,部分NaCl结晶成晶粒而留在母液中。操作停止后,分析母液的成分为:50%NaOH,2%NaCl及48%H2O。若每批处理1000kg原料液,试求每批操作中:①获得的母液量;②蒸发出的水分量;③结晶出的NaCl量。
解:(1)选择计算基准。本题为间歇过程,因此以每批处理量为基准进行物料衡算。
(2)画物料流程简图

(3)列物料衡算式
NaOH 1000×0.1=0.5F4
NaCl 1000×0.1=0.02F4+F3
H2O 1000(1-0.1-0.1)=F2+0.48F4
解方程得:F2=704kg,F3=96kg,F4=200kg
【例3-2】 含CH490%和C2H610%(mol%)的天然气与空气在混合器中混合,得到的混合气体含CH448%。试计算100mol天然气应加入的空气量及得到的混合气量。
解:设A为所需空气量,M为混合气量,x为混合气中C2H6的含量。
(1)画物料流程简图

(2)计算基准:100mol天然气
(3)列物料衡算式
总物料 100+A=M ①
CH4 100×0.9=M×0.08 ②
C2H6 100×0.1=M×x ③
联立方程①、②、③,解得A=1025mol,M=1125mol,x=0.009mol。
(4)核算
空气含量 1-0.08-0.009=0.911
加入空气量 A=1025mol,占混合气含量为
1025÷1125=0.911
两者相等,所以计算正确。
【例3-3】 年产2000吨硬聚氯乙烯管材专用树脂的物料衡算。
解:
(1)计算基准的选取
①年工作时间 8h/天
365天-104天(休息日)-11天(法定节假日)=250天=2000h
②设备大修时间 20天/年=160h/年
③特殊情况停车 10天/年=80h/年
④设备启动、更换品种清洗设备时间:1次/天,0.5h/次
(250天-20天-10天)×1/7次/天×0.5h/次=110h≈14天
⑤实际开车时间 365-104-11-20-10-14=206天/年=1648h/年
⑥设备利用系数 k=实际开车时间/年工作时间=1648/2000=0.824
(2)工艺流程图
①物料配比 为了计算方便,通常将配方中的各组分份数换算为百分含量。见表1。
【例3-3】表1 物料配比表

②绘制流程框图,见图1。

【例3-3】图1 流程框图
(3)确定计算任务
挤出造粒机为连续操作,其他均属于间歇操作,需要建立时间平衡。由设计任务和生产现场可知生产规模、生产时间、消耗定额、各装置损失以及配方等工艺操作条件。可以物料流向展开计算,并按间歇过程与连续过程分别确定基准依次计算。
间歇过程基准:kg·B-1;连续过程基准:kg·h-1。
(4)生产的基础数据
挤出造粒机启动等物料损失:2000t/年÷1648h×110h≈133.5(t/年);
筛选机物料损耗率0.1%;
螺旋输送机损耗率0.1%;
高速混、冷混总损耗率0.2%;
筛分机的产品率92%;
筛分机的物料损耗率0.1%;
破碎机的物料损耗率0.5%;
废料利用率90%;
包装损耗率0.05%。
(5)过程物料计算
进入本工序的物料量=出料量÷(1-本工序的损失率)。通常是从得到的产品开始推算,即从后往前算。
①进入包装工序的物料量 2000/(1-0.05%)≈2001(t/年)
包装工序的损失量 2001-2000=1(t/年)
②进入中间贮存工序的物料量 2001/(1-0.1%)≈2003(t/年)
中间贮存工序的损失量 2003-2001=2(t/年)
③筛分的成品率为92%,设筛分出的大块和小块废料各占50%,则
进入筛分机的物料量 2003/[(1-0.1%)×92%]≈2179.4(t/年)
筛分机的损失量 2003×0.1%≈2(t/年)
筛分出的大块废料量 (2179.4-2003-2)×50%=87.2(t/年)
筛分出的小块废料量 (2179.4-2003-2)×50%=87.2(t/年)
④进入挤出造粒机的物料量
⑤进入螺旋输送机的物料量 2312.9/(1-0.1%)≈2315.3(t/年)
⑥因破碎机的损耗率为0.5%,废料的利用率为90%,则
回收料量 [(87.2+133.5)×(1-0.5%)]+87.2≈306.8(t/年)
进入混合工序的物料量
混合工序的损失量 2315.3×0.2%≈4.6(t/年)
⑦进入混合工序的各组分量分别为
PVC 2043.9×87%≈1778.2(t/年)
CaSt 2043.9×2.6%≈53.1(t/年)
硫醇甲基烯 2043.9×1.7%≈34.7(t/年)
马来酸二正辛基锡 2043.9×0.87%≈17.8(t/年)
CaCO3 2043.9×6.96%≈142.3(t/年)
石蜡 2043.9×0.87%≈17.8(t/年)
⑧PVC投料量 1778.2/(1-0.1%)≈1780(t/年)
PVC损失量 1780-1778.2=1.8(t/年)
⑨生产中废料产生总量 1+2+2+133.5+87.2+87.2+2.4+4.6+1.8=321.7(t/年)
回收利用量=306.8×90%=276.1(t/年)
实际损耗=321.7-276.1=45.6(t/年)
(6)填写物料平衡表(表2)
【例3-3】表2 全过程物料平衡表

