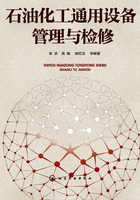
第七节 阀 门
阀门在机械工程图中是以符号的形式标注其所在位置,《综合材料表》给出各种阀门的类型、公称通径、公称压力、材料、总的数量和阀门标准号等,《管段表》则给出阀门所在某一具体管段的管段编号、起止点、管道等级、设计温度、设计压力、阀门类型、公称通径、公称压力、材料、数量和标准号。
一、阀门概述
阀门是通过改变其流道面积大小来控制流体流量压力和流向的机械产品。阀门规格品种繁多,为统一制造标准及正确选用和识别阀门,我国阀门行业规定了“三化”标准,即系列化、通用化、标准化的标准。
(一)阀门的种类
阀门的种类繁多,称谓也不统一,有按使用功能分类的,有按公称压力分类的,有按阀体材料分类的等等。
1.按使用功能分类
(1)截断(或闭路)阀类 接通或截断管路中介质,包括闸阀、截止阀、旋塞阀、隔膜阀、球阀和蝶阀等。
(2)止回(或单向、逆止)阀类 防止管路中介质倒流,包括止回阀和底阀。
(3)调节阀类 调节管路中介质流量、压力等参数,包括节流阀、减压阀及各种调节阀。
(4)分流阀类 分配、分离或混合管路中的介质,包括旋塞阀、球阀和疏水阀等。
(5)安全阀类 防止介质压力超过规定数值,对管路或设备进行超载保护,包括各种形式的安全阀、保险阀。
2.按公称压力分类
(1)真空阀 工作压力用真空度表示。
(2)低压阀 公称压力PN≤1.6MPa。
(3)中压阀 1.6MPa<PN<10MPa。
(4)高压阀 10MPa≤PN<100MPa。
(5)超高压阀 PN>100MPa。
3.按驱动方式分类
(1)手动阀 用人力操纵手轮、手柄或链轮驱动阀门。
(2)动力驱动阀 利用动力源驱动阀门,包括电磁阀、气动阀、液动阀、电动阀及各种联动阀。
(3)自动阀 凭借管路中介质本身能量驱动阀门,包括止回阀、安全阀、减压阀、疏水阀及各种自力式调节阀。
4.按阀体材料分类
(1)铸铁阀 阀体材料采用压铸铁、可锻铸铁、球墨铸铁和高硅铸铁等。
(2)铸铜阀 阀体材料包括青铜、黄铜。
(3)铸钢阀 阀体材料包括碳素钢、合金钢和不锈钢等。
(4)锻钢阀 阀体材料包括碳素钢、合金钢和不锈钢等。
(5)钛阀 阀体材料采用钛及钛合金。
5.按使用部门分类
(1)通用阀 广泛用于各种工业部门。
(2)电站阀 应用于火力、水力、核电厂(站)。
(3)船用阀 应用于船舶、舰艇。
(4)冶金用阀 应用于炼铁、炼钢等冶金部门。
(5)管线阀 应用于输油、输气管线。
(6)水暖用阀 应用给排水、采暖设施。
(二)阀门的压力-温度等级
阀门的最大允许工作压力随工作温度的升高而降低。压力-温度等级是阀门设计和选用的基准,在选用阀门时应特别注意。
采用GB/T 9112~GB/T 9122标准法兰的钢制阀门在不同工作温度下的最大允许工作压力按式(2-6)计算:
p=ϕ·PN (2-6)
式中 ϕ——系数(请查有关阀门手册);
PN——阀门的公称压力,MPa。
二、阀门检验与管理
(一)阀门检验
1.一般规定
(1)阀门必须具有质量证明文件。阀体上应有制造厂铭牌,铭牌和阀体上应有制造厂名称、阀门型号、公称压力、公称通径等标识,且应符合《通用阀门标志》(GB/T 12220)的规定。
(2)阀门的产品质量证明文件应有如下内容:
①制造厂名称及出厂日期;
②产品名称、型号及规格;
③公称压力、公称通径、适用介质及适用温度;
④依据的标准、检验结论及检验日期;
