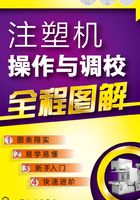
四、塑化部件
塑化部件的作用就是将塑料塑化成高质量、均匀的熔体,然后将其注入型腔内。因此,对于任何塑化部件在设计时都应有一个明确的要求,以实现较高的塑化能力。一般注塑机构的塑化部件主要由螺杆、料筒和喷嘴组成。
1.螺杆
(1)螺杆的作用及分类
作为注塑机构的重要塑化部件,螺杆是塑化部件的核心。它是在电动机或液压马达的驱动下转动,完成树脂的受热、受压、塑化,并在熔体的输送中充分混合、均匀塑化,完成后将塑化好的熔料注入模具型腔的部件。
为适应加工塑料性能(如软化温度范围、硬度、黏度、摩擦系数、比热容、热稳定性、导热性等)的不同要求,需将螺杆制成不同的形式。螺杆根据塑料性质不同,一般可分为通用型螺杆、渐变型螺杆和突变型螺杆,如图1-22所示。

图1-22 螺杆的类型
①通用型螺杆。通用型螺杆的压缩段长度介于渐变和突变之间,3~5个螺距。适应性比较强的通用型螺杆,可适应多种塑料的加工,避免频繁更换螺杆,有利于提高生产效率。
②渐变型螺杆。压缩段较长,塑化时能量转换缓和,多用于聚氯乙烯等,软化温度较宽、高黏度的非结晶型塑料。
③突变型螺杆。压缩段较短,塑化时能量转换较剧烈,多用于聚烯烃、聚酰胺类的结晶型塑料。
通用型螺杆也有缺点。对某种塑料来说,它在塑化和能耗等方面比不上专用型螺杆。螺杆材料要求耐磨、抗腐蚀,大多采用优质氮化钢。螺杆应有较高的精度和较低的表面粗糙度值。
(2)螺杆的结构类型及几何参数
①螺杆的结构类型。螺杆是注射装置的关键部件,主要功能是对塑料原料进行搅拌、剪切并将熔融的塑料熔注入模具内。螺杆的基本结构如图1-23所示,主要由有效螺纹长度和尾部的连接部分组成。螺杆头部设有装螺杆头的反向螺纹。

图1-23 螺杆基本结构
螺杆的几何参数将直接影响塑料的塑化质量、注射率、使用寿命,并将最终影响注塑机的注塑成型周期和制品质量。普通螺杆螺纹有效长度(L)通常分成三段,即加料段(输送段,L1)、压缩段(塑化段,L2)、均化段(计量段,L3)。螺杆的分段指的是这三段在整个螺杆有效工作长度中所占的百分比。相比挤出机的螺杆,注塑机螺杆因为轴向移动,加料段比较长,一般占整个螺杆长度的一半左右,其余两部分各点四分之一。各段的具体长度的比例可参考表1-11。
表1-11 螺杆各段长度

②螺杆的几何参数。螺杆的几何参数说明见表1-12。
表1-12 螺杆的几何参数


(3)加工热塑性塑料用的常规螺杆
通常一台注塑机配备一根标准的中径螺杆及两根高、低压的常规螺杆(图1-24)就能满足通用塑料及工程塑料的加工。

图1-24 加工热塑性塑料的常规螺杆
L—螺杆螺纹部分的有效长度;L1—加料段长度;L2—熔融段长度;L3—计量段长度;D—螺杆直径;h3—计量段螺槽深度;h1—加料段螺槽深度;S—熔融段螺距;t—加料段螺距;e—螺棱宽度
注塑机螺杆的工作特性与挤出机螺杆的工作特性有很大的不同,所以螺杆各部分的尺寸存在着较大的差异。表1-13所示为常规注塑机螺杆的主要尺寸。
表1-13 常规注塑机螺杆的主要尺寸(平均) mm

