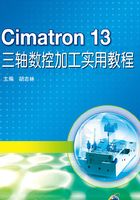
1.2 Cimatron编程流程
Cimatron软件的编程流程根据编程者的经验和零件的复杂程度会稍有不同,下在将详细介绍完成零件的编程步骤。
1.2.1 读取模型
读取模型就是将一个完整的CAD模型调入到编程环境,对模型(加工对象)进行程序的编制,读取的模型可以是单个零件也可以是一个包含多个零件的组件,但无论是单个零件还是组件均要求是Cimatron格式,如果不是Cimatron格式,需要使用导入功能转换为Cimatron格式。
按照本书1.1节中介绍的方法,进入到图1-3所示的编程环境窗口后,单击“编程向导”栏上的“读取模型”按钮,系统将打开Cimatron浏览器(图1-15),选择文件路径和文件名,单击“选择”按钮,或者双击“飞机模型”即可将模型调入到编程环境。

图1-15 调入模型
模型调入到编程环境后,可以指定模型的放置位置,系统默认设置是直接放置到当前坐标系的原点,同时不做旋转。在“特征向导”栏中有两个可选项,如图1-16所示,可以对模型重新定位或者根据要求进行旋转。

图1-16 “特征向导”栏
模型加载完毕,会在图1-4中“4”所示的交互区域出现零件模型,如图1-17所示。

图1-17 模型加载到交互区域
1.2.2 NC_Setup设置
双击图1-17中NC程序管理器里的“NC_Setup”,可以设置的参数包括零件材料、参考坐标系、使用的机床和后处理等(图1-18),用于后续各种NC操作的默认选项数据。详细的设置见第7章的练习。

图1-18 将模型加载到交互区域
1.2.3 创建零件
单击图1-17中NC程序管理器里的“目标零件”,会弹出“零件”对话框,同时窗口上显示的所有曲面自动被选中用来创建零件,如图1-19所示。在“零件”对话框可以显示出选择曲面的数量、最大和最小位置的尺寸,这些信息可以通过单击对话框“收起”按钮隐藏起来,单击“确定”按钮,即可完成零件的创建。

图1-19 “零件”对话框
提示:1)零件类型有以下3种。
①“目标”:表示理想情况下的最终产品,在后期的模拟中用来与实际加工结果进行比较,从中可以发现程序编制是否合适以满足加工要求。
②“夹具”:用在机床模拟里。以检查机床部件是否和实际夹具干涉。
③“其他”:表示机床有多个加工任务的情形,也是用在机床模拟里。
2)创建零件时,系统默认模型的所有面为要创建的零件面,如果打算取消选择的所有面,则可以单击图1-19对话框中“重置选择”按钮,或者右击后在弹出的快捷菜单中选择“重置所有”命令,如图1-20所示。

图1-20 零件面的选取和取消
1.2.4 创建毛坯
单击图1-17中NC程序管理器里的“毛坯_自动”,会弹出“初始毛坯”对话框(图1-21),用以定义合适的毛坯参数。

图1-21 “初始毛坯”对话框
使用“毛坯类型”右侧的“限制盒”选项,单击“确定”按钮以完成毛坯的创建。零件和毛坯程序名称都会显示在NC程序管理器里,此时零件和毛坯程序名称前面的“状况”显示的是绿色对号,表示已经完成创建,如图1-22所示。

图1-22 NC程序管理器中显示的零件和毛坯
提示:
1)毛坯是模型在加工之前的状态,创建毛坯可以用于机床实际加工模拟,也可以优化刀具路径,提高加工效率和安全。
2)单击图1-21中“毛坯类型”下拉列表框可以选择创建毛坯的类型,共有7种方式。
①“根据曲面”:通过曲面偏移来创建毛坯,常用来创建铸件毛坯。
②“根据轮廓”:通过选择一条轮廓来创建毛坯。
③“长方体”:通过两个角点定义矩形毛坯。
④“限制盒”:根据选择的曲面创建一个包容盒来创建毛坯,各个方向可以再加上偏移量。
⑤“自文件”:从STL格式的文件创建毛坯。
⑥“自网格面”:从保存过的网格文件创建毛坯,只能选择网格面。
⑦“固化残留毛坯”:在程序间创建剩余毛坯。
图1-21显示的是用“限制盒”毛坯类型创建毛坯的情形,是系统创建毛坯的默认方式。这种方式可以自动创建一个能包容所有曲面的长方体,毛坯的透明度可以通过拖动该对话框中的“透明度”上的导滑条来控制。
该对话框中显示出了选择的零件曲面数量以及角点的位置,如果默认的曲面不是所需要的,则可以通过单击“重置选择”按钮取消选择,再通过手动或者根据规则重新拾取曲面。
该对话框可以对X、Y、Z方向做偏置,Z方向还可以有正负之分。
1.2.5 模型数据分析
模型数据指的是模型的关键尺寸、各处圆角大小以及模型的拔模角大小等,对模型进行数据分析可以帮助编程者选择刀具和制定合理的加工工艺。以下是常用的数据分析功能:
1)通过图1-4所示工具栏中的“测量”按钮,可以测量模型最大长度、宽度和高度,如图1-23a所示。
2)通过选择图1-4所示菜单栏中“分析”|“曲率图”命令,可以了解零件最小圆角以及其他部位的圆角大小,例如底部圆角是R3,如图1-23b所示。
3)通过选择图1-4所示菜单栏中“分析”|“方向分析”命令,可以了解零件各处的拔模角大小,例如通过分析可以知道零件四周是垂直的面,如图1-23c所示。