(7)计算出实际每年原料消耗量,并填写原料消耗表(表3)
【例3-3】表3 原料消耗表

(8)根据计算结果画出物料衡算流程图(图2)

【例3-3】图2 物料衡算流程图
【例3-4】 甲醇制造甲醛的反应过程为:
反应物及生成物均为气态,若使用50%的过量空气,且甲醇的转化率为75%,试计算反应后气体混合物的摩尔组成。
解:(1)画出流程图

(2)计算基准 1mol CH3OH
(3)物料衡算
根据反应方程式可知,完全反应时需要的氧气量为0.5mol,则氧气输入量
O2(输入)=1.5×0.5=0.75mol
氮气不参加反应,故反应前后氮气量不变,即
N2(输入)=N2(输出)=0.75×(79/21)=2.82mol
CH3OH为限制反应物,其转化率为75%,故参与反应的CH3OH为
CH3OH(反应)=0.75×1=0.75mol
于是,
HCHO(输出)=0.75mol
CH3OH(输出)=1-0.75=0.25mol
O2(输出)=0.75-0.75×0.5=0.375mol
H2O(输出)=0.75mol
(4)计算结果(表1)
【例3-4】表1 反应后气体混合物的摩尔组成

【例3-5】 用氟石(含96%CaF2和4%SiO2)为原料,与93%H2SO4反应制造氟化氢,其反应式如下。
主反应:CaF2+H2SO4 CaSO4+2HF
副反应:SiO2+6HF H2SiF6+2H2O
氟石分解度为95%,每千克氟石实际消耗93%H2SO4为1.42千克。计算:①每生产1000千克HF消耗的氟石量;②H2SO4的过量百分数。
解:(1)计算基准:100kg氟石
(2)物料衡算
①物质分子量

②HF量的计算
生成的HF量
100×96%×95%×(2×20)/78=46.77(kg)
副反应消耗的HF量
100×4%×95%×(6×20)/60=7.6(kg)
实际得到的HF量
46.77-7.6=39.17(kg)
③氟石耗量的计算
每生产1000kgHF的氟石消耗量为
(100/39.17)×1000=2553(kg)
④硫酸量的计算
因每千克氟石实际消耗93%H2SO4为1.42千克,故100kg氟石实际消耗H2SO4量为
100×1.42×93%=132.06(kg)
100kg氟石完全分解需要H2SO4的理论量为
100×96%×98/78=120.61(kg)
H2SO4过量百分数为
(132.06-120.61)/120.61×100%=9.49%
【例3-6】 年生产2万吨PVC车间的物料计算。
(1)画流程示意图

(2)写出化学反应式

(3)确定计算任务
聚合与沉析(混料槽)均属于间歇操作,需要建立时间平衡。由设计任务和生产现场可知生产规模、生产时间、消耗定额、各装置损失以及聚合配方等工艺操作条件。可以物料流向展开计算,并按间歇过程与连续过程分别确定基准依次计算。
间歇过程基准:kg·B-1;连续过程基准:kg·h-1。
(4)生产的基础数据
①生产规模 20000吨PVC/年;
②生产时间 8000h;
③聚合釜 体积33m3、装料系数0.9、每釜投料量10t、平均每釜产量8486kg;
④生产周期 见表1。
【例3-6】表1 生产周期/h

⑤损耗分配 聚合车间总收率为94.8%,总消耗为6.2%。各步骤的损失分配如表2所示(间歇过程以单体进料量为准,连续过程以聚合釜内反应生成的聚合物为准)。
【例3-6】表2 各步骤的损失分配