⑤出厂编号;
⑥检验人员及负责检验人员签章。
(3)设计要求做低温密封试验的阀门,应有制造厂的低温密封试验合格证明书。
(4)铸钢阀门的磁粉检验和射线检验由供需双方协定,如需检验,供方应按合同要求的检验标准进行检验,并出具检验报告。
(5)设计文件要求进行晶间腐蚀试验的不锈钢阀门,制造厂应提供晶间腐蚀试验合格证明书。
(6)阀门安装前必须进行外观检查。
2.外观检查
(1)阀门运输时的开闭位置应符合下列要求:
①闸阀、截止阀、节流阀、调节阀、蝶阀、底阀等阀门应处于全关闭位置;
②旋塞阀、球阀的关闭件均应处于全开启位置;
③隔膜阀应处于关闭位置,且不可关得过紧,以防止损坏隔膜;
④止回阀的阀瓣应关闭并予以固定。
(2)阀门不得有损伤、缺件、腐蚀、铭牌脱落等现象,且阀体内不得有脏污。
(3)阀门两端应有防护盖保护。手柄或手轮操作应灵活轻便,不得有卡涩现象。
(4)阀体为铸件时,其表面应平整光滑,无裂纹、缩孔、砂眼、气孔、毛刺等缺陷;阀体为锻件时,其表面应无裂纹、夹层、重皮、斑疤、缺肩等缺陷。
(5)止回阀的阀瓣或阀芯动作应灵活准确,无偏心、移位或歪斜现象。
(6)弹簧式安全阀应具有铅封,杠杆式安全阀应有重锤的定位装置。
(7)衬胶、衬搪瓷及衬塑料的阀体内表面应平整光滑,衬层与基体结合牢固,无裂纹、鼓泡等缺陷,用高频电火花发生器逐个检查衬层表面,以未发现衬层被击穿(产生白色闪光现象)为合格。
(8)阀门法兰密封面应符合要求,且不得有径向划痕。
3.阀门传动装置的检查与试验
(1)采用齿轮、蜗轮传动的阀门,其传动机构应按下列要求进行检查与清洗:
①蜗杆和蜗轮应啮合良好、工作轻便,无卡涩或过度磨损现象。
②开式机构的齿轮啮合面、轴承等应清洗干净,并加注新润滑油脂。
③有闭式机构的阀门应抽查10%且不少于一个,其机构零件应齐全、内部清洁无污物、传动件无毛刺、各部间隙及啮合面符合要求。如有问题,应对该批阀门的传动机构逐个检查。
④开盖检查如发现润滑油脂变质,将该批阀门的润滑油脂予以更换。
(2)带链轮机构的阀门,链架与链轮的中心面应一致。按工作位置检查链条的工作情况,链条运动应顺畅不脱槽,链条不得有开环、脱焊、锈蚀或链轮与链条节距不符等缺陷。
(3)气压、液压传动的阀门,应以空气或水为介质,按活塞的工作压力进行开闭检验。必要时,应对阀门进行密封试验。
(4)电动阀门的变速箱除按上述(1)中的规定进行清洗和检查外,尚应复查联轴器的同轴度,然后接通临时电源,在全开或全闭的状态下,检查、调整阀门的限位装置,反复试验不少于三次,电动系统应动作可靠、指示准确。
(5)电磁阀门应接通临时电源,进行开闭试验,且不得少于三次。必要时应在阀门关闭状态下,对其进行密封试验。
(6)具有机械联锁装置的阀门,应在安装位置的模拟架上进行试验和调整。两阀门应启闭动作协调、工作轻便、限位准确。
4.其他检查和检验
(1)对焊接连接阀门的焊接接头坡口,应按下列规定进行磁粉或渗透检测:
①标准抗拉强度下限值σb=1540MPa的钢材及Cr-Mo低合金钢材的坡口应进行100%检测;
②设计温度低于或等于-29℃的非奥氏体不锈钢坡口应抽检5%。
(2)合金钢阀门应采用光谱分析或其他方法,逐个对阀体材质进行复查,并做标记。不符合要求的阀门不得使用。
(3)合金钢阀门和剧毒、可燃介质管道阀门安装前,应按设计文件中的“阀门规格书”对阀门的阀体、密封面以及有特殊要求的垫片和填料的材质进行抽查,每批至少抽查一件。若有不合格,该批阀门不得使用。