图1-23 模型的数据分析
1.2.6 创建刀具
创建刀具就是创建加工程序中所需要的所有刀具,单击图1-4所示编程向导栏上的“刀具”按钮,进入到“刀具及夹持”对话框,如图1-24所示。
在该对话框里,可以创建各种类型和规格的刀具,定义刀具的加工参数和运动参数,定义的这些参数可以被自动输入到程序参数里。
完成图1-24所示的刀具定义后,单击“确定”按钮退出“刀具及夹持”对话框。

图1-24 “刀具及夹持”对话框
提示:编程时可以在预设定处设置自动加载刀具库,这样可以自动把事先定义好的刀具加载进来,以节约创建刀具的时间,提高编程效率,如何加载刀具库后面有介绍。
1.2.7 创建刀轨
单击图1-4所示编程向导栏中的“刀轨”按钮,弹出“创建刀轨”对话框,如图1-25所示。在该对话框中完成以下内容的设置。
1)输入刀轨的名称,可以输入中文,名称一般与编程内容有关。
2)选择加工类型,类型指的是使用机床的加工轴数量,例如3轴,由零件的加工工艺决定。
3)微铣削:此选项加工精度可以达到0.0001mm,可加工精度更高的零件。
4)指定加工坐标系:选择一个合适的编程坐标系,可在下拉列表中进行选择,也可以单击黄色箭头进入交互区选择坐标系。
5)指定起始点:起始点是程序最初的位置点,一般“X”为0,“Y”为0,“Z(安全高度)”在零件最高点上方50mm处,后处理中可以输出起始点的坐标值。
6)输入注释:输入刀轨注释。通过后处理,注释也可在G代码文件里体现出来,供操作者参考。
单击“确定”按钮完成刀轨的创建。

图1-25 “创建刀轨”对话框
提示:创建刀轨的全称是创建刀路轨迹,这里关键的是确定需要几轴(有2.5~5轴可供选择)加工。刀路轨迹包含一个或者多个程序,一个NC编程文件可以包含多个刀路轨迹,多轴编程时每个刀路轨迹还可以使用不同的坐标系,但是后处理时使用的坐标系是同一个。
1.2.8 创建程序
在向导模式下(设置方法详见1.1.6节),单击图1-4所示编程向导栏中的“程序”按钮,弹出“程序向导”对话框,如图1-26所示。

图1-26 “程序向导”对话框
在“程序向导”对话框,按照以下步骤可完成程序的创建:
1)选择加工策略和工艺。单击“主选项”下的按钮选择“体积铣”策略,在“子选择”下选择“环绕粗铣”工艺。
2)选择加工对象。单击“轮廓(可选)”右侧的“数量”按钮,弹出“轮廓管理器”对话框(此处选择了底部外轮廓);单击“零件曲面”右侧的“数量”按钮,可以去交互区选择加工曲面。对于粗加工,如果选中“多个曲面组”,系统允许对加工曲面进行分组,不同的组可以给定不同的加工余量。
单击“零件曲面”右侧“数量”按钮,弹出曲面选择相关按钮,如图1-27所示,单击其中“选择所有显示曲面”,再单击鼠标中键就可以完成曲面的选择操作,所选择的零件曲面的数量会在数量按钮上显示。图1-28所示的已经选择了91张面。

图1-27 零件曲面选择

图1-28 选择的加工对象数量显示
提示:
1)不同的加工工艺所选择的加工对象是不同的,常见的加工对象有加工轮廓、零件曲面、检查曲面等,零件曲面是加工的参考对象,检查面是用来防止干涉的。
2)使用普通2.5轴和普通钻孔工艺时不需要选择零件曲面,但使用3轴里的策略编程必须选择零件曲面,否则不能计算出轨迹。
3)加工轮廓用来确定刀具加工范围,可根据需要进行选择,加工轮廓不是必须要选择的。
3)选择刀具。完成加工对象的定义后,单击图1-26所示“程序向导”对话框上的“刀具”按钮,弹出“刀具及夹持”对话框,如图1-29所示,和1.2.6节中创建刀具的对话框一样。在这个对话框可以选择刀具库中已经存在的刀具,也可以创建新的刀具。