注:螺杆的长径比约为20,螺距P=D,螺棱宽度为0.1D,最大进料长度等于D,表面粗糙度为Ra2~4μm。
(4)加工热塑性塑料用的特殊螺杆
针对某种物料特殊的加工性能,螺杆往往要设计成特殊的形式。对于高速注射成型,螺杆的长径比一般比较大,特别是像PP、PS等包装产品的加工所采用的螺杆长径比能达到25。
无计量段螺杆一般又被称为“ZM”螺杆。这种螺杆没有计量段,只有加料段和压缩段,两段各占螺杆长度的50%,长径比一般为20。没有计量段可以减少熔体过热现象的发生,提高物料的塑化能力和混炼效果,特别适合于注塑ABS和一些易发生剪切过热的非结晶型材料,如PVC、PC和填充PA等。
(5)新型螺杆
随着塑料的用途越来越广泛,对塑料制品的要求也越来越高。传统的三段式通用型螺杆已经很难满足物料的共混、着色混合、高度均化等的成型工艺要求。因此,各种新型螺杆,如销钉型螺杆、屏障型螺杆、分离型螺杆和波状螺杆等,就开始发展起来。这些新型螺杆弥补了普通螺杆的很多不足之处,提高了螺杆的混合、均化等性能。
①销钉型螺杆。对于普通螺杆,在加料段聚合物初步熔融的同时,在螺棱后缘也形成了熔膜。所以,整个固体床实际上被熔膜包围,降低了熔融效率。所谓销钉型螺杆(如图1-25所示)是指在螺杆的计量段设置混炼元件——销钉,起到混合和均化的作用。物料在塑化过程中,充分利用了销钉的分流作用,通过分流使物料得到进一步均化,在分流过程中,在前段未塑化好、被熔膜包覆的微小碎块会不断地从已熔融的物料中吸收热量,从而使整个熔融物料的温度降低。同时,当塑料通过销钉时,物料中的固相被粉碎细化,加速物料的塑化。经过销钉的多次分流及混合,大大提高了塑化质量。这种结构比较适合HPVC、PET等对温度控制要求较高,加工中要求温升小的物料。

图1-25 销钉型螺杆
销钉在塑化过程中主要起到混合和均化的作用,对销钉的选择要注意:销钉不应该具有输送作用;销钉对料流的阻力要小;要考虑机械制造加工的可能性。因此,要注意对销钉的位置、数量及环流面积等参数的选择。如图1-26所示为螺杆上销钉的多种排列形式,其中第Ⅴ项排列方式的混炼效果最好。

图1-26 多种销钉排列形式
对于销钉型螺杆,销钉段的长度一般为(4.5~5)D,销钉高度为0.07D,轴向间距为(0.3~0.35)D,圆周方向间距(0.3~0.35)D,销钉边宽为0.15D。
②屏障型螺杆。屏障型螺杆与销钉型螺杆相似,在计量段设置屏障型混炼元件。它的作用与销钉一样,有利于混合和均化的作用。因此,屏障型螺杆也应注意销钉型螺杆所应注意的问题。
屏障型混炼元件有直槽型(Maddock元件)、螺旋型和斜槽型等多种形式。如图1-27(a)、(b)分别为带有Maddock元件和斜槽型混炼元件的屏障型螺杆。对于带有Maddock元件的屏障型螺杆,物料在塑化过程中首先被分流成几股进入到进料槽内,塑化不良的小颗粒受到进料槽与出料槽之间屏障棱的强剪切作用,释放大量的热进一步熔融未熔的小颗粒,经过屏障型混炼元件后,物料得到均化和混合。对于这种结构,物料在进入均化段之前应含有一定的固相料,以发挥这种元件的最大效应。这种混炼结构的混合及塑化效果都比较好,但因物料经过屏障棱时存在高剪切的作用,因此,对某些透明度高的制品或热稳定性差的原料要注意混炼元件的参数选择。

图1-27 屏障型螺杆
③分离型螺杆。分离型螺杆又称为BM螺杆。这种螺杆的特点是在螺杆的熔融段(加料段、压缩段)增加一条副螺棱,其外径小于主螺棱,将主螺槽分为两部分,如图1-28所示。副螺棱的螺距比主螺棱的要大,副螺棱在熔融的结束段与主螺棱相交。副螺棱将主螺槽分为两部分,其中副螺棱的后缘与主螺棱的正推面构成了液相槽,液相槽逐渐由窄变宽;副螺棱的推进面与主螺棱的后缘构成了固相槽,固相槽逐渐由宽变窄。在塑化过程中,螺棱将熔料刮入到液相槽中,固相料全部留在固相槽中。因固相槽越来越窄,固相槽中的气体在压力的作用下向后,自料中排出,减少了制品中的气泡。同时,因固体床与熔池分开,保持固体床与料筒内壁的良好接触,也增大了固相料与料筒内壁的热交换面积,便于输送和传热。