(二)阀门试验(SH 3518—2013)
1.一般规定
(1)阀门试验包括壳体压力试验、密封试验和安全阀、减压阀、疏水阀的调整试验。
(2)阀门应按相应规范确定的检查数量进行壳体压力试验和密封试验,具有上密封结构的阀门,还应进行上密封试验。
(3)对于壳体压力试验、上密封试验和高压密封试验,试验介质可选择空气、惰性气体、煤油、水或黏度不高于水的非腐蚀性液体。低压密封试验介质可选择空气或惰性气体。
(4)用水作试验介质时,允许添加防锈剂,奥氏体不锈钢阀门试验时,水中氯化物含量不得超过100mg/L。
(5)无特殊规定时,试验介质的温度宜为5~50℃。
(6)阀门试验前,应除去密封面上的油渍和污物,严禁在密封面上涂抹防渗漏的油脂。
(7)试验用的压力表,应鉴定合格并在周检期内使用,精度不应低于1.5级,表的满刻度值宜为最大被测压力的1.5~2倍。试验系统的压力表不应少于两块,并分别安装在储罐、设备及被试验的阀门进口处。
(8)装有旁通阀的阀门,旁通阀也应进行壳体压力试验和密封试验。
(9)试验介质为液体时,应排净阀门内的空气,阀门试压完毕,应及时排除阀门内的积液。
(10)经过试验合格的阀门,应在阀体明显部位做好试验标识,并填写试验记录。没有试验标识的阀门不得安装和使用。
2.阀门壳体压力试验
(1)阀门壳体压力试验的试验压力应为阀门公称压力的1.5倍。
(2)阀门壳体压力试验最短保压时间应为5min。如果试验介质为液体,壳体外表面不得有滴漏或潮湿现象,阀体与阀体衬里、阀体与阀盖接合处不得有泄漏;如果试验介质为气体,则应按规定的检漏方法检验,不得有泄漏现象。
(3)夹套阀门的夹套部分应以1.5倍的工作压力进行压力试验。
(4)公称压力小于1MPa且公称通径大于或等于600mm的闸阀,壳体压力试验可不单独进行,可在管道系统试验中进行。
3.阀门密封试验
(1)阀门密封试验包括上密封试验、高压密封试验和低压密封试验,密封试验必须在壳体压力试验合格后进行。
(2)阀门密封试验项目应根据直径和压力按规定进行选取。当公称直径小于或等于100mm、公称压力小于或等于25MPa和公称直径大于100mm、公称压力小于或等于10MPa时,应按表2-21选取;当公称直径小于或等于100mm、公称压力大于25MPa和公称直径大于100mm、公称压力大于10MPa时,应按表2-22选取。
(3)阀门高压密封试验和上密封试验的试验压力为阀门公称压力的1.1倍,低压密封试验压力为0.6MPa,保压时间见表2-23,以密封面不漏为合格。
(4)公称压力小于1MPa且公称通径大于或等于600mm的闸阀可不单独进行密封试验,宜用色印方法对闸板密封副进行检查,接合面连续为合格。
表2-21 阀门密封试验(一)

①要求对所有阀门进行上密封试验,但具备上密封特征的波纹管密封阀除外。
②对润滑旋塞阀来讲,进行高压密封试验是强制性的,而低压密封试验是可选择的。
③如果购买商同意,阀门制造厂可用低压密封试验代替高压密封试验。
④弹性座阀门进行高压密封试验后在低压情况下使用可能会降低其密封性。
⑤对于动力操作截止阀,高压密封试验应按确定动力阀动器规格时设计压差的1.1倍来进行。
表2-22 阀门密封试验(二)

①这些阀门均必须进行上密封试验,但具备上密封特征的波纹管密封阀除外。
②经买方同意后,阀门制造厂家可以使用低压密封试验代替高压密封试验。