⑥聚合配方 为方便起见,单体纯度按100%计算;新鲜料与回收料比例为9∶1,水油比(软水/VC)为1.85。其他助剂用量如表3所示。
【例3-6】表3 助剂配方

⑦操作时间与控制指标 见表4。
【例3-6】表4 设备的操作时间与控制指标

⑧原料、助剂、产品规格(略)。
⑨理化数据 物化常数:42%液碱比重为1.45;热数据见表5。
【例3-6】表5 热数据

(5)全过程物料计算(表6、表7)
【例3-6】表6 物料计算表


【例3-6】表7 全过程物料平衡表

(6)各装置物料衡算
①聚合釜装置(表8、表9)
【例3-6】表8 聚合釜物料计算表

【例3-6】表9 聚合釜物料平衡表

②混料槽装置(表10、表11)
【例3-6】表10 设备及物料升温(包括VC气化)需热量计算表

注:1.助剂所占比例甚微,并入水中一起计算。
2.由于去汽提塔的VC量甚微,这里并入气化部分一起计算。
【例3-6】表11 混料槽装置物料平衡表

混料槽装置进入的料除聚合釜来料外,尚需加液碱和通入直接蒸汽。按工艺条件规定加42%NaOH水溶液14L,重量为
1.45×14=20.3(kg)
其中,纯NaOH 20.3×42%=8.526(kg)
水 20.3-8.526=11.774(kg)
假设未反应的VC液体除在混料槽及后续的汽提操作中损失外,全部在混料槽内气化予以回收。碱处理时,通直接蒸汽升温所产生冷凝水量可由热量衡算求得。故混料槽内的总水量为
18680.633+11.774=18692.407(kg)
H2O汽化热2370kJ/kg。按热损失10%及系数1.1计算,每个混料槽在每次操作中需通入蒸气量W为
水的出料量 18680.633+11.774+818.48=19510.887(kg)
VC损失量 10000×0.8%=80(kg)
PVC损失量 9000×0.8%=72(kg)
气化回收VC量 10000×9%=900(kg)
混料槽VC出料量 990-900-80=10(kg)
PVC出料量 8982-72=8910(kg)
助剂量 2.5+3.65+3.65+2.5+4.6+2+4=22.9(kg)
③汽提塔装置(表12)
【例3-6】表12 汽提塔装置物料平衡表

从此装置开始转入连续操作过程,计算基准由kg/釜改为kg/h。质量以聚合釜内生成的聚合物为基准。根据全年生产任务和生产时间求出每小时PVC产量为
20000t/7200h=2777.78(kg·h-1)
产品中含水0.2%,则绝干树脂产量为
2777.78×(1-0.002)=2772.22(kg·h-1)
以2772.22÷(1-5.2%)=2924.28(kg/h)为连续过程质量基准进行计算。
考虑到各步损失后,汽提塔进料中应含绝干树脂量为:
2924.28×(1-1%)=2895.04(kg·h-1)
其中,1%为聚合釜和混料槽中PVC损失百分数,按混料槽出料组成,以2895.04kg·h-1为基准,计算各组分的含量:
VC 10×(2895.04÷8910)=3.25(kg)
水 19510.887×(2895.04÷8910)=6339.48(kg)
助剂+NaOH(22.9+8.526)×(2895.04÷8910)=31.426×(2895.04÷8910)=10.21(kg)
PVC损失量 2924.28×0.2%=5.85(kg·h-1)
PVC出料量 2895.04-5.85=2889.19(kg)
VC损失量 2924.28×0.1%=2.92(kg·h-1)
VC汽提量 3.25-2.92=0.33(kg),进入废气处理系统或直接燃烧。
水的出料量 6339.48+700=7039.48(kg)
④离心装置(表13)
【例3-6】表13 离心操作物料平衡表

进料量为汽提塔出料量,其中VC含量可忽略不计。
洗涤热水用量 1500(kg·h-1)
离心操作损失PVC量2924.28×0.5%=14.62(kg·h-1)
PVC出料量 2889.19-14.62=2874.57(kg)
离心后湿物料仍含水分20%,则
含水量 2874.57×(20%÷80%)=718.64(kg)
母液中含水 7039.48+1500-718.64=7820.84(kg)
⑤气流干燥(表14)
【例3-6】表14 气流干燥物料平衡表

进料量为离心操作的出料量。
气流干燥损失PVC 2924.28×1%=29.24(kg·h-1)
PVC出料量为 2874.57-29.24=2845.33(kg)
离心后湿物料仍含水分5%,则
含水量 2845.33×(5%÷95%)=149.75(kg)
脱走水 718.64-149.75=568.89(kg)
⑥沸腾干燥(表15)
【例3-6】表15 沸腾干燥物料平衡表

进料量为气流干燥出料量。
沸腾干燥损失PVC量 2924.28×1%=29.24(kg·h-1)
PVC出料量 2845.33-29.24=2816.09(kg)
离心后湿物料仍含水分0.2%,则
含水量 2816.09×(0.2%÷99.8%)=5.64(kg)
脱走水量 149.75-5.64=144.11(kg)
(7)筛分包装(表16)
【例3-6】表16 筛分包装装置物料平衡表

进料量为沸腾干燥出料量。
筛分包装损失PVC量 2924.28×1.5%=43.86(kg·h-1)
包装入库的绝干PVC量 2816.09-43.86=2772.23(kg)
随PVC树脂损失的相应水量 43.86×(0.2%÷99.8%)=0.09(kg)
树脂中含水量 5.64-0.09=5.55(kg)
(8)原材料消耗表(略)
(9)画出物料衡算流程图(略)