图1-28 分离型螺杆
分离型螺杆的结构有许多种,其差异主要体现在副螺纹的螺距、螺纹升角及起始位置等。要根据实际情况合理地选定螺杆参数,包括压缩比、三段的分配及副螺棱的位置等。
④波状螺杆。波状螺杆不同于一般新型螺杆,它采用与新型螺杆不同的熔融和混炼机理。波状螺杆有单波和双波之分。单波螺杆是指在螺杆上只有一个螺纹,螺杆外径保持不变,两个相邻螺槽的底径虽然相等,但却是偏心的,而且偏心距相等并对称于螺杆轴线。螺槽深度在轴向呈现出波浪形变化。
双波螺杆是指在单波螺杆的螺槽中再附加一条平行副螺棱,且螺距相等,副螺棱低于主螺棱,一个螺槽的波峰对应另一个螺槽的波谷。在塑化过程中,主、副螺棱周期性变化的螺槽和螺棱间隙,不仅可以对物料进行周期性的强挤压剪切作用,吸收大量机械能并进行能量的转化,而且还可以不断进行汇合,有利于均化。进入到波谷的物料能够得到松弛,进行能量的均衡与温度的均化。已经熔融的聚合物将很快通过强剪切区,而剩余的固体物料将被迫受强剪切作用,从而加速了固体床的解体和熔融。所以,相对其他螺杆形式,波状螺杆不仅可以提高塑化能力,而且能增加混炼效果。
物料在深螺槽处停留时间较长,受到剪切作用较小;在浅螺槽处受到强剪切作用,但是作用时间较短。因此温升不大,可以实现低温注射。由于流道中不存在死角,所以还可以实现高速注射。这种螺杆非常适于含有填料、颜料及发泡剂的物料的注射成型,能得到混合均匀的组分,也适用于HPVC等热敏性原料,可减少降解。但是,这种螺杆的加工精度要求比较高,加工也比较困难,所以使用相对较少。
⑤加工热固性塑料螺杆。因其加工的物料为热固性塑料,因此应该防止出现因过剪切产生大量的热量而使其固化。常使用的螺棱深度比为(1∶1)~(1∶1.3)。加工热固性塑料螺杆的长径比通常要比加工热塑性塑料螺杆的小,为12~15。
与加工热塑性塑料螺杆相比,加工热固性塑料螺杆的压缩比较小而且不使用止逆阀。由于螺杆没有使用止逆阀,在注射保压阶段将会有很多的物料回流,所以螺棱深度与宽度就显得非常重要。螺棱宽度比加工热塑性塑料螺杆的螺棱要宽,为(0.15~0.2)D。宽螺棱能够增加抗磨性,同时减小螺槽截面,增加了物料回流的阻力。表1-14为加工热固性塑料螺杆的重要参考尺寸。
表1-14 加工热固性塑料螺杆的重要参考尺寸

⑥专用螺杆。螺杆的选用应该考虑加工材料的性能,如软化温度、黏度、硬度和热稳定性等方面的因素。对于特殊的材料,例如热敏性材料PVC、PC等,螺杆应该根据材料的特性来选用。
专用螺杆类型及说明见表1-15。
表1-15 专用螺杆类型及说明


