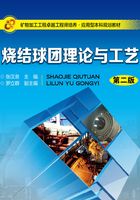
1.2 现代高炉精料方针
1.2.1 合理的高炉炉料结构
从理论上和高炉经营管理的角度看,使用单一矿石并把熟料率提高到100%是合理的。然而目前还没有一种理想的矿石能够完全满足现代大型高炉强化的需要。炉料结构合理与否直接影响高炉冶炼的技术经济指标。目前高炉炉料结构:
①100%酸性球团矿,但每吨生铁需加250kg以上的石灰石。
②以酸性球团为主,配加超高碱度烧结矿。
③100%自熔性烧结矿。
④以高碱度烧结矿为主,配加天然矿或酸性球团矿。
采用什么样的炉料,应依据国家的具体条件,即合理利用国家资源而定。合理炉料结构应从国家和本企业实际情况出发,充分满足高炉强化冶炼的要求,才能获得较高的生产率,比较低的燃料消耗和好的经济效益。符合这些条件的炉料组成就是合理的炉料结构。
国内外高炉炼铁的实践表明,精料(high-grade burden)对高炉炼铁科技进步的影响率在70%左右。精料工作是高炉的基础,精料技术是钢铁企业的核心竞争优势,是成本领先的关键。
炼铁高炉的精料技术要重点突出“高品位、高强度、高碱度、高熟料率、净炉料、粒度均匀、稳定性好、有害杂质少、冶金性能好”等技术特点。精料的基本因素包含入炉矿品位高、矿石的冶金价值高、烧结矿和球团矿的强度高、烧结矿碱度高等内容。
高碱度烧结矿与熔剂性烧结矿相比,具有强度好、含 FeO 低、还原性好、软化温度高等优点。目前,国内外炼铁企业大多数采用70% 左右的高碱度烧结矿的炉料结构。
精料技术的内容:精料技术对高炉炼铁技经指标的影响率在70%,其中焦炭质量的影响占30%左右,高炉操作占10%。精料技术的内涵有:高、熟、稳、均、小、净、少、好八个方面。
(1)高 入炉矿含铁品位高,原燃料转鼓指数(强度)高。品位高是精料的核心,经验数据表明,高炉入炉矿石品位提高1%,焦比下降2.5%,产量提高3%,吨铁渣量减少30kg,允许多喷煤粉15kg。2013年我国高炉入炉矿品位较高的企业是:宝钢和太钢均为59.61%、包钢59.42%、兴澄59.21%、沙钢58.77%、鞍钢58.70%等。国际上最先进水平高炉入炉矿品位为64%,其相应渣量在150kg/t铁左右。
(2)熟 指烧结矿加球团矿占入炉料比例。熟料比下降1%,焦比会升高2~3kg/t。国内外高炉炼铁生产实践表明,使用熟料炼铁可大幅度改善高炉各项技术经济指标。因为熟料可提高铁矿在高炉内的间接还原比例,提高炉料透气性,降低燃料消耗,提高产量。2007年上半年全国重点企业熟料比为92.48%,宝钢为81.42%,海鑫为76.32%,鞍钢为97.21%,首钢为83.05%,莱钢为91.55%,三明为96.88%,邯钢为87.96%。2013年我国重点企业熟料比为91.73%。每提高1%的熟料比可降低焦比1.2kg/t,增产0.3%左右。近些年我国高炉的熟料比已从小于50%提高到80%~90%。首钢、鞍钢、本钢一般在95%以上,接近100%。
(3)稳 原燃料化学成分和物理性能要稳定,波动范围要小。要求:品位波动<0.5%,碱度波动<0.05;影响:品位波动1%,产量影响3.9%~9.7%,焦比2.5%~4.6%;碱度波动0.1,产量影响2%~4%,焦比1.2%~2.0%。目前,我国高炉生产中存在的最大问题之一是原燃料成分波动大。