③弹性座阀门进行高压密封试验后在低压情况下使用可能会降低其密封性。
④在动力操作的球阀中,高压密封试验应按确定动力阀动器规格时设计压差的1.1倍来进行。
表2-23 密封试验保压时间

(5)上密封试验的基本步骤:封闭阀门进、出口,松开填料压盖,将阀门打开并使上密封关闭,向腔内充满试验介质,逐渐加压到试验压力,达到保压规定时间后,无渗漏为合格。
(6)做密封试验时,应向处于关闭状态的被检测密封副的一侧腔体充满试验介质,并逐渐加压到试验压力,达到规定保压时间后,在该密封副的另一侧,目测渗漏情况。引入介质和施加压力的方向应符合下列规定:
①规定了介质流向的阀门,如截止阀等应按规定介质流通方向引入介质和施加压力;
②没有规定介质流向的阀门,如闸阀、球阀、旋塞阀和蝶阀,应分别沿每一端引入介质和施加压力;
③有两个密封副的阀门也可以向两个密封副之间的体腔内引入介质和施加压力;
④止回阀应沿使阀瓣关闭的方向引入介质和施加压力。
(三)安全阀调整试验
(1)安全阀的调整试验应包括如下项目:
①开启压力;
②回座压力;
③阀门动作的重复性;
④用目测或听觉检查阀门回座情况,有无频跳、颤振、卡阻或其他有害的振动。
(2)安全阀应按设计要求进行调试,当设计无要求时,其开启压力应为工作压力与背压之差的1.05~1.15倍,回座压力应不小于工作压力的90%。
(3)安全阀开启、回座试验的介质可按表2-24中的规定选用。
表2-24 试验介质

①如无适合的饱和蒸汽,允许使用空气,但安全阀投入运行时,应重新调试。
(4)安全阀开启和回座试验次数应不少于三次,试验过程中,使用单位及有关部门应在现场监督确认。试验合格后应做铅封,并填写“安全阀调整试验记录”。
(四)其他阀门调整试验
(1)减压阀调压试验及疏水阀的动作试验应在安装后的系统中进行。
(2)减压阀在试验过程中,不应做任何调整,当试验条件变化或试验结果偏离时,方可重新进行调整,且不得更换零件。
(3)疏水阀试验应符合下列要求:
①动作灵敏、工作正常;
②阀座无漏气现象;
③疏水完毕后,阀门应处于完全关闭状态;
④双金属片式疏水阀,应在额定的工作温度范围内动作。
(五)阀门管理
1.阀门存放
(1)阀门出入库房,应按照铭牌上的主要内容进行登记、建账。试验合格的阀门应做试验记录和标记。
(2)阀门宜放置在室内库房,并按阀门的规格、型号、材质分别存放。对不允许铁污染的钛材等有色金属阀门和超低碳不锈钢阀门,放置、保管时,应采取防护措施。
(3)返库的阀门,应重新登记。壳体压力试验和密封试验后的阀门,闲置时间超过半年,使用前应重新进行检验。
(4)阀门在保管运输过程中,不得将索具直接拴绑在手轮上或将阀门倒置。
2.阀门防护
(1)外露阀杆的部位,应涂润滑脂进行保护。
(2)除塑料和橡胶密封面不允许涂防锈剂外,阀门的其他关闭件和阀座密封面应涂工业用防锈油脂。
(3)阀门的内腔、法兰密封面和螺栓螺纹应涂防锈剂进行保护。
(4)阀门试验合格后,内部应清理干净,阀门两端应加防护盖。
3.阀门资料管理
(1)制造厂提供的质量证明文件,应与实物相对应,建账管理。
(2)检试验合格的阀门,检试验部门出具材质复验报告、阀门试验记录和安全阀调整试验记录等文件,并应由有关人员签字,专人保管。
(3)阀门出库时,应根据现行《石油化工工程建设交工技术文件规定》(SH 3503—2017)中的要求,将制造厂提供的质量证明文件和有关检试验记录交有关部门,作为交工资料。