(6)螺杆的磨损及磨损防护
注塑机螺杆的工作环境非常差,长时间处在高温、高压、高转矩、高摩擦及频繁启动环境下,而且在加工一些腐蚀性强的物料(如PVC)时,要受到非常强的腐蚀作用。高温、高压等环境因素,是注射成型工艺条件所需,所造成的磨损是不可避免的。一般螺杆都进行过表面氮化处理,以提高表面硬度,亦即提高抗磨损能力。但是如果忽略了引起磨损的原因,不设法将磨损尽量降低,必然会大大降低螺杆的工作寿命。
①塑料在进行加工前一般都要进行干燥处理,进入料筒内加料段后必然会出现干性摩擦。当这些塑料因受热不足而熔融不均时,很容易造成料筒内壁及螺杆表面磨损。同样,在压缩段和均化段,如果塑料的熔融状态不均匀,也将会对螺杆料筒造成磨损。每种塑料都有一个理想的塑化加工温度范围,料筒温度的设置应该接近这个温度范围。
②螺杆转速应调校得当。由于部分塑料中加有强化剂,如玻璃纤维、矿物质或其他填充料,这些物质对螺杆的摩擦力比熔融塑料大得多。例如,高转速塑化玻璃纤维时,在提高对玻璃纤维的剪切力的同时,也将会产生更多被撕碎的纤维,这些被撕碎的纤维含有锋利末端,对螺杆的磨损作用非常强。无机矿物质在金属表面高速滑行时,其刮削作用也不小。所以,螺杆转速不宜调得太高,应调校得当。
③去除塑料中的杂物。因各种原因,塑料原料中可能会含有小如金属屑末、大如螺母等的各种杂物,这对螺杆的损坏极其严重。因此,一般要在料斗加料口位置安装磁铁架,吸附各种金属杂质,严格监控加料过程。
④塑料中所含水分会对螺杆表面造成一定影响。未完全干燥的塑料,在加工时很可能会将残留的水分带入到螺杆压缩段,形成高温高压的“蒸汽粒子”,随着螺杆的推进,物料从均化段移至螺杆头部,在这一过程中,这些“蒸汽粒子”卸压膨胀,有如一颗颗微细的杂质硬粒,对壁面产生摩擦破坏作用。此外,对某些种类的塑料,在高温高压下,水分可能会变成促使塑料裂解的催化剂,产生能侵蚀金属表面的有害物质。因此,塑料注塑前一定要进行烘干,这不仅会影响制件的质量,而且还会影响到螺杆的工作寿命。
2.螺杆头
(1)螺杆头的结构形式与用途
根据加工目的不同,可选用不同结构的螺杆头。螺杆头可分为回泄型和止逆型两大类,共六种类型,见表1-16。回泄型中又可分为两种:尖头形和钝头形;而止逆型中可分四种:环形、爪形、销钉形和分流形。
表1-16 螺杆头的结构形式与用途


在加工类似RPVC类热敏性、高黏度的塑料时,采用平尖形螺杆头(也称为锥形)。其锥角α一般为20°~30°,其中一种为光滑圆锥头,另一种在锥形处加工出螺纹。这两种平尖形螺杆头结构简单,能消除滞料分解现象。而加工低黏度塑料和成型形状复杂的制品时,为了防止塑料的流涎,提高注塑效率,稳定工艺过程和工艺参数,常采用止逆型螺杆头。
以上几种均为普通型的止逆环,可应用于多种注塑机的螺杆上。但是,随着注射成型工艺要求的提高,如精密注射、高度均化等,普通型止逆环已经难以符合要求,并促使新型止逆环的诞生,以下为几种新型止逆环(见表1-17)。
表1-17 新型止逆环


(2)螺杆头磨损及磨损防护
螺杆头位于螺杆的最前端,主要作用是减少物料的回流,减少压力的损失及清料等。螺杆头的类型有尖头形、钝头形及止逆型。
如图1-31所示为普通尖头螺杆头。螺杆头与螺杆之间采用简单的螺纹连接。尖头夹角在60°~90°,角度可以根据物料的不同而改变,对于热敏性物料,螺杆头的夹角可以很小。螺杆头直径大于螺杆末端螺棱直径。虽然与料筒之间的狭小间隙促使压力上升,抑制了物料的回流,但是并不能够完全达到密封的效果。

图1-31 普通尖头螺杆头
如图1-32所示为加工硬质PVC的各种类型的螺杆头。对于PVC料,一般用敞开式结构的螺杆头,螺杆头的锥角一般很小,为20°~30°,以减少注射时物料流动的阻力,促进熔体流动并且可以在注射和保压阶段防止物料回流。在螺杆头上设有螺旋式结构,不但可以提高输送效率,而且可以排清易滞料分解的物料。

图1-32 加工硬质PVC螺杆头
止逆型螺杆头即在螺杆头上设有止逆阀,以防止中低黏度的物料在注射保压时沿螺槽回流。其具体工作过程为:塑化时利用熔料本身的压力顺利地通过止逆阀;注射和保压时,利用螺杆头部的高压将止逆阀闭紧,在防止物料回流的同时也达到精确计量的目的。
3.料筒
料筒大多数都采用整体结构,如图1-33所示。料筒是塑化装置重要的组成部分,一般都是一根直筒。目前,注塑机料筒多为整体式结构,材料可用45#钢表面镀铬、氮化钢内表面渗氮处理、加用合金钢衬套或双金属。双金属料筒是目前使用最为广泛的料筒类型,在料筒的内表面浇铸非常薄的一层特种合金,如“Xaloy”“Reiloy”和“BRUX”等,这些加入的合金大大提高了料筒的寿命和承载能力。