(4)均 入炉原燃料粒度要均匀。粒度均匀会提高炉料透气性,提高矿石间接还原度,炉料的填充作用,使孔隙度减少。粒度均匀会降焦增产。烧结和焦炭均要进行整粒,目的就是要实现粒度均匀,例如焦炭要保证60mm左右粒度占80%以上,>80mm的要小于10%,物料中-5mm含量的比例要小于5%,5~10mm比例要小于30%。
炉料中粒度尺寸大小的比例与大小粒级所占的百分比,对炉料在炉内的透气性起着决定性作用。混合料中大粒度级和小粒度级的增加,都会使混合料的孔隙度变小,使煤气通过料层的阻力增加而影响高炉的顺行。优化的粒级组成是粗细粒度级的粒度差越小越好。
(5)小 是指原燃料粒度要小。烧结25~40mm,焦炭25~45mm,球团8~15mm,块矿8~30mm。炉料粒度偏小,比表面积大,与还原剂接触面大,可提高矿石还原度,提高间接还原比例。个别企业加入的白云石粒度偏大,造成焦比升高。没完全熔化的白云石进入炉缸,消耗炉缸的热量。块矿、球团、白云石均有穿透现象,会比炉料提前进入炉缸。高炉炼铁实践表明,最佳强度的粒度是:烧结矿为25~40mm,对容易还原的赤铁矿和褐铁矿为8~20mm;入炉粒度由10~40mm降为8~30mm时,高炉产量可增加9.6%,焦比下降3.1%。
(6)净 要筛除小于5mm的粉末。净炉料能提高高炉炉料的透气性,为提高高炉冶炼强度、高炉顺行高产和增加喷煤比创造出有利条件,为减少炉料之间的填充作用,要求5~10mm粒度的炉料所占比例要<30%;要求5mm以下的炉料占全部炉料的比例不超过3%~5%,5~15mm的比例要小于30%,实现上述要求焦比下降0.5%,产量增加0.4%~1.0%。物料中-5mm含量从4%升到11%,煤气阻力由1.6升到2.9,焦比升高1.6kg/t。
(7)少 含有害杂质少。S≤0.3%、P≤0.2%、Cu≤0.2%、Pb≤0.1%、Zn≤0.08%As≤0.07%、K2O+N2O≤0.25%;焦炭灰分中含有K2O+N2O要少,煤中硫含量要小于2.0%。
(8)好 铁矿石冶金性能好。铁矿石还原性好:还原率大于60%;低温还原粉化率每升高5%,产量下降1.5%。
1.2.2 提高入炉矿品位
①配用高品位的矿石。进口矿的品位高,能有效地提高入炉矿品位。
②烧结采取高铁低硅新技术。“吃百家矿”的企业,尽可能选购高铁低硅的矿粉,提高烧结原料的品位,同时采取高铁低硅新技术生产高品位烧结矿。低SiO2烧结矿不仅具有良好的还原性能,还有较好的高温冶金性能。
③球团矿提高品位的方法是:将矿粉磨细,提高精矿细度,-0.074mm含量≥70%,TFe≥68%;减少皂土用量,提高球团矿的品位;降低球团矿SiO2含量,对于提高品位、改善球团矿性能也有良好的作用。
高炉入炉料的强度是用转鼓指数来表示的,我国大部分企业采用YB/T 5166—93行业标准和GB/T 27692—2011国家标准,高强度烧结矿的一级品转鼓指数ISO≥66.0%,优质烧结矿ISO≥70%。我国要求球团矿ISO>78%,抗磨强度A<5%,抗压强度>2000MPa。生产实践表明:在其他条件比较理想的情况下,入炉烧结矿和球团矿的转鼓指数稳定升高1%,高炉产量将提高1.9%左右。
1.2.3 提高烧结矿强度
①控制原料粒度:矿粉的粒度要控制在8mm以下,中间粒级0.125~1mm的部分要控制在一个合适的范围;焦炭粉和熔剂的粒度要<3mm,同时焦粉<0.25mm的细粒越少越好。
②严格控制混合料水分:混合料对磁铁矿和赤铁矿适宜的水分要求在7%~9%,而波动的范围一般<0.5%。原始混合料水分一般为混合料最大透气性时水分量的90%,一次混合时水量要加到合适总量的99%,以保障物料的潮湿和制粒,在二次混合中只添加1%的水分作调整。