图1-29 “刀具及夹持”对话框
选择图1-29显示的刀具规格,在右边显示的模型上任意点处单击可以显示要加载的刀具,这样便于查看所使用的刀具是否合适,单击该对话框上的“确定”按钮完成刀具的选择。
4)设置刀路参数。单击图1-26“程序向导”对话框中的“刀路参数”按钮,弹出“刀路参数设定”对话框(图1-30),设定刀路的各种参数,例如进、退刀方式,曲面余量和步距等。
提示:
1)在该对话框中,左侧显示的是参数名称,右侧列出了参数数值,单击参数组名称前面的“+”可以展开该组参数,单击“-”可以收起该组参数,不同的加工工艺,显示的参数是不同的。
2)在参数输入时,对话框上方会显示参数的含义,参数含义部分的显示和隐藏由工具栏上的“编程助手”按钮来控制。
5)设置机床参数。单击图1-26所示“程序向导”对话框中的“机床参数”按钮,弹出“机床参数设定”对话框,设定主轴转速、进给、切入和插入进给率等,可按图1-31所示的参数设置。

图1-30 “刀路参数设定”对话框

图1-31 “机床参数设定”对话框
6)快速预览编程结果。单击图1-26所示“程序向导”对话框中的“预览”按钮,弹出“预览”对话框,如图1-32所示。它不通过程序计算就可以方便地查看剩余毛坯的大小,也可以计算最小的刀长,图1-32所示为显示当前参数下程序加工后的毛坯剩余情况。

图1-32 快速预览编程结果
提示:“6)快速预览编程结果”可以在“5)设置机床参数”之前进行。
7)保存程序。完成各种参数设定后,即可退出图1-26所示“程序向导”对话框并保存程序,退出的方式有以下两种:
① 保存并关闭。用以保存参数设置并退出参数设置状态,程序并不立刻进行计算,程序状态显示的是黄色“
”号,表示程序的参数设定完毕,但尚未执行计算,它是不能用来进行后处理操作的,多个保存并关闭的程序会在后面一起进行计算。
② 保存并计算。用以对设置的程序参数进行计算,计算完成后,会在编程窗口交互区显示刀路轨迹,并在NC程序管理器中显示刚生成的加工程序。
单击“保存并计算”按钮,可得到图1-33所示的结果,在NC程序管理器的“状况”中显示绿色的
,说明程序已经完成计算。

图1-33 保存并计算后的NC程序管理器和刀路轨迹
1.2.9 模拟程序
单击图1-4所示编程向导栏中的“机床模拟”按钮,弹出“机床模拟”对话框,如图1-34所示。需要完成以下参数的设置。

图1-34 “机床模拟”对话框
1)选择要模拟的程序。
图1-34中的绿色按钮是把选择的单个程序添加到右侧“模拟的程序序列”,
是把左侧所有程序添加到右侧“模拟的程序序列”进行模拟。按钮
和
是把在“模拟的程序序列”里的单个程序或者所有程序取消。
此处选择即可把左侧程序导入到“模拟的程序序列”里。
2)选择模拟方式。
模拟方式有标准、快速和超快3种,如图1-34所示。标准和快速方式下均可以带着机床模拟,超快方式下不可以带机床模拟。标准方式下模拟得更准确,快速方式下模拟得比较快,但是精度不高。
提示:
1)在图1-34所示的“机床模拟”对话框里,选中“材料去除”选项,可以把毛坯加载到模拟环境中,刀具会按照刀路轨迹对毛坯进行模拟切削。
2)在“机床模拟”对话框里,系统默认设置是选中“检查参照体”选项,参照体就是最开始做的那个“零件”程序,用以发现模拟的加工过程中是否产生碰撞和过切,便于为实际加工提供指导。
在“机床模拟”对话框的“方式”中选择默认的“标准”选项,不选中“使用机床”选项,单击“确定”按钮可进入到图1-35所示模拟环境。单击图中箭头所指的“播放”按钮,即可进行实时模拟。图1-36所示是模拟铣削加工的结果。

图1-35 机床模拟环境

图1-36 模拟结果
1.2.10 后置处理
单击图1-4所示“编程向导”栏中的“后处理”按钮,弹出“后处理”对话框(图1-37),按照图中所示进行设置后再单击“确定”按钮,即可弹出G代码文件,如 图1-38所示。

图1-37 “后处理”对话框

图1-38 G代码
1.2.11 生成加工报告
单击图1-4所示“程序向导”栏中的“NC报告”按钮,弹出“NC报告”对话框,如图1-39所示。该对话框用以选择输出格式和模板名称。先将零件拖动至矩形框中间以复制图片并将其自动输出到报表里。
单击“确定”按钮就可以得到一张加工报告,如图1-40所示。
提示:
1)加工报告便于车间的管理,可以根据不同客户的要求来定制,可以输出.xls、.mht、.pdf等格式的文件。
2)报告使用的模板需要放到Cimatron软件安装目录\date\nc\Customized Reports下,否则无法生成报告。

图1-39 “NC报告”对话框

图1-40 加工报告
综上所述,Cimatron软件的编程流程为:加载模型→NC_Setup设置→创建零件→创建毛坯→数据分析→创建刀具→创建刀轨→创建程序→模拟程序→后处理→生成加工报告。