图1-33 料筒结构
料筒与螺杆之间配合非常紧密。螺杆与料筒之间的径向间隙一般为0.2mm。如果螺杆直径不大于40mm,则间隙约为0.15mm。对于排气类料筒则要在其上开设排气口。
塑料在塑化过程中所需的热量主要由料筒提供。料筒的热量则来自于包覆在料筒外部的加热圈。加料口及附近的几个螺棱处一般不设置加热圈,以防止物料过早熔融,降低输送能力,因此这些地方需要进行冷却。温度对制品的质量有着非常大的影响,对温度需要进行精确的控制。目前,对料筒温度控制多采用PID控制,其精度可以达到±1℃。采用模糊控制,控制精度可以达到±0.1℃,而且对温控制区应实现多段闭环的控制。
注塑机加料一般采用自动加料的方式,因此,加料口必须保证能满足自动加料的输送能力。加料口有圆形也有矩形,目前大部分料筒开的是矩形的料口。加料口开口长度为(1~2)D。料筒加料口轴线可正对称于料筒轴线,也有偏置类型。为了能提高进料速度,加料口稍向螺杆旋转反方向偏一定位置。
为了提高固体输送效率,一般会在料筒的加料段开设纵向的沟槽或加装固体输送套。对于固体输送套,一般的推荐长度为(4~5)D,沟槽锥度为3°~5°,槽数为6~8。
当料筒受磨损严重或因物料滞留需要清理时,料筒要能够方便地拆卸。因此,应尽量使用螺栓和螺钉类元件。随着注塑机的快速发展,料筒更换方式的发展也非常快,有半自动也有全自动的方式。
(1)料筒间隙
料筒间隙是指料筒内壁与螺杆外径的单面间隙。此间隙太大,塑化能力降低,注射回泄量增加,注射时间延长;如果太小,热膨胀作用使螺杆与料筒摩擦加剧,能耗加大,甚至卡死,此间隙Δ=(0.002~0.005)ds,见表1-18。
表1-18 料筒间隙值 mm

(2)料筒的加热与冷却
料筒加热方式有电阻加热、陶瓷加热、铸铝加热,应根据使用场合和加工物料合理配置。常用的有电阻加热和陶瓷加热,后者较前者承载功率大。
①为根据注塑工艺要求,料筒需分段控制,小型机三段,大型机五段。控制长度为(3~5)ds,温控精度±(1.5~2)℃。而对热固性塑料或热稳定性塑料,为±1℃。
②注塑机料筒内产生的剪切热比挤出机要小,常规下,料筒不专设冷却系统,靠自然冷却,但是为了保证螺杆加料段的输送效率和防止物料堵塞料口,在加料口处设置冷却水套,并在料筒上开沟槽。
4.喷嘴
(1)功能
喷嘴是连接注射装置与模具流道之间的重要零部件。其主要功能包括:预塑时,在螺杆头部建立背压,阻止熔体从喷嘴流出;注射时,建立注射压力,产生剪切效应,加速能量转换,提高熔体温度均化效果;保压时,起保温补缩作用。
(2)分类
喷嘴可分为敞开式喷嘴、自锁型喷嘴、液压控制喷嘴、热流道喷嘴和多流道喷嘴,其说明见表1-19。
表1-19 喷嘴的分类


(3)喷嘴的使用要求
对喷嘴的要求主要包括以下方面。
①喷嘴安装。喷嘴头与模具的浇套要同心,两个球面应配合紧密,否则会溢料。一般要求两个球面半径名义尺寸相同,而取喷嘴球面为负公差,其口径略小于浇套口径0.5~1mm为宜,二者同轴度公差应小于或等于0.25~0.3mm。
②喷嘴口径。喷嘴口径尺寸关系到压力损失、剪切发热以及补缩作用,与材料、注塑座及喷嘴的结构形式有关,见表1-20。高黏度物料取(0.1~0.6)ds,低黏度物料取(0.05~0.07)ds,ds为螺杆外径。
表1-20 喷嘴口径尺寸的影响因素