③加强混合料的制粒:二次混合的主要任务是强化粒度。一次混合与二次混合的时间比约为2∶1,总的混合时间在9min左右为佳。混合时间长造球性能好,进而改善烧结机的透气性,但会增加设备投资。均匀混合的制粒是提高烧结矿强度的关键,一些单位甚至加长了圆筒混合机的长度或增加混合次数。
④以细精矿为主的烧结厂,可适当添加石灰。预热混合料到烧结废气的露点以上;石灰作为粘结剂,强化混合料的制粒。
⑤加强对烧结机的点火温度、料层厚度、机速、抽风等工艺参数的控制。
1.2.4 提高球团矿强度
①要细精矿粉的-0.074mm粒级含量>85%;-0.044mm粒级含量>60%。
②高球团矿质量的关键是精矿粉造球的质量,对添加水分和皂土量要根据不同矿物性能选择最佳值。
③生产实践表明,采用大型链箅机-回转窑生产的球团矿质量要比竖炉工艺好。
要求荷重软化温度高,铁矿石熔滴温度高,铁矿融化区间窄。
1.2.5 铁矿石的冶金性能
铁矿石的冶金性能(metallurgical properties)包括还原性、低温还原粉化性、荷重还原软化性和熔滴性等,是指矿石在冶炼状态下(高温、还原性气氛)表现出的一些性能。
①矿石的还原性——还原指数(reduction index) 铁矿石的还原性取决于矿物性质、矿石种类、矿石所具有的气孔度及气孔特性等。矿物特性是Fe2O3易还原,Fe3O4难还原,2FeO·SiO2更难还原,其次是赤铁矿,而磁铁矿难还原。
还原指数RI>60%的矿石为还原性好的铁矿石,大高炉要求矿石还原性要改善10%,其波动范围在±1%。矿石的还原性与FeO含量相关性强,一般FeO含量高还原性能差。
目前在部分企业对烧结矿还原性好的认识还很一般,缺乏深入的研究,没有有效的技术措施控制烧结矿还原性。
②低温还原粉化性(reduction degradation index) 高炉原料(特别是烧结矿)在高炉上部的低温区还原时会严重破裂、粉化,使料柱的空隙度降低,煤气透气性恶化。
低温还原粉化性RDI每升高5%,高炉产量下降1.5%,CO利用率也会下降。RDI的高低与烧结生产使用的矿粉种类有关。富矿粉生产出来的烧结矿RDI偏高,含TiO2高的精矿粉生产的烧结矿RDI也高,而采用磁精矿粉RDI就低。降低RDI的办法是设法减小造成烧结矿RDI升高的骸晶状菱形赤铁矿的数量,可适当增加FeO含量和添加卤化物CaF2,CaCl2等。许多企业在烧结矿成品表面喷洒3%的卤化物溶液,使RDI降低了10.8%~15%,高炉产量提高约5%。
③荷重还原软化性能(softening point under load) 铁矿石软化温度是指矿石在荷重还原条件下,收缩率在到达3%~4%时的温度。为有利于高炉煤气顺利通过软熔带,要求铁矿石软化温度要高一些,软熔温度区间要窄。
影响矿石软熔性的主要因素是渣相的数量和熔点,矿石中FeO含量和其生成矿物的熔点,还原过程中产生的含铁矿物及金属铁熔点也对矿石的熔化和滴落产生重大影响。2FeO-SiO2的熔化温度低(1205℃),而2FeO-SiO2-SiO2共熔混合物熔点仅1178℃,2FeO-SiO2-FeO熔点为1177℃。所以,要减少烧结矿中的FeO含量。将炉渣中MgO含量控制在4%~10%,提高碱度有利于提高脉石熔点,这也就提高了矿石的软熔性。
④熔滴性(melting-down properties) 滴落温度是指铁矿石在高炉开始还原熔化的温度。为使高炉生产顺行,要求铁矿石熔滴温度高、区间窄,这可使高炉内煤气压差低一些。